Cleanroom antistatic garments are specialized protective clothing you'll need when working with sensitive electronic equipment or in controlled environments. They're made from ESD (electrostatic discharge) fabrics, typically high-density polyester with carbon fibers, designed to prevent static electricity buildup that could damage components or create safety hazards. You'll find these garments incorporate features like conductive strips and grid patterns to safely dissipate static charges while meeting strict industry standards like ANSI/ESD S20.20. Proper maintenance guarantees their effectiveness for up to 100 washes, making them an essential investment in your cleanroom safety protocol. Understanding their complete role in static control can greatly impact your facility's success.
Purpose of Antistatic Cleanroom Garments

Anti-static cleanroom garments step up to protect sensitive electronic equipment and components from potentially damaging static electricity. These specialized garments prevent the buildup of static charges on your clothing, which could otherwise discharge and harm delicate electronics.
You'll find them essential when you're working with high-voltage equipment or handling flammable chemicals, as they considerably reduce the risk of electrostatic discharge (ESD) incidents. The required garments are made from ESD fabric to ensure proper static control. Static-generating clothing can attract and hold harmful microorganisms, making proper protective garments crucial.
When you're working in environments with sensitive equipment, even a small static discharge from your clothing can cause substantial damage. That's why you'll need to wear these protective garments that effectively dissipate static electricity before it can accumulate to dangerous levels.
The garments work by incorporating conductive or dissipative materials that safely channel static charges away from your body and clothing.
You'll often encounter these garments as part of mandatory safety protocols, especially in industries where static-related accidents could lead to serious consequences.
Materials and Design Features
High-density polyester fabrics form the backbone of cleanroom anti-static garments, typically incorporating 1-2% carbon fibers or conductive strips. Regular cleanroom laundering protocols must be followed to maintain garment integrity and performance.
You'll find widely-used materials like Burlington C3 and Maxima ESD, which feature ESD gridded stripes designed specifically for semiconductor and pharmaceutical applications. These materials must meet strict service resistivity requirements to effectively control charge accumulation and dissipation. For specialized environments requiring additional protection, materials like Tyvek offer microporous barriers against particles down to 0.5 microns, while Nomex serves in high-heat or explosive settings.
The design features of these garments focus on both protection and static dissipation.
You'll notice the incorporation of ESD grid fabrics like TX4000 and Integrity 2000, which provide thorough particle protection while maintaining static control. These materials use specialized weave patterns, such as the taffeta weave, offering chemical and abrasion resistance suitable for various cleanroom classes.
To guarantee effectiveness, these garments undergo rigorous testing for air permeability, moisture vapor transmission, and static dissipation properties.
You'll see specific designs like the TX40CR Series coveralls and TX40FR Series frocks implementing these materials with practical features such as raglan sleeves and ESD knit cuffs, maximizing both comfort and protection.
Meeting Industry Standards
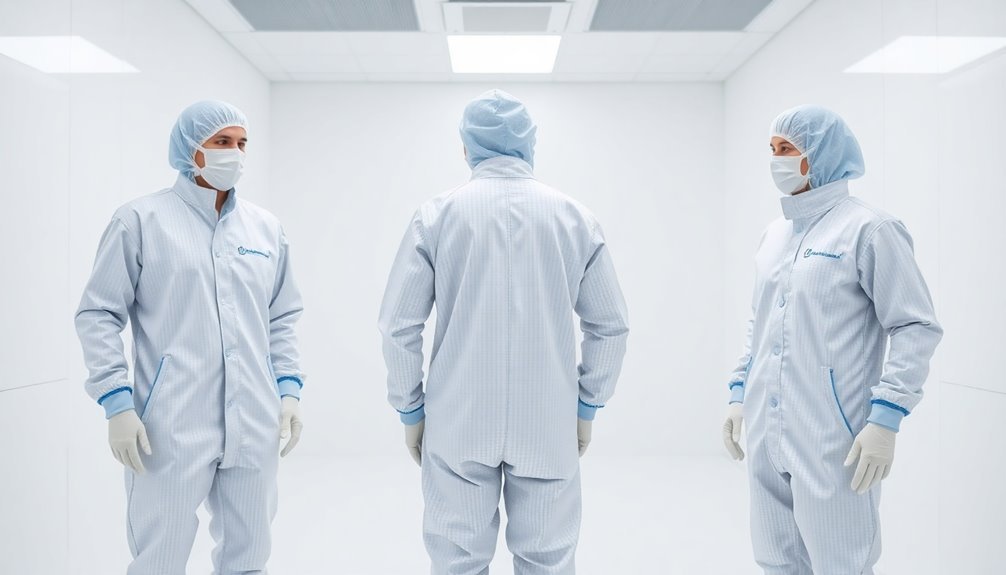
Building upon these material specifications, cleanroom garments must meet rigorous industry standards and certifications to guarantee proper ESD protection.
