When selecting ESD floor runners for electronics manufacturing, you'll want to focus on products meeting ANSI/ESD standards with resistance ranges between 10e4-10e6 ohms. Your best options include natural rubber or conductive vinyl runners that provide permanent conductivity through carbon black distribution. Look for materials rated for heavy traffic areas with documented resistance-to-ground (RTG) test results. You'll get ideal protection using runners that combine static dissipative properties with proper grounding methods. While initial costs range from $7-12 per square foot, the investment typically yields a 1,000% annual return in prevented damage to sensitive electronics. Understanding the key specifications will help you make an informed choice.
Understanding ESD Floor Runners
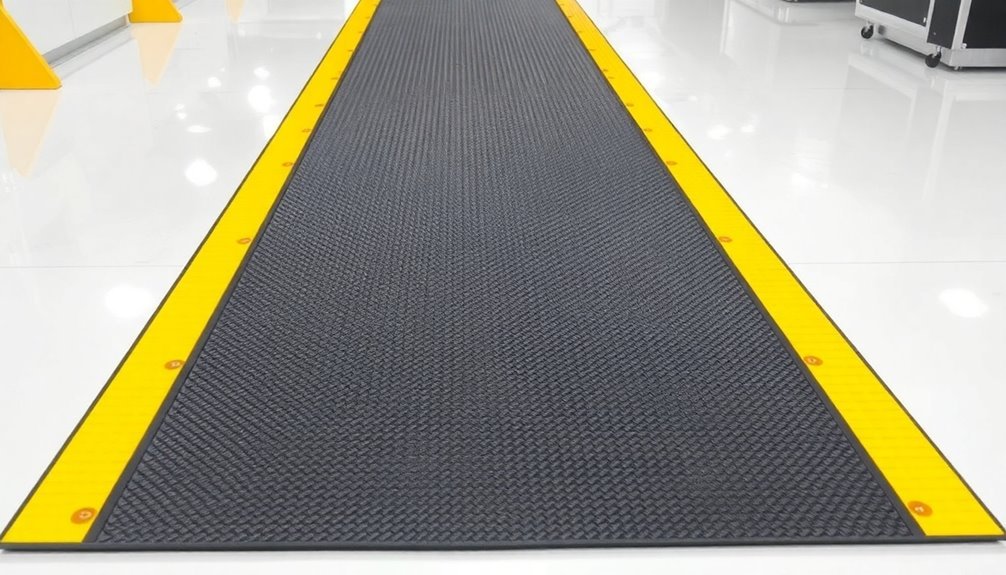
Remember that different industries have varying requirements.
While electronics manufacturing demands strict static control, other environments like telecom facilities or FAA flight towers may have different specifications. With a resistance range of 10e4-10e6 ohms, these floor runners meet strict ANSI/ESD standards.
You'll need to assess your specific risks and choose floor runners that meet your industry's standards while providing adequate protection for your sensitive equipment. Regular post-installation testing of floor runners is essential for maintaining compliance with static control requirements.
Essential Material Properties
You'll need to understand two key electrical conductivity levels when selecting ESD floor runners: conductive materials (with resistance less than 1 x 10^5 ohms/square) and static dissipative materials (with higher resistance ranges).
While conductive materials offer the fastest path to ground, static dissipative materials provide a more controlled discharge rate that can be preferable in some sensitive electronics environments. Natural rubber and nitrile rubber are commonly used materials in the construction of these specialized mats. Regular testing using ANSI STM7.1 standards ensures these materials maintain their protective properties.
The choice between these properties depends on your specific application requirements, including the types of electronic components you're protecting and your facility's overall ESD control program.
Electrical Conductivity Levels Explained
Three critical electrical conductivity ranges define effective ESD floor runners in electronics manufacturing. You'll need to verify your flooring maintains a surface resistance between 1.0 x 10^4 and 1.0 x 10^8 ohms to achieve both safety and proper conductivity. This range provides an effective path to ground while preventing dangerous electrical discharge. VinylSTAT FM7 mats deliver permanent conductivity that remains stable through years of industrial use.
You'll find that conductive vinyl floor runners offer reliable performance through their homogeneous distribution of carbon black and proprietary polymers. These materials create a continuous path to ground that won't degrade over time. Regular maintenance and cleaning are essential since static-control sprays or waxes should never be used to achieve conductivity.
