You'll find top US foam manufacturers protect sensitive electronics better through advanced closed-cell technology and specialized anti-static properties. Their foam solutions feature pure nitrogen gas enhancement and customizable designs that perfectly cushion your devices against impacts and vibration. Leading manufacturers meet strict quality standards like ISO 9001 and EIA-541, ensuring consistent protection that prevents up to 99.9% of static discharge damage during shipping and handling. From precision-molded inserts to sustainable materials, these innovative foam technologies offer extensive safeguards that keep your valuable electronics secure. Discover how these cutting-edge protection methods work together to maximize your equipment's safety.
Advanced Foam Protection Technologies
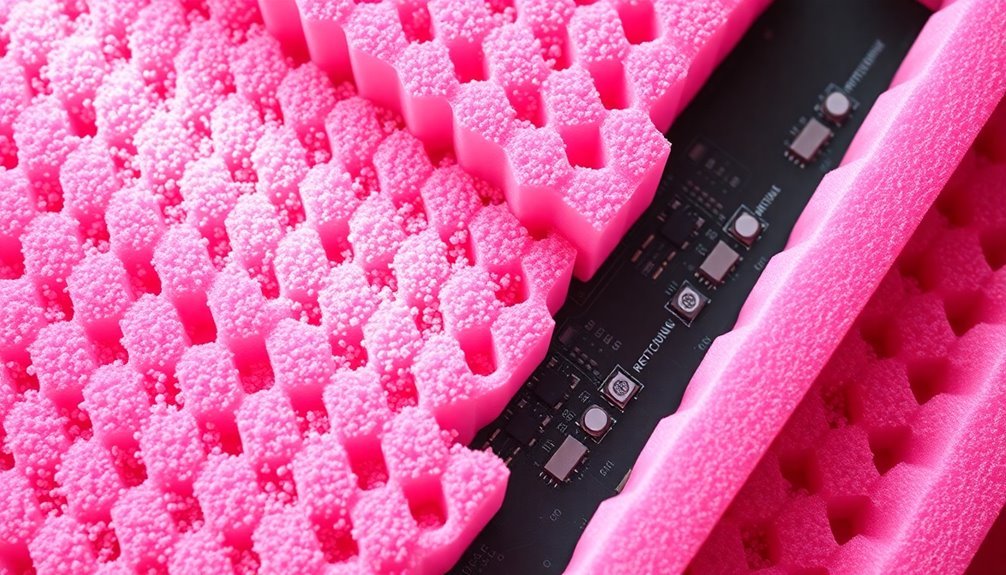
In recent years, foam protection technologies have revolutionized how we safeguard sensitive electronics. You'll find that closed-cell foams deliver exceptional cushioning and shock absorption, making them ideal for protecting your valuable devices.
When you're looking for reliable protection, materials like polyurethane, polyethylene, and EVA foams stand out due to their resilience and lightweight properties. These materials are enhanced with pure nitrogen gas during manufacturing to ensure optimal performance.
You can count on advanced solutions like ETHAFOAM cushion packaging to provide superior anti-static protection while guarding against impact and vibration. The innovative AiroFoam technology takes protection even further by using intelligent molecules that form strong hydrogen bonds upon impact.
You'll appreciate how these materials create a snug fit around your electronic components, effectively cushioning them from mechanical shocks.
What makes these foams particularly effective is their anti-static properties, which prevent ESD damage during manufacturing, storage, and transport. They're also instrumental in thermal management, ensuring your electronics perform efficiently under various temperature conditions.
When you need to protect sensitive components, you can choose from different foam densities, firmness levels, and flexibility options, all customized to meet your specific performance requirements in the electronics industry.
Static Control Material Benefits
Building on these advanced foam technologies, static control materials offer a powerful set of benefits that you'll find invaluable for protecting electronic components. You'll notice immediate improvements in ESD protection, as these materials effectively prevent static discharge damage to your sensitive electronics during handling and storage.
The safety benefits can't be overlooked – you're reducing workplace hazards by minimizing the risk of dangerous static discharges that could ignite flammable materials or cause accidents. Your employees will appreciate the protection from static shocks, while conductive foams guarantee safer handling of components. These materials provide a reliable conductive surface that consistently dissipates static charge.
You'll see a direct impact on product quality, as static control materials maintain the integrity and reliability of your electronic components. They're preventing performance degradation and premature failures that could affect your product's reputation.
The cost benefits are substantial – you're reducing warranty claims, minimizing costly repairs, and avoiding production downtime. By implementing proper static control materials, you'll protect your investment in electronic components while improving manufacturing efficiency.
