For electronics protection, you'll commonly find anti-static foam packaging in five standard sizes: micro-component trays at 1.5 x 1.5 x 0.5 inches, standard chip trays at 2 x 2 x 1 inches, circuit board shippers at 7 x 5 x 1.5 inches, half sheets measuring 72 x 40 inches, and full sheets spanning 48 x 108 inches. These dimensions accommodate everything from tiny electronic parts to large equipment, with thickness options ranging from 1/4 inch to 3 inches depending on your protection needs. Understanding the relationship between component size and foam dimensions can help you maximize both protection and cost-efficiency.
Understanding Anti-Static Foam Materials
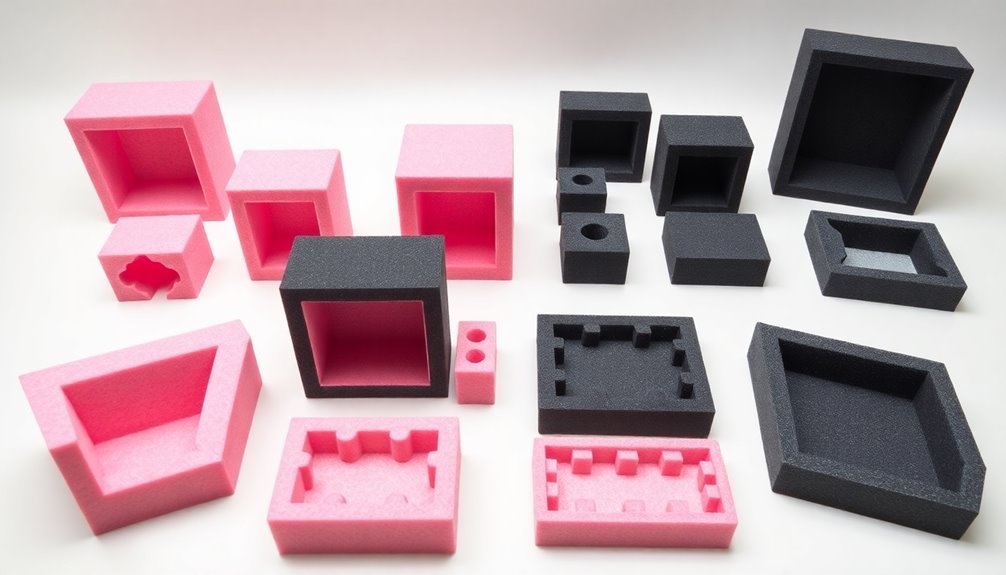
Anti-static foam protection plays a crucial role in safeguarding sensitive electronic components during storage and transit. When you're selecting anti-static foam materials, you'll find several options including EVA, EPE, PU, and PE foams, each offering unique protective properties. EVA foam provides a permanent anti-static performance at a higher density of 85kg/m³.
EVA foam provides a softer cushioning effect, while PE foam offers more rigidity for heavier components.
You'll need to evaluate the foam's static dissipation properties, which help prevent damaging static buildup on your electronic components. The surface resistance typically ranges from 10^3 to 10^9 ohms/sq, depending on the foam type you choose. The open-cell structure of these materials enhances static control while providing necessary cushioning against physical shock.
When selecting your anti-static foam, you'll want to match the material to your specific needs. Evaluate factors like component fragility, required surface resistance, and packaging requirements. You can customize the foam's thickness, shape, and compartmentalization to fit your electronic components precisely.
For eco-conscious choices, EPE foam offers an environmentally friendly alternative while maintaining effective static protection. Remember to balance cost-effectiveness with the level of protection your electronics require.
Standard Electronics Foam Sizes
When you're packaging small electronic components, you'll find that protective foam trays typically come in standardized dimensions that align with common shipping container sizes.
Standard foam inserts for electronics often measure 48" x 108" for full sheets of Ethafoam AS and Stratocell AS, while pink anti-static foam comes in full sheets of 80" x 72", with half sheets and third sheets available at 72" x 40" and 72" x 24" respectively. These materials are enhanced with non-static properties to safely cushion sensitive electronics like computer chips and circuit boards.
