You'll find electrical discharge monitoring standards essential in cleanrooms because even minimal static charges of 30 volts can disrupt sensitive equipment and damage microelectronic components. Static electricity builds up easily in cleanroom environments due to low humidity levels and constant movement of personnel and materials. Your cleanroom's effectiveness depends on controlling these invisible threats, particularly in semiconductor and aerospace manufacturing. You'll need strict monitoring standards to prevent static discharge events that could compromise product quality and worker safety. Exploring proper monitoring protocols will help you maintain the pristine conditions your cleanroom demands.
Understanding ESD Risk Thresholds
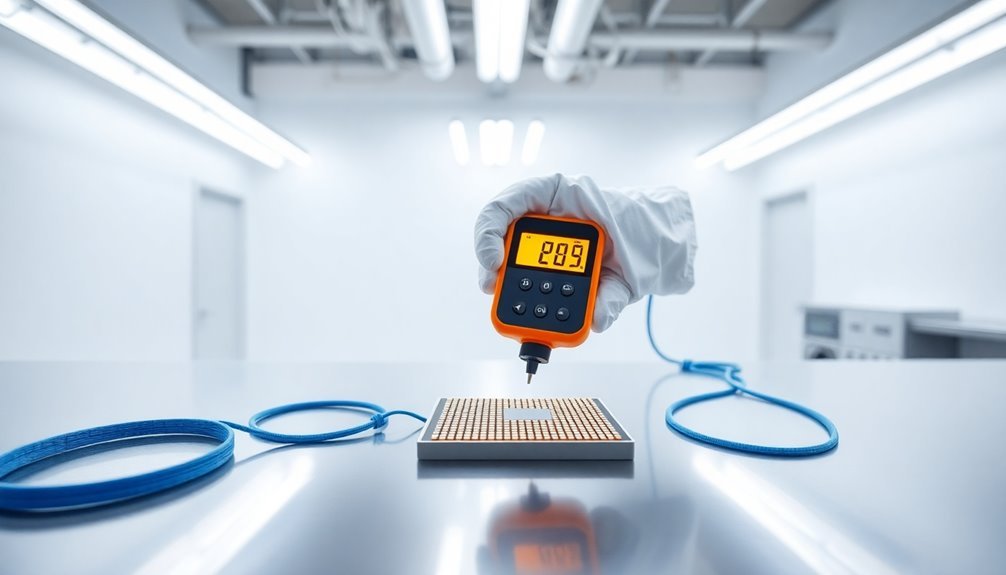
Over the past decade, electrical discharge sensitivity has become increasingly critical in cleanroom operations. You'll need to understand that even minimal static charges of just 30 volts can disrupt your cleanroom's balance and damage sensitive components during production.
As electronic components continue to shrink in size, they've become more vulnerable to ESD damage, requiring less energy to sustain significant harm. The most vulnerable industries include semiconductor fabrication and aerospace manufacturing.
You must pay particular attention to common insulating materials in your cleanroom, such as plate glass, Teflon, and various polymers, as they can become highly charged and pose substantial risks.
When your cleanroom's humidity drops below 40%, you'll notice that static electricity accumulates more readily, creating an environment where ESD events are more likely to occur.
What's particularly concerning is that ESD doesn't just cause immediate damage – it can create latent issues that worsen over time with normal use.
You'll need to monitor these risks carefully, especially when working with semiconductors, electrical circuits, and medical devices.
This sensitivity to ESD has made it essential for you to maintain strict monitoring standards, particularly as manufacturing processes become more sophisticated and components become increasingly delicate.
Static Generation in Cleanrooms
A cleanroom's unique environment creates the perfect storm for static electricity generation. The controlled environment's low humidity levels, combined with extensive use of insulating materials and constant air filtration through HEPA systems, greatly amplifies static charge buildup. You'll find that even routine activities like walking or handling materials can generate substantial static charges. This is particularly problematic in plastics processing operations, where static control has become increasingly critical.