Your bottom line benefits from fewer replacements, reduced rework requirements, and better overall cost management throughout your production process.
Quality Standards and Certifications
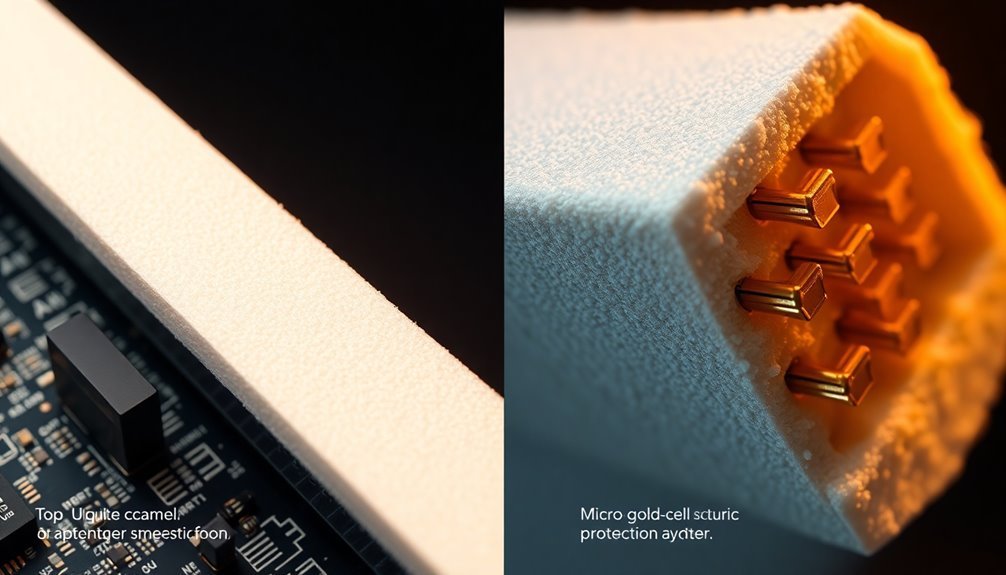
A thorough set of quality standards and certifications governs the production of protective foams for electronics. When you're choosing foam protection for your sensitive components, you'll find that top US manufacturers adhere to multiple critical certifications, including ISO 9001 for quality management and EIA-541 for electrostatic protective materials.
You'll benefit from strict military standards like MIL-I-45208A and MIL-Q-9858A, which guarantee rigorous inspection and quality control processes. These standards work alongside UL and ULC approvals to verify the foam's safety and compliance. The cushioning and shock absorption capabilities of closed-cell foams make them essential for protecting sensitive electronics during transport.
The quality control measures include quarterly and yearly audits, thorough material testing, and continuous process improvement through ISO9001 alignment.
The foam's material standards are equally impressive. You're getting anti-static properties with density ranges from 2 to 6 lbs. pcf in anti-static polyurethane foams.
The EVAZOTE process, using pure nitrogen gas, creates superior closed-cell crosslinked foams. Whether you need closed-cell foam for bulky items or open-cell foam for delicate components, you'll find that each product meets strict design and manufacturing guidelines, guaranteeing consistent protection for your electronic equipment.
Custom Electronics Packaging Solutions
When selecting protective foam for electronics packaging, quality standards alone won't guarantee the perfect fit for your specific needs. Custom electronics packaging solutions require careful consideration of your product's unique characteristics, shipping conditions, and protection requirements.
You'll need to evaluate several critical factors to guarantee optimal protection for your sensitive electronics:
- Material selection between anti-static, non-abrasive, or conductive foam based on your product's electromagnetic sensitivity
- Precise cushioning calculations that account for product weight, fragility, and expected shipping conditions
- Custom-molded designs that perfectly match your product's dimensions and provide secure placement
- Multilayer configurations that optimize space while maintaining maximum protection
The fast turnaround from New Hampshire facilities ensures your packaging solutions are delivered efficiently. Your custom packaging solution should incorporate specific design elements based on thorough fragility and vibration assessments. Whether you're shipping delicate medical devices or complex computer components, you'll benefit from tailored foam inserts that account for both protection and practicality.
The combination of proper material choice and engineering considerations guarantees your electronics arrive safely at their destination. With options like polyurethane for precise molding and polyethylene for moisture resistance, you can create packaging that addresses your exact specifications.
