To build a cleanroom protection system, you'll need to follow seven essential steps. Start by evaluating your static control requirements and selecting appropriate ESD protective materials for your facility. Next, design and install a robust grounding infrastructure with copper connections and test points. Install personnel protection equipment including airlocks and gowning areas. Set up environmental controls to maintain proper temperature and humidity levels. Implement thorough monitoring systems to track contamination and environmental parameters. Finally, train your staff on protection protocols and proper cleanroom procedures. These fundamental steps will set the foundation for your cleanroom's success, but there's much more to explore about each component.
Assess Static Control Requirements
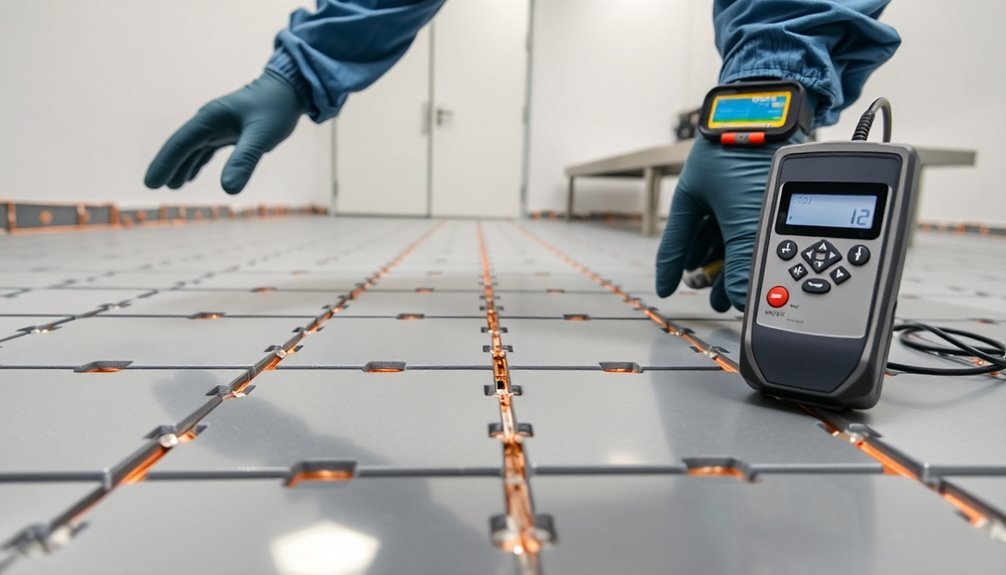
Before implementing a cleanroom protection system, you'll need to evaluate your facility's static control requirements based on specific applications and risks. If you're working in electronics manufacturing, air traffic control, chemical labs, semiconductor production, or medical device manufacturing, you'll require specialized static control measures to protect sensitive equipment and processes.
Your assessment should focus on identifying potential static hazards in your cleanroom environment. While cleanrooms effectively exclude particulates, they can inadvertently generate static electricity through various means. Low relative humidity, the use of gloves that prevent natural static dissipation, and HEPA filtration systems that remove ions from the air all contribute to static buildup.
You'll need to reflect on how these factors impact your specific operations. Pay particular attention to the presence of glass or plastic insulators, as these materials can retain static charges. Static discharge damage can lead to significant financial losses in manufacturing processes.
You'll also need to evaluate how static charges might affect your electronic equipment, as they can cause physical damage, attract contaminants, and generate high-frequency electrical pulses that may corrupt data. Contemplate how personnel movement and interaction with equipment could create static risks that need addressing in your protection system.
Select ESD Protective Materials
You'll need to carefully assess your cleanroom's substrate conditions and conduct proper vapor emission testing before installing ESD flooring materials.
Your selection of installation methods, whether using adhesive-based systems or interlocking tiles like GroundLock Extreme, must align with your facility's specific requirements and downtime constraints. Maintaining comprehensive atmospheric control helps prevent static electricity buildup that can damage sensitive components.
To guarantee ongoing ESD protection, you should regularly test the conductivity of your installed materials using industry-standard resistance meters and maintain detailed performance logs.
ESD Flooring Installation Requirements
Three critical factors drive the selection of ESD protective flooring materials: facility requirements, durability needs, and conductivity specifications. You'll need to start with a thorough pre-installation assessment of your facility's conditions, including moisture levels, subfloor integrity, and environmental factors. This evaluation helps you select appropriate materials and installation methods. The subfloor requires a 90-day cure time for new concrete installations.