Source | Generation Mechanism | Impact |
---|---|---|
Human Activity | Friction between clothes and body movement | Personnel discomfort, risk of shock |
Air Systems | HEPA filtration and air movement | Particle attraction, contamination |
Materials | Insulating surfaces like plastic and glass | Charge retention, equipment damage |
Processes | Spraying, washing, and peeling operations | Product damage, yield reduction |
Understanding these generation mechanisms is essential because they're intensified in cleanroom environments. Your standard static control methods that work in regular environments often prove insufficient here. The combination of low relative humidity, filtered air that removes natural ions, and the prevalence of insulating materials means you're dealing with persistent static challenges. This is why you need specialized monitoring and control strategies specifically designed for cleanroom environments.
Critical Humidity Control Measures
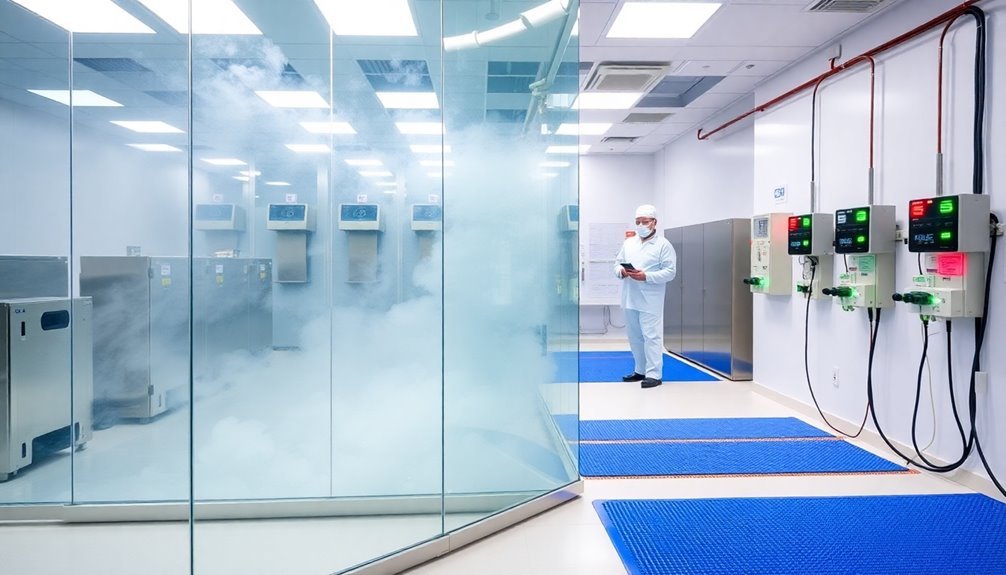
Maintaining precise humidity control stands out as one of the most critical factors in cleanroom operations. You'll need to keep humidity levels between 40-60% to minimize static electricity buildup, which can damage sensitive equipment and compromise product quality.
This control isn't just about comfort – it's essential for FDA compliance and maintaining CGMP manufacturing standards. Modern dedicated AC units are crucial for preconditioning outside air before it enters the cleanroom environment.
You can implement several effective methods to control humidity in your cleanroom. Industrial dehumidifiers using desiccants work well for moisture removal, while resistive steam humidifiers offer precise control when you need to add moisture.
Double airlocks help you prevent unwanted humidity changes from personnel movement. For accurate monitoring, you'll need to install hygrometers and implement continuous monitoring systems that can make real-time adjustments.
Your specific industry requirements will determine the exact humidity levels you'll need to maintain. You'll want to integrate advanced HVAC systems with high-precision sensors and intelligent control algorithms to achieve these targets.
Regular testing and verification guarantee you're meeting your cleanroom's specific humidity requirements while preventing contamination from bacteria and mold growth.