When you're selecting ESD floor runners, you must confirm they meet ANSI/ESD S20.20 standards, which require floor systems to generate no more than 100 volts of static when tested with ESD footwear.
To verify your floor runners' effectiveness, you'll need to conduct system resistance (97.1) and charge generation (97.2) tests with each type of footwear used in your facility. Don't rely solely on manufacturer specifications – testing with your specific footwear guarantees you're getting the protection your electronics manufacturing environment demands.
Static Dissipative Vs Conductive
Understanding the distinction between static dissipative and conductive floor runners shapes your ESD protection strategy. The key difference lies in their resistance levels and dissipation rates: static dissipative materials measure between 1.0 x 10^6 and 1.0 x 10^9 ohms, while conductive materials register less than 1.0 x 10^6 ohms. Walking on these surfaces helps prevent electron accumulation from occurring.
You'll find static dissipative runners ideal for electronics manufacturing and cleanroom environments where controlled, slower discharge is preferred. Regular maintenance checks are essential to ensure consistent performance and longevity of the flooring system. They'll draw charges more gradually and prevent static generation, though you'll need static-protective footwear for peak performance.
For areas with extremely sensitive equipment or hospital ORs using flammable anesthetics, you'll want conductive runners. They provide rapid charge dissipation through direct ground paths, typically utilizing copper grounding strips for every 1,000 square feet.
When selecting between the two, consider your specific application. Conductive runners contain higher ratios of conductive particles or exposed filaments, offering the quickest dissipation but requiring careful grounding.
Static dissipative runners use materials with higher resistance, providing more controlled discharge rates. Both types must comply with ASTM F150 or ANSI/ESD STM7.1 standards and maintain proper grounding connections for safe charge dissipation.
Grounding Requirements And Methods
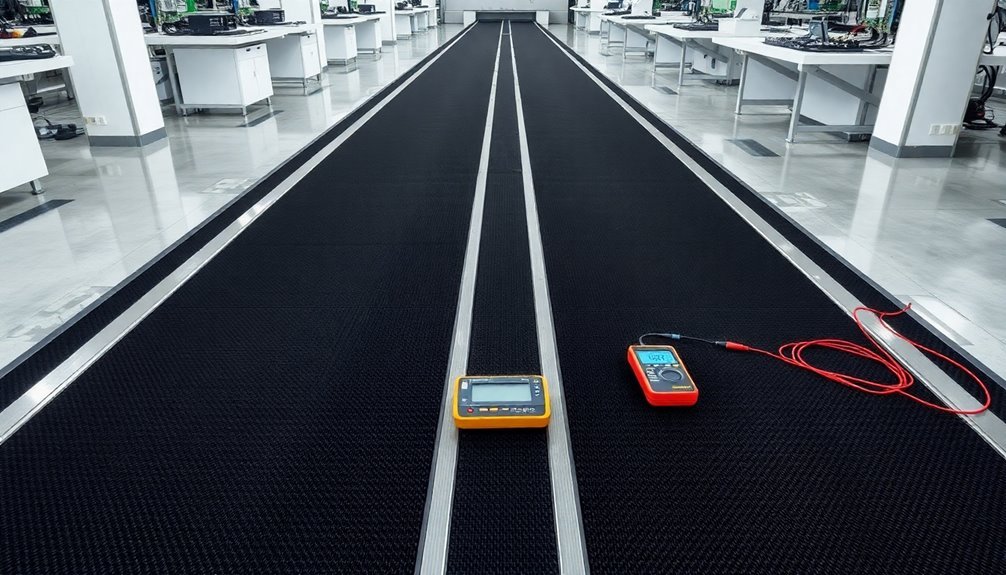
A robust grounding system forms the backbone of effective ESD floor runner installations. When you're installing ESD mats on ESD floors, you'll need to understand that they don't always require hard grounding. If your setup passes a resistance-to-ground (RTG) test with less than 1.0 x 10^9 ohms, you can skip the grounding wire. However, you'll need to add one if the test fails.
You've got several options for grounding your ESD floor runners. You can place them on conductive work surfaces or use grounding cables with resistors connected to electrical outlets. The resistors guarantee static discharges at a controlled rate, preventing sudden discharge events that could damage sensitive electronics.
For monitoring your grounding system, you can use continual monitors as an alternative to traditional mat grounds. These devices apply a test voltage and alert you to any grounding issues.
