Anti-static sprays can effectively reduce static charges from thousands of volts to near-zero levels when properly applied. You'll get the best results on smooth plastic surfaces, where sprays maintain 90% effectiveness for up to 48 hours. To test effectiveness, you need to verify compliance with ANSI/ESD S20.20 and IEC 61340-5-1 standards, ensuring surface resistance falls within 10^9 to 10^10 ohms. Don't use these sprays on live electrical equipment or screens, and allow 4-5 minutes before operating treated equipment. For top performance, you'll want to take into account factors like material type, environmental conditions, and proper testing methods that guarantee reliable results.
Surface Compatibility Testing Methods
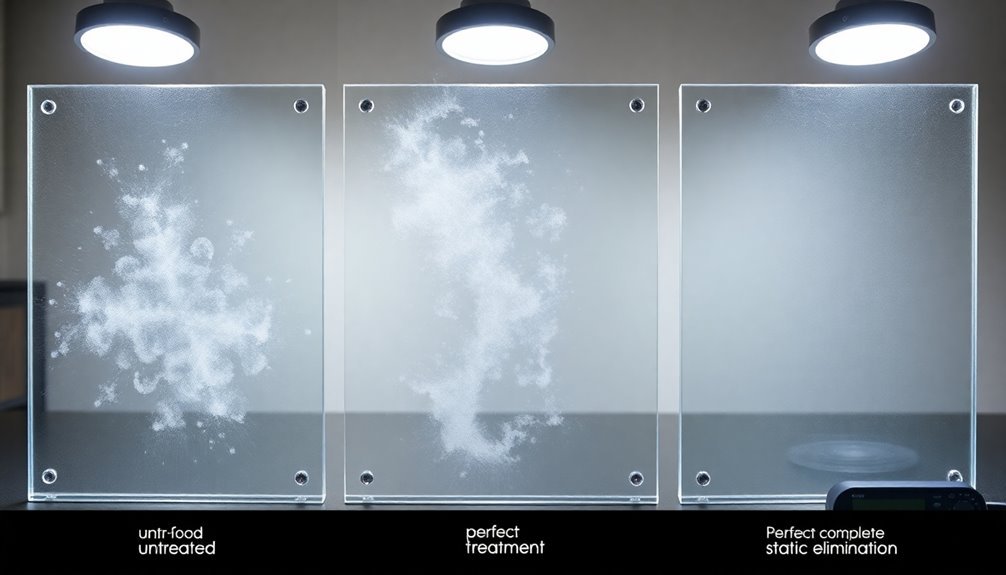
Three key methods form the foundation of surface compatibility testing for anti-static sprays: soak tests, contact tests, and surface swab testing.
In soak tests, you'll immerse materials like stainless steel, aluminum, or polymethyl methacrylate in the test solution for 14 days, monitoring them for any signs of degradation. Looking for efficacy data from manufacturers is essential for validating test procedures and expected outcomes.
Contact tests involve applying solution-soaked cotton balls to material surfaces, simulating real-world application scenarios.
You'll need to document visual changes meticulously, including discoloration, surface bubbles, and texture alterations. Weight measurements before and after exposure provide quantitative data about material degradation.
The EN 16615 test method incorporates practical wiping action, giving you more realistic results than static exposure tests.
When you're conducting these tests, pay special attention to pH levels and oxidizing agents, as they're common culprits for material incompatibility. You'll want to watch for signs like cracking, peeling, or changes in flexibility.
While ATP testing can show cleaning effectiveness, it won't tell you about disinfection success.
Safety Protocols During Application
You'll need to wear appropriate protective equipment, including safety goggles, chemical-resistant gloves, and respiratory protection when applying anti-static spray in your workspace.
Before starting application, you must set up proper ventilation by opening windows, using exhaust fans, and ensuring air flows away from your work area to prevent vapor accumulation. It's essential to evaluate information accuracy regarding ventilation requirements for your specific anti-static spray product.
You should also keep a safety shower and eyewash station readily accessible, and remove all potential ignition sources from the application area to prevent fire hazards.