Installation Requirement | Key Consideration |
---|---|
Subfloor Assessment | Check for cracks, moisture, contamination |
Material Selection | Match to traffic load and industry standards |
Adhesive Choice | Determine conductive vs. standard options |
Grounding Method | Plan copper strip placement and connections |
Testing Protocol | Define acceptance criteria and test points |
Before installation, you'll need to properly prepare the subfloor by cleaning, repairing any damage, and guaranteeing appropriate moisture levels. When installing ESD flooring, you must follow manufacturer guidelines precisely, particularly regarding adhesive application and grounding methods. Don't forget to document each step of the installation process and conduct post-installation testing to verify compliance with your facility's requirements. Regular maintenance and testing will guarantee your ESD flooring continues to perform effectively throughout its lifetime.
Material Conductivity Testing Methods
Testing material conductivity follows naturally after ESD flooring installation to affirm proper protection levels throughout your cleanroom.
You'll need to verify that all materials meet ANSI/ESD S20.20 and IEC 61340 standards while evaluating your specific environmental conditions and product sensitivity requirements. Grounding and bonding systems must be thoroughly tested to ensure equipotential connections across all conductive surfaces.
The four-point probe technique stands out as your primary testing method for assessing conductive materials.
This approach delivers accurate measurements by applying current through outer probes while measuring voltage drop with inner probes, effectively minimizing contact resistance interference.
Here's what you'll need to focus on when conducting material conductivity tests:
- Set up your testing environment with a non-conductive plastic block and precision current source to guarantee accurate four-point probe measurements.
- Test all conductive materials, including floors, work surfaces, and tools, to verify they'll quickly dissipate static electricity.
- Evaluate your materials according to EN 61340-5-1 and ANSI/ESD S541 specifications, paying attention to both conductivity and static dissipative properties.
- Document your test results and maintain regular testing schedules to affirm continued ESD protection effectiveness.
Remember to evaluate your cleanroom's humidity levels and temperature when interpreting test results, as these factors can greatly impact material conductivity performance.
Design Grounding Infrastructure
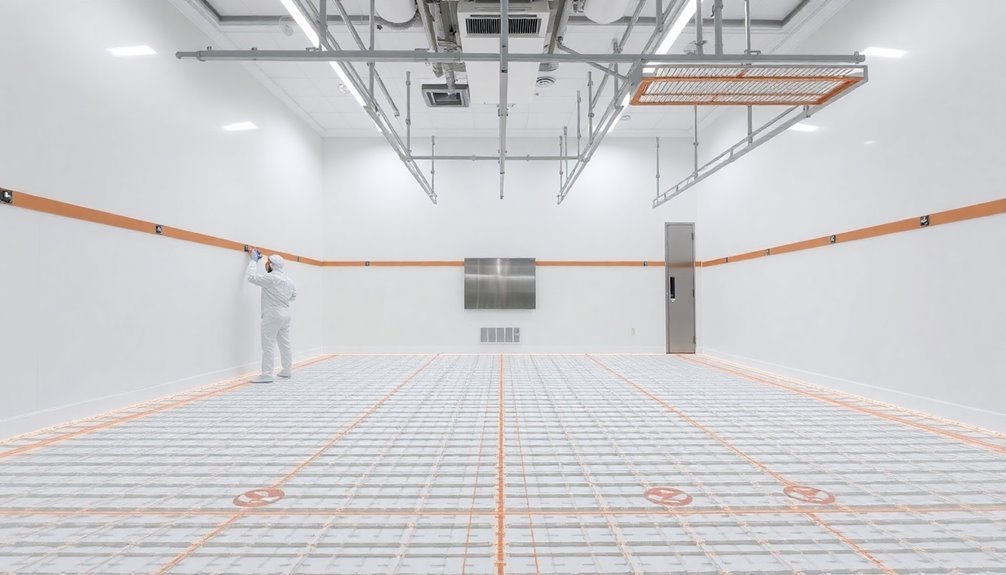
You'll need to install grounding plates and strips strategically throughout your cleanroom, connecting them to create an all-encompassing static control network.
Your grounding infrastructure should include copper wire distribution points at regular intervals to maintain consistent potential across all surfaces and equipment. Low humidity conditions can increase static discharge voltage up to 10 times, making proper grounding essential.
