Exact measurements for static control film facilitate you'll achieve ideal performance and prevent costly ESD damage to sensitive components. You'll save money by avoiding material waste and rework while maintaining surface resistivity between 10^6 and 10^8 ohms/sq. Precise measurements help your films maintain rapid decay times under 0.05 seconds, guaranteeing immediate static dissipation. Your production yield rates will improve with accurate monitoring, and you'll reduce energy consumption by up to 29% annually in climate-controlled environments. Proper measurement practices release a world of benefits for your static control applications.
Precise Measurement Benefits
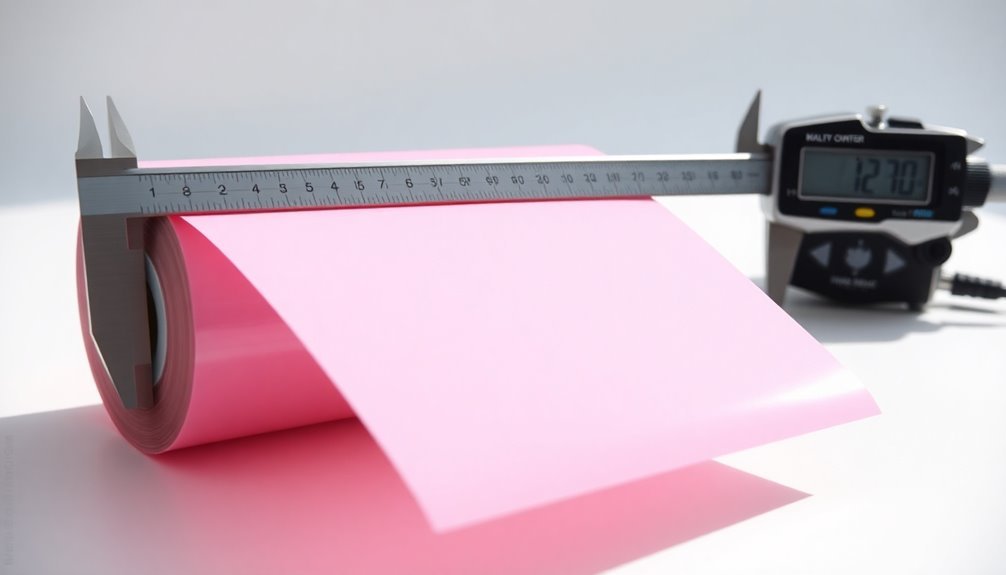
When working with static control film, precise measurements serve as the foundation for effective static management. You'll find that accurate measurements help you enhance your static eliminators and markedly improve your production yield rates.
By implementing high-precision measurement practices, you're better equipped to prevent costly ESD damage and reduce component failures in your manufacturing process. The rapid decay time of 0.05 seconds ensures immediate dissipation of harmful static charges.
You can't afford to rely on guesswork when it comes to static control, especially in high-value electronics manufacturing. With precise measurements, you'll be able to identify specific areas where static buildup occurs and evaluate how effectively your current static elimination methods are working. The enhanced durability of properly measured ESD PET films provides reliable protection against mechanical stress during handling.
This allows you to make data-driven decisions about your static control strategies and maintain ideal conditions without resorting to excessive humidity levels.
Your ability to continuously monitor static electricity levels will help you detect new problem areas before they cause damage.
You'll also find that accurate measurements are essential for preventing contamination-related rejects in clean manufacturing operations.
Film Performance Standards
In accordance with industry requirements, static control film must meet rigorous performance standards to assure reliable ESD protection. You'll find that high-quality films like TMF-300 Check Film and ABF-300 ESD Control Film deliver surface resistivity between 10^6 and 10^8 ohms/sq, assuring consistent static dissipation across their surfaces.