Essential Material Control Standards
Effective material control standards form the foundation of cleanroom operations, requiring careful attention to both design elements and ongoing maintenance procedures.
You'll need to focus on selecting non-particulate materials like stainless steel and coated aluminum that don't release contaminants into your cleanroom environment.
Your facility's design must incorporate specialized flooring and modular elements that allow for future expansion while maintaining contamination control.
Static discharge concerns require implementing electrical grounding systems throughout the cleanroom to protect sensitive equipment.
HEPA or ULPA filters are vital for your air filtration system, working alongside proper material selection to maintain cleanliness standards.
You'll want to guarantee all surfaces are easily cleanable and resistant to the disinfectants you'll use regularly.
To maintain these standards, you must implement strict cleaning protocols using approved agents that don't leave residues.
Your environmental monitoring program should include regular particulate counts and microbial testing to verify compliance with ISO 14644-1 and other relevant standards.
Don't forget to maintain extensive records of all cleaning activities and monitoring results – they're essential for identifying trends and demonstrating regulatory compliance.
Regular data analysis will help you spot potential contamination sources before they become significant issues.
ESD Protection System Components
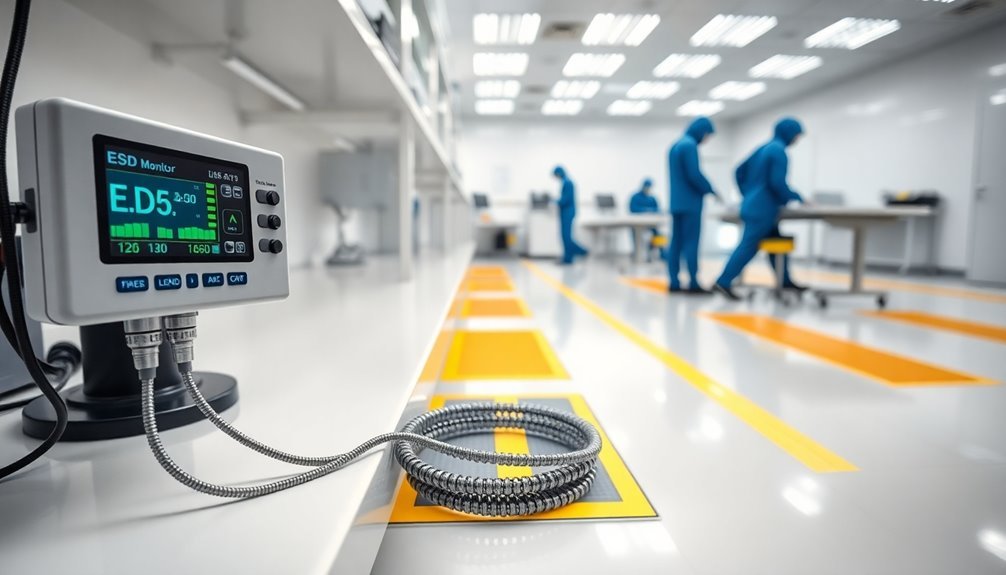
Selecting the right ESD protection components is vital for your cleanroom's electrical discharge control system. You'll need to carefully choose from various components like transient voltage suppressors (TVS), multi-layer varistors (MLVs), and zener diodes to guarantee proper protection of your sensitive electronic equipment.
These components work by bypassing high voltage currents and absorbing ESD energy to prevent damage to your circuits. Since static voltages generated from walking can reach up to 35,000 volts, proper component selection is crucial.
When you're setting up your cleanroom's ESD protection system, consider these important components:
- TVS diodes that actively limit voltage spikes and provide rapid response to electrical surges
- MLVs that offer both surge protection and capacitance benefits, particularly useful in high-speed applications where insertion capacitance isn't a concern
- Chip varistors that maintain high resistance at low voltages but switch to low resistance during surges
- Multi-layer ceramic capacitors (MLCCs) that can serve as ESD protection when capacitance limitations aren't an issue
You'll need to test and validate your chosen components to confirm they meet required standards.
