You'll prevent costly cleanroom packaging damage by following three key practices. First, store your materials properly in enclosed stainless steel cabinets with controlled humidity to protect against contamination. Second, handle products using clean technique principles – always double-bag items in clear polyethylene and use nitrogen purging when sealing to maintain sterility. Third, verify packaging quality before distribution by checking seal integrity, proper labeling, and intact vacuum seals. These fundamental steps will safeguard your cleanroom's reputation and protect product quality. Discover more ways to enhance your cleanroom packaging protocols to achieve ideal results.
Proper Storage Methods Matter
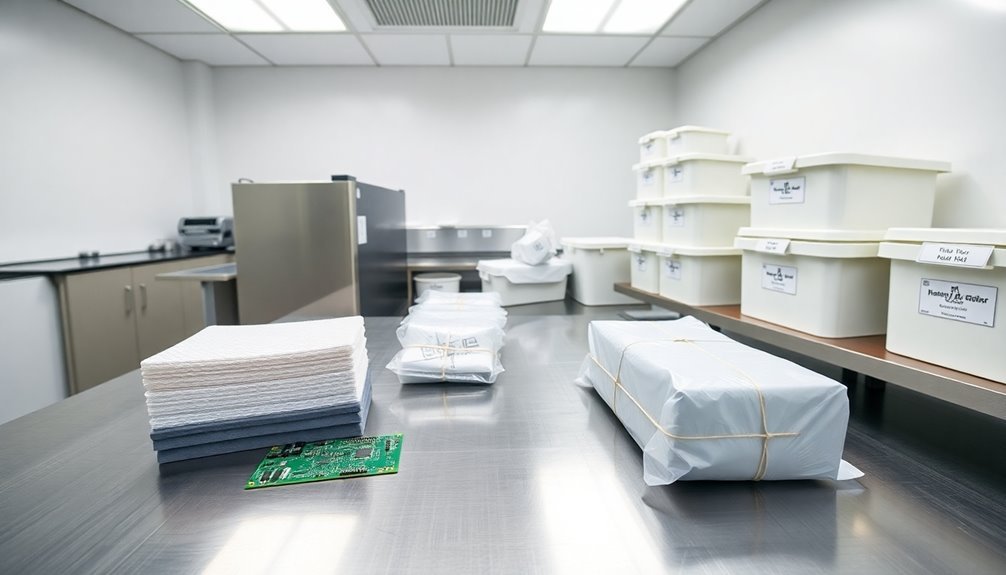
When you're managing a cleanroom environment, proper storage methods can make or break your contamination control efforts. You'll need to implement specialized storage solutions that actively protect your cleanroom wipes and materials from potential contamination sources.
Start by installing enclosed storage units, such as stainless steel cabinets and lockers, to shield your supplies from dust, bacteria, and moisture. You'll want to use cleanroom-specific dispensers like Grab-EEZ that prevent accidental contamination while providing easy access.
For moisture-sensitive materials, you should utilize controlled humidity chambers to maintain ideal conditions and prevent ESD issues. Open wire shelving is recommended to promote adequate air circulation throughout the storage area.
Don't overlook the importance of your storage infrastructure. Install corrosion-resistant stainless steel shelving and modular stackable bins to keep your supplies organized and protected.
You'll need to maintain cleanroom conditions in your storage areas by using fan filter modules with proper internal airflow. For critical components, consider creating a nitrogen-enriched atmosphere to protect against oxygen and humidity damage.
Remember to clean your storage areas and racking surfaces regularly, and keep materials double-bagged in the cleanroom or material transfer area to maintain their integrity.
Handle With Clean Technique
Three fundamental principles guide clean technique handling in cleanroom packaging: material selection, proper sealing, and contamination prevention.
When selecting materials, you'll need to choose between polyethylene options like LDPE, MDPE, HDPE, or SDLDPE based on your product's sensitivity to particles, moisture, and electrostatic discharge. Metalized polyester laminates provide excellent ESD protection while maintaining barcode visibility. Tyvek and transparent paper are excellent alternatives when you require minimal particle contamination.
To maintain sterility, you'll want to implement proper sealing techniques, including nitrogen purging and vacuum-sealing to eliminate unfiltered air.
Double bagging in clear plastic is essential for preventing cross-contamination during transfers. Don't forget to use carton liners to protect against contamination during shipment.
You should always practice flat packaging for easy loading into gown room dispensers and perform thorough visual inspections for any damage or breaches in packaging integrity.
If you suspect contamination during unpacking, follow established cleaning protocols immediately.
Remember that not all PPE and medical-grade products use cleanroom-compliant packaging, so source your materials from trusted suppliers who specialize in controlled environment solutions.
Confirm all your cleanroom products are packed within controlled environments to maintain sterility standards.
