Testing your protective garments requires a systematic approach using specialized equipment. You'll need surface resistance meters, charge decay testers, and wrist strap testing stations to verify electrical safety compliance. For physical integrity, you must inspect seams and conduct movement simulations to guarantee they meet EN 14325:2004 standards. Chemical resistance testing demands tools for measuring breakthrough times and penetration levels, while particulate testing requires equipment to monitor inward leakage. Don't forget calibration tools and environmental monitors to maintain testing accuracy. Understanding your equipment options will help you create a thorough testing protocol for maximum protection.
Basic Testing Requirements
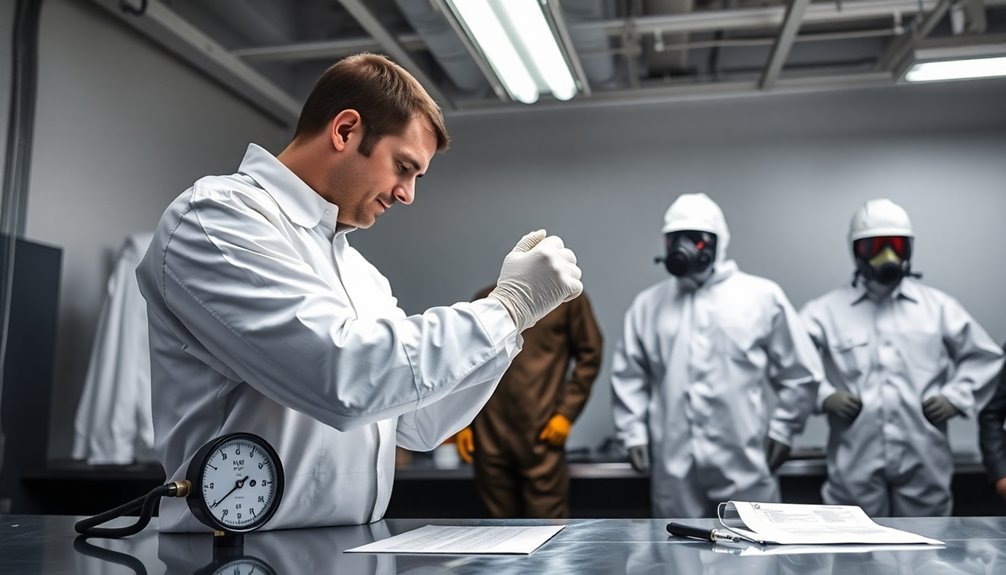
When testing protective garments, you'll need to follow three fundamental testing protocols: physical integrity, inward leakage, and chemical resistance testing.
For physical integrity testing, you must verify that all seams meet the EN 14325:2004 standard, achieving at least Class 1 with strength greater than 30N. You'll need to inspect the garment visually and through palpation to detect any tears, breaks, or discontinuities. Testing should include movement simulations like climbing and crawling to ensure suit integrity during use.
Don't forget to check seam construction to confirm solid particles can't penetrate through stitch holes.
Your inward leakage testing should follow EN ISO 13982-2:2004 protocols. You'll need to measure particulate concentrations inside and outside the suit while test subjects perform standard movements at normal working speed.
The total inward leakage mustn't exceed 15% for at least 80% of all measurements, using sodium chloride aerosol as your test agent.
For chemical resistance, you'll conduct tests using ASTM F903 for visual penetration assessment and ISO 6530 for liquid repellency. You must measure breakthrough times according to ISO 6529 (1.0 µg/cm²/min) or ASTM F739 (0.1 µg/cm²/min) standards, testing against relevant chemicals for your specific application.
Surface Resistance Measurement Tools
You'll find a range of surface resistance measurement tools essential for testing protective garments, from basic handheld meters to sophisticated data-logging instruments that can measure up to 10^12 ohms.
Modern testing devices like the PRS-812B offer data storage capacity for up to 120 measurements, allowing comprehensive documentation of your testing results.
When selecting your testing equipment, consider tools with automatic functions and variable test voltages to guarantee accurate measurements across different garment materials and conditions.
Your measurement tools should meet calibration requirements and comply with ESD standards like ANSI/ESD STM 2.1, guaranteeing reliable and repeatable results for your garment testing program.