Remember that your selection should be based on specific surge types and whether you're protecting signal lines or power circuits.
Cleanroom Classification Requirements
You'll need to understand ISO standards 14644-1 for cleanroom classifications, which range from ISO 1 (cleanest) to ISO 9 (least clean) and directly impact your ESD monitoring requirements.
Your cleanroom's particle count requirements will determine the frequency and stringency of ESD monitoring, with stricter ISO classes demanding more frequent testing and tighter controls.
When it comes to air quality testing methods, you must regularly verify both particle concentrations and ESD-related parameters to maintain your cleanroom's designated ISO classification and protect sensitive electronics.
Professional consultation and monitoring should be conducted for each transition between cleanroom classes, as skipping class levels during movement between zones can compromise cleanliness standards.
ISO Standards Overview
One of the most essential aspects of cleanroom management is understanding ISO 14644-1, the primary standard that governs cleanroom classifications worldwide. This standard establishes nine distinct classes, ranging from ISO 1 (the cleanest) to ISO 9 (least clean), based on the quantity and size of particles per cubic meter of air.
You'll need to understand these critical factors that affect your cleanroom's ISO classification:
- Environmental controls including temperature, humidity, airflow, and pressure must be precisely maintained.
- Performance requirements must be tested in three conditions: as-built, at rest, and operational.
- Different industries require specific ISO classes – from ISO 1-2 for semiconductor manufacturing to higher classes for food production.
- Filtration systems must meet strict specifications to maintain particle count requirements.
Your cleanroom's classification directly impacts your product quality and regulatory compliance. HEPA filtered air must be continuously supplied to maintain the required cleanliness levels within the controlled environment.
Whether you're in pharmaceuticals, electronics, or biotechnology, you must adhere to specific cleanliness standards.
The ISO 14644 standard provides extensive guidelines for design, operation, and monitoring, ensuring your cleanroom maintains the required environmental conditions for your specific industry needs.
Particle Count Requirements
The effective monitoring of particle counts forms the cornerstone of cleanroom classification systems. When you're evaluating your cleanroom's particle count requirements, you'll need to take into account both the ISO and FS209E standards, though ISO 14644-1 has become the predominant global standard.
You'll find that ISO classifications range from ISO 1 (cleanest) to ISO 9 (least clean), with pharmaceutical facilities typically operating in ISO 5, 7, and ISO 8 ranges. Non-unidirectional airflow is sufficient for achieving and maintaining cleanliness in ISO 7 and 8 environments.
To properly classify your cleanroom, you'll need a particle counter capable of detecting particles as small as 0.5 microns. Your measurements must be taken at specified grid locations throughout the space, and you'll need to achieve a 95% confidence level in your data.
The classification process requires testing in three distinct phases: As-Built, At-Rest, and Operational conditions. Each phase provides essential data about your cleanroom's performance.
Remember that different applications demand different cleanliness levels. If you're working in pharmaceutical manufacturing, you'll need to comply with both ISO 14644-1 and EU GMP Annex 1 standards, which specify strict particle count limits for various manufacturing processes.
Air Quality Testing Methods
Beyond particle counting, thorough air quality testing forms a complete picture of cleanroom performance.
You'll need to conduct multiple tests to guarantee your cleanroom maintains its required classification and meets operational standards. These tests work together to verify that your HVAC systems, filtration, and room construction are functioning as designed.
To maintain cleanroom integrity, you must regularly perform these essential air quality tests:
- Filter integrity testing of HEPA/ULPA systems to detect leaks and verify filtration efficiency – this prevents unfiltered air from compromising your controlled environment.
- Airflow visualization studies using fog to confirm proper air movement patterns and identify potential dead zones or turbulent areas.
- Room pressure differential measurements to guarantee your cleanroom maintains positive pressure against surrounding spaces, preventing contamination ingress.
