To properly test static-free packaging, you'll need to employ seven key methods. Start with surface resistance testing using a concentric ring fixture in controlled humidity conditions. Then perform volume resistance measurements with specialized electrometers to check through-material properties. Next, evaluate electrostatic decay performance and conduct static shielding tests with a 1kV Human Body Model discharge. You'll also want to analyze charge retention, run environmental impact tests in varying conditions, and verify material compliance against ANSI/ESD standards. The deeper you explore these testing protocols, the better you'll protect your sensitive electronic components.
Surface Resistance Testing Methods
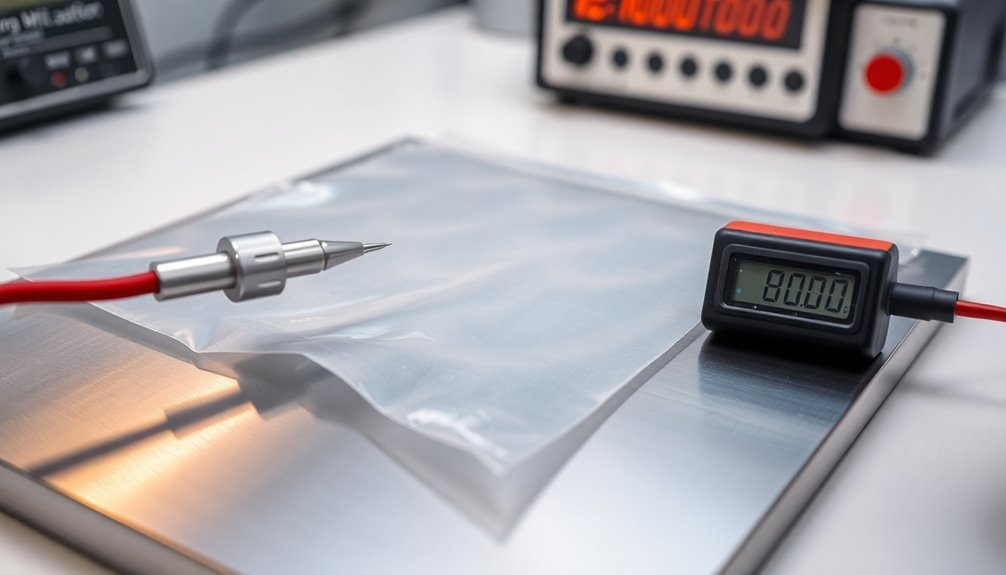
Various international standards govern surface resistance testing for static-free packaging, with key protocols including ESD STM11.11-2015, ASTM D257, and IEC 62631-3-1.
You'll need to follow specific test conditions, including maintaining 12%±3% relative humidity and 73±5°F for a minimum of 48 hours before testing, as specified by ANSI/ESD STM11.11.
To conduct surface resistance testing, you'll use a concentric ring fixture that measures both the inside and outside surfaces of packaging materials. You'll place an electrode assembly on your test specimen and apply a DC potential for 60 seconds to obtain resistance measurements.
Your test specimens should be 4-inch disks or squares, though you can use specimens as small as 3.5 inches. Testing should be performed at varying humidity levels to ensure consistent performance across different environmental conditions.
When you're testing static-free packaging, you'll need to take into account several critical factors. Humidity greatly affects surface resistance, so you must maintain strict environmental controls. Visual inspection alone is not sufficient for determining proper ESD protection compliance.
You'll also need to take into account material variability, as different packaging materials display varying levels of static dissipation.
Remember to calculate surface resistivity using both the measured resistance and your specimen's dimensions to guarantee compliance with the standard's requirement of <1.0 x 10^11 ohms.
Volume Resistance Measurement Techniques
You'll need specialized equipment like electrometers and resistivity meters to accurately measure the through-material resistance of static-free packaging materials.
Before testing, verify your equipment is properly calibrated and your test specimens are prepared according to ASTM D257 standards, with appropriate electrodes placed on opposite sides of the material.
Using source voltage methods instead of source current is recommended above 1G ohm when testing static-free packaging materials.
Through-Material Testing Methods
Testing static-free packaging requires a thorough understanding of through-material measurement techniques, particularly volume resistance testing.
You'll need to evaluate the electrical properties through the material's thickness using electrodes that measure resistance in liquids, powders, and solids. This testing method helps you determine if your packaging materials fall within the static dissipative range of 1×10^4Ω/sq to 1×10^11Ω/sq.
