Compressed air ionizers help you prevent static damage and contamination across seven key industrial applications. You'll find them protecting sensitive electronic components during manufacturing, maintaining cleanroom integrity for medical devices, and controlling static in cleanroom environments. They're essential for flat panel display assembly lines, preventing film adhesion in plastic processing, and safeguarding semiconductor wafers during handling. You'll also see them integrated into circuit board protection systems, where they neutralize charges that could harm delicate components. Understanding these applications can transform your approach to static control and manufacturing efficiency.
Electronic Component Manufacturing
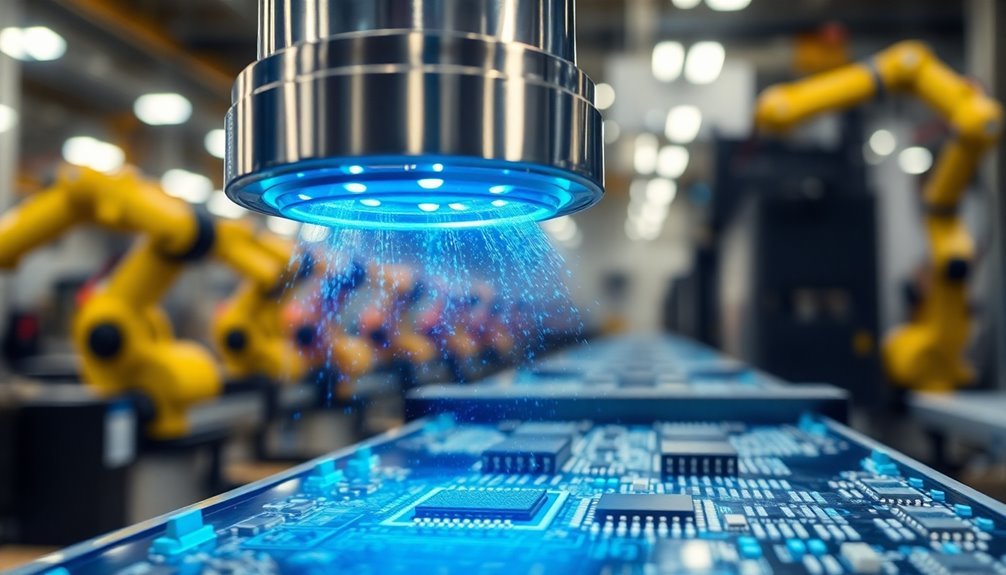
Static electricity poses a significant threat in electronic component manufacturing, where even minor electrostatic discharges can damage sensitive parts.
You'll find compressed air ionizers playing a vital role in protecting components throughout the production process, from semiconductor fabrication to PCB assembly.
When you're operating high-speed production lines, you'll need efficient ionizers like Panasonic's ER-X series to guarantee rapid neutralization of static charges. The system's remarkable ability to balance charges in under 1 second makes it particularly valuable for high-volume manufacturing operations.
These systems use pulsed AC operation to cover large working zones effectively. For semiconductor production, SMC's IZS series provides essential protection against electrostatic charging, while table ionizers maintain ESD protection at professional workstations. Operating at 5.5 to 6 kV, these ionizers deliver reliable static elimination performance.
To maximize your ionizer's effectiveness, you'll need to take into account proper installation positioning and maintain clean, dry compressed air quality.
You can achieve ideal results by implementing dual-AC ionizers, which reduce potential amplitude by emitting positive and negative ions simultaneously.
For confined spaces in your manufacturing system, you'll benefit from space-saving solutions like SMC's IZT series.
Modern ionizers with feedback sensors will automatically detect and adjust to electrostatic charges, enhancing discharge speed and guaranteeing consistent protection of your electronic components.
Medical Device Production Systems
Your medical device production systems need robust contamination prevention measures that include compressed air ionizers to maintain an ultra-clean manufacturing environment.
The integration of pulsed DC ionizers helps maintain consistent charge neutralization by cycling multiple times per second for optimal stability.
Manufacturers report 50% to 90% reductions in particle contamination when implementing proper ionization systems in their cleanroom facilities.
You'll find ESD-protected assembly lines are essential to prevent static-related damage to sensitive components while ensuring consistent product quality throughout the manufacturing process.
Quality control applications benefit from ionization technology by reducing particle attraction and contamination by up to 80%, leading to higher production yields and fewer product returns.
