You'll effectively control static electricity with these 7 essential anti-static tools: evaporative humidifiers for consistent moisture levels, high-precision dry fog systems for ultra-fine water distribution, wrist straps for personal grounding, ESD-protective shoes with regular testing capability, antistatic mats for workstation protection, digital hygrometers for accurate humidity monitoring, and multi-zone humidity control systems for facility-wide management. These tools work best when humidity levels stay between 40-60% relative humidity, preventing equipment damage and protecting sensitive electronics. Understanding how to combine these solutions will maximize your static protection strategy.
Understanding Static and Humidity Basics
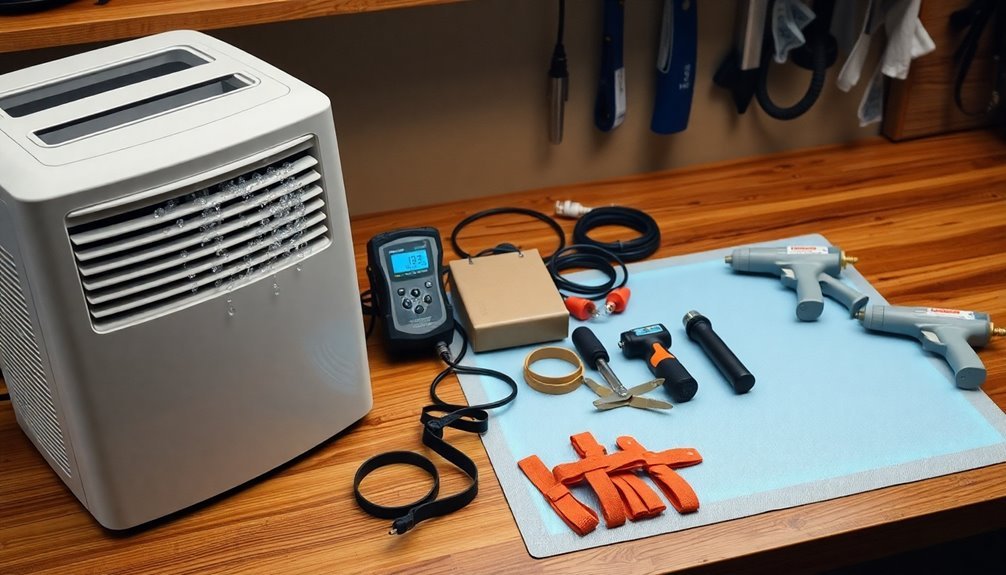
In today's electronically-driven world, understanding the relationship between static electricity and humidity is essential for maintaining safe environments. When you're working with sensitive electronic equipment, you'll find that static electricity poses a substantial risk, especially in low-humidity conditions. Evaporative humidifiers can effectively maintain consistent humidity for optimal static control.
Static charges build up when relative humidity drops below 40%, creating potential hazards for your devices and equipment.
Humidity acts as a natural conductor, helping to earth any static charges that might develop. When moisture levels in the air increase above 55% relative humidity, you're creating ideal conditions for preventing static buildup. This is why you'll experience more static shocks during winter months when the air is typically drier and colder.
The relationship between static and humidity works through a simple principle: moisture allows electrons to flow freely between materials. When you maintain humidity levels between 40-60% RH, you're markedly reducing the risk of static discharge.
However, you'll need to be careful not to exceed 65% relative humidity, as excessive moisture can lead to condensation and potential equipment damage through rust or corrosion.
Dry Fog Systems
Among the most advanced solutions for humidity management, dry fog systems stand out for their precision and efficiency. These systems produce ultrafine water droplets of 4.2 microns or less, allowing you to achieve precise humidity levels up to 99% without causing wet spots on surfaces or equipment. The smart nozzle technology ensures consistent adhesion while minimizing droplet cohesion for optimal performance.
You'll find that dry fog technology offers significant advantages over traditional humidification methods, particularly in electronics manufacturing and industrial settings. The system reduces operating costs by up to 68% compared to steam systems, while cutting CO2 emissions by 70%.
