You need anti-static protection in today's workplace because static electricity poses serious risks to both you and your equipment. Modern work environments are filled with sensitive electronics and flammable materials that can be damaged or ignited by static discharge. Even routine actions like walking on carpets or sliding in chairs can generate harmful static charges, especially in low-humidity conditions. Static shocks aren't just uncomfortable – they can cause accidents, damage expensive equipment, and lead to workplace injuries. With annual losses from static damage reaching billions of dollars, proper anti-static measures have become essential for your safety and productivity. Understanding the full scope of protection can help you avoid costly mistakes.
Understanding Static Electricity Risks
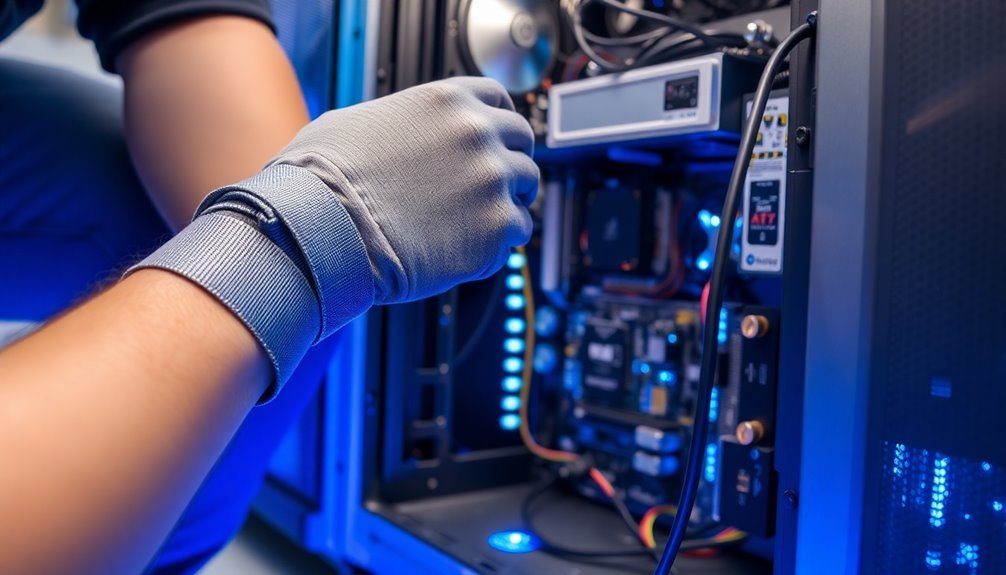
In industrial settings, static electricity poses significant risks that workers can't afford to ignore. When static charges build up in your workplace, they can create dangerous conditions that threaten both your safety and the integrity of your operations.
You're facing multiple hazards, from the risk of fires and explosions when static sparks ignite flammable materials to potential damage to sensitive electronic equipment. Many common workplace practices still rely on rule of thumb rather than precise scientific understanding.
You'll encounter static electricity most frequently in environments with low humidity, where friction between materials is common. If you're handling non-conductive materials like plastics or working with flammable liquids, you're at an increased risk. Using an ESD safe chair can help discharge static electricity safely while working.
The dangers become even more serious when you consider that static discharge can cause sudden shocks, which might lead to accidents or pose serious health risks, especially if you have heart conditions.
Static electricity doesn't just affect your safety – it can also impact your work quality. When materials become electrostatically charged, they may stick together or attract dust, causing production issues and compromising product quality.
Understanding these risks is essential because they can occur in any industrial setting where you're working with equipment, materials, or processes that generate static charges.
Modern Workplace Static Hazards
You'll find modern workplaces packed with sensitive electronics that create multiple ESD risks, from smartphones to industrial control systems.
Seemingly harmless actions like sliding across office chairs or handling plastic packaging can generate damaging static charges that silently degrade electronic components.
The rise of automated manufacturing and robotic systems has introduced new static electricity hazards, as moving parts and conveyor belts constantly generate electrostatic charges that require proper grounding and monitoring. Static electricity can also accumulate during routine tasks like pouring and pumping liquids. Maintaining workplace humidity levels at minimum 60 percent helps reduce static electricity buildup and protects equipment.