Contamination Prevention Systems
Medical device production systems require three fundamental contamination prevention strategies: cleanroom environments, extensive quality management systems, and strict regulatory compliance. You'll need to implement thorough monitoring systems and employee training programs to maintain these standards effectively.
To protect your medical devices from contamination, you'll want to focus on advanced control techniques like proper humidity management and air quality validation. You'll also need to conduct regular bioburden testing and use specialized cleanroom supplies, including sterile packaging and adhesive mats. Implementing proper work environment controls helps maintain high product quality standards while minimizing infection risks. Following a risk-based approach ensures effective identification and mitigation of potential contamination sources.
Control Method | Purpose | Key Components |
---|---|---|
Air Management | Particle Control | HEPA filters, pressure differentials |
Surface Control | Contact Prevention | Adhesive mats, cleanroom wipers |
Material Processing | Quality Assurance | Ultrasonic cleaning, vibratory deburring |
Storage Solutions | Product Protection | Double-bagging, sterile packaging |
Testing Protocols | Verification | Rapid microbial testing, bioburden analysis |
Your contamination prevention strategy should incorporate proper material handling procedures and sterilization processes. It is crucial to use cleanroom-specific equipment and supplies, including autoclavable labels and specialized stationery. Remember to regularly validate your prevention systems through quality management protocols and documentation to maintain ISO 13485 and EU GMP compliance.
ESD-Protected Assembly Lines
Production lines' vulnerability to electrostatic discharge demands thorough ESD protection protocols in medical device manufacturing.
You'll need to implement multiple control measures, as statistics show that 60% of device failures stem from ESD and electrical overstress. Your assembly line must incorporate conductive floor mats, proper grounding systems, and anti-static equipment to minimize these risks.
Your technicians should wear anti-static wrist straps or heel straps when handling PCBs, along with ESD-safe clothing and shoe coverings. Regular cleaning with low-alcohol ESD wipes is essential for maintaining surface conductivity and minimizing static buildup.
You'll want to maintain humidity levels between 40-70% in your facility to prevent static build-up. It's essential to use ESD-safe connectors and static-controlled containers throughout your production process. Implementing IEC 60601-1-2 compliant connectors ensures reliable operation of medical devices.
To protect against both catastrophic and latent failures, you'll need to establish consistent ESD control protocols across your entire supply chain.
Regular audits will help guarantee compliance with international standards like IEC, ANSI, and CENELEC.
Remember that up to one-third of PCB failures can be traced to ESD damage, so you can't afford to overlook any aspect of your ESD protection strategy.
Your investment in thorough ESD controls directly impacts product reliability and patient safety.
Quality Control Applications
When integrating compressed air ionizers into quality control systems, you'll need to maintain strict compliance with ISO 8573-1:2010 standards to verify medical device safety. You'll want to implement real-time monitoring solutions to detect contamination risks immediately and ascertain your compressed air meets specific purity requirements for medical device manufacturing.
Your quality control process should include regular testing of compressed air systems every six months, focusing on critical control points from intake to final delivery. You'll need to monitor bioburden risks carefully, as contaminated air can introduce harmful bacteria, yeast, or mold to your medical devices.
Control Aspect | Monitoring Requirement | Action Steps |
---|---|---|
Particle Content | Daily Checks | Filter Inspection |
Moisture Levels | Continuous Monitoring | Dryer Maintenance |
Oil Content | Weekly Testing | System Cleaning |
Microbial Load | Monthly Analysis | UV Treatment |
System Pressure | Real-time Tracking | Leak Detection |
You'll need to maintain detailed documentation of your air quality audits and implement a holistic safety management process. Don't forget to regularly inspect your filtration systems and maintain your compressors to prevent quality issues that could compromise your medical device production.
