You need dissipative protection on cleanroom chairs because static electricity poses serious risks in controlled environments. In cleanrooms, low humidity and HEPA filters create conditions where static charges can easily build up to 4,000 volts through simple movements. These charges attract contaminating particles and can damage sensitive electronic components, leading to immediate failures or reduced lifespans. Dissipative chairs help channel static safely away, keeping charges below 100 volts while protecting your valuable equipment and maintaining cleanroom integrity. Understanding the full scope of static protection can save you significant costs and prevent production delays.
Understanding Static Electricity Risks
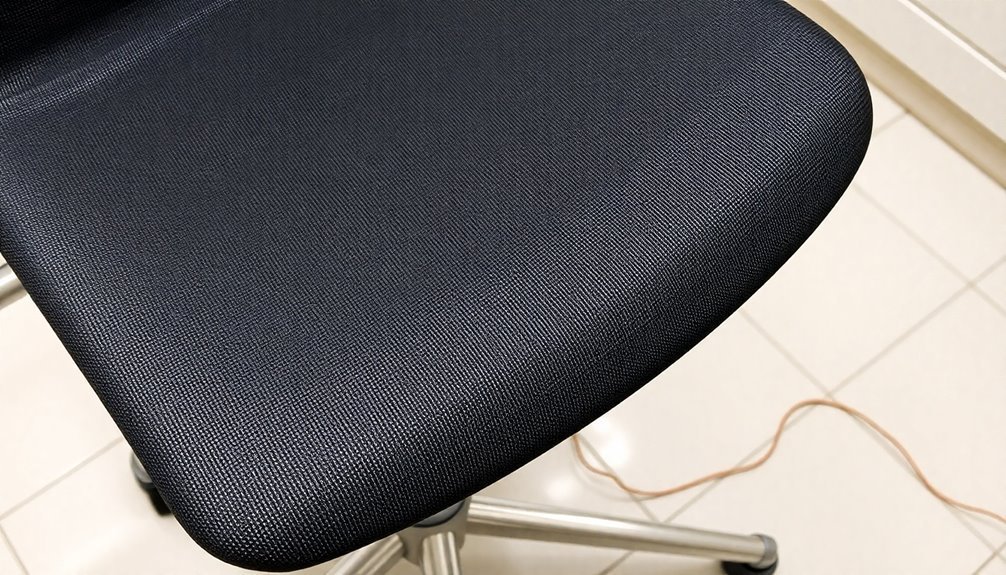
Nearly every cleanroom operation faces significant static electricity challenges, particularly due to the controlled low-humidity environment and extensive use of insulating materials.
You'll find that HEPA filters, while essential for removing particulates, actually compound the problem by eliminating natural ions that would typically help dissipate static charges.
When you're working with electronic components or high surface-to-weight ratio products like hollow plastic moldings, you're particularly at risk.
Static electricity doesn't just pose a threat to your products – it creates a cascade of problems throughout your cleanroom.
You'll find that static charges attract and hold airborne particles, compromising your contamination control efforts and potentially disrupting critical processes.
The impact on your operations can be severe.
Electrostatic discharge can physically damage your electronic components and corrupt microprocessor-controlled applications.
What's more, you'll find that these static-related issues often lead to costly delays and increased operational expenses.
Chairs equipped with drag chains and casters provide essential grounding connections to effectively manage static discharge risks.
In cleanrooms used for electronics, medical devices, or plastics processing, you're dealing with especially sensitive processes that require robust static control measures to maintain product integrity and prevent expensive failures.
Benefits of Dissipative Chair Protection
You'll greatly reduce equipment damage costs by using dissipative chairs that safely channel static electricity away from sensitive electronics and components.
Your workplace safety standards will improve as these chairs minimize the risk of static-related accidents and maintain consistent electrical potential throughout your cleanroom environment.
