Static-safe lighting in protected workspaces requires careful attention to both illumination and ESD protection standards. You'll need to maintain 30 foot-candles (320 lux) for high visual acuity areas while ensuring your lighting fixtures don't interfere with ESD safety measures. Install adjustable fixtures that avoid direct overhead positioning, and use varistors and TVS diodes to protect LED systems from static discharge. Your lighting should incorporate proper grounding connections, and workstations should feature static-dissipative materials. Keep lighting elements at safe distances from sensitive components, and implement regular testing protocols. The intersection of proper illumination and static protection holds many critical considerations for your workspace setup.
ESD Safety Lighting Fundamentals
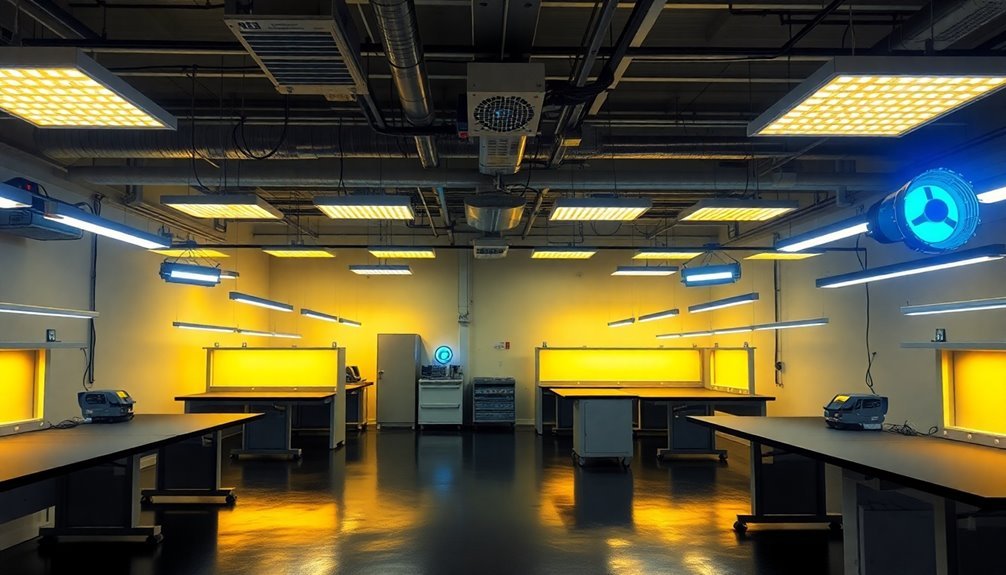
When designing your workstation layout, you must guarantee that lighting solutions don't interfere with ESD protection measures.
You'll need to carefully consider the placement of each lighting unit to maintain proper protection while providing adequate illumination. Installing proper ESD protection devices like varistors and TVS diodes helps safeguard LED systems from damaging static discharge events.
Remember that your workstation's design should actively prevent static buildup around sensitive components while keeping all lighting elements at safe distances according to established standards.
Workplace Illumination Requirements
You'll need to understand the specific light levels required for different work areas in your ESD-protected workspace, starting with the minimum requirement of 5 foot-candles in corridors and up to 750 lux in machinery areas.
Your task-specific lighting must align with both general workplace standards and ESD safety protocols, ensuring adequate illumination for detailed electronics work while preventing static discharge risks. First aid stations must maintain at least 30 foot-candles of illumination to ensure proper visibility for medical care.
Emergency lighting in your static-safe areas must maintain these protective standards while meeting OSHA's minimum illumination requirements for safe evacuation routes.
Minimum Light Level Standards
Proper illumination stands as a critical safety requirement in workplace environments, with specific minimum light levels established for different areas and tasks. You'll need to guarantee your workspace meets these standards to maintain safety and productivity.
Area Type | Required Light Level |
---|---|
Offices & First Aid | 30 foot-candles |
Plants & Machine Shops | 10 foot-candles |
Warehouses & Corridors | 5 foot-candles |
Loading Platforms | 3 foot-candles |
For office spaces and medical areas like first aid stations, you must maintain a minimum of 30 foot-candles of illumination. Manufacturing and mechanical work areas require at least 10 foot-candles, while storage areas and corridors need 5 foot-candles. You'll find that underground work areas, such as tunnels and shafts, also require 5 foot-candles minimum.