Electronic Device Density Risks
Modern workplaces are increasingly packed with sensitive electronic equipment, making static electricity a more serious threat than ever before. Your everyday actions, like walking across carpeted floors or handling non-conductive objects, can generate harmful static charges. Regular training sessions help workers stay updated on the latest ESD safety protocols.
When you're wearing synthetic clothing or shoes, you're particularly vulnerable to building up these charges, which can discharge suddenly onto sensitive equipment. The risk becomes even more significant in workstations that aren't properly grounded or when you're using non-conductive tools and containers. Static spark incidents have caused fires in facilities using solvent materials.
Your electronic devices, especially integrated circuits and PCBs, are constantly at risk of damage from these electrostatic discharges.
- Your synthetic clothing and shoes can generate thousands of volts of static electricity simply through normal movement
- Ungrounded equipment and non-ESD materials in your workspace create additional discharge risks
- Electronic components are most vulnerable when you're handling them outside their protective packaging
To protect yourself and sensitive equipment, you'll need proper grounding measures and static-dissipative materials. This includes using anti-static mats, wearing conductive footwear, and ensuring your workstation has appropriate grounding connections.
Hidden ESD Damage Sources
Static hazards lurk in unexpected places throughout your workplace, often striking sensitive electronics without warning. You'll find hidden ESD risks in everyday items like layered clothing that generates friction, non-ESD safe cleaning supplies, and even the air circulation systems in your facility. When humidity levels drop, these dangers become more pronounced as dry conditions prevent static charges from dissipating naturally. Poor ESD practices can result in product longevity issues that impact overall business performance. According to industry research, one-third of PCB failures are directly linked to electrostatic discharge events.
Hidden Source | Risk Factor | Prevention Method |
---|---|---|
Synthetic Clothing | High friction between layers | Wear ESD-safe garments |
Cleaning Tools | Non-conductive materials | Use ESD-safe cleaning equipment |
HVAC Systems | Air movement disruption | Monitor humidity levels |
Workstation Materials | Insulating surfaces | Install grounded mats |
Packaging Materials | Non-dissipative wrapping | Choose ESD-safe packaging |
You're particularly vulnerable to hidden ESD damage when working with multiple grounding points that create potential differences, or when using non-ESD safe tools that appear harmless. Even plastic furniture components and standard office supplies can silently build up charges that may discharge into sensitive components. To protect against these concealed threats, you'll need extensive ESD protection that addresses both obvious and subtle static generators in your workspace.
Automation Creates Static Hazards
Every automated system in today's manufacturing environment introduces new static electricity risks. As robotic arms move swiftly through assembly processes and high-speed equipment operates continuously, they generate static charges through friction and movement.
You'll find that automated systems, while boosting productivity, create unique electrostatic challenges that require careful management.
- Robotic arms and automated equipment generate constant static charges during their repetitive movements
- High-speed assembly lines increase friction and static buildup across multiple contact points
- Non-conductive tools and containers in automated processes accumulate charges that can discharge unexpectedly
You're facing greater risks because modern automation often involves handling static-sensitive electronic components while operating in environments that naturally generate electrostatic charges.
The combination of rapid equipment movement, sensitive electronics, and continuous operation means you'll need extensive static protection. This includes proper grounding techniques, ESD-safe furniture, and integrated safety systems.
Advanced sensing technologies and automated safety protocols can help you monitor and manage static risks in real-time. By implementing proper static control measures and maintaining regular safety audits, you'll protect both workers and sensitive equipment from harmful electrostatic discharge events.