When you factor in the protection of valuable equipment and the prevention of production delays, dissipative chairs prove to be a smart long-term investment for your facility. The incorporation of conductive materials in these chairs ensures reliable static discharge management across various industrial applications.
Prevents Equipment Damage Costs
Static discharge poses a vital financial risk in cleanroom environments, with equipment damage costs that can quickly escalate into substantial losses.
When you consider that simple movements like sitting and standing can generate static charges exceeding 4,000 volts, you'll understand why protecting your sensitive electronics is essential. These ESD events don't just lead to immediate equipment failure; they can also greatly reduce the lifespan of your electronic components. Long-term comfort while working helps maintain proper posture and reduces distractions that could lead to costly mistakes.
You can effectively mitigate these risks by implementing dissipative chairs as part of your ESD protection strategy.
These specialized chairs draw static charges away from you and your staff, safely dissipating them to ground while maintaining your body at the same electrical potential as your surroundings. They're specifically designed to reduce static charges to below 100 volts, working in conjunction with your ESD flooring system.
Your investment in ESD chairs provides important protection through their carefully engineered features.
With ESD-safe vinyl upholstery and dissipative fabrics containing metal filaments, these chairs guarantee consistent static dissipation. You'll benefit from their chemical-resistant materials and durable construction, making them a reliable component in your thorough ESD control measures.
Enhanced Workplace Safety Standards
Beyond protecting valuable equipment, dissipative chairs play a key role in maintaining workplace safety standards. You'll find these chairs notably reduce the risk of static shock to employees who handle sensitive electronics while providing a reliable grounding mechanism. They prevent unexpected static discharge injuries in high-risk environments and guarantee your facility stays compliant with essential ESD safety protocols. Precision operations require stable seating to minimize errors and accidents.
These specialized chairs meet vital regulatory requirements, including BS EN 61340-5-1 for conductivity and ANSI/ESD ST 12.1-2006 for static dissipative fabric. You'll appreciate how they're designed to comply with stringent cleanroom standards while incorporating features like conductive casters that meet DIN EN specifications.
You won't have to compromise comfort for safety, as these chairs offer adjustable features like seat height and lumbar support. The non-shedding, non-porous materials maintain air quality while making certain your workers remain comfortable during long shifts.
To maintain these safety benefits, you'll need to implement regular cleaning routines and testing procedures. The chairs' easy-to-clean materials and drag chains require consistent maintenance to preserve their ESD effectiveness and protect your workplace's safety standards.
Long-Term Investment Protection
Investing in high-quality dissipative chairs delivers substantial long-term returns for cleanroom operations. When you choose chairs with ESD-safe vinyl and urethane materials, you're protecting your investment through their resistance to harsh chemical cleaners and disinfectants. These materials won't degrade with frequent cleaning, ensuring your chairs maintain their protective properties and appearance over time. Movement flexibility allows efficient workflow adaptation in dynamic cleanroom environments.
You'll find that quality-certified chairs, backed by UL, ANSI/BIFMA, and SEFA standards, provide reliable durability that prevents costly replacements and operational disruptions. The non-shedding, non-porous construction keeps your cleanroom's ISO classification intact while supporting your team's precise work requirements.
By selecting chairs with proper ergonomic design, you're also investing in your workforce's productivity and comfort. The ESD protection these chairs provide isn't just about immediate safety – it's about long-term equipment preservation. You'll avoid expensive repairs and replacements caused by static discharge damage to sensitive electronics.
When you factor in reduced downtime, maintained air quality, and enhanced worker efficiency, dissipative chairs prove to be a strategic investment that pays dividends through sustained cleanroom performance and compliance.