You'll need to verify your garments comply with ANSI/ESD S20.20 standards for groundable static control systems and incorporate proper conductive elements like threads and ground snaps for electrical continuity.
Your cleanroom garments must meet specific ISO classifications and ASTM E1549/E1549M-13(2016) requirements for ESD-controlled clothing. The garments should be made from low linting fabrics to effectively contain personnel-generated contaminants.
Different industries have their own stringent guidelines – aerospace, electronics, pharmaceutical, semiconductor, and medical device manufacturers each maintain unique specifications you'll need to follow.
Superior conductivity for 100 washes is essential for maintaining long-term ESD protection in cleanroom garments.
You'll also need to comply with broader regulatory frameworks.
OSHA requirements for workplace safety, NFPA 70E standards for electrical safety, and IEST guidelines for cleanroom operations are all essential considerations.
The garments you choose must feature static dissipative properties, high-density fabric construction, and non-linting materials that meet tear and heat resistance specifications.
Each of these elements plays a significant role in maintaining the integrity of your cleanroom environment while protecting sensitive equipment from potentially damaging electrostatic discharge.
Proper Maintenance and Testing
To maintain the effectiveness of your cleanroom garments, proper maintenance and regular testing are vital for guaranteeing consistent ESD protection.
You'll need to monitor your garments' dissipative properties using hand-held surface resistance measurement devices and verify they meet standards like IEST-RP-CC052 and ANSI ESDS.2020.
When it comes to washing, you should know that some garments, like the TX4000 system, can maintain their continuity readings for up to 100 wash cycles.
However, you shouldn't wash or decontaminate garments with anti-static treatments, as this can compromise their dissipative properties.
Choose garments made with static dissipative fabrics, conductive threads, and carbon fibers to guarantee proper ESD protection. The garments must maintain a surface resistance requirement of less than 2.5 x 10^9 ohms to be considered effective.
Store your garments properly to prevent damage and contamination. Air showers can help remove static charges before entering clean environments.
You'll want to maintain their integrity by avoiding unnecessary folding or creasing.
Regular inspections are vital to guarantee your garments remain in good condition.
Remember to test the entire garment system, including hood, coverall, and boots, to verify electrical continuity and static charge dissipation.
Pay special attention to non-linting and continuous filament fabrics, as they're vital for maintaining cleaner environments.
