When shipping electronics, you'll need either anti-static or conductive foam to protect against electrostatic discharge (ESD) damage. Anti-static foam, often pink in color, prevents static buildup through chemical treatment, while conductive foam creates a Faraday cage around your components. For delicate items like circuit boards, choose soft open-cell foam that won't scratch surfaces. Larger electronics benefit from rigid closed-cell foam's moisture resistance and impact protection. Your choice should factor in the item's sensitivity, size, and shipping conditions. Exploring foam density, custom solutions, and regulatory standards can help you make the best selection for your specific needs.
Understanding Electronics Foam Types
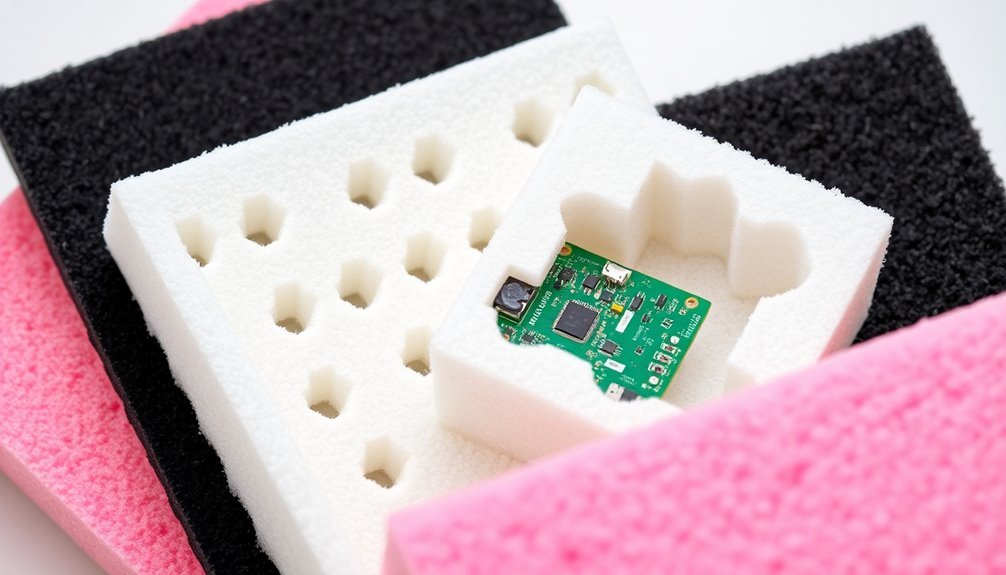
Electronics manufacturers rely on specialized foam materials to protect sensitive components during shipping and storage. The two main categories you'll encounter are open-cell and closed-cell foams, each serving distinct purposes in electronics protection.
Open-cell foam, like polyurethane, offers excellent cushioning for fragile components such as circuit boards and CPUs. You'll find it's lighter and softer, making it perfect for delicate items. The non-abrasive properties ensure electronic surfaces remain scratch-free during transit.
It's available in sheets or convoluted (egg crate) patterns and can be custom-molded to fit specific shapes.
Closed-cell foam, including cross-linked polyethylene, provides a more rigid and durable solution. You'll want to use this type for larger electronic items like computers and sound equipment, especially when moisture resistance is vital.
When it comes to static protection, you have three main options. Conductive foam contains carbon and acts as a Faraday cage, blocking electromagnetic fields.
Anti-static foam prevents static buildup through chemical treatment but doesn't provide full shielding.
Static dissipative foam offers a middle ground, allowing gradual discharge of static charges. Choose your foam type based on your specific static protection needs and the sensitivity of your electronic components.
Static Protection Requirements
Having examined foam types, let's focus on the specific requirements for static protection that you'll need to implement.
You'll need to guarantee your electronic components are protected against static charges that can occur through tribocharging (friction) during shipping. To meet EIA-541 standards, you must use approved anti-static materials like pink anti-static foam or carbon-filled conductive foam. These materials create a Faraday cage effect that shields sensitive electronics from damaging static charges. Regular ESD training procedures help ensure proper handling techniques are followed.