These films provide exceptional material properties that you can rely on:
- High tensile strength and tear resistance for durability in demanding manufacturing environments
- Chemical resistance to protect against solvent damage while maintaining dimensional stability
- Optical clarity that won't compromise visibility during PC board inspection processes
The pressure-sensitive adhesive enhances versatility during installation on smooth, flat surfaces. Pentastat's extensive product line ensures optimal film selection for every application. You'll appreciate how these films maintain their performance regardless of humidity levels, with electrostatic decay times under 0.05 seconds per Federal Test Standard 101C.
When properly grounded, they can't generate triboelectric charges, making them ideal for electronics manufacturing and packaging applications. Meeting stringent standards like ASTM D257 and EOS/ESD S11.11, these films are produced in GMP-compliant facilities worldwide to assure consistent quality and supply.
Their thermoforming capabilities and adhesive backing options give you flexibility in creating custom protective solutions for your sensitive electronic components.
Quality Control Essentials
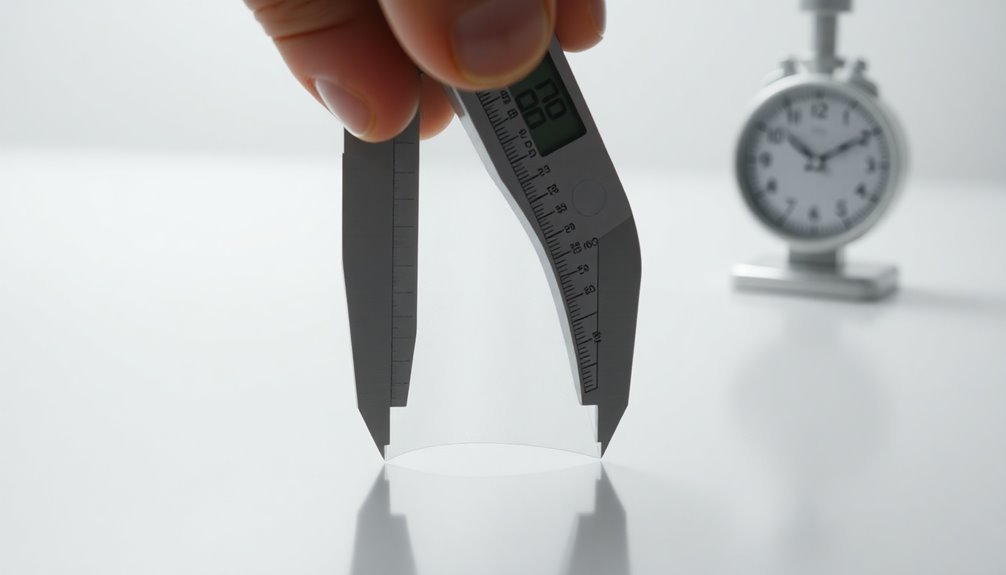
Maintaining proper static control requires precise measurement techniques and reliable quality control protocols. You'll need to use appropriate static measurement tools, such as handheld static meters in non-hazardous environments or ATEX-certified meters in hazardous areas, to effectively monitor your static control film's performance. The surface voltage measurement at 100mm distance provides optimal capacitance for accurate readings.
When you're taking measurements, remember that accuracy depends heavily on proper technique. You'll want to approach the object slowly from a distance to avoid sensor damage and discharge issues. Many facilities incorporate AC and DC ionizers to ensure balanced static neutralization during measurements.
Keep in mind that nearby grounded bodies, small objects, or incorrect measurement distances can lead to errors in your readings.
To guarantee consistent quality control, you'll need to regularly check your static eliminators' performance and identify areas requiring additional static control. Use calibration plates (200mm x 200mm) when calibrating your instruments, and take special care when measuring objects of different sizes.
Your measurements should focus on voltage levels and polarity across various parts of your machinery, including rollers and sheets. By maintaining precise measurement protocols, you'll be able to identify static buildup early, improve your production processes, and maintain better control over issues like runnability and color consistency.
Cost Savings Through Accuracy
Achieving precise measurements for static control film directly impacts your bottom line through substantial cost savings. When you take accurate measurements, you'll prevent costly overestimation that leads to wasted materials and unnecessary expenses.