Remember to maintain proper ESD footwear when working on these surfaces to guarantee effective grounding. Whether you choose common point grounding or separate mat grounding, always verify your setup meets ANSI/ESD S20.20 standards with regular RTG testing using tools like the Metriso 3000 test kit.
Industry Standards And Compliance
When you're implementing ESD floor runners in your electronics manufacturing facility, you'll need to follow ANSI/ESD S20.20 testing guidelines to guarantee proper static dissipation.
Your footwear-flooring system must maintain resistance between 1 million and 100 million ohms while generating less than 100 volts of static electricity.
You'll need to verify that your floor runners can dissipate a 5000V charge to below 50 volts within 2 seconds, as specified by current voltage control protocols.
ANSI/ESD S20.20 Testing Requirements
The ANSI/ESD S20.20 standard sets forth rigorous testing requirements for manufacturers to protect electronic components from up to and beyond 100 volts of electrostatic discharge. You'll need to implement thorough testing protocols that verify your facility's compliance with these strict standards.
Test Component | Frequency | Acceptable Range |
---|---|---|
Wrist Straps | Daily | 750K – 35M ohms |
Floor Materials | Quarterly | 1M – 1B ohms |
Work Surfaces | Monthly | 1M – 1B ohms |
Ionization | Weekly | ±50V discharge time |
Your compliance verification plan must include regular audits of all ESD control items, including floor runners and other protective materials. You're required to maintain detailed documentation of all testing procedures and results. This documentation serves as evidence of your ongoing commitment to ESD protection and helps maintain your facility's certification status.
When testing your floor runners, you'll need to verify both the resistance to ground and the resistance point-to-point measurements. Your records must demonstrate consistent compliance with the standard's requirements, and you'll need to address any deviations promptly through your corrective action procedures. Remember to coordinate these tests with your broader ESD control program plan to guarantee thorough protection.
Footwear Resistance Specifications
Building upon your facility's ESD testing protocols, proper footwear specifications represent a cornerstone of effective static control measures.
When selecting ESD floor runners, you'll need to confirm they're compatible with your facility's footwear requirements as outlined in ANSI/ESD S20.20-2014 and ISO 20345 standards.
Your ESD footwear must maintain specific resistance values that create an effective electrical bond between personnel and the floor runner. You'll want to verify that your footwear's conductive elements meet the resistance specifications detailed in DIN EN 61340 and ESD TR-53 guidelines.
Whether you're using full ESD shoes, heel straps, or sole straps, they must provide consistent electrical contact with the floor runner's surface.
To maintain compliance, you'll need to implement regular testing procedures for all ESD footwear. This includes daily verification of resistance values and thorough inspection of conductive elements.
Don't forget to clean your ESD footwear regularly to prevent insulative residue buildup that could compromise its effectiveness.
Voltage Control Protocols
Maintaining strict voltage control protocols forms the foundation of your ESD floor runner implementation. You'll need to guarantee your flooring-footwear system generates less than 100 volts during walking body voltage tests, as required by ANSI/ESD S20.20. For Class-0 environments, you must achieve even stricter control, keeping voltage generation below 20 volts.
Your floor runners must provide a reliable path to ground while maintaining resistance-to-ground (RTG) measurements below 1x10E9 ohms. You'll need to test your system with the actual footwear that'll be used in your facility, including street shoes if protective footwear isn't mandatory. Remember that some ESD vinyl materials might generate unwanted charges when used with ordinary footwear.
You should implement quarterly verification testing using ANSI STM97.2 to evaluate walking body voltage levels. Don't forget to properly mark your EPA boundaries with appropriate signage and aisle tape.
When working with voltages exceeding 250 VAC or 500 VDC, avoid grounding personnel directly. Instead, focus on establishing proper equipment grounding conductors to maintain equal electrical potential across all ESD protective materials.
