Your antistatic facility inspection should cover several critical areas to maintain ESD protection. You'll need to test antistatic flooring resistance with a megohmmeter to verify compliance with ANSI/ESD standards, inspect workstation grounding systems for proper connections, and check personnel testing equipment like wrist straps and foot grounders. Don't forget to evaluate ESD protected area boundaries, review static control documentation, and verify proper material handling procedures. Regular checks of equipment calibration records, ESD protective packaging, and ionization system maintenance are also essential. Understanding these inspection components will help you build a thorough ESD control strategy.
Antistatic Flooring Assessment
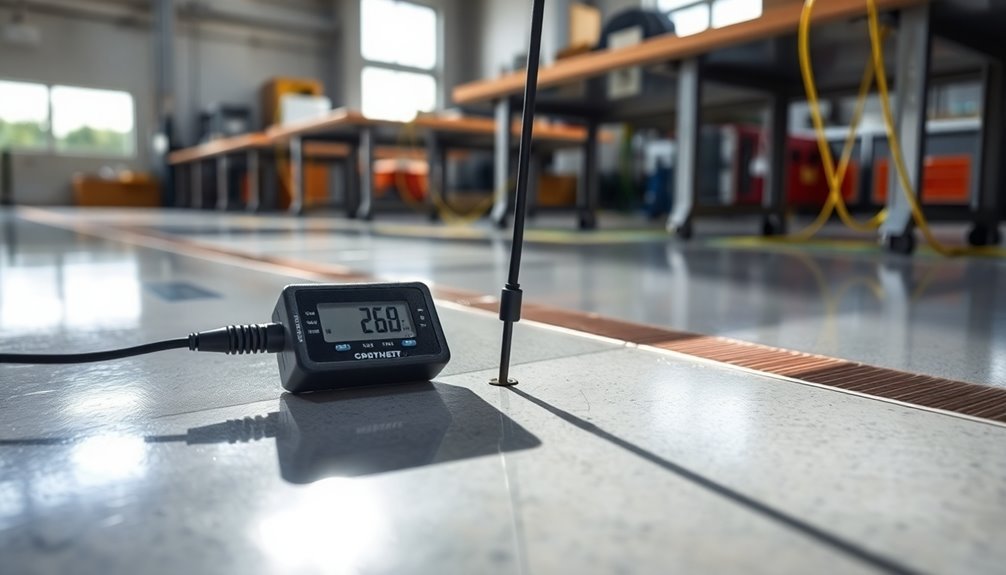
With safety and performance in mind, evaluating antistatic flooring requires a systematic approach that examines multiple critical factors.
You'll need to start with surface resistance testing using a megohmmeter or resistance meter to verify if your floors meet essential standards like ANSI/ESD STM 7.1 and BS EN 61340-5-1. Conducting regular testing helps ensure long-term reliability of your ESD protection system. Confirm your conductive floors measure less than 1.0 x 10^6 ohms, while static dissipative floors should fall between 1.0 x 10^6 and 1.0 x 10^9 ohms.
Don't stop at resistance testing alone. You'll want to conduct walking tests and body voltage measurements to assess real-world performance.
Consider how environmental factors like temperature and humidity affect your floor's conductivity. Check if your flooring requires ongoing treatments, such as special waxes or sprays, as these maintenance requirements impact long-term effectiveness.
Examine the floor's durability, particularly in high-traffic areas or where you're using soldering equipment and harsh chemicals. Look for signs of wear that might compromise its static control properties.
Remember to document your findings and compare them against industry-specific requirements for your facility's particular needs.
Workstation Grounding Systems
You'll need to examine ground points and connectors to verify proper connections through metallic crimps, snaps, and banana plugs at each ESD workstation.
Regular evaluation of ESD control performance helps maintain consistent safety standards across all workstation installations.
When testing the grounding system's resistance, you must confirm compliance with ANSI/ESD S6.1 requirements and document the measurements at each connection point.
Your ESD mat installation should follow a proper two-step grounding process, connecting both the work surface and floor mats to a common ground point using appropriate grounding cords or copper foil strips.
Ground Points and Connectors
Ground points and connectors serve as the backbone of any effective ESD workstation grounding system. When you're inspecting these vital components, you'll need to verify that all elements connect to a common point ground, which must link to the equipment grounding conductor.
