Always package electronics in anti-static bags that meet Mil-B-81705 standards and use static shielding materials with three-layer protection. Ground yourself with an ESD wrist strap before handling components and wear static-dissipative gloves during packaging. Keep your workspace's humidity between 40-60% to prevent static buildup. Use ESD-safe tools and avoid direct contact with sensitive parts. Test your static shielding equipment regularly with proper meters. Include desiccant packets and humidity indicators in packages, and select appropriate static-dissipative storage solutions. Store items in ESD cabinets for protection, and always check component sensitivity ratings. These foundational steps will help you master the complete spectrum of static-control shipping practices.
Choose Anti-Static Packaging Materials
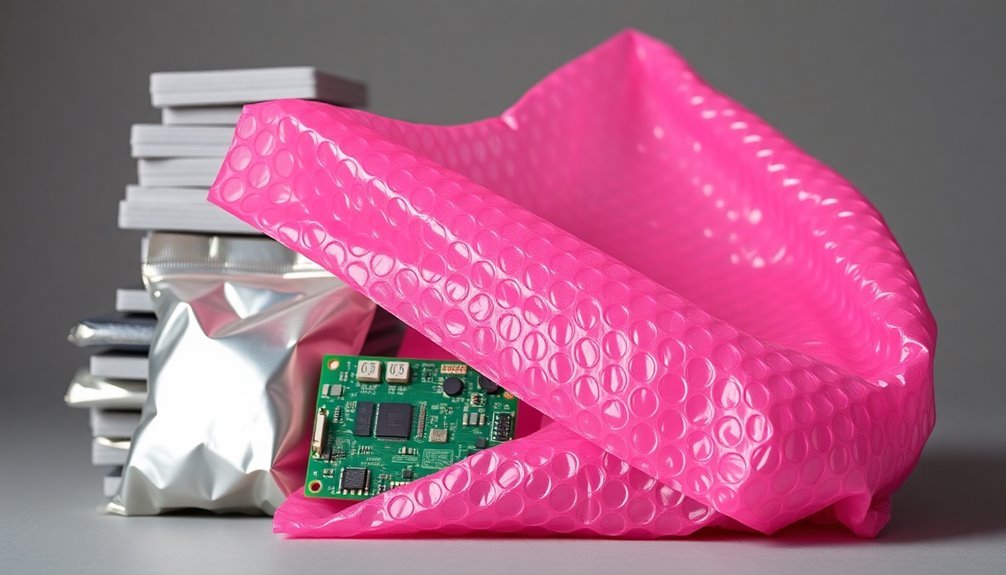
Static-control packaging materials form your first line of defense against damaging electrostatic discharge when shipping electronics. You'll need to select appropriate anti-static bags or foam inserts specifically engineered for electronic components. These materials are manufactured from amine-free static protective polyethylene that effectively dissipates and prevents electrical charge buildup. Our recommended bags feature a 70 micron thickness for reliable protection during shipping and handling.
When choosing anti-static bags, look for products that meet Mil-B-81705 requirements and are made from 100% virgin, recyclable materials. You'll find options in 2 Mil, 4 Mil, and 6 Mil thicknesses to suit different shipping needs.
For maximum protection of sensitive items like circuit boards, hard drives, GPUs, and CPUs, consider using static shielding bags that create a Faraday cage effect.
Remember that anti-static materials have a limited shelf life, so you'll need to replace them periodically. When handling components, verify you're properly grounded and following ESD procedures.
While anti-static bags work well for short-term storage in controlled environments, you might need more robust static-shielding containers for long-distance shipping or challenging conditions. Choose your packaging based on your specific component requirements and shipping circumstances.
Properly Ground Your Workspace
In a properly grounded workspace, you'll need to establish a thorough grounding system that connects all equipment, work surfaces, and personnel to a common ground point.