You're also protecting yourself from underestimation scenarios that require additional film purchases and create project delays. Proper measurements help prevent static generation issues that commonly occur through material contact and separation.
Professional installations demand precision, and you'll find that exact measurements contribute to financial efficiency in several ways:
- You'll minimize material waste by ordering exactly what you need, reducing excess inventory costs and disposal of unused film.
- You'll save on labor costs by avoiding time-consuming rework and adjustments that stem from measurement errors.
- You'll maintain warranty compliance and customer satisfaction, preventing potential financial losses from rejected installations.
With installation costs ranging from $4 to $19 per square foot, accurate measurements become even more critical.
Your investment in accurate measurement practices pays off through streamlined installations and reduced overall project costs.
By following professional measurement standards and verifying dimensions twice, you're setting yourself up for profitable installations.
Material Waste Prevention Methods
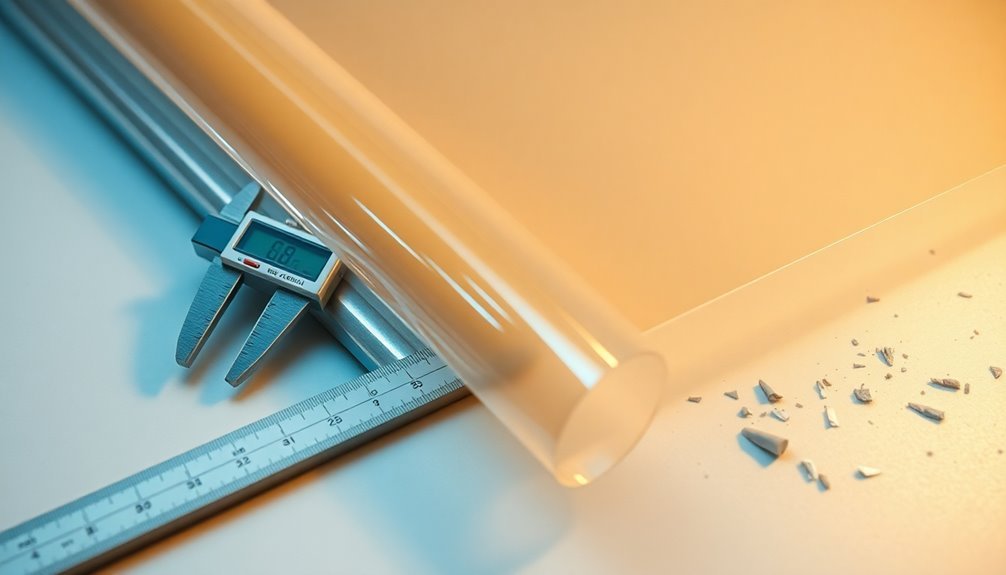
Building on the cost-saving benefits of precise measurements, effective material waste prevention starts with strategic static control implementation. You'll find that properly positioned static eliminators at vital points in your production line can dramatically reduce material waste and prevent costly production interruptions. Eliminating static during unwinding and sealing helps maintain product integrity in packaging lines. A comprehensive maintenance program for static control devices ensures optimal performance and prevents unexpected downtime.
Process Point | Problem | Solution |
---|---|---|
Film Unwinding | Dust attraction & contamination | Static eliminators before sealing bars |
Bottle Processing | Misalignment & jamming | Static control during sleeving/banding |
Material Handling | Static-induced defects | Eliminators at winder/unwinder stations |
To maximize your waste reduction efforts, you'll need to pay special attention to packaging material optimization. When you're working with thinner films, it's important to select the right anti-static additives, like Einar® 601, which offers superior migration efficiency in PE films. You'll also want to take into account that reduced thickness can affect migratory additive performance, so you might need to adjust concentrations or explore alternative technologies. Remember that proper static control isn't just about preventing waste – it's also essential for maintaining consistent quality in processes like form-fill-seal operations and injection molding.
Automated Measurement Systems
Your automated measurement systems can now provide real-time monitoring of static control film quality through integrated electrostatic sensors that continuously track electric field intensity.
