Beyond standard wrist straps, you'll find seven powerful ESD protection methods to safeguard your sensitive electronics. Install conductive ESD flooring to create a complete ground path, and pair it with static dissipative work surfaces for thorough protection. Use protective ionization systems to neutralize static charges in your workspace, while ESD protective garments provide personal safety layers. Maintain proper environmental humidity control between 35-45% RH, implement anti-static storage solutions, and establish bonded ground points throughout your facility. These proven methods work together to form a robust ESD protection strategy, with each layer adding critical defense against costly static damage.
Conductive ESD Floor Installation

Four key phases make up a successful conductive ESD floor installation: subfloor preparation, material selection, grounding implementation, and proper maintenance.
You'll need to start with thorough subfloor preparation by removing all debris and contaminants. Fix any cracks or uneven areas to prevent future tile lifting and guarantee maximum conductivity. This clean, smooth foundation is essential for proper bonding and ESD control. Moisture testing and barrier installation may be necessary to protect the flooring integrity. A minimum surface profile CSP-2 is required to ensure proper adhesion of the coating system.
When selecting materials, you'll want to choose conductive tiles or mats that meet industry standards and are compatible with your grounding system. Your adhesive must also be conductive and appropriate for your chosen flooring materials.
For grounding, you'll connect components using conductive adhesives or copper strips. Install copper tape with conductive adhesive at a rate of one strip per 1,000 square feet, connecting to grounding points.
You can also use metal floor joints, equipment bases, and steel columns as grounding points if they pass electrical testing.
Proper maintenance is crucial to ensure the longevity and effectiveness of your ESD flooring. Regular cleaning and inspections will help identify any issues early and maintain the integrity of the conductive properties.
Protective Ionization Systems
Most protective ionization systems rely on a balanced stream of positive and negative ions to neutralize static charges on insulators and isolated conductors. You'll find these systems using either corona or alpha methods to produce ions, while air flow helps distribute them effectively across your work area. The neutralization process happens quickly, often taking just seconds to eliminate static electricity. Regular maintenance intervals can be extended using auto-balancing feedback technology, which helps optimize performance over time.
You'll need ionizers in environments where traditional grounding methods aren't sufficient or possible, such as electronic assembly, medical device manufacturing, and cleanrooms. They're particularly essential in PCB manufacturing and semiconductor industries, where they help maintain strict contamination control standards while protecting against ESD damage. Many facilities utilize overhead ionizers positioned strategically above workbenches for comprehensive coverage.
When you're selecting an ionizer, you'll need to evaluate whether AC or DC ionization better suits your needs. AC ionization works best for automated assembly lines, while you might use either type for handheld applications.
For the most effective static control, you should focus on localized workstation ionization rather than room-wide solutions. Don't forget that regular testing and calibration are vital to maintain peak performance.
These systems will help you increase yields, enhance production efficiency, and prevent contamination in your static-sensitive operations.
Static Dissipative Work Surfaces
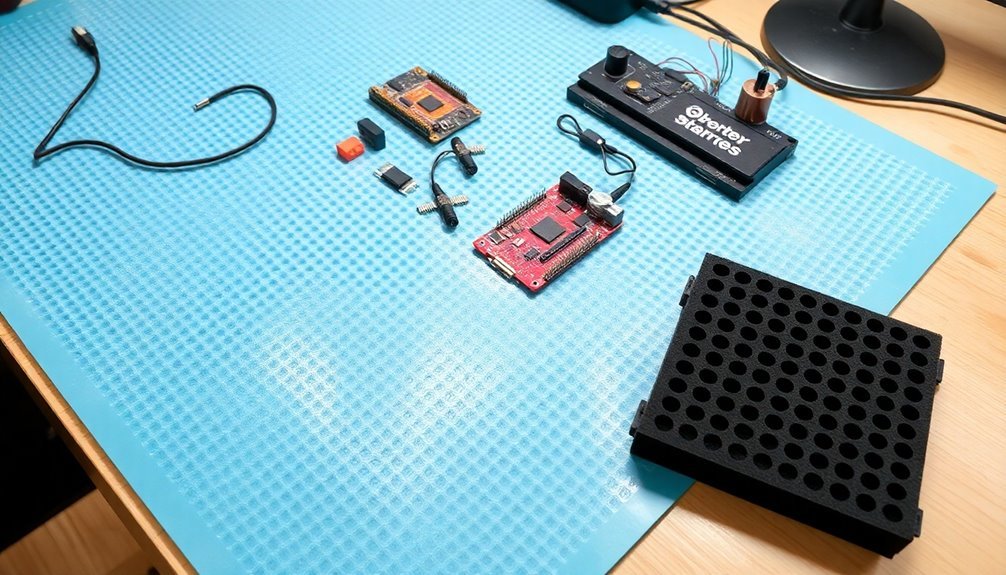
Static dissipative work surfaces serve as your primary defense against unwanted ESD events in sensitive electronic environments.
