You'll need these 10 essential cleanroom anti-static control audit tests to protect your sensitive components and maintain high yields. Start with electrostatic field measurements and body voltage generation testing using specialized probes and meters. Validate surface resistance and analyze static decay rates across materials. Don't forget ESD flooring performance checks, ionization equipment efficiency tests, and material static control property validation. Include environmental humidity monitoring and equipment grounding integrity verification in your protocol. Regular personnel static level measurements round out your testing arsenal. These proven methods will help you build a thorough ESD protection strategy.
Electrostatic Field Measurement Tests
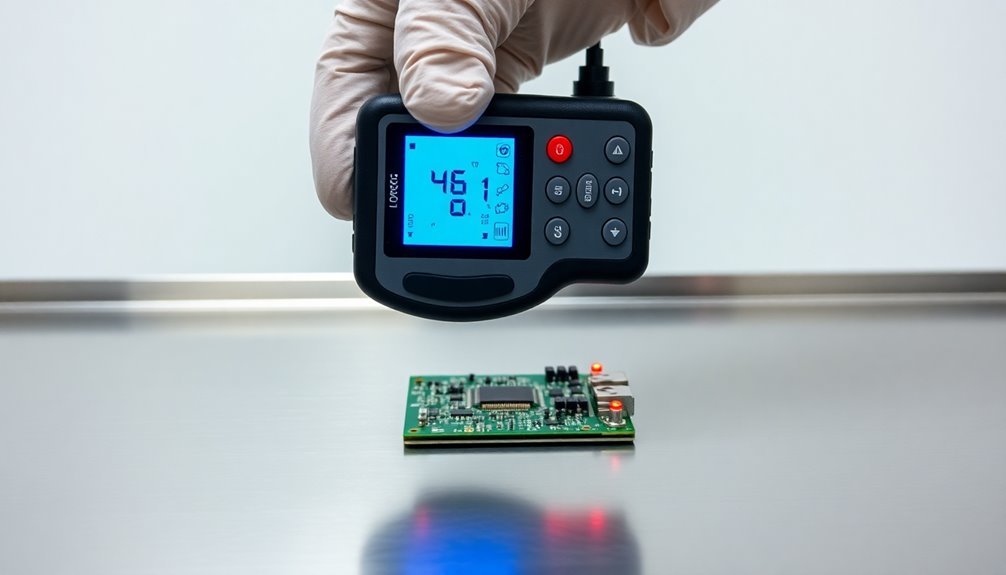
Through electrostatic field measurement tests, you'll accurately measure the force between induced charges in a sensor and charges present on object surfaces. Using a charge monitoring probe placed near the surface, you can achieve high accuracy measurements that aren't greatly affected by variations in probe-to-surface distances.
You'll want to select from several fieldmeter types based on your specific needs. The most common type directly measures electric fields and converts readings to voltage or field intensity. For enhanced accuracy, you can use meters with electronic circuits that drive the probe body to match the measured potential. These devices typically measure from 0.1 to 20K volts per centimeter. The user-friendly design makes it easy for personnel of all skill levels to operate these meters effectively.
To guarantee reliable results, you'll need to calibrate your fieldmeter using two large parallel conductors set at a known spacing with an applied voltage. When conducting tests, you can take portable measurements throughout your cleanroom to verify compliance with ANSI/ESD S20.20 and IEC 61340 standards.
Remember that you'll need to perform periodic zeroing on some meter types, and you can't continuously monitor a single area over extended periods. Maintaining proper humidity levels will help you manage static electricity more effectively during testing.
Body Voltage Generation Testing
You'll need specialized shoes with electrodes connected to a charge plate meter to accurately measure static voltage levels generated by personnel walking on ESD floors.
Testing includes analyzing real-world movement patterns as individuals perform their typical cleanroom activities, providing data that reflects actual working conditions.
Per industry standards, target measurements should show personnel generate no more than 100 volts during testing operations.
The setup requires careful attention to environmental factors like humidity and temperature while following ANSI/ESD S97.2 guidelines for equipment placement and calibration.
Measuring Personnel Static Levels
Measuring personnel static levels requires specialized equipment and precise testing procedures to evaluate the effectiveness of ESD control measures.
You'll need a body voltage meter setup consisting of a digital multimeter and two probes to accurately measure the voltage difference between a person and ground.
E-fields from devices move from high to low pressure areas throughout cleanroom spaces, making measurement essential for identifying risk zones.
