ESD flooring must maintain electrical resistance between 100,000 and 1 billion ohms to meet industry standards like ANSI/ESD S20.20 and IEC 61340-5-1. You'll need your floors to dissipate a 5000V charge to less than 50V within 2 seconds. For most applications, you should target resistance between 1 million and 100 million ohms, while aerospace requirements follow FAA STD 019f standards of 1.0 x 10^6 to 1.0 x 10^9 ohms. Your complete person/footwear/flooring system shouldn't exceed 35 million ohms. These standards guarantee proper static control, but there's much more to maintaining an effective ESD floor system.
Understanding ESD Floor Resistance Ranges
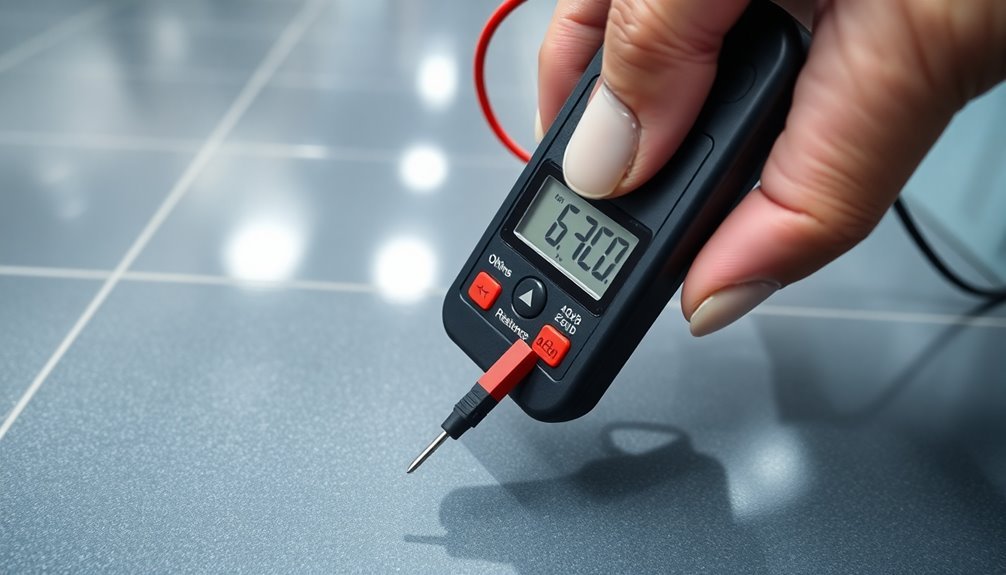
Nearly all ESD flooring must maintain electrical resistance between 10^5 and 10^9 ohms to meet industry standards.
You'll find that major guidelines like ANSI/ESD S20.20 and IEC 61340-5-1 specifically require resistance below 1.0 x 10^9 ohms, though most industry applications target a narrower range between 1 million and 100 million ohms.
You'll need to distinguish between two main categories of ESD flooring.
Static dissipative flooring operates in the 10^6 to 10^9 ohm range, making it ideal for electronics labs and server rooms.
Static conductive flooring, with resistance between 25,000 and 10^6 ohms, suits highly sensitive areas but carries a higher shock risk due to its lower resistance. Modern graphene nanotube technology has revolutionized conductive flooring materials with improved performance at lower loading rates. Regular copper grounding strips must be properly connected to ensure optimal conductivity.
When you're testing your ESD flooring, remember that environmental factors greatly impact resistance readings.
Temperature and humidity variations can affect performance, which is why testing often occurs in low-humidity conditions.
You'll want to maintain regular testing schedules following ANSI/ESD STM7.1 standards to guarantee your flooring continues meeting specifications.
Different industries may require specific ranges, such as FAA 019f's requirement of 10^6 to 10^9 ohms, so you'll need to verify your particular industry standards.
Essential Grounding Requirements
Proper ESD floor resistance depends heavily on a reliable grounding system. You'll need to ascertain your floor maintains a resistance of less than 1.0 x 10^9 ohms to ground, with all flooring pieces connected through copper grounding strips that create a traceable path to the ground source. Epoxy coating systems provide excellent chemical resistance while maintaining required conductivity standards. Resistance measurements must be conducted under controlled environments where humidity testing conditions can be maintained at 12% RH.