Cleanroom Static Control
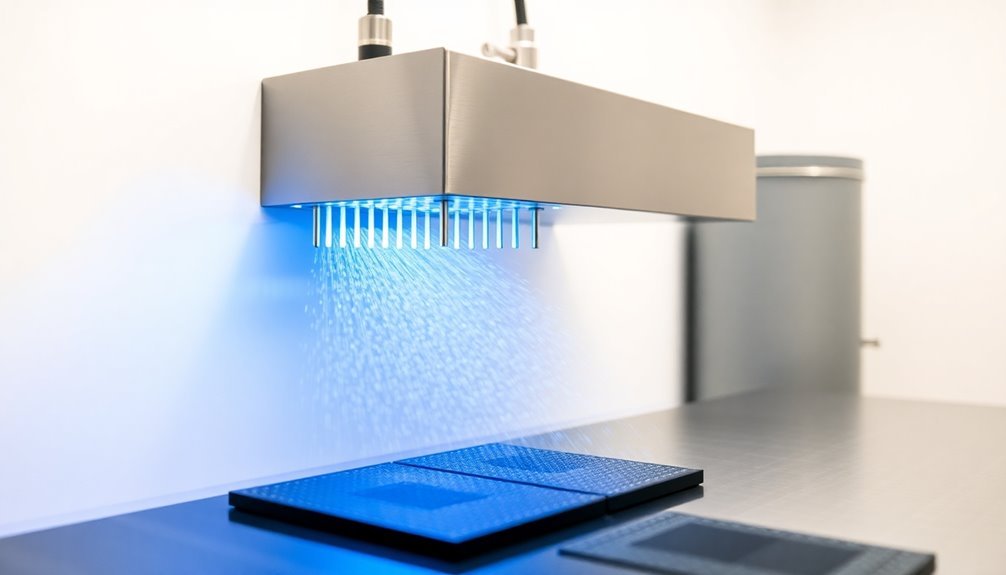
When you're managing cleanroom environments, compressed air ionizers serve as your primary defense against static-related contamination by neutralizing charges that attract unwanted particles.
You'll find that effective ionization can reduce particle attraction by up to 80%, greatly improving the cleanliness of your cleanroom operations.
Your implementation of ionization methods, particularly corona ionization systems, creates a controlled environment where static charges are kept below 500 volts, ensuring ideal protection for sensitive components and materials.
Contamination Prevention Through Ionization
Through advanced ionization technology, compressed air ionizers have revolutionized contamination control in cleanroom environments. You'll find these systems particularly effective in reducing particle contamination by 50-90% while protecting sensitive electronic components from electrostatic discharge damage.
The technology excels at neutralizing static charges on isolated objects, preventing particle re-attraction and improving production yields across various industries.
- Semiconductor wafer fabs achieve significant contamination reduction, with static charges dropping from 20,000-40,000 volts to under 500 volts
- Medical device manufacturing facilities see enhanced yields through reduced particulate contamination
- Flat panel display production benefits from both mini-environment and full room ionization systems
You'll need to implement proper maintenance protocols, including regular cleaning of emitter tips, to maintain peak performance.
Corona ionization, which uses high voltage over sharp metal points, serves as the primary mechanism for creating positive and negative ions.
For best results, you should use localized ionization rather than room-wide systems, as it offers faster performance and greater flexibility in production line modifications.
The system requires clean, dry air to function effectively, making it ideal for cleanroom environments where chemical sprays aren't suitable.
Particle Attraction Control Methods
In cleanroom environments, effective particle attraction control demands a multi-faceted approach to static management.
You'll need to implement proper grounding techniques while replacing insulating materials with conductive alternatives whenever possible. Since static charges increase with lower humidity levels, maintaining ideal humidity around 50% will greatly reduce your static-related issues.
You can detect potential problems by using electrostatic field meters and EMI-locator instruments to identify charge buildup areas. Regular static audits will help you pinpoint specific issues that require attention.
For materials that can't be grounded, you'll want to employ ionization technology, which creates conductive air to neutralize static charges effectively.
To maximize your particle control efforts, verify your cleanroom design incorporates proper air flow patterns. You should focus on both minimizing airborne particle ingress and controlling internal particle movement through turbulent flow systems.
When selecting equipment, opt for components with low electrostatic properties and low-friction features to reduce particle generation. Remember that human movements can generate static charge, so you'll need to account for this in your control strategy through proper protocols and protective measures.
Flat Panel Display Assembly
Modern flat panel display assembly relies heavily on ionized air systems throughout its complex manufacturing stages. You'll find these systems particularly critical during color filter formation, liquid crystal filling, cell assembly, and polarizer attachment processes where static control is essential.
- Contamination prevention during photolithography and color filter creation
- Protection of sensitive electronic components during TFT substrate handling
- Static elimination when attaching delicate polarizing plates
When you're working with color filter formation, you'll need precise static control as you apply and develop the red, green, and blue filters through multiple coating stages.
The liquid crystal filling process is equally demanding – you're dealing with transparent electrodes and sensitive alignment layers that can be disrupted by static charges.
During cell assembly, you'll use specialized machines to align and combine glass plates under vacuum conditions, where static interference must be minimized.