To conduct the test, you'll need to connect the black lead of your voltmeter to a reliable ground point, such as a properly verified ground stake or outlet ground conductor.
Then, attach the red lead to the test subject's skin using a specialized probe. Remember that skin impedance can affect your readings, so you'll want to account for factors like wet or dry skin conditions.
You should perform these measurements as part of your regular compliance verification audits. It's essential to document baseline measurements before implementing static control methods so you can track the effectiveness of your ESD program.
When testing personnel, you'll want to analyze their movement patterns through the cleanroom, identifying potential ESD event points from entry to exit.
This data helps you determine where defects and losses might occur in your manufacturing process and guides your anti-static control strategy adjustments.
Real-World Movement Analysis
Building on personnel static measurements, real-world movement analysis offers deeper insights into how workers generate static charges during their actual cleanroom activities. You'll need to conduct walking tests while personnel wear static-control footwear on ESD flooring, ensuring body voltage generation stays below 100 volts per ANSI/ESD S20.20 standards. Modern high reliability organizations have demonstrated that deference to expertise significantly improves the accuracy of movement analysis testing.
Movement Type | Common Voltage | Mitigation Strategy |
---|---|---|
Walking with cleanroom shoe covers | >1,000V | Use conductive shoe covers with grounded floors |
Walking with heel grounds | Moderate | Increase contact area with conductive shoes |
Regular footsteps with proper ESD shoes | <100V | Maintain regular testing and verification |
You'll want to use instruments like electrostatic field meters and Human Body Voltage Checkers to monitor real-time charge generation. Focus on testing the complete flooring-footwear system, as individual components might pass standards but fail when combined. Remember that skin conditions and environmental factors can affect your measurements, so it's essential to conduct periodic tests following ANSI/ESD STM97.2. For sensitive devices, you may need to implement stricter controls than the standard 100-volt limit.
Testing Equipment Setup Guidelines
A proper equipment setup forms the foundation for accurate body voltage generation testing in cleanrooms. You'll need to follow ANSI/ESD S97.2 standards while using electrostatic field meters and EMI-locator instrumentation to measure static charges effectively. Your testing environment must maintain controlled humidity levels, as environmental factors can greatly impact your results. Conductive wrist straps should be worn by personnel conducting the tests to prevent any interference from human-generated static charge.
To guarantee reliable measurements, you'll need to implement these essential setup components:
- Install properly grounded ESD flooring made of conductive or static-dissipative materials to create a controlled testing surface.
- Equip test subjects with approved static-control footwear that meets conductivity requirements.
- Position body voltage meters correctly to measure the interaction between footwear and flooring.
- Set up humidity control systems to maintain consistent environmental conditions.
Don't forget to verify that your electrostatic voltmeters are calibrated and functioning correctly before beginning any tests. Your measurement accuracy depends heavily on proper equipment positioning and connection to grounding systems.
When using standard shoe covers, verify they're properly grounded to prevent false readings from high static voltage generation. Regular equipment maintenance and verification will help you maintain consistent testing conditions and reliable results.
Surface Resistance Validation
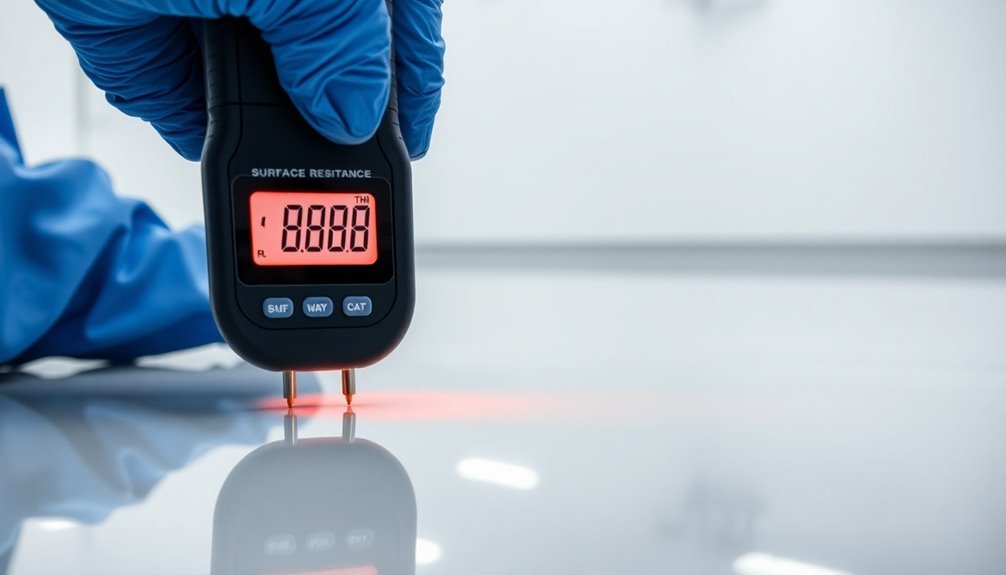
You'll need to employ ASTM-D-257 and ANSI/ESD standards for accurate surface resistance measurements, using calibrated surface resistivity meters and conductive probes to evaluate your cleanroom materials.
