Test your static control wrist strap daily using a calibrated tester to verify resistance falls between 750k ohms and 10 megohms. Visually inspect the band and cord for wear, cuts, or fraying. Check that the strap fits snugly against bare skin without restricting blood flow. Confirm all connections are secure at the buckle, banana jack, and ground point. Use continuous monitoring systems for real-time feedback on effectiveness. Document your test results and maintain detailed records of any failures or replacements. Apply ESD lotion if you experience high resistance readings. Watch for both "high fail" and "low fail" indicators. These essential checks are just the beginning of proper ESD protection.
Daily Testing Procedures
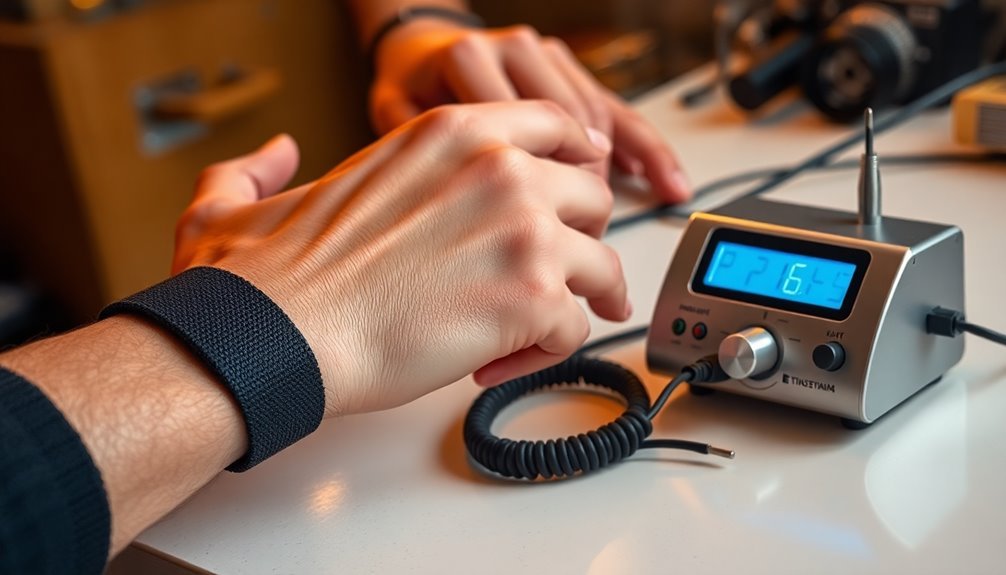
To maintain the effectiveness of static control wrist straps, daily testing is essential using specialized testers that verify proper electrical resistance.
You'll need to test your entire wrist strap system, including the wristband, ground cord, and grounding point, using either battery-powered or AC-powered testers that meet compliance verification requirements.
When you're ready to test, wear your wrist strap as you normally would during work. Connect the free end of your ground cord to the tester and, if required, press the hand contact plate. Industry standards require that total resistance should be less than 35 megohms.
Your wrist strap system should show a resistance reading between 750 kilohms and 10 megohms to pass. You'll see a green LED for a passing result and a red LED for failure.
If you get a failed reading, stop work immediately and test the wristband and cord separately to identify the faulty component. You'll need to replace any defective parts and retest the system before resuming work.
Remember that you must perform this testing at the start of each shift, and it's vital to document your results as part of your compliance verification plan. Always make certain your test equipment is calibrated to NIST standards for accurate readings.
Visual Inspection Methods
While daily electrical testing guarantees proper functionality, visual inspection serves as your first line of defense in maintaining static control wrist straps. You'll need to examine three key areas: the strap itself, how it's worn, and potential common issues.
Start by checking the strap's physical condition. Look for any breakages in the strap material, coil cord, or connectors. Examine the cord for cuts or frays, and make sure the buckle's securely attached. Don't forget to inspect the banana jack and stud snap connections. Dirty wrist cuff interiors can significantly reduce the effectiveness of grounding.