When packaging your electronics, you'll need to wrap each component individually in anti-static material. You should use static shielding bags or boxes for additional protection, especially for long-distance shipping.
Don't forget to check that your anti-static materials haven't degraded, as this can compromise their protective properties.
Remember that you must comply with specific carrier regulations, particularly when shipping items containing lithium batteries. These require non-metallic packaging and proper separation.
You'll also need to maintain proper documentation and labeling. If you're handling PCBs directly, guarantee you're fully grounded according to ESD safe handling procedures.
Source your anti-static packaging materials from reliable suppliers to maintain high protection standards.
Foam Density and Cushioning Properties
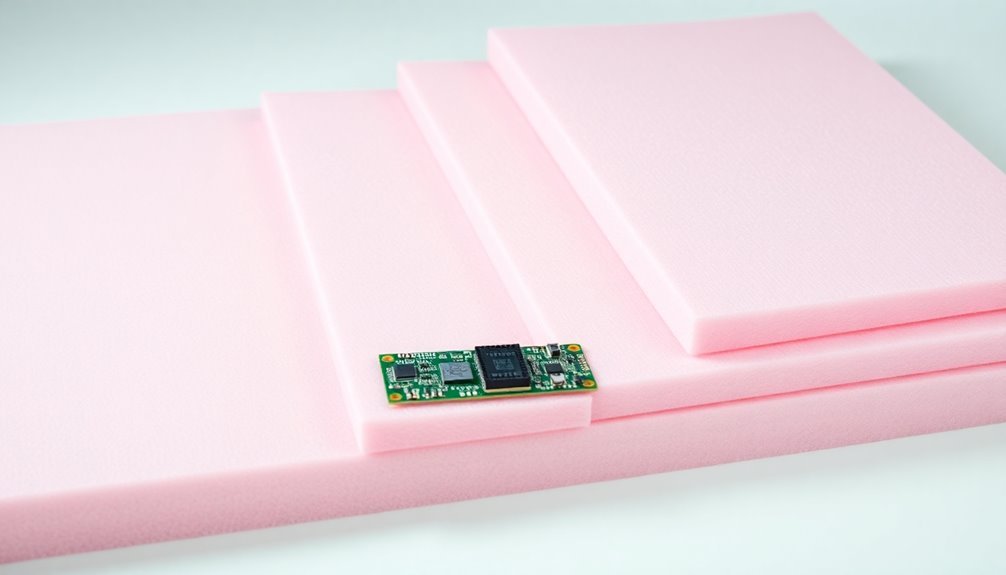
For successful electronics shipping, choosing the right foam density and cushioning properties is essential to preventing damage during transit. You'll find foam densities ranging from light 1.8 pcf ETHAFOAM to heavy 4.8-5.2 lbs conductive memory foam, each serving specific protective purposes.
For maximum protection, match the foam density to your electronic component's needs. Cross-linked polyethylene foam at 1.99 lbs density works well for most standard electronics, while sensitive components require higher-density conductive memory foam. The foam's thickness also plays a vital role in impact protection. Pure nitrogen gas is used to manufacture certain anti-static foams like Evazote, ensuring consistent quality and performance.
When selecting foam for your electronics shipping needs, consider these key cushioning properties:
- Shock absorption capabilities – closed-cell polyethylene and polyurethane foams excel at protecting against impacts
- Non-abrasive surfaces – prevents scratching of delicate components during transit
- Thermal management properties – helps maintain stable operating temperatures
Your choice should factor in both the item's weight and sensitivity. For small, delicate components, opt for open-cell polyurethane foam.
Larger electronic devices benefit from closed-cell cross-linked polyethylene foam's structural rigidity, while extremely fragile or expensive items require high-density conductive memory foam for maximum protection.
Custom Foam Solutions
When shipping valuable electronics, custom foam solutions offer unparalleled protection through precisely engineered designs. You'll find that manufacturers can create tailored packaging using materials like polyurethane, polyethylene, and expanded polystyrene foams, each cut precisely to match your device's contours. Fast production turnaround is available from dedicated manufacturing facilities.