Start by identifying key areas that require grounding, including your packing stations, work benches, and shipping centers. Regularly evaluate and maintain the ESD grounding system to ensure consistent protection. Connect your common ground point to an electrical grounding conductor, typically through an AC ground or third wire electrical connection.
You'll want to implement specific ESD grounding methods to protect your electronic components. Use ESD wrist straps connected to unpainted surfaces or grounded workstations, and install ESD mats to eliminate static electricity through electrical bonding.
If you're working at standing stations, incorporate shoe grounders to maintain consistent grounding with the facility.
Make sure you connect all work surfaces to the common point ground, which should be clearly marked with the ANSI/ESD S8.1 symbol.
Check that your total system resistance, including personnel, garments, and grounding cords, stays below 35 megohms. Bond any auxiliary grounds to your equipment grounding conductor to minimize potential differences and maintain consistent protection throughout your workspace.
Handle Components With ESD Gloves

You'll need to wear ESD-safe gloves whenever you're directly handling sensitive electronic components or working in static-controlled areas.
For maximum protection, choose gloves made from dissipative or conductive materials that meet ASTM D 257 specifications and have surface resistivity less than 10^5 OHMS/SQ.
Nitrile ESD-safe gloves offer excellent protection while maintaining the tactile sensitivity you need for precise handling of electronic components. These gloves are treated with carbon to safely dissipate static charges that could damage delicate electronics.
When Gloves Are Required
Electronics' most sensitive components demand proper handling with ESD gloves in specific situations. You'll need to wear ESD gloves whenever you're handling components directly, especially when working with circuit boards or touching pins and leads. Don't forget that gloves must be paired with a properly grounded wrist strap for maximum protection against static discharge.
Situation | Gloves Required? | Additional Protection |
---|---|---|
Direct component handling | Yes | Wrist strap |
Circuit board assembly | Yes | Anti-static mat |
Pin/lead contact | Yes | Grounding point |
EPA work | Yes | ESD smock |
Component transport | Yes | Anti-static containers |
When you're working in static-controlled areas (EPA), you'll need to maintain consistent protection by wearing both gloves and appropriate dissipative clothing. Make sure you're using conductive or dissipative gloves that meet ANSI/ESD S20.20 and IEC 61340-5-1 standards. You should also store your ESD-sensitive components in anti-static bags and containers when they're not being handled. Remember to keep your workstation clean and free of static-inducing materials like plastic, foam, or vinyl that could compromise your ESD protection measures. A comprehensive ESD Control Program Plan should guide all handling procedures to ensure consistent protection of sensitive components.
Best Glove Material Types
Selecting the right ESD glove material directly impacts your component handling safety. While latex gloves are common and cost-effective, they're not suitable for static-sensitive electronics due to their insulative properties and high tribocharging characteristics. You'll want to avoid them, especially if you're handling delicate components.
Nitrile gloves are your best choice for ESD protection. They're inherently anti-static, extremely puncture-resistant, and suitable for all workers, including those with latex allergies. You'll find their dissipative properties particularly effective, though their performance can vary based on surface contamination. Always remember to use them with a grounding wrist strap for optimal protection.
If you're working in a cleanroom or laboratory environment, consider using vinyl gloves. They're suitable for workers with latex allergies, but keep in mind they're less durable than nitrile and can contribute to contamination issues due to high ionic residues.
For long-term cost savings, fabric gloves offer a reusable option. However, if you choose neoprene gloves, be aware that their inner coating might compromise ESD performance.
Whatever material you select, make certain it meets ESD certification standards like EN 1149-1:2006, and always consult manufacturer guidelines for your specific application.
Test Static Shielding Equipment
For reliable static protection, testing static shielding equipment requires specific tools and standardized procedures. You'll need an electrostatic fieldmeter, a 5-pound probe, resistance meters, and a 200-MHz oscilloscope to conduct thorough tests that meet ANSI/ESD standards.