You'll benefit from immediate alerts and consistent measurements across multiple points in your production line, helping you identify and address static issues before they affect product quality.
The integration of these sensors with static eliminators guarantees precise control and ideal placement of static control measures, greatly reducing the risk of material waste and production delays.
Real-Time Quality Monitoring
Modern static control demands precision monitoring, and automated measurement systems deliver exactly that through real-time quality control.
You'll benefit from continuous feedback systems that instantly alert you to any deviations from established parameters, ensuring your static control film maintains ideal performance. These sophisticated monitoring solutions provide immediate visual and audible alarms if failures occur, eliminating the need for time-consuming manual testing.
With PLC integration and closed-loop systems, you're able to harness Industry 4.0 capabilities for automated adjustments and thorough data logging. The permanently mounted sensors give you a live picture of charge presence and neutralization effectiveness, while user-defined thresholds trigger automatic process modifications.
- Real-time visualization software lets you monitor entire facilities with color-coded statuses and hyperlinked devices, making facility-wide oversight straightforward and efficient.
- Advanced data management systems enable you to generate summary reports categorizing faults by type and duration, helping you identify trends and potential issues.
- Remote adjustment capabilities allow you to modify monitor limits through the app, ensuring you maintain precise control without physical intervention.
These automated systems greatly reduce human error while improving both accuracy and production efficiency, making them essential for modern static control operations.
Sensor Integration Benefits
Successful static control strategies hinge on the powerful benefits of integrated sensor systems. You'll achieve enhanced production efficiency through real-time monitoring and instant adjustments, reducing reject rates and cutting prototyping time by up to 30%. The integration of thin film sensors provides precise measurements across multiple parameters, guaranteeing your production processes maintain peak performance.
Benefit Category | Key Features | Impact |
---|---|---|
Production | Real-time monitoring | 30% faster prototyping |
Static Control | Multi-point measurement | Prevents equipment damage |
Material Usage | Precise measurement | Reduced waste costs |
Safety | Continuous monitoring | Fire risk reduction |
Integration | Universal application | Easy system adaptation |
Your manufacturing process benefits from advanced static control capabilities, where electrostatic sensors continuously measure and respond to static electricity levels. You'll notice improved product quality through consistent monitoring and precise adjustments. The system's flexibility allows you to integrate these sensors into existing equipment, regardless of machine geometry or production conditions. The durability of thin film sensors guarantees reliable performance under high pressures and temperatures, while their standardized design keeps integration costs manageable. You'll also gain valuable insights through real-time data analysis, enabling immediate fault detection and dynamic process enhancement.
Static Control Testing Requirements
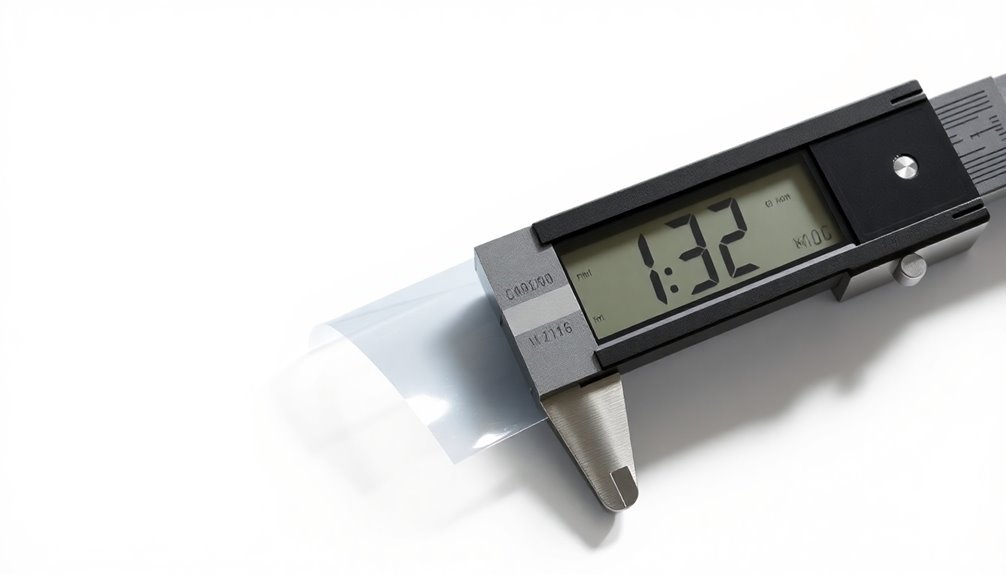
Effective static control testing requires a thorough approach to identify, measure, and manage static electricity in film production environments.