You can choose between several specialized foam types based on your needs. Anti-static foam, treated with special agents, will protect against electrostatic discharge, while conductive foam with carbon content acts as a Faraday cage. For sensitive surfaces, non-abrasive foam prevents scratches and damage during transit.
Your custom foam solution can incorporate multiple layers or convoluted designs to maximize protection. Using water jet or CNC machines, manufacturers can create precise cuts that guarantee a snug fit for your electronics.
You'll benefit from reduced damage rates and fewer returns, which ultimately safeguards your brand reputation.
When ordering custom foam solutions, you can work with specialized manufacturers like Quality Foam or Wisconsin Foam Products. They'll help you select the right density, material type, and design features to match your specific electronic product's requirements. Some suppliers even offer eco-friendly options using recycled materials.
Regulatory Standards for Electronics Packaging
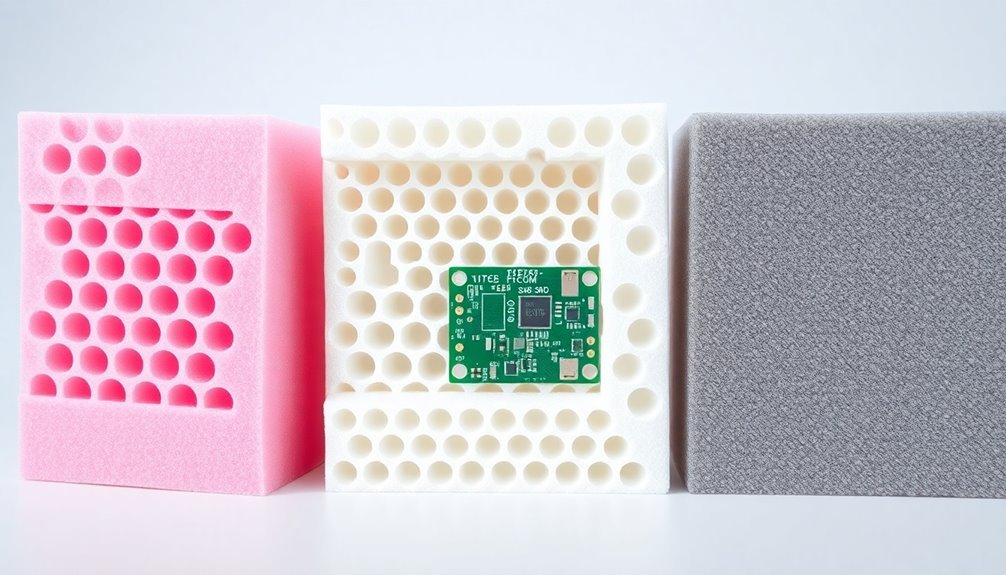
When shipping electronics with foam packaging, you'll need to comply with industry standards like NIGP 108 and EIA 625, which govern protective measures against damage, contamination, and electrostatic discharge.
Your foam materials must meet specific ESD protection requirements, including surface resistance specifications of 10^4-10^9 ohms and proper conductivity for sensitive components.
You'll also need to verify that your packaging passes ISTA certification testing and adheres to environmental regulations that limit heavy metals and mandate proper labeling for hazardous materials. Manufacturers must participate in Extended Producer Responsibility programs to ensure proper disposal and recycling of foam packaging materials.
Industry Safety Guidelines
Within the electronics shipping industry, strict regulatory standards govern the safe packaging and transport of sensitive components. You'll need to follow EIA-541 standards that specify requirements for ESD-sensitive items, including the use of anti-static and conductive materials that prevent damage during transit.
When selecting foam for electronics shipping, you must guarantee it meets these critical safety requirements:
- Surface resistance specifications for anti-static properties
- Carbon content requirements for conductive foam to create Faraday cage protection
- Non-abrasive material standards to protect delicate surfaces
You'll need to take into account both physical and environmental requirements in your packaging design. Custom foam inserts that precisely match product dimensions provide the most reliable protection during shipping. The foam you choose should match the item's size and weight – opt for open-cell foam for smaller components and closed-cell foam for heavier items.
For corrosion protection, you might need to incorporate VCI packaging solutions like bags or emitters.