Feature | Benefit |
---|---|
Droplet Size | 4.2 microns or less, preventing surface wetting |
Energy Usage | 68% less than traditional steam systems |
Safety Rating | Suitable for explosion hazard areas |
Temperature Range | Functions down to -60°C with protection |
When you're managing static electricity in your facility, dry fog systems provide exceptional control through consistent humidity maintenance. The technology's modular design allows for flexible installation, and you can choose between pneumatic systems using compressed air or hydraulic systems for lower operating costs. For facilities requiring precise environmental control, dry fog technology delivers superior performance while conserving water and energy resources.
Industrial Humidification Solutions
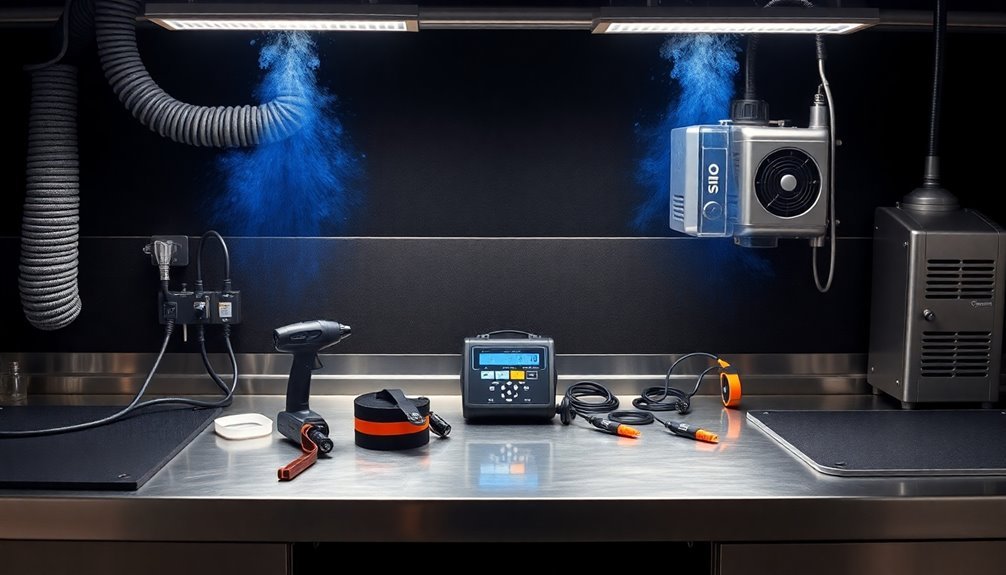
You'll find that advanced spray control systems offer precise management of humidity levels through sophisticated nozzle arrangements and automated monitoring.
Dry fog atomization provides superior benefits by creating ultra-fine water droplets that evaporate instantly, preventing wetness while maintaining desired humidity levels.
Climate zone distribution methods let you target specific areas within your facility, ensuring ideal humidity levels exactly where you need them most. These systems can reduce energy consumption by up to 70 percent compared to traditional steam humidification methods.
Advanced Spray Control Systems
Modern industrial humidification solutions frequently rely on advanced spray control systems that combine precision engineering with flexible functionality. You'll find these systems particularly effective in managing static electricity through precise humidity control at 55%RH, which is essential for manufacturing environments.
The systems feature high-precision nozzles that deliver uniform droplets between 10-40 microns without compressed air, while oil-free hydraulic pumps maintain water pressure at 50-70 bar. Installation can be completed with zero production downtime while keeping existing operations running smoothly.
You can choose from single-zone to multi-zone control options, with humidifying capacities ranging from 15 to 1200 litres per hour to match your specific needs.
Built-in safety hygrostats guarantee your operation stays within controlled parameters, while the patented pump technology recirculates water every 24 hours to reduce contaminants.
You'll appreciate the economic benefits too – these systems offer up to 60% lower capital costs and 90% reduced operating expenses compared to conventional options. When you integrate reverse osmosis, you'll extend nozzle life and minimize maintenance requirements by eliminating mineral buildup.
This combination of precision control and cost-effectiveness makes these spray systems an ideal choice for various industrial applications, from packaging to electronics manufacturing.
Dry Fog Atomization Benefits
Dry fog atomization stands out as a game-changing solution for industrial humidity management, delivering exceptional energy efficiency while maintaining precise environmental control.