Installation Best Practices
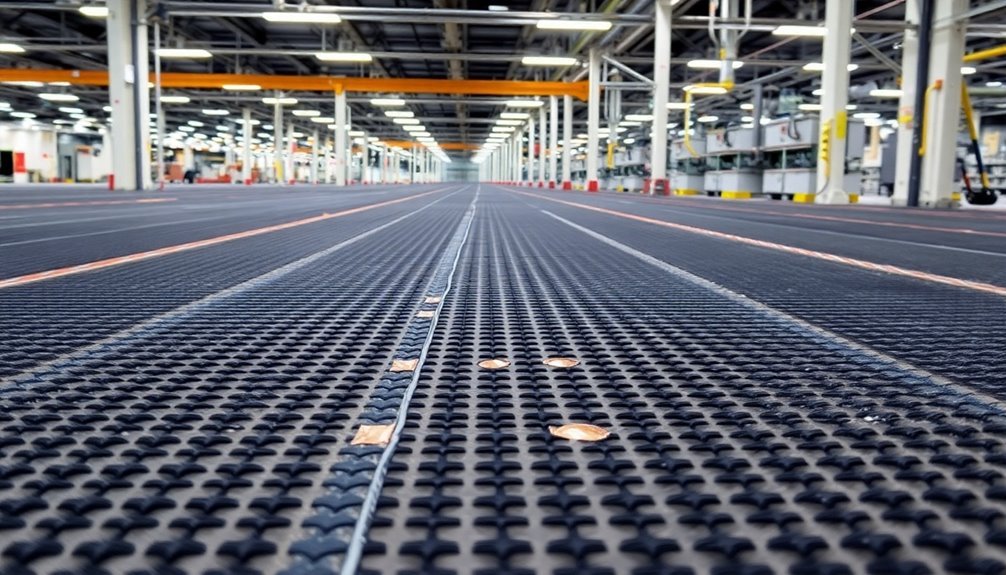
Successful installation of ESD floor runners requires three essential preparation steps before any materials touch the ground.
First, you'll need to thoroughly clean the subfloor, removing all dirt, dust, and debris that could interfere with proper adhesion.
Second, you must ascertain the subfloor is completely dry, as moisture can compromise both the substrate and your new ESD flooring.
Third, you'll need to acclimate your floor runners to the facility's environment to prevent future expansion or contraction issues.
When you're ready to install, follow the manufacturer's specific guidelines for adhesive application and grounding connections.
You'll need to use conductive adhesives or copper strips to create proper grounding points, confirming your runners meet the required resistance level of ≤ 1.0 x 10E9 ohms.
Position each section carefully to maintain consistent spacing and alignment throughout the installation.
Don't skip testing after installation.
Using specialized equipment, verify that your floor runners effectively control static charges below 100 volts and provide the necessary path to ground.
Remember to test the system with ESD-protective footwear to ascertain complete compliance with industry standards like ANSI/ESD S20.20.
Maintenance And Cleaning Guidelines
You'll need to establish a daily cleaning routine using neutral, low-alcohol cleaners that won't compromise your ESD floor runners' conductive properties.
Your maintenance schedule should include regular electrical resistance testing and inspection for wear patterns, especially in high-traffic areas where chair casters frequently roll.
To prevent damage, it's crucial to use only ESD-approved cleaning products and implement preventive measures like routine checks for scratches or scuff marks that could affect conductivity.
Daily Cleaning Best Practices
To protect the integrity of ESD floor runners, proper daily cleaning practices are essential. You'll need to clean these surfaces daily using neutral cleaners with low alcohol content and high surfactant formulas. For best results, use deionized water to prevent mineral contamination, and perform quick maintenance with soft cloth dry cleaning when needed.
Your cleaning toolkit should include microfiber cloths, soft-bristle brushes, and anti-static mops with conductive handles. Make certain all cleaning tools are static-dissipative and properly grounded to prevent static buildup.
You'll want to avoid harsh chemicals, including strong acids and alkalis, as they'll degrade the ESD properties of your floor runners. When cleaning, wear ESD-protective footwear and work in sections to prevent dirt from spreading to clean areas.
Use neutral pH cleaners like 4020 Concentrate Neutral Cleaner, and opt for ESD-friendly disinfectants when necessary. Don't oversaturate the surface with water, as moisture accumulation can compromise the floor's ESD properties.
Remember to inspect the runners regularly for signs of wear or damage to guarantee they maintain their static-control effectiveness.
Preventive Maintenance Schedule
A thorough preventive maintenance schedule forms the backbone of effective ESD floor runner protection.
You'll need to implement regular inspections to detect wear, damage, or any issues that could compromise the ESD performance of your runners. It's vital to document all maintenance activities and guarantee your staff follows proper procedures.
You should schedule deep cleaning sessions periodically using only ESD-safe cleaning products.