When installing an ESD floor, you must consider these critical requirements:
- Use conductive flooring products and adhesives specifically designed for ESD applications
- Install copper grounding strips that connect all flooring sections to the ground source
- Verify continuous conductivity between all floor sections during installation
- Test the complete system using both point-to-point and point-to-ground measurements
You'll need to conduct regular resistance testing using ANSI/ESD STM7.1-2013 standards, particularly at low relative humidity (12% RH) to eliminate moisture variables.
Walking voltage tests following ANSI/ESD STM97.2-2016 are also essential for evaluating your floor's performance.
Don't forget to maintain your ESD floor according to manufacturer guidelines and conduct regular inspections to identify any degradation in grounding capabilities.
Key Standards and Compliance
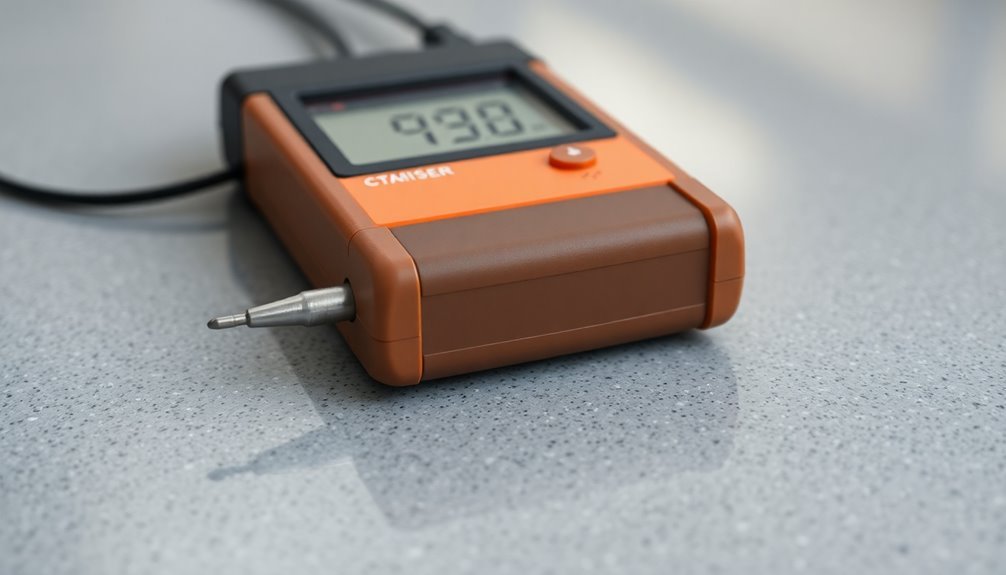
Standards governing ESD flooring systems set strict resistance requirements to guarantee effective static discharge control. Key regulations like ANSI/ESD S20.20 and IEC 61340-5-1 specify that flooring resistance must remain below 1×10^9 ohms at all points, while maintaining the ability to dissipate a 5000V charge to less than 50 volts within two seconds. Third-party testing must be conducted to verify resistance specifications. Global compliance standards provide assurance across different countries and regions.
You'll find industry-specific requirements vary based on application. The FAA STD 019f for aerospace environments requires resistance between 1.0×10^6 and 1.0×10^9 ohms, while telecommunications standards (ATIS 0600321) allow a slightly higher range up to 10^10 ohms.
To confirm compliance, you must test your flooring under controlled conditions, particularly at low humidity (12% RH).
When you're implementing ESD flooring, you'll need to take into account the complete person/footwear/flooring system, which shouldn't exceed 3.5×10^7 ohms. Static dissipative flooring typically ranges from 10^7 to 10^9 ohms, while conductive flooring measures below 10^5 ohms.
Regular testing is vital as traffic and maintenance chemicals can affect performance over time. Remember, meeting these standards isn't just about compliance—it's essential for preventing damage to sensitive electronics.