Verify Before Distribution
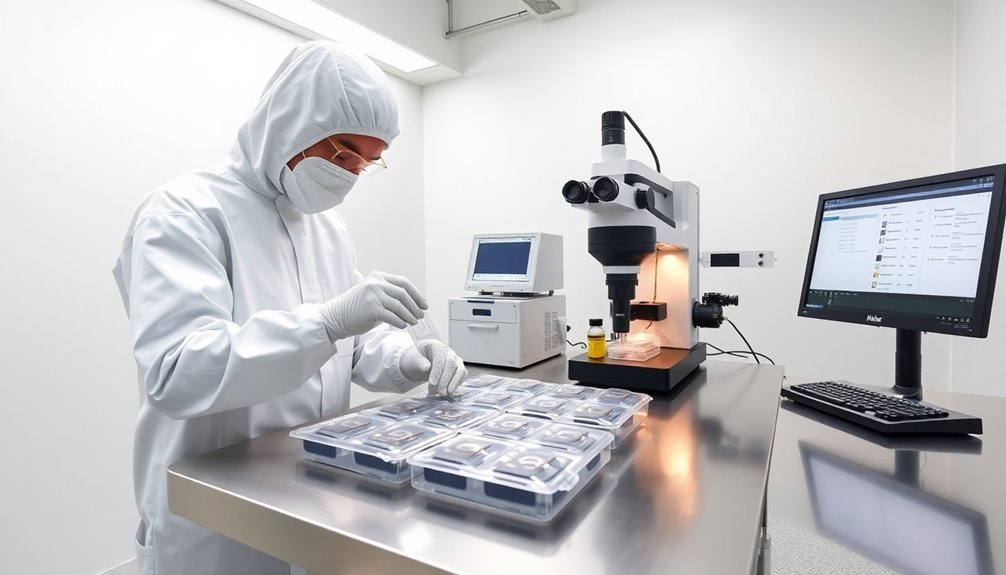
Quality verification checkpoints guarantee your cleanroom products maintain their integrity from packaging through distribution.
You'll need to verify both the packaging materials and structure, confirming sturdy corrugated boxes and proper double or triple-bagging techniques are used. Check that vacuum-sealed inner packs remain intact and carton liners are properly positioned to protect against shipping damage. Nitrogen purging systems ensure product sterility during the packaging process.
Always verify labeling accuracy and traceability elements before distribution. Each package should clearly display product details, lot numbers, and application guidelines. Color-coding systems help you quickly identify product types and their intended use, while batch documentation attached to the exterior ensures proper tracking without compromising sterility.
- Your cleanroom's reputation depends on every package that leaves your facility
- You're the last line of defense against contamination reaching your customers
- You'll sleep better knowing you've thoroughly inspected each shipment
- Your attention to detail prevents costly recalls and rework
- You're protecting not just products, but patient safety and company trust
Conduct thorough visual inspections of packaging integrity, checking for damage or compromise.
Train your team to minimize handling and maintain proper storage conditions.
Frequently Asked Questions
How Often Should Cleanroom Packaging Materials Be Tested for Material Degradation?
You'll need to test cleanroom packaging materials quarterly for bioburden levels, while conducting weekly handling rotations. Don't forget to perform regular integrity tests and monitor storage conditions to prevent degradation risks.
What Temperature Ranges Are Ideal for Storing Different Types of Cleanroom Packaging?
You'll want to store most cleanroom packaging at 20°C-25°C (68°F-77°F). Keep refrigerated items at 2°C-8°C (36°F-46°F), and frozen materials below -15°C (5°F). Never exceed 30°C for standard storage.
Can Automated Packaging Systems Completely Eliminate the Need for Manual Handling?
No, you can't completely eliminate manual handling with automation. While automated systems handle most packaging tasks efficiently, you'll still need human oversight for maintenance, quality control, and handling special or complex situations.
Which Packaging Materials Provide the Best Protection Against Electromagnetic Interference?
You'll get the best EMI protection from conductive metals like copper and aluminum, metalized fabrics, and mu-metal. For complete shielding, consider using conductive coatings or specialized EMI-blocking composite materials.
How Do Different Sterilization Methods Affect the Shelf Life of Cleanroom Packaging?
You'll find that autoclaving reduces shelf life due to material degradation, EtO requires extended outgassing time, while gamma irradiation offers longer shelf life but needs proper storage away from UV light and moisture.
In Summary
You've learned the key elements of clean room packaging that protect sensitive materials from contamination and damage. By storing items correctly, maintaining pristine handling practices, and performing thorough verification checks, you'll guarantee product integrity throughout the distribution chain. Don't skip these essential steps – they're your best defense against costly mistakes and quality issues in your clean room operations.
Leave a Reply