These surfaces, designed to dissipate static charges in a controlled manner, must maintain a surface resistance between 1×10^5 and 1×10^11 Ω/square to meet ESD safety standards.
You'll find these surfaces integrated into complete ESD protective workstations, where they work alongside other grounding devices. Different options like 2-layer rubber and 3-layer vinyl materials offer versatile solutions for various applications.
They're manufactured using static dissipative polymers or surfactant-based ESD additives, providing both durability and reliable charge dissipation. The addition of conductive carbon black creates networks within the polymers to enhance conductivity.
To comply with ANSI/ESD S20.20 standards, they offer a controlled path to ground while protecting your sensitive components.
You'll need to maintain these surfaces properly to guarantee continued effectiveness.
Use only approved ESD mat cleaners that won't leave insulative residues, and test the surface regularly to confirm it maintains a resistance of less than 1×10^9 ohms after cleaning.
Your cleaning routine should include regular verification using continuous monitors or periodic testing to guarantee compliance with IEC 61340-5-1 and related standards.
This maintenance isn't just good practice—it's essential for maintaining the integrity of your ESD protection system.
ESD Protective Garments
You'll achieve ideal ESD protection by strategically layering your protective garments, starting with ESD-safe undergarments and building up to outer layers like lab coats or high-visibility vests.
Modern smart fabric technology has revolutionized ESD protective clothing through the integration of carbon-infused fibers and static dissipative yarns that create an effective Faraday Cage around your body. Regular performance testing is recommended since ESD properties can degrade over time due to wear and washing. For optimal effectiveness, conductive fibers must be positioned on the outer layer of garments with a specific mesh pattern.
These advanced materials work together with proper grounding systems to give you thorough protection against potentially damaging static discharge in sensitive environments.
Layering For Maximum Protection
Proper layering techniques with ESD protective garments form your first line of defense against static damage in sensitive environments.
You'll need to start with a Class A groundable smock as your primary protective layer, guaranteeing it's correctly fastened to prevent exposure of underlying clothing. This creates a vital Faraday Cage effect that contains any static charges from your regular clothes.
To maximize your protection, you'll want to properly ground your ESD garment using either a wrist strap, conductive wrist cuff, or dedicated ground cord.
Don't forget that your smock's effectiveness depends on maintaining continuous panel-to-panel conductivity, so you should test regularly using a resistance test kit.
When layering, verify there aren't any gaps or exposed areas larger than 20mm x 20mm that could compromise the protective barrier.
You'll achieve superior protection by combining Category 2 or 3 garments with proper grounding methods.
Remember that you can't modify your ESD garments, as alterations will compromise their protective properties.
Regular maintenance, including appropriate cleaning according to manufacturer specifications, will help maintain your layered protection's effectiveness over time.
Smart Fabric Technology Advancements
Recent breakthroughs in smart fabric technology have revolutionized ESD protective garments beyond traditional layering methods. Graphene nanotubes and conductive polymers are now being integrated into textiles, creating highly effective anti-static protection while maintaining comfort and durability. You'll find these advanced materials particularly effective when embedded in knitted structures, which naturally excel at charge dissipation.
