When choosing between reusable and disposable anti-static protection, you'll need to weigh several key factors. Reusable options offer significant long-term cost savings with up to 85% waste reduction and superior durability, featuring thicker materials for better hazard resistance. While disposables may seem cheaper initially, they increase waste management costs and environmental impact. Consider your facility's specific needs, contamination levels, and budget constraints. Proper maintenance of reusable gear, including regular testing and cleaning, guarantees consistent performance. The right choice depends on your unique requirements, and understanding the complete picture will help you make an informed decision.
Understanding Anti-Static Protection Basics
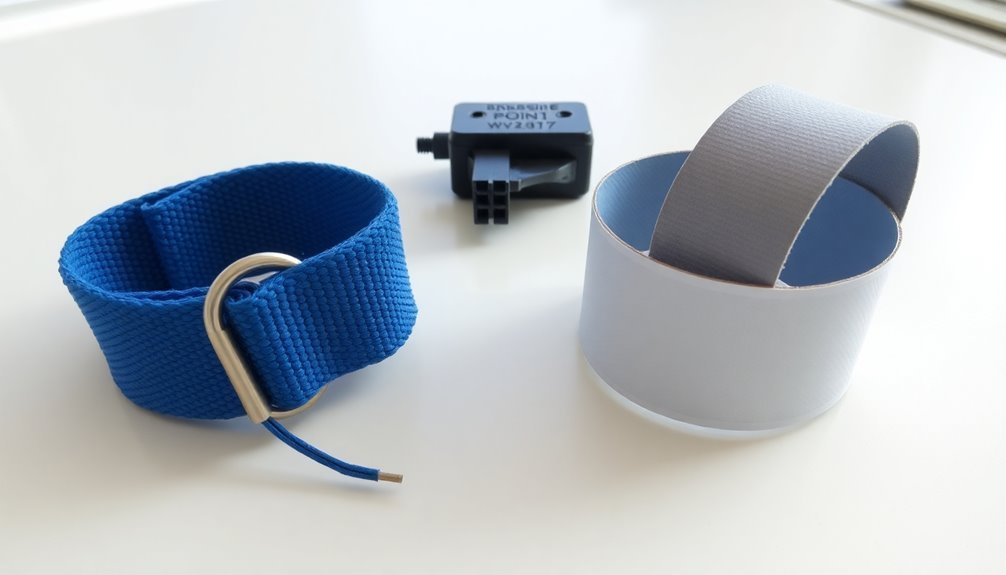
Anyone working with electronic components needs to understand anti-static protection basics. When you handle electronics, you're dealing with components that can be severely damaged by electrostatic discharge (ESD). This invisible threat occurs when static electricity builds up and suddenly discharges, potentially destroying sensitive electronic parts. Up to 33% of production losses in electronics manufacturing can be attributed to static-related failures.
Ionizer deployment can neutralize static on materials that cannot be removed from your workspace. You'll need to focus on three key areas: materials, grounding, and environment control. Dissipative materials allow static charges to flow safely to ground, while conductive materials help manage electrical potentials. You'll want to use proper grounding equipment, including wrist straps and anti-static mats, to guarantee you're not carrying harmful charges.
Creating a controlled environment is vital for your work. You'll need to eliminate static sources like carpets and plastic materials, while implementing proper storage solutions using ESD-safe containers.
Regular testing of your anti-static equipment isn't optional – it's essential for maintaining effective protection. Remember to follow ESD standards like ANSI/ESD S8.1 and establish a common point ground in your workspace.
Using these protective measures consistently will help prevent costly damage to electronic components and guarantee your safety.
Cost Analysis Over Time
After establishing proper anti-static protection measures, you'll want to evaluate the long-term costs of your ESD prevention strategy.
When comparing reusable and disposable anti-static garments, you'll need to take into account the total cost of ownership rather than just the initial purchase price.
For reusable garments, factor in the procurement cost, washing, drying, and potential repairs over their lifespan. While the upfront investment is higher, you'll typically see notable cost savings over time, especially in manufacturing settings where garments aren't frequently contaminated. Proper use of reusable garments can achieve a carbon footprint reduction of up to 27%. Similar to medical gowns, industrial laundering effectively maintains the protective properties of reusable anti-static garments.