You can also request custom-cut foam inserts to match your specific electronic component dimensions, ensuring maximum protection during storage and transport.
Popular Small Parts Trays
Standard foam trays come in a wide range of sizes to protect everything from tiny resistors to complex circuit boards. You'll find that smaller components like capacitors and resistors typically require trays measuring 1.5 x 1.5 x 0.5 inches, while standard chip packages fit well in 2 x 2 x 1-inch trays.
Component Type | Tray Size (inches) | Common Applications |
---|---|---|
Micro Parts | 1.5 x 1.5 x 0.5 | Resistors, Capacitors |
Standard Chips | 2 x 2 x 1 | IC Packages, Small PCBs |
Medium Parts | 3 x 3 x 2 | Transistors, Connectors |
For circuit board protection, you'll want to use 4 x 4 x 1-inch trays, while small electronic modules fit better in 5 x 5 x 2-inch containers. When you're dealing with sensitive components, it's vital to select ESD-safe foam materials that prevent static discharge. These protective trays incorporate specific design features to minimize static stress and often use materials like polyurethane or polystyrene. You can also get custom-sized trays tailored to your specific component dimensions, ensuring maximum protection during storage and transport. The ergonomic pockets in these trays ensure components remain properly oriented during handling and inspection.
Protective Insert Dimensions
Selecting the right protective foam dimensions starts with understanding common sheet sizes available for electronics packaging. The most widely used options include 48" x 108" sheets for Ethafoam AS and Stratocell AS materials, while anti-static urethane comes in 49" x 84" sheets.
Pink anti-static foam is available in full sheets of 80" x 72", half sheets of 72" x 40", and third sheets of 72" x 24". These foam materials offer excellent vibration dampening properties that help protect sensitive components during transit.
You'll find thickness options ranging from 1/4" to 3" for pink anti-static foam, with density variations available across different materials. Ethafoam AS offers 2.2# and 4# densities, while Stratocell AS and anti-static urethane come in 1.7# and 1.2# densities.
When selecting your protective insert dimensions, consider these critical factors:
- Product size and weight distribution to determine ideal sheet dimensions
- Required thickness based on shock absorption needs and drop testing results
- Density requirements for proper cushioning and vibration dampening
- Space constraints within your shipping container or storage area
Custom dimensions are available for special requirements, including convoluted sets and multilayer trays designed to your specifications. You'll also find custom-molded solutions when standard sizes don't meet your needs.
Small Component Protection Dimensions
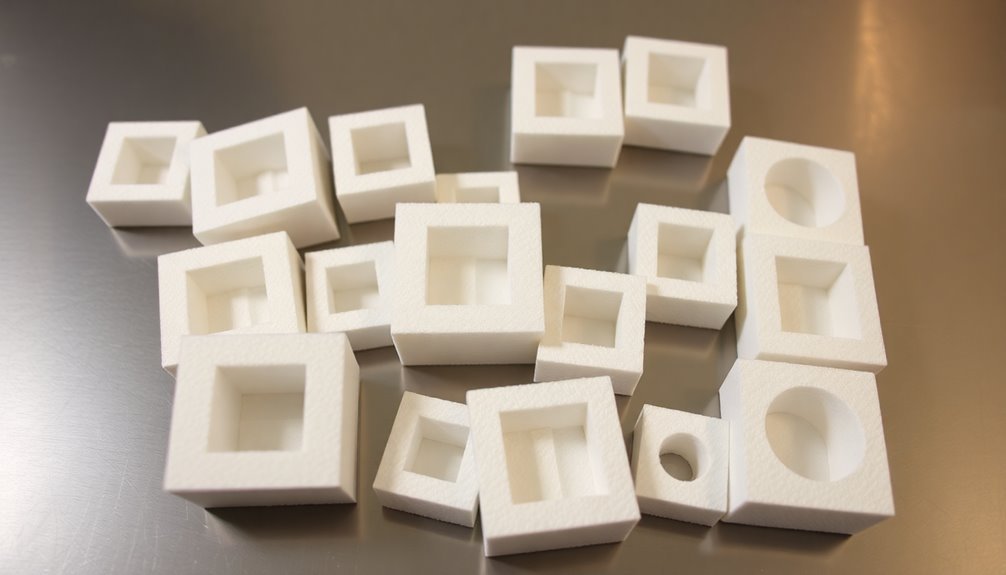
Since protecting small electronic components requires precise measurements, foam packaging dimensions must be carefully selected to guarantee maximum protection. We find standard foam sheets starting at ⅛ inch thickness, with sizes ranging from 3×4 inches to 24×24 inches. For more delicate items, polyethylene foam pouches are available in thicknesses from 1/32 inch to ¼ inch. Anti-static properties in specialized foam packaging help prevent damage from electrostatic discharge during handling and shipping.