Technology | Benefit | Application |
---|---|---|
Graphene-infused fabrics | High conductivity with comfort | General workwear |
Smart sensors | Real-time static monitoring | High-risk environments |
Nanotube-based textiles | Superior durability | Heavy-duty protection |
Smart garments now offer real-time monitoring capabilities, alerting you to potential static hazards before they become dangerous. These advanced fabrics pair with sensors to continuously track static build-up and environmental conditions, enhancing workplace safety protocols. You'll benefit from the integration of PVC, PI, and PMMA encapsulation, which guarantees your protective gear remains effective even in challenging conditions. As nanotechnology continues to advance, you can expect even more improvements in anti-static fabric capabilities, though standardization and sustainability remain key challenges in the industry.
Environmental Humidity Control
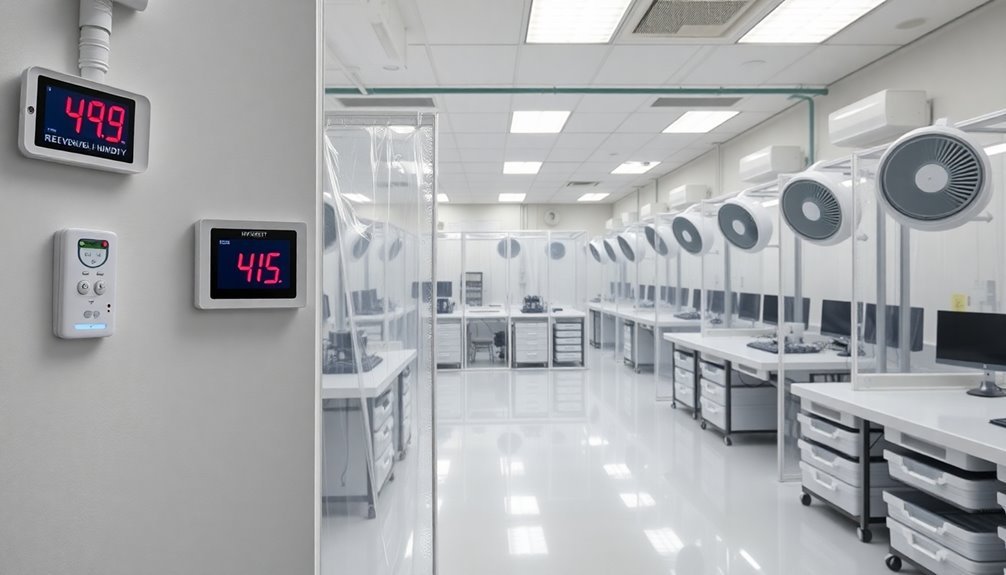
To protect your sensitive electronics from ESD damage, you'll need to maintain relative humidity levels between 35% and 45% using specialized humidifiers or dehumidifiers.
In dry climates, you should implement additional humidification measures and run regular checks to prevent static buildup from low moisture conditions.
Your facility must incorporate humidity sensors and monitoring systems to track moisture levels continuously and guarantee ideal ESD protection across all work areas.
Optimal Humidity Level Settings
Maintaining precise humidity levels plays an essential role in ESD protection within electronics manufacturing environments. You'll want to keep your facility's relative humidity between 30% and 70% RH, with the ideal range being 40% to 60% RH. This range effectively reduces ESD risks while avoiding moisture-related problems like corrosion.
When your humidity drops below 30% RH, you'll notice a significant increase in static charge buildup and ESD events. This is particularly problematic during dry seasons or in facilities with aggressive heating systems.
While you might be tempted to raise humidity levels higher for better charge dissipation, don't exceed 70% RH, as this can damage sensitive components and lead to PWB delamination.
You shouldn't rely solely on humidity control for ESD protection. Instead, use it as part of your thorough ESD control strategy. If you can't maintain ideal humidity levels consistently, consider using ionized air systems as a supplementary measure.