Static Control Best Practices
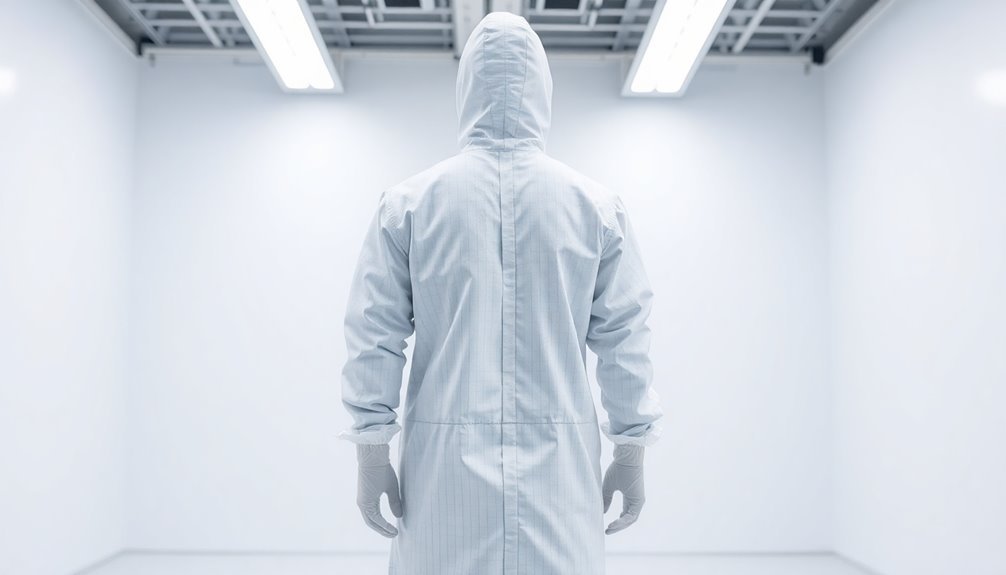
Effective static control in cleanrooms requires a detailed approach that extends beyond garment maintenance. You'll need to implement extensive measures that address all potential sources of static electricity in your cleanroom environment.
Control Area | Best Practice |
---|---|
Flooring | Install static-dissipative or conductive materials with proper grounding |
Equipment | Use ESD-safe furniture and tools with verified conductivity ratings |
Personnel | Follow strict gowning procedures with ESD-compliant garments |
To maintain effective static control, you must guarantee your cleanroom meets industry standards like IEST-RP-CC052 and ANSI ESDS.2020. Start by selecting appropriate flooring materials that provide consistent static dissipation. Your walls should incorporate anti-static panels that prevent particle accumulation while controlling static buildup.
When outfitting your personnel, choose garments made from static-dissipative materials like polyester with carbon filaments. Make sure there's electrical continuity between all garment components, including hoods, coveralls, and boots. Don't forget to regularly test your static control measures and maintain proper documentation. You'll also need to provide ongoing training to your staff about static control procedures and guarantee they understand the importance of following established protocols.
Frequently Asked Questions
How Long Can Antistatic Garments Be Stored Before Their Properties Deteriorate?
You'll need to monitor your antistatic garments carefully, as their properties can deteriorate based on storage conditions. While treated garments have limited shelf life, those with conductive threads can last through 100 washes.
Can Antistatic Cleanroom Garments Be Worn During Outdoor Facility Maintenance?
You shouldn't wear antistatic cleanroom garments outdoors during facility maintenance. They're designed for controlled indoor environments only, and outdoor exposure will compromise their protective properties and violate safety standards.
Do Different Colors of Antistatic Garments Affect Their Static-Dissipative Properties?
No, you don't need to worry about color choices. The static-dissipative properties of your antistatic garments come from their conductive materials and treatments, not their color. All colors perform equally when properly manufactured.
What Happens if Antistatic Garments Get Wet During Cleanroom Operations?
If your antistatic garments get wet, they'll lose their static-dissipative properties, risking equipment damage. You'll need to replace them immediately as moisture compromises both safety and effectiveness in controlling electrostatic discharge.
Are There Temperature Limitations for Wearing Antistatic Cleanroom Clothing?
Yes, you'll need to observe temperature limits for your antistatic cleanroom clothing. Extreme heat can degrade the fabric's antistatic properties, while excessive cold might affect its conductivity and protective performance.
In Summary
You'll need to maintain your cleanroom antistatic garments properly to guarantee continuous protection against static discharge and particle contamination. Regular testing, correct washing procedures, and careful handling will extend their effectiveness. Remember to follow your facility's protocols for garment use and always verify that your attire meets current industry standards before entering sensitive areas. Don't compromise on static control best practices.
Leave a Reply