Studies show reusable options can reduce usage ratios by 20:1000 compared to disposables.
However, your specific application will determine the most cost-effective choice. If you're working in environments with high contamination risks or frequent exposure to hazardous materials, disposable garments might prove more economical despite their higher per-unit cost.
You'll need to include waste disposal costs in your calculations for disposables, as these can greatly impact your total expenses.
Take into account the garment's lifecycle, durability requirements, and your facility's specific needs when making your decision.
Environmental Impact Assessment
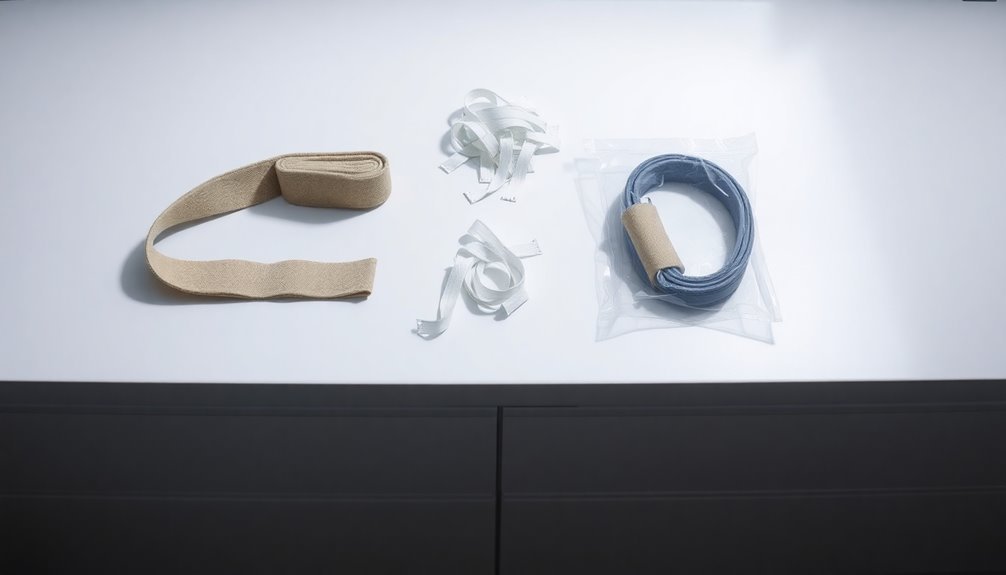
When you're comparing anti-static protection options, you'll find that reusable garments can reduce waste by up to 85% compared to disposable alternatives that contribute to landfill accumulation.
Your choice between traditional polyester-based materials and newer eco-friendly fabrics made from recycled or biodegradable components will greatly impact your environmental footprint. Some manufacturers like Mechanix Wear are leading the way with eco-friendly nitrile options that incorporate sustainable technologies.
While disposables offer advantages in infection control, reusable options remain a viable choice for facilities prioritizing sustainability.
Waste Reduction Statistics
Environmental impact assessments reveal significant waste reduction potential through anti-static PPE choices.
When you switch to reusable PPE, you'll reduce your disposal rates by eliminating single-use items that typically end up in landfills. Reusable options require more upfront cost but deliver long-term environmental benefits. Life cycle assessments consistently show that reusable options create less environmental impact over time, despite requiring more resources during initial manufacturing.
You'll see measurable waste reduction through extended product life spans. While disposable PPE requires constant replacement and generates continuous waste, reusable equipment can last through multiple uses with proper maintenance. Choosing reusable protection delivers cost savings over time through eliminating constant purchases of new products.
Statistics show that reusable PPE programs can decrease your overall material consumption by up to 95% compared to disposable alternatives.
The numbers become even more compelling when you consider supply chain efficiency. By reducing frequent orders and shipping requirements, you'll cut down on packaging waste and transportation-related emissions.
Additionally, many reusable PPE materials are recyclable at the end of their service life, unlike disposable options that often contain non-biodegradable materials like nitrile and latex.
These factors combine to create significant waste reduction potential, supporting both environmental conservation efforts and your bottom line through reduced waste management costs.
Eco-Friendly Material Analysis
Modern manufacturers have stepped up their game with eco-friendly ESD materials that pack a double punch: protecting sensitive electronics while safeguarding the environment.