When checking how the strap's worn, verify it's making direct contact with your skin, not over clothing. The strap shouldn't be loose and must be properly sized for your wrist. Pay attention to skin conditions that could affect conductivity.
Watch for common problems like stretched-out straps, worn-out materials, and improper cord connections. Don't connect the wrist cord to an ESD mat stud, and check for signs of shorted resistors in the coil cord.
You should perform these visual checks before each use and maintain detailed records of your inspections. Proper training in these procedures will help you spot potential issues before they become problems.
Resistance Testing Equipment
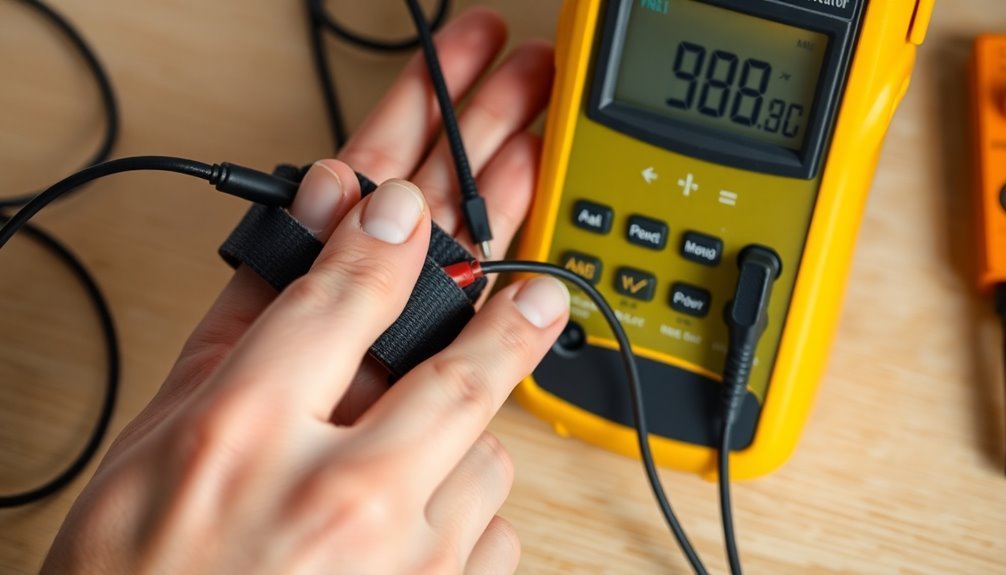
You'll find several types of resistance meters available for wrist strap testing, including portable handheld units and fixed test stations with digital displays that can measure resistances between 800 kilohms and 10 megohms.
Your daily testing options range from simple pass/fail indicators like the WST200 to advanced systems like the PDT800K that feature "near-fail" technology and data logging capabilities.
When using these devices, you'll need to maintain proper calibration by regularly testing them with known resistance values and following the manufacturer's specified procedures. Testing should confirm readings are less than 3.5 megohms for wrist straps to meet safety standards.
Understanding Resistance Meter Types
Resistance meters stand out as essential tools in the world of static control, with several specialized types designed for different testing applications. You'll find that digital megohmmeters offer high precision for testing in electrostatic protected areas, while surface resistance meters use parallel bar sensing to measure various surface types. Quality digital megohmmeters can deliver test results in numbers rather than using logarithmic scales.
Meter Type | Key Features |
---|---|
Digital Megohmmeters | High precision, ideal for EPAs |
Surface Resistance Meters | ASTM Standard parallel bar sensing |
Combo ESD Testers | Visual LEDs, audible alarms |
When selecting a resistance meter for wrist strap testing, you'll need to think about measurement ranges from 10³ to 10¹² Ohms per Square. Look for features like automatic ranging and LED indicators that provide clear pass/fail results. Most quality meters offer accuracy within +/- 5% and include interchangeable probes for versatile testing options.
