When selecting anti-static packaging foam, you'll need to take into account both density and ESD protection levels. Higher-density foams (above 1.7 PCF) offer better durability and component protection, while lower-density options provide improved airflow. Pink anti-static foam works well for short-term storage of general electronics, whereas black conductive foam delivers superior protection for sensitive components. Your choice should factor in the foam's resistance values, ranging from conductive (10³-10⁵ ohms) to static dissipative (10⁸-10¹⁰ ohms). Environmental conditions like humidity and temperature also affect performance, making proper material selection vital for your specific application needs.
Understanding Foam Density Types
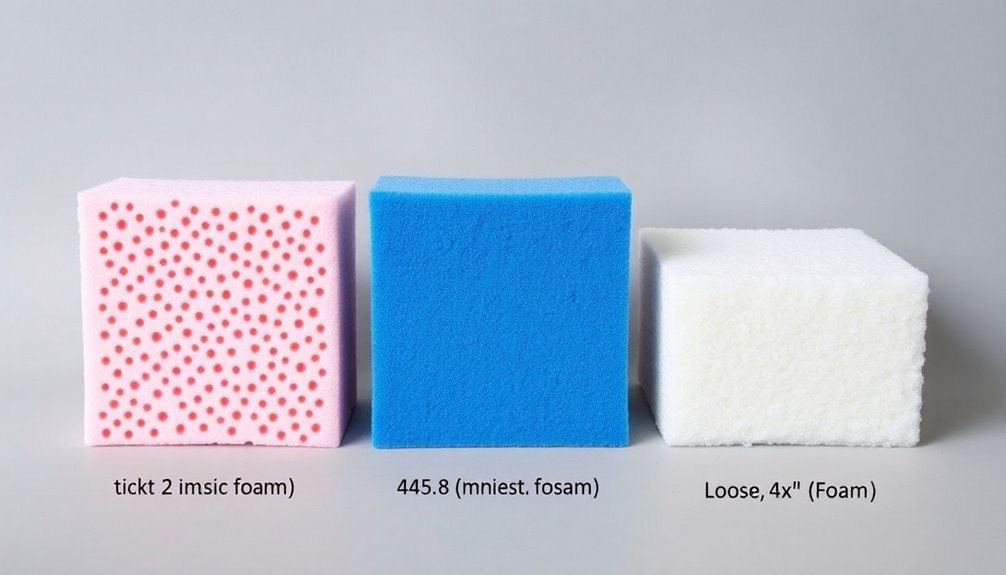
Understanding foam density is essential when selecting the right material for your needs. You'll find density measured in pounds per cubic foot (PCF), which is calculated by dividing a foam sample's weight by its volume.
When you're comparing different foam materials, remember that density ranges from 1.5 PCF to over 5 PCF, with higher numbers indicating greater density. Testing has shown that delicate items requiring 40-60 Gs of protection typically need specialized foam densities.
You'll encounter various foam types, each serving distinct purposes. Polyethylene foam offers versatility in color and density, making it ideal for packaging. If you're looking for a plush feel, polyurethane foam delivers flexibility and softness.
Cross-linked polyethylene foam works well for marketing materials, while expanded polyethylene foams can be either rigid or flexible based on their density.
When selecting foam density, you'll need to take into account three main categories: low-density (0.8-1.5 LB), medium-density (1.5-3.0 LB), and high-density (3.0-5.0 LB). Your choice should depend on factors like fragility, drop heights, and PSI requirements.
For instance, if you need foam for items requiring 0.1-0.3 PSI, you'll want to select 2 lb./ft³ polyurethane. Higher density foams typically offer greater durability and longer-lasting performance.
Anti-Static Protection Levels
Your choice between pink anti-static foam (10^6 – 10^9 Ω) and black conductive foam (10^3 – 10^5 Ω) depends on your specific ESD protection needs.
You'll find that pink foam offers controlled dissipation suitable for general electronics packaging, while black foam provides rapid charge dissipation for highly sensitive components.
When selecting foam materials for static protection, you'll need to match the foam's resistance value range to your application's requirements, considering whether you need conductive, dissipative, or basic anti-static properties. This approach mirrors how gradual charge bleed-off occurs in anti-static mats to prevent harmful accumulation.
Pink Vs Black Foam
Protective packaging manufacturers offer two main types of anti-static foam: pink and black, each serving distinct ESD protection needs.
Pink foam, made of anti-static polyethylene, provides surface resistance between 10^5 to 10^11 ohms and is ideal for short-term packaging solutions. The foam's closed cell structure provides excellent cushioning properties for sensitive components.