- Temperature and humidity monitoring to verify environmental controls are maintaining consistent conditions throughout the space.
Regular testing helps you identify potential issues before they affect product quality.
You'll also need to document all test results for compliance purposes and establish baseline performance metrics for your facility's ongoing maintenance program.
Real-Time Monitoring Systems
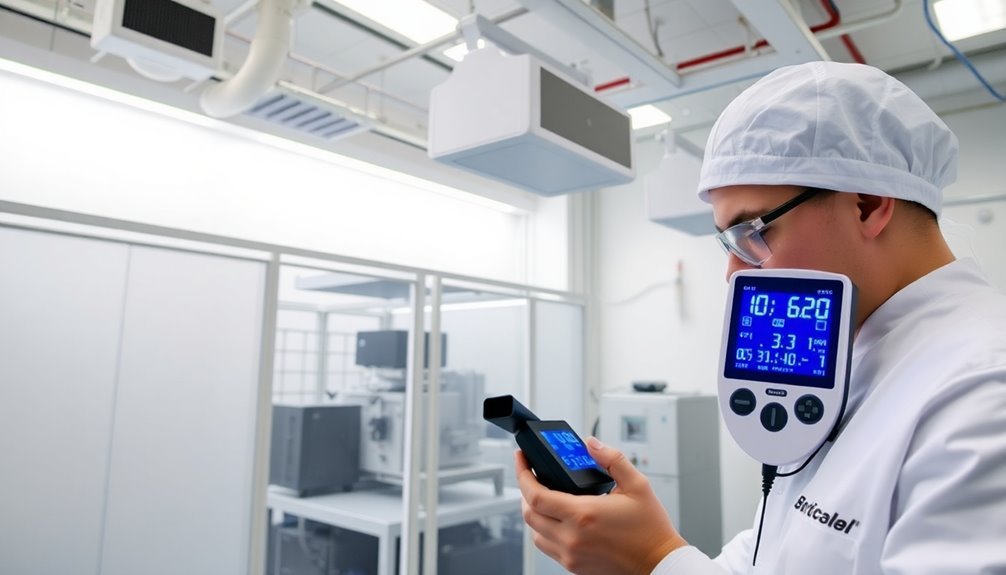
Modern real-time monitoring systems represent a considerable advancement in cleanroom management, combining sophisticated sensors with integrated software to provide immediate insights into environmental conditions.
You'll find these systems continuously tracking multiple parameters, including particle counts, temperature, humidity, and differential pressure, ensuring your cleanroom maintains ideal conditions.
The benefits of implementing real-time monitoring are substantial. You're able to receive immediate alerts when parameters deviate from acceptable ranges, allowing for quick responses to potential contamination events.
This proactive approach greatly reduces downtime and waste while ensuring compliance with FDA and USP standards through automated reporting.
You can easily integrate these systems with your existing Building Management Systems (BMS), and monitor conditions remotely through web interfaces or dedicated apps.
The setup process involves strategic risk assessment to determine ideal sensor placement, and you'll work with technicians following GAMP V model guidelines for implementation.
What's particularly convenient is that these systems are scalable – you can start with a few sensors and expand as needed.
They're designed to meet worldwide regulatory requirements, including FDA 21 CFR part 11 and GMP standards, keeping your facility audit-ready at all times.
Personnel Safety Protocol Standards
Implementing extensive personnel safety protocols stands as a cornerstone of effective cleanroom management, particularly regarding electrical discharge control.
You'll need to guarantee your staff consistently wears ESD-safe clothing made with conductive threads, which effectively prevents static buildup while maintaining cleanroom standards. Your facility's humidity control must stay between 40-60% to minimize static charge accumulation and protect both personnel and sensitive equipment.
To maintain proper ESD safety standards, you must follow these critical protocols:
- Require all personnel to use appropriate grounding equipment, including wrist straps and booties with grounding tabs before entering sensitive areas.
