To clean antistatic cleanroom surfaces effectively, you'll need to follow a systematic process. First, remove all debris using a HEPA vacuum, working from high to low areas. Then, gather cleanroom-grade supplies and wear proper ESD-safe attire, including wrist straps and garments. Apply antistatic cleaning solutions using the quarter-fold technique with parallel, overlapping passes. Let surfaces dry for 20-30 minutes before rinsing with IPA wipes or clean water. Don't forget to maintain humidity levels between 40-60% and regularly test surface resistance. Following these essential steps will help you master the complete cleanroom maintenance protocol.
Essential Cleanroom Surface Preparation
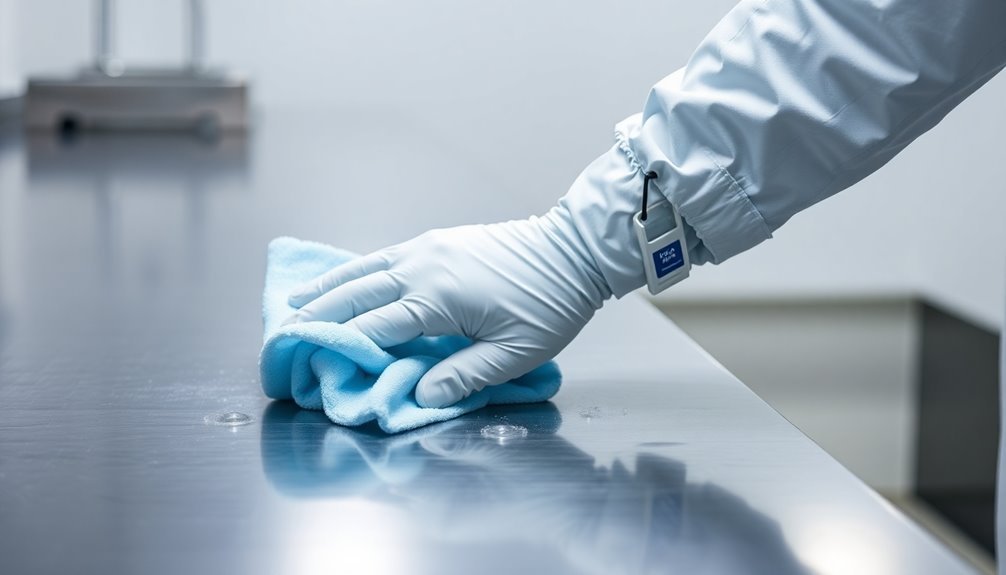
Before beginning any cleanroom surface cleaning tasks, proper preparation is essential to confirm effective antistatic cleaning and contamination control.
You'll need to start by removing all visible debris, tools, equipment, and waste materials from the cleanroom environment. Use a HEPA-filtered vacuum cleaner to eliminate dust and particulates, working from the highest points downward. Implementing a top to bottom cleaning approach ensures debris falls onto uncleaned surfaces.
You'll want to gather all necessary cleanroom-grade cleaning supplies, including appropriate cleaning agents and lint-free disposable wipes. Select cleaning agents that match your specific needs – fungicides for spores, degreasers for oils, and proper disinfectants for biological contaminants.
When preparing your cleaning solutions, follow manufacturer specifications for dilution and consider factors like temperature and pH levels that affect their efficacy.
Remember to work systematically from the cleanest areas toward dirtier zones to prevent cross-contamination.
Don't forget to wear proper cleanroom attire, including gloves, gown, and face mask. You'll need to confirm your cleaning materials are compatible with the cleanroom environment and won't generate particles or lint.
Pre-wet your wipes with the appropriate cleaning agent and maintain a consistent wiping pattern with 10-25% overlap.
Choosing Static Control Products
Selecting effective static control products requires careful consideration of your cleanroom's specific needs and ESD risks.
You'll need to implement a combination of flooring, garments, and equipment to create a thorough static control system.
Start with your flooring choices by installing either conductive or static dissipative vinyl that matches your required resistance levels.
Complement this with ESD-safe garments featuring conductive threads and appropriate footwear to prevent static buildup during movement.
Don't forget to equip your staff with grounding wrist straps and heel straps for additional protection.
For active static neutralization, you'll want to invest in ionizing equipment such as air guns, bars, and blowers.
These tools effectively eliminate static charges in your workspace.
Install air shower systems at entry points to control static before personnel enter the cleanroom.
Regular use of static neutralizing tools like blow-off guns and fans helps maintain optimal static control conditions.
Maintain proper storage solutions by using ESD-safe cabinets, totes, and dispensers.
Apply conductive tapes for sealing sensitive materials, and install anti-static wall panels with storage bins where needed.