Remember that your packaging must comply with environmental guidelines too. You should prioritize recyclable components and minimize single-use plastics wherever possible.
The packaging unit design must maximize space efficiency while maintaining proper protection, and you'll need to include detailed delivery documentation with every shipment.
Compliance Testing Requirements
Maintaining compliance with electronics packaging standards requires rigorous testing protocols and detailed documentation. You'll need to verify that your packaging materials meet EIA-541 standards for ESD-sensitive items and comply with global regulations like RoHS and REACH.
When selecting foam packaging, you must confirm it's made from non-static generating materials and doesn't contain ozone-depleting substances.
You'll need to maintain thorough documentation of your compliance testing, including supplier information, packing quantities, and production dates. Your foam packaging must be certified CFC-free and meet heavy metal concentration requirements.
If you're using returnable packaging, you must clearly identify these items and include proper handling instructions.
To meet environmental regulations, you should select foam materials that minimize environmental impact and support recyclability. You'll need to demonstrate that your packaging design considers waste reduction and meets Extended Producer Responsibility requirements.
Your documentation should include test results confirming that the foam packaging protects against handling hazards and meets all necessary safety standards. Remember to keep records of your design specifications and testing procedures to prove compliance during audits.
Environmental Factors During Transport
Shipping electronics safely requires careful management of several environmental threats that can compromise product integrity. During transport, your electronic components face risks from temperature fluctuations, moisture exposure, and static electricity buildup, making proper protective measures essential.
Temperature control is vital as extreme heat can warp components while cold conditions may cause cracking. You'll need foam solutions that maintain stable temperatures and provide real-time monitoring capabilities through integrated sensors. Climate-controlled vehicles are essential for maintaining consistent temperatures throughout the transportation process.
Humidity poses another significant challenge, as moisture can lead to corrosion and short circuits in delicate circuitry.
To protect against these environmental factors, you'll want to implement:
- Multi-layered foam packaging with varying densities to create thermal barriers
- Anti-static foam treatments that prevent electrostatic discharge damage
- Moisture-resistant closed-cell foams that block humidity penetration
Your foam packaging should incorporate ventilation features to prevent condensation while maintaining protective qualities. Consider using conductive foam materials that act as Faraday cages, blocking electromagnetic fields from reaching sensitive components.
When combined with dehumidification measures and proper climate control, these foam solutions make certain your electronics arrive safely at their destination.
Cost Versus Protection Analysis
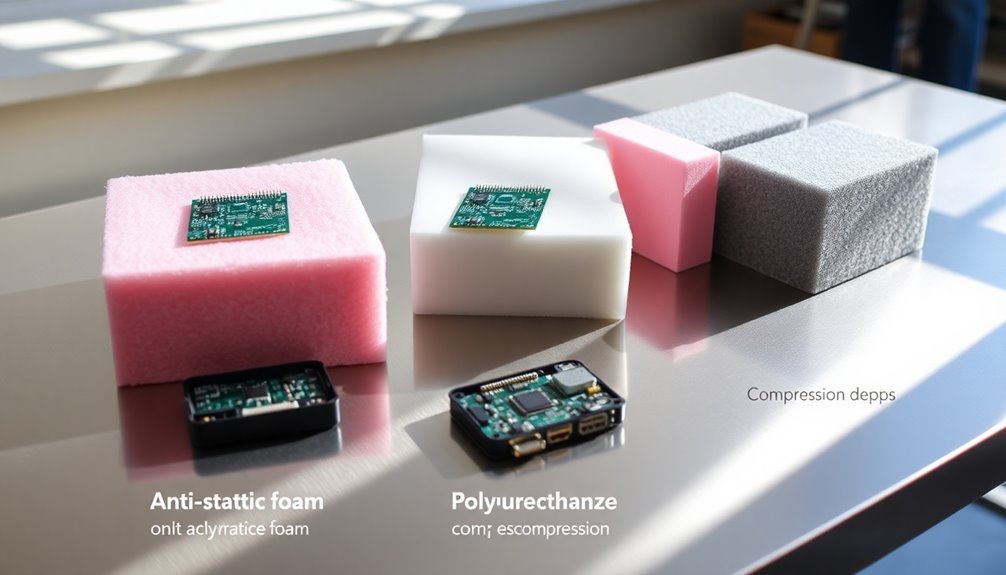
Making smart decisions about foam packaging requires careful analysis of both costs and protection benefits. While initial costs for custom foam inlays can range from $30 to hundreds of dollars, you'll need to weigh these expenses against the long-term savings from reduced damage claims and improved customer satisfaction.