Similar to evidence collection procedures in financial audits, your testing schedule should include weekly point-to-point resistivity checks and monthly thorough surface resistance validation tests, with additional testing after any significant environmental changes or material modifications.
Maintain detailed calibration records for all measurement equipment, ensuring your surface resistivity meters are calibrated every six months according to manufacturer specifications and ISO guidelines.
Measurement Methods and Standards
Three vital standards govern the measurement of surface resistance in cleanroom environments: ASTM-D-257, AATCC-76, and ESD test standards ANSI/ESD S20.20 and IEC 61340.
You'll need to understand these methods to effectively validate your cleanroom's anti-static controls and guarantee compliance with industry requirements. Regular assessments of these controls are essential as proper static control directly impacts product quality and safety.
When you're conducting surface resistance measurements, you'll want to follow these standardized procedures:
- Apply the Surface Resistivity Test to quantify your fabric's electrical resistance from point to point, measuring in Ohms to determine its conductivity level.
- Implement the Static Electricity Decay FTM 4046 to measure discharge time from 500V to 50V, confirming your materials meet rapid dissipation requirements.
- Use the ASTM-D-257 method for precise DC resistance measurements of insulating materials, particularly essential for validating cleanroom garments.
- Follow ANSI/ESD S20.20 and IEC 61340 guidelines specifically for cleanroom applications, as they provide thorough testing parameters for ESD control.
Your measurement results must align with these standards to maintain proper static control.
Remember that consistent validation helps prevent contamination risks and guarantees your cleanroom maintains its required cleanliness classification.
Testing Frequency Guidelines
Regular surface resistance validation forms the cornerstone of effective ESD control in cleanroom environments.
You'll need to establish testing frequencies based on your facility's specific requirements and document them in your ESD control plan. Your testing schedule should reflect both the criticality of ESD-sensitive items and the reliability history of your ESD protective equipment.
Performance monitoring helps detect significant changes in your ESD equipment's effectiveness over time. You should adjust your testing frequencies based on historical test results. If you're consistently meeting specifications, you might relax the schedule, but if you're detecting issues, you'll need to increase testing frequency.
Pay special attention to materials that lack permanency, such as ESD floor finishes, as they'll require more frequent monitoring.
For cleanroom garments, incorporate both ESD and particulate testing into your validation schedule.
You'll want to measure static decay rates and surface resistivity of conductive yarns while also performing Helmke drum tests to assess particle shedding.
Remember to align your testing schedule with ISO 14644-1:2015 requirements, which mandate specific intervals for different cleanroom classifications.
Document all test results thoroughly, as they'll serve as evidence during audits and help you optimize your testing frequencies over time.
Equipment Calibration Requirements
In accordance with industry standards, surface resistance test equipment must undergo rigorous calibration before conducting validation tests in cleanroom environments.
You'll need to verify your calibration processes comply with ISO and ANSI standards, maintaining proper documentation through calibration certificates for traceability and audit requirements.
To maintain accurate and reliable test results, you'll need to implement thorough validation protocols that specify testing locations, frequencies, and environmental conditions.
Your maintenance schedule should align with manufacturer recommendations, protecting equipment from damage while documenting all activities.
Here's what you'll need for effective equipment calibration:
- Compare your meter readings against known reference standards, documenting any deviations and implementing corrective actions when results fall outside acceptable ranges.
- Protect your testing equipment from environmental factors and damage, sourcing replacement parts only from approved suppliers.
- Train and assess your personnel regularly to verify they're competent in equipment operation and result interpretation.
- Maintain detailed records of calibration certificates, maintenance activities, and training documentation for audit purposes.