When testing your shielding materials, you must evaluate them at both 12% and 50% relative humidity levels. Start by measuring surface and volume resistance using the 5-pound probe and resistance meter, ensuring readings stay below 1.0 x 10^11 Ω. Next, perform electrostatic decay tests with a 5kV discharge, confirming decay occurs within 2.0 seconds. The test must include 1kV HBM discharge measurements to assess energy penetration through shielding materials.
Test Type | Equipment Needed | Acceptable Range |
---|---|---|
Surface Resistance | 5-lb probe, meter | <1.0 x 10^11 O |
Volume Resistance | Resistance meter | <1.0 x 10^11 O |
Electrostatic Decay | Fieldmeter | <2.0 seconds |
Charge Retention | Faraday cup | <1.0 nC |
Energy Penetration | Capacitive probe | <20 nJ |
Don't forget to use a Faraday cup for charge retention measurements, which shouldn't exceed 1.0 nC. Your final check should measure energy penetration using a capacitive probe sensor, ensuring it stays below 20 nJ for adequate protection.
Avoid Direct Contact With Electronics
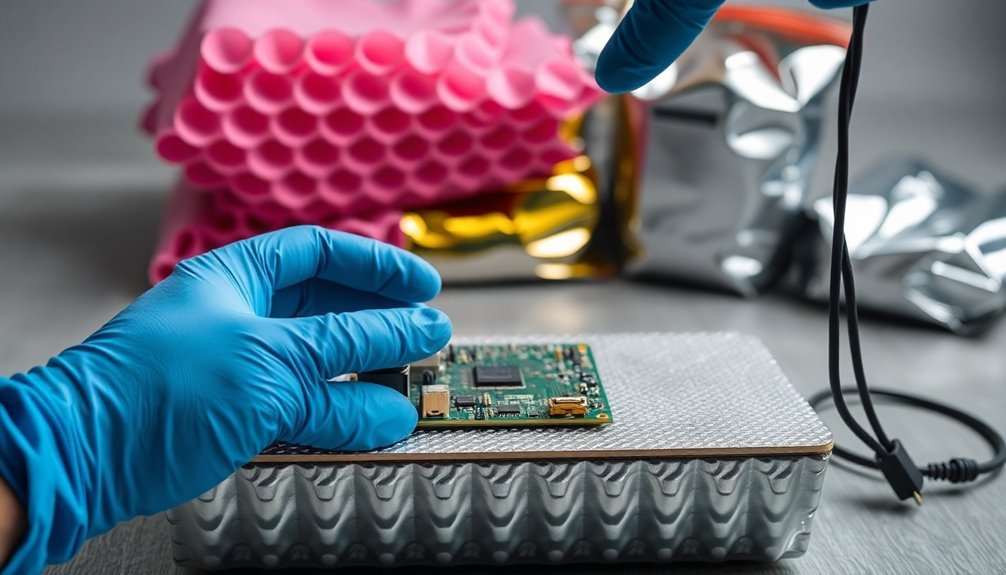
When handling electronic components, you'll need to wear clean static-control gloves to prevent damaging static discharge from your hands.
You must properly ground your workstation using appropriate static-control equipment before beginning any electronics handling.
Keep metal tools away from direct contact with electronic components, as they can transfer harmful static charges and potentially cause permanent damage. Using anti-static wrapping materials provides an additional layer of protection against electrostatic discharge during preparation for shipping.
Use Clean Gloved Hands
To properly handle electronics during shipping preparation, always protect them with specialized ESD gloves. These gloves are made from carbonized cotton or conductive polyester and create a low-resistance barrier that shields sensitive components from static electricity damage.
You'll need to make certain you're using fresh gloves for each handling session to prevent cross-contamination.
When cleaning electronics before shipping, you'll want to pair your ESD gloves with appropriate cleaning materials. Use a microfiber cloth slightly dampened with 70% isopropyl alcohol solution, but don't spray the solution directly onto the devices. Make sure you let all surfaces air-dry completely before packaging.