Keep humidity levels between 40-60% to naturally reduce static buildup.
Remember to select ESD-safe furniture, including cleanroom seating, to complete your static control measures.
Proper Cleaning Methods
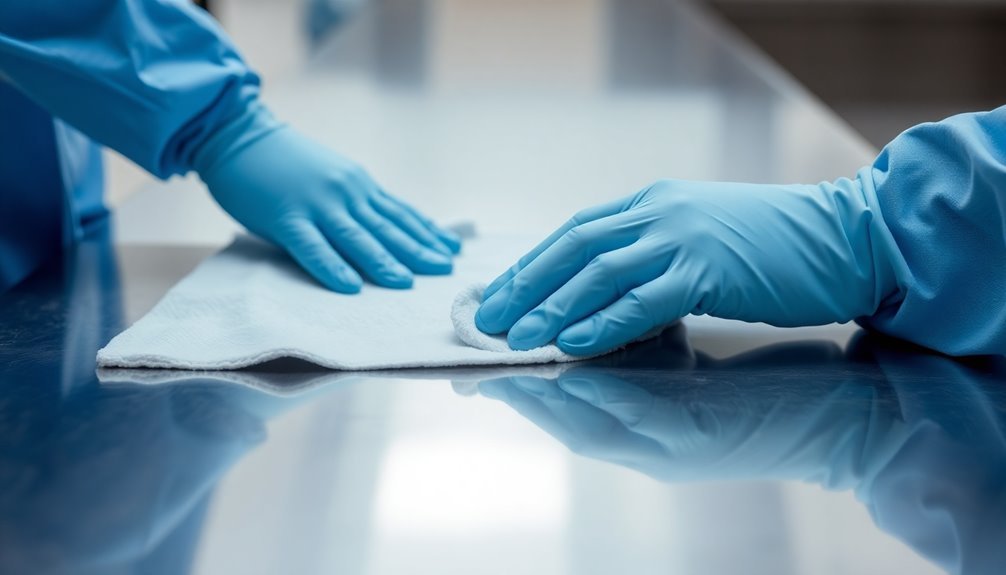
Effective cleanroom surface cleaning demands a systematic approach to maintain static-free conditions.
You'll need to start by removing loose debris using disposable wipes or water, always wearing gloves to prevent contamination from hand oils and salts. Before cleaning, evaluate your surface type and confirm you've removed any existing static charges from raw plastic and fiberglass parts.
When cleaning, use the quarter-fold technique with your wipes to maximize clean surface area. Apply parallel, overlapping passes with a pull-and-lift motion, working from the cleanest to least clean areas and from top to bottom. For irregular surfaces, confirm thorough contact and clean several inches around the target area. Ensure wipes overlap by 10% to 25% for optimal coverage.
After applying specialized anti-static cleaners, allow 20-30 minutes for surfaces to dry completely.
You'll need to rinse the surface with clean water or IPA wipes, followed by thorough drying with a clean cloth. Don't forget to dispose of used rags in sealed containers to prevent spontaneous combustion.
Finally, inspect the surface to confirm it's free of contaminants and maintain it regularly through proper dusting and vacuuming to prevent recontamination.
Disinfection Best Practices
Cleanroom disinfection protocols require strict adherence to material compatibility and contamination control. You'll need to select disinfectants that match specific hazards while considering surface compatibility and ESD requirements. For best results, implement a multi-step process starting with thorough cleaning before applying disinfectants. Monthly cleaning must be performed for areas beneath work trays to maintain contamination control standards.
Process Step | Agent Type | Key Considerations |
---|---|---|
Initial Clean | Detergent | ESD-safe formulation, surface compatibility |
Disinfection | IPA/H2O2 | 70% IPA or 3% H2O2, avoid mixing agents |
Sanitization | Quaternary/Phenolic | Never combine, rotate as needed |
Final Rinse | Sterile DIW | Complete residue removal |
When applying disinfectants, use controlled motions aligned with room airflow patterns to prevent particle attraction. You'll want to wipe surfaces in slow, overlapping strokes for maximum effectiveness. For specialized equipment or large areas, consider UV irradiation or autoclave sterilization. Don't forget to protect your floors using shoe cleaners and sticky mats to minimize contaminant introduction. After disinfection, always remove any residues using sterile DIW or 70% IPA to prevent surface damage and maintain cleanliness standards.