Check that your facility isn't using isolated ground receptacles, as these can compromise your ESD protection system.
You'll want to examine all grounding materials, including ground cords, wrist straps, and footwear, ensuring they meet specific resistance requirements. The current limiting resistor in wrist strap ground cords should be checked to confirm it maintains the standard 1 megohm safety rating. Make sure all equipment connects properly to the common point ground to eliminate potential differences. If your facility uses auxiliary grounds, verify they're correctly bonded to the equipment grounding conductor.
During your inspection, pay special attention to the connectors' condition and fit. You shouldn't find any loose connections or alligator clips being used as permanent solutions. Look for proper installation of copper tape and grounding plates where needed, particularly in flooring applications.
Don't forget to evaluate the entire grounding path's integrity, ensuring continuous connectivity from personnel through wrist straps and worksurface mats to the common point ground. Your inspection should confirm compliance with ANSI/ESD S6.1 and JEDEC Standard No. 625-A requirements.
Resistance Testing Requirements
A thorough workstation grounding system inspection requires specific resistance testing protocols to verify its effectiveness.
You'll need to perform both RTT and RTG tests on ESD mats, guaranteeing they maintain a surface resistance between 1.0 x 10^6 and 1.0 x 10^9 ohms to ground. These measurements must comply with ANSI/ESD STM4.1 and STM4.2 standards. Latent defects and failures can occur if proper resistance testing is neglected.
You should regularly test your wrist straps to confirm they're maintaining a total system resistance below 35 megohms.
For personnel using foot grounders, verify they're wearing them on both feet and that they're making proper contact with the ESD flooring. Your body voltage testing must show readings under 3.5 x 10^7 ohms.
When inspecting workstation grounding setups, check that all conductive and dissipative items are electrically bonded to a common point ground.
Verify your ground cords have secure connections using metallic crimps or banana plugs.
You'll want to guarantee continuous monitoring systems are functioning correctly to maintain proper grounding of both personnel and equipment.
Remember to document all resistance measurements as part of your compliance with IEC61340-5 standards.
ESD Mat Installation
Proper ESD mat installation begins with selecting the right mat type for your specific workstation needs.
You'll need to take into account whether you're installing table mats for electronics handling or floor mats for standing areas. Confirm you're placing them in areas where static-sensitive work occurs, covering entire work surfaces completely. Maintaining optimal humidity levels between 40-60% helps maximize mat effectiveness.
Before installation, prepare your surfaces by cleaning them thoroughly and removing all debris.
You'll need to install grounding snaps at regular intervals, typically every 10 feet for longer mats. Connect these to your facility's common ground point using dedicated grounding cables, and verify the connections using continuity testers.
Your mat installation should be part of a thorough ESD control system.
Make certain you're connecting all workstation components to the same electrical ground point, including ionizers, wrist strap grounds, and other ESD equipment.
Don't rely on temporary connections like alligator clips for permanent installations. Instead, use proper grounding hardware following manufacturer specifications.
Remember to test the installation thoroughly before use.
Check resistance readings and verify that your ground connections are secure and properly terminated. This confirms your ESD protection system will function effectively when handling sensitive components.