Your gloved hands act as a Faraday Cage, protecting components from static buildup that could otherwise cause malfunctions or complete failures. Without proper ESD protection, the natural oils and moisture from bare hands can damage sensitive electronics.
Remember that even minor static discharge can compromise electronic components, so don't skip this vital step in your shipping preparation process. If you're handling multiple items, change your gloves between devices to maintain cleanliness and prevent any transfer of contaminants.
Ground Your Work Station
A properly grounded workstation forms the foundation of safe electronics handling during shipping preparation. Start by installing an anti-static floor mat that meets ANSI/ESD S4.1 standards, featuring two-ply nitrile rubber with a static dissipative top surface and conductive bottom layer.
Connect your mat to a common point ground using appropriate grounding cables.
You'll need to wear a conductive wrist strap with a 6-foot coil cord and alligator clip, guaranteeing it's connected to the same common point ground as your floor mat. Make sure your grounding cables include a 1 meg ohm resistor to prevent overcharge and use secure connections like #10 ring terminals.
Create an Electrostatic Protective Area (EPA) by incorporating ESD-safe workbenches alongside your anti-static floor mats and grounding equipment. Keep all materials within your EPA either non-conductive or properly grounded.
Don't forget to test your equipment regularly – both wrist straps and floor mats need consistent inspection to maintain their static-control effectiveness. Remember to secure all grounding connections through a common point that ties into an outlet or earth ground, and guarantee your cables are long enough to reach your grounding points comfortably.
Avoid Metal Tool Contact
Every electronic component requires careful handling to prevent static discharge damage. When working with electronic components, you'll need to use specially designed insulated tools to avoid direct metal contact that can cause static discharge. These tools protect both you and the sensitive electronics from potential ESD damage.
Tool Type | Purpose | ESD Protection Feature |
---|---|---|
Insulated Screwdrivers | Component removal/installation | Non-conductive handle coating |
Anti-static Tweezers | Small part handling | Static-dissipative materials |
Insulated Pliers | Wire manipulation | Protective grip coating |
ESD-safe Probes | Circuit testing | Resistance-controlled tips |
Static-free Cutters | Wire trimming | Grounded handles |
You'll want to pair your insulated tools with other ESD protection measures like anti-static wrist straps and gloves. Make sure you're properly grounded before handling any components, and always store unused parts in anti-static bags or containers. When you're working on electronics, keep metal objects away from the workspace and use static-dissipative mats on your work surface. Remember that proper tool selection isn't just about functionality – it's vital for protecting your electronic components from costly ESD damage.
Layer Multiple Static Protection Barriers
The most effective defense against electrostatic discharge (ESD) relies on multiple protective barriers working together. You'll need to combine different types of static protection to create a thorough shield for your electronic components.
Start with static shielding bags that feature three essential layers: an inner static dissipative polyethylene layer, a middle conductive layer made of carbon or aluminum for grounding charges, and an outer static dissipative polyester coating.
For additional protection, use conductive component boxes when you're shipping multiple items, as they'll guard against both static and physical damage.
Don't rely on anti-static bags alone, as they only prevent static buildup but won't protect against ESD. Instead, incorporate specialized materials like carbon-loaded plastics and metalized films that actively dissipate static electricity.
For handling trays and tubes, you'll want to use static dissipative polymers with surface resistivity between 10^6 to 10^11 ohms/square.
Remember to match your protection level to your components' sensitivity. For complex SMD components, use specific packaging solutions like component reels.
This layered approach won't just protect against immediate damage – it'll also prevent latent issues that could surface later.