Key Design Features
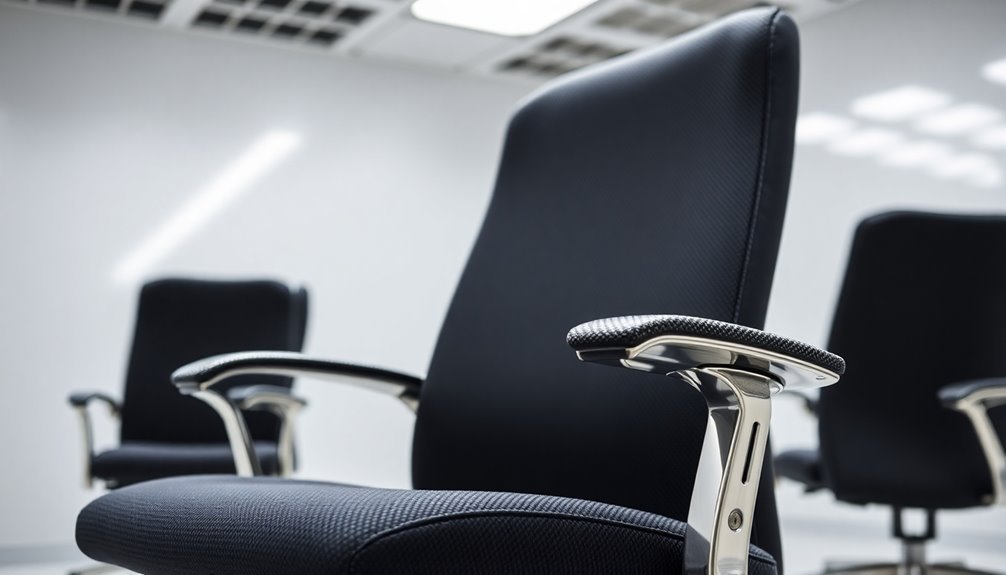
The essential design features of clean room chairs extend across from ergonomic comfort to particle control capabilities. You'll find these chairs equipped with adjustable heights, 360-degree swivel mechanisms, and built-in lumbar support to guarantee your comfort during long work sessions.
The largest wheelbase in the industry, combined with chrome hooded dual wheel casters, provides you with maximum stability and safety. The chairs include a waterfall front seat design that enhances circulation during extended periods of use.
For particle control, you're protected by 99.99% efficient HEPA filters integrated into the seat and backrest, capturing particles as small as 0.5 microns.
The sealed construction, featuring fully wrapped vinyl backs and bottoms, prevents particle accumulation while making cleaning easier. You'll also benefit from the air reservoir system in some models, which prevents particle-laden air from escaping the seat cushion.
The static dissipative protection includes ESD-safe vinyl upholstery with surface resistivity between 10^5 to 10^9 ohms.
You're safeguarded by materials that effectively redirect and dissipate static charges, while drag chains help manage charges generated by chair movement.
These features are complemented by chemical-resistant materials that won't deteriorate when exposed to common cleanroom disinfectants.
Meeting Industry Standards
When you're selecting cleanroom chairs with ESD protection, you'll need to confirm compliance with rigorous testing protocols like ANSI/ESD S20.20-2014 and STM12.1-2013.
Your chairs must carry essential safety certifications that demonstrate both ESD control capabilities and cleanroom particle containment standards under BS EN ISO 14644-1.
Global standards alignment guarantees your ESD chairs meet international requirements for static dissipation, chemical resistance, and particle control across different cleanroom classifications. The Skai Mano-S vinyl material used in modern cleanroom chairs ensures optimal conductivity while maintaining strict cleanliness standards.
Compliance Testing Protocols
Modern clean room chairs must undergo rigorous compliance testing to meet stringent industry standards like ANSI/ESD S20.20, ISO 14644-1, and ANSI/BIFMA X5.1-02. You'll need to verify that your chairs meet specific testing requirements for ESD safety, including proper grounding and the use of static dissipative materials. Critical specifications include the utilization of filtered vent systems that minimize airborne particle dispersion.