The technology's precision is remarkable, as it creates ultra-fine droplets that can achieve humidity levels up to 99% without causing wet spots. You won't need high-powered pumps or compressed air, which further enhances energy savings. Advanced zone control valves provide customized humidity levels for different areas of your facility.
In sensitive industrial settings like electronics manufacturing, you can maintain ideal humidity levels above 55%RH to prevent static buildup effectively.
Your facility will benefit from targeted humidity control around hot machines, preventing localized dry air pockets that can compromise production quality.
The system's versatility makes it invaluable across various industries, from electronics and pharmaceuticals to textiles and printing. You'll notice improved worker productivity and reduced sick leave, as the system maintains relative humidity at 50% or above.
Additionally, you'll see fewer ESD-related issues and pick-and-place errors in SMT processes, ensuring consistent product quality throughout your manufacturing operations.
The technology uses 50-90% less energy and water than traditional humidification methods, cutting operating costs by up to 68% in SMT processes.
Climate Zone Distribution Methods
When designing industrial humidification systems, effective climate zone distribution demands a strategic approach to maintain consistent humidity levels across different facility areas.
You'll need to implement multiple steam distribution systems for shorter distances while ensuring precise zoning meets your specific building constraints and machinery requirements.
For ideal anti-static performance, your system should maintain humidity levels between 45% and 55% RH. The biofilm prevention measures are crucial for maintaining system hygiene and preventing contamination in water supply lines.
High-pressure water fog systems offer superior distribution capabilities while keeping both capital and operational costs lower than traditional methods. You'll want to position humidity sensors strategically after expansion and mixing zones to prevent unwanted condensation.
Consider these essential distribution methods for different climate zones:
- Grid-like nozzle systems with specialized hydraulic tubing that follow room contours for uniform coverage
- Adiabatic humidification systems utilizing hybrid humidifiers for built-in distribution distance
- Direct-steam conditioning through four-step processes for enhanced efficiency in larger zones
- Localized spray systems targeting heat-generating machinery areas
You can optimize your distribution by incorporating variable-speed pump units and reverse osmosis systems, which will extend nozzle life while eliminating dusting issues commonly found in industrial settings.
Personal Static Control Equipment
Although managing static electricity requires multiple tools, personal static control equipment serves as the primary line of defense against electrostatic discharge (ESD).
You'll find that wrist straps are essential when working with sensitive electronics, as they ground you and prevent static buildup that could damage components. These come in both wired and wireless options to suit your specific needs.
Your footwear choices are equally important, with ESD shoes and testers ensuring proper grounding as you move through your workspace. You can install wall-mounted or free-standing testers to verify your footwear's effectiveness regularly.
To create a thorough static-controlled environment, you'll need antistatic mats and flooring, which work in conjunction with your other personal equipment. Maintaining relative humidity above 40% helps these tools work more effectively by naturally dissipating static charges.
Don't forget about protective apparel and accessories. You'll want to wear antistatic clothing, gloves, and finger cots, especially in high-risk environments like electronics manufacturing facilities.
These items help maintain consistent static control while handling sensitive components. When you combine all these elements – from wrist straps to ESD apparel – you're creating a complete personal static control system that effectively protects both you and your sensitive electronic equipment.