Essential Anti-Static Safety Equipment
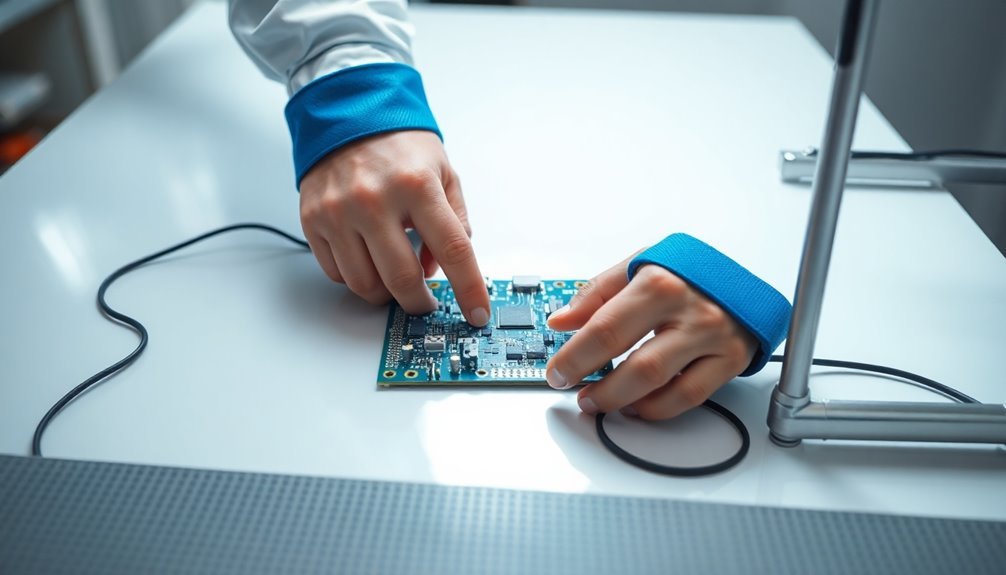
The safety and reliability of anti-static equipment stands out among the most vital aspects of workplace protection.
You'll need multiple layers of protection to effectively control static electricity in your workspace, starting with proper floor coverings and anti-static mats that dissipate charges and prevent buildup.
Your primary personal protection should include properly fitted wrist straps and grounding equipment, which create an uninterrupted path to ground.
These devices are essential when you're handling sensitive electronics, as they continuously dissipate any static charges that could damage components or create safety hazards.
You'll also need appropriate protective clothing, including static-dissipative gloves and garments made from specialized materials like polyester or nylon.
These items protect both you and the sensitive equipment you're working with from potentially harmful static discharge.
Don't forget to incorporate ionizers and air purifiers into your workspace.
They'll help create a balanced environment by neutralizing static charges in the air.
When you combine these with other anti-static equipment, you'll establish an extensive protection system that keeps both workers and sensitive equipment safe from electrostatic discharge events.
The Cost of Static Damage
The financial toll of electrostatic discharge (ESD) on the electronics industry is staggering, with annual losses ranging from $500 million to $5 billion.
You'll find that ESD accounts for a quarter of all electronic part failures, leading to both immediate breakdowns and hidden damage that surfaces later.
Your company's bottom line takes a particularly hard hit when ESD-damaged products reach customers, as warranty claims and returns typically cost more than in-house repairs.
Financial Impact of ESD
Billions of dollars are lost annually across industries due to electrostatic discharge damage, making ESD protection a critical financial consideration for manufacturers.
If you're managing a manufacturing facility, you'll find that investing in proper ESD protection measures can greatly reduce operational costs and boost your bottom line. The long-term financial benefits of implementing effective ESD prevention strategies far outweigh the initial investment costs.
In high-tech manufacturing environments, particularly in semiconductor and electronics production, you're facing substantial risks of financial losses without proper ESD protection.
Here's what you're looking at regarding financial impact:
- Immediate costs from damaged components and products that must be scrapped or repaired
- Hidden costs from latent defects that surface after products have been shipped, leading to warranty claims and reputation damage
- Operational losses from reduced productivity and equipment downtime
You'll find that consistent investment in ESD protection measures yields measurable returns through reduced product failures, fewer warranty claims, and improved manufacturing efficiency.
Regular assessment and updating of your ESD protection strategies guarantee continued cost-effectiveness and help maintain your competitive edge in the market.
