Top US foam protects your sensitive electronics better through advanced material engineering and rigorous testing standards. You'll find specialized anti-static foams like PE, EVA, EPE, and PU that prevent harmful static discharge while offering superior shock absorption. These materials maintain surface resistance between 10^4 to 10^11 ohms, meeting strict ANSI/ESD S20.20 and IEC 61340-5-1 standards. They're also fully customizable through precise fabrication methods like CNC routing and water jet cutting, ensuring perfect fits for your devices. The combination of physical protection and static control makes premium US foam solutions an investment that pays for itself. Discover how these innovative materials can safeguard your valuable electronics.
Anti-Static Foam Material Types
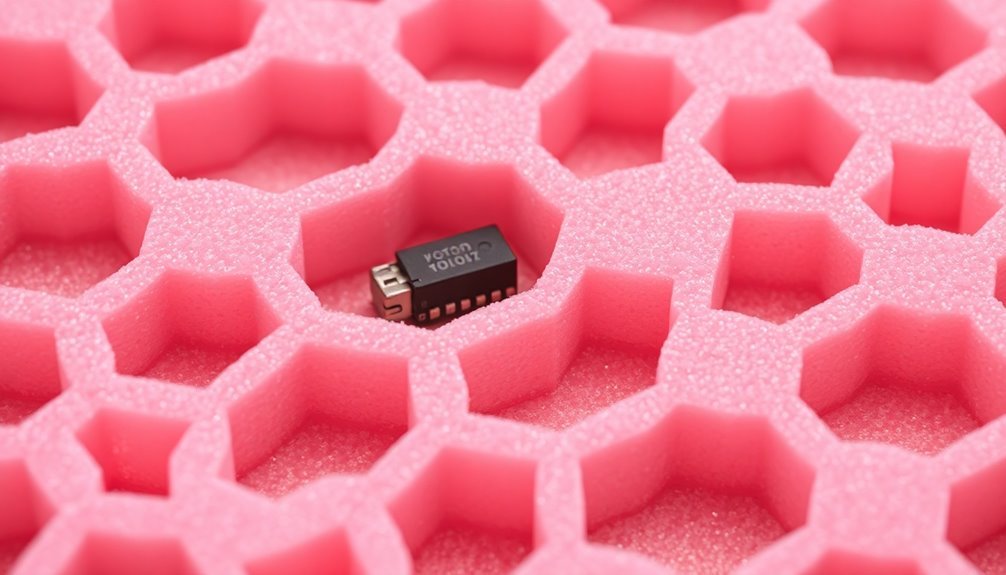
Anti-static foam protection comes in several distinct varieties, each engineered to safeguard sensitive electronic components. You'll find four main types dominating the market: PE, EVA, EPE, and PU foam, each offering unique protective qualities while preventing static build-up.
PE foam features a closed-cell structure made from polyethylene with conductive agents, available in densities of 45kg/m3 and 67kg/m3. It's typically black and offers surface resistance ranging from 10^3 to 10^9 ohms. These materials must comply with ANSI/ESD standards to ensure effective protection.
EVA foam, constructed from ethylene vinyl acetate, provides higher hardness than PE and comes in various colors including black, blue, red, and white, with a density of 85kg/m3.
EPE foam, made from expandable polyethylene, features a non-cross-linked closed-cell structure and is available in pink or red.
PU foam differs with its open-cell structure, incorporating polyurethane with conductive fillers.
All these materials share key properties: they're lightweight, flexible, and highly customizable to your specific needs. You can adjust their size, shape, and compartmentalization to create the perfect protective environment for your electronic components while maintaining consistent anti-static properties.
Static Discharge Protection Standards
When you're selecting anti-static foam for electronics, you'll need to verify that it meets key ESD standards like ANSI/ESD S20.20 and IEC 61340-5-1 through certified testing procedures.
Your foam's surface and volume resistivity ratings must fall within 1 x 10^4 to 1 x 10^11 ohms to comply with most international standards for static-sensitive device protection.
You'll also want documentation showing the foam has passed triboelectric charge generation tests and maintains consistent electrical properties across varying humidity levels. Regular static surveys and monitoring of foam materials helps prevent latent damage that could lead to unexpected component failures.
ESD Compliance Testing Requirements
Electronic devices require strict ESD compliance testing to protect against potentially devastating static discharge damage. When you're handling sensitive components, you'll need to guarantee your facility meets key standards like ANSI/ESD S20.20 and IEC 61340-5-1, which establish thorough guidelines for ESD control programs. Testing isolated conductors must ensure a potential difference <35 volts between conductor and ESDS items.