Measuring Humidity Effectively
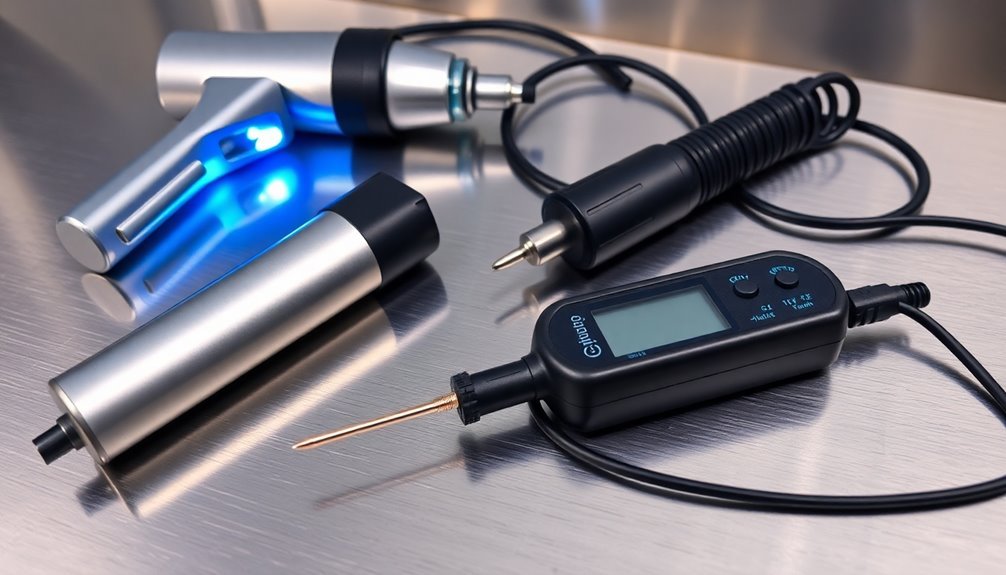
You'll find various humidity monitoring devices available for static control, including digital hygrometers, psychrometers, and capacitive sensors that offer different levels of accuracy and functionality.
For ideal measurement, you should place your sensors at workstation height and in multiple locations throughout your facility to account for variations in humidity levels.
When selecting sensor locations, you'll want to avoid areas near doors, windows, or HVAC vents that could give misleading readings of your facility's true humidity conditions.
Humidity Monitoring Device Types
The accuracy of humidity monitoring hinges on selecting the right type of sensor for your specific needs. You'll find that capacitive sensors dominate the market, accounting for about 75% of humidity measurement applications, particularly in HVAC systems and weather stations.
Their high accuracy and long-term stability make them ideal for professional anti-static control.
If you're working with budget constraints, resistive humidity sensors offer a cost-effective alternative while still providing reliable measurements for basic anti-static applications. Thermal sensors excel in industrial settings where you need quick response times and accurate readings at high humidity levels.
- Capacitive sensors achieve ±2-3% accuracy using a hygroscopic material between conductive plates
- Resistive sensors measure humidity through changes in electrical resistance, requiring simple readout circuits
- Thermal sensors use dual thermistors to detect moisture content through thermal conductivity differences
- Specialized options like optical and quartz crystal sensors offer unique solutions for specific applications
When choosing your humidity monitoring device, consider the operating environment, required accuracy, and response time needs. For most anti-static applications, you'll find capacitive sensors provide the best balance of performance and reliability.
Ideal Placement For Sensors
Placing humidity sensors strategically guarantees accurate measurements and reliable anti-static control. You'll need to think about three main mounting scenarios: wall, duct, and outdoor installations, each requiring specific placement criteria for best performance.
For wall-mounted sensors, install them 4-6 feet above the floor in areas with good air circulation, away from heat sources and direct sunlight. When mounting in ducts, position the probe at the duct's center, avoiding fans, coils, and dampers that could affect readings. For outdoor installations, choose a sheltered north-facing location under an eave to prevent sun-heated air from skewing measurements.
Mounting Type | Ideal Height | Key Considerations |
---|---|---|
Wall Mount | 4-6 feet | Away from heat sources, sunlight |
Duct Mount | Center of duct | Avoid fans, coils, dampers |
Outdoor | Under eave | North-facing, sheltered location |
Remember to use multiple sensors in large spaces and regularly calibrate duct-mounted sensors annually. Keep sensors away from moisture sources, fumes, and vibration-prone areas. For effective anti-static control, make sure your sensor placement allows for quick adaptation to environmental changes while providing representative measurements of the area's conditions.
Large Space Humidification Tools
Inside large industrial and commercial spaces, maintaining proper humidity levels requires specialized humidification systems that can handle vast areas up to 3,700 square feet. You'll find several types of systems designed to combat static electricity while improving overall production efficiency and worker safety.
For ideal anti-static control, you'll want to take into account these primary humidification tools:
- Ultrasonic systems that use piezoelectric transducers to create a fine mist, perfect for sensitive electronic manufacturing areas
- High-pressure nozzle systems that deliver precise water mist directly into the airstream, ideal for textile and printing facilities
- Wetted media assemblies for industrial applications requiring consistent humidity levels
- Hybrid systems that combine multiple functions and offer enhanced control capabilities
You'll need to maintain these systems regularly by cleaning filters and using pre-treated water to prevent mineral buildup.