Testing Methods and Equipment
You'll need specialized resistance meters that comply with ANSI/ESD STM 7.1-2013 to properly test your ESD flooring materials.
Your testing protocols must include both point-to-point and point-to-ground measurements taken under controlled humidity conditions of 12% RH.
When conducting these measurements, you're required to use standardized monitoring equipment to verify that floor resistance falls between 1 x 10^6 and 1 x 10^9 ohms.
Ohmmeter Testing Requirements
Conducting reliable ESD floor testing requires specific ohmmeter equipment and testing methods that comply with ANSI/ESD STM7.1-2013 standards.
You'll need to follow strict testing protocols in a controlled environment, particularly maintaining low humidity levels (12% RH) to guarantee accurate measurements of both point-to-point and surface-to-ground resistance.
For compliant testing, you must adhere to these critical requirements:
- Pre-condition your flooring samples in a controlled environment before testing to achieve stable readings.
- Take multiple measurement points across the floor surface to verify consistent resistance values.
- Use calibrated ohmmeters that meet ANSI/ESD STM7.1-2013 specifications.
- Document both system resistance (including footwear) and walking body voltage measurements.
When conducting tests, you'll need to verify that your flooring meets specific resistance requirements, which vary by industry standard.
For example, ANSI/ESD S20.20 requires resistance less than 1.0 x 10^9 ohms, while FAA 019f specifications demand readings between 1.0 x 10^6 and 1.0 x 10^9 ohms.
Remember that installation quality and regular maintenance directly impact your floor's resistance performance, so you'll need to implement ongoing testing protocols to maintain compliance.
Resistance Measurement Protocols
Proper resistance measurement of ESD flooring requires specific testing protocols and specialized equipment conforming to ANSI/ESD STM7.1 standards.
You'll need to conduct both point-to-point (RTT) and resistance-to-ground (RTG) measurements to fully assess your floor's ESD control capabilities.
To guarantee accurate results, you must perform these tests in a controlled environment with low humidity (12% RH). This removes moisture as a variable that could affect your readings.
You should expect higher resistance readings in these drier conditions, which provides a more conservative assessment of your floor's performance.
Your testing protocol must verify that the flooring can dissipate a 5000V charge to less than 50 volts within 2 seconds.
You'll also need to conduct walking body voltage tests following ANSI/ESD STM97.2 to confirm that your floor prevents static charge accumulation.
The acceptable resistance range for ESD flooring typically falls between 10^5 and 10^9 ohms, though specific requirements may vary by industry standard.
For instance, FAA 019f specifies 10^6 to 10^9 ohms, while ATIS 0600321 allows up to 10^10 ohms for resistance to ground.
ESD Monitoring Equipment Standards
Guaranteeing accurate ESD floor testing requires specific monitoring equipment that meets rigorous industry standards. When you're conducting ESD floor tests, you'll need to follow established protocols like ANSI/ESD STM7.1, which provides standardized methods for measuring both point-to-point and surface-to-ground resistance.
Your testing environment must maintain controlled humidity levels to eliminate moisture as a variable, guaranteeing consistent and reliable results.
You'll need several essential components to properly test ESD flooring systems:
- Two-point resistance meters that comply with ANSI/ESD S20.20 specifications
- Copper grounding strips for connecting flooring to ground sources
- Calibrated electrodes for surface resistance measurements
- Temperature and humidity monitoring equipment
The testing process must incorporate both the flooring material and the complete system, including footwear and grounding straps.
When using conductive materials like carbon black or graphene nanotubes, you'll need equipment capable of measuring resistance ranges between 10^6 and 10^10 ohms, as specified by industry standards like ATIS 0600321 and FAA 019f.
Regular testing with proper equipment guarantees your ESD flooring maintains ideal performance throughout its service life.