To guarantee accurate results, you must perform tests under controlled conditions while considering these critical factors:
- Material composition and purity – contamination can greatly affect your measurements and lead to misleading results.
- Environmental conditions – testing at various humidity levels simulates real-world scenarios your packaging will encounter.
- Surface characteristics – roughness and moisture content directly impact static properties.
Specialist support is available through consultation services for complex testing inquiries.
You'll need to comply with ANSI/EOS/ESD S11.11-2001 standards when conducting these tests. Regular impedance measurement tests should be performed to evaluate the resistance between two points on the material surface.
The data you collect helps determine if your packaging materials provide adequate ESD protection for sensitive electronic components during shipping and storage.
Equipment Setup and Calibration
Building on the principles of through-material testing, proper equipment setup and calibration form the backbone of accurate volume resistance measurements.
You'll need to start by confirming your surface resistance meters and rubber electrodes meet current ESD standards and have valid calibration certificates traceable to national standards.
When setting up your testing equipment, you'll want to connect your 2-point probes or concentric rings correctly to measure point-to-point resistance. For specialized needs, consider exploring ESD Check's test equipment for reliable measurement tools.
It's essential to verify that your variable resistance indicators are functioning properly before beginning any measurements. Consider using the Warmbier METRISO® 3000 for comprehensive testing capabilities. You must maintain regular calibration schedules and document all calibration activities to guarantee measurement accuracy.
Before conducting any tests, you'll need to confirm that your equipment complies with recognized ESD standards.
During setup, position your measurement devices according to the specific test requirements – whether you're performing point-to-point measurements or surface-to-ground testing.
You should check all connections and confirm proper contact between electrodes and the packaging material.
Remember to record baseline measurements and verify that your data collection system is ready to capture and store results systematically.
If you're using ionization testing equipment, make sure it's properly positioned to evaluate charge neutralization effectiveness.
Environmental Impact Factors
Environmental conditions consistently play a crucial role in volume resistance measurements of static-free packaging. You'll need to maintain precise temperature and humidity control during both conditioning and testing phases to guarantee accurate results. Super megohm meters provide the most reliable testing capabilities for these measurements.
The standard conditioning requirements of 23°C and 50% RH for 24 hours serve as your baseline, though some applications may require stricter controls like ANSI/ESD STM11.11's specifications of 12%±3% RH at 73°F±5°F for 48 hours.
Humidity's impact on your measurements can't be overstated, as it directly affects material resistivity. You'll notice that your packaging materials become more conductive at higher humidity levels and more insulative in drier conditions. To achieve reliable test results, you must carefully monitor and control these environmental factors. When testing sensitive electronic components, remember that electrostatic discharge as low as 20 volts can cause damage.
Consider these critical environmental aspects when testing:
- Material conditioning time must extend beyond 24 hours if your samples show signs of moisture retention.
- Temperature fluctuations of even a few degrees can greatly alter your resistance measurements.
- Surface contamination from handling or exposure can skew results, so you'll need to maintain clean testing conditions.
Follow standard testing protocols like ASTM D257 or IEC61340-2-3 to guarantee your measurements remain consistent and comparable across different testing sessions.
Evaluating Electrostatic Decay Performance
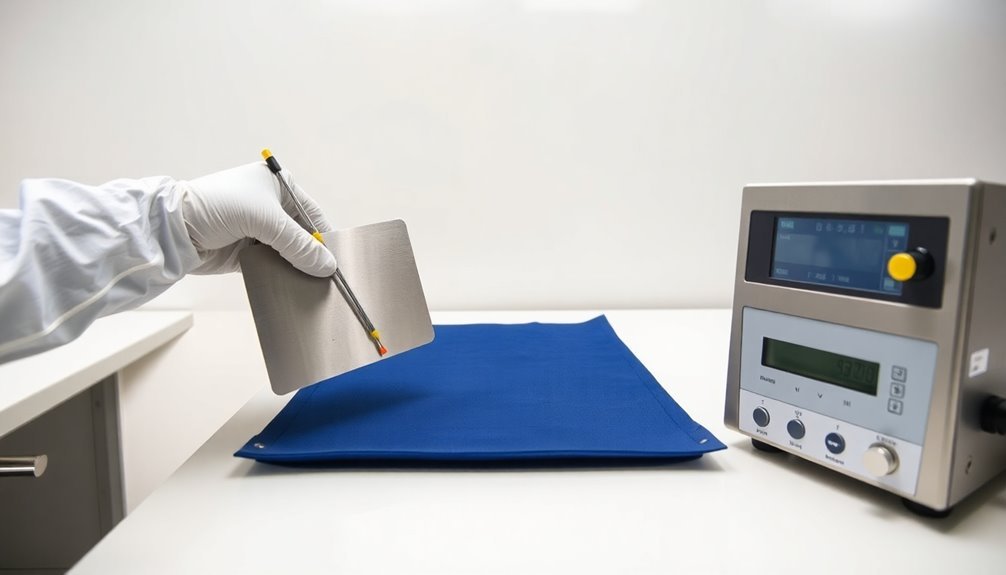
Several vital factors determine a material's ability to protect electronics from static damage, with electrostatic decay performance being the most important metric.