You'll find innovative options like Eco-Corr Film ESD and EcoSonic ESD Paper, which incorporate sustainable materials such as soybean oil and natural starches while maintaining robust static protection.
When you're analyzing these eco-friendly alternatives, you'll notice significant environmental benefits. For instance, recyclable materials like Wellplast ESD Protect can reduce your waste management costs, while Corstat packaging eliminates heavy metals and halogens from your supply chain.
You're looking at up to 75% energy savings when recycling corrugated cardboard compared to traditional materials.
You can choose from various sustainable solutions that match your specific needs. Whether it's biodegradable ESD bags with clear recycling symbols or compostable films for electronics packaging, you'll find options that align with environmental regulations.
By selecting these materials, you're not just cutting costs – you're also building a positive corporate image and extending your material lifecycle through recyclability and compostability.
These choices help you meet growing sustainability standards while maintaining essential static protection.
Material Quality Comparison
Through careful analysis of material compositions, reusable safety gloves demonstrate superior durability and protection compared to their disposable counterparts.
You'll find that reusable gloves, with their thickness ranging from 11 to 33 mil, offer considerably more robust protection than disposable options, which typically measure around 4 mil. The enhanced thickness directly contributes to their superior chemical resistance and longevity.
When you're evaluating material quality, you'll notice that reusable gloves made from neoprene, nitrile, or latex provide exceptional resistance against various chemicals.
While disposable gloves excel in tasks requiring fine dexterity due to their thinness, they can't match the protective qualities of reusable options during prolonged exposure to hazardous substances.
You'll need to take into account that disposable gloves, despite their convenience, often compromise on material strength to maintain flexibility.
The material composition of reusable gloves also supports their sustainability advantages.
You can wash and reuse them multiple times while maintaining their protective properties, provided they remain undamaged.
This durability not only guarantees consistent protection but also contributes to their superior cost-effectiveness over time compared to disposable alternatives.
Durability Testing Results
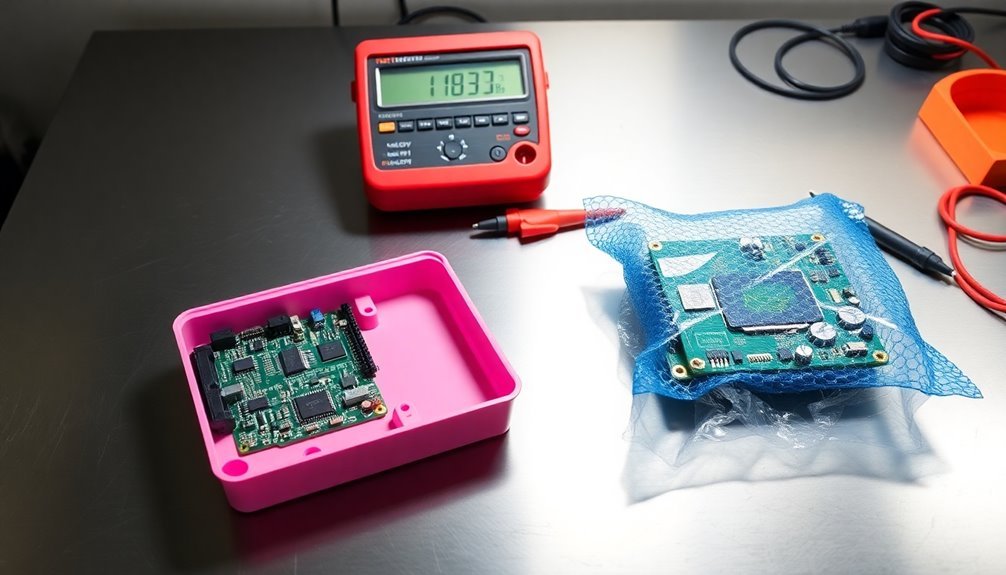
Standardized durability testing reveals crucial differences between disposable and reusable PPE performance.
While nonwoven fabric-based disposable protection offers less structural strength than woven alternatives, it can still provide excellent barrier protection and breathability. You'll find that high-quality disposable garments feature reinforced seams and heavier materials to enhance their protective capabilities.