Material Selection for ESD Flooring
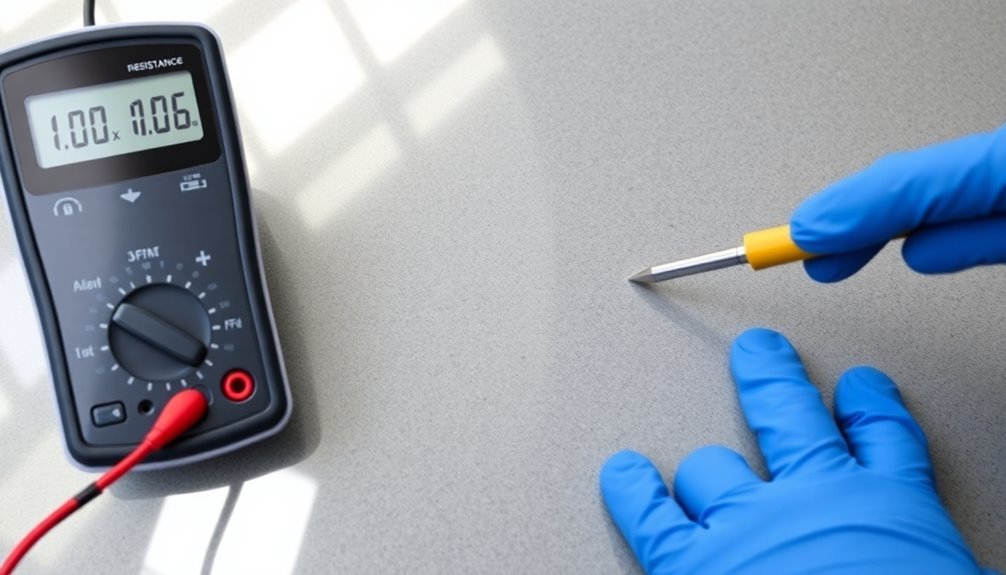
When you're selecting ESD flooring materials, you'll need to weigh the benefits of traditional options like carbon black and metal fibers against modern alternatives such as graphene nanotubes.
Traditional materials often present installation challenges and color limitations, while graphene nanotubes offer better aesthetic control and simpler installation processes.
Your material choice will impact both initial costs and long-term performance, with factors like durability, maintenance requirements, and resistance stability playing vital roles in the overall value proposition.
Traditional Vs Modern Materials
Making informed decisions about ESD flooring materials has evolved considerably over the past decade, with a clear divide between traditional and modern options.
While traditional materials like carbon black and tin oxide have served the industry, they often require high loading rates (6-20%) and complex installation processes, including conductive primers.
You'll find that modern materials, particularly graphene nanotubes, offer significant advantages over conventional options. These advanced solutions require minimal loading rates (0.01-0.05 wt%) and eliminate the need for conductive primers, simplifying your installation process.
- Traditional materials pose installation challenges and limited color control due to high loading requirements.
- Modern graphene-based solutions create effective 3D conductive networks with minimal material usage.
- Conventional options often require special primers and risk creating "hot spots."
- Advanced materials provide better resistance stability across temperature and humidity variations.
When you're choosing between traditional and modern materials, consider that newer options like graphene nanotubes not only reduce environmental impact but also offer better color control and finish options.
You'll achieve more reliable static dissipation while avoiding the common pitfalls of traditional materials, such as orange peel effects and inconsistent conductivity.
Performance by Material Type
Through careful material selection, you'll discover significant performance variations between static dissipative and conductive ESD flooring options.
Static dissipative materials offer resistance between 1 × 10^6 and 1 × 10^9 ohms, making them ideal for electronics manufacturing facilities. You'll find they effectively prevent static buildup while avoiding shock hazards common with more conductive options.
When you're considering conductive materials, you'll need to account for their resistance levels below 1 × 10^5 ohms. While they're highly effective at dissipating charges, they can pose shock risks, especially below 2.5 × 10^4 ohms. You'll mostly see these materials in specialized applications like munitions handling areas.
Modern innovations have introduced graphene nanotubes, which you can implement at minimal loading (0.01-0.05 wt.%). You'll appreciate their ability to maintain color control and finish quality without the dark shades and hot spots typical of traditional conductive materials.