You'll need to evaluate this performance through three primary testing methods: surface resistance, volume resistance, and electrostatic decay testing.
When you're conducting these tests, you must maintain strict environmental conditions at 12%±3% relative humidity and 73°F±5°F.
You'll use specialized equipment like electrometers and Faraday cups to measure how quickly static charges dissipate. Your material needs to demonstrate it can discharge static within 2.0 seconds to meet compliance standards.
You'll find that various factors can affect your test results. Low humidity levels will greatly impact decay rates, while the material's thickness and composition play vital roles.
If your material contains conductive fibers or antistatic coatings, you'll typically see better performance. However, you'll need to account for potential degradation over time, as the effectiveness of antistatic properties can diminish.
To guarantee compliance, you must document all test results according to standards like ANSI/ESD STM11.31 and MIL-STD-3010C, Method 4046.
Static Shielding Test Procedures
To properly test static shielding bags, you'll need a calibrated electrometer and concentric ring fixture operating in a controlled environment of 12%±3%RH and 73±5°F.
You must apply a 1kV Human Body Model discharge to the bag's exterior while measuring energy penetration, which shouldn't exceed 20 nJ for the bag to pass certification.
Using a Faraday cup and capacitive sensor setup, you can track real-time shielding performance through peak current and energy measurements inside the bag.
Equipment Setup Requirements
Proper equipment setup forms the foundation of accurate static shielding tests. You'll need a static electricity generator or static gun as your primary charge source, along with a calibrated field meter to measure electrostatic fields accurately.
It's vital to establish a controlled testing environment where all equipment is properly grounded and free from external static interference.
Before conducting any tests, you must verify your workspace meets these critical requirements:
- All testing equipment must be calibrated before each session – this includes your static generator, field meter, and any auxiliary measurement devices you're using.
- Your testing area needs proper grounding systems installed, including anti-static flooring and grounded workbenches to prevent unwanted charge buildup.
- You'll need to maintain controlled environmental conditions, keeping the area free of dust, moisture, and other contaminants that could affect test results.
Don't forget to wear appropriate anti-static gear, including a ground strap and protective clothing.
Position your package testing platform at the recommended distance from the static generator, and verify all connections are secure before initiating any tests.
Remember to document your setup configuration for consistency in future testing sessions.
Energy Penetration Test Methods
Energy penetration testing stands as the cornerstone of evaluating static shielding effectiveness in protective packaging. You'll need to apply a 1kV Human Body Model discharge to the bag's exterior while it's clamped between discharge, capacitive sensor, and ground electrodes. This test measures the energy that penetrates through the material, helping you determine if it meets the protective requirements for sensitive electronics.
Test Parameter | Requirement | Standard Reference |
---|---|---|
Energy Threshold | <50 nanoJoules | ANSI/ESD S541 |
Surface Resistance | ≥1.0×10^4 to <1.0x10^11 Ohms | ANSI/ESD STM11.31 |
Test Environment | 12% and 50% RH | ANSI/ESD S541 |
You'll need to conduct these tests under controlled environmental conditions, typically at both 12% and 50% relative humidity levels. The results will tell you if your packaging meets the ANSI/ESD STM11.31 specifications. To guarantee compliance, you must test multiple samples and compare the energy penetration readings against the standard's threshold of 50 nanoJoules. This testing method is essential for the packaging industry, particularly when safeguarding completed PCBs and electronic components that are sensitive to static discharge.
Real-Time Shielding Measurements
Real-time shielding measurements consistently provide critical data about the effectiveness of static-protective packaging.
You'll need to conduct these tests under specific conditions of 12%±3% relative humidity at 73±5°F for 48 hours to guarantee accurate results. Using a concentric ring fixture, you can measure surface resistance both inside and outside static shielding bags, assuring they meet the standard of less than 1.0 x 10^11 Ω.