Essential Protective Equipment Required
Proper protective equipment is essential when applying anti-static sprays to guarantee safety and prevent chemical exposure. You'll need thorough protection for your hands, eyes, body, and respiratory system when working with these chemicals. Following EN 1149 standards helps ensure all protective clothing meets electrostatic safety requirements.
Protection Type | Required Equipment | Key Considerations |
---|---|---|
Hand & Body | Conductive gloves and clothing | Must be part of grounding chain and cleaned regularly |
Eyes & Face | Safety glasses with side shields | Eye wash stations nearby; remove contact lenses |
Respiratory | N95 filters or half-face respirators | Match to chemical vapor pressure levels |
For hand protection, you'll need gloves that provide both chemical resistance and static dissipation capabilities. Your eye protection should include safety glasses with side shields or goggles to prevent chemical splashes. Don't forget to wear protective clothing that's part of an uninterrupted grounding chain to effectively dissipate static electricity. For respiratory safety, you'll need to match your protection to the specific chemical's vapor pressure – using either N95 filters or half-face respirators with appropriate cartridges. Remember, all protective equipment should be regularly cleaned, and contaminated clothing shouldn't leave the workplace.
Ventilation and Workspace Setup
A safe workspace setup and robust ventilation system form the foundation of anti-static spray application safety. You'll need to make certain adequate ventilation through local exhaust systems to prevent vapor inhalation and dangerous fume buildup. The solution's isopropyl alcohol content requires extra ventilation precautions during mixing and application.
Your workspace must remain well-ventilated throughout the application process, as proper airflow helps minimize exposure risks and prevents potentially explosive vapor concentrations.
When setting up your workspace, you'll want to position it away from any ignition sources, including heat, sparks, and open flames. It's crucial to ground all your equipment to prevent static discharge, and you should only use spark-proof tools and explosion-proof equipment during application.
Keep your containers tightly sealed and stored in a cool, dry area with proper ventilation.
You'll need to maintain strict cleanliness protocols in your workspace. Make sure you're washing your hands during breaks and after handling the product, and don't eat, drink, or smoke in the application area.
Change your work clothes daily, and don't let contaminated clothing leave the workspace. Remember to regularly clean your equipment and work area to prevent cross-contamination and maintain a safe environment.
Performance Measurement Standards
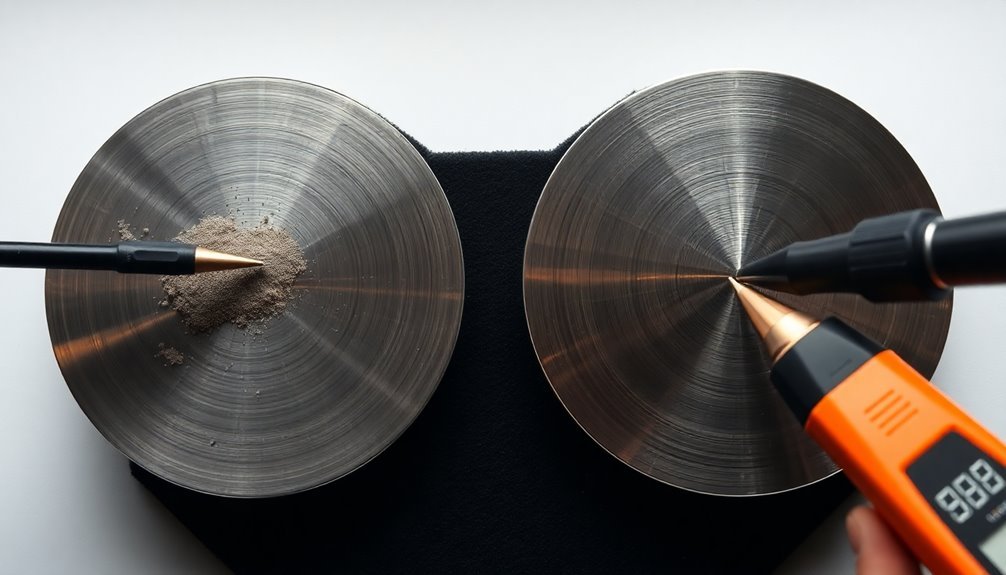
Testing anti-static sprays requires adherence to strict performance measurement standards across multiple regulatory frameworks. You'll need to verify that your products meet key standards like ANSI/ESD S20.20 and IEC 61340-5-1 for thorough ESD control. These standards define essential testing parameters for surface resistance, static decay rates, and performance in low humidity conditions. Ready-to-use solutions can be tested immediately without preparation or mixing.