You'll need to implement regular testing schedules and use specific equipment to maintain ideal static control in your production process.
Your testing requirements should include consistent fieldmeter measurements to monitor static charges, surface resistance testing to evaluate material performance, and film wrap tests to assess charging characteristics.
It's essential to conduct these tests during product changes, seasonal variations, and as part of your routine quality assurance procedures.
- You must use proper testing equipment, including fieldmeters, handheld static meters, and surface resistance meters, to obtain accurate measurements.
- You'll need to establish regular testing frequencies that account for environmental changes, equipment maintenance, and product modifications.
- You should integrate ionization techniques and static bars into your testing protocol to verify neutralization effectiveness.
Environmental Impact Considerations
You'll find that precise measurements in static control film production directly reduce material waste by minimizing scrap rates and preventing quality control issues.
Your attention to exact specifications enables eco-friendly production methods through thinner packaging layers and optimized anti-static additives that maintain effectiveness while using fewer resources.
When you implement proper static control measurements, you'll achieve significant energy conservation through reduced machine cleaning time, fewer production slowdowns, and more efficient overall processes.
Waste Reduction Through Precision
Precision in static control film measurements plays a pivotal role in reducing environmental waste throughout the manufacturing process. When you're working with exact measurements, you'll greatly minimize scrap material while maintaining stringent quality standards.
This precision-focused approach doesn't just cut down on waste – it translates into substantial cost savings and a reduced carbon footprint.
By implementing precise measurements in your static control film applications, you'll optimize material usage across multiple areas:
- Custom-sized films eliminate excess packaging waste while ensuring proper protection for static-sensitive components
- Efficient production processes reduce energy consumption in manufacturing and transportation
- Exact measurements extend product shelf life, minimizing replacement needs and disposal requirements
Your commitment to precision directly impacts sustainable disposal practices. When you use exactly measured static control films, you'll reduce the volume of materials requiring disposal.
If you're using biodegradable options like Eco-Corr Film ESD, you'll further minimize environmental impact through commercial composting facilities. This approach aligns with ISO 14001:2015 standards while ensuring efficient waste management practices throughout the product lifecycle.
Eco-Friendly Production Methods
Modern eco-friendly production methods consistently transform the landscape of static control film manufacturing.
When you choose exact measurements for your static control film, you're supporting production techniques that greatly reduce environmental impact through precision extrusion and multi-layer co-extrusion, minimizing waste and energy consumption.
You'll benefit from films made with sustainable polymers derived from renewable sources like sugarcane and cornstarch, which comply with strict standards such as EN 13432 for compostable plastics.
These materials reduce dependency on non-renewable resources while maintaining high performance standards.
The EUCertPlast certification guarantees you're getting products with verified recycled content claims.
Energy Conservation Practices
Energy conservation practices in static control film applications deliver substantial environmental benefits through advanced window technologies.
You'll find that precise measurements in window film installation maximize energy efficiency, leading to significant reductions in heating and cooling costs. When you install properly measured static control films, they can reject up to 58% of total solar energy while maintaining ideal indoor temperatures year-round.
- Your building's energy consumption can decrease by up to 29% annually in warm climates through strategically installed window films.
- You'll contribute to climate change mitigation efforts by reducing your carbon footprint through decreased energy demand.
- Your investment in properly measured films guarantees long-term environmental benefits through continuous energy savings.