The final polarizer attachment stage requires exceptional cleanliness and static management, as you're applying critical polarizing plates that control light orientation.
You'll need to maintain strict static control throughout these processes to guarantee proper molecular alignment and prevent particle contamination that could compromise display quality.
Plastic Film Processing
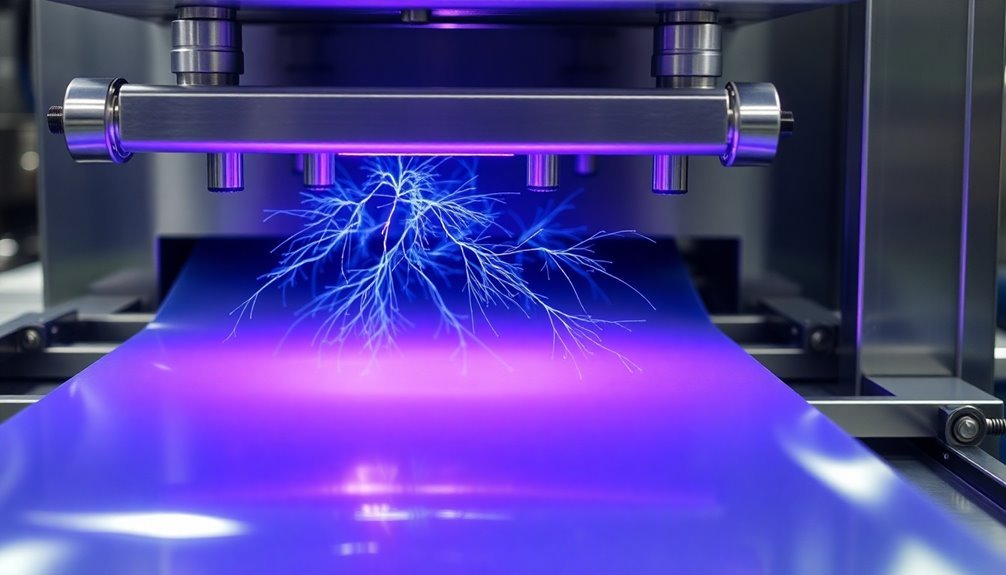
The plastic film processing industry faces similar static control challenges to display manufacturing, but with unique demands for continuous high-speed production.
You'll find that plastic films can generate static charges between 20,000 and 40,000 volts during processing, which severely impacts product quality and production efficiency.
To combat these issues, you'll need specialized ionization equipment. Ionized air blowers and anti-static bars are your primary tools for neutralizing static charges on moving film surfaces.
These systems can reduce static levels to below 500 volts, preventing dust attraction and contamination issues that could compromise your product quality.
You can integrate in-line ionizers like the Conveyostat into your pneumatic conveying systems to prevent film from clinging and clogging.
When you're setting up your system, verify your compressed air is free from oil and water contaminants.
You'll want to adjust your ionization units for the best balance of positive and negative ions based on your specific process requirements.
The benefits you'll see are significant: an 80% reduction in contamination, less frequent maintenance (from weekly to once every six weeks), and improved cleaning efficiency through prevented particle re-entrainment.
Semiconductor Wafer Handling
Since semiconductor manufacturing requires pristine environments, you'll need specialized ionization systems to protect sensitive wafers during handling and processing. These systems can reduce static charges from up to 40,000 volts down to under 500 volts, preventing costly damage and contamination issues.
You'll find ionizers integrated into various wafer handling equipment, from spin rinser driers to cassette transfer tools.
- Reduces maintenance downtime from weekly to once every six weeks
- Decreases particle contamination by 50-90% on semiconductor wafers
- Meets cleanroom standards 10 times better than Class 3 requirements
When you're handling wafers, you'll want to use specific ionizer types based on your application. In-tool ionizers like Simco-Ion's Micro Series provide ultra-clean ionization in tight spaces, while compressed gas ionizers work well for blowoff operations.
For ideal performance, you can choose between tungsten emitters for efficient ionization or single crystal silicon emitters for reduced particle generation.
Modern automated wafer handling systems often incorporate ionizers directly into robotic transfer mechanisms, ensuring consistent ESD protection throughout the entire handling process while maintaining ISO2 cleanliness levels.