You can choose between portable pocket-sized meters for quick on-site testing or advanced data logging testers that connect to PCs for detailed record-keeping. Remember that regular calibration and maintenance are vital for maintaining accuracy, regardless of which type you select. For daily wrist strap testing, prioritize meters that offer simple operation and clear results.
Daily Testing Device Options
Building on our understanding of resistance meters, the specific tools needed for daily wrist strap testing deserve focused attention.
You'll find that portable battery-powered testers offer the most practical solution for daily checks, providing quick pass/fail results through LED indicators. These devices typically switch between 10V and 100V test voltages automatically, verifying accurate measurements within the standard range of 800 kΩ to 10 MΩ. Regular compliance verification records must be maintained to document all test results.
For reliable daily testing, you'll want to think about these essential features:
- Calibration verification – Your tester must maintain ±1% accuracy through regular calibration
- Clear pass/fail indicators – Look for color-coded LEDs that instantly show test results
- Compliance with standards – Verify your device meets EN 61340-5-1 and ANSI/ESD S1.1
- Proper voltage selection – Choose testers with automatic voltage switching capability
Several proven models like the Vermason 225220 and StaticWorx Analog Surface Resistance Test Kit offer these features.
When testing, you'll need to watch for both high fails (above 10 MΩ) and low fails (below 750 kΩ). Remember that dry skin can affect readings, so keep moisturizer handy for retesting if needed.
Calibration Best Practices
A tester's calibration accuracy directly impacts ESD safety program effectiveness, making proper calibration practices essential for reliable wrist strap monitoring.
You'll need to calibrate your testing equipment annually or more frequently based on your critical ESD handling needs and item sensitivity. Using surface resistance meters helps verify your calibration accuracy against known standards.
To properly calibrate your wrist strap tester, you'll need a resistance decade box with a range of 700 kilohms to 11 megohms and ±1% tolerance, along with two compatible test leads. Connect one lead to the wrist strap jack and the other to the tester's test switch.
Set your decade box to test both lower and upper resistance limits (750 kilohms and 10 megohms) to verify proper pass/fail indicators.
If you encounter calibration issues, check for common problems like improperly insulated test clips or faulty ground paths. Low-hazard failures below 750 kilohms often indicate shorted resistors, while readings above 10 megohms may point to defective wrist straps or cords.
When your tester fails calibration checks, you'll need to return it to the manufacturer for recalibration. Remember that all calibration procedures must follow NIST traceable standards and comply with ANSI/ESD S20.20 guidelines for accurate results.
Proper Fit Assessment
You'll need to adjust your wrist strap so it makes consistent contact with your skin without causing discomfort or restricting blood flow.
Test the fit by moving your wrist in different directions while working to confirm the band stays in place but doesn't feel tight.
Check your wrist strap's position and comfort level daily, especially if you're wearing it for extended periods, to verify it maintains proper skin contact throughout your work shifts.
Elastic wristbands offer better adjustability for achieving an optimal fit compared to metal versions.
Snug Without Skin Pressure
Professional technicians know that achieving the perfect fit for a static control wrist strap requires careful balance. You'll need to guarantee the strap maintains consistent skin contact without causing discomfort or restricted blood flow.
When you're adjusting your wrist strap, focus on achieving a snug fit that doesn't slide around but also doesn't leave marks on your skin.
- Test the fit by sliding one finger under the band – it should move freely but maintain contact with your skin.
- Adjust the clasp or links until you've eliminated any gaps while keeping circulation unrestricted.
- Check that the conductive portion stays flat against your skin without bunching or twisting.
- Verify that movement of your wrist doesn't cause the strap to lose contact or become too tight.
You'll know you've achieved the right fit when the strap stays in place during normal arm movements without causing pressure points. If you're using an elastic band, adjust it through the clasp until it's secure but comfortable.