When you're examining reusable PPE, you'll notice noticeably thicker materials, particularly in gloves that blend nitrile with PVC. These materials can withstand extreme temperatures and handle hazards like impacts, cuts, and harsh chemicals more effectively than their disposable counterparts.
You'll also find protective design elements such as anti-impact padding and puncture-proof palms in reusable options.
Before making your selection, you'll need to reflect on your specific application requirements. While disposable PPE excels in scenarios involving biological agents and certain chemicals, reusable options might be more suitable for long-term wear across multiple shifts.
Remember that any PPE, whether disposable or reusable, must undergo application-specific testing and proper risk analysis to guarantee it meets your anti-static protection needs.
Don't reuse any PPE that shows signs of contamination or damage.
Workplace Safety Standards
The extensive workplace safety standards for anti-static protection require strict adherence to key regulations like ANSI/ESD S20.20 and ASTM D257. When you're selecting reusable anti-static protection, you'll need to verify your equipment meets all industry-specific standards for electrical component handling to prevent shock and static electricity risks.
You'll find that proper maintenance plays a vital role in maintaining safety compliance. It's important to inspect your anti-static protection before and after each use, clean it with mild detergent when necessary, and store it in cool, dry areas away from direct sunlight.
If you notice any damage, you must repair or replace the equipment immediately to maintain protective performance.
Your choice of reusable anti-static protection not only guarantees workplace safety but also offers environmental and financial benefits. While you'll make a higher initial investment, you'll see significant long-term savings through reduced replacement needs and disposal costs.
Additionally, you're contributing to environmental sustainability by minimizing waste, reducing resource consumption, and decreasing landfill impact. Remember to factor in maintenance and replacement costs when calculating your total cost of ownership.
Performance in Different Industries
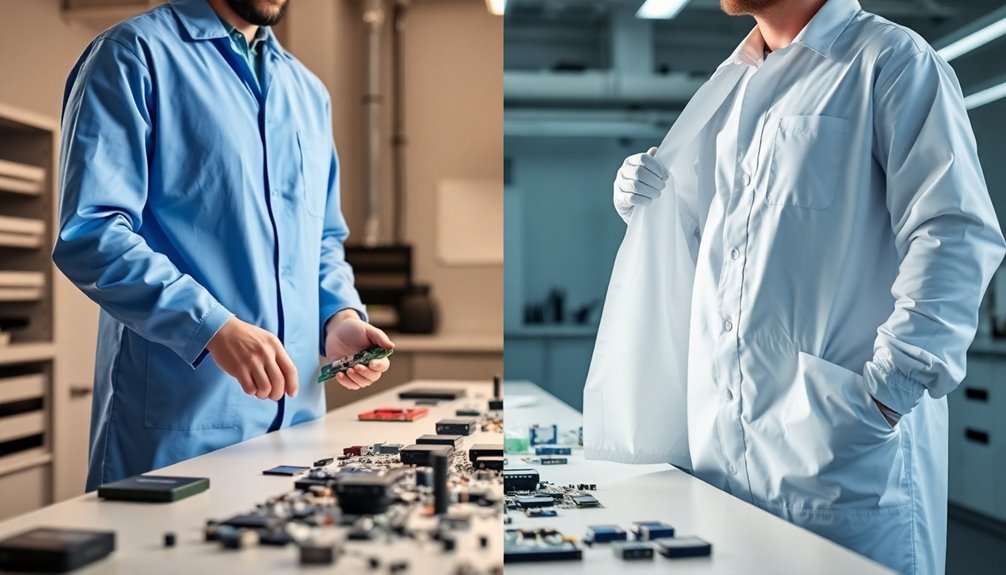
When you're assembling electronic components, you'll need anti-static PPE that meets strict dissipative requirements to protect sensitive circuits from electrostatic discharge.
In chemical manufacturing, your anti-static protection must balance conductivity with chemical resistance to prevent both static buildup and chemical exposure risks.
Your choice between reusable and disposable anti-static gear will depend on your specific application, with electronics typically favoring reusable options for consistent performance and chemical processing often requiring disposable protection for contamination control.
Electronics Assembly Best Practices
Manufacturing electronic assemblies across different industries demands rigorous attention to best practices that can make or break product quality. To guarantee successful assembly, you'll need to implement thorough planning and standardization from the earliest design stages.