You'll need to verify specific resistance measurements across your protection systems. Your wrist strap and groundable static control garment systems must maintain resistance below 3.5 x 10^7 ohms.
For footwear and flooring systems, you can't exceed 1.0 x 10^9 ohms resistance and must keep peak voltage under 100 volts. Similarly, your seating needs to demonstrate point-to-ground resistance below 1.0 x 10^9 ohms.
To maintain compliance, you'll need to create an electrostatic protective area (EPA) where you handle ESD-sensitive items. This includes implementing proper grounding systems, using ESD-safe packaging materials, and conducting regular testing.
You'll also need to guarantee your staff receives proper training on using protective equipment and following ESD control procedures. Regular audits will help you verify that all these elements continue meeting the required standards.
Foam Resistivity Rating Standards
Understanding foam resistivity ratings is vital for protecting your sensitive electronic components from static discharge damage. You'll need to evaluate the surface resistivity ratings that range from 10^3 to 10^9 ohms, depending on your specific protection requirements.
When you're working with highly sensitive electronics, you'll want to choose conductive foam with resistivity between 10^3 and 10^5 ohms. This type creates a Faraday cage around your products, eliminating the need for additional static shielding bags. The foam's surface resistivity of <0.08 ohms/sq provides exceptional conductivity for maximum protection.
For less sensitive components, anti-static foam with resistivity between 10^6 and 10^9 ohms will provide adequate protection against static buildup.
You'll need to verify your foam selection complies with recognized standards like ANSI/ESD S20.20 or IEC 61340-5-1. These standards provide key guidelines for implementing effective electrostatic discharge control programs.
They'll help you establish proper grounding systems, packaging protocols, and environmental controls. When you're setting up your electrostatic protective areas (EPAs), you'll need to regularly test your foam's surface resistance to maintain compliance and guarantee consistent protection for your electronic components.
Physical Durability and Strength
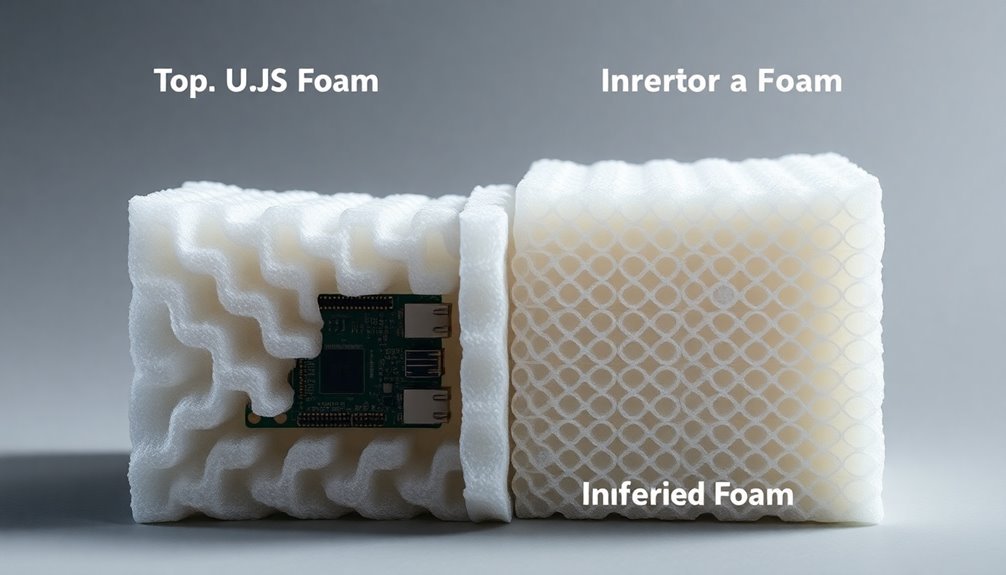
Physical durability and strength consistently rank among the most essential aspects of protective foam for sensitive electronics. You'll find that closed-cell polyethylene offers exceptional dimensional stability and recovery, making it ideal for protecting delicate components. When you're selecting foam, you'll need to take into account density ranges from 2 to 6 lbs. pcf, as these variations directly impact the foam's protective capabilities. For optimal electronics protection, materials like Dow Ethafoam provide superior anti-static properties through their specialized internal additives.