- Enforce strict gowning procedures using static-dissipative materials that incorporate conductive fibers.
- Conduct regular audits of your ESD prevention measures, including testing ground connections and verifying proper use of safety equipment.
- Maintain detailed cleaning protocols that address both contamination control and static prevention.
Your maintenance team should regularly verify the effectiveness of these measures through systematic testing and monitoring.
Remember that proper ESD control isn't just about protecting equipment – it's essential for maintaining a safe working environment for your personnel while guaranteeing product quality.
Equipment Calibration Best Practices
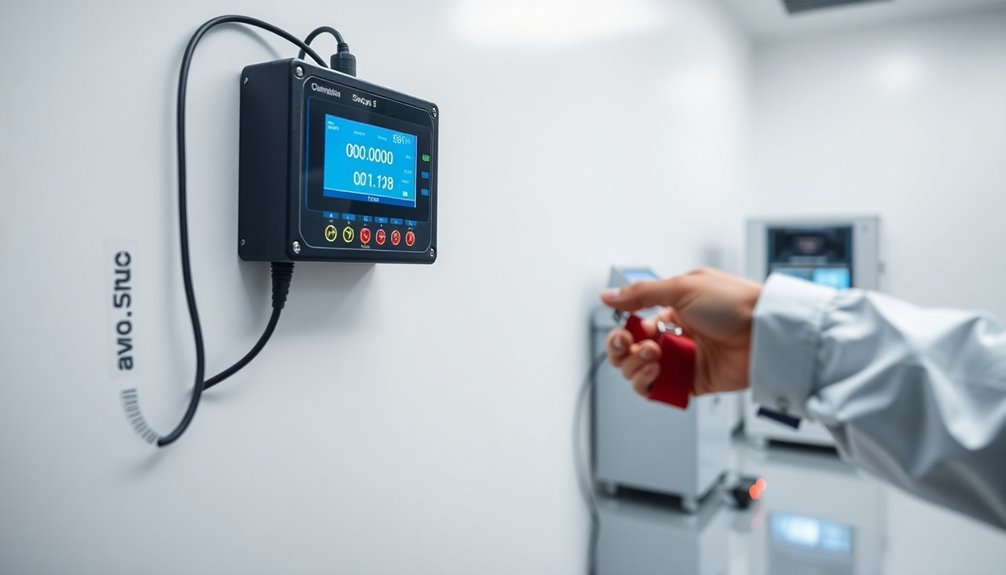
You'll need to establish regular calibration check schedules for all electrical discharge monitoring equipment to maintain accuracy and compliance with cleanroom standards.
Your documentation must include detailed records of testing protocols, calibration dates, results, and any corrective actions taken when deviations occur.
Testing protocols should align with manufacturer specifications and industry standards while incorporating routine verification of sensor accuracy, system response times, and alarm thresholds.
Regular Calibration Check Schedules
Effective calibration check schedules form the backbone of cleanroom electrical discharge monitoring systems.
You'll need to establish proper intervals based on manufacturer recommendations, historical data, and environmental conditions. Your calibration program should account for both the frequency and type of equipment use while maintaining alignment with industry standards.
To guarantee your calibration schedule remains effective, you'll want to implement these essential practices:
- Track all calibration intervals in a computerized database, making sure they're outlined in your standard operating procedures and readily accessible to relevant personnel.
- Adjust intervals based on continuous trending analysis of calibration data, but remember to get QA approval before making any changes.
- Schedule regular comparisons with reference standards, using either primary standards or approved in-house alternatives when primary standards aren't practical.
- Maintain detailed records of all adjustments and verification testing to support your calibration program.
Your proactive maintenance approach should include certified professionals performing complex calibrations while following cleanroom protocols.
Don't forget to factor in environmental conditions and usage patterns when determining check frequencies, as these variables can considerably impact your equipment's calibration stability.
