Professional training is essential for today's smart cleanrooms to maintain strict quality control and prevent costly contamination. You'll need extensive programs that combine theoretical knowledge with hands-on practice, covering everything from proper gowning procedures to ESD prevention protocols. Your staff must master controlled movements, understand detailed cleaning procedures, and stay current with industry regulations. Through effective training, you'll guarantee adherence to certification standards, reduce error rates, and optimize operational efficiency. Whether you're in semiconductor manufacturing or pharmaceutical production, proper training remains your first line of defense against contamination risks. Discover how professional training can transform your cleanroom operations.
Training Impacts Quality Control
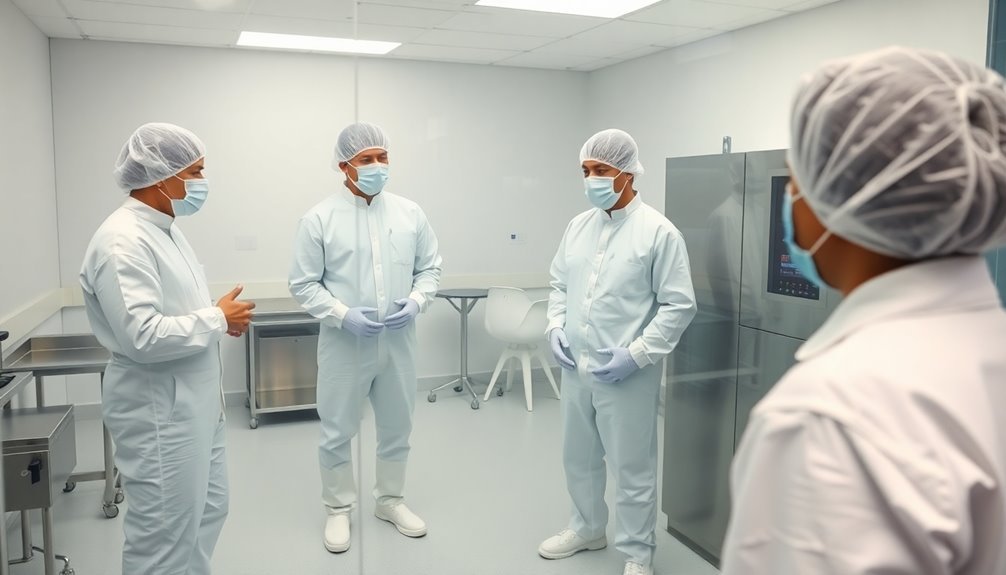
A well-trained cleanroom technician stands as the first line of defense against contamination. When you invest in extensive training programs, you're directly strengthening your quality control measures and reducing the risk of product failures. CPD-certified courses ensure compliance with key industry standards.
Training guarantees your team understands the critical connection between their daily behaviors and contamination prevention, ultimately protecting your facility's integrity.
You'll find that effective training combines both theoretical knowledge and hands-on practice. Through virtual reality simulators and practical sessions, your staff can master essential skills like proper hand hygiene, gowning procedures, and surface cleaning protocols. These training methods help identify potential contamination sources and teach specific techniques to minimize risks.
Your quality assurance efforts depend heavily on maintaining regulatory compliance with EU GMP and ISO 14644 standards. By implementing regular training assessments and feedback sessions, you're reinforcing best practices and preventing costly errors.
E-learning platforms offer consistent messaging across your organization, while customized training programs address your facility's unique needs. Remember, the investment in professional training directly translates to reduced downtime, fewer product failures, and maintained cleanroom certification.
This systematic approach to training guarantees your team maintains high levels of cleanliness and control in your smart cleanroom environment.
ESD Prevention Best Practices
While operating in smart cleanrooms, effective electrostatic discharge (ESD) prevention forms a vital foundation for protecting sensitive components and maintaining product integrity. You'll need to implement thorough measures, starting with proper grounding equipment like antistatic wrist straps and conductive floor mats. Connecting all workstations and equipment to a common grounding point system ensures comprehensive protection.
Maintaining humidity levels between 40-60% and using ESD-compliant equipment substantially reduces static buildup risks.
To guarantee consistent ESD protection, you must focus on these essential practices:
- Wear complete anti-static gear, including gowns, shoe coverings, and gloves before entering the cleanroom.
- Use designated entryways and minimize unnecessary movements to reduce static generation.
- Handle materials with appropriate tools rather than direct contact, and store items in antistatic bags.