When selecting dimensions for your small components, you'll need to take into account both the component's fragility and its static stress requirements. You can choose from various foam types: polyurethane for lighter items, polyethylene for heavier ones, and ESD foam for static-sensitive parts.
Custom-sized cavity trays and foam inserts can be designed to fit your specific boxes or components.
Before finalizing your foam packaging dimensions, you'll want to evaluate several factors, including cushioning curves for the best thickness and drop height requirements. You should also take into account vibration testing to validate your chosen dimensions.
Remember to factor in the component's weight and size when determining cavity depths and overall tray dimensions. This safeguards your small electronic components remaining secure during shipping and handling.
Circuit Board Packaging Measurements
While small components require specific foam dimensions, circuit boards present their own unique packaging challenges. You'll need to carefully measure your circuit boards following a specific order: length (top to bottom), width (left to right), and thickness between dividing cells.
When components or leads extend beyond the board's edge, you'll want to reverse the length and width measurements to guarantee proper fit. For delicate circuit boards with a fragility factor of 40-60 Gs, extra cushioning layers are necessary.
Standard foam shippers, like the 7 x 5 x 1-1/2 inch black ESD-protective options, accommodate many common board sizes. However, you'll need to take into account board layer counts when determining appropriate packaging, as manufacturing capabilities differ substantially:
- Single and double-layer boards can reach up to 59" x 50", making them suitable for larger foam containers
- Four to six-layer boards max out at 32" x 28", requiring mid-sized packaging solutions
- Eight to twenty-layer boards are limited to 30" x 24", fitting in standard foam shippers
- Minimum board sizes start at 0.2" x 0.2" for simple layers, increasing to 0.4" x 0.4" for complex ones
The foam's density should match your board's PSI requirements, calculated by dividing the weight by the surface area of each side.
Large Equipment Foam Solutions
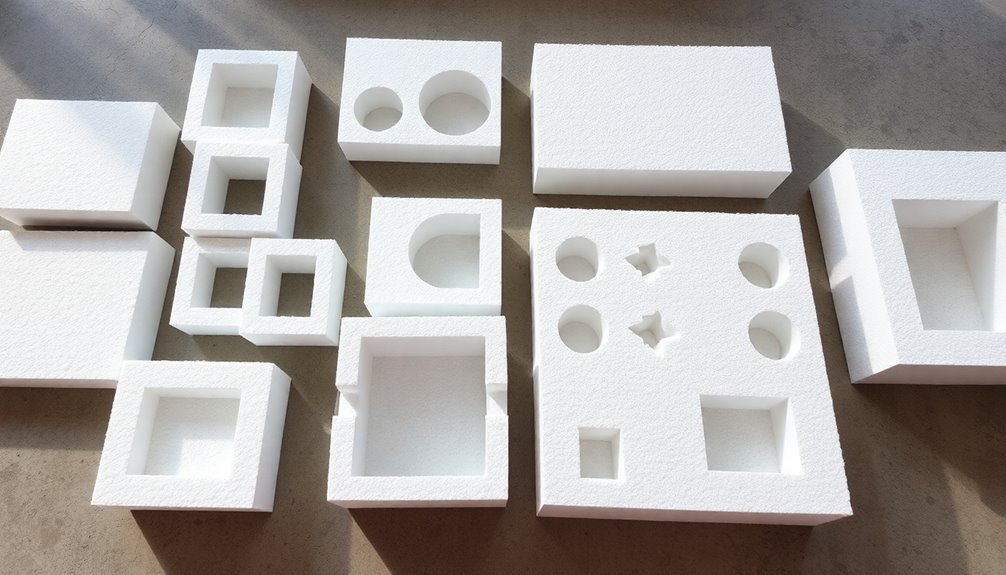
Today's large equipment packaging demands robust foam solutions that adapt to unique product dimensions and fragility requirements. When you're packaging large electronics, polyurethane foam stands out as your primary choice due to its exceptional shock absorption and lightweight properties. The foam's ability to expand up to 250x its liquid volume makes it incredibly efficient for large-scale packaging operations.