Personnel Testing Equipment
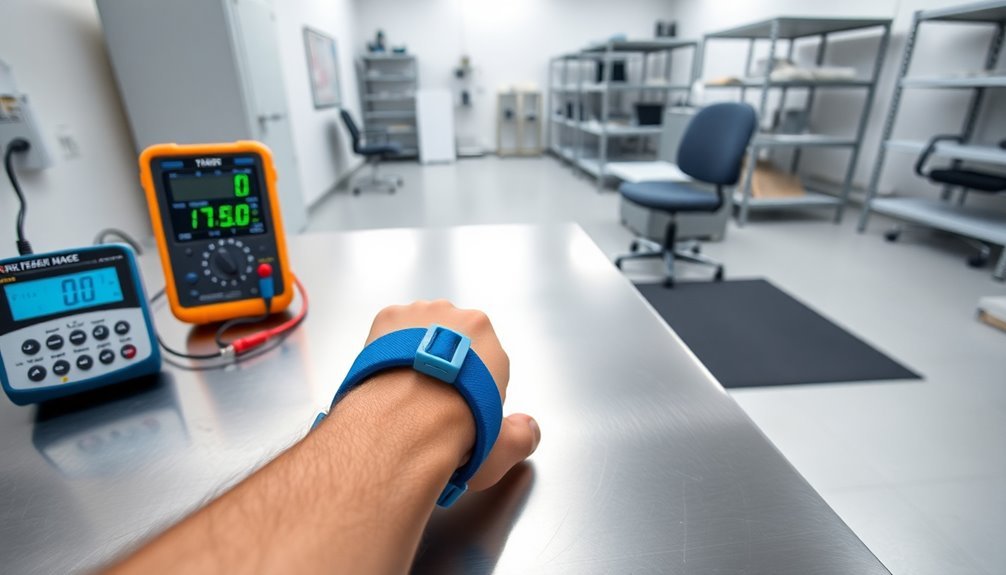
You'll need to test your ESD wrist straps daily using a dedicated wrist strap tester to verify proper grounding and functionality.
Your footwear must also undergo regular resistance verification using footplate testers to confirm they meet static control standards.
These personnel testing requirements help maintain consistent ESD protection and prevent potential damage to sensitive electronic components.
Comprehensive testing stations are available with wall mount options to ensure efficient and convenient verification of both wrist straps and footwear.
Wrist Strap Testing Requirements
To guarantee the safety and effectiveness of ESD protection, personnel must regularly test their wrist straps using standardized testing equipment.
You'll need to ascertain your wrist straps maintain resistance between 750,000 ohms and 35 megohms, as specified by ANSI/ESD S20.20 standards. Regular training sessions should be conducted to ensure proper ESD awareness and testing procedures. Testing should be performed daily before beginning work in simple EPAs, while some facilities use continuous monitoring systems that provide real-time alerts for connection problems.
When testing your wrist straps, you should watch for both high and low resistance failures. High resistance failures can result from soiled wristbands, poor skin contact, or damaged coil cords, potentially leading to dangerous voltage buildup.
Low resistance readings below 750,000 ohms might indicate a shorted resistor or an unwanted ground path, compromising the safety function of the 1-megohm current-limiting resistor.
You'll need to document your test results to track EPA effectiveness and maintain compliance.
Whether you're using portable testers or wall-mounted stations, your testing equipment must meet current industry standards and provide clear pass/fail indicators. This documentation helps identify trends and ascertains your facility maintains proper ESD protection protocols.
Footwear Resistance Verification
Testing footwear resistance requires three essential pieces of equipment: ESD testers, calibrated resistance meters, and verification devices. You'll need to verify antistatic footwear properties according to standards like EN ISO 20345 and ASTM F2413, guaranteeing your facility maintains proper ESD protection.
When testing footwear, you must first condition the shoes in a controlled environment. Fill them with stainless steel balls and apply 100V DC for one minute while measuring contact resistance between a copper plate and the balls. Regular cleaning and maintenance of shoes is essential as dirty contact areas can significantly impact measurement accuracy. Remember that environmental factors can affect your results, so maintain consistent temperature and humidity levels during testing.
Test Condition | Requirements | Classification |
---|---|---|
Dry State | <1x10^8 O | Antistatic |
Wet State | >1×10^5 Ω | Antistatic |
Dry State | <1x10^5 O | Conductive |
Wet State | >1×10^3 Ω | Conductive |
Both States | >1×10^9 Ω | Insulating |
Your testing equipment must be regularly calibrated and maintained to guarantee accurate readings. Keep testing surfaces clean and conductive, as contaminants can interfere with measurements. Don't forget to document your results according to relevant standards like EN 61340-5-1 or EN 61340-4-3.
ESD Protected Area Boundaries
ESD Protected Area (EPA) boundaries serve as critical control points in antistatic facilities. You'll need to guarantee these boundaries are clearly marked using visible indicators like signs, floor tapes, or distinctly colored floor tiles.
Your EPA boundaries define where all surfaces, objects, and people must maintain the same electrical potential to prevent static discharge incidents.
When you're inspecting EPA boundaries, verify that all entry points are properly designated and that required ESD control items are present. Check that the area contains essential components including ESD working surface mats, grounding cords, wristbands, and a common point ground system.