Regular monitoring and maintenance of your ESD control systems isn't optional – it's essential for maintaining effectiveness. You'll need to conduct routine compliance audits and guarantee all technicians receive proper training in ESD protocols.
Remember to minimize personnel presence in cleanrooms and pre-plan activities to reduce entry and exit frequency, as each movement can generate potentially harmful static charges.
Certification Benefits and ROI
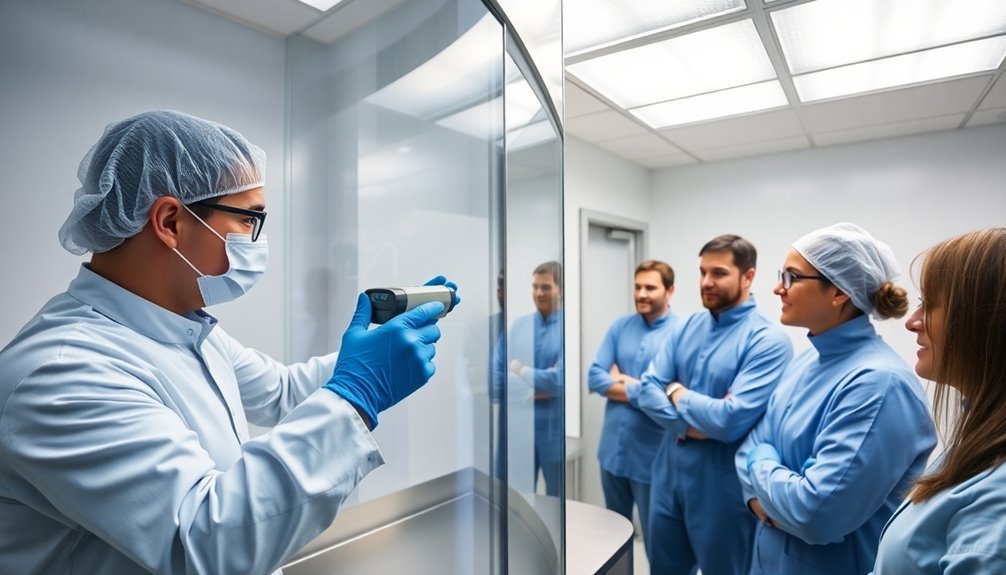
Beyond implementing robust ESD protocols, obtaining and maintaining proper cleanroom certification delivers significant returns on investment across multiple operational areas. You'll see immediate benefits in reduced contamination risks through controlled environments, regular HVAC maintenance, and thorough sampling procedures that guarantee both staff and products remain contaminant-free. Maintaining at least 60 air changes per hour ensures optimal cleanroom conditions.
Your certification investment pays off through improved regulatory compliance, helping you meet essential industry standards like ISO 14644, EU Annex 1, and USP 797. You'll avoid costly legal consequences while demonstrating your commitment to quality standards and worker safety.
These certifications also provide clear metrics for measuring operational excellence and identifying areas for improvement.
You can expect significant cost reductions through enhanced operational efficiency, fewer product rejections, and minimized contamination risks. The certification process helps you establish clear training standards and identify specific staff development needs, guaranteeing your team maintains the highest level of competency.
Hands-On Training Requirements
Implementing effective hands-on training in cleanroom environments requires a structured approach that combines thorough initial education with practical demonstrations. You'll need to guarantee your training program covers contamination control fundamentals, specialized protocols, and ongoing assessments to maintain high standards of cleanliness and safety.
Your training methodology should incorporate small class sizes and interactive sessions that deliver measurable learning outcomes. Regular feedback and improvement monitoring helps optimize training effectiveness over time. By focusing on practical applications, you're able to help staff understand critical aspects of cleanroom operations:
- Equipment handling and materials transfer procedures that minimize contamination risks
- Proper gowning techniques and hand hygiene protocols specific to your facility
- Emergency response procedures and risk management strategies
Don't overlook the importance of continuous monitoring and refresher training. You'll want to establish regular assessments to identify knowledge gaps and guarantee protocol adherence.
Remember that your training program must align with industry regulations like EU GMP and ISO 14644. By implementing thorough hands-on training requirements, you're not just meeting compliance standards – you're building a foundation for operational excellence and contamination control in your smart cleanroom facility.