You'll find that these foam solutions can effectively protect heavy items or those with sharp edges through customized molds created by on-demand systems.
To determine the right foam solution for your equipment, you'll need to calculate the PSI based on weight and size, while considering the product's fragility factor.
Custom foam packaging systems offer you significant advantages, including reduced material waste, lower transport costs, and minimal storage requirements. You can choose between different foam types: polyurethane for maximum durability, EPS for lighter applications, or recycled foam options for enhanced sustainability.
On-demand foam systems let you create precise, tailored protection that fully encapsulates your equipment when needed. You'll benefit from superior cushioning against impact shock and vibration, while the system's versatility allows for void filling, blocking, or bracing as your specific application requires.
These solutions guarantee your large electronics remain secure throughout shipping and handling.
ESD Safe Packaging Options
Beyond standard foam packaging for large equipment, electronics require specialized protection against electrostatic discharge (ESD). You'll find various anti-static and conductive materials designed to prevent damage from electrical charges. These specialized materials include anti-static polyurethane ether foam, which won't contaminate or corrode your components, and closed-cell polyethylene foam that offers superior cushioning in different densities. With a global market value of $2.4 billion, ESD-safe packaging continues to be a critical investment for electronics protection.
When selecting ESD safe packaging for your electronics, consider these critical factors:
- Surface resistance levels between 10^4 and 10^9 Ohms guarantee proper static dissipation while protecting sensitive components.
- Customized foam inserts cut precisely to your component specifications provide thorough protection against movement and static.
- Metalized shielding bags combined with anti-static foam create a complete barrier against electromagnetic interference.
- Closed-cell foam solutions offer better durability for heavier electronic items while maintaining ESD protection.
You'll need to match your packaging to specific industry standards, particularly EIA-541 for ESD-sensitive items. Consider working with reputable suppliers who can provide tailor-made solutions, including anti-static foam pads and conductive packaging materials that maintain their protective properties throughout use.
Custom Sizes For Special Projects
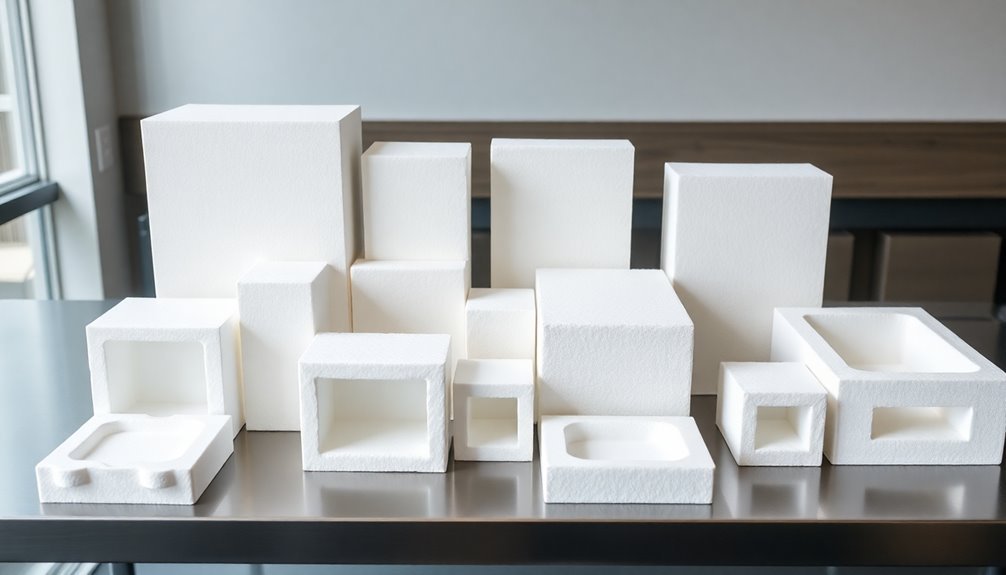
When your electronics protection needs go beyond standard dimensions, you'll find custom foam packaging solutions that can accommodate virtually any size or shape requirement.
