You'll find the best protection for your circuit boards with leading conductive tapes like 3M's 3304BC-S Ni/Cu nonwoven foil-backed tape and 9707 adhesive transfer tape with silver particles. Other top performers include 3M 9711S Series with double-sided conductivity, 3M 9701 for medium adhesion, copper foil tapes for superior EMI shielding, nickel-based tapes for corrosion resistance, and aluminum foil tapes for cost-effective protection. These options provide excellent EMI/RFI shielding across frequencies from 100K to 3GHz while withstanding dynamic friction and extreme temperatures. Understanding the specific features of each tape will help you make the ideal choice for your circuit board protection needs.
Understanding Conductive Tape Benefits
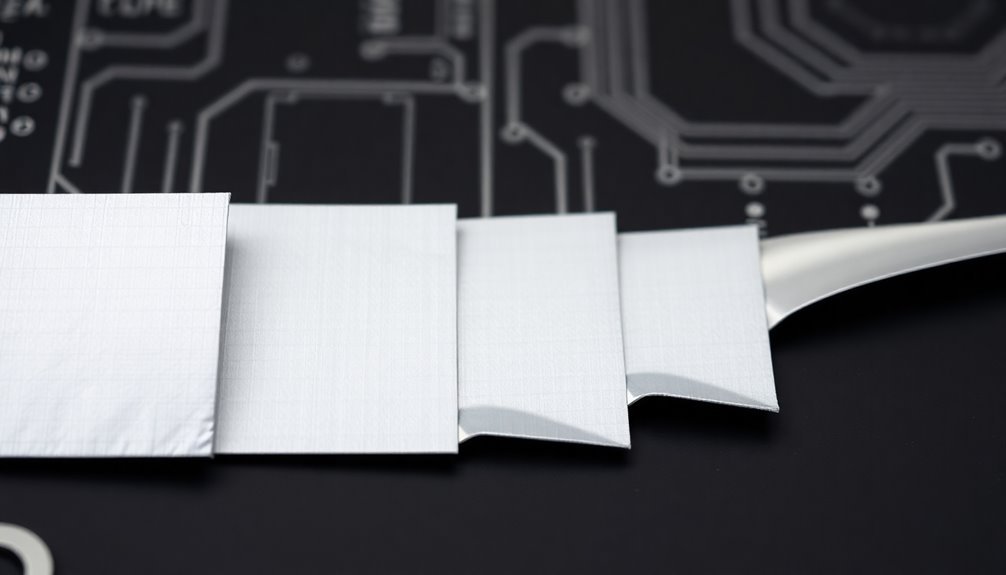
Through its unique combination of flexibility and conductivity, conductive tape has revolutionized circuit board assembly and electronic component protection. You'll find that this versatile material offers superior electrical conductivity compared to metal while being substantially easier to handle and apply in various electronic applications.
When you're working with sensitive electronic components, you'll appreciate how conductive tape provides reliable EMI and RFI shielding, protecting your circuits from electromagnetic interference across a broad spectrum (100K to 3GHz). The tape's ability to withstand dynamic friction makes it ideal for applications with moving parts.
The tape's composition of matrix resin and conductive filler guarantees you get both excellent conductivity and strong adhesion to metal surfaces.
You'll notice the tape's exceptional versatility in electronic applications, from plasma TVs to mobile phones. Its high linear resolution makes it perfect for working with miniaturized components and high-density electronic assemblies.
The soft, burr-free texture means you won't damage delicate components during application, while the anti-oxidation treatment guarantees long-lasting performance.
For circuit board repairs or modifications, you'll find conductive tape invaluable. It provides reliable grounding surfaces and works effectively for static charge draining, making it an essential tool in your electronic assembly and repair toolkit.
Common Types of Shielding Materials
When selecting shielding materials for your circuit board protection, you'll encounter three primary options: metal foils and laminates, conductive fabric solutions, and foam-based EMI protection.
Metal foils, particularly copper and aluminum laminates, offer superior conductivity and excellent EMI shielding properties for your electronic components. These materials function as a Faraday cage effect to effectively block electromagnetic fields from entering or exiting the protected area.
Conductive fabric and foam-based solutions provide flexible alternatives that you can easily conform to complex shapes while maintaining effective EMI protection.
Metal Foils and Laminates
Metal foils and laminates stand as the workhorses of circuit board shielding, offering versatile solutions for electromagnetic and radio frequency interference protection.