Don't use water or excessive moisture, as these can damage the runners' ESD properties. Instead, rely on static-reducing cleaning solutions and dry sweeping or vacuuming for regular debris removal.
To protect your investment, you'll want to install walk-off mats at entrances and use floor protectors under heavy equipment.
Make sure you're regularly checking and maintaining grounding systems, and confirm all personnel are wearing ESD-compliant footwear.
Set up a systematic schedule for maintenance checks and keep detailed records of all activities.
You'll need to conduct periodic audits to verify compliance with industry standards.
If you notice any changes in floor performance or usage patterns, don't hesitate to adjust your maintenance schedule accordingly.
Runner Width And Length Options
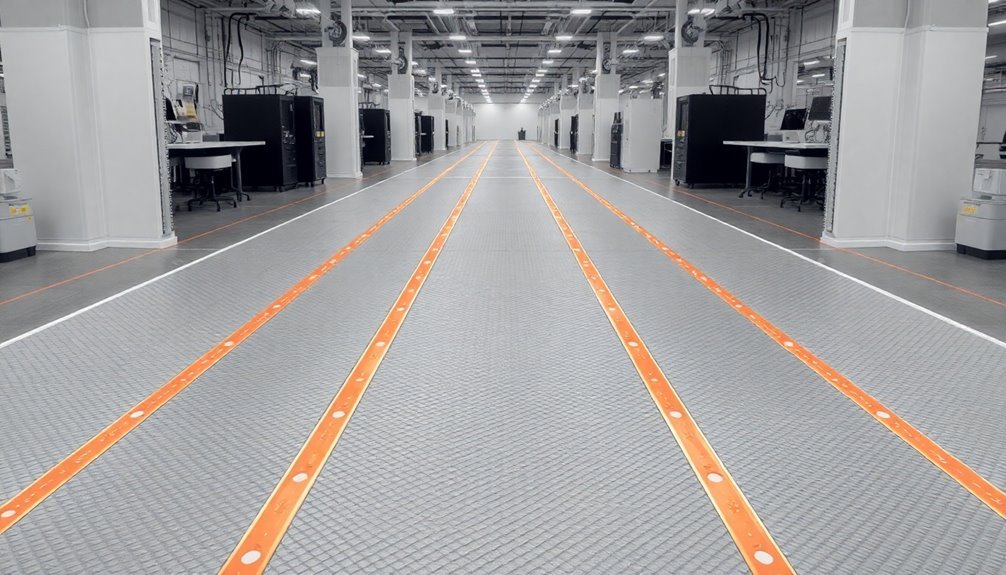
ESD floor runners come in several standard and custom sizes to accommodate diverse workspace requirements. You'll find common widths ranging from 2 feet to 4 feet, with 3-foot and 4-foot options being the most popular for typical manufacturing environments. Vendors like Bertech and Transforming Technologies offer these standard sizes, while also providing custom width options for specialized needs.
When it comes to length, you've got plenty of flexibility. Standard lengths include 3, 5, and 10 feet for smaller workspaces, while vendors like Exterior Coatings offer extended lengths up to 75 feet for larger areas. You can also purchase full rolls from companies like Transforming Technologies and cut them to your exact specifications.
For quick installation, you'll find pre-cut mat kits that come with ground kits included. If you need a custom solution, vendors like Bertech can accommodate special orders for both width and length.
You can easily modify most runners using a utility knife to achieve the perfect fit for your workspace, making them versatile for any manufacturing environment.
Durability And Wear Resistance
The durability and wear resistance of floor runners greatly impact their long-term performance in electronics manufacturing. When selecting runners, you'll find that rubber mats offer superior durability compared to vinyl, especially those with single molded layers. Thicker mats ranging from 1/2" to 9/16" provide better resistance to heavy traffic and daily wear.
Feature | High Durability | Standard Durability |
---|---|---|
Material | Rubber with TriGard ESD | Vinyl |
Surface | Textured/Diamond-plate | Smooth |
Wear Rating | 4x greater resistance | Basic resistance |
To maintain ideal performance, you'll need to take into account both material composition and environmental factors. Runners with textured surfaces withstand heavy traffic better than smooth ones, while nitrile rubber variants offer excellent chemical resistance. For areas with automated equipment like AMRs or AGVs, choose mats specifically designed for high-frequency traffic.