For more demanding visual tasks, you'll need to follow international standards that specify much higher illumination levels. The EN 12464 standard recommends 500-1000 lux for office environments, while detailed mechanical work may require up to 1000 lux. Tasks involving very small components or low contrast can demand anywhere from 2000 to 5000 lux, and prolonged, precise work might need up to 10000 lux. Regular office lighting should avoid surpassing 500 lux to prevent excessive contrast with computer screens.
Task-Specific Lighting Requirements
Task lighting precision determines the success of specialized workplace activities, requiring careful attention to both ambient and focused illumination.
You'll need to guarantee specific light levels based on your workspace type: offices requiring high visual acuity need at least 30 foot-candles (320 lux), while factory settings demand up to 750 lux for safe machinery operation. Loading bays and entry/exit points should maintain 300-400 lux for maximum visibility.
To implement effective task lighting, you'll want to position desk lamps and spotlights strategically over workstations, particularly in production and dismantling areas where detailed work occurs. A color temperature range of 4000-5000 Kelvin provides optimal balance for productivity.
You should align rows of diffuse lights parallel to workstation sight lines to minimize glare, and maintain ambient lighting between 200-500 lux for digital work environments.
Don't forget to manage natural light by installing vertical blinds for east-west windows and horizontal blinds for north-south exposures.
For maximum results, you'll need to balance task and ambient lighting. Position computers at right angles to outside light sources, and use light-colored, matte finishes for walls and ceilings to reduce contrast and reflection.
This approach guarantees both safety and productivity while minimizing eye strain.
Emergency Illumination Protocols
Emergency lighting plays a vital role in maintaining workplace safety during power outages and emergencies. You'll need to guarantee your static-safe workspace meets strict illumination requirements that include both primary and backup lighting systems.
Your emergency lights must activate automatically during power failures and maintain illumination for at least 90 minutes. Regular monthly activation tests are essential to verify proper system operation.
You must install hardwired emergency lighting that provides an initial average illumination of one foot-candle along egress paths at floor level. The lighting shouldn't create harsh contrasts – your maximum-to-minimum illumination ratio can't exceed 40:1. Over the 90-minute emergency period, illumination can decline to an average of 0.6 foot-candles.
Your exit signs require specific attention too. They must feature six-inch-high lettering with strokes at least three-fourths of an inch wide. For externally illuminated signs, you'll need five foot-candles of illumination and a contrast ratio of at least 0.5.
Whether you choose battery-operated systems or generator backup power, you'll need to conduct regular testing to guarantee reliable operation. Remember that all installations must comply with NFPA 101 and IBC standards for workplace safety.
Task-Specific Lighting Solutions
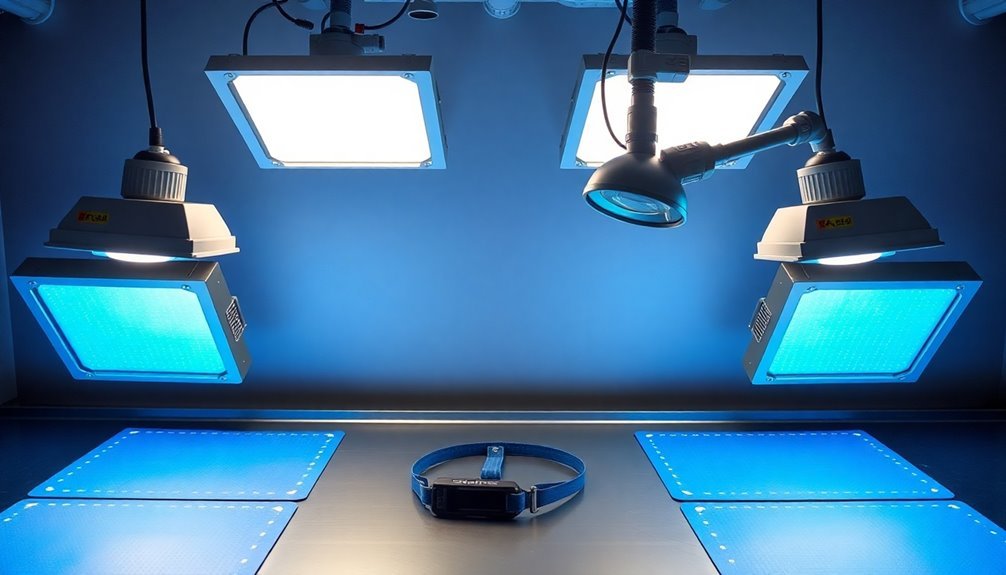
Developing effective lighting solutions for specific tasks requires careful consideration of three key factors: directional focus, adjustability, and ergonomic positioning. You'll need to make certain your workspace lighting directly illuminates specific areas while avoiding glare and unwanted shadows that can impact your safety and productivity.