For metal bands, carefully position the links to find the sweet spot between too loose and too tight. Remember, you can't get proper grounding if the strap's too loose, but restricting circulation is equally problematic.
Daily Band Movement Check
During daily operations, checking your wrist strap's movement and fit is essential for maintaining reliable ESD protection. You'll need to verify that your band maintains consistent electrical contact with your skin while allowing comfortable movement throughout your workday.
For elastic bands, you can adjust the fit by pulling the material tail through the clasp until it's snug but not restrictive.
If you're using metal expansion bands, slide the links into the stainless steel backplate to achieve the proper fit. Remember, you don't want the band so tight that it causes skin pressure or discomfort.
Use specific testers to verify electrical resistance and skin contact daily, unless you're working with continuous monitoring systems. If you get a bad reading, test the wristband and cord separately to identify the faulty component.
Replace any failed parts immediately and conduct another test to confirm proper function.
Consider using ESD lotion to improve skin contact if needed, but never use your wrist strap with equipment exceeding 250 VAC.
For sensitive ESD items, continuous monitoring provides the most reliable protection by constantly testing the wrist strap system during use.
Continuous Monitoring Systems
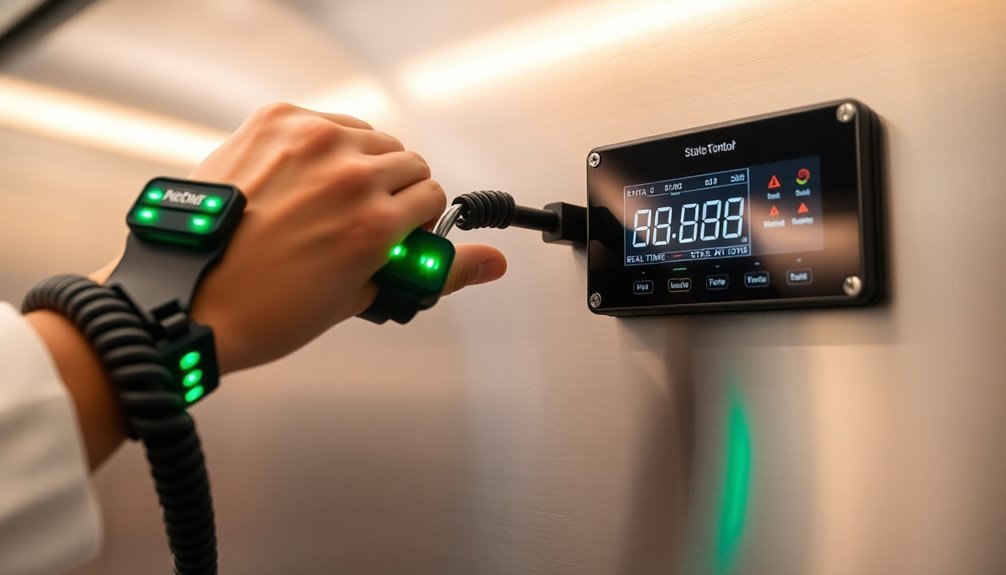
Continuous monitoring systems consistently provide real-time feedback on the effectiveness of static control wrist straps and worksurfaces. These systems immediately detect and alert you to any failures through visual and audible alarms, including split-second issues that periodic testing might miss.
You'll find both single-wire and dual-wire monitoring options available, with dual-wire systems offering enhanced reliability for critical applications.
When you install a continuous monitoring system, you're investing in a robust solution that can replace daily testing requirements while maintaining compliance with industry standards. The systems can be integrated into your existing ESD setup and mounted on mats, benches, or under workstations.
You'll get instant data displays and logging capabilities that help you track patterns and make informed decisions about your ESD control program.