Start by arranging your components logically, grouping related parts together while maintaining adequate spacing to prevent overcrowding. You'll want to follow your PCB manufacturer's Design for Manufacturability guidelines closely and perform early DFM checks to catch potential issues before they become costly problems.
During production, you must maintain strict quality control measures. Screen your SMT solder paste carefully, conduct X-ray inspections after reflow soldering, and utilize both automated and manual inspection methods to verify assembly quality.
You'll benefit from establishing clear communication channels with your manufacturers and maintaining detailed documentation throughout the process.
To optimize your assembly process, implement modular design principles and stick to standardized, Commercial Off-the-Shelf (COTS) parts whenever possible. This approach will simplify your supply chain, reduce inventory complexities, and minimize assembly errors.
Remember to reflect on ergonomic factors in your design to guarantee efficient assembly and maintenance procedures.
Chemical Manufacturing Applications
Selecting appropriate chemical protection garments requires careful evaluation of your specific industry applications and risk factors. In chemical manufacturing, you'll need to take into account both the physical properties of your protective gear and the specific chemicals you're handling to guarantee adequate protection.
When working with highly toxic chemicals, you'll want to prioritize garments with proven barrier protection and welded seams. If you're handling multiple chemicals, reusable garments with strong chemical resistance might be your best choice, though you'll need to implement proper decontamination procedures. For less hazardous tasks, disposable options can provide adequate protection while offering cost benefits.
Reflect on the thickness and material configuration of your chosen garments, as these factors directly impact chemical permeation rates.
You'll also need to evaluate your facility's specific needs – if you're working in areas requiring frequent garment changes, disposable options might be more practical. However, if you're dealing with sustained exposure to harsh chemicals, investing in durable reusable garments could offer better long-term protection and value.
Remember to base your final selection on a thorough risk assessment of your specific manufacturing processes and chemical exposure levels.
Maintenance Requirements
Proper maintenance of anti-static protection equipment requires a systematic approach to guarantee consistent performance.
You'll need to establish regular cleaning schedules and use appropriate ESD-approved cleaning products to maintain the effectiveness of your anti-static equipment and surfaces.
For ESD floors, you must implement daily cleaning routines like sweeping or dry mopping, alongside weekly wet mopping and monthly deep cleaning sessions.
It's vital that you avoid using non-ESD chemicals or wax, as these can compromise the floor's protective properties.
You'll also need to conduct regular testing in both high and low traffic areas.
Your ESD worksurfaces demand daily visual checks of ground wire connections and periodic resistance measurements.
You should use continuous monitors to track wrist straps and ground connections in real-time.
For anti-static equipment like ionizing guns and blowers, you'll need to remove dirt regularly and verify their functionality.
Training your staff is essential – they must understand proper maintenance procedures and best practices.
You'll need to control foot traffic in protected areas and perform regular inspections to identify any damage or areas requiring additional attention.
Risk Management Strategies
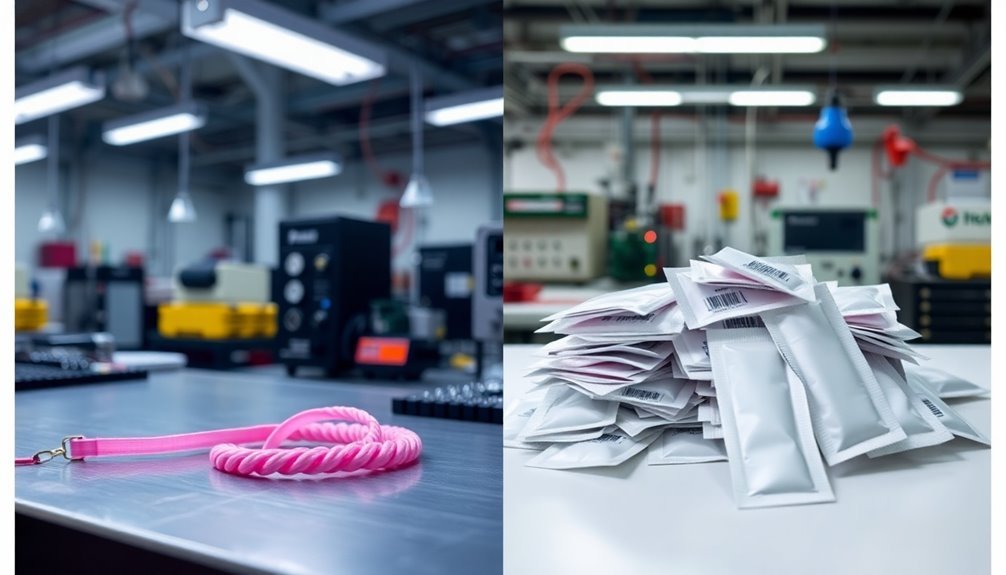
Effective risk management for anti-static protection begins with a thorough assessment of your facility's ESD vulnerabilities.