Remember to conduct periodic competency assessments of your testing personnel to verify ongoing proficiency in surface resistance validation procedures.
Static Decay Rate Analysis
Static decay rate analysis forms the cornerstone of cleanroom anti-static control, measuring how quickly electrostatic charges dissipate from material surfaces. You'll need to understand both the testing methods and equipment requirements to guarantee accurate measurements.
Testing Method | Key Characteristics |
---|---|
Corona Charge | Variable charging levels, useful for dissipative analysis |
Triboelectric | Simulates real use but can alter materials |
Direct Contact | Reveals surprising decay times in homogeneous materials |
Federal Test 101C | Standard method using contact or Corona discharge |
The industry-standard Electro-Tech System 4406 offers automated testing with programmable charging voltages from ±600-5,250V and precise decay time measurements to 0.001 seconds. You'll achieve the most reliable results when testing at humidity levels below 50% RH.
For effective testing, you'll need to select the appropriate sample holder: magnetic holders work best for films and fabrics, while clamps suit non-flexible sheets. Don't forget to maintain regular calibration according to Method 4046 specifications. When conducting thorough cleanroom audits, combine your decay rate analysis with electrostatic field meters and EMI-locator instrumentation to get a complete picture of static control effectiveness.
ESD Flooring Performance Assessment
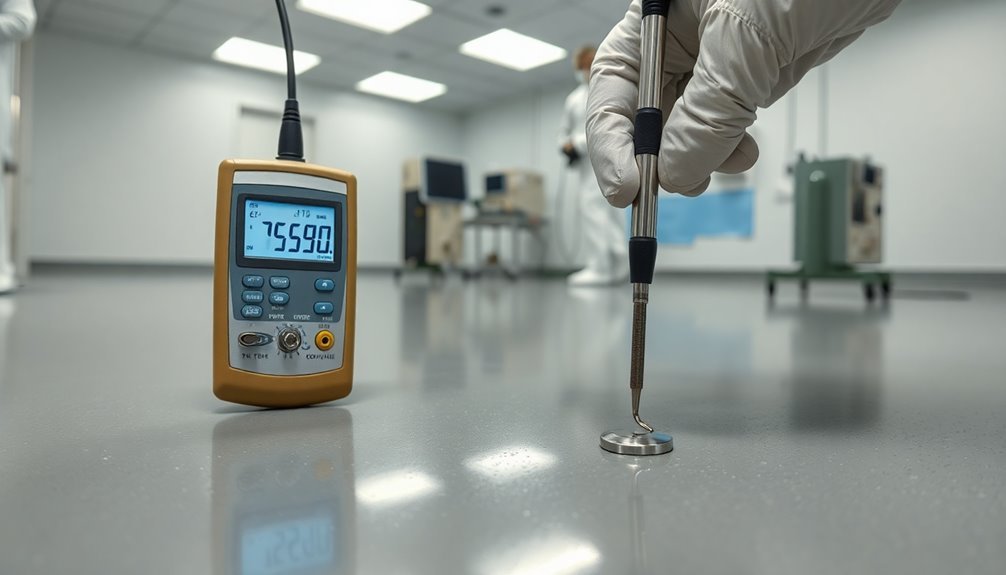
Effective ESD flooring assessment requires a multi-faceted approach combining resistance testing, body voltage measurements, and material evaluation.
You'll need to verify your flooring meets industry standards like ANSI/ESD STM 7.1 and ASTM F150, particularly for electronics manufacturing where resistance should be less than 1.0 x 10^9 ohms.
When conducting performance assessments, you'll want to focus on these key testing components:
- Resistance testing using a megohmmeter or multimeter, placing electrodes on the floor to measure resistance to ground.
- Body voltage generation through walking tests that measure real-world static buildup using a static charge plate recorder.
- Material compatibility checks to verify your flooring works effectively with ESD footwear and meets cleanroom requirements.
- Environmental condition monitoring to account for temperature and humidity effects on performance.
You'll need specialized equipment for accurate measurements, including resistance meters and voltage recording devices.
Don't forget to evaluate maintenance requirements and ergonomic factors in your assessment.
For the most reliable results, it's often best to work with ESD specialists who can provide thorough testing and evaluation services tailored to your cleanroom's specific needs.
Personnel Grounding System Verification
Proper verification of personnel grounding systems stands at the heart of cleanroom ESD control. You'll need to confirm your wrist straps meet essential requirements, including a secure connection to a common ground point and regular functionality testing.