Property | Benefit | Application |
---|---|---|
Shock Absorption | Protects against impacts | Transportation & Handling |
Vibration Dampening | Reduces mechanical stress | Equipment Operation |
Dust Sealing | Prevents contamination | Storage & Shipping |
Thermal Management | Controls temperature | Heat-sensitive Components |
Cross-linked polyethylene's enhanced structural rigidity provides superior tear resistance, while its non-abrasive surface safeguards your sensitive components from getting scratched. You'll appreciate how these foams excel at cushioning protection, effectively absorbing mechanical shocks that could otherwise damage your electronics. When you're dealing with environmental factors, these materials offer reliable protection against extreme temperatures and other hazards. For the best results, you'll want to regularly inspect the foam's quality to maintain its protective properties over time.
Customization Options for Electronics Storage
When you're looking to protect sensitive electronics, precision-cut foam solutions offer unmatched customization by perfectly matching your device's exact dimensions and contours.
You'll find that professionally cut foam inserts create secure, snug compartments that prevent movement and reduce the risk of damage during handling or transport.
The modular nature of these storage solutions lets you adapt and reconfigure spaces as your electronics collection grows, making it a smart long-term investment for your storage needs. Anti-static materials provide additional protection against electrostatic discharge that could harm delicate components.
Precision Cut Foam Solutions
The precision cut foam solutions industry has revolutionized electronics storage with advanced customization options that safeguard sensitive components.
You'll find multiple foam types designed for specific needs: PU foam offers excellent shock absorption and custom molding capabilities, while PE foam provides moisture resistance and cost-effective anti-static options. For temperature-sensitive items, EPS foam delivers superior insulation. The versatility allows for thermal management solutions that enhance electronic system performance.
When you're selecting fabrication methods, you'll have access to cutting-edge technologies. CNC routing creates custom precision parts without expensive tooling, while water jet cutting guarantees clean, precise cuts ideal for protective case inserts.
You can also opt for die cutting or foam molding to achieve specific dimensions for your devices.
You'll notice immediate benefits from implementing custom foam solutions. Your electronics receive maximum protection against damage during handling and transport, while maintaining a professional appearance that enhances brand perception.
The anti-static properties prevent electrostatic discharge, and the organized storage systems reduce the risk of component loss. Whether you're in electronics manufacturing, energy storage, or developing wearable devices, you'll find precision cut foam solutions that match your specific requirements.
Modular Storage Design Benefits
Building on precision cut foam solutions, modular storage designs offer unprecedented flexibility for organizing and protecting electronic components. This flexibility is crucial as these systems adapt seamlessly to your changing inventory needs while maximizing vertical space utilization in your production areas. The ability to be stacked without reinforcement makes these storage solutions exceptionally space-efficient.
When you're storing sensitive electronics, you'll appreciate how modular systems incorporate specialized features like ESD protection and customizable compartments. You can easily configure the storage layout with partitions and dividers to accommodate components of various sizes, ensuring each item has its dedicated space.
The build-as-you-grow approach means you won't need to invest in excess storage capacity upfront. This approach allows for incremental expansion as your storage needs evolve.
Your productivity will increase thanks to automated storage features like laser pointers and LED bars that enhance picking accuracy. The vertical carousel systems bring components directly to you, improving ergonomics and reducing the risk of handling damage.
You'll also benefit from reliable inventory management, as these systems make it simple to track and access components on demand. With modular storage, you're not just organizing parts – you're creating a sophisticated system that protects your sensitive electronics while optimizing your workspace efficiency.