When selecting your humidification solution, focus on energy-efficient options that include automatic dry-out modes and water refill indicators. These features help prevent over-humidification while maintaining the ideal 50-60% relative humidity range needed for static control and ideal production conditions.
Localized Static Prevention Methods
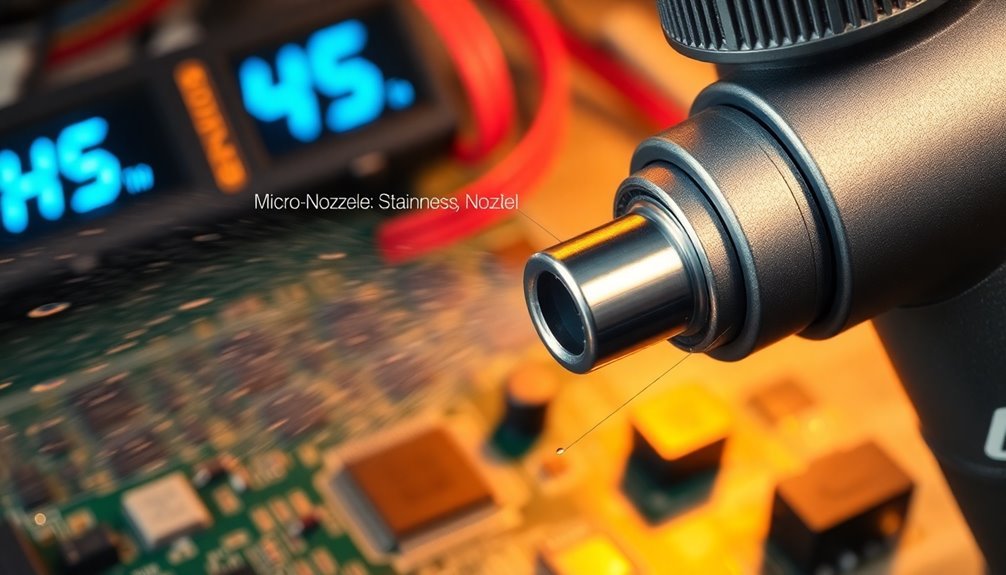
Modern static elimination requires precise control at specific points where static charges build up most intensely. You'll find that high-performance ionizers can neutralize static in just 0.5 seconds, covering areas up to 3 meters with instant verification through visual indicators and alarms.
Device Type | Coverage Area | Key Features |
---|---|---|
High-Performance Ionizers | Up to 3m | 0.5-second elimination, visual indicators |
Micro Static Eliminators | 600×1500mm | High-temp resistant, ultra-small heads |
Bar-Type Eliminators | Room-wide | Low-frequency ion generation |
For precise control in tight spaces, you'll want to evaluate micro static eliminators. They're ideal when you need targeted static elimination at specific points, featuring ultra-small heads that can operate in temperatures up to 80°C. In production environments, you can mount these compact units flexibly while monitoring their performance through built-in diagnostics.
For larger areas, you'll benefit from bar-type static eliminators that effectively prevent static build-up across wide spaces. They're particularly useful in warehouse settings where you're storing electronic parts or managing film materials. These systems work effectively on both conductive and non-conductive surfaces, making them versatile for various manufacturing applications.
Advanced Atomizing Technologies
You'll find advanced atomizing technologies offer remarkable control over droplet size through their crab claw nozzle designs, producing particles as small as 5-7.5 μm for ideal static prevention.
The strategic placement of nozzle distribution systems guarantees uniform coverage across your facility, with quick-connect options making installation and maintenance straightforward.
Modern mist generation leverages multi-stage atomization principles to deliver superior humidity management while maintaining energy efficiency through low gas and water consumption.
Precision Droplet Size Control
The precise control of droplet size stands at the forefront of advanced atomizing technologies, where adjustments to nozzle types, orifice dimensions, and application pressures determine the exact formation of liquid particles.
Pulse-width modulation (PWM) sprayers offer exceptional control through electronically actuated solenoid valves, maintaining consistent flow rates across varying speeds while minimizing overlap.