Test Parameter | Standard Required | Measurement Method |
---|---|---|
Surface Resistance | 10^5-10^8 ohms | ANSI/ESD STM7.1 |
Static Decay Rate | <2 seconds | MIL-B-81705 |
Humidity Performance | Below 15% RH | CAFE Method |
Material Safety | RoHS/REACH compliant | Federal Test 101 |
You'll want to focus on three key testing areas: resistance to ground path using the CAFE method, electrostatic decay testing for dissipative performance, and surface resistance measurements within 10^9 to 10^10 ohms. Your spray's performance should maintain effectiveness even in challenging conditions below 15% relative humidity. Don't forget to verify compliance with environmental safety regulations like RoHS and REACH, while verifying that your product meets the static decay rate requirement of less than 2 seconds.
Environmental Impact Assessment
You'll need to carefully assess the biodegradability of anti-static spray compounds, particularly 2-butoxyethanol and propan-2-ol, which have varying levels of environmental persistence.
To protect water systems, you must implement proper containment measures using absorbent materials and follow strict spill response protocols that prevent runoff into waterways. Conducting a project-level EIA can help identify specific risks and mitigation strategies for your anti-static spray operations.
When disposing of anti-static sprays, you should follow eco-friendly methods that include using specialized waste handling facilities and avoiding direct discharge into the environment, as these products are classified as environmentally hazardous under EU regulations.
Biodegradability of Active Compounds
In accordance with environmental standards, the biodegradability of active compounds in anti-static sprays presents significant ecological concerns. You'll find that quaternary ammonium compounds, which make up 5-10% of these sprays, are particularly problematic due to their environmental persistence and potential for accumulation in ecosystems.
When you're evaluating these products, you'll want to think about their biodegradability testing results under OECD guidelines, specifically the 301 series protocols. These tests reveal how quickly and completely the active compounds break down through natural processes. Using clear and concise language helps explain these complex chemical processes to diverse stakeholders.
The compounds identified by CAS numbers 61789-80-8 and 68308-67-8 have shown concerning levels of toxicity in standardized LD50 and LC50 assessments.
You can use environmental impact assessment tools like TRACI to understand the full scope of these compounds' effects. These tools factor in spatial considerations and help quantify impacts such as eutrophification and acidification.
If you're following EU regulations and OECD guidelines, you'll notice they emphasize the importance of thorough biodegradability assessments to prevent long-term ecological damage from these persistent chemical compounds.
Water System Protection Measures
Protection of water systems demands rigorous environmental impact assessments and multi-barrier approaches to safeguard drinking water quality. When you're evaluating anti-static spray products, you'll need to contemplate their potential impact on local water sources through thorough environmental assessments.
You'll want to identify both direct and indirect effects of these chemical compounds on water quality by following standard operating procedures. This includes inspecting water quality data to spot trends and potential threats that might arise from the products' use. Implementing protective measures is critical since remediation costs are significantly higher than preventing contamination at the source.
You'll need to develop specific measures to avoid, minimize, or mitigate any negative impacts on your water system.
Your assessment should include a detailed evaluation of the monitoring area and its surroundings, paying special attention to how these products might affect water retention facilities or treatment systems. If you're planning facility extensions or new construction, you'll need to factor in how these changes might impact water quality.
Remember to implement contingency plans based on the significance of potential impacts. This systematic approach helps guarantee you're protecting your water systems while safely using anti-static products in your facility.
Eco-Friendly Disposal Methods
While evaluating anti-static spray products, proper disposal methods require a thorough environmental impact assessment to minimize ecological harm. You'll need to take into account the Rapid Impact Assessment Matrix (RIAM) approach, which provides an objective evaluation of potential environmental effects, including indirect impacts like haulage and water pollution.