- Single-wire monitors provide economical monitoring for standard wrist straps
- Dual-wire systems guarantee grounding even if one conductor fails
- Real-time monitoring eliminates the need for pre-shift testing and logging
- Data logging capabilities support audit requirements and compliance verification
Choose the configuration that best suits your needs, whether it's a single-user setup or a multi-user system with ESD worksurface monitoring capabilities.
Calibrating Test Equipment
You'll need to check your wrist strap test equipment calibration annually to maintain accurate resistance measurements and prevent ESD damage to sensitive components.
Your equipment verification process should include connecting a resistance decade box to verify proper operation across the full range of acceptable resistance values (700 kilohms to 11 megohms).
Make sure you document all calibration checks, including dates, test values, and verification results in your maintenance records to maintain compliance with industry standards.
Recommended Calibration Check Intervals
Regular calibration checks keep ESD test equipment operating within specified parameters. Most ESD test equipment requires annual calibration to maintain accuracy and reliability.
You'll need to take into account your specific environment and the sensitivity of components you're handling when determining calibration frequency. In high-risk environments or when working with extremely sensitive devices, you might need more frequent calibration checks.
Your calibration intervals should account for:
- Environmental conditions in your workspace, including temperature fluctuations and humidity levels that can impact equipment performance
- Usage patterns and wear on your test equipment, as heavily used devices may need more frequent calibration
- Industry standards and quality control requirements specific to your manufacturing process
- The criticality of ESD-sensitive items you're handling and potential risks of equipment failure
Don't forget to maintain detailed calibration records that include verification dates, NIST traceability, and scheduled recalibration dates.
Your documentation serves as evidence of compliance with ESD control standards and helps track equipment performance over time.
You should also use verification testers periodically to verify your wrist strap monitors maintain proper functionality between formal calibrations.
Equipment Verification Test Steps
Testing your ESD equipment requires a systematic approach to guarantee accurate and reliable performance. You'll need to start by checking that your test equipment has proper power, either through batteries or a manufacturer-specified power adapter.
Make sure all electrical connections are secure and properly grounded before proceeding.
To verify your test equipment's accuracy, connect it to a resistance decade box and check the readings at key resistance values, particularly at 750 kilohms and 10 megohms. Your equipment should display appropriate pass/fail indicators (typically green LED for pass, red for fail) when testing these values.
During verification, avoid touching other metal objects that could interfere with the readings.
When conducting the actual tests, plug the wrist strap into the test equipment and press the test switch. The equipment should register within the acceptable range of 750k ohms to 10 megohms.
If you encounter failures, check for common issues like dry skin conditions or faulty coil cords. You can address dry skin by applying moisturizing lotion and retesting.
Remember that all calibration should be traceable to NIST standards for compliance.
Documenting Calibration Records
Proper documentation serves as the backbone of any effective calibration program. When you're testing static control wrist straps, you'll need to maintain detailed records of your test equipment's calibration status.
Using standardized formats and digital record-keeping systems helps guarantee accuracy and accessibility of your calibration data, while making it easier to track recalibration schedules.
Your calibration records must include essential information for traceability and compliance with industry standards. Document the instrument's identification details, calibration dates, test results, and environmental conditions during testing. Don't forget to record the technician's name and qualifications, as this information is vital for audit trails.
- Store your calibration records securely for at least 4 years, using encryption and access controls to protect sensitive data
- Set up automated alerts to notify you when equipment needs recalibration
- Include measurement uncertainty and original observations in your documentation
- Maintain traceability to national or international standards through proper certification
Remember to conduct regular audits of your calibration records and invest in training programs to enhance your team's competence in both calibration procedures and documentation practices.