Yearly Losses From Static
Static electricity's destructive power costs the electronics industry anywhere from half a billion to $5 billion annually, with companies experiencing losses ranging from 8-33% of their revenue.
You'll find these losses are particularly severe across different sectors of the industry, with component manufacturers facing up to 97% losses, while subcontractors and end-users can see losses as high as 70%.
When you look at the real cost of ESD damage, you'll discover it extends far beyond just replacing damaged parts.
You're also paying for repair work, shipping, labor, and overhead expenses.
What's even more concerning is that you mightn't immediately detect the damage – these latent defects can surface later, leading to costly field failures and customer returns that often exceed your in-house repair expenses.
You're facing an increasingly critical challenge as modern devices become smaller and faster, making them more susceptible to ESD damage.
While you can't eliminate all risks, implementing proper ESD control programs can give you a significant return on investment – up to 10:1 – by reducing both immediate failures and long-term defects that might otherwise go unidentified.
Protecting Electronics in Manufacturing
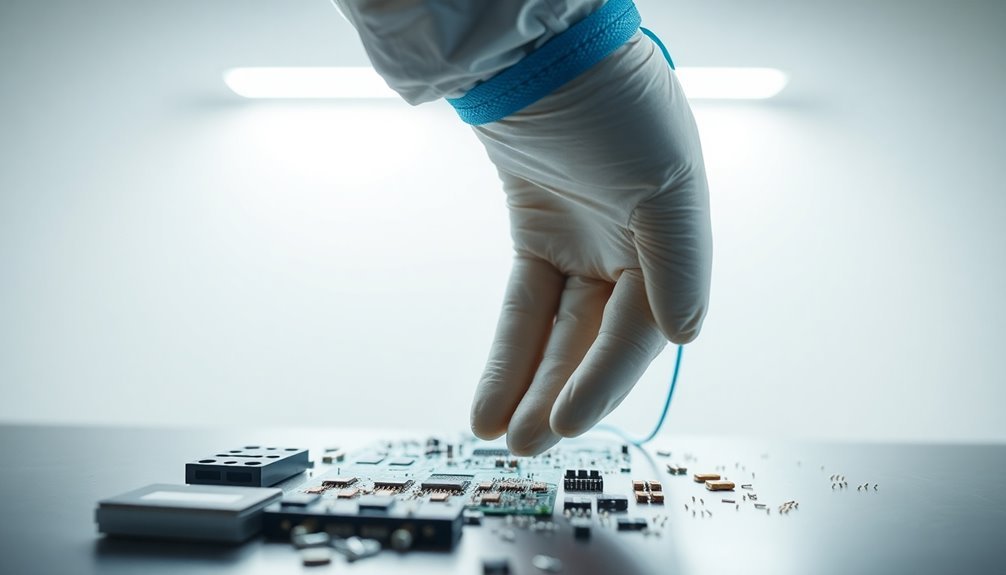
When handling sensitive electronic components in manufacturing environments, proper ESD protection isn't just important – it's essential for survival in today's competitive market.
You'll need to implement extensive ESD protection measures throughout your manufacturing facility to safeguard electronic components and prevent costly damage. With 25% of all electronic damage attributed to ESD, you can't afford to overlook proper protection protocols.
Your manufacturing facility requires multiple layers of protection, from properly grounded workstations to ESD-safe storage solutions.
You'll need to establish clearly marked Electrostatic Discharge Protected Areas (EPAs) and verify they're equipped with the right tools and materials to prevent static build-up.
- Your assembly lines must use ESD-safe bins and containers to protect components during handling
- Your packaging areas require anti-static materials for safe storage and shipping
- Your workstations need ESD-controlled mats and grounding systems for static dissipation
Remember to maintain proper humidity levels and conduct regular ESD testing to verify your protective measures remain effective.
You'll also need to invest in extensive training for your employees, teaching them proper handling techniques and the importance of following ESD protocols consistently.