Copper foil leads the charge in electronic applications due to its superior conductivity and strong adhesive properties, making it ideal for printed circuit boards and telecommunication equipment.
When you're working with large-scale applications or need a cost-effective solution, aluminum foil provides excellent shielding against radio frequencies while maintaining a lightweight profile. It's particularly effective in medical devices and automotive applications where consistent conductivity is vital.
For complex surfaces, you'll want to take into account expanded metal foils (EMFs). These specially processed materials won't fray or unravel, and they're available in various metals like copper, aluminum, and nickel. Their slit-and-stretch construction maintains flexibility while preserving strength. These materials can be easily shaped with minimal impact on performance since there is minimal deterioration when bending or cutting the material.
If you're dealing with magnetic interference below several hundred kHz, laminated metal foils are your best choice. The mu-ferro shielding foil on PET film combination offers exceptional magnetic shielding capabilities.
You can layer these foils for stronger protection, and they're particularly useful in shielded room applications where large-scale magnetic protection is necessary.
Conductive Fabric Solutions
Moving beyond traditional metal foils, conductive fabric solutions offer remarkable flexibility and versatility for EMI shielding applications. You'll find several specialized options, including VeilShield's transparent copper-plated polyester mesh and FlecTron's durable nylon ripstop construction. The conductive traces created add only about 1 ohm or less to the resistance.
For medical applications, silver-coated fabric stands out with its impressive conductivity that increases up to 25% when stretched. You can stretch this material up to 100% lengthwise and 60% crosswise, while maintaining surface resistivity below 0.5 Ohm/sq.
It's particularly effective for EMI shielding, providing 35+dB protection from 1-10 GHz.
When you're working with conductive fabrics, you can create flexible circuits using etching techniques with ferric chloride. You'll need to apply clear resist over inkjet images before etching, and you can attach components using conductive glue or thread.
For cable shielding, these fabrics work exceptionally well as wrap-around solutions.
The temperature range of -30 to 90ºC makes silver-coated fabrics suitable for various environments, while specialized options like Conduct-O-Knit provide dedicated EMI shielding through its knitted wire mesh construction.
Foam-Based EMI Protection
Foam-based EMI solutions stand out as versatile shielding materials that combine lightweight properties with effective electromagnetic protection. You'll find these materials are typically fabricated using polyurethane foam with metal plating like copper or nickel, or they're enhanced with carbon-based nanoparticles for improved conductivity. The incorporation of multi-walled carbon nanotubes through volume exclusion effect creates an efficient bi-conductive network.
When you're selecting foam-based EMI protection, you'll notice impressive electrical conductivity ratings of up to 2799.8 S m^−1 in specialized composites like Ni@MF/CNT/TSM/PDMS. These materials can achieve shielding effectiveness up to 58 dB while maintaining low density around 0.28 g/cm^3, making them ideal for weight-sensitive applications.
You can count on foam-based solutions to provide absorption-dominant shielding, which reduces secondary electromagnetic pollution. They're particularly useful when you need materials that can withstand soft compression forces and offer flexibility.
The materials' performance can be fine-tuned by adjusting template characteristics and incorporating hybrid fillers. When you're implementing these solutions, you'll need to evaluate environmental factors like water resistance and guarantee proper sealing. The selection of metal plating or conductive fillers will directly impact your EMI shielding effectiveness.