Documentation and Testing Protocols
Documentation and testing protocols serve as the cornerstone of reliable equipment calibration practices in cleanroom environments.
You'll need to maintain thorough records that include calibration data, maintenance activities, and testing results to meet regulatory requirements and guarantee continuous improvement in your cleanroom operations.
When implementing your testing protocols, you must verify equipment performance against design specifications under various operational conditions.
You'll want to include failure response assessments in your validation procedures to assure equipment operates within predetermined limits. Your documentation should capture all these test results systematically and accurately.
Your record-keeping system should be organized and easily accessible, with clear procedures for storing and retrieving calibration and maintenance data.
You'll need to retain these records for the duration specified by regulatory guidelines, which helps demonstrate compliance during audits.
Make sure you're documenting every calibration check, maintenance activity, and performance test thoroughly.
Static Discharge Prevention Methods
Controlling static discharge in cleanrooms requires a detailed approach that combines specialized materials, design elements, and operational practices.
You'll need to implement multiple layers of protection to effectively manage electrostatic discharge (ESD) and maintain the integrity of your cleanroom operations.
The foundation of static control starts with your cleanroom's infrastructure. You'll want to install anti-static flooring and wall panels that can effectively ground charges, while maintaining proper humidity levels between 40-60%.
Your HEPA filtration system should work in tandem with ionization equipment to neutralize airborne static charges.
To guarantee an all-encompassing static discharge prevention, you'll need to follow these essential steps:
- Outfit your staff with ESD-safe clothing, including static-dissipative garments, wrist guards, and appropriate footwear.
- Install and maintain de-ionization systems throughout critical areas.
- Implement proper grounding techniques for all equipment and work surfaces.
- Monitor humidity levels consistently and adjust your environmental controls accordingly.
Don't forget to adhere to ANSI/ESD S20.20 and IEC 61340 standards when developing your static control protocols.
Your air shower systems should include ionization features to enhance both cleaning efficiency and static control during entry and exit procedures.
Compliance Documentation Requirements
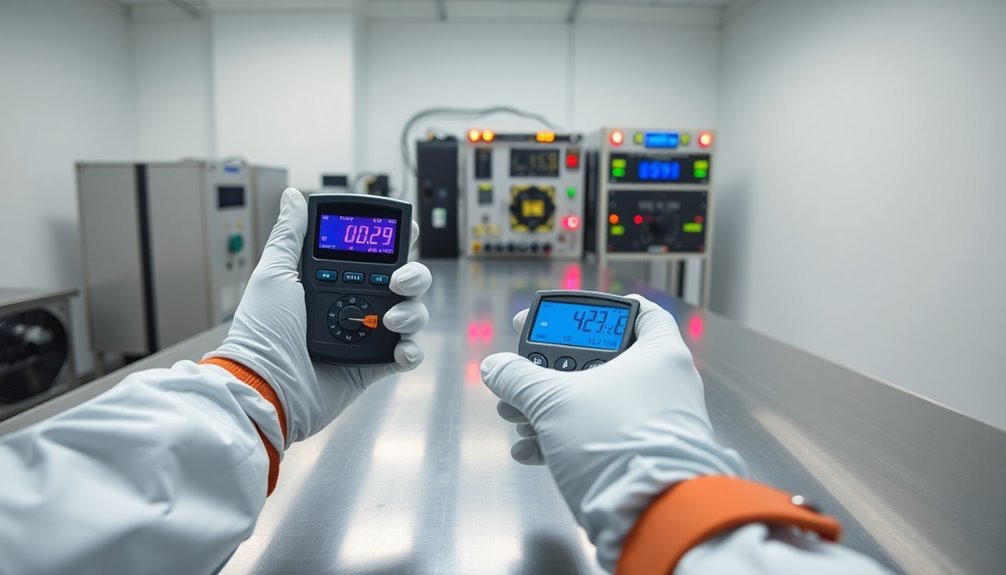
Three critical components form the backbone of cleanroom compliance documentation: detailed activity logs, standardized reporting formats, and secure data management systems.