Test Category | Requirements |
---|---|
ESD Safety | Surface resistivity 10^5 to 10^9 Ω |
Particle Control | HEPA filtration compliance |
Material Integrity | Chemical resistance testing |
Component Sealing | Air-tight verification |
To guarantee compliance, you must subject your chairs to independent laboratory testing that evaluates multiple critical factors. These include the effectiveness of static dissipative fabrics, the integrity of sealed components, and the performance of air reservoir diaphragm lung seat cushions. You'll also need to verify that your chairs' frames are designed without gaps or crevices that could trap particles.
Regular maintenance and cleaning protocols are essential to maintain compliance. Your chairs must demonstrate continued adherence to standards through periodic testing and certification renewal, ensuring they maintain their protective properties throughout their service life.
Essential Safety Certifications
Three essential safety certifications form the cornerstone of clean room chair compliance: BS EN ISO 14644-1 for air cleanliness, Federal Standard 209 for particulate control, and BS EN 61340-5-1 for ESD protection.
You'll need to guarantee your clean room chairs meet these standards through specific material choices and construction methods. The chairs must use non-shedding, non-porous materials that won't release particles into your controlled environment.
You'll also need chemically resistant components that can withstand regular cleaning with industrial disinfectants.
For ESD protection, your chairs must incorporate conductive materials and proper grounding systems. The vinyl and fabric used should safely dissipate static charges, meeting ANSI/ESD STM 12.1 requirements for static-control programs. These materials aren't just about safety—they're vital for protecting sensitive equipment and maintaining product integrity.
The chairs' ergonomic features can't compromise their clean room compatibility. You'll want adjustable settings for proper body support, but these mechanisms must be sealed to prevent particle accumulation.
Each component needs to balance user comfort with strict cleanliness standards, guaranteeing you're maintaining both productivity and contamination control in your facility.
Global Standards Alignment
Global industry standards create a complex framework for clean room chair compliance across multiple sectors.
You'll find that these standards intersect across ISO 14644-1, Federal Standard 209E, and ANSI/BIFMA requirements, ensuring your cleanroom seating meets stringent international specifications.
When you're selecting chairs for your controlled environment, they must align with both regional and global certifications.
Your cleanroom chairs need to meet specific standards based on your industry:
- For semiconductor and aerospace applications, you'll require Class 10 or Class 100 compliant seating with verified particle control.
- If you're in pharmaceutical manufacturing, your chairs must meet USP 797 regulations and provide ESD protection.
- For medical device production, you'll need seating that maintains ISO 3 to ISO 8 cleanliness levels.
Testing and certification documentation should verify that your chairs meet ANSI/ESD STM 12.1 for static dissipative properties, with surface resistivity between 10^5 to 10^9 ohms.
The materials must withstand rigorous cleaning protocols while maintaining their protective properties, and independent laboratory testing should confirm compliance with your required cleanliness classification.
Material Selection Matters
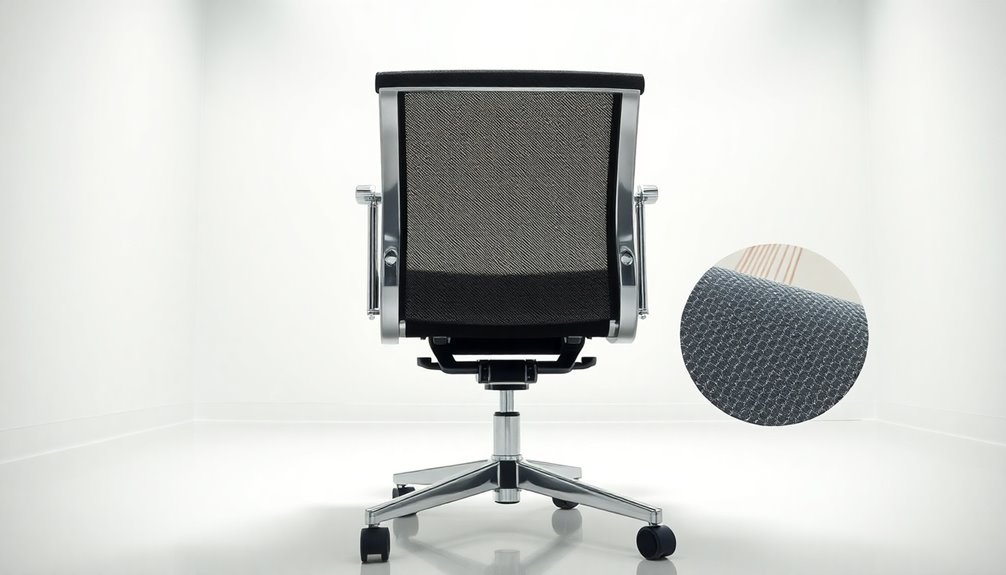
Selecting the right materials for cleanroom chairs isn't just about durability – it's about maintaining a controlled environment while protecting sensitive equipment and processes.