When performing electrostatic shielding tests, you'll apply a 1 kV discharge to the outer package while measuring the energy that penetrates through. The detected energy inside shouldn't exceed 20 nJ, confirming adequate protection for sensitive components.
To effectively implement these measurements, follow these key steps:
- Use specialized measurement systems like ElectroTech Systems' 4431 to obtain reliable shielding effectiveness data.
- Conduct volume resistance measurements according to ANSI/ESD STM11.12-2015 standards to assess charge dissipation.
- Verify that charge bleed-off doesn't occur when opening static control bags.
These measurements help you evaluate different bag materials and designs, guaranteeing your packaging meets required protection standards.
Remember to document all test results using the system's software for detailed reporting and quality control purposes.
Charge Retention Analysis
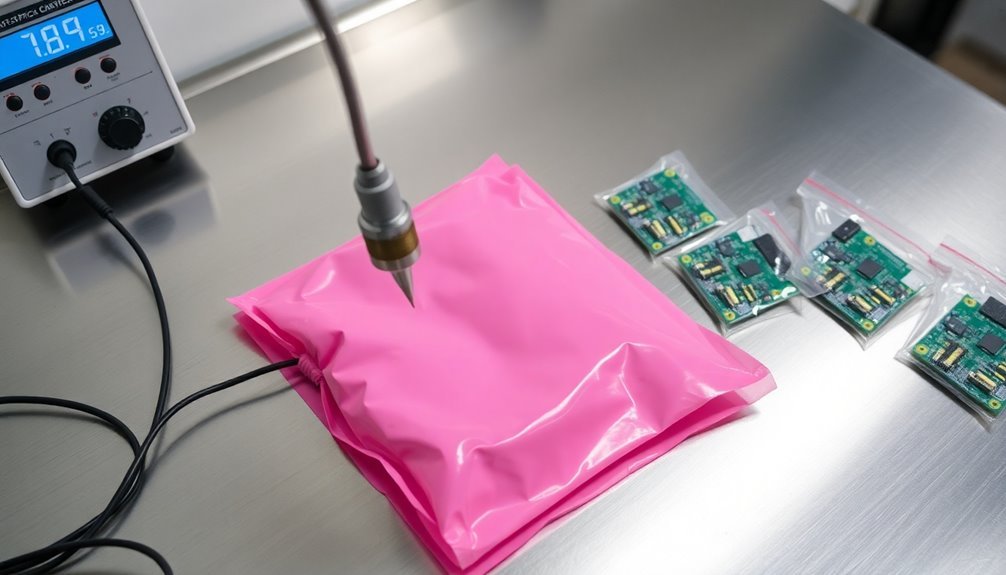
During the essential phase of static-free packaging testing, charge retention analysis serves as a cornerstone measurement that determines a material's ability to dissipate or retain static charges.
You'll need to verify your materials retain less than 1.0 nC of charge to meet industry standards, following the ESD Adv.11.2-1995 guidelines for Faraday Cup testing.
To conduct proper charge retention analysis, you'll use a Faraday Cup to measure retained charges and perform discharge testing to evaluate the material's response.
The testing process will help you classify materials into specific categories: conductive materials that rapidly dissipate charges (less than 10^4 Ω/sq), static dissipative materials with slower dissipation rates (between 10^4 and 10^11 Ω/sq), and insulative materials that hold charges longer (greater than 10^11 Ω/sq).
Environmental Impact Testing
Thorough environmental impact testing kicks off with a series of standardized procedures designed to evaluate your static-free packaging's resilience under various conditions.
You'll need to apply ASTM and ISTA protocols while conducting vibration, resonance, and drop testing to simulate real-world distribution scenarios. Using environmental chambers, you can expose your packaging to extreme temperatures and humidity levels that mirror subzero, tropical, and desert environments.
For extensive static-free packaging evaluation, you'll want to focus on these critical testing aspects:
- Run ESD STM11.31 assessments to measure energy penetration and verify your package's static shielding capabilities during environmental exposure.
- Conduct atmospheric conditioning tests for a minimum of 72 hours to guarantee sustained protection against varying environmental conditions.
- Perform gross leak detection and bubble testing to confirm package integrity remains intact after environmental stress.
Don't forget to incorporate sustainability considerations into your testing strategy.
You can reduce material usage while maintaining protection by applying Damage Boundary principles and selecting recyclable materials.
Remember to document all test results and package integrity checks after each environmental exposure to guarantee your static-free packaging meets required performance standards.