Maintain Proper Humidity Levels
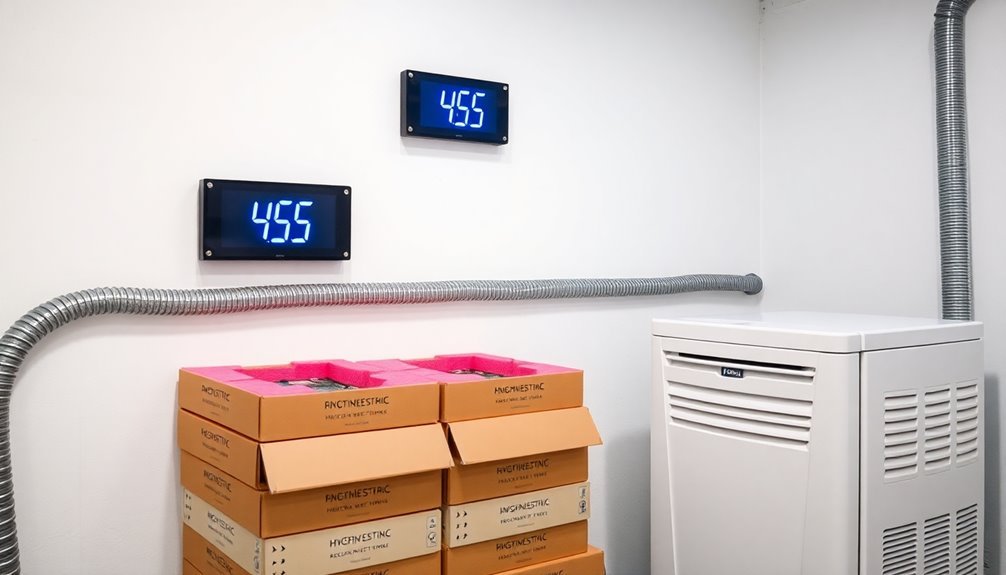
You'll need to closely monitor your storage area's humidity levels using reliable measurement tools to maintain the ideal 40-60% relative humidity range for electronics.
If your facility's air becomes too dry, you're risking increased static electricity buildup that can damage sensitive components.
Installing humidity monitoring systems and implementing regular checks will help you prevent costly ESD damage while ensuring ideal storage conditions for your electronic shipments.
Monitor Storage Area Conditions
Maintaining proper humidity levels stands as a critical factor in protecting electronic components during storage and shipping. You'll want to keep relative humidity (RH) between 30% and 70%, with 40% being the ideal target. Installing humidity sensors throughout your storage area helps you monitor and respond to fluctuations before they cause damage.
Condition | Risk | Prevention |
---|---|---|
Low Humidity (<30%) | ESD & Static Build-up | Use humidifiers & moisture control systems |
High Humidity (>70%) | Condensation & Corrosion | Install dehumidifiers & proper ventilation |
Temperature Fluctuation | Thermal Stress | Maintain stable temperature control |
Poor Monitoring | Undetected Issues | Install sensor networks & alerts |
To effectively monitor your storage conditions, you'll need to implement a thorough system that includes temperature and humidity sensors, regulatory mechanisms, and specialized storage solutions. Make sure your storage area remains clean and static-free, as dust and contaminants can compromise your humidity control efforts. Don't forget to regularly check and calibrate your monitoring equipment to guarantee accurate readings. When you maintain proper environmental conditions, you'll protect your electronics from moisture damage, static electricity, and material degradation while complying with industry standards.
Prevent Excessive Dry Air
Building on proper storage monitoring, preventing excessive dry air requires careful attention to humidity control. You'll need to maintain humidity levels between 40% and 80% to protect your electronics from static damage while avoiding moisture-related issues.
When humidity drops below 40%, you're at greater risk of static electricity buildup and electrostatic discharge that can harm sensitive components.
To protect against dry conditions, you'll want to implement several key measures. Install dehumidifiers in your storage areas and guarantee your climate control systems are working effectively.
When packaging electronics, use anti-static materials and static shielding bags to create protective barriers against ESD. Don't forget to include desiccant packets and humidity indicator cards to monitor moisture levels during transit.