Anti-Static Clothing Requirements
When you're working around sensitive electronics or in explosive environments, you'll need anti-static clothing that meets specific safety standards, including a surface resistance below 2.5 x 10^9 ohms and conductive fibers woven throughout the fabric.
Your protective gear must feature dust-proof performance, limited metal accessories, and properly maintained seams to guarantee consistent static dissipation.
Regular maintenance and proper earthing of your anti-static garments are essential to maintain their protective properties and meet daily safety requirements in high-risk environments.
Essential Protective Features
Throughout industrial environments, protecting workers from electrostatic discharge (ESD) requires specific clothing made from specialized materials. You'll find that synthetic, dissipative fabrics enhanced with graphene nanotubes provide stable protection while maintaining conductivity for proper grounding. These materials form the foundation of a thorough ESD protection strategy that's vital in sensitive work areas.
Your ESD-safe garments must include specific features to guarantee complete protection:
- Conductive materials that create an uninterrupted path to ground, including treated fabrics and specialized coatings
- Durable construction that withstands repeated washing while maintaining anti-static properties
- Versatile designs that accommodate various work environments, from cleanrooms to chemical processing areas
You'll need to complement your anti-static clothing with additional protective gear. This includes ESD-safe wrist straps, specialized footwear, and appropriate accessories like heel grounders or hairnets depending on your work environment.
Each component plays a significant role in maintaining a complete grounding chain. Remember, your ESD protection is only as strong as its weakest link, so you must verify all elements work together effectively through regular testing and maintenance.
Meeting Safety Standards Daily
Consistently meeting safety standards for anti-static protection requires strict adherence to multiple international regulations.
You'll need to guarantee your protective gear complies with key standards like EN 1149-5 for electrostatic protection and EN ISO 14116 for flame propagation safety. These regulations aren't just suggestions – they're essential benchmarks that protect you and your workplace.
You must wear your anti-static clothing properly over your regular clothes and keep it on throughout your work activities.
Don't remove or open these garments while you're in hazardous areas, as this compromises their effectiveness. If you're working in electronics manufacturing, pharmaceuticals, or petrochemical industries, you'll need to pair your anti-static clothing with electroconductive shoes for proper grounding.
To maintain your gear's protective properties, you'll need to follow specific care instructions.
You can use aluminum foil or antistatic spray when washing your work clothes to preserve their anti-static qualities.
Grounding Methods and Best Practices
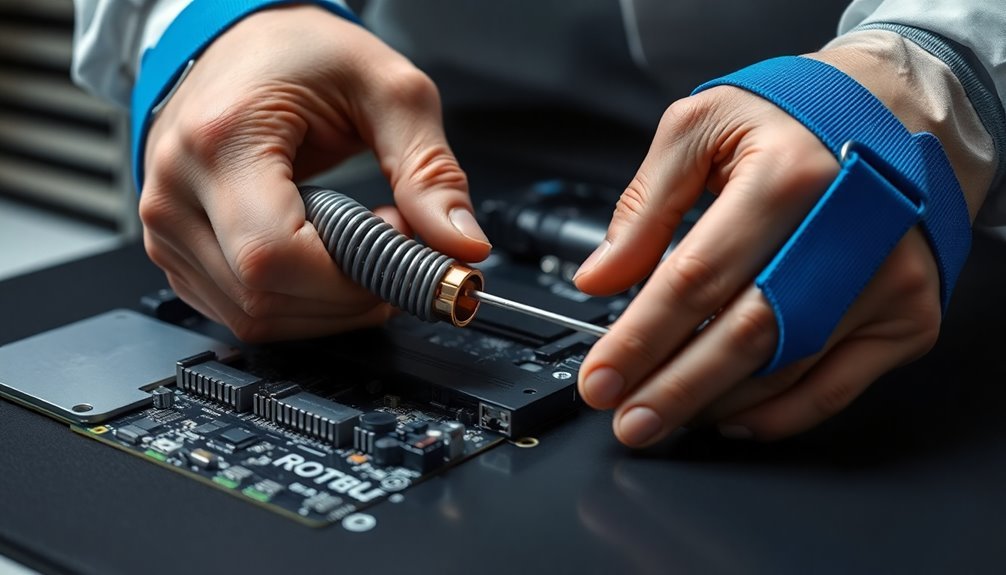
In the domain of workplace safety, proper grounding methods form the foundation of effective anti-static protection.