Regular maintenance is essential for preserving ESD properties. You'll want to verify your runners meet ANSI ESD-S20.20 standards, with surface resistance less than 1 x 10^5 ohms/square. The TriGard ESD coating system provides three times greater wear resistance than standard options, making it ideal for high-traffic manufacturing environments.
Cost Analysis And ROI
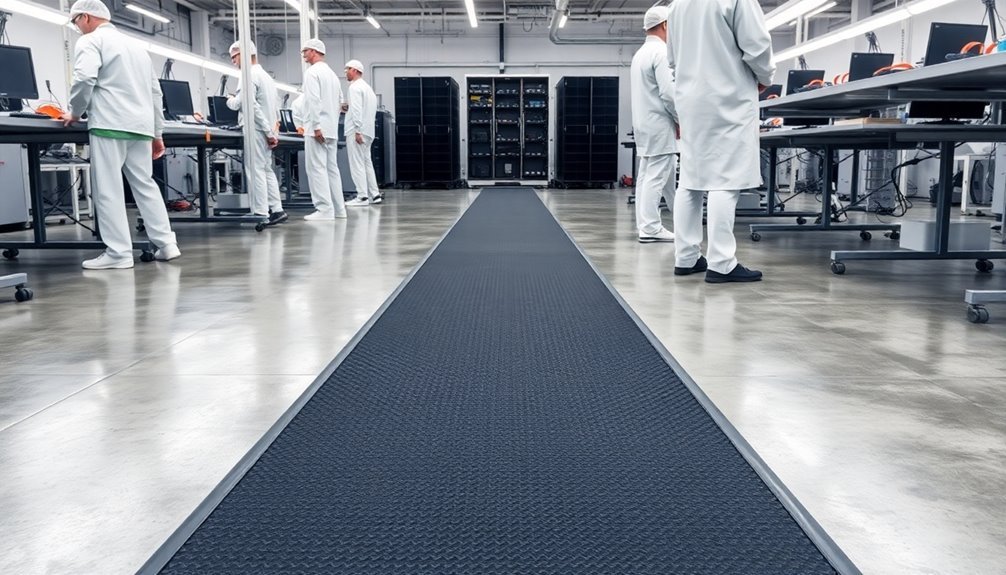
While durability guarantees long-term performance, understanding the financial implications of ESD floor runners will help you make informed investment decisions.
When comparing options, you'll find ESD floor runners range from $7.00 to $12.00 per square foot, with epoxy paint being the most economical at $1.65 PSF and tiles costing around $6.39 PSF.
You can't ignore the compelling ROI statistics: ESD control programs typically yield a 1,000% return annually. For every dollar you invest in ESD protection, you'll save approximately $95 in potential damage costs. This is significant considering the electronics industry faces $5 billion in annual ESD-related damages.
Consider your facility's specific needs when calculating total costs. Floor preparation, installation expenses, and maintenance requirements will affect your long-term investment.
If you're managing areas with heavy machinery or high foot traffic, you'll need thicker flooring, which increases upfront costs but reduces future repairs.
Remember that facility size can work to your advantage through volume discounts, though larger spaces naturally require higher initial investment.
Performance Testing Methods
Testing procedures form the backbone of ESD floor runner performance verification, with three primary methods guaranteeing your installation meets industry standards.
You'll need to conduct electrical resistance testing using ANSI/ESD STM 7.1, which measures how effectively your floor runners transport static charges to ground. For this test, you'll place electrodes on the runner's surface and measure resistance using a megohmmeter.
The walking body voltage test, following ANSI/ESD STM 97.2, simulates real-world conditions. You'll need to walk on the runners wearing special shoes connected to a charge plate meter, guaranteeing the generated voltage stays below 100V for electronics manufacturing environments.
Remember to maintain 15% humidity during testing to get accurate results.
For point-to-point (RTT) and point-to-ground (RTG) testing, you'll measure resistance between surface points and from surface to ground. Your floor runners should register between 1 x 10^6 and 1 x 10^9 ohms to qualify as static dissipative.
It's recommended that you have an independent lab conduct these tests during the qualification phase to guarantee compliance with ANSI/ESD S20.20 standards.