For particularly sensitive items, consider using heat-sealed vapor-barrier bags with vacuum tools. You'll also want to utilize climate-controlled shipping containers and trailers when transporting electronics.
Remember that manufacturing environments typically require humidity levels between 30% and 70%, so adjust your controls based on specific component requirements and ambient conditions.
Regular maintenance of your climate control equipment will help guarantee consistent humidity levels and protect your electronics from static-related damage.
Humidity Measurement Tools Essential
Proper humidity measurement tools stand out as essential equipment for protecting electronics during shipping and storage. You'll find various options available, from digital electronic meters to therma-hygrometers, each offering accurate measurements across a 0-100% relative humidity range.
These tools help you maintain the ideal 30-70% RH levels needed to prevent damaging static discharge while protecting components from moisture-related issues.
Today's digital humidity measurement tools offer several advantages for shipping electronics:
- High accuracy ratings of +/-5% and fast 5-second sampling periods guarantee you're getting reliable, real-time data
- Battery-powered operation with auto-power-off features makes them practical for both warehouse and in-transit monitoring
- Compact dimensions (many under 8 inches long) allow for easy placement in shipping containers
- Additional features like dew point indication and min/max hold help you track environmental conditions throughout the shipping process
Select Static-Dissipative Storage Solutions
When shipping electronic components, selecting the right ESD storage solutions is crucial for protecting sensitive devices from static damage. You'll need to choose between anti-static and conductive storage options based on your specific requirements. While anti-static bins dissipate charges slowly, conductive bins offer quicker grounding capabilities.
Storage Type | Best For | Key Features |
---|---|---|
ESD Cabinets | Long-term storage | Steel frame, grounding connectors |
Anti-static Bins | Controlled dissipation | Slow charge transfer |
Conductive Bins | Quick grounding | Rapid charge transfer |
Static Shield Bags | Transport protection | Faraday cage effect |
ESD-safe Foam | Component cushioning | Permanent anti-static properties |
You'll want to guarantee your storage solutions comply with EN 61340-5-1 standards and can be vertically stacked for space efficiency. For shipping areas, combine ESD bins with static shielding bags that act as Faraday cages. When handling integrated circuits, semiconductors, or printed circuit boards, use storage solutions made from permanently ESD-safe materials. Remember that proper grounding is essential – your ESD cabinets should always be connected to earth leads for maximum protection.
Check Component Sensitivity Ratings
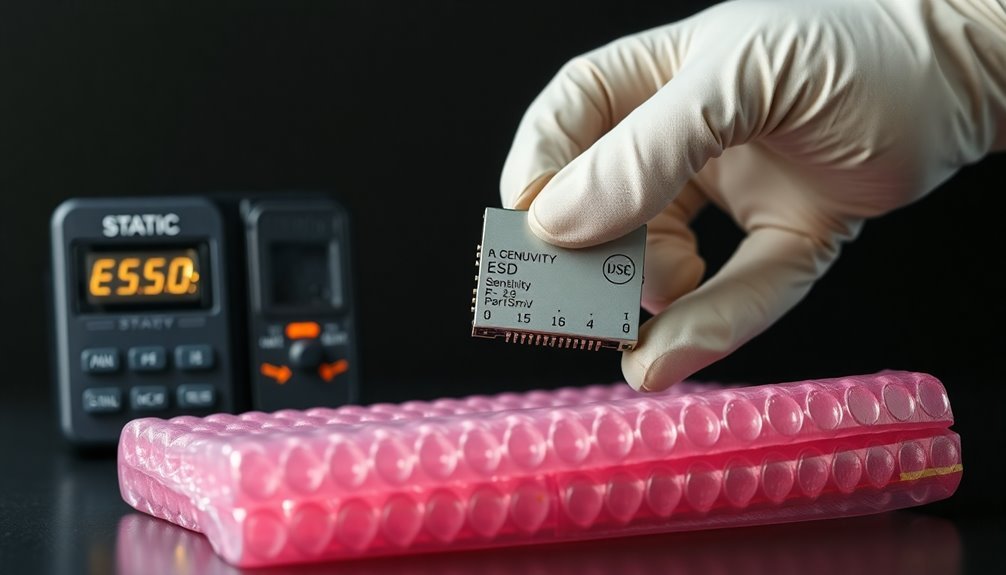
Understanding component sensitivity ratings forms the foundation of effective ESD protection during shipping. You'll need to identify the ESD sensitivity classifications for all components using the Human Body Model (HBM), Machine Model (MM), and Charged Device Model (CDM).