When you're handling ESD-sensitive items while seated, wrist straps serve as your primary grounding method, working alongside dissipative work mats and other grounding solutions.
Your flooring and footwear system must work together effectively, maintaining a total resistance to ground of less than 1.0 x 10^9 ohms when including the person, footwear, and floor. You'll want to verify that body voltage stays below 100 volts during standard walking tests and confirm all mobile equipment uses appropriate dissipative or conductive casters.
To maintain compliance, you must implement a thorough static control program with regular audits. You'll need specific testing equipment, including electrostatic field meters and resistance meters, to verify system effectiveness.
Your audit process should incorporate walking voltage tests, resistance measurements, and detailed documentation. Remember to regularly test all grounding components and maintain detailed records of your verification results to confirm continuous ESD protection in your cleanroom environment.
Ionization Equipment Efficiency Testing
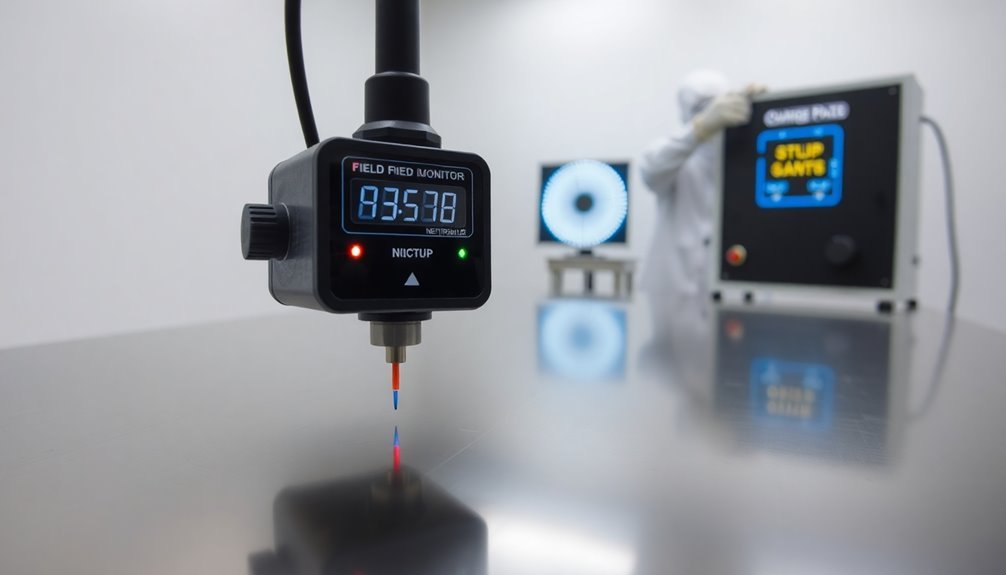
You'll need to verify three critical aspects of your ionization equipment: air ion balance, decay time performance, and ion coverage patterns.
Your ion balance testing confirms whether positive and negative ions are properly equilibrated, while decay time analysis shows how quickly static charges dissipate in protected areas.
Air Ion Balance Verification
Within cleanroom environments, air ion balance verification serves as a critical test to verify ionization equipment maintains equilibrium between positive and negative ions. You'll need to conduct these tests regularly to guarantee your static control measures effectively prevent particle contamination and protect sensitive materials.
The verification process aligns with ANSI/ESD S20.20 and IEC 61340 standards, providing you with clear benchmarks for maintaining proper ionization levels. You're looking for balanced outputs that can neutralize static charges effectively, especially in critical areas like gown-up rooms and transfer zones.
Here's what you'll monitor during verification:
- Ion balance measurements to confirm equal distribution of positive and negative ions
- Strategic placement effectiveness of ionizers near entrances and critical zones
- Response times of external sensors to environmental changes
- Continuous performance metrics through automated monitoring systems
You'll find that proper verification can lead to significant improvements, with facilities reporting up to 95% reduction in yield losses from particle contamination.
Remember to maintain certification requirements for your specific ISO class cleanroom and regularly clean your ionization equipment to guarantee consistent performance.
Decay Time Analysis
Building on the importance of ion balance verification, decay time analysis provides a quantitative method to evaluate how effectively your ionization equipment dissipates static charges.
You'll need to condition your test materials at 50% relative humidity for at least 12 hours before charging them to approximately 5000V using corona or triboelectrification methods.
