When measuring surface resistance for workwear, you'll need three essential tips for accurate results. First, use a calibrated digital surface resistance meter with both parallel electrodes and ground lead capabilities, ensuring it can measure between 10^4 to 10^12 ohms. Second, maintain consistent environmental conditions, particularly 25% relative humidity, and precondition your fabric samples for 24 hours before testing. Third, document your measurements carefully, distinguishing between surface resistivity (ohms/square) and surface resistance (ohms) according to ESD standards. Understanding these fundamentals opens the door to more advanced testing techniques and reliable ESD protection.
Equipment Setup and Calibration
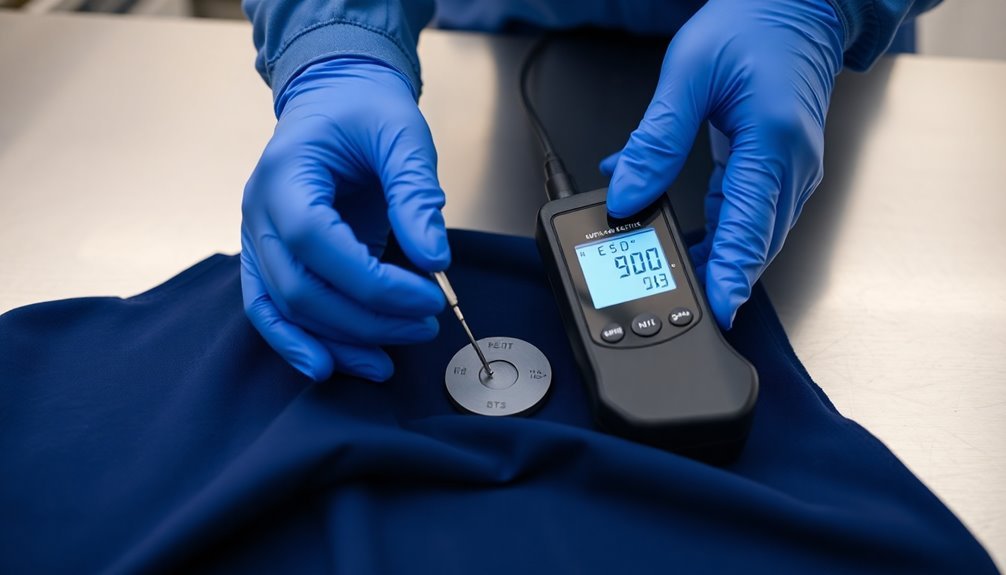
Three key components make up the essential equipment for surface resistance measurement: a digital surface resistance meter, electrodes, and calibration tools.
You'll want to select a digital surface resistance meter like the SCS SRMETER2 or SCS 770760, which offers automatic test voltage selection between 10V and 100V based on the resistance range you're measuring.
For accurate measurements, you'll need both parallel electrodes for point-to-point measurements and a single electrode with a ground lead for resistance-to-ground testing. The meter should be capable of measuring resistance ranges from 10^4 to 10^12 ohms, which is typical for ESD applications. When testing ESD smocks, use 2.5 kg cylindrical electrodes placed 30 cm apart for proper measurement.
Before using your equipment, verify it's properly calibrated. You'll need ±1% tolerance resistors for each decade range to perform in-house calibration.
Make it a habit to check your meter's calibration annually. Don't forget to inspect the electrodes for damage before each use and replace the battery whenever the low battery indicator lights up.
When you're not using the meter, store it in a dry, protected environment to maintain its accuracy and extend its lifespan.
Environmental Testing Conditions
Testing experts understand that environmental conditions substantially impact surface resistance measurements of workwear. When you're conducting these measurements, you'll need to follow standardized conditions, particularly the EN 1149-1 standard that requires 25% relative humidity.
You must precondition your fabric samples for 24 hours in controlled humidity settings to guarantee accurate results. The industry's shift towards sustainable materials has made testing even more critical due to varying conductivity properties.
Remember that moisture absorption plays a vital role in anti-static treatments' effectiveness. While testing occurs in low humidity conditions, most real-world work environments have higher humidity levels, which typically enhances the treatment's performance.
You'll notice that synthetic fibers respond differently to these conditions, and their surface resistance can vary markedly.
If you're working with critical applications, you'll need to conduct thorough risk assessments and may require specialized garments. It's imperative to maintain properly earthed points for effective charge dissipation.
Don't forget that anti-static treatments can erode over time, especially in low-humidity environments. When selecting workwear, consider garments with intrinsic anti-static properties for applications where consistent performance is vital.
You can enhance treatment effectiveness by controlling environmental conditions in your testing area.