Custom sizes are particularly valuable for complex parts and specialized equipment that don't fit conventional packaging options. You can get precise, non-standard dimensions tailored to your specific project needs, whether it's for intricate electronic components or large-scale industrial equipment.
This level of customization is achieved through advanced design software and precise cutting techniques, such as water jet or CNC machines, which ensure a perfect fit that secures the electronics within the packaging[2.Dto prevent damage, custom foam inserts are made from specialized materials like polyurethane foam, polyethylene foam, or expanded polystyrene foam. These materials possess unique properties ideal for electronic packaging, including shock absorption, precision fit, and protection against impacts.
The design process involves understanding the dimensions and fragility of the electronic device, selecting the appropriate foam material based on factors like weight and sensitivity, and then precisely cutting the foam to match the device's contours.
Additionally, custom foam packaging can contribute to sustainability efforts by using recyclable materials and minimizing the need for replacements due to damage during transit.
Non-Standard Dimensions Available
Through advanced manufacturing capabilities, custom foam packaging solutions are readily available for electronics that don't fit standard dimensions. You'll find extensive size options ranging from tiny components (.125" X .125") to large industrial equipment (up to 50" X 72" X 72"). This flexibility guarantees you're never limited by standard sizing constraints when protecting your electronic devices.
When you need non-standard dimensions, you can choose from various foam materials, including polyurethane, polyethylene, and EPS foam, each offering specific benefits for electronics protection.
The manufacturing process adapts to your unique requirements through:
- Rapid prototyping within 1-5 days to test and validate your custom design
- Large-scale production capabilities with 3-7 day turnaround times
- Material laminating options to combine different foam types for enhanced protection
- Custom shape creation to precisely fit your electronic components
You'll benefit from thorough design considerations that account for your product's fragility, required cushioning, and vibration protection needs. Whether you're shipping sensitive medical devices or temperature-dependent electronics, these custom solutions guarantee the best protection while maximizing space efficiency through tailored dimensions and multilayer designs.
Design For Complex Parts
Designing protective foam packaging for complex electronic parts requires meticulous attention to multiple factors. When you're working with intricate components, you'll need to carefully assess the product's size, weight, and fragility before selecting the appropriate foam material.
You can choose from several foam options depending on your specific needs. EPS provides lightweight rigidity, while polyurethane foam offers superior shock absorption. If you need water resistance, polyethylene foam is your best choice, and EVA foam delivers versatile protection. For electronics sensitive to static, you'll want to incorporate antistatic foam materials.
The design process starts with precision measurements and analysis of your product's handling requirements. You'll need to take into account factors like temperature conditions and transportation methods.
Using advanced cutting techniques, such as water jet or CNC machines, you can create exact fits for your components. For complex shapes, custom molding might be necessary. You can also implement multilayer trays or convoluted foam inserts to maintain stable product positioning.
Remember to factor in shock absorption capabilities by selecting the right foam density and thickness based on cushioning curves. This guarantees the best protection against impact forces during shipping and handling.
Density Requirements For Electronics
The precision of foam density plays an essential role in safeguarding sensitive electronic components during storage and transit. You'll need to evaluate density requirements between 20-35 Kg/m3 for conductive sponge sheets, which provide the best protection while maintaining essential physical properties for electronics packaging.
When selecting foam packaging density, you must account for multiple protection factors, particularly in preventing electrostatic discharge (ESD). Your foam materials should maintain a surface resistance between 10^4-10^9 ohms to effectively dissipate static charges, while the density directly impacts shock absorption and vibration protection capabilities.
For standard electronic components, maintain density levels below 25% to guarantee proper cushioning and static protection.