Remember to factor in your specific manufacturing processes – some operations, like wafer fabrication, may require lower humidity settings despite the increased ESD risk.
Dry Climate Control Measures
Controlling humidity levels in dry climates requires a strategic approach to ESD protection. You'll need to maintain humidity levels between 35-45% to effectively dissipate static charges and protect your electronic components. Install humidifiers in your workspace and monitor humidity levels regularly to guarantee they stay within this ideal range.
In dry environments, you'll want to implement multiple layers of protection. Start by setting up humidity-controlled areas where you handle sensitive electronics. Use ionizers to neutralize static charges in the air, and install conductive flooring and benchtop mats to create a properly grounded environment.
Don't forget to equip your team with ESD smocks, which are particularly important in dry climates where static charges accumulate more easily on clothing.
You should also regularly test your ESD equipment and materials to confirm they're functioning effectively in dry conditions. Consider using dehumidifiers when necessary to prevent excessive moisture that could lead to corrosion.
Remember to restrict access to your ESD-protected areas to minimize the introduction of static charges from external sources. These measures, combined with proper humidity control, will greatly reduce your risk of ESD-related damage.
Humidity Monitoring Equipment
Effective humidity control starts with reliable monitoring equipment. You'll find various sensor types available for ESD protection, each offering distinct advantages for your specific needs.
Capacitive sensors provide excellent linearity across the full humidity range, while resistive sensors offer a cost-effective solution for basic monitoring requirements. For precise control in ESD-sensitive environments, you'll want to focus on sensors that deliver ±2% accuracy or better.
Modern humidity monitoring solutions from manufacturers like Rotronic and Atlas Scientific integrate seamlessly with IoT systems, allowing you to track and adjust humidity levels in real-time. These systems can alert you when conditions fall outside acceptable ranges for ESD protection.
- Capacitive sensors provide continuous monitoring across 0-100% RH, ideal for maintaining ideal ESD protection levels
- Advanced IoT-enabled systems offer remote monitoring capabilities and automated alerts
- Industrial-grade sensors from Rotronic deliver the accuracy needed for critical ESD-protected areas
- Andivi's DIP switch functionality allows for quick range adjustments without recalibration
When selecting humidity monitoring equipment, consider response time, accuracy requirements, and integration capabilities with your existing ESD protection infrastructure.
The right monitoring solution guarantees consistent environmental conditions necessary for effective ESD control.
Anti-Static Storage Solutions
Protecting sensitive electronic components from electrostatic discharge requires proper anti-static storage solutions. You'll need storage containers made from permanent antistatic conductive materials, typically polypropylene with a surface resistivity of 10^3-10^9 ohms. These containers provide reliable protection for your sensitive electronics and PCBs during storage and transport.
When selecting storage solutions, you'll find various options including ESD storage bins, conductive containers, and modular systems. Conductive containers, often black due to their carbon content, can be grounded to prevent ESD events and withstand temperatures from -20°C to +100°C. You can stack them efficiently and use dividers for better organization.
For a thorough approach, consider implementing modular ESD storage systems that comply with international standards like EN 61340-5-1. These systems create protected areas where all surfaces maintain the same electrical potential.
You'll find them particularly useful in workshops, laboratories, and cleanrooms. If you're working in specialized industries like medical or pyrotechnic manufacturing, look for containers made from anti-static HDPE that minimize particle slough and meet industry-specific requirements.