You'll need to maintain an uninterrupted grounding chain through anti-static clothing, conductive materials, and properly equipped workstations. This includes using specialized footwear, wrist straps, and grounding mats that work together to dissipate static electricity effectively.
To guarantee your safety and protect sensitive equipment, you'll want to implement these essential grounding practices:
- Use grounding mats at your workstation and wear anti-static clothing, including gloves enhanced with graphene nanotubes for superior conductivity.
- Connect yourself to the ground through proper footwear and wrist straps that meet industry standards.
- Participate in regular ESD training to understand and maintain proper grounding techniques.
You can't overlook the importance of consistent training and awareness programs.
Whether you're a manager, operator, or temporary worker, you need to understand how to use ESD protective equipment correctly.
The combination of proper grounding techniques, quality materials like graphene nanotubes, and ongoing education guarantees you're protected against potentially harmful static discharge in your workplace.
Dangers in Flammable Environments
Static electricity poses a lethal threat in environments where flammable materials are present. When you're working in areas containing flammable gases, vapors, or combustible dust, a single spark from static discharge can trigger devastating explosions and fires.
These risks are particularly severe in ATEX-sensitive environments, where even minor static buildup can have catastrophic consequences. You'll find these hazards are intensified in dry conditions, as moisture typically helps dissipate static charges naturally.
During routine operations like material handling, unwinding materials, or filling containers, static charges can accumulate rapidly. OSHA Standard 1910.106(e) specifically addresses these risks, emphasizing the critical need to eliminate ignition sources, including static electricity.
If you're handling flammable substances, you must understand that static-related incidents can cause significant production losses and equipment damage. In fact, 33% of production losses in electronics manufacturing stem from static-related failures.
That's why you need to follow strict safety protocols, including proper grounding procedures and using appropriate anti-static PPE. Remember, in flammable environments, static electricity isn't just an inconvenience – it's a serious safety hazard that requires constant vigilance and proper protection.
Worker Safety and Comfort
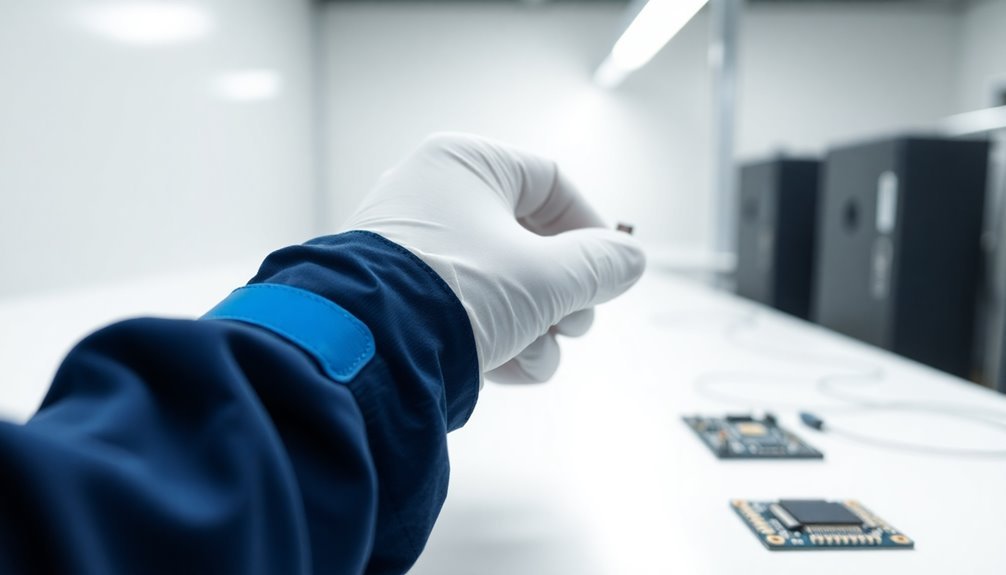
While guaranteeing protection against static electricity is essential, worker comfort remains equally important for maintaining safety and productivity.