When setting up task lighting, you shouldn't position light sources directly overhead or in front of your work area. Instead, opt for adjustable fixtures that you can customize throughout the day. These systems can deliver up to 90% energy savings compared to traditional lighting setups.
You'll want to incorporate smart lighting systems that can automatically adjust color temperature and brightness to match natural daylight patterns, reducing eye strain and maintaining your circadian rhythm.
To optimize your protected workspace, you should balance task lighting with ambient illumination to prevent harsh contrast zones. Consider implementing motion sensors and automated controls that'll adjust lighting based on your presence and specific task requirements.
Don't forget to integrate these solutions with proper training on lighting ergonomics – understanding how to position and adjust your lighting will help prevent accidents and maintain the static-safe environment your workspace requires.
Emergency Lighting Protocols
You'll need to guarantee your static-safe workspace has reliable emergency backup power that can sustain critical lighting for at least 90 minutes during power failures. The system must undergo regular visual inspections every 30 days to verify proper operation and readiness.
Your emergency lighting system must maintain minimum illumination levels of 1 foot-candle average and 0.1 foot-candle at any point along designated exit pathways.
You're required to install clearly marked and properly illuminated exit signs with surface values of at least 5 foot-candles to guide occupants safely during evacuations.
Emergency Backup Power Requirements
Strong backup power protocols serve as the backbone of static-safe lighting systems in protected workspaces. You'll need to guarantee your emergency lighting system meets specific duration requirements based on your facility type. Most buildings require 1.5 hours of backup power, while sleep risk areas and entertainment venues must maintain 3 hours of emergency lighting capacity. LED bulbs are commonly used due to their reliability and extended lifespan.
Building Type | Duration | Initial Illumination | Testing Frequency |
---|---|---|---|
Standard Facilities | 1.5 hours | 1 foot-candle | Monthly |
Sleep Risk Areas | 3 hours | 1 foot-candle | Monthly |
Entertainment Venues | 3 hours | 1 foot-candle | Monthly |
Residential Buildings | 3 hours | 0.5 lux min. | Monthly |
Your battery backup systems must connect to the building's power supply for charging while maintaining sufficient capacity to operate during outages. You'll need to implement regular testing protocols to verify your system's functionality. Remember to position luminaires strategically at exits, safety signs, and near firefighting equipment. Document all maintenance activities and tests to demonstrate compliance with standards like NFPA 101 and BS5266-1:2011. Regular risk assessments will help you identify areas requiring additional lighting coverage.
Critical Exit Path Illumination
Building on proper backup power systems, critical exit path illumination demands precise light levels and strategic placement to guarantee occupant safety during emergencies.
You'll need to maintain initial illumination levels of at least 1 foot-candle along egress paths at floor level, with a minimum of 0.1 foot-candle at any point. These levels can decline to 0.6 foot-candles average after 1.5 hours of emergency operation.
Your exit signs must meet strict visibility requirements, including 6-inch letter heights and minimum luminance standards of 0.06 footlamberts for self-luminous signs.
You'll need to verify external illumination provides at least 5 foot-candles at the sign's surface with a contrast ratio of no less than five-tenths. Position signs so they're visible from up to 100 feet away and clearly mark the path to exit doors.
You must test your emergency lighting monthly and annually, maintaining detailed records of all inspections. The system should activate automatically during power interruptions and provide emergency illumination for at least 1.5 hours.
Remember to keep the maximum-to-minimum illumination ratio at 40:1 or less throughout the protected workspace.