When using PowerCSP technology, you can increase density to 40-70% due to continuous Cu substrates.
Select polyurethane or polyethylene foams based on your specific density and protection requirements.
Evaluate thermal conductivity needs when determining the best density, especially for heat-sensitive components.
Remember that packaging density affects not just protection but also manufacturing processes and rework capabilities. You'll need to balance these factors while guaranteeing compliance with standards like EIA-541 for ESD-sensitive items.
Foam Thickness Selection Guide
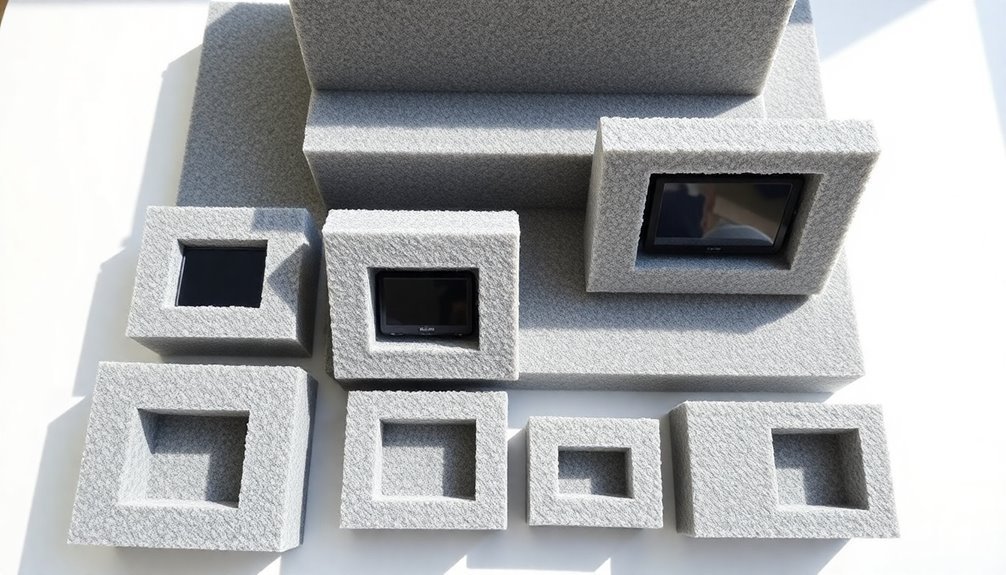
Selecting the right foam thickness stands as your first line of defense in electronics protection. When choosing the appropriate thickness, you'll need to think about your product's weight, fragility, and the surface area that'll contact the foam.
Standard thicknesses range from 1/4″ to 2″, with options up to 4″ for heavy-duty applications.
To determine the ideal thickness, you'll first need to calculate the static loading by dividing your product's weight by its largest surface area touching the foam. Next, match your product's fragility level to its corresponding G-value using fragility charts. This helps you select the most suitable foam thickness for the best protection.
For lighter, delicate electronics, you'll typically want to use thinner foams between 1/4″ to 1/2″. Heavier items require thicker options, potentially up to 2″ or more.
Keep in mind that sheets thicker than 1/2″ may be laminated from smaller sheets, which can cause slight variations in thickness. While charts provide good starting points, you should think about conducting drop tests for precise G-factor determination, especially for valuable or sensitive electronics.
Material Properties And Applications
Understanding foam material properties takes your electronics protection to the next level, building on proper thickness selection. You'll find two main types dominate the market: closed-cell polyethylene foam for larger electronics and polyurethane foam for smaller, static-sensitive components. Each offers distinct advantages in protecting your valuable equipment during storage and transport.
When selecting foam materials for your electronics packaging, think about these critical factors:
- Protection needs – Match your foam choice to specific threats, whether it's impact resistance from polyethylene or ESD protection from anti-static polyurethane.
- Device specifications – Factor in weight and fragility to determine the best foam density and cushioning requirements.
- Environmental concerns – Choose eco-friendly options like biodegradable foams when sustainability is a priority.
- Budget constraints – Balance cost considerations between standard EPS foam and premium XLPE options.