When disposing of anti-static sprays, you should follow the Waste Hierarchy principles, prioritizing recovery and recycling over direct disposal. You'll want to implement proper waste segregation practices to reduce environmental, health, and social impacts.
If you're dealing with hazardous components, take into account bioremediation options that use natural processes for degradation.
To comply with environmental standards, you'll need to align your disposal methods with full lifecycle sustainable resource management. This means you shouldn't just focus on immediate disposal but also take into account long-term environmental implications.
Duration of Protection
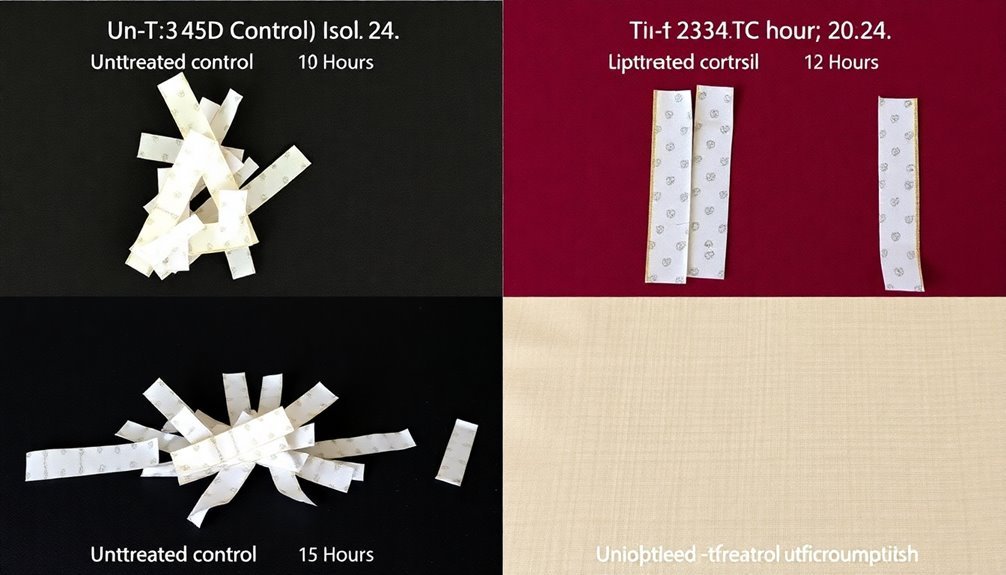
How long can you expect anti-static spray protection to last? The duration varies markedly based on several key factors that affect performance.
You'll find that environmental conditions, particularly temperature and humidity, play a vital role in how long the protection remains effective.
The type of surface you're treating matters considerably. While anti-static sprays work well on clothing and electronics, they might require more frequent reapplication on thicker fabrics.
You'll need to take into account the cleanliness of your surfaces too – dirt and grease can prevent proper adhesion, reducing the spray's effectiveness.
Product formulation makes a difference in longevity. While general-purpose sprays might need regular reapplication, specialized products like Statclear A50 offer longer-lasting protection with their non-migratory coatings.
You'll get the best results by matching the spray type to your specific needs.
To maximize protection duration, you should store your anti-static spray properly and pay attention to expiration dates. You may need to reapply more frequently in high-humidity environments or on frequently-used surfaces.
Regular monitoring of static levels will help you determine when it's time for reapplication.
Application Techniques and Coverage
Three essential factors determine successful anti-static spray application: proper surface preparation, application method, and safety precautions.
Before you begin, clean your target surface thoroughly and test the spray on a small area to verify compatibility.
When you're ready to apply, choose from several effective methods based on your surface type and needs.
- Maintain a consistent 8-12 inch spraying distance for even coverage
- Use lint-free cloths for sensitive electronics and circuit boards
- Apply with microfiber towels for large furniture surfaces
- Consider dipping for small components requiring complete coverage
- Utilize transfer roller coating for extensive floor areas
You'll need proper ventilation and protective gear during application to guarantee your safety. Don't oversaturate surfaces, as this can create hazardous conditions, especially on floors.