EMI Protection Best Practices
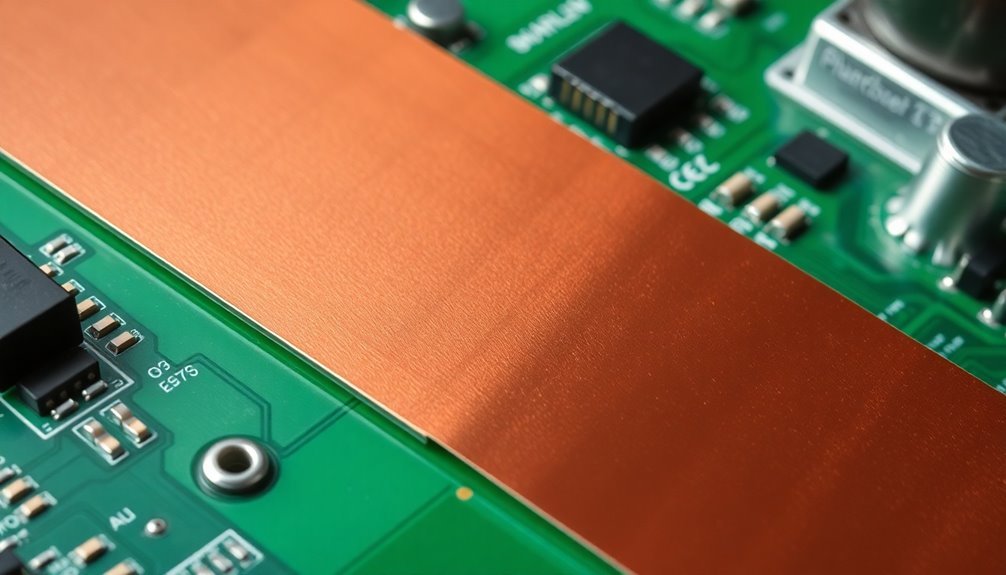
Effective EMI protection practices are essential for maintaining the integrity and reliability of circuit board designs. You'll need to implement several key strategies to guarantee your circuit boards remain protected from electromagnetic interference. Start by carefully considering your component placement and trace routing to minimize potential noise coupling between different sections of your board. Simulation tools can help validate your EMI protection strategies before physical implementation.
Practice | Implementation |
---|---|
Grounding | Use solid ground planes and low-impedance paths |
Shielding | Apply conductive tapes and metalized vias strategically |
Filtering | Incorporate ferrite beads and decoupling capacitors |
Your PCB stackup design plays a vital role in EMI protection. You'll want to include dedicated power and ground planes while maintaining proper impedance control throughout your board. Don't forget to partition your analog and digital sections effectively to prevent unwanted interference. When selecting materials, opt for those with low dielectric constants and loss tangents, especially for high-frequency applications. Remember to implement thorough decoupling strategies using appropriate capacitors to stabilize power supply voltages and reduce noise. Consider using shielding cans or conductive coatings in particularly sensitive areas, and guarantee your metalized vias create effective grounding paths throughout the board.
Temperature Performance and Durability
Beyond EMI protection, understanding the temperature performance and durability of conductive tapes will shape your PCB design success. When you're working with high-temperature applications, you'll need specialized tapes like polyimide that can withstand lead-free soldering conditions. Products like PPI 701 excel at protecting gold contacts during wave soldering while offering flame-retardant properties.
You'll find that copper tapes serve dual purposes in thermal management. They're exceptional heat conductors, performing about 1,000 times better than plastic or air, making them ideal for high-power circuit applications. You can optimize their layout to maximize heat dissipation in your designs. The low parasitic properties of copper tape make it particularly suitable for demanding high-power switching regulator circuits.
However, you must evaluate durability factors carefully. Copper tapes can be fragile and may crack when folded repeatedly. While they offer excellent chemical resistance, their longevity varies based on environmental exposure.
If you're designing for harsh environments or applications with significant mechanical stress, you might want to evaluate board-level shields instead of adhesive tapes. Remember to test your chosen tape's stability under your specific operational conditions, as temperature fluctuations and humidity can impact its long-term performance and adhesion strength.
Adhesive Strength Considerations
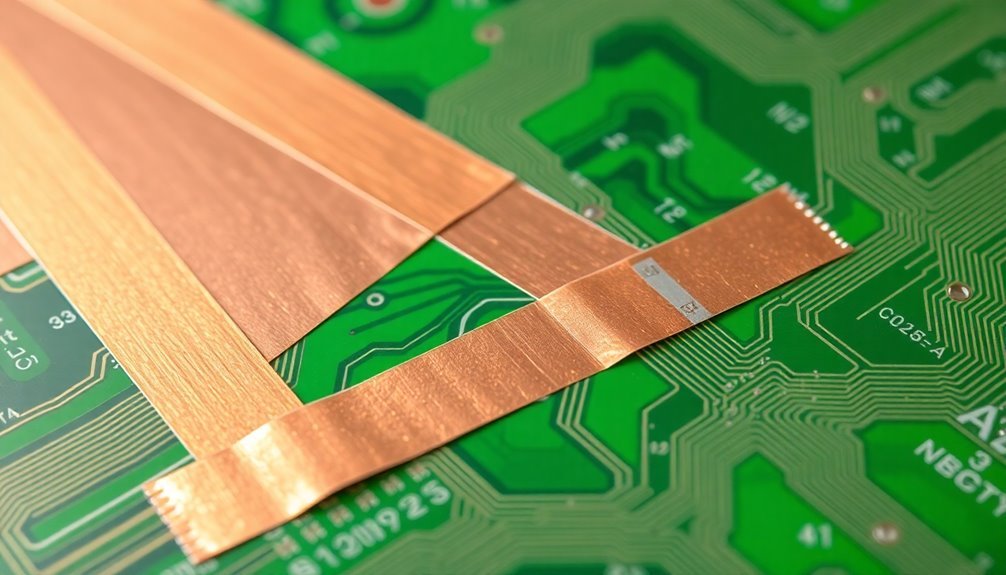
For ideal long-term bond performance, you'll need to match your conductive tape's adhesive strength to your circuit board's specific requirements and environmental conditions.