Skin Contact Verification
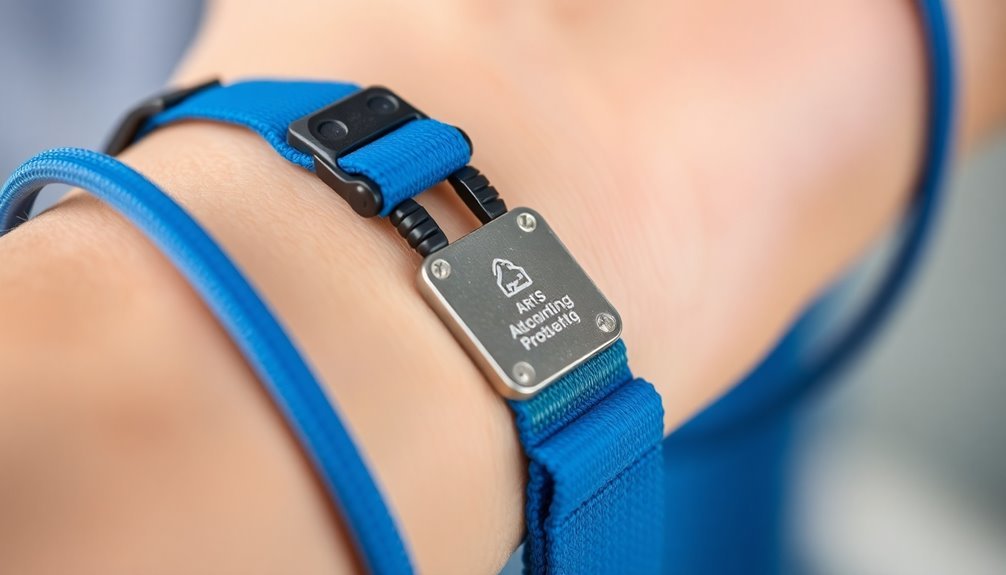
The effectiveness of your wrist strap depends heavily on maintaining reliable skin contact, as even the best ESD protection can fail without proper conductivity between your skin and the device. You'll need to guarantee direct contact between the strap and your skin, never wearing it over clothing or sleeve cuffs.
If you're experiencing dry skin issues, which often cause high resistance readings, you can apply ESD lotion as part of your donning process. Metal wristbands might work better for you if you have persistent dry skin problems, as they typically provide better contact.
When testing your wrist strap, you must perform checks while wearing the device to verify the entire system's functionality, including the skin interface. If you're not using continuous monitoring, conduct daily tests to confirm proper resistance levels.
During testing, watch for common issues like high resistance readings, which often indicate poor skin contact or soiled wristbands.
You'll need to clean your wristband regularly and check for wear and tear. If you're getting failed readings, first verify secure connections between components, clean the contact areas, and retest after addressing any skin contact issues you've identified.
Cord Resistance Measurement
Measuring your wrist strap's cord resistance helps guarantee reliable ESD protection within the critical range of 800 kilohms to 1.2 megohms. You'll need to use a calibrated wrist strap tester to check the entire system, including the ground point, cord, and cuff.
Daily testing is essential unless you're using continuous monitoring equipment to track performance.
To maintain safety and effectiveness, you should verify that your wrist strap's built-in resistor limits current flow below human perception levels while maintaining proper grounding capabilities. When testing, you'll need to watch for both high and low resistance failures, as these indicate different problems that require immediate attention.
- High resistance readings (above 1.2 megohms) suggest compromised voltage removal capability
- Low resistance readings (below 800 kilohms) may indicate a shorted resistor or unwanted ground path
- Soil buildup or mechanical damage can cause resistance changes over time
- Failed components must be replaced immediately to restore proper protection
Remember that your wrist strap mustn't be used with circuits exceeding 250 volts, and the resistor should be rated for at least 1/4 watt with 250 volts working voltage.