Basic Resistance Testing Tools
Several key tools and methods are essential for measuring surface resistance in protective garments. The four-point collinear probe method and four-point probe technique stand out as primary testing approaches.
When you're testing protective garments, you'll want to follow established standards like ANSI/ESD STM 2.1 and IEC 61340-4-9. These standards verify that your measurements meet industry requirements for different garment types, including static control and groundable static control systems. Temperature control during testing is critical since temperature fluctuations can significantly affect measurement accuracy.
You'll need to verify that your testing equipment can apply DC current between outer probes while measuring voltage differences between inner probes for accurate results.
Your testing accuracy directly impacts worker safety in hazardous environments.
Proper resistance measurements prevent costly equipment damage from static discharge.
Regular testing helps maintain compliance with safety regulations and protects your company's reputation.
For situations where standard resistance measurements aren't suitable, you'll need to evaluate alternative testing methods outlined in IEC/TS 61340-4-2 and EN 1149-3. These might include decay time measurements or triboelectric charging tests.
Remember that geometric correction factors are necessary when testing non-standard sample sizes, and your material should be thinner than 40% of the probe spacing for accurate readings.
Advanced Measurement Equipment
Advanced surface resistance measurement tools consistently require precise instrumentation for reliable protective garment testing. You'll need specialized equipment like four-point probes, which consist of four equally spaced, co-linear electrical contacts that allow you to measure surface resistance accurately.
When you're testing protective garments, you'll use a DC current source connected to the outer probes while measuring voltage drops between the inner probes. The sheet resistance calculation (Rs = ΔV / I) will help you determine the material's protective qualities in ohms per square.
You'll need to take into account geometric correction factors if your fabric sample's thickness exceeds 40% of the probe spacing. Modern testing methods have evolved significantly since the early protective gear of the 1900s that relied on basic materials.
For more complex measurements, you might want to use the Van der Pauw method, which lets you test arbitrarily shaped samples with four contacts placed around the edges. This technique's particularly useful when you're working with smaller fabric samples, as the exact spacing between contacts isn't critical.
You'll need to take eight measurements around the sample's periphery to calculate accurate resistivity values. Remember to calibrate your equipment regularly to guarantee your measurements remain reliable and consistent.
Calibration and Accuracy Standards
Proper calibration of surface resistance measurement tools demands strict adherence to international standards like ISO 17025 and MIL-STD-45662.
You'll need to verify that your equipment meets the Test Uncertainty Ratio of 4:1 and maintains traceability to National Metrological Institute standards through proper certification. Regular verification checks and adjustments are vital for maintaining accuracy in your measurements.
When working with protective garments, you'll encounter various calibration standards specific to your testing needs, including certified coating thickness standards and static control requirements outlined in IEC 61340-4-9. Controlled environments are essential for performing accurate calibrations that meet industry specifications.
It's imperative to maintain documented procedures for all calibration processes and keep detailed records of verification results.
- Your testing accuracy directly impacts worker safety – improperly calibrated equipment could mean life or death in hazardous environments.
- Every measurement you take affects quality control decisions that protect countless lives.
- Your commitment to precise calibration upholds international safety standards that safeguard workers worldwide.
Remember that all calibration certificates must be traceable to recognized National Metrological Institutes, and you'll need to verify accuracy before each use.
The global alignment of standards through Mutual Recognition Agreements ensures your testing meets worldwide safety requirements.