Cost Benefits of Quality Foam
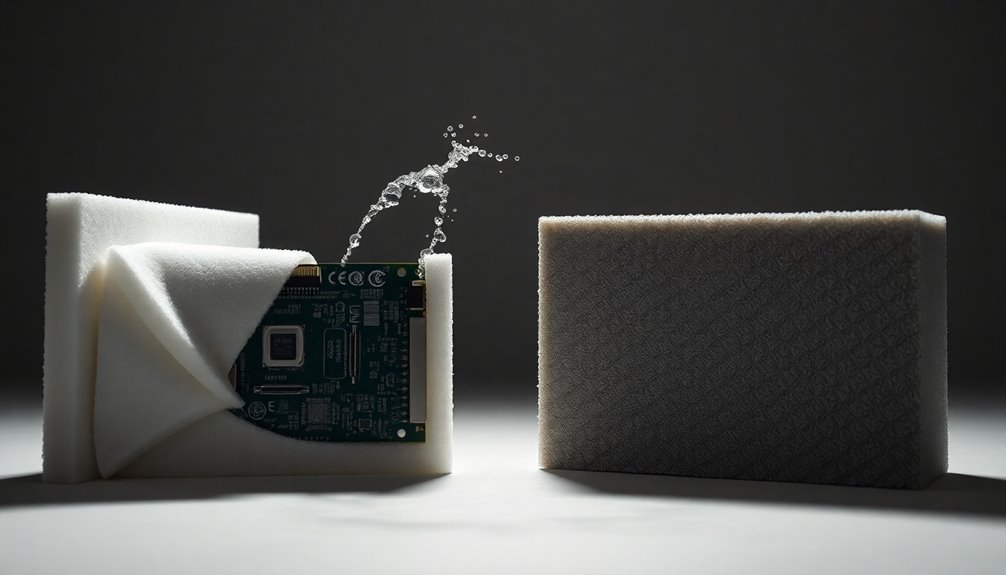
Investing in quality foam for electronics packaging delivers substantial financial benefits across multiple business areas. You'll see immediate returns through reduced damage costs, lower shipping expenses, and enhanced operational efficiency.
When you protect sensitive electronics with premium foam solutions, you're effectively preventing costly returns, warranty claims, and replacement part expenses.
Consider these tangible savings opportunities:
- You'll eliminate up to 90% of shipping-related damage claims by using custom-cut foam inserts that cradle your electronics perfectly.
- Your warehouse team will pack products 40% faster with well-designed foam solutions that streamline the handling process.
- You'll reduce customer service costs by 60% through fewer damage complaints and returns processing.
The long-term ROI extends beyond immediate cost savings. Your brand reputation strengthens when customers consistently receive undamaged products, leading to increased loyalty and repeat business.
The initial investment in quality foam quickly pays for itself through improved operational efficiency, reduced damage rates, and enhanced customer satisfaction. By implementing professional foam packaging solutions, you're not just protecting products – you're protecting your bottom line while building a more efficient and profitable operation.
Environmental Impact and Sustainability
Modern electronics packaging has stepped up to meet growing environmental challenges through sustainable foam solutions. You'll find that polyethylene foam leads the charge in sustainability, being 100% recyclable and generating minimal VOC emissions. When you're protecting sensitive electronics, you're also safeguarding the environment through foam's efficient material usage and waste reduction properties.
Aspect | Benefit | Impact |
---|---|---|
Material | 100% Recyclable | Reduces landfill waste |
Production | Minimal VOCs | Improves air quality |
Usage | Customizable sizing | Decreases material waste |
Durability | Long-lasting | Less frequent replacement |
Efficiency | Lower transport weight | Reduced carbon footprint |
You'll appreciate how closed-cell polyethylene foam maintains its structural integrity without absorbing water or chemicals, making it ideal for multiple uses. Its thermal insulation properties help you save energy by reducing the need for additional temperature control. When you're choosing packaging materials, you're supporting sustainable practices through foam's compatibility with eco-friendly recycling technologies. These materials align perfectly with global environmental standards like RoHS and REACH, ensuring you're meeting both protection and sustainability goals in your electronics packaging.
Material Testing and Certification
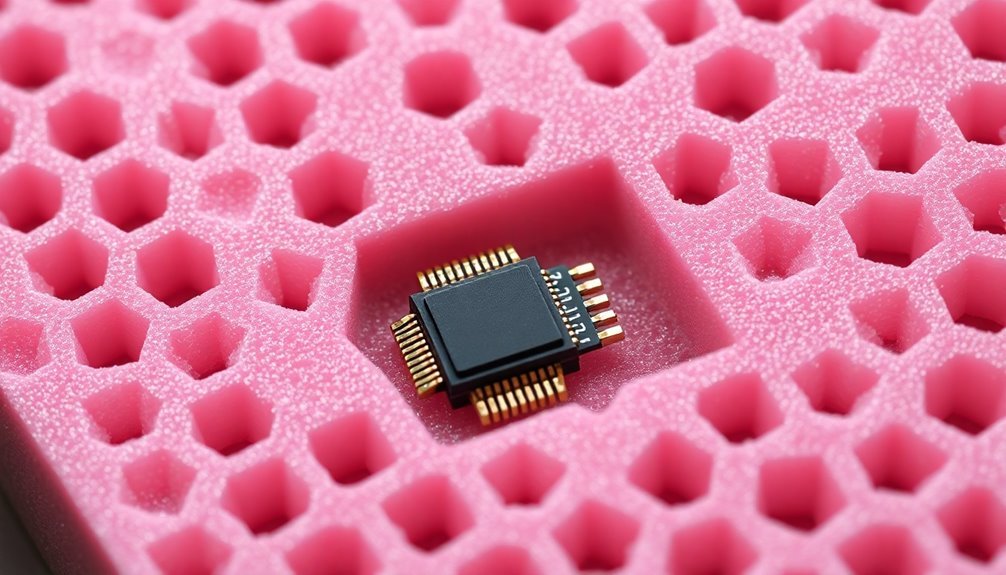
Material testing and certification complement sustainable packaging by validating that environmentally friendly solutions also meet rigorous performance standards. When you're protecting sensitive electronics, you'll need foam materials that have passed thorough testing under ASTM D3574 for physical properties and ASTM E84 for flame resistance. These standards, combined with ISO/IEC 17025 accreditation, verify that your protective foam meets international quality benchmarks.