You'll need materials that won't generate particles or shed, while simultaneously providing ESD protection and chemical resistance. When you're choosing cleanroom chair materials, focus on electropolished stainless steel for structural components and ESD-safe fabrics with surface resistivity between 10^5 to 10^9 Ω.
You'll want to incorporate vinyl or polyurethane upholstery that's both chemical-resistant and easy to clean, particularly against common agents like bleach and peracetic acid.
Don't overlook the importance of sealed designs that minimize gaps and crevices where particles could accumulate. You should consider chairs with in-seat filtration systems using polypropylene media that can trap particles as small as 0.1 microns.
The chair's construction must include conductive casters and drag chains to maintain consistent grounding with your cleanroom floor.
Remember to balance these technical requirements with ergonomic features like adjustable height, lumbar support, and tilting mechanisms. Your chair needs to provide comfort while meeting stringent cleanroom standards.
Clean Room Compliance Requirements
Compliance with cleanroom standards demands rigorous adherence to multiple regulatory frameworks.
You'll need to guarantee your cleanroom chairs meet specifications outlined in ISO 14644-1 and Federal Standard 209E, while also satisfying ESD protection requirements under BS EN 61340-5-1. These standards aren't just suggestions – they're essential requirements for maintaining clean room integrity.
Your chairs must undergo regular testing and certification to maintain compliance:
- HEPA filter leak testing and particle classification every 6 months for ISO Class 5 environments or lower
- Annual airflow volume and air pressure difference testing
- Regular ESD grounding verification and conductivity measurements
You're also responsible for maintaining detailed documentation of all testing procedures and results.
This includes tracking your chairs' performance regarding particle shedding, ESD protection levels, and overall cleanliness maintenance.
Remember, your cleanroom furniture must be compatible with your facility's cleaning protocols and disinfectant procedures.
The cGMP guidelines are particularly strict if you're operating in pharmaceutical environments, requiring additional documentation and more frequent testing schedules.