You'll need to maintain thorough records of all monitoring and maintenance activities to demonstrate your adherence to cleanroom standards, particularly ISO 14644-1 and ANSI/ESD S20.20.
Your documentation system must include robust security measures to protect sensitive data. You'll want to implement encryption, access controls, and reliable backup systems to prevent data loss and unauthorized access.
Regular trend analysis of your records will help you identify potential issues before they escalate into major problems.
To guarantee compliance, you'll need to conduct regular audits and engage third-party verifiers to assess your documentation practices.
These audits will verify that you're meeting both industry-specific regulations and general cleanroom standards. You must also maintain clear audit trails for regulatory inspections.
When auditors identify areas for improvement, you'll need to implement corrective actions promptly.
Remember to train your personnel on proper documentation procedures to maintain consistency and accuracy in your record-keeping system.
Environmental Control Verification Systems
Reliability in environmental control systems forms the foundation of effective cleanroom operations.
You'll need thorough verification systems to monitor and maintain critical parameters that guarantee your cleanroom's integrity. These systems integrate various monitoring devices and technologies to track temperature, humidity, differential pressure, and particle counts in real-time.
To maintain compliance with ISO 14644-1 and other regulatory standards, you'll want to implement these essential verification components:
- Particle counters that measure both 0.5µm and 5µm particles, giving you precise data on air cleanliness levels
- Digital probes for temperature and humidity monitoring, assuring ideal conditions for your processes
- Differential pressure sensors that verify proper airflow patterns and prevent cross-contamination
- Automated alarm systems that instantly alert you when parameters deviate from acceptable ranges
Your environmental monitoring system must comply with FDA 21 CFR Part 11 for electronic records, while following GMP and GLP guidelines.
Remember that continuous monitoring isn't optional – it's a regulatory requirement under ISO 14664-2.
You'll need to regularly analyze the collected data and maintain detailed reports for compliance documentation and system enhancement.
Frequently Asked Questions
How Often Should Cleanroom Staff Undergo Refresher Training for ESD Protocols?
You'll need to complete ESD protocol refresher training on a quarterly or bi-annual basis to maintain proper safety standards. Your training must cover tools, application techniques, grounding methods, and inspection routines.
What Are the Cost Implications of Upgrading From ISO Class 1000 to 100?
You'll face significant costs when upgrading from ISO Class 1000 to 100, including major HVAC modifications ($200K-500K), new filtration systems ($50K-100K), and increased operational expenses for maintenance and monitoring ($75K-150K annually).
Can Mobile Phones Be Modified for Safe Use Within Cleanroom Environments?
You can't safely modify standard mobile phones for cleanroom use. Instead, you'll need to purchase specialized cleanroom-certified phones that meet ESD standards and feature particulate-free surfaces with proper grounding mechanisms.
How Do Seasonal Changes Affect Cleanroom ESD Monitoring System Maintenance Requirements?
You'll need to maintain consistent ESD monitoring year-round, as HVAC systems typically control seasonal variations. However, you should increase system checks during extreme weather changes to guarantee continued effectiveness and proper calibration.
What Insurance Considerations Are Specific to Cleanrooms With ESD Monitoring Systems?
You'll need insurance coverage for ESD equipment damage, system failures, employee training, business interruption, and compliance requirements. Don't forget to maintain documentation of regular maintenance to support potential claims and certification needs.
In Summary
You'll need robust electrical discharge monitoring standards in your cleanroom to protect sensitive components and maintain product quality. Without proper ESD controls, you're risking equipment damage, product failures, and costly production delays. By implementing thorough monitoring systems, controlling humidity levels, and following strict material handling protocols, you're safeguarding your operations and ensuring regulatory compliance in your controlled environment.
Leave a Reply