Your electronics deserve protection that's been verified through:
- Tensile and tear resistance testing, which confirms the foam won't break or tear when protecting your devices during rough handling or shipping
- Compression and resilience testing, which certifies the foam maintains its protective shape even after repeated impacts and pressure
- ESD protection verification, which validates the foam's ability to prevent static electricity from damaging your sensitive components
The testing process incorporates both on-site laboratory analysis and specialized material testing facilities.
You'll receive detailed certificates of analysis upon request, documenting your foam's compliance with military specifications and quality management standards under ISO 9001:2015.
This rigorous testing framework guarantees superior performance for electronic component protection.
Applications Across Industries
Throughout the electronics industry, protective foam solutions play a vital role in safeguarding sensitive components during manufacturing, storage, and shipping. You'll find polyurethane and polyethylene foams at the forefront of electronics protection, offering superior impact resistance and ESD prevention.
Application Area | Key Benefits |
---|---|
Product Storage | Anti-static properties prevent ESD damage to components |
Transportation | Custom inserts provide shock absorption during shipping |
Manufacturing | Sound and thermal insulation for sensitive processes |
Quality Control | Non-abrasive surfaces protect delicate components |
Workspace Safety | ESD protection in handling and assembly areas |
When you're working with sensitive electronic components, you'll appreciate how these foam solutions can be customized to fit your specific needs. They're particularly effective in creating multilayer packaging that protects against multiple hazards simultaneously. You'll notice that modern foam materials don't just protect – they're also helping meet sustainability goals through their recyclable nature. For manufacturing facilities, these materials are transforming workspaces by providing both protection and functionality. Whether you're shipping delicate circuits or storing valuable components, foam materials certified to standards like EIA-541 guarantee your electronics remain safe and functional.
Frequently Asked Questions
How Long Does Anti-Static Foam Protection Typically Last Before Needing Replacement?
You'll typically get about 3 years of protection from anti-static foam, though environmental factors can affect this. For maximum safety, you should replace standard static dissipative packaging materials annually to maintain effective protection.
Can Foam Materials Interfere With Wireless Signals or Device Connectivity?
Most standard foam materials won't substantially interfere with your wireless signals. However, you'll want to avoid foams with metal backing or high conductivity, as these can block or weaken device connectivity and WiFi transmission.
What Temperature Ranges Can Protective Foam Materials Safely Withstand?
You'll find protective foams offer diverse temperature ranges: Silicone foam handles -67°F to 392°F, Neoprene works from -65°F to 250°F, Viton withstands -10°F to 400°F, and ESD foam operates between 14°F to 185°F.
Are There Specific Cleaning Methods Recommended for Maintaining Protective Foam Materials?
You'll want to use gentle solvents like isopropyl alcohol, soft cloths, and spot cleaning techniques. Don't soak the foam or use harsh chemicals. Always dry clean when possible to maintain protective properties.
How Do Extreme Humidity Conditions Affect Foam's Protective Properties?
When humidity's too low (<30%), your foam loses its static-dissipating abilities. Too high (>60%), and it can degrade. You'll get the best protection when you maintain humidity between 40-60% for ideal foam performance.
In Summary
You'll find top US foam provides superior protection for your sensitive electronics through proven anti-static properties and customizable solutions. It's worth investing in quality foam that meets rigorous testing standards and offers long-term cost savings. Whether you're storing microchips or shipping delicate components, you're making a smart choice by selecting materials that protect against static discharge while maintaining environmental responsibility.
Leave a Reply