Ergonomic Considerations for Safety
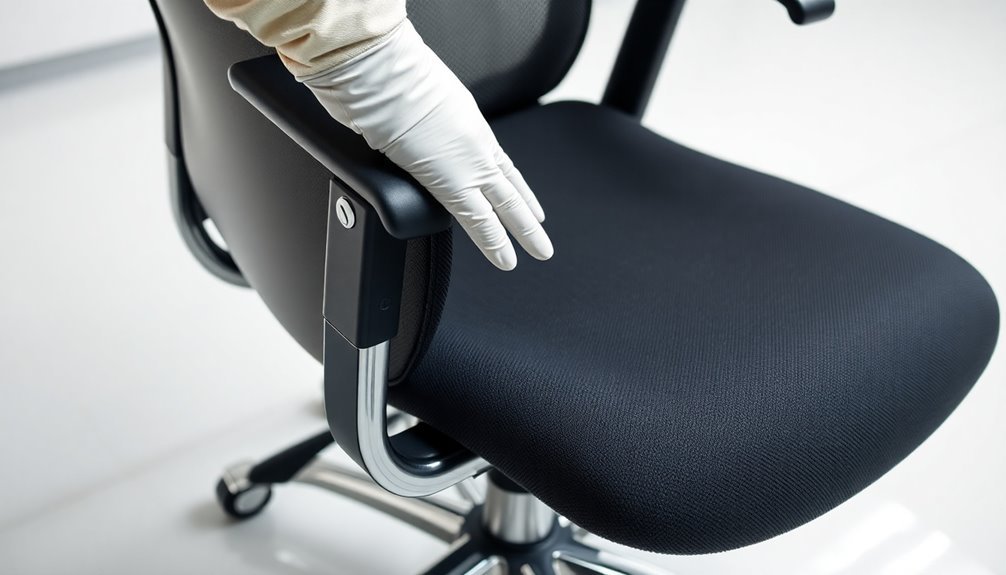
Four essential ergonomic principles drive cleanroom chair safety: adjustability, support, comfort, and durability. When you're working in a cleanroom environment, you'll need a chair that adapts to your body while maintaining strict contamination control standards. Proper lumbar support and adjustable armrests prevent musculoskeletal disorders during long work sessions.
Your chair's ergonomic features directly impact both safety and productivity. The right combination of height adjustment and cushioning guarantees even weight distribution, reducing fatigue and allowing you to focus on critical tasks.
Feature | Safety Benefit |
---|---|
Adjustable Height | Prevents strain on legs and feet |
Lumbar Support | Reduces back stress and injury risk |
Cushioned Seat Pan | Eliminates pressure points |
The materials used in your cleanroom chair must balance comfort with cleanroom compliance. You'll want non-shedding, easy-to-clean surfaces that maintain their ergonomic properties even after repeated exposure to chemicals and disinfectants. When selecting a chair, consider your specific work requirements, body size, and the duration of your seated tasks to guarantee ideal safety and comfort without compromising cleanroom integrity.
Static Control Testing Methods
In accordance with ESD safety protocols, you'll need to conduct specific testing procedures to verify your cleanroom chair's static control effectiveness. Testing involves both contact and air discharge methods using specialized ESD testing equipment that follows IEC 61000-4-2 standards.
You'll use an ESD gun to apply controlled electrostatic discharges to various points on your chair's surface while monitoring its performance. The testing setup requires a Ground Reference Plane (GRP) to provide the necessary current return path, along with horizontal and vertical coupling planes to simulate indirect discharges.
Your chair must demonstrate consistent static dissipation across all test points to meet safety requirements.
- You'll need to test all four sides of your chair using contact discharge methods, where the ESD gun directly touches the surface.
- Air discharge testing simulates real-world conditions by approaching the chair with a charged probe.
- Test voltages will range from 2 kV up to 15 kV depending on your specific requirements.
Remember that ESD pulses occur in sub-nanosecond timeframes, so proper testing equipment calibration is essential. Your chair's static control effectiveness must be verified at multiple points to guarantee thorough protection throughout its entire surface area.