You'll need to conduct regular audits to identify high-risk areas, especially where sensitive electronic components are handled. Evaluate your work environment and determine the ESD sensitivity of components to establish appropriate protection levels.
Once you've identified risks, implement targeted control measures. Install ESD-safe workbenches and grounding mats in your electrostatic protected areas (EPAs), and consider adding ionization systems to neutralize static charges.
You'll also need to select appropriate ESD-safe storage solutions and protective packaging based on your specific requirements.
Don't overlook the importance of training and compliance. Ascertain your staff understands proper ESD safety protocols by developing clear standard operating procedures.
Use monitoring tools to assess the effectiveness of your protection measures in real-time, and conduct periodic audits to maintain compliance.
Remember to stay flexible and adapt your strategies as needed – you'll want to incorporate feedback from audits and keep up with the latest developments in ESD protection technology to maintain an effective risk management program.
Proper Grounding Methods
You'll need to select the right ground wire connections to effectively dissipate static charges, with options including snap-on connectors, alligator clips, and banana plugs that connect to common ground points.
Static dissipative floor systems work together with ESD-protective footwear to create a reliable path to ground for personnel movement throughout protected areas.
When installing these systems, you must guarantee proper resistance measurements between 1.0 x 10^6 to 1.0 x 10^9 ohms to maintain effective static control while preventing electrical shock hazards.
Ground Wire Connection Types
Ground wire connections form the backbone of any reliable anti-static protection system, requiring specific materials and methods to safely dissipate static electricity.
You'll need to verify your grounding system uses conductive materials like copper or copper alloys, with special attention to maintaining resistance levels below 10 ohms for effective bonding.
When you're setting up your ground wire connections, you can choose from various materials including rubber, PVC, PU, or aluminum, which offer excellent resistance to environmental factors.
You'll want to connect your grounding wires to either the equipment grounding conductor or the green third wire electrical ground. For static control, a 1MΩ ± 20% safe grounding resistor is often your best choice.
In ESD-sensitive environments, you'll find that one ground connection per 1000 square feet is sufficient when using conductive flooring.
You can create effective connections using 24-inch flexible copper bridges between conductive adhesive and building steel.
Don't forget that all your electrical tools should have 3-prong grounded AC plugs.
For peak performance, you'll want to use grounding assemblies with clamps that can pierce through paint, ensuring proper metal-to-metal contact.
Static Dissipative Floor Systems
Installing static dissipative floor systems requires precise grounding methods to guarantee ideal ESD protection. You'll need to install one copper grounding strap for every 1,000 square feet of flooring, ensuring each room has at least one ground connection.
When working with exposed steel structures, affix the copper tape directly to bare metal surfaces.
To properly install the system, start by applying a primer coat to your floor. Then, lay down copper tape and extend it up the wall to connect with your chosen grounding point. You can secure the tape using either adhesive backing or conductive adhesive before applying the ESD flooring material over it.
When connecting to electrical outlets, remove the cover and grounding screw, then attach your copper strap through a punched hole. Run the strap down the wall and onto the floor, securing it with adhesive. For a professional finish, conceal the strap beneath the outlet cover and wall base.
Remember to follow ANSI/ESD S6.1-2005 guidelines and use AC equipment grounds when available. While you can use multiple grounding methods, adding more attachments won't increase your floor's conductivity.