Your foam selection should align with industry standards, particularly for ESD-sensitive components requiring compliance with EIA-541 guidelines.
You'll want to think about both general and specific applications, from vibration dampening to component organization, ensuring your electronic devices receive thorough protection suited to their unique requirements.
Industry Specific Size Requirements
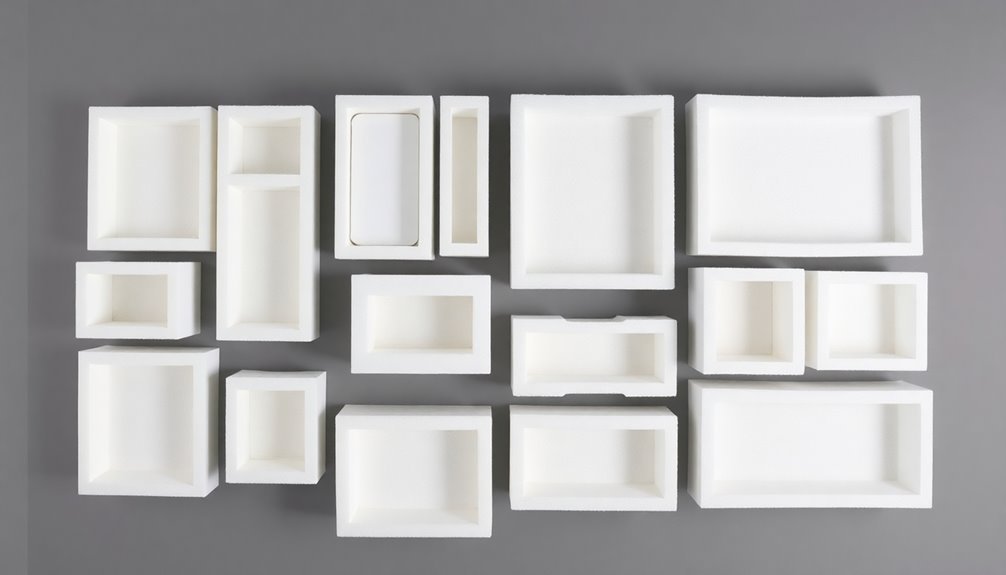
When you're packaging medical devices, you'll need to follow strict dimensional requirements that account for both device protection and sterilization needs.
For medical devices, the packaging process involves various steps, such as design and layout, materials selection, sterilization compatibility, and validation testing. The package must protect the device and keep it sterile during all stages of the distribution channel and while in storage. Factors to consider include device dimensions, weight, density, and materials used; sterilization compatibility and requirements; packaging material needs; validation testing; and regulatory requirements.
For computing hardware, you'll want to take into account standard rack dimensions and spacing requirements for proper airflow and heat dissipation. The most popular modern server rack and cabinet dimensions are 24 inches (600mm) wide, 42 inches (1066.80mm) deep, and 73.6 inches (1866.90mm) tall. These dimensions support most IT equipment and typically handle power loads of about 8kW per rack or less.
These industry-specific size requirements guarantee your foam packaging not only protects the equipment but also complies with relevant standards. For server racks, the EIA-310 standard provides guidelines, with each Rack Unit (U) equaling 1.75 inches (44.45 mm), and the rack opening must be at least 17 3/4 inches (450 mm) wide, while the front panel width remains a standard 19 inches (482.6 mm).
These standards, such as EIA-541 and MIL-SPECs, ensure that the packaging complies with the necessary regulations and provides the required protection for the equipment.
Standard Medical Device Dimensions
Medical device packaging requires precise dimensional standards that align with ISO 11607 requirements while maintaining sterility and functionality. You'll need to guarantee your packaging materials are non-toxic, traceable, and free from any physical defects that could compromise the device's integrity.
When designing foam packaging for medical devices, you must consider the specific nature of each device, including its intended use, transportation requirements, and storage conditions.