All materials within these boundaries should be groundable with resistance less than 10^9 ohms.
You'll want to confirm that your EPA follows ANSI/ESD S20.20 guidelines and incorporates proper testing methods for all ESD control equipment. Make sure you've removed any unnecessary non-conductors and replaced them with dissipative or conductive materials.
During your inspection, verify that all conductors are properly grounded and bonded. Don't forget to check that your continuous monitoring systems are functioning correctly to validate grounding effectiveness throughout the protected area.
Static Control Documentation
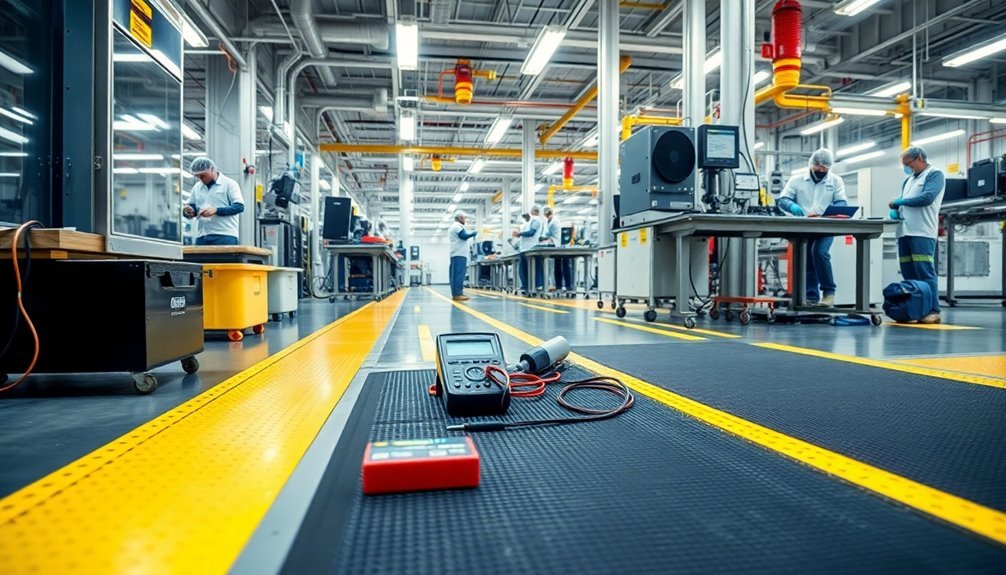
Within any antistatic facility, proper documentation forms the backbone of an effective static control program. You'll need a thorough written ESD Control Plan that outlines both administrative and technical requirements, with clear identification of the lowest ESD device sensitivity levels you're handling.
Make sure you've designated and documented an ESD Program Manager to oversee your static control efforts.
Your documentation should include detailed training records for all personnel who handle ESD-sensitive items. You'll want to maintain proof of both initial and recurring training sessions that cover ESD control principles, procedures, and awareness of ESD damage risks.
Don't forget to document any deviations from standard procedures, including tailoring statements and rationales.
Keep detailed records of your static control materials and equipment specifications, including resistance measurements for worksurfaces and verification of proper grounding connections.
You'll need to maintain logs of regular testing and maintenance for all ESD control equipment. Your documentation must also include audit findings and subsequent corrective actions, demonstrating your facility's compliance with standards like ANSI/ESD S20.20-2014.
Remember to regularly review and update your ESD Control Plan to reflect any changes in procedures or requirements.
Environmental Monitoring Systems
Building on your documented ESD control procedures, you'll need robust environmental monitoring systems to maintain and verify proper facility conditions. These systems combine specialized sensors, data collection hardware, and monitoring software to track critical environmental parameters that affect static control effectiveness.
Your facility's environmental monitoring system should strategically position sensors throughout the workspace to provide thorough coverage. You'll want temperature sensors at multiple heights, humidity sensors near air handling points, and specialized sensors for tracking other relevant metrics. The system should integrate with your building management system (BMS) for centralized control and real-time monitoring.