Black foam, composed of low-density conductive polyethylene, offers surface resistance of 1 x 10^3 to 1 x 10^9 ohms and suits long-term protection requirements.
You'll find that pink foam is more cost-effective for temporary applications, and you can easily customize it through die-cutting and laminating processes. However, it's crucial to highlight that pink foam's electrical properties deteriorate over time, and its color may yellow with age.
In contrast, black foam maintains its conductive properties and color stability throughout its lifetime.
When you're selecting between these materials, consider your specific application needs. If you're packaging ESD-sensitive devices for short periods, pink foam will serve your purposes well.
For permanent ESD protection or lead insertion applications, you'll want to choose black foam. Black foam also offers superior environmental stability, making it the preferred choice for challenging storage conditions.
Resistance Value Ranges
Protection Level | Resistance Range (ohms) |
---|---|
Conductive | 10³ to 10⁵ |
Anti-Static | 10⁶ to 10⁹ |
Static Dissipative | 10⁸ to 10¹⁰ |
Surface Specific | 10¹⁰ to 10¹² |
You'll find that conductive foams offer the highest level of ESD protection, with resistance values between 10³ to 10⁵ ohms. These materials are ideal when you're handling extremely sensitive components. Anti-static foams, with resistance ranges of 10⁶ to 10⁹ ohms, provide standard protection for most electronic components.
If you're working with moderately sensitive items, static dissipative foams (10⁸ to 10¹⁰ ohms) will meet your needs. Surface-specific resistance values typically range from 10¹⁰ to 10¹² ohms/cm, offering the most basic level of protection. Pink static dissipative foam balances protection and cushioning capabilities for various electronic applications. Each foam type complies with IEC/EN 61340-5 and ASTMD257-78 standards, ensuring you're getting reliable protection for your specific application.
Static Protection Classifications
Most electronic components require specific levels of static protection, which fall into distinct classifications based on their sensitivity and storage needs.
You'll find various packaging types designed to provide different levels of protection, from basic anti-static bags to advanced static shielding solutions.
For moderate protection, you can use anti-static packaging that prevents charge buildup during handling. The electronics industry loses approximately $5 billion annually due to ESD-related damage.
When you need higher protection levels, consider conductive or shielding packaging, which either conducts charges away from sensitive components or creates a Faraday Cage effect.
Dissipative packaging offers a middle ground by controlling the flow of static charges more gradually.
You'll need to match your packaging choice with your storage duration. While anti-static bags work well for short-term storage of less sensitive items, you should opt for static shielding bags with metal-in or metal-out construction for long-term storage of critical electronics.
In clean room environments, you'll want to use materials like Corriplast that resist contaminants.
For direct component protection, anti-static foams provide both cushioning and static control, making them ideal for circuit boards and computer chips.
Material Properties Explained
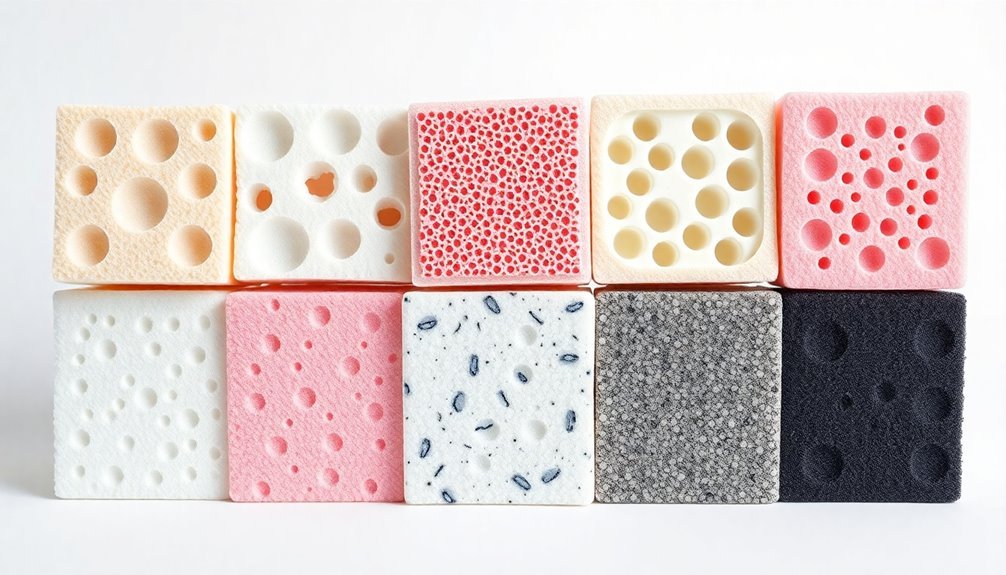
You'll find that foam density and compression strength aren't directly related, as a high-density foam can be soft while a low-density foam might be firm.