Charge Decay Testing Equipment
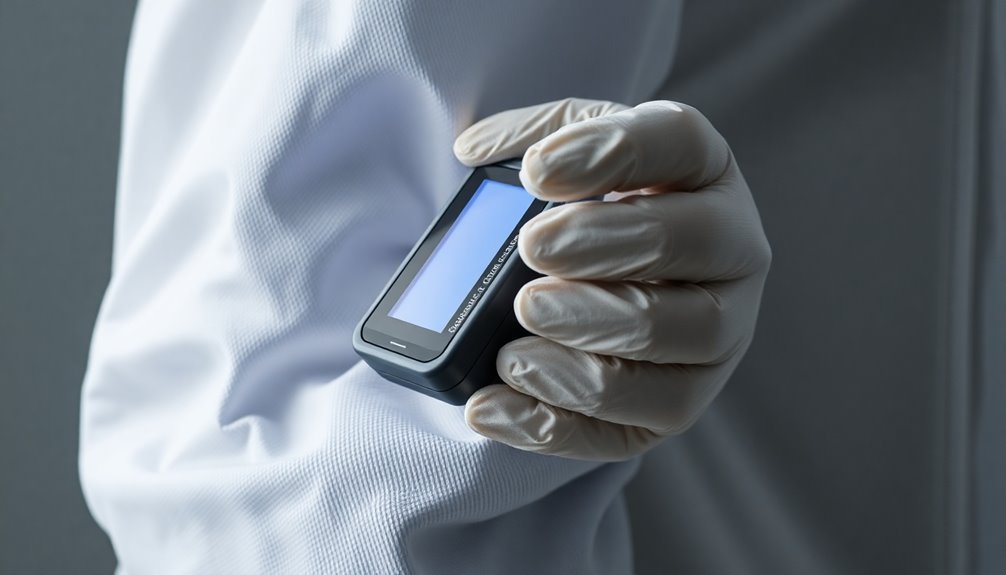
Testing garments' electrostatic discharge properties requires specialized charge decay equipment that measures how quickly static charges dissipate from protective clothing. You'll find instruments like the ID917 and ID946 offer essential features for this testing, including selectable test voltages of 1kV or 5kV and adjustable polarity options. These meters provide graphical displays that show the complete discharge curve during testing.
When you're testing protective garments, you'll need to guarantee your equipment complies with BS EN1149-3:2004 standards. The ID913 and ID923 meters are specifically designed for this purpose, allowing you to evaluate garments under real-world conditions.
You can monitor discharge curves in real-time and measure both 50% and 90% discharge points.
Your testing should follow NT ELEC 037 methods, which involve evaluating the garment while it's worn. You'll need to verify each panel's ground connection and overall continuity.
The equipment lets you test both tribocharging and induced charging scenarios, giving you thorough data on the garment's protective capabilities. With USB connectivity, you can store and analyze your test results, ensuring proper documentation of compliance testing.
This helps you maintain consistent safety standards and verify your protective clothing meets required specifications.
Groundable Points Verification Systems
The essential equipment for verifying protective garment grounding points includes specialized testing devices that measure electrical continuity and resistance values. You'll need to focus on testing equipment specifically designed for protective garments rather than aerial mapping systems, as proper grounding verification guarantees your safety when wearing protective clothing. Similar to how checkpoints validate results, verification systems confirm your protective gear meets requirements.
When testing your protective garments, you'll want to use equipment that meets international safety standards and provides accurate measurements of protective properties. Modern testing systems like the LINEV Systems FLOWD offer automated detection capabilities to identify weak points and verify grounding effectiveness.
You'll feel more confident knowing your garment's grounding points have been verified with precision testing equipment that meets DIN 6857-2 and ÖNORM S5213 standards.
You can trust your safety equipment better when it's undergone thorough testing with certified verification systems.
You'll work with peace of mind knowing your protective gear has passed rigorous quality control inspections.
Remember to maintain regular testing schedules using proper verification equipment to guarantee your protective garments continue meeting safety requirements. Focus on equipment that offers detailed reporting features and can test various material types, including lead-based and lead-free protective materials.