Material Compliance Standards
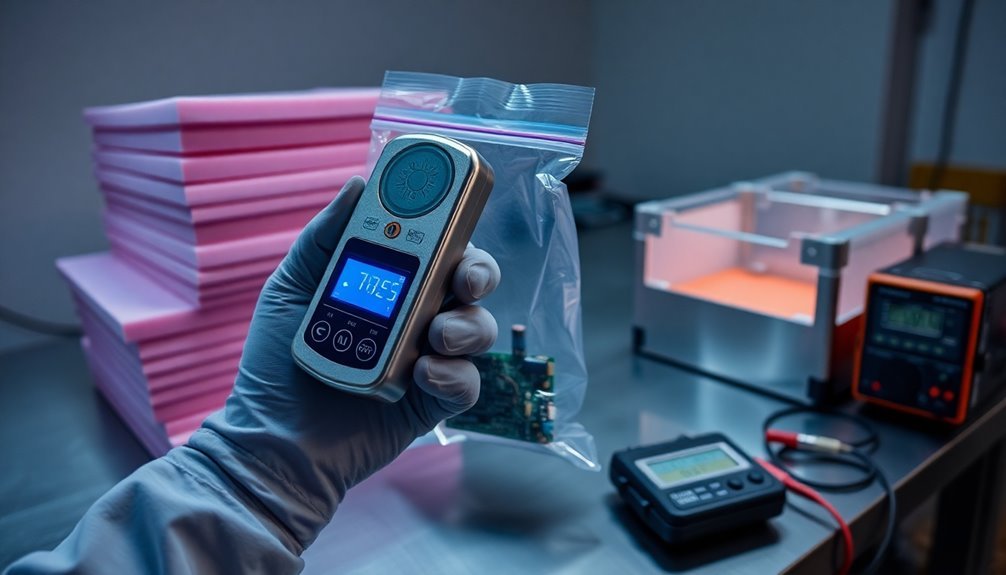
To meet industry requirements for static-free packaging, you'll need to comply with strict material standards governed by ANSI/ESD protocols. Your materials must fall into either conductive or dissipative categories, each with specific resistance requirements that you'll need to verify through testing.
For conductive materials, you'll want to guarantee resistance measurements fall below 1.0 x 10^4 ohms using ANSI/ESD STM11.11, STM11.12, or STM11.13 testing methods.
If you're working with dissipative materials, they'll need to measure between 1.0 x 10^4 and 1.0 x 10^11 ohms under the same testing protocols.
You'll find that packaging system requirements are defined by ANSI/ESD S541, which you must follow while considering your specific organization's needs.
When you're packaging items sensitive to less than 100 volts human body model, you'll need to take extra precautions.
Remember, you can't skip compliance verification – it's mandatory for all ESD control materials. Your packaging must demonstrate low charge generation properties and, when used outside EPAs, provide electrostatic discharge shielding.
Keep in mind that customer contract requirements might override standard guidelines.
Frequently Asked Questions
How Often Should Static-Free Packaging Materials Be Retested After Initial Certification?
You'll need to retest your static-free packaging every 6-12 months, especially if materials face extreme conditions. Don't forget to follow manufacturer's guidelines and schedule additional testing when environmental or process changes occur.
Can Static-Free Packaging Be Safely Reused Without Compromising Its Protective Properties?
You can safely reuse static-free packaging, but you'll need to regularly test it, inspect for damage, and follow manufacturer guidelines. Don't reuse if you notice deterioration, as this compromises its protective properties.
What Causes Static-Free Packaging to Fail Prematurely During Storage?
Your static-free packaging can fail prematurely if you store it in low humidity, expose it to extreme temperatures, or let it suffer physical damage. Poor climate control and material aging also reduce its effectiveness.
Do Temperature Fluctuations Affect the Performance of Static-Free Packaging Materials?
Yes, temperature changes will greatly impact your static-free packaging's performance. You'll notice decreased conductivity when temperatures fluctuate, especially in low humidity conditions, which can compromise the material's ability to protect against static.
How Do Different Cleaning Methods Impact the Effectiveness of Static-Free Packaging?
You'll find that harsh chemical cleaning can reduce your static-free packaging's effectiveness by altering surface resistance and leaving residues. It's best to use gentle, approved cleaners to maintain the material's static dissipative properties.
In Summary
You'll get the most reliable static-free packaging results by implementing multiple testing methods rather than relying on just one. Focus on surface resistance, volume resistance, and decay performance as your core tests. Remember to document your findings and maintain consistency in your testing procedures. Stay up-to-date with material compliance standards to guarantee your packaging meets current industry requirements.
Leave a Reply