Modern anti-static PPE incorporates advanced materials like graphene nanotubes that provide both effective static dissipation and enhanced comfort. You'll find that these innovative textiles don't compromise on protection while allowing proper ventilation and movement throughout your workday.
Your safety equipment must comply with specific standards like EN 1149-5 and EN ISO 13688 to guarantee reliable protection. When you're wearing certified anti-static gear, you're protected from electric shocks that could cause injuries or trigger dangerous ignition in ATEX-sensitive environments.
The right combination of conductive clothes, gloves, and boots creates an uninterrupted grounding chain that effectively dissipates static electricity.
- Anti-static safety shoes with resistance between 100 kiloohms and 1 gigaohm keep you grounded while remaining comfortable for extended wear
- Graphene nanotube-enhanced textiles provide permanent ESD protection while maintaining breathability
- Proper ventilation and humidity control in your workspace complement your PPE's effectiveness
This extensive approach to anti-static protection doesn't just keep you safe – it guarantees you can work efficiently and comfortably throughout your shift.
Static Control Success Stories
A remarkable transformation has occurred in electronics manufacturing since the widespread adoption of extensive static control measures. You'll find compelling evidence in the numbers: up to 33% of production losses were previously attributed to static-related failures, but companies have drastically reduced these losses through proper static control implementation.
When you look at successful manufacturing facilities today, you'll see workers equipped with ESD protective gloves, anti-static clothing, and essential equipment like wrist straps and ionizers. These measures aren't just protecting components – they're safeguarding your bottom line.
Companies that have invested in thorough static control programs have seen significant reductions in product failures and workplace incidents.
You can't ignore the economic impact of proper static protection. While static-related damage costs businesses billions annually, you'll find that facilities using appropriate anti-static measures experience fewer setbacks, improved product reliability, and reduced workplace hazards.
The investment in static control products pays off through enhanced productivity, fewer component failures, and decreased liability risks. When you implement these measures effectively, you're not just protecting workers – you're ensuring the success of your entire manufacturing operation.
Industry Compliance and Standards
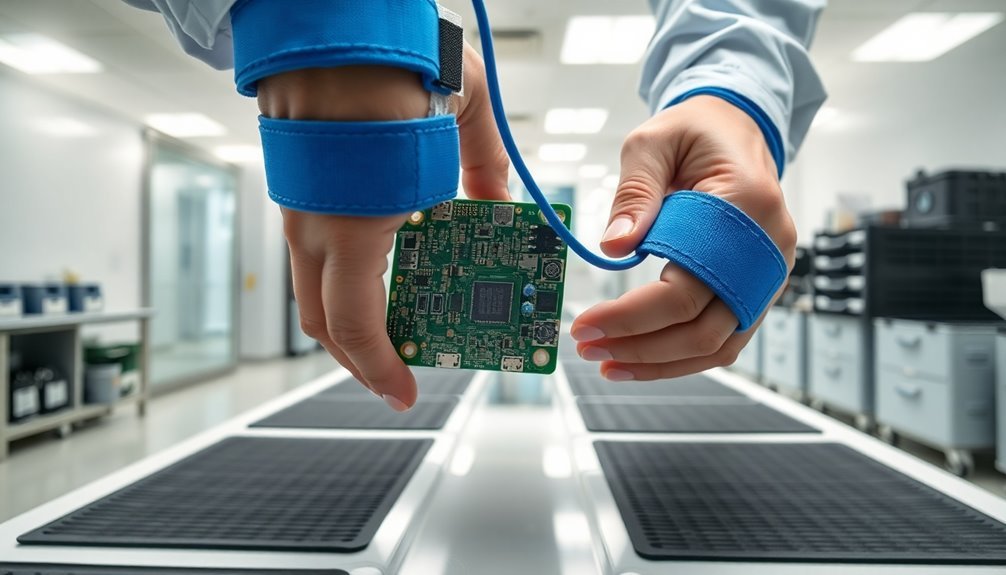
Manufacturing facilities must measure up to strict industry standards when implementing anti-static protection measures. Key regulations like ANSI/ESD S20.20 and IEC 61340 govern how you'll need to design, implement, and maintain your ESD control program. You'll find that compliance isn't optional – it's vital for both worker safety and product quality.