Wrist Strap Testing Stations
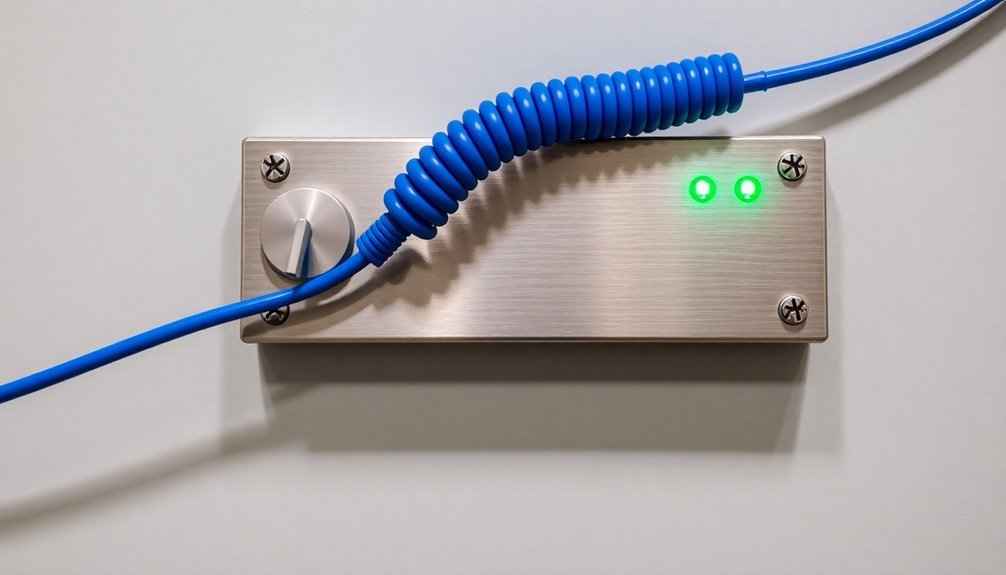
Your wrist strap testing station needs essential features like LED indicators, audible alarms, and resistance measurements to properly assess ESD protection.
Regular testing is crucial since wrist straps commonly fail due to wear and tear during daily use.
You'll find that modern testing stations offer both basic pass/fail readings and advanced capabilities like data logging and near-fail detection.
Daily calibration checks of your testing equipment will guarantee accurate readings and maintain compliance with ESD safety protocols.
Modern testing stations, such as the ESD Test Station, assess the resistance of the wrist strap system (including the operator) and provide a pass/fail indication. Some more advanced test stations will also provide the actual resistance measurement and can even log test data on a computer.
The frequency of testing differs from company to company. Some require testing just once at the beginning of the shift. Other companies may require re-testing several times a day.
Constant monitors can eliminate the risk of wrist strap failure during a shift. These monitors provide immediate notification of a problem and alert the operator to not handle the product until the problem is resolved. They monitor the wrist strap at the work location, eliminating the possibility of a functional wrist strap but a defective ground attachment. They also eliminate the need for recording and storing test results.
Testing stations like the WST2 and WST200 ensure that basic ESD protection is met by quickly and accurately measuring the resistance between an operator, wrist strap, and ground cord. These testers indicate three levels of resistance: HI, LO, and OK with easy-to-read LED lights and audible alarms.
The WST2 Test Station is supplied with a WST1 meter, wall mounting board, 6-inch cord (0 meg-ohm), and a 9V battery. It has a single test range of 0.75 meg-ohm to 35 meg-ohm, meeting the IEC 61340-5-1 specification. The instrument has a green light for PASS and 2 red lights which indicate either HIGH resistance fail or LOW resistance fail. A buzzer sounds in any fail situation.
The GTS900K Premium Combination Wrist Strap and Footwear Testing Station tests both ESD wrist straps and ESD footwear to determine if the grounding device is functioning correctly. It features a split footplate design to test both feet simultaneously and independently, and it gives both Low and High failure alarm modes. This tester fully supports the Compliance Verification Plan requirements as stated in the ANSI ESD S20.20.
Key Testing Station Features
Modern wrist strap testing stations deliver essential resistance measurements between an operator's wrist strap system and ground, ensuring reliable ESD protection.
Your testing station should verify resistance levels between 800K and 10M ohms, falling well within industry standards of 35 megohms. You'll find clear indicators through LED lights and audible alarms that signal whether your resistance levels are HI, LO, or OK.
Using a low 9-volt DC test voltage, these stations effectively monitor the continuous grounding path between your wrist band and coil cord. Advanced models can provide detailed resistance measurements and data logging capabilities, while also monitoring your work surfaces.
Here's why you can't afford to skip proper testing station implementation:
- A single undetected wrist strap failure can destroy thousands of dollars worth of sensitive electronics
- Without immediate notification of grounding issues, you're risking your entire production line
- Continuous monitoring stations eliminate the possibility of ESD damage between periodic tests
Whether you need a simple portable tester like the WST200 or an advanced station with near-fail technology like the PDT800K, you'll find options that match your operational requirements and budget constraints.
Daily Calibration Requirements
Proper calibration of wrist strap testing stations guarantees reliable ESD protection across your facility. You'll need to implement daily calibration procedures based on your facility's ESD sensitivity levels and equipment usage patterns.