To conduct the analysis, you'll use a static monitor and grounding cable while following standards like MIL-STD-3010 and IEC-61340-4-4.
Using measurement devices such as a Picoscope or IST 40.2 analyzer, you'll record the time it takes for charges to dissipate to 50%, 10%, and 1% of their initial value. Materials that reach 10% of their initial charge within 5 seconds are considered static dissipative.
You'll want to pay special attention to this testing in cleanroom environments, where proper ionization can greatly reduce particle counts and yield losses.
The data you collect will help you make informed decisions about implementing ESD control measures, including grounding techniques and humidity control.
When you're working with static-sensitive equipment like photolithography tools, these measurements become essential for maintaining ideal cleanroom conditions and preventing ESD-related malfunctions.
Ion Coverage Mapping
Ion coverage mapping serves as an essential diagnostic tool for evaluating the effectiveness of cleanroom ionization systems. You'll find this testing particularly important in gown-up rooms and transfer areas where static charges pose significant contamination risks.
Using both overhead and blower-type ionizers, you can achieve thorough coverage that directly impacts your facility's particle control and yield improvement.
When you're conducting ion coverage mapping, focus on these key areas:
- Identify all important zones requiring ionization coverage, especially in gown-up rooms where static reduction can lead to a 25% decrease in yield losses.
- Test ion distribution patterns from your installed equipment, ensuring balanced positive and negative ion delivery.
- Measure decay times across different points in your mapped area to verify uniform neutralization.
- Document areas where coverage might be insufficient or where ion balance needs adjustment.
You'll want to prioritize this testing as part of your anti-static control program, as proper ionization coverage can reduce contamination-related losses by 80-90% when implemented facility-wide.
Remember that automatic balancing systems and regular emitter cleaning maintenance will help maintain peak performance of your ionization equipment throughout the mapped areas.
Material Static Control Properties
Three essential material categories define static control properties in cleanroom environments: conductive, dissipative, and insulative materials. You'll need to understand each type's characteristics to implement effective static control measures in your cleanroom.
Conductive materials, with resistance below 104 Ω, offer the fastest path to ground and are ideal for tools, equipment, and flooring. They'll continuously guide charges safely to ground, protecting your sensitive components from damage.
Dissipative materials, featuring resistance between 104 Ω and 109 Ω, provide a controlled method to disperse static charges. You'll find these in specialized mats, tools, and furniture designed for cleanroom use.
You must be particularly cautious with insulative materials, which have resistance above 109 Ω. These materials can't be effectively grounded and will retain static charges, potentially damaging your products and disrupting operations.
When developing your ESD control strategy, you'll want to minimize or eliminate insulative materials, replacing them with conductive or dissipative alternatives. Your thorough static control program should incorporate proper material selection and grounding strategies to guarantee consistent protection against electrostatic discharge throughout your cleanroom facility.
Environmental Humidity Level Monitoring
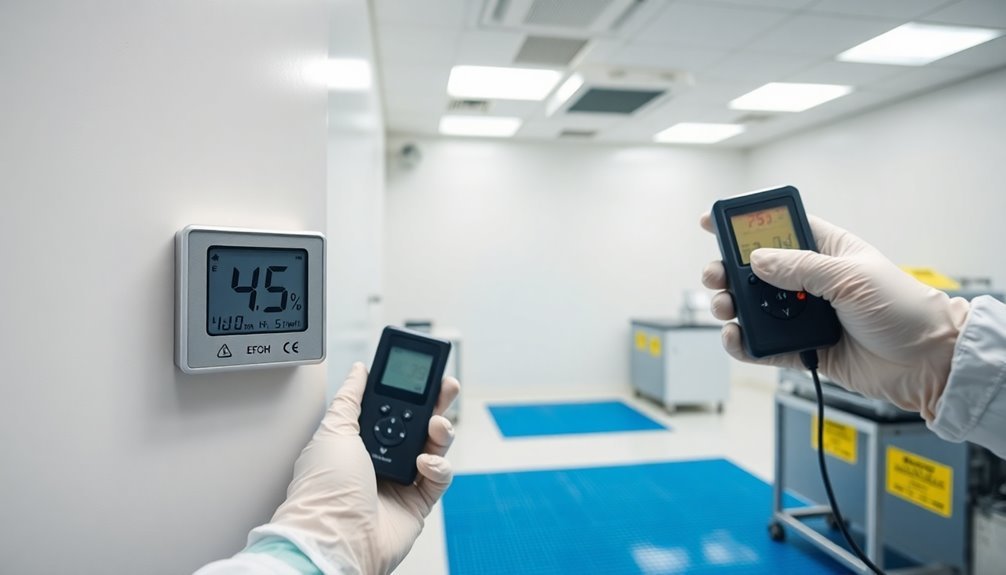
Throughout your cleanroom operations, maintaining proper humidity levels is essential for preventing electrostatic discharge and ensuring product quality. In environments with low humidity, static electricity risks increase dramatically, potentially damaging sensitive electronic components and disrupting manufacturing processes.