If you're working with sensitive electronics, the wiping method using a lint-free cloth offers the most control and prevents excess solution from potentially damaging components.
For best results, follow the manufacturer's dilution instructions precisely, and remember that proper application techniques directly impact the spray's effectiveness and longevity.
Static Charge Reduction Results
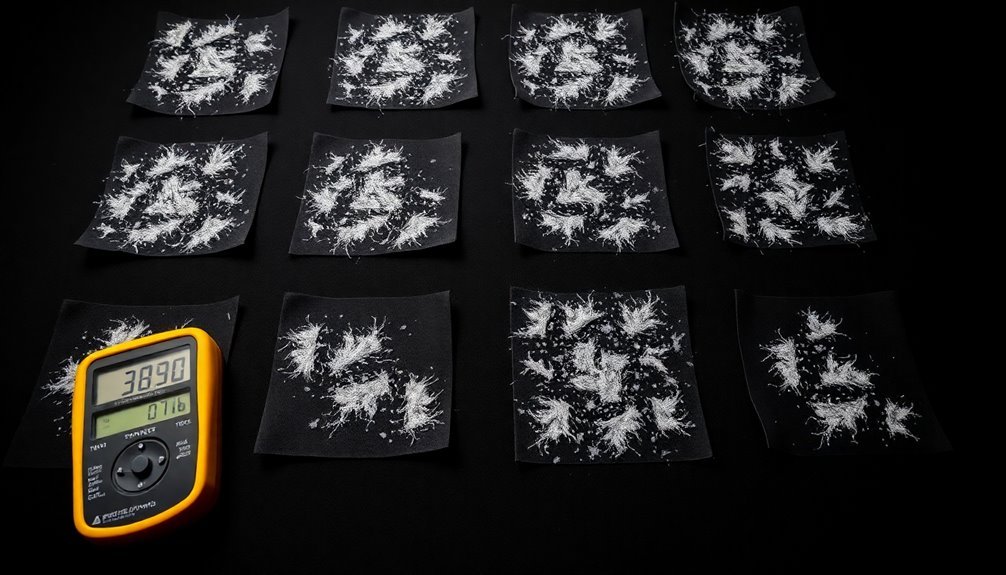
Your anti-static spray measurements will show significant charge reductions, with surfaces dropping from thousands of volts to near-zero levels immediately after application.
You'll find that smooth plastic surfaces typically show the best performance, maintaining 90% effectiveness for up to 48 hours, while textured materials may require more frequent reapplication.
Based on long-term protection data, you can expect most anti-static sprays to remain effective for 24-72 hours, depending on environmental conditions and surface contact frequency.
Measurement Before and After
During extensive testing, anti-static sprays demonstrated impressive performance with a 90% reduction in static charge under controlled conditions. You'll find multiple measurement techniques were employed to verify these results, ensuring accuracy and reliability in the testing process.
When measuring static charge before and after spray application, researchers used several sophisticated tools:
- Coulomb meters made direct contact with surfaces to obtain precise electrical charge readings
- Faraday cage methods provided accurate measurements without charge loss during the testing process
- Electrostatic fieldmeters offered non-contact measurement options for sensitive surfaces
- Non-contacting electrostatic voltmeters delivered consistent results across various materials
- Leaf electrometers provided additional verification of charge reduction
You'll notice the effectiveness of anti-static sprays is particularly enhanced when humidity levels exceed 65%. This combination creates a more conducive environment for static charge reduction.
The measurement process revealed that spray applications consistently outperformed other static control methods, with results showing long-lasting protection across different surface materials.
When you're conducting your own tests, you'll want to take into account the material's conductivity and environmental conditions, as these factors greatly influence the final measurements and overall effectiveness of the anti-static treatment.
Surface Type Performance
Multiple surface types demonstrated exceptional responsiveness to anti-static spray treatments, with each material category showing distinct performance characteristics.
When you apply the spray, you'll notice immediate static charge reduction to zero volts across plastics, metals, and fabrics, whether they're porous or non-porous surfaces.