Long-Term Investment Benefits
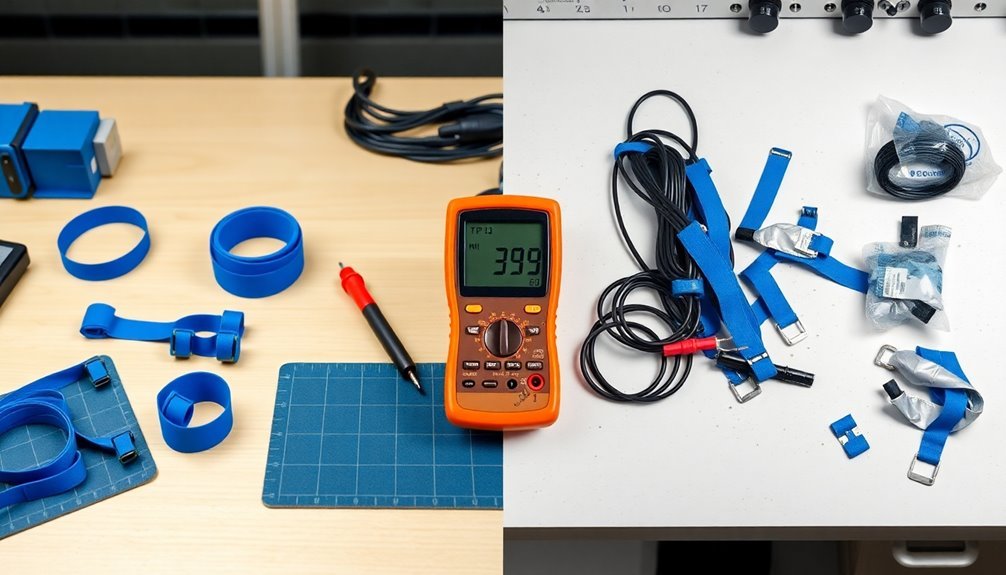
When evaluating anti-static protection options, considering the long-term investment benefits can greatly impact your bottom line. While reusable anti-static equipment requires a higher upfront investment, you'll find significant cost savings over time compared to disposable alternatives.
The durability of reusable protective gear means you won't need frequent replacements, making it easier to plan and manage your budget effectively.
You'll benefit from the superior material strength of reusable anti-static protection, as it's specifically designed to maintain its protective properties through extended use. These products are engineered to withstand regular wear and tear, ensuring consistent performance across multiple tasks or shifts.
Additionally, you're making an environmentally responsible choice, as reusable options substantially reduce waste and minimize your facility's environmental footprint.
However, you'll need to factor in proper maintenance costs and procedures. Implementing thorough cleaning and sanitation protocols is essential to prevent cross-contamination and maintain hygiene standards.
When calculating your return on investment, consider both the direct cost savings and the indirect benefits of reduced waste management expenses and improved sustainability compliance in your operation.
Frequently Asked Questions
Can Anti-Static Protection Fail if Exposed to Extreme Humidity Levels?
Yes, your anti-static protection can fail in extreme humidity. When it's too high, it'll degrade materials and cause corrosion, while low humidity increases static build-up and reduces the effectiveness of protective measures.
How Often Should Anti-Static Testing Be Performed on Reusable Equipment?
You'll need to test your anti-static equipment daily before use. Test wrist straps, footwear, and work surfaces at the start of each shift. You might need additional testing throughout the day in high-risk environments.
Do Anti-Static Properties Diminish When Mixing Different Brands of Protection?
Yes, mixing different brands can weaken your anti-static protection due to varying material compositions and manufacturing processes. You'll get more reliable protection if you stick to a single brand for consistent performance.
What Temperature Ranges Affect the Conductivity of Anti-Static Protective Gear?
You'll notice reduced conductivity in your anti-static gear below 23°C and above 35°C. Cold temperatures with low humidity especially decrease effectiveness, while extreme heat can permanently degrade protective properties.
Are There Special Storage Requirements to Maintain Anti-Static Effectiveness?
You'll need to store anti-static gear in dry, climate-controlled areas away from direct sunlight. Keep items in sealed containers, handle them with clean hands, and follow manufacturer guidelines to maintain effectiveness.
In Summary
Whether you're choosing reusable or disposable anti-static protection, you'll need to weigh your specific needs against cost, environmental impact, and long-term value. While disposables offer convenience, reusable options typically provide better protection and cost savings over time. You'll find that proper maintenance of reusable gear and consistent grounding practices will maximize your investment, regardless of which option you select.
Leave a Reply