To guarantee your environmental monitoring system performs at its best, focus on these key aspects:
- Regular sensor calibration and maintenance to maintain accuracy and reliability
- Strategic placement of sensors in critical areas like work stations, storage areas, and near sensitive equipment
- Implementation of real-time alerts and automated responses to environmental changes that could compromise static control
With proper environmental monitoring in place, you'll be able to quickly identify and address conditions that could lead to static-related issues, maintaining compliance while protecting sensitive components and processes.
Material Handling Procedures
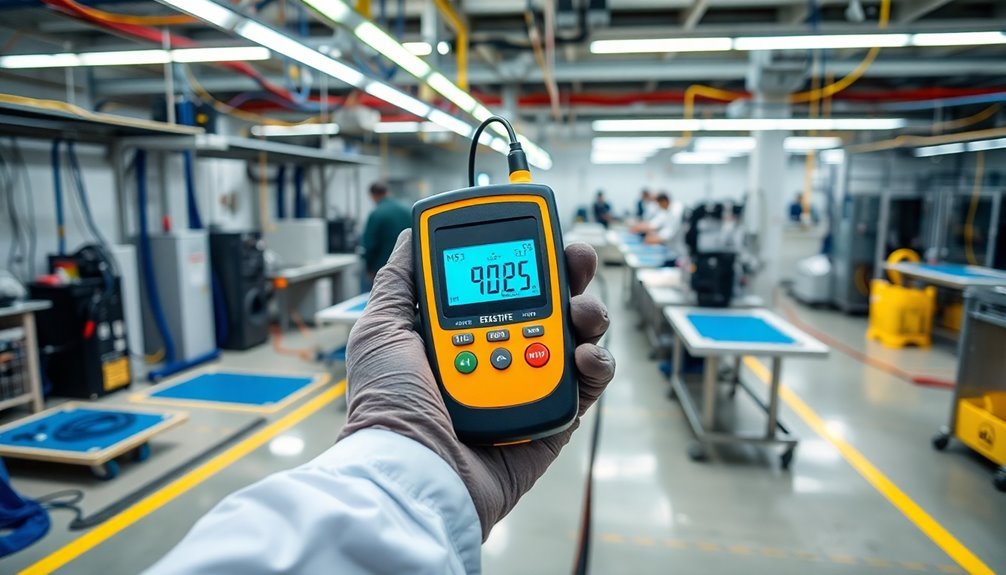
Proper material handling procedures represent a critical line of defense against static damage in your antistatic facility. You'll need to implement strict protocols starting from receiving through production to guarantee thorough ESD protection.
Begin by verifying that incoming components arrive in appropriate ESD-protective packaging. Remove non-ESD materials like bubble wrap and packing peanuts immediately, and repackage items in shielded containers if necessary. Don't forget to clearly mark packages with ESD warning labels to alert handlers.
Your storage areas must feature grounded shelving with dissipative bins and storage boxes. Ascertain your staff uses heel grounders or ESD floor mats while handling components.
When transporting ESDS items, you'll need ESD-safe carts with proper covers, and all transport equipment should maintain ground contact with your ESD flooring.
In production areas, you must maintain ESD-safe workstations where components can be safely removed from shielding bags. Install grounded conveyors and dissipative trays throughout your production line.
Mark your ESD-protected areas clearly with appropriate signage and floor tape, and verify that your entire production system maintains proper grounding connections.
Equipment Calibration Records
Your test equipment's accuracy must be verified through regular calibration checks against certified standards, with all results documented in detailed logs that include measurement data, standards used, and pass/fail status.
You'll need to maintain strict calibration schedules for each piece of equipment, ensuring timely recalibration based on manufacturer specifications and usage patterns.
Store all calibration records, including certificates, adjustment data, and maintenance logs, in a centralized system that's easily accessible for audits and compliance verification.
Test Equipment Accuracy Checks
Regular calibration of ESD test equipment stands as a vital cornerstone of any antistatic facility's maintenance program. You'll need to guarantee your equipment meets precise specifications, typically within ± 5% for full-scale accuracy on devices like electrostatic fieldmeters.
Your calibration process should align with industry standards such as NIST Certified Calibration Services and follow international guidelines including BS EN 1149-1 and BS EN 1149-2.