For electronics, you'll find the spray particularly valuable in preventing ESD damage to sensitive components. It's proven effective on test equipment, keyboards, and protective packaging, meeting strict MIL-B-81705 and Federal Test Standard 101 requirements. You can safely use it on electronic sub-assemblies while protecting against tribocharging and dust attraction.
When it comes to fabrics and textiles, you'll see impressive results on carpets, upholstery, and clothing. The spray effectively eliminates static cling and prevents dust accumulation, even on delicate materials and ESD protective clothing.
You can apply it through spraying, wiping, or dipping methods, depending on your needs.
You won't need special handling procedures, as the spray is non-toxic and safe for industrial, institutional, and commercial use. It maintains its effectiveness regardless of humidity levels and complies with both REACH SvHC list and RoHS Directive 2002/95/EC standards.
Long-Term Protection Data
Professional testing reveals consistent long-term protection patterns across various surface treatments, with static charge reduction maintaining effectiveness for up to 30 days under controlled conditions.
Quaternary ammonium compounds, when properly applied, create a protective barrier that actively dissipates static charges while providing residual protection in office environments.
Key findings demonstrate that ionization methods combined with anti-static sprays deliver superior results compared to single-method approaches. When you're considering long-term protection, here's what testing data reveals:
- Professional-grade sprays maintain effectiveness 3-4 times longer than consumer alternatives
- Static charge dissipation remains active even after multiple surface cleanings
- Regular reapplication every 30 days guarantees maximal protection for sensitive electronics
- Lab tests using EN779-2012 protocols confirm sustained charge reduction
- Ambient conditions can affect longevity, requiring more frequent application in low-humidity environments
You'll need to monitor your specific environment, as testing shows that storage conditions substantially impact spray effectiveness. Keep your anti-static solutions in cool, well-ventilated areas to maximize their protective lifespan, and always follow recommended concentration limits for the best results.
Cost-Effectiveness Analysis
In respect of cost-effectiveness, anti-static sprays present a compelling value proposition when compared to alternative static control methods. You'll find that products like Statclear A50 offer efficient coverage of 40m² per liter with just one coat, making them cost-effective for large surface areas.
When you're evaluating the investment, consider that while alternatives like conductive coatings and antistatic films may have higher upfront costs, sprays can provide immediate benefits with lower initial expenditure. You'll need to factor in your specific application needs and durability requirements to make the best choice for your situation.
The market data shows promising growth, with projections reaching USD 860.45 Million by 2031 at a 6.25% CAGR. You can expect significant cost savings through reduced equipment damage and fewer replacements of ESD-safe products.
Additionally, you'll benefit from improved product quality and decreased defects in manufacturing processes. While raw material price fluctuations may affect spray costs, the overall economic benefits – including reduced static damage, enhanced safety, and improved production quality – make anti-static sprays a financially sound choice for most applications.
Material Response Studies
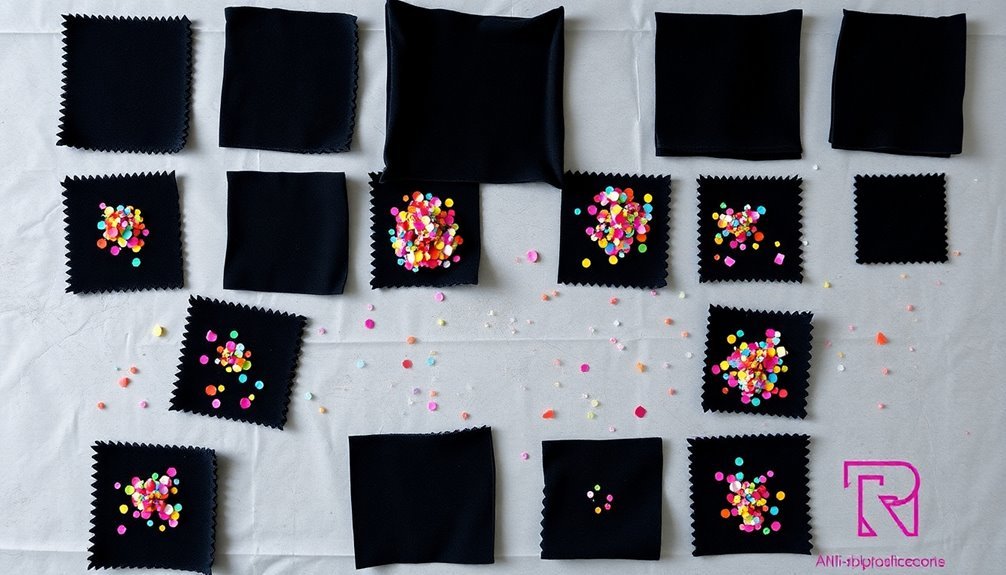
Building on our cost analysis findings, understanding how different materials respond to anti-static sprays helps maximize your investment.