When you're managing humidity levels, you'll need to take into account specific droplet sizes for ideal performance. Modern atomizing nozzles can effectively produce droplets ranging from 20 to 200 microns, perfect for humidification and cooling applications.
Here's what you can expect from precision droplet control:
- Ultra-fine droplets accelerate air-liquid interaction, maximizing evaporative cooling efficiency
- Compressed air entrainment creates micron-level spray patterns for superior surface coverage
- Flow-focusing microdroplet generators deliver monodisperse droplets at extremely small sizes
- Closed-loop control systems guarantee consistent droplet formation in microfluidic devices
You can measure these droplet sizes using laser diffraction in low-speed wind tunnels, guaranteeing your humidity management system operates at peak efficiency. This precision becomes particularly vital when you're dealing with anti-static applications where consistent moisture levels are essential.
Nozzle Distribution Systems
Through strategic placement and advanced engineering, nozzle distribution systems form the backbone of effective atomizing technologies. You'll find these systems particularly effective in managing static electricity through precise humidity control, whether you're operating in industrial, commercial, or agricultural environments.
When you're selecting a nozzle distribution system, you'll need to take into account both air and water supply requirements. Air atomizing nozzles offer superior control but require both utilities, while high-pressure systems might better suit your needs if compressed air isn't available.
You'll achieve the best results by positioning nozzles to create wide, uniform droplet distribution patterns that maximize evaporation efficiency.
Your system's effectiveness depends heavily on proper installation and environmental factors. You'll want to account for air movement patterns, temperature variations, and ventilation systems when planning nozzle placement.
Modern systems come with sophisticated controls that let you adjust flow rates based on real-time sensor data, ensuring you maintain ideal humidity levels consistently.
For anti-static applications, you'll benefit from modular designs that allow for customization based on your space's specific requirements. These systems typically feature advanced impeller-type or air atomizing nozzles that deliver the fine droplets necessary for effective static control.
Energy-Efficient Mist Generation
Several groundbreaking advances in mist generation technology now make it possible to achieve superior humidity control while minimizing energy consumption.
Modern atomizing systems combine high-pressure operation with smart automation to deliver precise humidity levels while reducing your energy costs and environmental impact.
The integration of nanotechnology and ultrasonic humidification has revolutionized how you can generate fine mist particles. These systems produce droplets between 1-7.5 microns, ensuring ideal dispersion and rapid evaporation. You'll benefit from both the humidity control and the adiabatic cooling effect, which provides additional temperature management at no extra energy cost.
Here's what makes today's mist generation systems particularly efficient:
- Advanced atomizing nozzles that create ultra-fine particles using minimal energy input
- Smart sensors that automatically adjust output based on real-time humidity readings
- Integration with renewable energy sources to reduce operational costs
- Digital monitoring systems that enable remote control and optimization
Static-Free Workspace Design
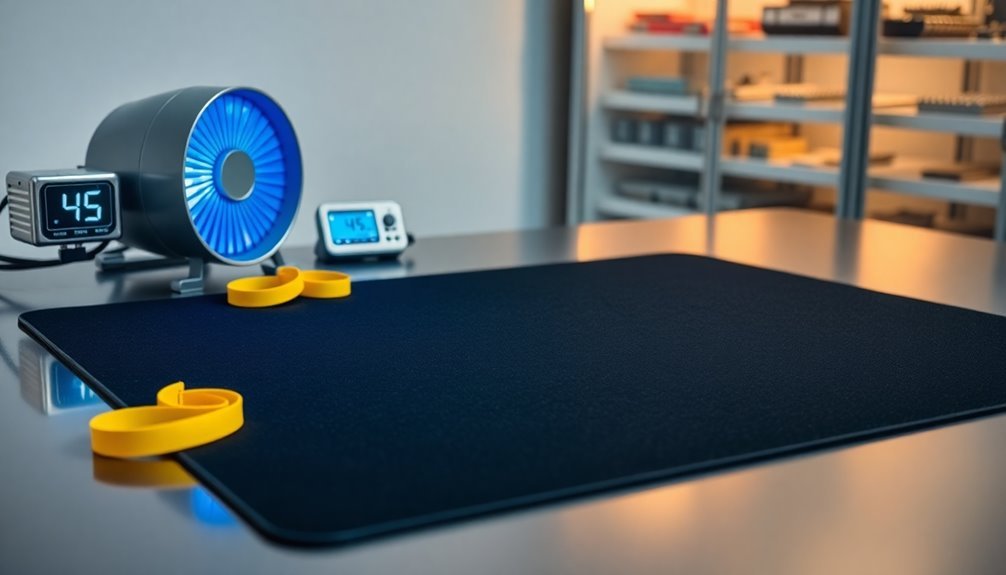
Creating an effective static-free workspace requires careful attention to both furniture selection and layout design. You'll need to avoid all-metal furniture and instead opt for specialized anti-static installations that incorporate ESD laminate surfaces and conductive flooring. When designing your workspace, make certain proper cable management and grounding systems are in place.