For effective accuracy checks, you should maintain extensive records that detail:
- Calibration dates and procedures for each piece of equipment, including electrostatic fieldmeters, resistivity meters, and constant monitors
- Specific adjustments made during calibration and any observed deviations from standard specifications
- Verification of compliance with industry standards like ESD S.20.20 and relevant certifications such as CE and ISO 17025
You'll want to perform these accuracy checks annually, guaranteeing each piece of equipment maintains its precision.
Don't forget to test your wrist strap/heel grounder testers and combo meters, as they're essential for maintaining workplace safety.
Your calibration records serve as vital documentation for audits and compliance reviews, so keep them detailed and easily accessible.
Calibration Schedules and Logs
Maintaining thorough calibration schedules and logs forms the foundation of effective ESD equipment management. You'll need to implement a robust system that tracks each instrument's identification details, including model numbers, manufacturers, and specific locations within your facility.
Set up calibration intervals that align with both manufacturer recommendations and regulatory requirements for your ESD equipment. Your calibration records should detail the procedures used, standards applied, and accuracy measurements before and after calibration.
Make sure you're documenting all calibration certificates and maintaining clear records of any adjustments or non-conformances discovered during the process. You'll want to implement an automated scheduling system that sends reminders for upcoming calibrations and clearly label all equipment with their next calibration dates.
When you encounter calibration anomalies, document them thoroughly and implement corrective actions immediately. Remove any equipment that falls outside acceptable tolerance ranges from service until it's properly calibrated.
Keep your records easily accessible through calibration management software, ensuring you can quickly retrieve historical data and demonstrate compliance during audits. Regular system maintenance and consistent data entry will help you maintain traceability and meet ISO 17025 requirements.
Documentation Storage Guidelines
Organized documentation storage lies at the heart of effective calibration record management. You'll need to maintain thorough records of your antistatic equipment calibrations, including test dates, technician information, and environmental conditions during testing.
Your storage system should incorporate both physical and digital solutions, with encrypted access controls to protect sensitive data.
To guarantee your documentation meets ISO standards and regulatory requirements, you'll want to:
- Store calibration records for a minimum of 4 years, maintaining standardized formats that include instrument identification, reference standards used, and complete audit trails.
- Implement an electronic management system that provides automated alerts for upcoming recalibrations and enables quick access to historical data.
- Use digital solutions like Skippet to customize your documentation processes and automatically trigger corrective actions when discrepancies arise.
Your storage system should support easy retrieval while maintaining data integrity. Keep your records in a structured format that aligns with both ISO 17025:2017 and ISO 9001:2015 requirements.
Remember to include environmental conditions during calibration, as these factors can appreciably impact equipment performance and measurement accuracy.
ESD Protective Packaging
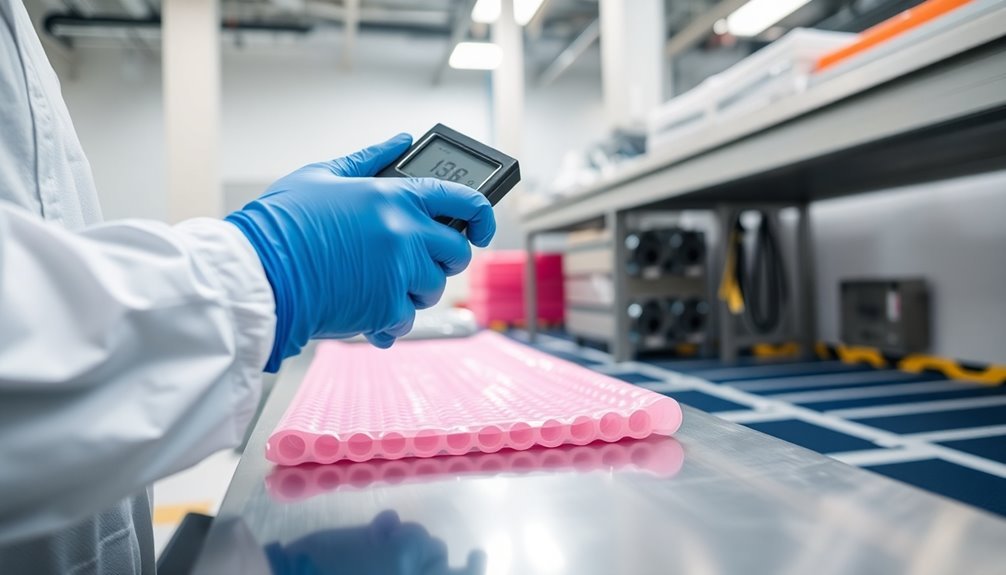
Proper ESD protective packaging serves as a critical defense against electrostatic discharge during storage, handling, and transportation of sensitive electronic components.