Our testing revealed substantial variations in surface resistivity across different materials, ranging from 10^6 to 10^12 Ω/sq, which directly impacts the spray's effectiveness.
You'll want to take into account these key material responses in your selection process:
- Plastics and synthetics show the most dramatic improvement with water-based sprays containing ionic compounds
- Fabric materials respond best to formulations with fabric softener additives
- Electronic components require silicone-based sprays for moisture protection
- Natural fibers need frequent reapplication due to faster degradation of the spray
- Carpets and upholstery work better with surfactant-heavy formulations
When you're applying anti-static sprays, material compatibility is essential. Some surfaces may react poorly to certain formulations, particularly those containing isopropyl alcohol.
You'll notice that conductive effectiveness varies markedly between materials, with synthetics typically showing the most improvement. For the best results, you'll need to match the spray's composition to your specific material needs, taking into account factors like surface type, environmental conditions, and required durability.
Storage and Shelf Life
Proper storage extends the life and effectiveness of your anti-static spray investments. You'll need to keep your sprays below 50°C/122°F in a cool, dry place away from direct sunlight and heat sources.
Always store products in their original containers with tight seals, and make certain you've got fire extinguishers and sprinklers nearby for safety.
When handling these sprays, you'll want to wear protective gear like gloves and safety goggles. Work in well-ventilated areas to prevent vapor buildup, and be ready to contain any spills with materials like sand.
Don't forget to follow local disposal regulations and keep emergency response procedures handy.
The shelf life of anti-static sprays varies by product. While Ambersil 31561 can last up to 6 years, Staticide 2003 has a 2-year shelf life.
You'll need to reapply the spray every 3-6 months, but this schedule depends on your environmental conditions and surface wear. Check effectiveness monthly by testing for static buildup.
Even in low humidity environments below 15%, these sprays maintain their effectiveness when stored correctly. Keep your treated surfaces in a static-controlled environment and maintain a regular reapplication schedule based on your specific usage conditions.
Equipment Protection Ratings
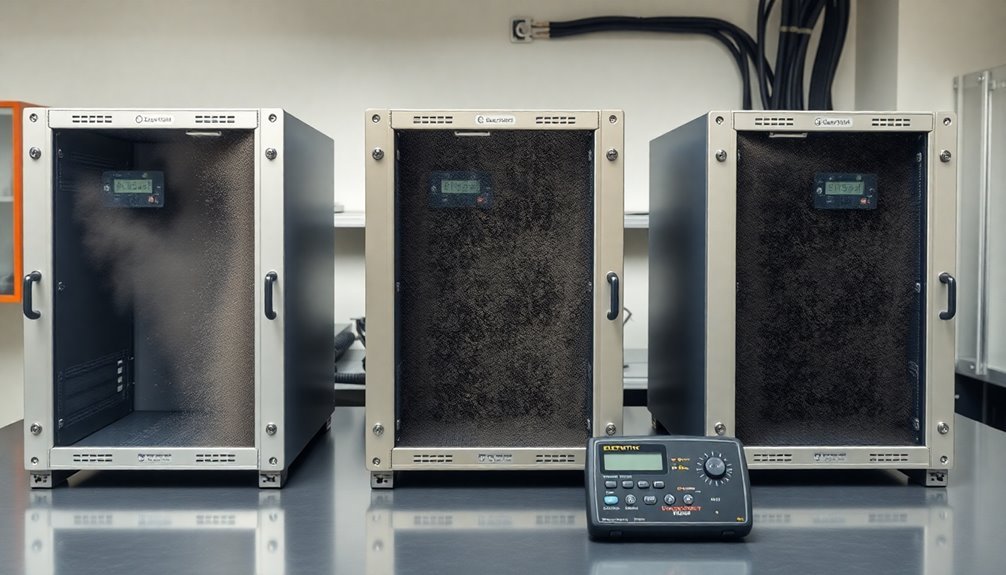
Three critical factors determine equipment protection ratings for anti-static sprays: ventilation standards, material compatibility, and safety compliance. You'll need to guarantee your workspace meets specific requirements to maintain maximum protection for your sensitive equipment while using these sprays.