Critical dimensions in medical device packaging directly impact functionality and regulatory compliance. You'll want to focus on dimensions that affect:
- Sterile barrier system performance – guaranteeing proper sealing and maintaining sterility until point of use
- Device protection during transport – preventing movement and potential damage
- Aseptic presentation capabilities – allowing proper handling by healthcare professionals
- Interchangeability requirements – maintaining consistent sizing for standardized components
Your foam packaging design should incorporate moment-ratio definition systems for calculating mean sizes and standard deviations. Don't forget to validate critical dimensions early in the development process, as this will streamline production and guarantee regulatory compliance.
Remember that all measurements must be documented using SI units for standardization across international markets.
Computing Hardware Space Needs
Computing hardware space requirements vary across four key dimensions that determine ideal foam packaging design.
When you're packaging laptops, you'll need to account for devices ranging from 13" to 15" in display size, with additional clearance for ports and connections along the sides. Your foam design must protect both USB/USB-C ports and video outputs like HDMI or DisplayPort.
The internal components also influence packaging dimensions. Modern laptops house powerful processors like Intel Core i5/i7 or Apple M2 chips, requiring adequate cushioning around heat dissipation areas.
Storage components, whether 256GB or 512GB SSDs, need specific protection zones within the foam layout. You'll want to guarantee the foam cavity accommodates various RAM configurations, from 8GB to 16GB installations, which can affect overall device thickness.
Consider additional space for external peripherals like power adapters, USB dongles, or Ethernet adapters that often ship with laptops. Your foam design should include dedicated cutouts for these accessories while maintaining proper density to absorb shock.
The packaging must also account for wireless antenna locations and prevent signal interference during shipping and handling.
Cost Effective Size Selection
Through careful analysis of foam packaging dimensions, selecting cost-effective sizes involves balancing material density, thickness, and customization options. You'll find that higher density and thicker foam isn't always the best choice, as it can increase costs without providing additional protection.
The key is to calculate the PSI requirements based on your product's weight and surface area.
When choosing foam packaging sizes, you'll want to take into account these critical factors:
- Calculate your product's PSI requirements by dividing total weight by the surface area in square inches.
- Select foam thickness based on cushioning curves that match your product's fragility and drop height requirements.
- Take into account reusability factors if you're shipping products regularly – closed-cell polyethylene foam can be reconfigured.
- Factor in environmental impact by choosing recyclable materials like biodegradable polyurethane.
You can optimize costs by selecting standard foam sheet sizes ranging from 3×4 inches to 24×24 inches, or opt for custom foam inserts that precisely fit your electronics. For larger items, EPS foam offers dimensions up to 48×96 inches, while foam pouches provide flexibility with various thicknesses from 1/32 inch to ¼ inch.
Frequently Asked Questions
Can Foam Packaging Be Safely Recycled After Use With Electronic Components?
Yes, you can safely recycle foam packaging used with electronics. Just make sure it's clean, identify the foam type (EPS, PE, or PU), and take it to a proper recycling facility or community program.
How Long Does Anti-Static Foam Maintain Its Protective Properties in Storage?
You'll need to regularly test your anti-static foam as its shelf life varies substantially. While proper storage helps, there's no guaranteed duration. It's best to verify protective properties annually through compliance testing.
What's the Maximum Temperature Foam Packaging Can Withstand During Shipping?
You'll find most foam packaging can withstand temperatures between 82-100°C (180-212°F), with polypropylene foam being the most heat-resistant. However, it's best to keep your packages below these maximum limits during shipping.
Are There Specific Cleaning Methods for Reusable Electronic Foam Packaging?
You'll need to use a soft-bristled brush, ESD-safe foam swabs, and anti-static cleaners for reusable electronic foam packaging. Avoid harsh chemicals and high-pressure washing, then let it dry completely before reuse.
Does Foam Packaging Require Special Storage Conditions to Maintain Effectiveness?
Yes, you'll need to store foam packaging in low humidity (under 60%), at room temperature, and away from direct sunlight. For electronics protection, use antistatic foam and avoid crushing or excessive handling.
In Summary
You'll find that selecting the right foam packaging size is essential for protecting your electronic components. By understanding standard dimensions, material properties, and industry requirements, you can make cost-effective choices that guarantee proper protection. Whether you're shipping small components or large equipment, choosing appropriate foam thickness and anti-static properties will safeguard your electronics during transport and storage.
Leave a Reply