Bonded Ground Points
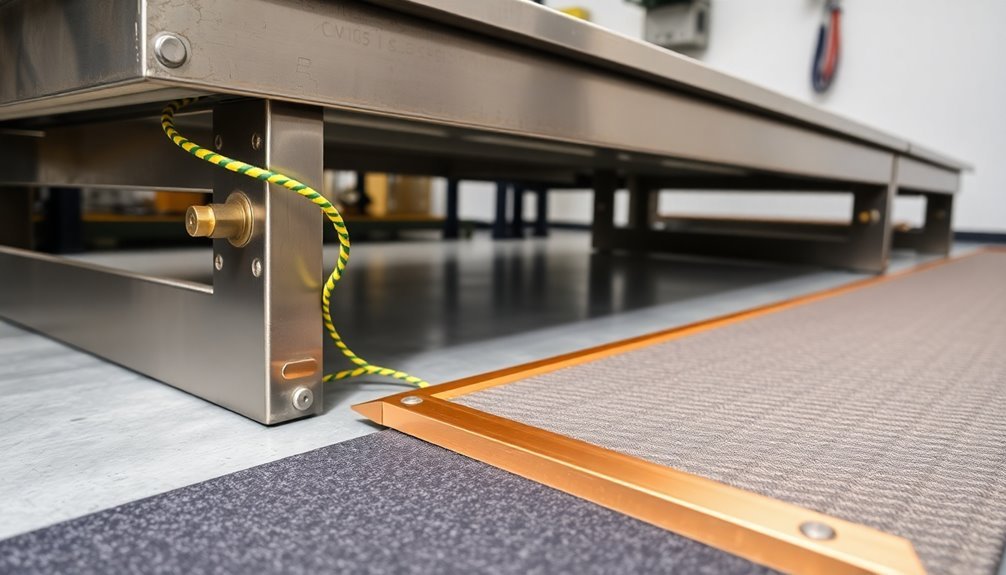
Through proper implementation of bonded ground points, you'll establish an essential foundation for ESD protection in your workspace. These connections guarantee all conductive components maintain the same electrical potential, preventing damaging static discharge between surfaces and equipment.
You'll need to install copper grounding straps for every 1,000 square feet of ESD flooring, with at least one strap per room.
- Connect grounding straps to AC electrical outlets, bare metal I-beams, or aluminum studs
- Test continuity to confirm compliant electrical ground connections (less than 1.0 ohm impedance)
- Use copper bus bars as dedicated common point connections for ESD flooring
- Verify all bonding points have less than 1.0 x 10E9 ohms impedance
When setting up your bonded ground points, you'll need to focus on equipotential bonding, which brings all ESD protective materials and personnel to the same electrical potential.
Your grounding system should include appropriate conductors, ESD protective worksurfaces, and conductive tools. Don't forget to ground hand tools through the ESD protective worksurface and the grounded person using them.
Regular testing and maintenance of these connections will help maintain the integrity of your ESD protection system.
Frequently Asked Questions
Can ESD Protection Methods Interfere With Wireless Communication Devices in the Workspace?
Yes, your ESD protection methods can interfere with wireless devices. You'll find that metal components, grounding systems, and conductive materials can create electromagnetic interference or physically block wireless signals in your workspace.
How Often Should Ionizer Maintenance Be Performed to Ensure Optimal Performance?
You'll need to maintain your ionizer daily for basic checks, perform monthly calibrations, conduct quarterly deep cleaning, and complete yearly overhauls. Don't skip these intervals to keep your ionizer working at peak performance.
Do ESD Protection Measures Remain Effective During Power Outages?
Yes, most ESD protection measures stay effective during power outages. Your wrist straps, mats, and dissipative surfaces don't need electricity to work. However, you'll need backup power for ionizers to maintain functionality.
What Temperature Conditions Affect the Performance of ESD Protective Materials?
You'll notice temperature impacts on ESD materials between -75°C to 125°C. Your protective materials' performance decreases at higher temperatures, reducing breakdown voltage levels. Heat and cold both raise your risk of ESD incidents.
Are There Specific ESD Requirements for Handling Quantum Computing Components?
You'll need enhanced grounding measures, including conductive gloves and full-body suits. Use ESD-safe tools, maintain 35-45% humidity, and work in controlled areas with ionizers for quantum computing components' protection.
In Summary
You'll find these seven ESD protection methods work together to create an all-encompassing static defense system for your facility. Don't rely solely on wrist straps when you can implement multiple layers of protection. By combining proper flooring, ionization, work surfaces, clothing, humidity control, storage solutions, and grounding points, you're safeguarding your sensitive electronics and critical components from costly ESD damage.
Leave a Reply