For compliance, you'll need to ascertain your chosen material meets ANSI/ESD S20.20 standards, dissipating 5000V charges to under 50 volts within 2 seconds. Regular testing using ANSI/ESD STM7.1-2013 methods will confirm your floor's ongoing performance.
Cost-Benefit Material Analysis
Anyone evaluating ESD flooring materials must weigh several key cost factors against performance benefits. While traditional materials like carbon black and tin oxide have been industry standards, they often require higher loading rates of 6-20%, leading to increased material costs and installation complexities. Modern cleanroom and pharmaceutical applications have driven innovation in ESD flooring materials.
Consider these vital cost-benefit factors when selecting ESD flooring materials:
- Graphene nanotubes offer significant savings with loading rates of just 0.01-0.05%, reducing both material costs and environmental impact.
- You'll eliminate the need for conductive primers with certain materials, cutting installation costs and simplifying the process.
- Traditional conductive materials limit color options and create installation challenges, potentially increasing your overall project expenses.
- Long-term compliance testing requirements affect your maintenance budget, making material durability essential.
Graphene nanotube-based floors provide superior value through consistent performance and easier installation. They meet all ANSI/ESD and IEC standards while offering better aesthetic control and sustainability benefits.
You'll achieve the required resistance range of 1.0 x 10^6 to 1.0 x 10^9 ohms without compromising on color choices or risking performance inconsistencies that could lead to costly replacements.
Installation Best Practices
The successful installation of ESD flooring systems requires careful attention to several critical components and procedures.
You'll need to ascertain proper electrical connectivity throughout the entire floor system by installing copper grounding strips that connect all flooring pieces. These strips, combined with conductive adhesive, create a continuous path for static charge dissipation.
To maintain compliance with industry standards, you must use conductive adhesive specifically designed for ESD applications. Don't substitute regular adhesives, as they'll compromise the floor's electrical performance.
You'll also need to verify that the resistance measurements fall between 1.0 x 10^6 and 1.0 x 10^9 ohms for both point-to-point and surface-to-ground readings.
Once you've completed the installation, implement a regular testing schedule to monitor the floor's performance. You should conduct resistance measurements using ANSI/ESD STM7.1 protocols and walking body voltage tests following ANSI/ESD STM97.2-2016.
Don't forget to establish a cleaning routine using appropriate ESD-safe cleaning products to maintain the floor's electrical properties. Remember that your occupants may need ESD footwear or ground straps to complete the static control system effectively.
Performance Monitoring Over Time
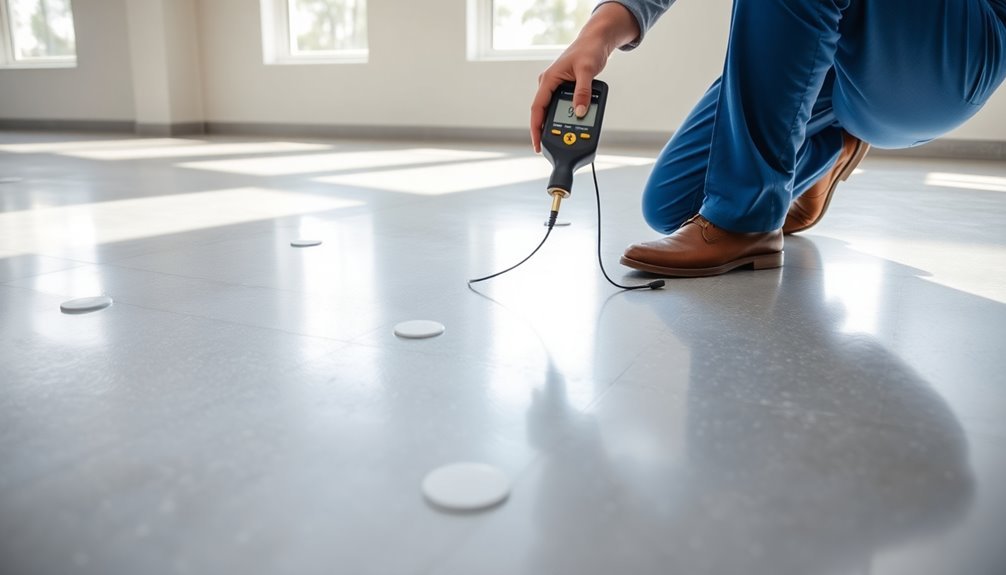
Regular monitoring of ESD floor performance involves three vital testing protocols that guarantee your flooring system maintains its protective qualities. You'll need to conduct both point-to-point and surface-to-ground resistance testing following ANSI/ESD STM7.1 and IEC 61340-4-1 standards to ascertain compliance.