While annual calibration is generally recommended for wrist strap testers, you should adjust the frequency according to your specific risk factors and production demands.
To perform calibration effectively, you'll need precision resistance boxes ranging from 700 kilohms to 11 megohms with ±1% tolerance. The Vermason Calibration Unit (VER-28532) is an excellent tool for testing high-speed, high-accuracy testers.
When calibrating, connect the test resistance from the banana jack to the test button, and verify that the display shows the correct readings.
Your calibration procedures must comply with ANSI/ESD S20.20 standards and be traceable to NIST. You'll want to confirm that all test clips are properly insulated from users' hands during the calibration process.
Remember to document all calibration activities as part of your Compliance Verification Plan, and maintain certification records for your calibration units, including NIST certificates.
Environmental Monitoring Devices
Environmental monitoring devices serve as vital components in protecting both workers and protective garments through four essential functions: air quality assessment, temperature and humidity tracking, chemical detection, and pressure monitoring. You'll find these devices integrated into smart PPE systems, providing real-time data to keep you safe in controlled environments while protecting valuable inventory from environmental damage.
When implementing these monitoring systems, you'll need to guarantee proper connectivity and sensor fusion capabilities. Your devices should incorporate low-power AI algorithms for efficient operation and connect to IoT networks for thorough remote monitoring.
Don't forget to maintain regulatory compliance with standards like 21 CFR Part 11 and GAMP.
For maximum protection, consider these essential monitoring aspects:
- Install CO and CO2 sensors to detect dangerous gas levels before they reach harmful thresholds
- Set up continuous temperature and humidity monitoring to prevent garment deterioration
- Deploy chemical detection systems to alert you of potential contaminants that could compromise your PPE
Regular maintenance and professional installation are essential for system reliability. You'll need to schedule periodic validations and keep your team trained on proper device operation and alert response protocols.
Garment Resistance Testing Methods
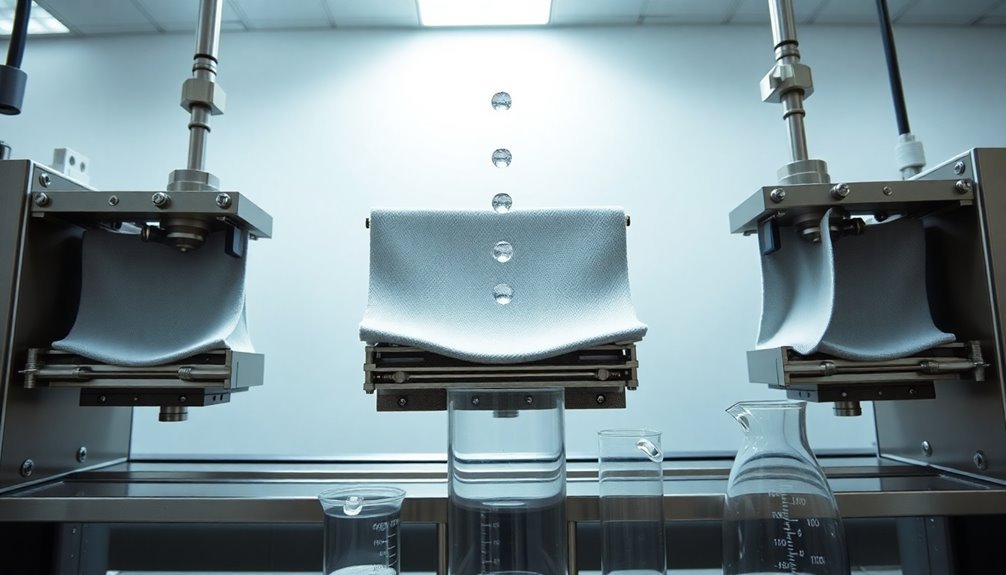
Technical garment resistance testing requires adherence to rigorous standards like ANSI/ESD STM 2.1 and IEC 61340-4-9 to guarantee protective clothing meets safety requirements.
You'll need to follow specific procedures that involve placing the garment on an insulative support surface with the inside surfaces laid flat and using insulative sleeve inserts to isolate fabric sides.