Element | Problem | Solution |
---|---|---|
Furniture | Metal surfaces build static | Use ESD laminate surfaces |
Flooring | Regular tiles cause friction | Install conductive pavement |
Upholstery | Standard fabrics create static | Choose antistatic materials |
You'll want to position your humidifiers strategically above or behind sensitive equipment while maintaining proper spacing for ideal moisture distribution. Install grounding devices, including wrist straps and work surface mats, at each workstation. Don't forget to secure all grounding connections using metallic crimps for reliability. When selecting countertops, choose static-reducing materials and make certain they're properly connected to your grounding system. Your wiring installations should follow anti-static guidelines, with cables properly shielded and grounded. Remember to incorporate humidity control solutions into your design, as maintaining appropriate moisture levels is vital for static prevention.
Environmental Monitoring Systems
Modern environmental monitoring systems serve as the backbone of effective static control and humidity management. They are equipped with sophisticated temperature and humidity sensors that continuously track environmental conditions in real-time. By integrating with your HVAC systems, they provide automated responses to maintain the best conditions for static control.
For effective implementation, you'll want to focus on these critical monitoring components:
- Temperature sensors (RTDs and thermistors) that offer precise measurements within ±0.5°C accuracy
- Capacitive humidity sensors that provide reliable relative humidity readings between 30-70%
- Cloud-based monitoring platforms that deliver instant alerts when conditions deviate from set parameters
- Data analysis tools that help you identify patterns and refine your humidity control strategy
You should position sensors strategically throughout your workspace, particularly in areas prone to static buildup. Consider implementing redundant sensors in critical zones to guarantee continuous monitoring even if one sensor fails.
For maximum effectiveness, you'll need to maintain regular calibration schedules and implement proper maintenance protocols. Remember to choose a system that's scalable and can integrate with your existing infrastructure while meeting any relevant regulatory requirements.
Maintenance Best Practices
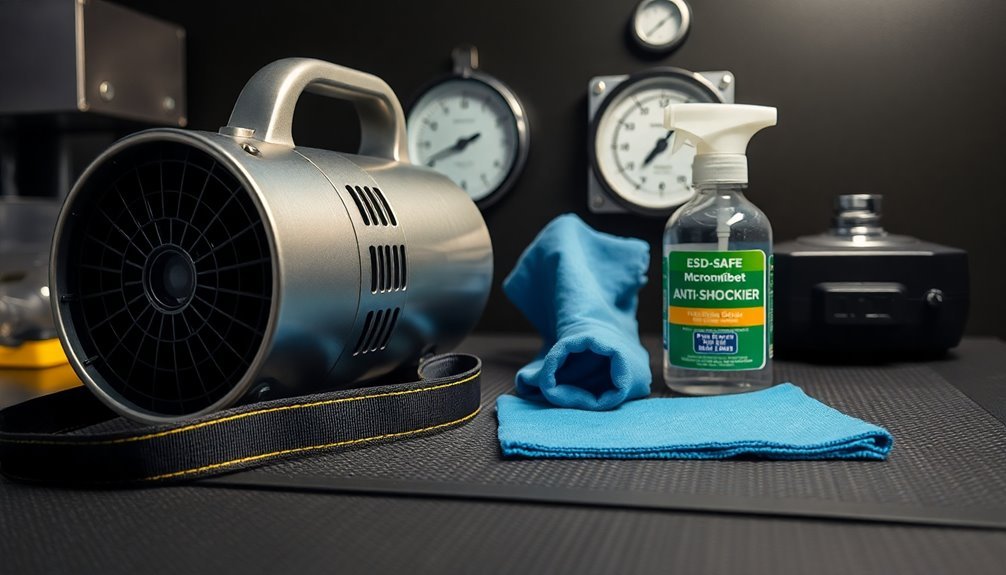
Diligence in maintaining anti-static equipment guarantees peak performance and longevity of your humidity management systems.