Production Process Optimization
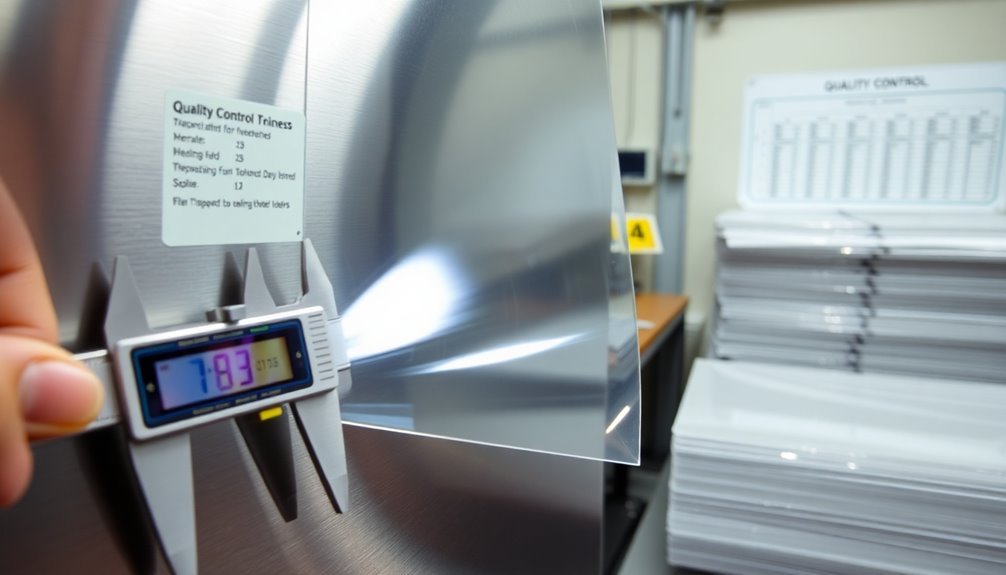
Maximizing production efficiency in static control film manufacturing requires a thorough approach to process enhancement. You'll need to focus on precise measurements and monitoring techniques to guarantee consistent quality while maintaining high productivity levels.
To enhance your production process, you'll want to implement continuous monitoring using field meters to identify static generation points. This allows you to strategically place static control devices for maximum effectiveness.
You should evaluate both passive and active control methods, selecting the most appropriate solution for your specific needs.
Your material selection plays a vital role in enhancement. By choosing materials with anti-static properties, you'll reduce static generation at the source. It's important to regularly audit your processes and maintain proper documentation of static levels throughout the production line.
Don't overlook the importance of equipment reliability in your enhancement strategy. You'll need to guarantee your static control devices are properly maintained and positioned for peak performance.
Consider partnering with OEM suppliers who can provide expertise in integrating effective static control solutions into your production line. Remember that successful enhancement requires a balance between quality control, safety measures, and production efficiency.
Measurement Equipment Selection
When you're selecting measurement equipment for static control film, you'll need to carefully match precision tool requirements with your specific production needs, considering factors like measurement range and accuracy levels.
While high-end static meters offer advanced features and superior precision, you'll want to weigh these capabilities against your budget constraints through a detailed cost-benefit analysis.
Regular calibration schedules must be established for your chosen equipment, as even the most expensive meters require consistent maintenance to guarantee reliable readings.
Precision Tool Selection Criteria
For accurate static control measurements in film applications, selecting the right precision tools is essential to your success. You'll need to take into account both the measurement range and sensitivity of your devices to guarantee they're suitable for your specific film applications.
When choosing precision tools, focus on equipment that offers the right balance of accuracy and practical functionality for your production environment.
Your measurement tools should align with these critical requirements:
- Direct measurement capabilities through fieldmeters for immediate static readings on film surfaces
- Appropriate sensitivity ranges that can detect subtle variations in static levels across different film types
- Certified compliance with safety standards, especially if you're working in hazardous environments
Reflect on the physical aspects of your measurement needs, including the size of your film materials and the distance at which you'll need to take measurements.