When you're evaluating costs versus protection, consider that high-quality foam materials might cost more upfront but offer superior protection for your electronic devices. You can offset these expenses through bulk purchasing and improved packing efficiency. Breaking down your requirements into distinct items helps ensure comprehensive protection without redundant materials.
Anti-static and non-abrasive foams are essential investments for protecting sensitive electronics, and they'll help you comply with industry standards like EIA-541.
Your cost-benefit analysis should account for both direct and indirect savings. Protection benefits include reduced damage rates, streamlined packing processes, and defense against environmental hazards.
You'll find that proper foam selection can substantially impact your bottom line through decreased damage claims and improved operational efficiency. By right-sizing your packaging and choosing appropriate foam types, you'll minimize waste while maximizing protection.
Remember that the true value of foam packaging lies in its long-term benefits rather than just immediate cost considerations.
Foam Selection Decision Matrix
Selecting the right foam for electronics shipping boils down to a structured decision-making process. You'll need to evaluate your specific requirements across multiple critical factors, including the type of electronics, shipping conditions, and required level of protection.
Start by evaluating your product's sensitivity to static electricity and physical damage. If you're shipping circuit boards, CPUs, or other static-sensitive components, you'll need anti-static foam with surface resistance between 10^4 and 10^9 ohms.
For delicate surfaces, non-abrasive foam is essential to prevent scratching during transit.
Consider these primary decision factors when selecting foam:
- Material Properties: Choose between open-cell polyurethane for lightweight items, closed-cell polyethylene for structural support, or cross-linked polyethylene for tear resistance.
- Protection Requirements: Determine if you need anti-static properties, shock absorption, or moisture resistance.
- Customization Needs: Factor in whether you need custom-cut inserts, specific densities, or special shapes for unique products.
Remember to verify that your chosen foam meets EIA-541 Packaging Material Standards for ESD-sensitive items. The right foam should effectively balance protection against static, vibration, and impact while considering your shipping environment's demands.
Frequently Asked Questions
How Long Can Anti-Static Foam Maintain Its Protective Properties?
You'll find anti-static foam typically maintains its protective properties for about one year, but its effectiveness depends on storage conditions, handling frequency, and humidity levels. Regular testing helps guarantee continued protection.
Can Foam Packaging Be Reused for Multiple Electronic Shipments?
Yes, you can reuse foam packaging for electronic shipments if it's undamaged and properly maintained. Make sure to inspect for wear, clean thoroughly, and verify that anti-static properties remain effective before each reuse.
What Cleaning Methods Are Safe for Electronic Shipping Foam?
You'll want to use non-abrasive cleaners and anti-static solutions with foam swabs. Apply gentle strokes, avoid moisture buildup, and use products like Electrolube Safewash Super for safe, effective foam cleaning.
Does Extreme Humidity Affect the Performance of ESD Foam?
Yes, extreme humidity will affect your ESD foam's performance. High moisture can alter its conductivity and protective properties, while excessive humidity may degrade the material over time, compromising its ability to protect electronics.
Are There Special Storage Requirements for Unused Electronic Packaging Foam?
You'll need to store unused electronic packaging foam in a clean, dry area away from sunlight. Keep it flat, well-ventilated, and protected from dust. Don't stack heavy items on top of it.
In Summary
When you're shipping electronics, you'll want to choose either anti-static polyethylene or ESD-safe polyurethane foam. Make sure it's high-density enough to protect against impacts but not so rigid that it can't absorb shock. Consider your budget, but don't skimp on quality—damaged electronics cost far more than proper packaging. Cross-reference foam specifications with your specific electronic components to make the best choice.
Leave a Reply