During your facility inspection, you'll need to verify that all packaging materials meet ANSI/ESD S20.20 standards and are appropriate for your specific device sensitivity levels.
Check that you're using the right combination of conductive, dissipative, and anti-static materials. Your packaging should include proper shielding materials, often metallized, to create an effective barrier against electrostatic discharge.
Don't forget to inspect moisture protection measures, such as barrier bags or desiccant inclusion, especially if your distribution environment experiences humidity fluctuations.
You'll want to verify that your packaging system incorporates multiple protective layers when necessary, including static-proof materials like carbon-loaded components.
Ascertain you're following the correct implementation guidelines for both EPA and non-EPA areas.
Your inspection should also cover the condition of packaging materials – look for wear, tears, or degradation that might compromise their protective properties.
Make sure your staff is properly trained in handling and using ESD protective packaging, and maintain records of regular effectiveness testing.
Ionization System Maintenance
When was the last time you tested your ionization system? Regular testing and maintenance are essential for maintaining peak performance of your ionizers.
You'll need to use a Charged Plate Monitor (CPM) or Periodic Verification System (PVS) to verify discharge time and offset voltage according to ANSI/ESD STM3.1 standards.
To establish an effective maintenance schedule, you'll want to:
- Test your ionizers monthly to determine proper maintenance intervals and establish baseline performance metrics.
- Clean emitter points whenever performance drops below factory requirements, and immediately retest to confirm restoration.
- Document all maintenance activities and test results to meet quality audit requirements.
Don't forget that factors like compressed air pressure, air volume, and laminar flow conditions can affect your test results.
If you're looking to reduce maintenance time and costs, consider investing in ionizers with automatic emitter point cleaning features or auto-balancing closed-loop feedback technology. These features can greatly extend your maintenance intervals and help maintain consistent ion balance.
Remember to place your CPM at designated test locations, such as the center of the ionizing bar, to guarantee accurate and repeatable measurements.
Frequently Asked Questions
How Often Should Employees Undergo ESD Safety Training and Certification?
You'll need annual ESD safety training updates to maintain compliance with ANSI/ESD S20.20 and IEC 61340-5-1 standards. Your certification should be renewed yearly, with regular refresher sessions throughout the year for best practices.
What Emergency Procedures Should Be in Place for Esd-Related Incidents?
You'll need to implement immediate equipment shutdown protocols, isolate affected areas, guarantee proper grounding procedures, use ESD-safe tools for repairs, and maintain clear communication channels when responding to ESD-related emergencies.
Are Visitor Protocols Established for Entering Esd-Sensitive Manufacturing Areas?
Yes, you'll need strict visitor protocols including ESD awareness training, proper protective gear (smocks, wrist straps), testing verification, access control, and documentation requirements before allowing anyone to enter ESD-sensitive manufacturing areas.
How Do Seasonal Weather Changes Affect Antistatic Facility Requirements?
You'll need to adjust your facility's humidity controls as seasons change. During dry, cold weather, you must increase humidification, while in humid seasons, you'll monitor conditions to maintain ideal ESD protection levels.
What Insurance Considerations Are Specific to Esd-Protected Manufacturing Facilities?
You'll need specialized insurance coverage including ESD-specific property protection, equipment breakdown coverage, cyber liability, and product liability insurance. Don't forget business interruption coverage to protect against manufacturing downtime from ESD incidents.
In Summary
You'll need to regularly check all aspects of your antistatic facility to maintain effective ESD protection. Make sure you're inspecting your flooring, workstation grounding, personnel testing equipment, and protective boundaries. Don't forget to review your documentation, handling procedures, and equipment calibration records. Keep tabs on your ESD packaging integrity and ionization systems. These routine checks help prevent costly static damage.
Leave a Reply