These distribution points must connect to your facility's main ground, ensuring a complete path for static discharge while maintaining the integrity of your cleanroom's protection system.
Grounding Plates and Strips
A robust grounding infrastructure serves as the backbone of any cleanroom's protection system, with grounding plates and strips playing a critical role in managing static electricity. You'll need to select high-conductivity materials like copper or stainless steel for your grounding components, guaranteeing they're properly integrated with your cleanroom's flooring, walls, and equipment.
- Install grounding plates strategically throughout your cleanroom, focusing on areas beneath anti-static flooring and near sensitive equipment. The design should align with environmental control parameters to maintain optimal conditions. Maintain smooth, clean surfaces to prevent dust accumulation and guarantee effective electrical contact.
- Connect all grounding components to form a thorough network, securing them firmly to prevent disconnection or movement over time. You'll need to verify proper electrical bonding to the main grounding system.
- Test your grounding system thoroughly before operation, and implement a regular maintenance schedule to prevent degradation. This includes checking connections, cleaning surfaces, and verifying conductivity levels.
- Integrate your grounding infrastructure with other cleanroom systems, including HVAC and monitoring equipment. You'll want to guarantee compatibility between all components while maintaining compliance with ISO 14644 standards and local electrical codes.
Static Control Network Design
Effectively designing a static control network requires a thorough understanding of electrostatic discharge risks and their potential impact on cleanroom operations.
You'll need to implement a detailed approach that addresses static electricity at every level of your cleanroom design. Start by incorporating conductive materials into your foundational elements.
You'll want to use specialized flooring, walls, and furniture that can safely channel static charges to ground. Install ionizing blowers and air showers strategically throughout your cleanroom to neutralize static electricity before it accumulates.
The strategic placement of air showers with ionisation enhancement systems significantly improves their effectiveness in removing static charges. Don't forget to integrate ESD monitoring equipment to track static levels in real-time. Your static control network should include proper air flow patterns to prevent pressure differentials that could spread contaminants.
You'll need to select ESD-safe equipment, including gloves, footwear, and furniture, to maintain a static-free environment. Make sure you're using dissipative materials that allow controlled discharge of static electricity.
Remember to address static control from the initial design phase. You'll save time and money by sizing your cleanroom correctly and choosing appropriate materials like heat-welded vinyl floors that support your static control goals while meeting regulatory requirements.
Copper Wire Distribution Points
Proper distribution of copper wiring throughout your cleanroom requires strict adherence to critical spacing and separation guidelines.
You'll need to maintain at least 0.6m between power distribution facilities under 100A, while those above 100A must be separated by no less than 1m. It's crucial to lay electrical wires separately for clean versus non-clean areas, main versus auxiliary production spaces, and contaminated versus clean zones. Installing mineral insulated cables separately is essential in flammable environments.
Here's what you'll need to focus on for effective copper wire distribution:
- Never weld bracket bolts onto building steel structures when fixing distribution lines – instead, use appropriate mounting hardware that won't compromise structural integrity.
- Connect your grounding (PE) or zero-connecting (PEN) branch lines individually to their corresponding trunk lines, avoiding series connections.
- Install steel casings where grounding wires pass through building envelopes or floors, ensuring these casings are properly grounded.
- Seal all electrical conduits passing through building envelopes with non-shrinking, non-combustible materials, and make sure wiring openings into clean rooms are closed with non-corrosive, dust-free materials.
For cleanliness control, you'll need to embed all switchboards, control panels, and switch boxes, making sure their surfaces remain smooth and easy to clean.
Install Personnel Protection Equipment
Before entering a cleanroom environment, you'll need to follow precise gowning procedures and install essential personnel protection equipment (PPE).
Start by installing no-touch hand washing and drying stations at entry points, along with designated gowning areas that include storage for cleanroom-specific suits, gloves, and booties.
Set up air showers and sticky mats at changeover points to reduce particle contamination.
You'll need to install storage units for different PPE sizes, including cleanroom suits appropriate for your ISO class – frocks for ISO Class 7 or full coveralls for ISO Class 5.
Install closed storage systems for bouffants, beard covers, and shoe covers near the gowning area.
Make certain you've installed proper disposal bins for used PPE and establish cleaning stations with appropriate chemical solutions for maintaining reusable items.
You'll need to mount protocol charts showing the correct gowning sequence, starting from top to bottom.
Install storage lockers outside the cleanroom for personal items like jewelry, phones, and keys.