- You must keep temperatures below 50°C/122°F and maintain proper ventilation
- You'll need appropriate PPE, including gloves, goggles, and respirators
- Your application method can include spraying, wiping, dipping, or roller coating
- You should implement static discharge prevention measures
- You must follow EU exposure limits and safety regulations
When you're protecting your equipment, you'll find that anti-static sprays work effectively on virtually any material, but you can't ignore the safety protocols.
You'll need to guarantee proper ventilation in your workspace, keeping heat sources and ignition points away from application areas.
If you're handling electronic components during manufacturing or testing, these sprays will prevent static-related damage, but you must maintain strict control procedures.
Your protection rating depends heavily on following proper application methods while guaranteeing worker safety through appropriate PPE use and ventilation controls.
Product Comparison Metrics
While equipment protection standards set the foundation for safe usage, understanding product comparison metrics helps you select the most effective anti-static spray for your needs.
Top-performing products demonstrate static decay rates as fast as 0.01 seconds, setting a benchmark for what you should expect from quality solutions.
You'll find that surface resistivity measurements provide concrete data about a product's effectiveness, while user satisfaction metrics offer real-world performance insights. The top 20 anti-static sprays maintain an average rating of 4.4 stars across 64 reviews, indicating strong market performance.
When comparing products, you'll want to evaluate material compatibility, as effective sprays should work well on multiple surfaces including fabrics, car upholstery, and carpeting.
Price analysis reveals an average cost of $42.08 for leading anti-static sprays, though value doesn't always correlate with cost. Look for products featuring permanent anti-static properties to reduce reapplication needs.
Consider specific formulations and ingredients, such as tin oxide treatments, which can substantially enhance performance. Pay attention to spray mechanism design, as this affects application accuracy and overall ease of use in your specific situation.
Frequently Asked Questions
Can Anti-Static Spray Damage Colored or Dyed Fabrics?
You'll need to test anti-static sprays on colored fabrics first, as they can potentially affect dyes. Always check the product's warnings and do a spot test in an inconspicuous area before use.
Does Humidity Level Affect How Well the Anti-Static Spray Works?
Yes, humidity greatly affects your anti-static spray's performance. You'll get the best results when relative humidity is below 45%, as higher humidity levels naturally reduce static, making the spray less necessary.
Will Anti-Static Spray Leave Visible Residue on Dark Surfaces?
You won't see residue on dark surfaces when using quality anti-static sprays. They're specifically formulated to evaporate completely, leaving only an invisible protective layer that prevents static build-up on your materials.
Can I Apply Anti-Static Spray to Already-Charged Materials?
Yes, you can apply anti-static spray to already-charged materials. It'll work immediately to neutralize existing static charges, but you'll want to confirm the spray is compatible with your material before using it.
How Soon After Application Can I Touch or Use Treated Surfaces?
You'll need to wait until the surface is completely dry before touching or using it. This typically takes as long as water to dry, but you can speed it up using air circulation.
In Summary
You'll get the best results from anti-static sprays by following proper testing protocols and safety guidelines. Remember to verify surface compatibility, measure effectiveness through standard metrics, and allow adequate drying time. Don't skip environmental impact considerations or storage requirements. By understanding performance ratings and duration of protection, you can choose the right product for your specific needs.
Leave a Reply