Static Control Lighting Design
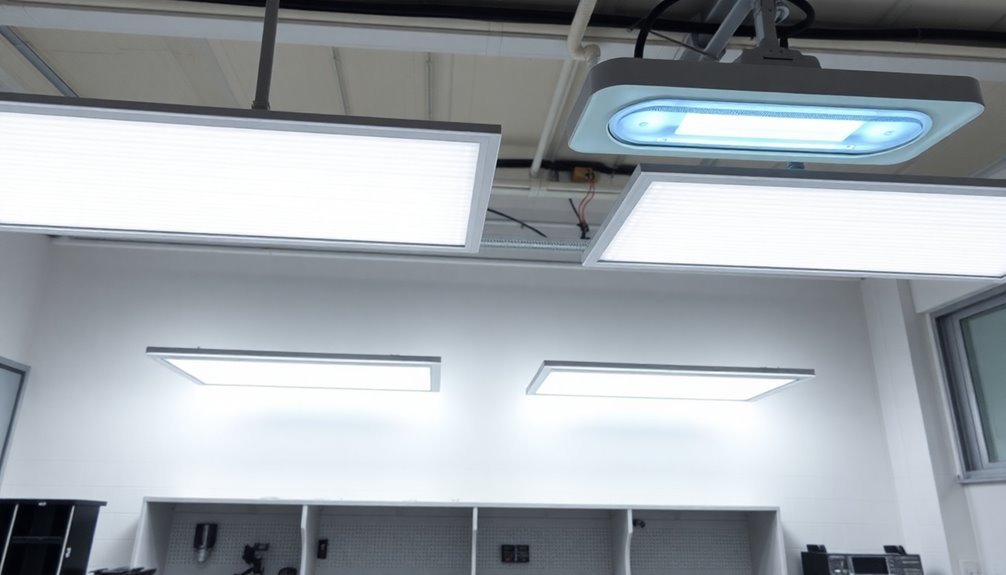
Over the past decade, implementing proper static control lighting design has become essential for protecting sensitive electronic equipment and maintaining safe workspaces. You'll need to focus on fundamental principles like guaranteeing proper grounding of all lighting equipment and using fully enclosed fixtures to prevent static discharge.
When designing your static control lighting system, you'll want to incorporate LED fixtures with built-in static protection and implement nitrogen or carbon dioxide purging where necessary. It's vital that you select materials with anti-static properties and install surge protectors to guard against overvoltage incidents.
You must follow specific installation guidelines to maintain static safety. Install shielded cables for all connections and keep them away from high-voltage lines. You'll need to secure your fixtures firmly to prevent any movement that could generate static electricity.
Don't forget to use surge-protected outlets for all your lighting equipment.
Regular maintenance is vital for system integrity. You should test your lighting systems for static resistance periodically and check grounding connections. Make sure you're documenting all maintenance activities and keeping your team trained on proper static control procedures.
This systematic approach will guarantee your lighting system maintains its static-safe properties.
Lighting Survey Methods
Systematically conducting a lighting survey helps guarantee your static-safe workspace meets essential illumination requirements. You'll need to measure illuminance levels using a light meter and assess multiple angles to get accurate readings of your workspace lighting conditions.
Start by checking if your lamps have proper diffusers and confirm workstations aren't positioned directly under overhead lighting. You should verify that all light fixtures provide steady illumination without flickering, as this can affect both comfort and safety in static-protected areas.
Survey Component | What to Check | Action Required |
---|---|---|
Light Levels | Illuminance readings | Measure in lux/ft-c |
Glare Sources | Reflective surfaces | Install anti-glare shields |
Distribution | Wall/ceiling coverage | Add fixtures if needed |
Safety | Fixture condition | Replace/repair damaged units |
Workspace Setup | Station positioning | Adjust to avoid direct light |
If you find insufficient lighting, you'll need to take corrective actions like installing additional fixtures or rearranging workstations. Don't forget to regularly clean light fixtures and replace bulbs to maintain ideal lighting conditions. Remember to document all measurements and observations for compliance with OSHA standards.