Environmental Impact and Sustainability
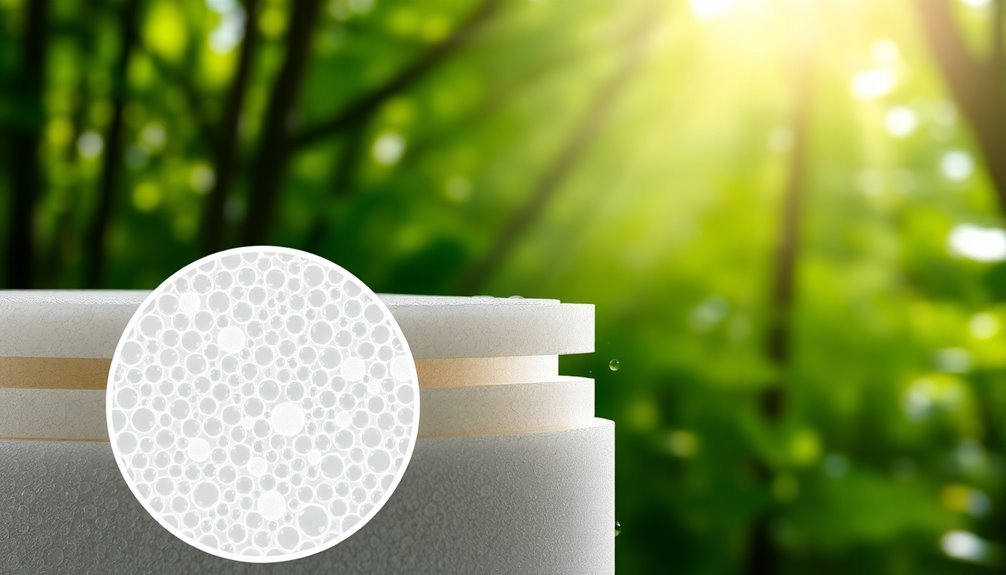
The environmental impact of foam packaging for electronics poses significant challenges for sustainability-conscious businesses. Traditional foam packaging contributes to landfill accumulation, ocean pollution, and greenhouse gas emissions during production and transportation. With 5.3 billion devices discarded annually, the packaging waste problem continues to grow exponentially.
You'll find several sustainable alternatives that are transforming the electronics packaging industry. Cornstarch-based foam offers a biodegradable solution that dissolves in water, while mushroom packaging provides a non-toxic option. You can also consider bamboo packaging, which regenerates quickly and offers excellent protection for your sensitive electronics.
When you choose sustainable foam packaging, you'll benefit from reduced environmental impact and improved brand reputation. You're not just protecting your electronics; you're also complying with environmental regulations and potentially saving costs through more efficient resource use.
To implement sustainable packaging effectively, you'll want to focus on design optimization and supply chain efficiency. You can incorporate QR codes to educate your customers about proper recycling practices, and utilize renewable energy sources in your production processes.
Frequently Asked Questions
How Long Does Anti-Static Foam Maintain Its Protective Properties?
You'll find anti-static foam's protective properties typically last 2-5 years, but it's heavily dependent on your storage conditions, handling practices, and the specific foam type. Regular testing helps guarantee continued effectiveness.
Can Foam Packaging Be Safely Reused After Exposure to Extreme Temperatures?
You shouldn't reuse foam packaging that's been exposed to extreme temperatures, as it may have suffered structural damage and chemical changes. Check for signs of warping, discoloration, or brittleness before considering reuse.
What Is the Average Cost Difference Between Standard and Anti-Static Foam?
You'll typically find anti-static foam costs twice as much as standard foam due to added static-protection agents. For example, if standard foam costs $50, you'd expect to pay around $100 for anti-static foam.
Are There Special Storage Requirements for Unused Electronic Protection Foams?
Yes, you'll need to store your electronic protection foams in controlled indoor environments, keeping them sealed, at recommended temperatures, and away from direct sunlight. Regular inspections and clean handling equipment are also essential.
How Quickly Can Custom Foam Inserts Be Manufactured for Urgent Orders?
You'll typically receive custom foam inserts in 3-4 weeks, but urgent orders might be completed faster. Be aware that complexity, material availability, and design approval can affect your production timeline.
In Summary
You'll find Top US Foam offers unmatched protection for your sensitive electronics through advanced static control materials and custom packaging solutions. Their products meet rigorous quality standards while maintaining eco-friendly practices. Whether you're shipping delicate components or storing valuable devices, you can trust their foam technology to defend against static, shock, and environmental damage. It's the smart choice for safeguarding your electronic investments.
Leave a Reply