Circuit Board Protection
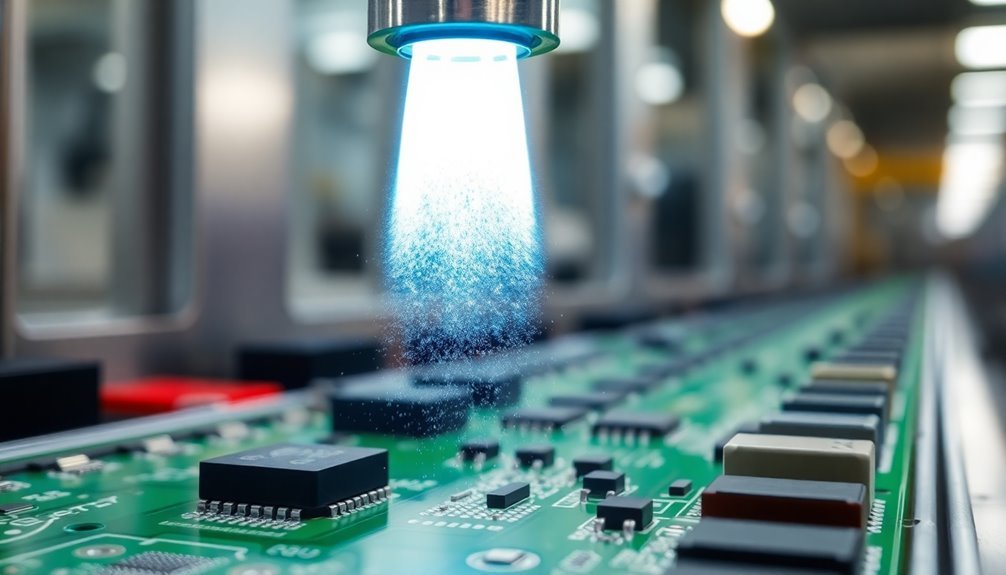
Protecting circuit boards from electrostatic discharge requires reliable compressed air ionization systems that can effectively neutralize static charges on both insulators and isolated conductors.
You'll find these systems particularly important when traditional grounding methods aren't feasible, making them an essential component of your ESD control strategy.
When you're handling sensitive electronic components, you can use various types of ionizers, including benchtop, overhead, and point-of-use systems.
Overhead ionizers provide consistent downward airflow across your workbench, while precision air ionizers target specific areas that need static neutralization.
You'll notice that these systems can neutralize charges within seconds, considerably reducing the risk of ESD damage to your circuit boards.
To maintain compliance with ANSI/ESD S20.20 and IEC TR 61340-5-2 standards, you'll need to regularly maintain and calibrate your ionization equipment.
Your ionizer system won't just protect against ESD damage; it'll also help eliminate electrostatic attraction that causes particles to cling to your products.
This dual benefit makes compressed air ionizers invaluable for maintaining product quality and preventing costly component failures in your circuit board manufacturing process.
Frequently Asked Questions
How Often Should Compressed Air Ionizers Be Calibrated for Optimal Performance?
You should calibrate your compressed air ionizers every six months, but if you're using them in critical clean rooms, calibrate more frequently. Be sure to test discharge time and offset voltage during each calibration.
What Are the Energy Consumption Costs Compared to Traditional Static Control Methods?
You'll find compressed air ionizers more energy-efficient than traditional static control methods, especially in targeted applications. They'll save you money through focused ionization, rather than having to ionize entire rooms or spaces.
Can Compressed Air Ionizers Function Effectively in High-Humidity Environments?
Yes, you'll find that compressed air ionizers work effectively in high humidity. In fact, moisture can enhance their performance, as ionizers need some humidity to create ions and neutralize static charges efficiently.
What Is the Typical Lifespan of Electrode Emitter Points in Industrial Ionizers?
You'll typically get around 20,000 operating hours from emitter points, but your environment's cleanliness and maintenance routine can greatly impact this. You'll need more frequent replacements in dirty or harsh conditions.
Are There Specific Compressed Air Quality Requirements for Ionizer Systems?
You'll need clean, dry compressed air for your ionizer system. It's crucial to use high-quality filters and maintain your air supply regularly to prevent moisture and contaminants from damaging the equipment or disrupting ionization.
In Summary
You'll find compressed air ionizers indispensable across these industrial applications, from keeping your electronic components pristine to maintaining sterile medical device production. Whether you're managing cleanrooms, assembling displays, or handling sensitive semiconductors, these systems effectively neutralize static and prevent contamination. Consider implementing ionized air solutions to protect your valuable manufacturing processes and boost product quality while reducing costly defects.
Leave a Reply