Common Application Areas
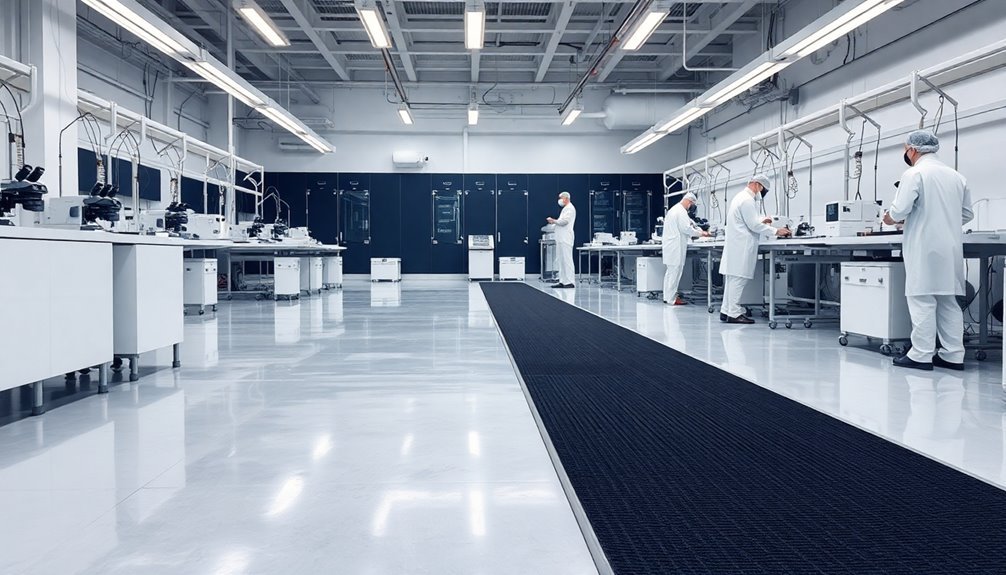
Throughout electronics manufacturing facilities, ESD floor runners serve four critical application areas, each with distinct requirements and challenges.
In electronics manufacturing areas, you'll need runners that meet ANSI/ESD S20.20 standards and provide a verifiable ground path of ≤ 1.0 x 10E9 ohms. You must pair these with ESD footwear to maintain static generation under 100 volts.
For microelectronics fabrication and cleanrooms, you'll require runners with enhanced static control properties due to highly sensitive components. Your flooring must withstand harsh cleaning chemicals while maintaining its electrical properties. Hydrin ESD mats work well in these environments.
In circuit board assembly and repair zones, you'll want anti-static floor runners that create a continuous path to ground when used with ESD footwear. These runners not only dissipate static charges but also protect against scratches and scuff marks.
For data centers and server rooms, you'll need runners that protect against static discharge without necessarily requiring ESD footwear. While these areas don't demand the strictest static control measures, your floor runners must still meet specific electrical standards to prevent data loss and system failures.
Frequently Asked Questions
Can ESD Floor Runners Be Safely Used on Top of Existing ESD Flooring?
Yes, you can safely install ESD floor runners on your existing ESD flooring. They'll enhance static protection and provide ergonomic benefits as long as you use compatible materials and guarantee proper grounding connections.
How Quickly Do Floor Runners Need Replacement in High-Traffic Automated Manufacturing Zones?
You'll need to replace floor runners in high-traffic automated zones every 3-6 months, depending on your maintenance routine. Regular testing and visual inspections will help you determine when they've lost their protective properties.
Do Temperature Fluctuations Affect the Static-Dissipative Properties of Floor Runners?
Yes, you'll find that temperature changes directly impact your floor runners' static-dissipative properties. Higher temperatures can alter the conductivity of materials, while extreme cold may reduce their effectiveness in static dissipation.
Can Floor Runners Be Temporarily Removed and Reinstalled Without Losing ESD Effectiveness?
Yes, you can safely remove and reinstall ESD floor runners without losing effectiveness, as long as you properly store them, avoid damaging the material, and test them after reinstallation to confirm performance.
Are There Specific Footwear Requirements When Using ESD Runners Versus Full Flooring?
You'll need ESD-compliant footwear for both runners and full flooring, but there's no difference in requirements. Your shoes or heel grounders must maintain proper grounding regardless of which surface you're using.
In Summary
Choose your ESD floor runners carefully, as they're a critical investment in protecting your electronics manufacturing process. You'll need to balance cost, durability, and compliance with industry standards while ensuring proper grounding and installation. Regular performance testing and maintenance will maximize your ROI. When properly implemented, these runners will safeguard your sensitive components and maintain a static-safe environment.
Leave a Reply