You'll want tools that can provide consistent readings while maintaining accuracy across your entire production line. Remember that continuous monitoring capabilities are particularly valuable for film applications, as they'll help you identify static issues before they affect product quality.
Choose devices that offer both portability and durability to guarantee reliable measurements throughout your facility.
Cost Vs Capability Analysis
Throughout the selection process for static measurement equipment, you'll need to weigh both cost implications and measurement capabilities against your specific requirements. While fieldmeters offer cost-effectiveness for long-term use, specialized ATEX-certified meters command higher prices due to safety certifications.
Consider your specific application needs when evaluating measurement tools:
Equipment Type | Cost vs. Capability Consideration |
---|---|
Fieldmeters | High initial investment but long-term savings through reduced waste and reliable measurements |
Coulomb Meters | Higher cost for precision but essential for lab-quality measurements on small samples |
Non-Contact Voltmeters | Premium pricing justified by contamination-free measurements and production line suitability |
Static Meters | Cost-effective for frequent measurements with immediate feedback capability |
Specialized Meters | Highest cost tier but necessary for hazardous environments |
You'll find that each tool offers distinct advantages that may justify its cost. Fieldmeters and static meters provide the best value for general applications, while specialized equipment like non-contact voltmeters and ATEX-certified meters deliver vital capabilities for specific scenarios where safety or contamination concerns are paramount. Match your selection to your process requirements while considering both immediate costs and long-term benefits.
Calibration Requirements Matter
Proper calibration stands at the core of reliable static measurement equipment selection. When you're choosing measurement devices for static control film, you'll need to guarantee they maintain their accuracy through regular calibration. Your equipment's precision directly impacts the effectiveness of your static control measures, making calibration requirements a vital factor in your selection process.
Consider these essential calibration aspects when selecting your measurement equipment:
- Verify that the device includes clear manufacturer guidelines for calibration intervals and procedures specific to static measurements.
- Check if the equipment comes with certification and compliance documentation for relevant industry standards.
- Confirm you have access to qualified personnel or services for performing calibration maintenance.
You can't afford to overlook calibration requirements, as incorrect measurements can lead to costly consequences. Your static control film's effectiveness depends on accurate readings, and non-calibrated equipment puts your entire process at risk.
Remember to factor in the ongoing costs and time requirements for regular calibration when evaluating different measurement options. By choosing equipment with straightforward calibration procedures and reliable support, you'll maintain the precision needed for effective static control.
Frequently Asked Questions
How Often Should Static Control Film Measuring Equipment Be Recalibrated?
You'll need to recalibrate your static control film measuring equipment every 6-12 months, depending on usage frequency, environmental conditions, and manufacturer's guidelines. More frequent use requires more frequent recalibration.
Can Static Control Films Be Measured Accurately in High Humidity Environments?
You'll face challenges measuring static control films in high humidity since moisture increases conductivity. While you can still take measurements, they won't be as accurate as in dry conditions. Consider environmental controls first.
What's the Maximum Thickness Variation Acceptable for Industrial-Grade Static Control Films?
You'll need to maintain thickness variations within ±0.5 V/mm for industrial-grade static control films. If you're working with standard Kapton films, don't exceed a 3.2x variation range between minimum and maximum thickness.
Do Different Colored Static Control Films Require Different Measurement Calibration Settings?
Yes, you'll need different calibration settings for colored static control films since pigments and additives can affect their electrical properties. You should adjust your measurement tools based on each film's specific characteristics.
How Do Temperature Fluctuations Affect the Accuracy of Static Film Measurements?
You'll find temperature changes considerably impact your static film readings. When temperatures rise, you'll get higher static levels, while drops can reduce measurements. You'll need regular calibration to maintain accuracy.
In Summary
You'll find that exact measurements for static control film aren't just about precision – they're essential for your bottom line. By implementing accurate measurements, you're ensuring peak performance, reducing waste, meeting quality standards, and maximizing cost efficiency. Whether you're handling sensitive electronics or managing production processes, precise measurements will protect your investment and deliver consistent, reliable static control results.
Leave a Reply