Your surface preparation methods, including cleaning with isopropyl alcohol and ensuring proper temperature during application, will substantially impact the tape's adhesive strength over time.
Proper pressure application and curing time are also essential for achieving maximum adhesion, especially in applications where thermal cycling or mechanical stress may occur.
Long-Term Bond Performance
Three critical aspects define long-term bond performance in conductive tapes: adhesive strength, environmental resilience, and material stability. Your choice of conductive tape must deliver robust adhesion while withstanding various environmental challenges to guarantee lasting circuit board protection.
You'll need to evaluate how temperature fluctuations affect your tape's performance, as thermal shock can reduce bond strength by up to 50%. However, you can benefit from controlled heat aging, which can increase average bond strength by 10-20%.
When selecting a tape, prioritize products with high thermal stability and chemical resistance.
For demanding applications like aerospace or automotive manufacturing, you'll want to choose tapes with specific features like anisotropic conductivity and low outgassing properties. The 3M 9703, for example, offers Z-axis conductivity while maintaining XY-axis insulation, preventing unwanted short circuits.
Don't overlook the impact of humidity and moisture exposure, as these factors can markedly degrade adhesive properties over time. In applications requiring exceptional reliability, you might need to implement additional mechanical reinforcement like clamping to enhance the tape's long-term bond stability.
Optimal Surface Prep Methods
Proper surface preparation stands as the cornerstone of achieving maximum adhesive strength with conductive tapes.
You'll need to begin with thorough cleaning using a 50-70% isopropyl alcohol and water mixture to remove surface contaminants. For circuit boards with heavy residues, start with a degreaser before the IPA treatment.
Surface abrasion can substantially improve your bond strength by increasing the contact area and removing oxidation. However, you'll want to be careful not to damage delicate circuit components. When you're working with copper-containing components, pay special attention as these may require specific preparation methods.
You should apply adhesion promoters or primers when working with challenging surfaces like certain plastics or painted areas. These pre-treatments can dramatically improve both initial tack and long-term bond strength.
Remember to maintain temperature control during application, as thermal conditions can affect your adhesive performance.
When applying the conductive tape, use firm, consistent pressure (at least 15 psi) to guarantee proper contact. You'll achieve the best results by using clean tools and implementing a uniform roll-down technique.
Consider the environmental factors in your application area, as humidity and temperature fluctuations can impact long-term adhesive performance.
Application Methods and Techniques
Successful conductive tape application begins with meticulous surface preparation and proven installation techniques. You'll need to start by cleaning the surface thoroughly with isopropyl alcohol and allowing it to dry completely before proceeding with any tape application.
When you're ready to apply the tape, start by partially peeling back the release liner from one end. This allows you to carefully align the tape while maintaining control over the application process.
You'll want to gradually unroll the tape, pressing down firmly as you go to prevent any air pockets or wrinkles from forming. Using a silicone roller, apply consistent pressure to guarantee maximum surface contact and ideal electrical conductivity.
At corners and joints, overlap the tape by at least 1/2 inch to maintain continuous conductive paths. Don't stretch the tape during application, as this can compromise its conductive properties.
When cutting the tape, use sharp scissors rather than tearing to preserve the tape's structural integrity. After installation, test the tape's conductivity to verify it meets your requirements, and regularly inspect for any signs of wear or damage that could affect its shielding performance.