Ground Connection Testing
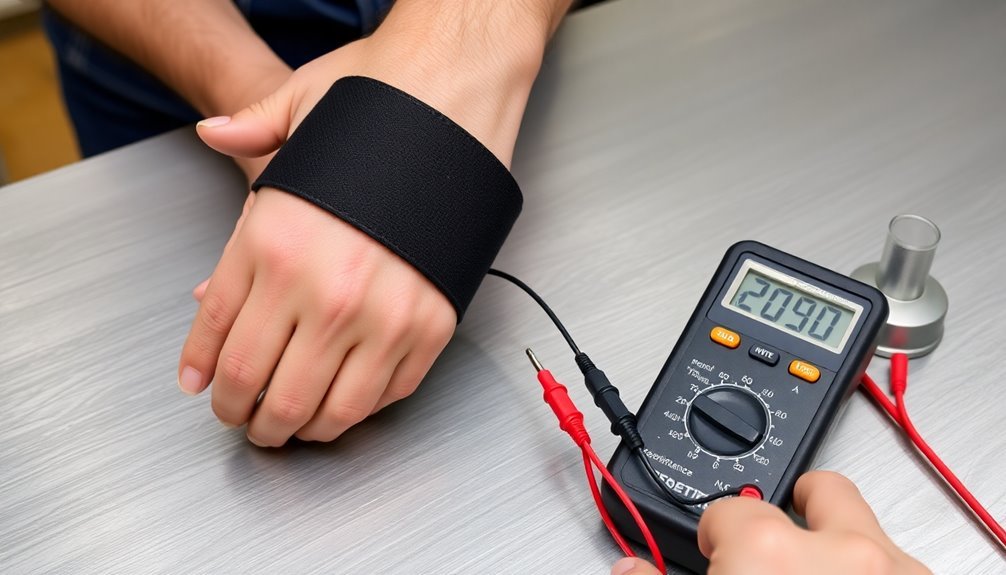
Regular ground connection testing confirms your ESD protection system functions reliably and safely. You'll need to test your wrist strap daily at designated test stations if you use it every day.
For critical applications requiring constant grounding, consider implementing continuous monitoring systems.
You can use commercial testers like the Vermason 225220 or portable options such as the Valtcan Exact. These testers typically include a banana jack for cord connection and hand contact plates to verify system resistance. Battery-powered units work well for small labs or spot-checking.
When testing, wear your wrist strap normally and plug the cord into the tester. Press the test button to check if resistance falls between 800k ohms and 10 megohms. If you get a bad reading, retest immediately. Replace the wrist strap or ground cord if values remain outside acceptable ranges.
Your testing program should verify all components, including the wristband, ground cord, and 1 megohm resistor. If dry skin affects results, apply moisturizer and retest.
Remember to calibrate your test equipment regularly and follow compliance standards like EN 61340-5-1 for accurate verification.
Failure Mode Analysis
While testing helps identify wrist strap issues, understanding common failure modes lets you quickly diagnose and resolve problems. You'll encounter two main types of failures: high resistance failures and low resistance failures.
High fails often result from dry or soiled skin, poorly fitted wrist bands, or broken coil cords. Low fails typically stem from shorted resistors, additional ground paths, or faulty cord connections.
When troubleshooting wrist strap failures, you'll want to check both the band and cord separately to pinpoint the exact issue. If you're experiencing high fails, first confirm proper skin contact and consider using moisturizer for dry skin conditions.
For low fails, inspect the coil cord for damage and verify you're not creating additional ground paths.
- Check your resistance readings against industry standards (800k ohms to 10 megohms)
- Test the wristband and coil cord independently to isolate the failing component
- Verify proper skin contact and band fit before replacing components
- Document failure patterns to identify recurring issues and prevent future problems
Remember to maintain regular testing schedules and replace components showing consistent failures to guarantee reliable static protection.