When selecting foam materials, you need to take into account both the density (measured in pounds per cubic foot) and the compression strength to determine the right protection level for your items. Anti-static polyethylene foam provides effective protection while preventing static electricity buildup during transport.
The foam's cell structure, whether closed or open, also plays a vital role in its performance, affecting properties like moisture resistance and cushioning ability.
Density vs. Compression Strength
Understanding the relationship between density and compression strength is fundamental when selecting foam materials for specific applications. While density measures the mass per unit volume, compression strength indicates a foam's ability to resist compression under load. You'll find that higher density generally correlates with higher compressive strength, though this isn't always the case.
When you're evaluating foam materials, you'll need to take into account both the ILD (Indentation Load Deflection) tests and density measurements. The ILD test measures firmness by determining the force needed to compress foam by 25%. Foam materials undergo flex fatigue testing to evaluate their long-term durability and performance.
The support factor (ratio of 65% to 25% ILD) ranges from 1.5 to 2.6, with higher numbers indicating better support. It's crucial to observe that firmness operates independently of density – you can have high-density foams that are soft and low-density foams that are firm.
For anti-static packaging applications, you'll want to balance these properties carefully. Dense foams offer better durability and retention of properties, making them suitable for heavier items, while less dense options work well for lighter, more delicate components.
The key is matching these characteristics to your specific packaging needs.
Closed vs. Open Cells
While density and compression strength inform foam selection, the cellular structure of foam materials plays an equally important role in determining their performance characteristics.
When comparing closed and open cell foams, you'll notice distinct differences in their properties and applications.
Closed cell foams feature sealed-off cells that provide superior moisture resistance and thermal insulation. You'll find them extensively used in automotive, marine, and aerospace applications where water resistance and durability are vital. With a typical density of 2.0 lb/ft³, these materials provide consistent performance across various applications.
Their high rigidity and excellent sealing efficiency make them ideal for protecting sensitive equipment and providing reliable cushioning, even with minimal compression.
Open cell foams, in contrast, have interconnected cells that allow air and moisture to pass through. You'll benefit from their flexibility and breathability in applications requiring air flow, though they're generally less durable than their closed cell counterparts.
While they can be manufactured at various densities, they don't offer the same level of moisture protection or thermal insulation.
When selecting between these options, consider your specific needs. Choose closed cell foam when you require moisture resistance, thermal insulation, and high durability.
Opt for open cell foam when breathability and flexibility are your primary concerns.
Selection Criteria for ESD Foam
When selecting ESD foam for electronic component protection, several critical factors must guide your decision-making process.
First, you'll need to evaluate the density requirements based on your application. Anti-static EVA foam at 85kg/m³ provides greater protection for heavier components, while PE foam at 45kg/m³ suits lighter items. ETHAFOAM Select Anti-Static, with its 29 kg/m³ density, offers a lighter alternative.
You should assess your ESD protection needs by considering your components' sensitivity levels. Test methods like EN 61340-5-1 will help you determine if you need conductive, static dissipative, or insulative materials. For instance, if you're working with components that require specific ESD protection, EPE foam's surface antistatic value of 10^8 to 10^11 might be suitable.
Don't forget to factor in environmental conditions such as humidity and temperature, as these can affect ESD performance. Calculate the PSI or static stress to guarantee proper cushioning.
If you're planning for returnable packaging, consider durability alongside ESD protection.
Finally, verify that your chosen foam meets all required specifications for conductivity, thickness, and cushioning performance to guarantee the best protection for your electronic components.