Cost Analysis of Shielding Options
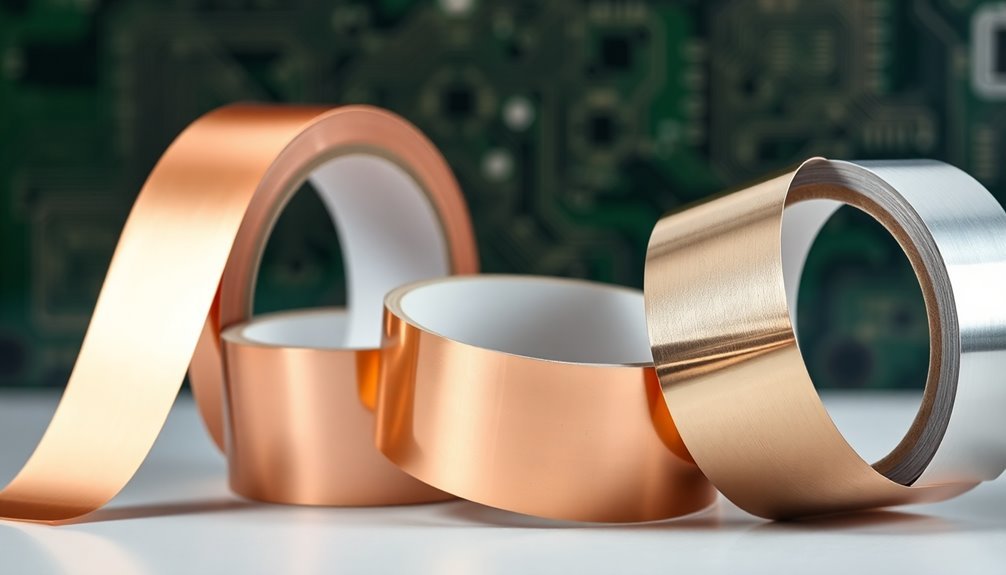
Understanding the cost implications of different shielding options helps you make informed decisions about your circuit board protection. While high-performance conductive adhesive tapes using silver, copper, or carbon nanotubes offer excellent protection, they'll impact your budget more substantially than aluminum-based alternatives.
Material selection greatly influences your overall costs. Copper foil tapes provide superior conductivity but come at a premium, while aluminum tapes offer a cost-effective solution without sacrificing shielding effectiveness.
The manufacturing process also affects pricing – achieving the right balance between conductivity and adhesion requires complex techniques that drive up production costs.
However, you can offset these initial investments through reduced installation and long-term maintenance costs. Conductive tapes are easy to apply, requiring minimal technical expertise, and they'll protect your devices from EMI damage, extending their lifespan.
When you consider that EMI-related failures can lead to costly repairs or replacements, investing in quality shielding solutions becomes more economical. For temperature-sensitive components, pressure-sensitive adhesive tapes offer a practical solution that's both cost-effective and reliable, minimizing future maintenance expenses and downtime.
Safety Standards and Compliance
For circuit board protection, safety standards and compliance requirements form the backbone of reliable PCB design. When selecting conductive tapes, you'll need to verify they meet essential certifications like UL 796 and UL 94 for fire resistance and electrical safety. These standards verify that your materials can withstand electrical stress and prevent fire hazards.
You must consider proper insulation and coating requirements outlined in UL 60950-1, which allows for reduced distances in functional isolation as long as you've verified them through electric strength tests.
For enhanced reliability, you'll want to implement a 25-micron nominal hole plating and specify appropriate soldermask thickness to protect against harsh environments.
To maintain compliance, you'll need to conduct regular audits and testing of your PCB components, including conductive tapes. Make sure you're using flame-retardant materials that meet IPC-4101 specifications and follow CAN/CSA-C22.2 guidelines for polymeric materials.
Remember that effective grounding techniques and proper heat dissipation are vital when applying conductive tapes. By adhering to IPC Class 3 standards or higher, you'll guarantee your circuit board protection meets the most stringent safety requirements for extreme conditions.