- Your facility needs ESD-safe workstations with proper grounding equipment.
- You must provide workers with anti-static clothing that meets EN 1149-5 standards.
- Your ESD control measures require regular testing and maintenance to guarantee effectiveness.
When you're setting up your anti-static protection program, you'll need to conduct thorough risk assessments to identify areas where static electricity poses the greatest threat. This helps you select appropriate protective measures and equipment.
Remember that different industries have specific requirements – aerospace and semiconductor manufacturing often need stricter controls than general manufacturing.
You'll also need to integrate these measures into your quality management system and provide extensive training to your workforce. Non-compliance can result in costly product damage, workplace accidents, and potential regulatory penalties, so it's critical to maintain proper documentation and perform regular audits of your ESD control measures.
Future of Anti-Static Protection
Building upon established industry standards, the future of anti-static protection promises groundbreaking advancements in technology and materials.
You'll see nanotechnology revolutionizing ESD protection with lighter, more effective solutions, while smart ESD systems will actively detect and neutralize static charges in real-time.
As you look ahead, you'll find IoT integration bringing unprecedented monitoring capabilities to your workplace. Smart sensors embedded in packaging will alert you to potential static risks before they cause damage.
You'll also benefit from new eco-friendly materials that don't compromise on protection, including biodegradable plastics and sustainable packaging options.
Your workwear will become more comfortable and efficient, featuring advanced conductive fabrics that are lighter and more breathable.
You'll have access to personalized ESD garments tailored to your specific industry needs, complete with antimicrobial properties.
The growing e-commerce sector and autonomous driving trends will drive further innovations in ESD protection.
While battery-powered devices still face limitations due to grounding issues, system-level approaches like SEED are developing new solutions to overcome these challenges.
These advancements guarantee you'll have better protection against static electricity in an increasingly electronic workplace.
Frequently Asked Questions
Can Anti-Static Protection Wear Out or Expire Over Time?
Yes, your anti-static protection will wear out over time due to material degradation, chemical exposure, and physical damage. You'll need to replace your gear regularly based on manufacturer guidelines and visual inspections.
How Often Should Workers Test Their Anti-Static Equipment for Effectiveness?
You'll need to test your anti-static equipment daily before shifts, conduct weekly functionality checks, perform monthly calibrations, and complete annual thorough reviews. Don't skip these tests—they guarantee your safety and equipment protection.
Does Humidity Affect the Performance of Anti-Static Protective Gear?
Yes, humidity affects your anti-static gear's performance, but high-quality protective equipment maintains effectiveness in varying conditions. While low humidity increases ESD risks, properly designed anti-static gear will still protect you consistently.
Are There Specific Washing Instructions to Maintain Anti-Static Properties in Workwear?
Yes, you'll need to use mild detergents, avoid fabric softeners, and skip high-temperature washes. Air dry your workwear instead of using heat, and don't mix it with regular laundry to maintain anti-static properties.
Can Workers With Medical Devices Safely Use Anti-Static Protective Equipment?
You can use anti-static protective equipment with medical devices, but you'll need proper consultation first. It's crucial to verify your PPE won't interfere with your medical device's function through professional guidance.
In Summary
You've seen how essential anti-static protection is in today's technology-driven workplaces. Whether you're handling sensitive electronics or working in manufacturing, proper anti-static measures protect both you and valuable equipment. Don't underestimate the risks – one static discharge can destroy components worth thousands. By following industry standards and using the right protective gear, you'll create a safer, more efficient workplace.
Leave a Reply