You'll need to implement thorough monitoring systems to maintain ideal conditions. Your humidity control strategy should incorporate both real-time monitoring and periodic testing protocols. Install temperature and humidity sensors throughout your cleanroom, ensuring they're strategically placed to detect variations in different zones.
When you're dealing with critical processes, don't rely solely on your HVAC system – implement redundant monitoring methods.
Here's what your environmental humidity monitoring program should include:
- Continuous sensor monitoring with real-time alerts when levels fall outside acceptable ranges
- Annual testing and calibration of all humidity control systems, including HVAC and industrial humidifiers
- Regular air sampling to detect any moisture-related microbial contamination
- Documentation of humidity levels during each shift, particularly in areas where static-sensitive products are handled
Consider using double airlocks and desiccant systems when you need precise humidity control, especially in areas requiring extremely low moisture levels or facing significant worker traffic.
Equipment Grounding Integrity Tests
Regularly testing your equipment's grounding integrity forms an essential cornerstone of any effective cleanroom ESD control program.
To maintain compliance with ANSI/ESD S20.20 and IEC 61340 standards, you'll need to conduct systematic grounding tests using specialized meters and multimeters.
Start by identifying all equipment requiring grounding verification. You'll measure the resistance to ground using a calibrated multimeter or dedicated grounding tester, ensuring readings remain below 1 ohm for proper ESD protection.
Don't forget to document your test results thoroughly for future audits and compliance reviews.
You'll need several key tools to perform these tests effectively: reliable multimeters for resistance measurements, specialized grounding testers, wrist straps for personnel grounding, and anti-static mats for workstation protection.
Make sure you've clearly identified all grounding points throughout your cleanroom facility.
Establish a regular testing schedule that meets your industry's specific requirements.
You'll want to maintain detailed records of all tests, including dates, readings, and any corrective actions taken.
Remember that certification audits will review your documentation to verify compliance with established standards, so keeping accurate records is vital for maintaining your cleanroom's ESD control certification.
Frequently Asked Questions
How Often Should Cleanroom Staff Undergo ESD Control Training Refresher Courses?
You'll need to complete ESD control training refresher courses at least annually. However, if you're handling highly sensitive items or using critical ESD equipment, you may need more frequent training throughout the year.
What Temperature Ranges Can Affect the Performance of Anti-Static Materials?
You'll find that anti-static materials work best at 23±2°C. They can fail above 25°C, while extreme temperatures from -40°C to 800°C can degrade performance. It's essential to maintain stable temperatures.
Can Wireless Devices Interfere With ESD Monitoring Equipment Accuracy?
Yes, your wireless devices can considerably interfere with ESD monitoring accuracy. Cell phones, WiFi, Bluetooth, and RFID systems all generate electromagnetic noise between 1MHz-8GHz, which overlaps with ESD event detection frequencies.
Are There Specific Cleaning Protocols for Maintaining Esd-Safe Flooring Systems?
You'll need to use pH-neutral cleaners, ESD-safe mops, and anti-static vacuums for your ESD flooring. Don't use standard cleaners or excess water, as they'll damage the floor's static-dissipative properties.
How Do Seasonal Changes Impact the Effectiveness of Anti-Static Control Measures?
You'll notice more static issues during winter's dry air. You need to adjust your humidity controls and anti-static measures seasonally, as low humidity drastically reduces the effectiveness of your static control systems.
In Summary
You'll need to regularly conduct these cleanroom anti-static control tests to maintain your facility's ESD protection standards. Make sure you're documenting all test results and addressing any issues immediately. Don't skip scheduled audits – they're essential for protecting sensitive components and maintaining product quality. By following these testing protocols, you're safeguarding your cleanroom operations and ensuring compliance with industry standards.
Leave a Reply