Market Leading Conductive Products
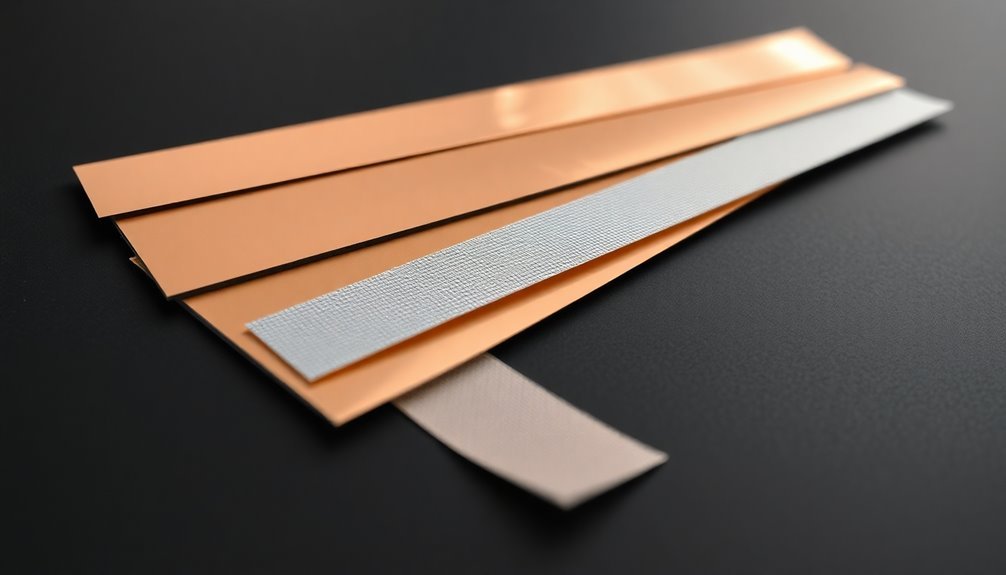
Now that safety standards are established, let's examine today's leading conductive tape products. 3M dominates the market with several high-performance options, including the 3304BC-S Ni/Cu nonwoven foil-backed tape, which offers superior EMI shielding and grounding capabilities.
You'll find specialized solutions like the 3M 9707, an adhesive transfer tape loaded with silver particles that delivers exceptional thermal conductivity and XYZ conduction paths.
The 9711S Series features a double-sided conductive adhesive on a Ni/Cu PET woven base, while the 9701 offers medium adhesion with excellent conformability for challenging applications.
These products serve multiple functions in electronics manufacturing. You can use them for component bonding, EMI shielding, and circuit protection across various frequencies.
They're particularly valuable in medical devices, automotive systems, and aerospace applications where traditional soldering isn't practical. The tapes' die-cutting capability lets you customize sizes and shapes to match your specific requirements.
For maximum flexibility in your design process, you'll appreciate these tapes' thin profiles and light weight. They provide reliable electrical connections while maintaining mechanical flexibility, making them ideal alternatives to conventional soldering methods.
Frequently Asked Questions
Can Conductive Tapes Be Recycled or Disposed of Safely?
You can't easily recycle most conductive tapes due to their mixed materials. However, you'll find that high-temperature tapes can be recycled, and repulpable tapes will disintegrate safely during paper recycling processes.
How Long Does Conductive Tape Remain Effective After Initial Application?
You'll get 1-5 years of effective performance from properly applied conductive tape, but it's heavily dependent on environmental conditions, maintenance, and usage patterns. Regular inspections will help you monitor its effectiveness over time.
Will Conductive Tape Interfere With Wireless Signals From Nearby Devices?
Yes, conductive tape will partially block wireless signals from nearby devices. That's actually one of its main purposes – you'll notice reduced WiFi, Bluetooth, and cellular signals in areas where you've applied the tape.
Can Conductive Tape Be Removed and Reapplied Multiple Times?
You shouldn't reapply conductive tape multiple times. Each reapplication weakens the adhesive, risks tearing the tape, and can damage your circuit board. It's best to plan carefully and apply it once.
Does Humidity or Moisture Affect the Conductivity of Shielding Tapes?
Yes, humidity and moisture can substantially affect your shielding tape's conductivity. You'll notice decreased effectiveness as moisture compromises the adhesive, causes oxidation, and degrades conductive particles. It's best to store them in dry conditions.
In Summary
You'll find that choosing the right conductive tape is essential for protecting your circuit boards. Consider durability, adhesive strength, and EMI shielding capabilities when making your selection. Remember to follow proper application techniques and verify compliance with safety standards. While cost matters, don't compromise on quality – investing in premium conductive tapes will save you money on repairs and replacements in the long run.
Leave a Reply