Workspace Lighting Best Practices
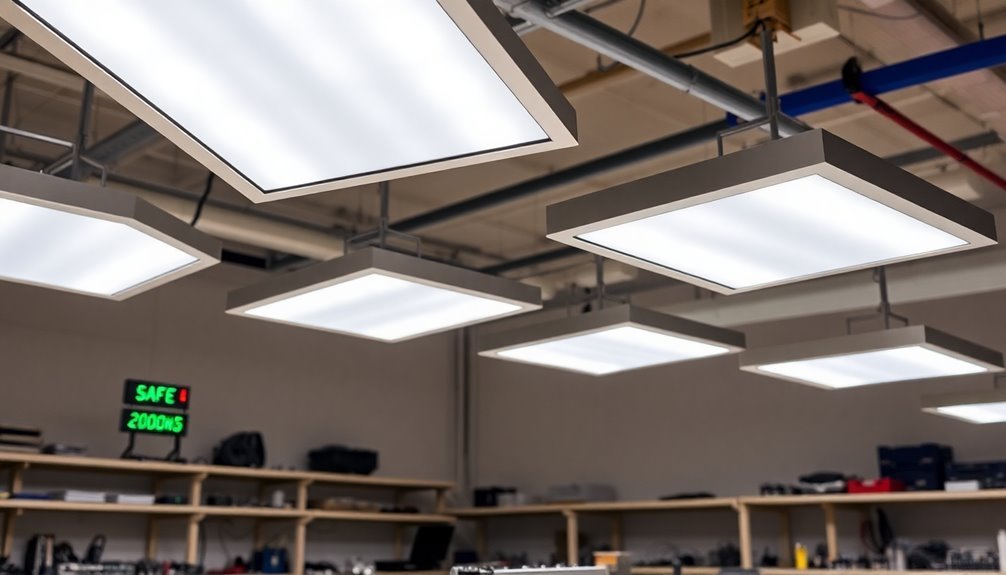
Implementing proper lighting practices in static-safe workspaces requires a thorough approach that balances visibility, safety, and ESD protection. You'll need to focus on both lighting design and static control measures to create an effective workspace environment.
Start by positioning workstations at right angles to windows and install appropriate blinds – vertical for east/west windows and horizontal for north/south windows.
You'll want to incorporate layered lighting, combining indirect ambient light with adjustable task lighting. Use LED fixtures with color temperatures between 3500K and 5000K to enhance alertness and productivity.
Ensure all lighting units are EPA-compatible and comply with ESD standard IEC 61340-5-1.
You should equip your workspace with proper static control equipment, including antistatic mats, wrist straps, and ionizers. Maintain dissipative surfaces and humidity control to minimize static risks.
Don't forget to follow OSHA standards for lighting levels and fixture requirements. Install protective plates and shatterproof shields where necessary.
Conduct regular inspections using light meters to verify compliance, and implement smart lighting controls with sensors to optimize energy usage while maintaining static-safe conditions.
Frequently Asked Questions
How Often Should LED Static-Safe Lighting Fixtures Be Tested for ESD Compliance?
You should test LED static-safe lighting fixtures quarterly through visual inspections and ESD simulator testing. Include additional tests after any modifications, repairs, or environmental changes that could affect ESD protection performance.
Can Uv-Filtered Lighting Affect the Performance of Esd-Protective Materials?
Yes, UV-filtered lighting can affect your ESD materials' performance. You'll find it typically helps preserve their static-dissipative properties by reducing harmful UV exposure that could otherwise degrade their protective capabilities over time.
What Temperature Ranges Are Safe for Static-Control Lighting in Cleanroom Environments?
You'll want to maintain your cleanroom lighting temperature between 68°F and 72°F (20°C to 22°C) for the best static control. This range, combined with proper humidity levels, helps guarantee effective static protection.
Do Wireless Lighting Controls Pose Static Risks in Esd-Protected Areas?
You don't need to worry about wireless lighting controls causing static risks. They're not direct sources of ESD. Instead, focus on controlling human movement, proper grounding, and workplace setup in your ESD-protected areas.
How Do Humidity Levels Impact the Effectiveness of Static-Safe Lighting Systems?
You'll find your static-safe lighting systems work best at 40-60% humidity levels. When humidity drops below 40%, your lights face increased static risks, while levels above 60% help prevent charge buildup.
In Summary
You'll need to regularly review and update your workspace lighting setup to maintain ESD safety standards while meeting illumination requirements. Don't forget to conduct quarterly lighting surveys and adjust task-specific solutions as needed. By following proper static control protocols and keeping emergency lighting systems well-maintained, you're ensuring both safety and productivity in your protected workspaces.
Leave a Reply