Measurement Techniques and Documentation
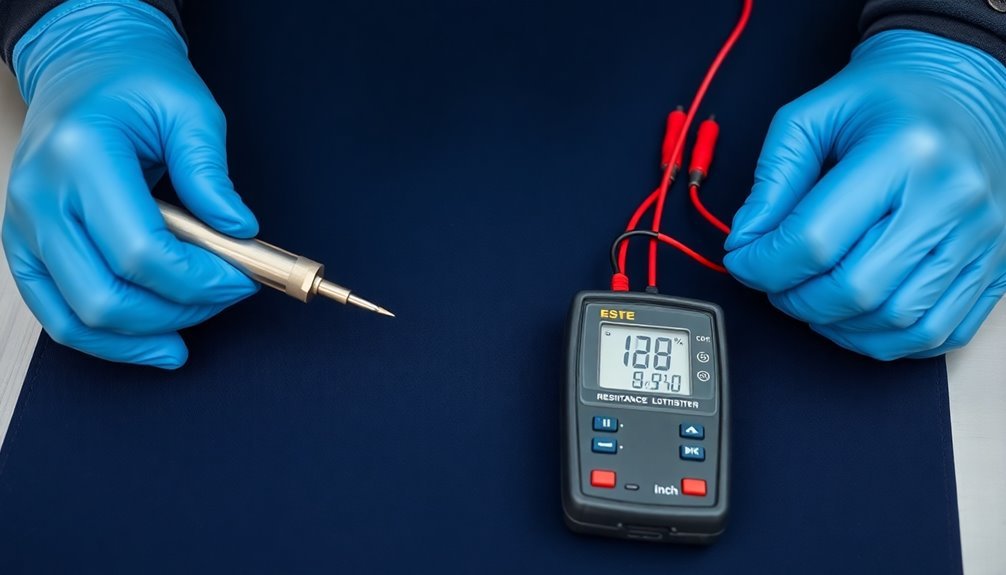
A thorough approach to surface resistance measurement requires mastering several key techniques. You'll need to understand both parallel bar sensing and surface resistivity cell methods to properly evaluate workwear materials.
For parallel bar sensing, you can measure surfaces ranging from 10³ to 10¹² Ohms per square using electrodes placed on the fabric surface. The ASTM standard method ensures consistent and accurate readings across different materials.
When using surface resistivity cells, you'll want to follow AATCC 76-2000 standards, especially for materials with resistivity above 10⁷ Ω-cm. You must take measurements at specific voltages and wait 60 seconds before recording results.
Choose between pressure probes for perpendicular measurements and surface probes for parallel measurements, with surface probes being more relevant for typical shielding applications.
For ESD-specific testing, you'll need to conduct both RTT (point-to-point) and RTG (resistance to ground) measurements using an ESD meter. Document your results carefully, distinguishing between surface resistivity (ohms/square) and surface resistance (ohms) as specified in ESD TR20.20.
Remember that static dissipative materials should fall between 1 x 10⁶ and 1 x 10¹² ohms for proper classification.
Frequently Asked Questions
How Often Should Workwear Be Replaced to Maintain Proper Surface Resistance Levels?
You'll need to replace your workwear when inspection reveals damage, poor fit, or compromised resistance levels. Don't wait for scheduled replacements – monitor regularly and replace immediately if there's any performance decline.
Can Washing or Dry Cleaning Affect the Surface Resistance Properties?
Yes, both washing and dry cleaning can affect your workwear's surface resistance. While proper washing with suitable detergents has minimal impact, dry cleaning solvents like PERC can substantially alter the surface resistance properties.
What's the Acceptable Resistance Range for Different Types of Workwear?
You'll need conductive workwear at <10^5 Ohms, static dissipative gear between 10^5-10^9 Ohms, and insulative clothing >10^9 Ohms. Always check your industry's specific requirements for compliance.
Do Different Body Areas Require Different Surface Resistance Specifications?
Yes, you'll need different resistance specs for each body area. Your upper body garments follow STM2.1 standards, while your footwear and flooring must meet STM97.1. Gloves require their own specialized specifications.
How Do Fabric Seams and Attachments Impact Overall Surface Resistance Measurements?
You'll find that seams and attachments create discontinuities in your fabric's electrical pathways, affecting resistance measurements. They can either increase resistance through gaps or decrease it when using conductive materials.
In Summary
You'll find that proper surface resistance testing of workwear is essential for maintaining safety standards in your workplace. By following the correct equipment setup, maintaining consistent environmental conditions, and using standardized measurement techniques, you're ensuring accurate and reliable results. Remember to document your findings thoroughly – it's not just about getting the measurements, but also about creating a traceable testing history for compliance purposes.
Leave a Reply