You'll need to establish a regular maintenance schedule that includes inspecting humidifier systems, cleaning filters, and checking humidity sensors for accuracy. It's vital to pay special attention to atomizing nozzles, keeping them free from debris to prevent clogging.
When performing maintenance, you should use distilled or filtered water in your humidifiers to minimize mineral buildup. If you're using water spray systems, monitor them closely for wetting issues and consider upgrading to dry fog systems like AKIMist for better performance.
Don't forget to verify that your humidifiers are properly integrated with existing HVAC systems to avoid operational conflicts.
To maintain ideal humidity levels above 55% RH, you'll need to regularly calibrate your sensors and check for dry air pockets, especially near heat-generating equipment.
When troubleshooting, start by confirming proper installation and configuration of all system components. If you notice static issues persisting, inspect your static-dissipative materials and consider upgrading to static-hardened electronics for sensitive applications.
Cost-Effective Static Control Solutions
Implementing cost-effective static control solutions doesn't require breaking your budget. You'll find various affordable options that effectively manage static electricity while maintaining ideal humidity levels in your facility.
AC anti-static bars and power units offer economical alternatives for basic static elimination needs, while passive solutions provide reliable performance for dust removal and cleaning tasks.
For thorough static control, consider these proven cost-effective approaches:
- Install direct room humidifiers to maintain 55% relative humidity throughout large spaces, effectively preventing static build-up without complex infrastructure.
- Deploy localized spray systems near heat-generating equipment to create targeted humidity zones, reducing overall system costs while maintaining effectiveness.
- Utilize ceiling-mounted atomizing nozzles for efficient humidity distribution, providing coverage exactly where it's needed.
- Implement basic AC anti-static bars for immediate static neutralization in less demanding applications.
When selecting solutions, focus on industry-specific tools that match your exact needs. For example, if you're in plastics manufacturing, passive neutralization systems can effectively address process control issues.
In printing environments, combining humidification systems with static elimination tools provides ideal results while keeping costs manageable.
Frequently Asked Questions
Can Static Electricity Affect Wi-Fi and Cellular Signals in Industrial Spaces?
While static electricity won't directly affect your Wi-Fi and cellular signals, it can damage your networking equipment that transmits these signals. You'll want to protect your devices from electrostatic discharge in industrial spaces.
How Quickly Does Static Electricity Dissipate After Installing Humidity Control Systems?
You'll notice static charges dissipate within minutes to hours after reaching 40-60% relative humidity. However, the exact time depends on your initial charge levels and environmental conditions in your space.
Do Air Purifiers Interfere With Industrial Humidification Systems?
You'll find that air purifiers generally don't interfere with industrial humidification systems. However, you should maintain proper spacing between devices and guarantee your purifier's sensors aren't affected by water droplets from humidifiers.
What Color Indicators Show Static Buildup on Different Material Surfaces?
You'll notice black or dark colors indicate conductive materials, clear/transparent allows visual inspection, and pink/red tints show general antistatic properties. These colors help you identify static-protective materials in your workspace.
Can Humidity Control Systems Trigger Smoke Detectors in Manufacturing Facilities?
Yes, your humidity control systems can trigger smoke detectors if they create rapid moisture changes or heavy airflow. You'll need proper placement and calibration of both systems to prevent false alarms in your facility.
In Summary
Managing static and humidity doesn't have to be complicated. You'll find the right solution by combining these anti-static tools based on your specific needs. Whether you've chosen dry fog systems for large spaces or personal static control equipment for smaller areas, remember to monitor conditions regularly and maintain your equipment. With proper implementation and consistent maintenance, you'll create a static-free environment that protects both equipment and productivity.
Leave a Reply