Test Result Documentation
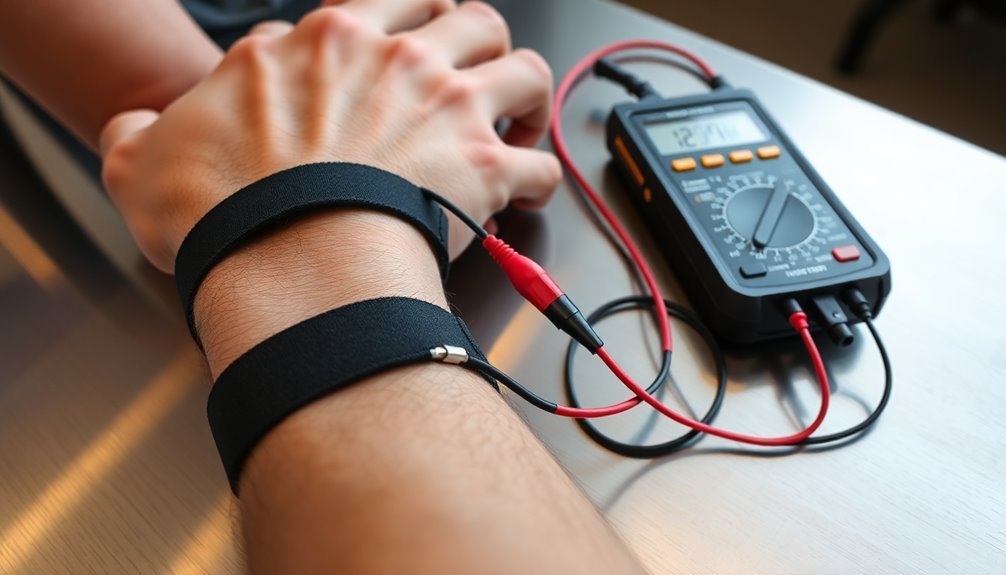
Proper documentation of test results forms the cornerstone of any effective wrist strap monitoring program. You'll need to record essential data including test dates, strap identification, and measured resistance values in a standardized format. Make sure to clearly indicate whether each strap passed or failed based on the acceptable resistance range of 800k ohms to 10 megohms.
You should document the calibration status of your testing equipment and maintain records that demonstrate NIST traceability.
When documenting test failures, include any corrective actions taken, such as strap replacement or ESD lotion application. You'll want to establish re-testing schedules for repaired or replaced straps and document these in your records.
Store your test results in a secure but easily accessible system that allows for quick retrieval during audits. You'll need to maintain audit trails to track any changes made to the documentation and specify retention periods for your records.
Remember to integrate these test results into your overall ESD program plan, which helps you identify trends and maintain compliance with ANSI/ESD S20.20 standards.
Frequently Asked Questions
Can I Wear My Wrist Strap Over Long Sleeves?
You shouldn't wear your wrist strap over long sleeves. It needs direct skin contact for proper grounding. If you're wearing long sleeves, roll them up or use a wrist strap designed for over-clothing use.
How Often Should I Replace My Static Control Wrist Strap?
You should replace your static control wrist strap annually, or sooner if you notice signs of wear like fraying or loss of conductivity. If you share workstations, consider replacing it every 3-6 months.
Does Sweating Affect the Effectiveness of Wrist Straps?
While sweating can improve conductivity between your skin and the strap, it won't enhance overall effectiveness. In fact, sweat may damage your wrist strap over time, so you'll need regular cleaning and testing.
Are Wireless Wrist Straps as Effective as Wired Ones?
No, wireless wrist straps aren't effective at all. They leave dangerous voltage levels even after 5 minutes, while wired straps discharge 1000V to 5V in 0.1 seconds. You should always use wired straps.
Can Multiple People Share the Same Wrist Strap?
No, you shouldn't share wrist straps. It's risky due to contamination, inconsistent grounding from different skin resistances, and increased wear and tear. You'll get better protection by having your own dedicated strap.
In Summary
You'll find that consistently testing your static control wrist straps is essential for maintaining a safe ESD-protected workspace. By following these testing methods and documenting your results, you're ensuring reliable static discharge and protecting sensitive electronic components. Don't skip any steps in the verification process – your diligence in testing wrist straps will prevent costly damage and maintain workplace safety standards.
Leave a Reply