When conducting resistance measurements, you'll start by attaching electrodes and applying 10 volts, observing the readings after 5 seconds. If you encounter high readings, you'll need to increase the voltage to 100 volts and extend the measurement time to 15 seconds.
For garments with buried or core conductive yarns, you'll follow IEC/TS 61340-4-2 procedures.
You can also employ alternative testing methods outlined in EN 1149-3, which measure field strength decay due to charge movement in the fabric.
If you're working with specialized garments, you might need to use a tribocharging method using a mannequin, where you'll apply specific rubbing pressures and speeds with either a Teflon rod or woollen cloth to evaluate static control performance through half decay time and shielding measurements.
Static Field Detection Equipment
Having covered testing methods for protective garments, you'll need reliable equipment to measure static fields accurately. Static field detection equipment allows you to measure electrostatic charges without making direct contact with surfaces, using specialized meters that display readings in volts per meter (V/m) or kilovolts per meter (kV/m).
Your static field meter should include essential features like chopper stabilization for accurate readings in ionized environments, a conductive case for proper grounding, and an LED rangefinder system for precise positioning.
You'll find most meters can measure up to ±19.99 kV with ±5% accuracy when properly maintained and calibrated.
For ideal results when testing protective garments, remember these vital points:
- Position your meter exactly 1 inch from the target surface – this distance is critical for accurate measurements
- Always zero-adjust your meter before testing to guarantee reliable baseline readings
- Use the hold function to capture measurements in challenging positions or when you need to record multiple readings
Regular maintenance and calibration of your static field detection equipment isn't optional – it's essential for maintaining measurement accuracy and guaranteeing your protective garments meet safety standards.
Quality Control Testing Instruments
To guarantee your protective garments meet quality standards, you'll need an extensive set of testing instruments that range from basic measurement tools to specialized PPE testing equipment.
Start with essential tools like measuring tapes, digital cameras for defect documentation, and Pantone color swatches for accurate color matching. You'll also want barcode scanners to track your products effectively through the testing process.
For X-ray protective clothing, you can utilize the FLOWD machine, which evaluates protective properties and automatically detects weak areas through red-green coloring. It's particularly useful as it doesn't require special protective rooms due to its low dose rate.
When testing specialized PPE, you'll find SatatonMall equipment invaluable for evaluating antistatic, fire-resistant, and chemical protective garments. These instruments comply with international standards like ISO, EN, and ASTM.
For thorough quality assurance, Intertek's testing services can help you assess respiratory protection, face masks, and protective apparel. Their equipment tests for biological and chemical resistance, while also providing certification for safety footwear and helmets.
Visual inspection tools remain vital for checking seam quality, label placement, and overall garment balance.
Frequently Asked Questions
How Often Should X-Ray Protective Garments Be Tested for Radiation Attenuation?
You should test your X-ray protective garments annually for radiation attenuation. You'll also need to inspect new garments before first use and perform regular visual checks for any damage or wear.
Can Chemical Barrier Tests Be Performed on Already Worn Protective Clothing?
You can test worn protective clothing for chemical barriers, but the results won't be as reliable as new garments. Wear and tear substantially affects protection levels, making standardized testing procedures less accurate and dependable.
What Temperature Changes Indicate Failure During Thermal Protective Clothing Tests?
You'll notice clothing failure when temperatures cause fiber breakdown, visible charring, or embrittlement. Watch for dye changes around 400°F and significant material degradation above 500°F during standardized five-minute exposure tests.
How Do Different Cleaning Methods Affect the Integrity of Protective Garments?
You'll need to avoid harsh chemicals when cleaning protective garments. Daily wipe-downs are safer than home washing, but industrial laundering's your best option to maintain protective properties and extend garment life.
When Should Protective Garments Be Retired Regardless of Test Results?
You must retire your protective garments after 10 years of use, regardless of their condition or test results. This mandatory retirement rule guarantees you're not relying on gear that may have hidden degradation or outdated protection.
In Summary
You'll need reliable testing tools to maintain your protective garment program's effectiveness. By regularly checking surface resistance, charge decay, and grounding points using the equipment discussed, you're ensuring worker safety and ESD protection. Don't forget to document all test results and calibrate your testing instruments regularly. Your commitment to proper testing procedures directly impacts your facility's ESD control success.
Leave a Reply