Performance in Different Environments
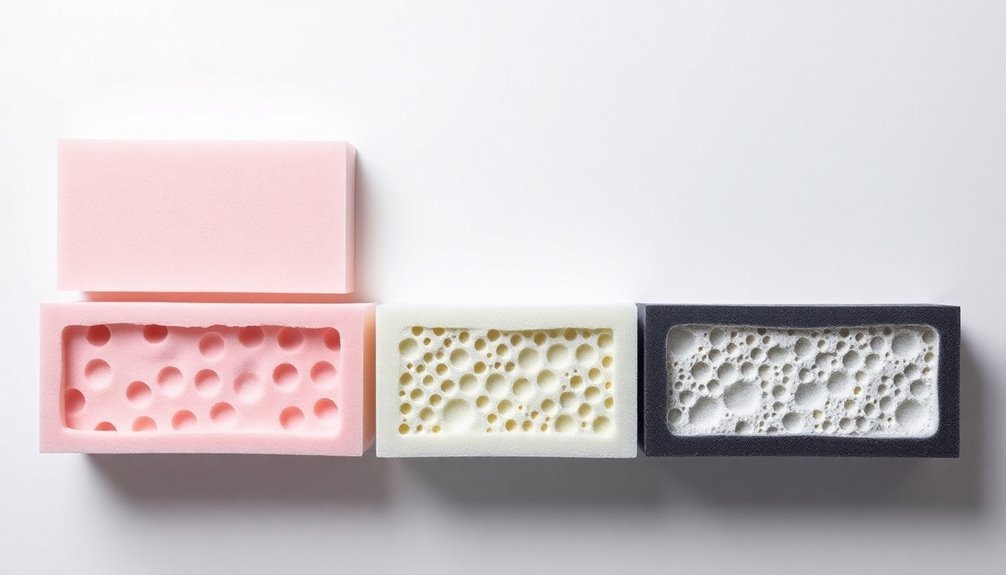
Throughout the lifespan of ESD foam packaging, environmental factors substantially impact its protective capabilities. You'll need to think about temperature ranges, humidity levels, physical stress, and electrostatic discharge properties when selecting the right foam density for your application.
For temperature considerations, most ESD foams work effectively between -20°C and 60°C. If you're working with extreme temperatures, you'll want to choose specialized formulations. PE foam offers superior heat resistance compared to EVA foam, while specific variants are available for cryogenic storage applications.
In humid environments, you'll want to select materials with low moisture absorption, such as PE foam, as high humidity can compromise ESD properties. You can also incorporate desiccants to maintain low humidity levels inside your packaging.
When it comes to physical stress, different foam densities offer varying levels of protection. PE foam provides higher compressive strength, while EVA and PU foams offer better flexibility for complex shapes.
The foam's ability to dissipate static charges varies too – conductive foams offer faster discharge rates than anti-static varieties, giving you options based on your specific protection needs.
Quality Standards and Testing
Testing labs and quality control facilities provide essential certification processes for ESD foam packaging. You'll need to certify that your materials meet ANSI/ESD STM11.11 standards, which require surface resistance between 10^6 and 10^9 ohms for proper static protection.
When selecting foam materials, verify they've passed MIL-STD 3010 for durability and ASTM F1249 for water vapor transmission testing.
For foam density verification, you'll want to rely on ASTM D3574 Test A, which calculates density from mass and volume measurements. If you're testing compression characteristics, use Test C with properly ventilated platens.
You should also check indentation hardness through Test B1 (IFD) and Test B2 (IRGL) to guarantee ideal protection for your components.
When selecting foam density, calculate the PSI requirements based on your item's specifications. You'll find that 2 lb./ft3 polyurethane works well for 0.1-0.3 PSI applications, while 4 lb./ft3 polyurethane suits 0.4-0.6 PSI needs.
For higher stress requirements of 0.7-1.0 PSI, consider 2 lb./ft3 polyethylene. Remember to verify that all materials meet FTMS 101C/4046 standards for corrosion resistance.
Frequently Asked Questions
Can Anti-Static Foam Lose Its Protective Properties Over Time?
Yes, your anti-static foam can lose its protective properties over time due to environmental factors, handling, chemical degradation, and repeated use. You'll need regular testing to verify it's still effective for ESD protection.
What Is the Recommended Storage Temperature Range for Anti-Static Foam?
You'll want to store your anti-static foam at room temperature, avoiding direct sunlight and extreme temperatures. While it's durable between -10°C and 85°C, room temperature storage guarantees best performance and longevity.
How Often Should Anti-Static Foam Packaging Be Replaced?
You'll need to replace your anti-static foam based on testing results, but typically every 2-3 years. Check regularly for degradation and test compliance with ESD standards to confirm it's still providing proper protection.
Can Anti-Static Foam Be Cleaned Without Compromising Its Protective Qualities?
Yes, you can clean anti-static foam safely by dry wiping or gentle vacuuming. Avoid chemical cleaners unless manufacturer-approved. It's best to stick with non-invasive methods to maintain the foam's protective anti-static properties.
Are There Environmental Disposal Guidelines Specific to Anti-Static Foam Materials?
You'll need to dispose of anti-static foam at licensed waste sites, following local hazardous waste regulations. You can recycle some types through specific programs, but PFAS-containing foams require special handling and reporting procedures.
In Summary
You've now got the knowledge to select the right anti-static foam density for your packaging needs. Remember to match your foam's properties with your electronic components' sensitivity levels, and don't forget to take into account environmental factors. When in doubt, opt for higher-density foams with verified ESD protection ratings. Keep testing standards in mind, and you'll guarantee your sensitive items remain safe during storage and transport.
Leave a Reply