Staff Performance Measurement Standards
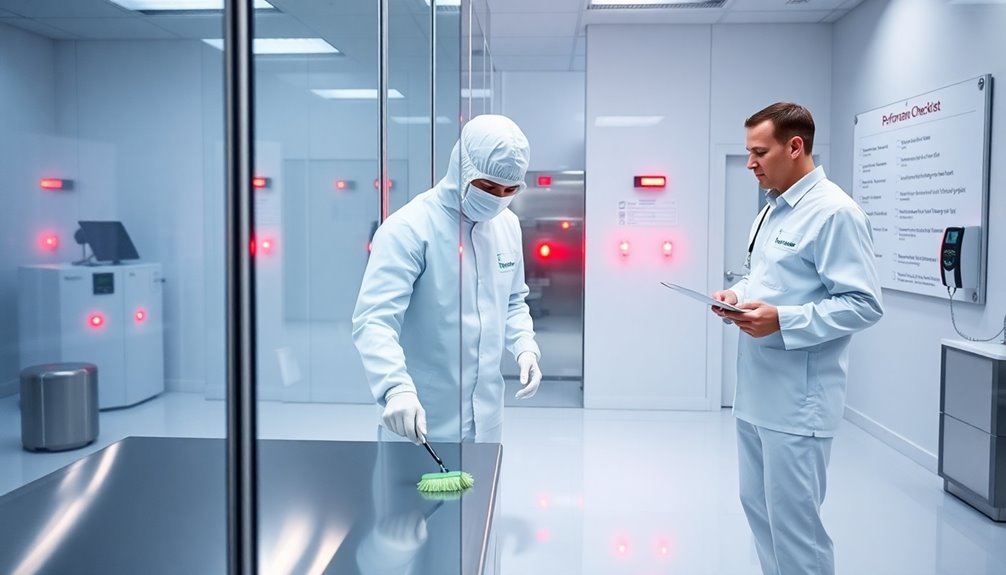
Building on a solid training foundation, effective staff performance measurement standards provide the framework for continuous improvement in smart cleanroom operations.
You'll need to implement thorough KPI dashboards that track essential metrics like turnaround time, throughput, and error rates to evaluate your team's effectiveness accurately.
To maintain high performance standards, you'll want to focus on measuring adherence to protocols through regular audit reports and quality control metrics. Your measurement tools should include both quantitative data from environmental monitoring systems and qualitative feedback from employee assessment mechanisms. Regular monitoring of automation efficiency levels helps optimize workflow and reduce manual processing errors.
You can benchmark your cleanroom's performance against industry standards by tracking key parameters such as environmental conditions, equipment efficiency, and staff competency levels. When you're evaluating performance, it's vital to consider operational efficiency metrics alongside quality control standards to guarantee a balanced assessment.
Your performance measurement system should align with training and development standards, including regular certification renewals and continuous improvement initiatives.
Frequently Asked Questions
How Often Should Cleanroom Air Filters Be Replaced for Optimal Performance?
You'll need to replace pre-filters every 6 months, while HEPA filters typically last 3-5 years. For critical operations, replace HEPA filters every 1-2 years. Always monitor system performance through regular inspections.
What Emergency Protocols Should Be Followed During Power Outages in Cleanrooms?
You'll need to assess the outage's extent, secure hazards, evacuate if necessary, check critical equipment, and monitor environmental conditions. Don't forget to document everything and follow established cleaning protocols once power's restored.
Can Personal Electronic Devices Ever Be Permitted Inside Cleanroom Facilities?
You shouldn't bring personal electronic devices into cleanrooms due to contamination risks. You'll only be allowed to use specially approved, cleanroom-certified devices that meet strict protocols for maintaining sterile conditions.
How Do Seasonal Changes Affect Cleanroom Humidity Control Requirements?
You'll need stronger humidity controls during extreme seasons. In summer, you'll battle high moisture, while winter's dry air requires active humidification. Your HVAC system must adjust constantly to maintain cleanroom specifications.
What Are the Protocols for Handling Equipment Malfunctions During Critical Operations?
You'll need to immediately halt operations, alert supervisors, and isolate the affected area. Document the incident, assess the malfunction's cause, and follow established repair protocols before resuming critical operations.
In Summary
You can't afford to skimp on professional cleanroom training – it's essential for maintaining quality standards and preventing costly contamination. Make sure you're investing in thorough certification programs that include hands-on practice and measurable performance metrics. When you properly train your staff in ESD prevention and cleanroom protocols, you'll see direct ROI through reduced errors and improved efficiency.
Leave a Reply