Maintenance and Performance Longevity
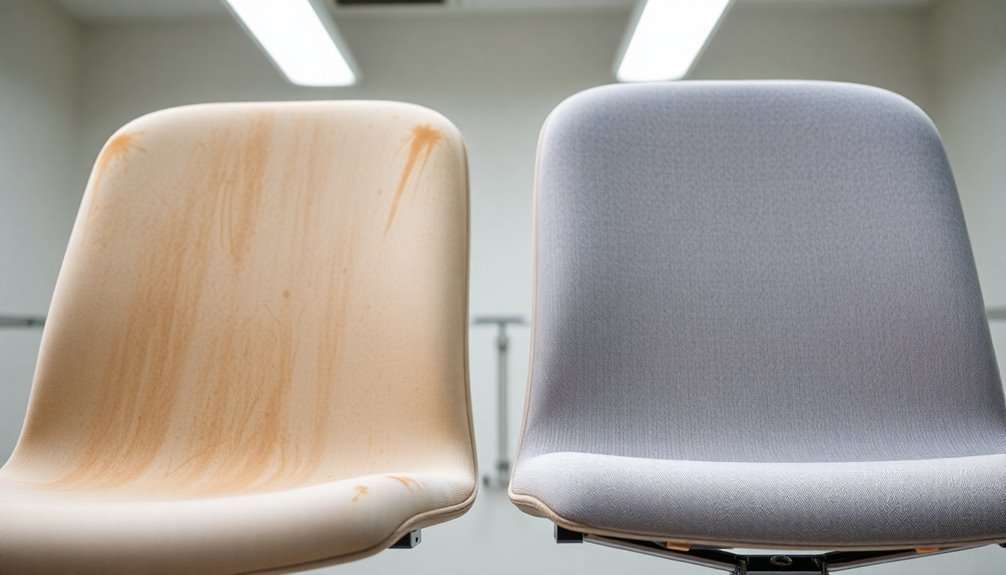
Proper maintenance of cleanroom chairs determines their long-term effectiveness and static control performance. You'll need to follow strict cleaning protocols using approved agents while guaranteeing you're not compromising the chair's static dissipative properties. Regular inspections of grounding systems, particularly drag chains and ESD-safe upholstery, are vital for maintaining conductivity.
Maintenance Task | Frequency |
---|---|
Conductivity Testing | Weekly |
Surface Cleaning | Daily |
Grounding Check | Monthly |
Full Inspection | Quarterly |
To extend your chair's performance longevity, you'll want to focus on both preventive maintenance and proper usage. Enclosed mechanisms help reduce particle contamination, while routine checks of the in-seat filtration system guarantee peak particle capture. When cleaning, use gentle techniques that won't degrade the static dissipative materials.
Don't overlook the importance of troubleshooting potential issues early. If you notice any static discharge symptoms or wear in the upholstery, address them immediately. Always use certified replacement parts to maintain ESD compliance with standards like BS EN 61340-5-1. Remember that your chair's effectiveness depends on consistent maintenance of all its protective features, from the static dissipative vinyl to the grounding components.
Frequently Asked Questions
How Often Should Clean Room Chairs Be Replaced to Maintain ESD Protection?
You'll need to replace clean room chairs every 3-5 years, but conduct monthly ESD testing, physical inspections, and performance checks. If your chair fails these assessments, replace it immediately regardless of age.
Can Regular Office Chairs Be Modified for Clean Room Use?
You shouldn't modify regular office chairs for cleanroom use. It's costly, difficult to meet cleanliness standards, and may compromise safety. Instead, invest in specially designed cleanroom chairs with proper ESD protection.
Do Temperature and Humidity Affect the Chair's Dissipative Properties?
Yes, your chair's dissipative properties are greatly affected by temperature and humidity. You'll notice reduced ESD protection in low humidity and potential material degradation in extreme temperatures, affecting the chair's conductive performance.
What Cleaning Solutions Are Safe to Use on ESD Chairs?
You can safely use mild soap solutions, isopropyl alcohol, or specialized ESD cleaners on your chair. Avoid harsh chemicals like bleach or ammonia that'll damage the chair's dissipative properties and material integrity.
Are There Different ESD Chair Requirements for Various Clean Room Classes?
Yes, you'll find different ESD chair requirements between clean room classes. Class 10 (ISO 4) needs stricter standards and better materials than Class 100 (ISO 5), including enhanced grounding and tighter seals.
In Summary
You'll find dissipative protection for clean room chairs is essential for protecting sensitive equipment and materials from static discharge. By ensuring your chairs meet industry standards and include proper static control features, you're safeguarding both your products and operations. Don't overlook regular maintenance and testing to maintain peak performance. Remember, proper material selection and ergonomic design work together to create a safer clean room environment.
Leave a Reply