Your ESD flooring's resistance properties can degrade over time due to:
- Heavy foot traffic wearing down conductive materials
- Harsh cleaning chemicals affecting the floor's composition
- Environmental factors like temperature fluctuations
- Uneven material dispersion across the surface
You'll want to perform your resistance testing in controlled environments with low humidity levels to get accurate readings. This guarantees your floors will perform effectively across all humidity conditions.
When testing, you're measuring how quickly current passes across the floor surface, which must fall between 1 million and 100 million ohms. If your floors don't meet these specifications, you'll need to evaluate restoration or replacement to maintain safety standards.
Environmental Impact on Resistance
Understanding environmental factors is vital when managing ESD floor resistance. You'll find that temperature and humidity greatly influence your floor's performance, with higher temperatures typically increasing conductivity while higher humidity reduces electrical resistance. To guarantee accurate testing, you'll need a temperature-controlled environment with low humidity levels (around 12% RH).
Factor | Impact | Control Measure |
---|---|---|
Temperature | Affects material conductivity | Maintain controlled testing environment |
Humidity | Reduces electrical resistance | Test at low RH (12%) |
Installation | Determines system effectiveness | Use proper conductive materials |
Degradation | Changes resistance over time | Implement regular testing |
Your floor's resistance properties will also depend on the type of conductive materials used and their installation method. Whether you're using carbon black, tin oxide, or metal fibers, proper installation with conductive adhesives and grounding strips is essential for meeting resistance requirements. Don't forget that your ESD floor will degrade over time due to foot traffic, cleaning chemicals, and general wear. You'll need to implement regular testing and maintenance programs to guarantee your floors continue meeting resistance standards throughout their service life.
Graphene Nanotube Technology Benefits
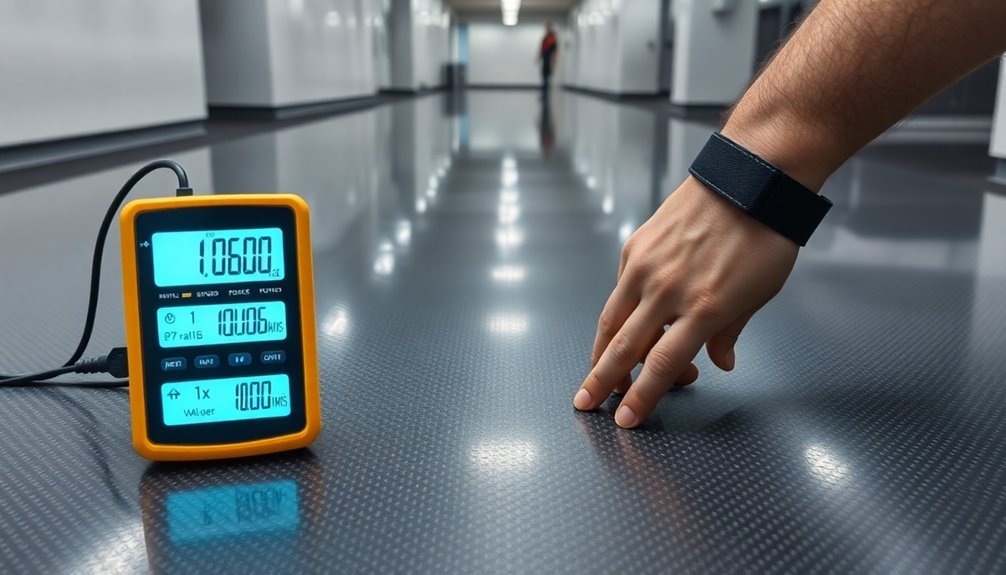
Recent advances in graphene nanotube technology have revolutionized ESD flooring solutions, offering unprecedented performance benefits. When you incorporate TUBALL graphene nanotubes into your ESD flooring, you'll gain enhanced electrical conductivity while maintaining structural integrity. The 3D reinforced network created by well-dispersed nanotubes ensures optimal performance throughout the material.