Don't forget to set up glove washing stations with alcohol solutions and regularly maintained cleaning supplies to guarantee ongoing PPE maintenance.
Establish Environmental Control Parameters
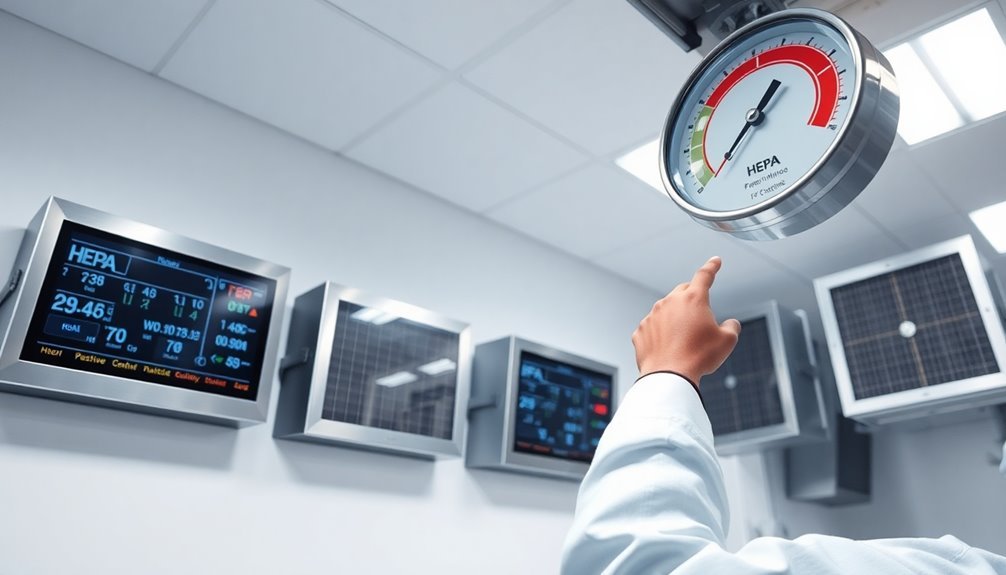
The core environmental parameters for your cleanroom must meet strict control standards across temperature, humidity, and air quality.
You'll need to maintain temperatures around 70°F (21°C) for standard cleanrooms, while aerospace facilities require a broader range of 67°F to 77°F. Your humidity control systems should keep relative humidity between 30-40% for standard operations or 40-60% for aerospace applications.
- Monitor your temperature consistently to prevent fluctuations that could compromise production standards and increase particle release from uncomfortable workers.
- Install robust humidification and dehumidification systems to combat risks of bacterial growth, corrosion, and static electricity that come with poor humidity control.
- Implement high-efficiency air exchange systems with steam distribution lances to guarantee proper air mixing and maintain consistent environmental conditions.
- Set up written specifications with clear action limits and corrective measures for when parameters fall outside acceptable ranges.
You'll need regular certification from independent agencies to verify your environmental controls meet industry standards.
Don't forget to establish a maintenance schedule for cleaning and system upkeep, as these are essential for maintaining your cleanroom's environmental integrity.
Implement Monitoring Systems
Building on your established environmental parameters, implementing an extensive monitoring system creates a foundation for consistent cleanroom performance.
You'll need to determine your monitoring requirements based on your cleanroom's classification and identify essential parameters like temperature, humidity, pressure, and particle counts.
Select your monitoring equipment carefully, guaranteeing it matches your cleanroom's specifications.
You'll want automated particle counters with remote monitoring capabilities and appropriate sensors for each parameter you're tracking.
Make sure your system can integrate with your building management system and is scalable for future expansion.
When implementing the system, conduct a strategic risk assessment to determine ideal sensor placement.
Follow GAMP V model guidelines during installation and guarantee your system provides real-time feedback with instant alerts.
You'll need to verify that all components comply with relevant regulations, particularly FDA CFR 21 Part 11 for software requirements.
Don't forget to establish a maintenance schedule for your monitoring system.
You'll need to regularly calibrate sensors according to ISO 17025 standards, secure data transfers, configure alarm behaviors, and keep all software updated.
This guarantees your system remains accurate and reliable over time.