These classifications determine the level of protection required during transportation and guide your packaging decisions.
- HBM classifications range from 0Z (under 50 volts) to 3B (8000+ volts)
- CDM sensitivity levels span from C0A (below 125 volts) to C3 (1000+ volts)
- Lower voltage ratings require more stringent protection measures
- The most sensitive component dictates the overall protection level needed
When checking sensitivity ratings, you'll want to refer to standardized test results or documentation from manufacturers. If you can't find specific ratings, it's safer to assume a standard sensitivity level of HBM 100 volts.
Remember that you'll need to maintain closed product loops with consistent protection levels throughout the shipping process. Don't mix components with different sensitivity levels unless you're providing protection adequate for the most sensitive item. This approach guarantees you're implementing appropriate static control measures for all components in transit.
Master Safe Component Removal
Safe removal of electronic components calls for systematic attention to detail throughout the entire disassembly process. You'll need to start by detaching all removable parts that don't require tools, including power cords, chargers, and adapters.
Package each component individually using anti-static bags to protect against electrostatic discharge (ESD).
When you're handling batteries, you must treat them with special care. Remove them from the equipment, make certain they're no more than 30% charged, and pack them separately using non-metallic inner packaging. You'll also need to comply with federal regulations and carrier requirements for shipping lithium batteries.
For maximum protection, wrap each component in bubble wrap and secure it with high-quality tape. Don't forget to use waterproof bags or plastic sheeting to guard against moisture damage. Place desiccant bags in the package if you're shipping moisture-sensitive components.
Once you've packaged everything, test the box by gently shaking it to verify that nothing moves inside. Remember to label each part clearly so the recipient can easily identify and reassemble the components upon delivery.
Always balance your packages for consistent weight distribution to manage shipping costs effectively.
Frequently Asked Questions
How Long Do Anti-Static Bags Remain Effective After First Use?
You'll get superior protection from anti-static bags for about 5 years if stored properly, but regular use can reduce effectiveness sooner. You should replace them if they're crinkled, punctured, or fail resistance tests.
Can Static Protection Materials Be Reused for Multiple Shipments?
You can reuse some ESD materials like conductive and dissipative packaging if they're undamaged and properly inspected. However, you'll need to check manufacturer guidelines and test the materials before each reuse.
What Temperature Ranges Affect Static Control Packaging Performance?
You'll find that static control packaging performs best between 20-25°C. Extreme temperatures can harm the materials – avoid exposing them to conditions below -55°C or above 125°C to maintain their protective properties.
Should Batteries Be Packaged Separately From Other Electronic Components?
You should always package batteries separately from other electronic components to prevent short circuits. It's essential to use non-conductive inner packaging for each battery and keep them isolated from other devices.
How Do Different Climates Impact Static Control Requirements During Shipping?
You'll need stronger static protection in dry climates where static builds up easily. In humid areas, you'll face less static risk but must guard against moisture. Temperature extremes require additional protective measures during shipping.
In Summary
You've learned the vital steps to protect sensitive electronics during shipping. By following these static-control guidelines, you'll minimize the risk of ESD damage and guarantee your components arrive safely. Remember, it's not just about using the right materials – it's about creating a complete static-safe environment. Don't skip any steps, as proper ESD protection is essential for maintaining product quality and customer satisfaction.
Leave a Reply