These nanotubes, with their single-layer structure and impressive length of ≥5 µm, create consistent conductive networks throughout the flooring material.
Here's what you can expect from graphene nanotube-enhanced ESD flooring:
- Superior conductivity performance with minimal material usage, thanks to the nanotubes' high CNT content of ≥80%
- Increased durability and longevity due to improved tensile strength and material cohesion
- Lighter weight flooring solutions without compromising protective qualities
- Consistent electrical resistance across the entire floor surface, eliminating hot spots and dead zones
The scalable production methods developed by industry leaders guarantee you'll have access to these advanced materials at competitive prices.
With patent protection in over 40 countries and continuous R&D developments, you can trust in the long-term viability of graphene nanotube technology for your ESD flooring needs.
Long Term Maintenance Protocols
While graphene nanotube technology enhances ESD flooring performance, maintaining these advanced surfaces requires a detailed, long-term approach.
You'll need to implement regular testing protocols to measure electrical resistance and charge dissipation, following ANSI/ESD STM7.1 standards in controlled environments, particularly at low humidity levels.
You must clean your ESD floors regularly using appropriate cleaning agents that won't compromise the floor's conductive properties. With proper maintenance, you can expect your ESD flooring to last 20 years or more.
However, you'll need to monitor how cleaning chemicals and foot traffic affect the floor's performance over time.
To maintain compliance with ANSI/ESD S20.20 and IEC 61340-5-1 standards, you'll need to verify your floors consistently maintain resistance between 1 million and 100 million ohms.
You should conduct walking body voltage tests using ANSI/ESD STM97.2-2016 to verify that your floors effectively dissipate static charges.
Remember, your floors must reduce a 5000V charge to less than 50 volts within 2 seconds.
Don't rely solely on resistance measurements; you'll need to evaluate both charge dissipation and voltage generation to guarantee thorough ESD protection.
Frequently Asked Questions
Can ESD Flooring Be Installed Over Existing Concrete With Moisture Issues?
You can install ESD flooring over concrete with moisture issues, but you'll need specialized moisture mitigation systems first. It's essential to address moisture problems before installation to guarantee proper ESD performance and longevity.
How Long Does Conductive Adhesive Take to Cure Before Use?
You'll find conductive adhesives typically cure in 24-96 hours at room temperature. If you're in a hurry, you can speed up curing with heat – some products cure in just 10 minutes at 65°C.
Do Cleaning Chemicals Affect the ESD Flooring's Resistance Properties?
Yes, cleaning chemicals can greatly affect your ESD flooring's resistance. They'll degrade the conductive materials over time, potentially increasing floor resistance. That's why you'll need regular testing after cleaning to verify proper performance.
What Happens if ESD Flooring Is Exposed to Direct Sunlight?
When your ESD flooring is exposed to direct sunlight, you'll face increased resistance due to temperature changes, UV degradation of conductive materials, and humidity variations. This can compromise your floor's static-dissipative properties over time.
Can Portable ESD Mats Achieve the Same Resistance Standards as Permanent Flooring?
Yes, you'll find that portable ESD mats can meet similar resistance standards (10^6 to 10^9 ohms), but they won't provide the same level of consistent grounding and charge dissipation as permanent flooring solutions.
In Summary
You'll need to regularly monitor and maintain your ESD flooring to guarantee it stays within the required resistance standards of 1.0 x 10^6 to 1.0 x 10^9 ohms. Remember to conduct quarterly resistance testing, keep the surface clean, and document all measurements. With proper care and attention to grounding requirements, your ESD flooring will continue providing reliable static protection for your sensitive equipment and operations.
Leave a Reply