Train Staff On Protection Protocols
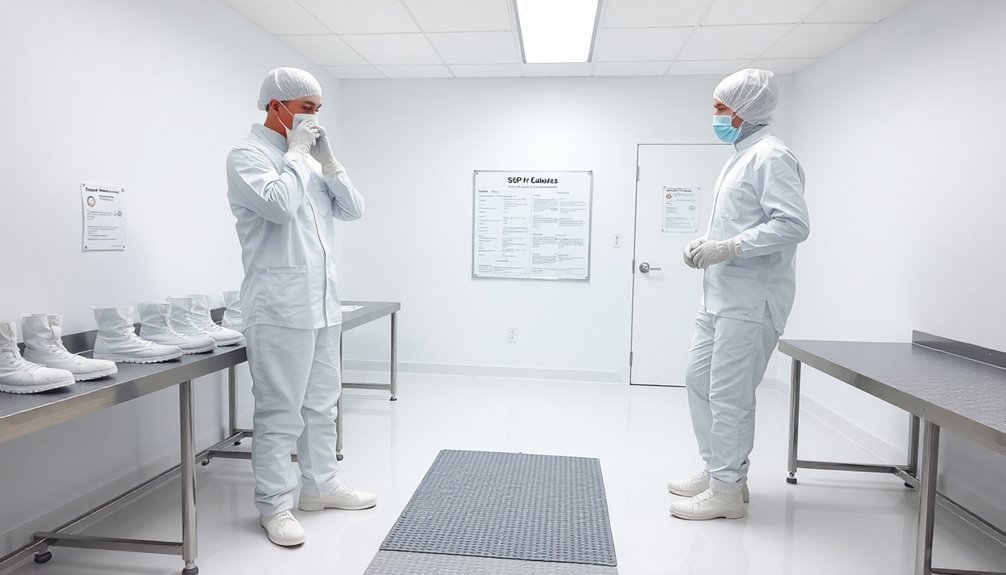
Professional competence in cleanroom operations hinges on thorough staff training protocols. You'll need to guarantee your staff understands both the technical aspects and behavioral requirements of working in a controlled environment. Your training program must cover everything from personal hygiene standards to complex decontamination procedures, with regular assessments to validate compliance.
- Start with strict selection criteria, focusing on staff accreditation and personal character traits that align with cleanroom discipline.
- Implement extensive gowning protocols, teaching proper techniques for wearing cleanroom attire, including gloves and face masks.
- Train your team on contamination control, emphasizing minimal touch points and proper handling of supplies and equipment.
- Establish regular testing routines using contact plates and finger dabs to verify protocol adherence.
Your staff must master entry and exit procedures, including proper handwashing and air shower usage.
You'll need to maintain detailed documentation of all training sessions and refresher courses.
Don't forget to include incident reporting procedures and decontamination training for selected personnel.
Regular audits and assessments will help you maintain high standards and identify areas for improvement in your protection protocols.
Frequently Asked Questions
How Often Should Cleanroom Protection Systems Undergo Complete Recertification?
You'll need annual certification for ISO 6 and above cleanrooms, while ISO 5 and below require certification every six months. Additionally, you must recertify after any significant changes or upgrades to your system.
What Are the Cost Implications of Upgrading From ISO Class 8 to 7?
You'll face significant costs ranging from $100-$1,000 per square foot, plus increased HEPA filter expenses and higher maintenance costs. Don't forget additional expenses for enhanced cleaning protocols and infrastructure modifications.
Can Existing Office Spaces Be Converted Into Cleanroom Facilities?
Yes, you can convert your office space into a cleanroom facility using modular panels and HardWall systems. You'll need proper planning, surface upgrades, and expert installation to meet the required ISO classification standards.
How Do Emergency Evacuation Procedures Differ in Cleanroom Environments?
You'll need to follow stricter protocols in cleanroom evacuations. Don't remove protective gear during exits, immediately halt critical operations when alarms sound, and use designated routes while maintaining contamination control procedures.
What Backup Systems Are Essential for Cleanroom Protection During Power Outages?
You'll need UPS systems for critical equipment, backup generators for HVAC, battery backup for emergency lighting, and redundant power systems. Don't forget to prioritize air handlers and primary engineering controls.
In Summary
You'll need ongoing commitment to maintain your cleanroom's protection system. Review and update your protocols regularly, train new staff thoroughly, and monitor your environmental controls daily. Don't skip routine maintenance of your grounding infrastructure and ESD protective materials. Keep detailed logs of all system checks and immediately address any issues that arise. Your diligence will safeguard your cleanroom's integrity.
Leave a Reply