Testing and Validation Steps
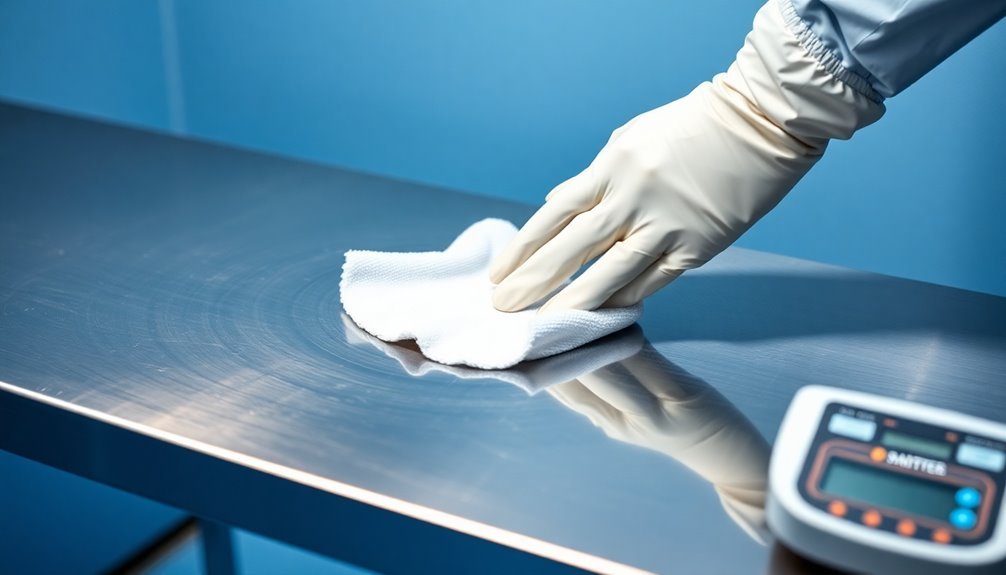
When testing your cleanroom surfaces, you'll need to carry out both ESD resistance validation and surface cleanliness verification.
Regular combo tester checks should be performed on personnel entering the cleanroom area. Start with ESD testing using the ANSI/ESD S4.1 standard, which requires both resistance top-to-top (RTT) and resistance-to-groundable point (RTG) measurements. Place two 5-pound electrodes 10 inches apart, keeping them 2 inches from edges and 3 inches from grounded points. Your readings should fall between 1 x 10^6 and 1 x 10^12 ohms for static dissipative materials.
For surface cleanliness validation, you'll first need to establish baseline measurements and define critical parameters for your specific cleanroom requirements.
Remove visible contaminants through thorough cleaning and decontamination protocols. When performing swab tests, use laundered polyester knit fabric swabs for ideal recovery rates. Moisten the swab head without saturating it, then swab a 5cm by 5cm area using consistent horizontal, vertical, and diagonal patterns.
Place your swabs in collection vials for analysis. Don't forget to maintain regular airborne particle and microbial monitoring to guarantee your cleanroom continues meeting required standards.
Remove all ESD-sensitive devices before conducting any tests.
Frequently Asked Questions
How Often Should Antistatic Cleaning Solutions Be Replaced During Continuous Use?
You'll need to replace your antistatic cleaning solutions every 2-4 weeks during continuous use. Don't forget to monitor surface resistance measurements and adjust replacement frequency based on your specific cleanroom's traffic and contamination levels.
Can Antistatic Cleanroom Surfaces Be Cleaned With Standard Household Cleaning Products?
No, you shouldn't use household cleaning products on antistatic cleanroom surfaces. They'll damage antistatic coatings, generate static, and introduce harmful contaminants. Instead, you must use specialized cleanroom-approved cleaning solutions for proper maintenance.
What Temperature Ranges Affect the Effectiveness of Antistatic Cleaning Solutions?
You'll find antistatic cleaning solutions work best between 20-45°C (68-113°F). If you use temperatures above 60°C (140°F), you'll reduce their effectiveness and potentially damage the antistatic properties of your surfaces.
Do Different Colored Cleanroom Surfaces Require Different Antistatic Cleaning Approaches?
No, you don't need different cleaning approaches for different colored surfaces. Surface color doesn't affect antistatic cleaning methods – it's the material type and contamination level that determine which cleaning approach you should use.
How Do Seasonal Changes Impact the Maintenance of Antistatic Properties?
You'll need to increase your maintenance during dry winter months since low humidity raises static charges. It's crucial to adjust your cleaning frequency and antistatic treatments to combat seasonal drops in relative humidity.
In Summary
You're now equipped to maintain antistatic cleanroom surfaces effectively. Remember to check your cleaning products' ESD ratings, follow proper contact times, and validate your work through regular testing. Don't skip surface preparation steps, as they're essential for ideal results. By implementing these practices consistently, you'll protect sensitive equipment and maintain the cleanroom's controlled environment to ISO standards.
Leave a Reply