You can slash your protective packaging costs by implementing five proven strategies. First, conduct regular audits to identify waste and inefficiencies in your current packaging process. Second, switch to sustainable materials like corrugated boxes and biodegradable options, which often cost less than traditional materials. Third, optimize package dimensions by using right-sized boxes and padded envelopes for smaller items. Fourth, streamline your handling processes by reorganizing workspace layout and consolidating shipments. Fifth, automate packaging operations where possible to reduce labor costs and improve consistency. These strategies can help you achieve 30-50% in packaging savings when properly executed.
Audit Your Packaging Methods
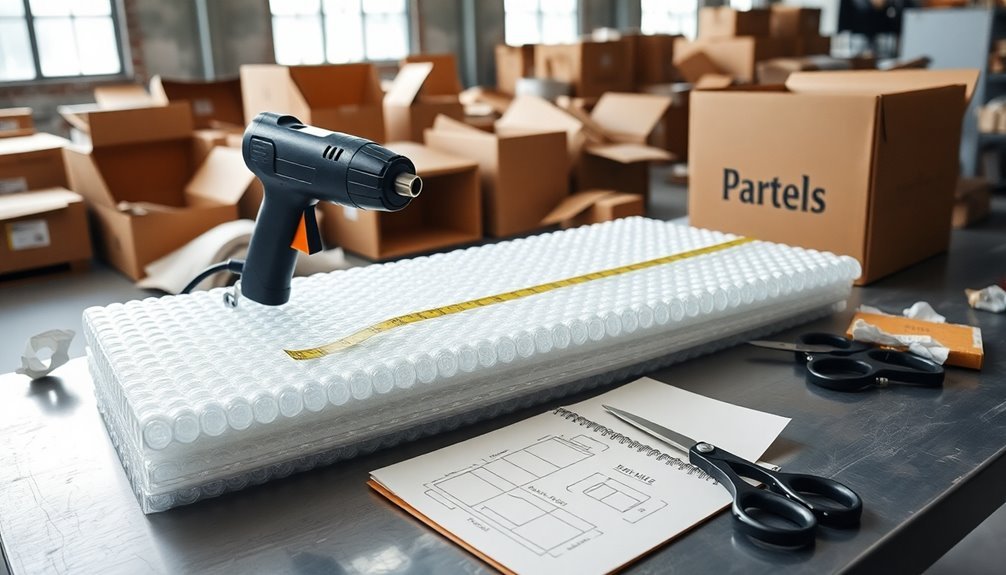
A thorough packaging audit can uncover significant cost-saving opportunities that you might be missing. Start by scheduling annual audits of your packaging areas, taking photos and documenting your current processes.
You'll want to review these findings with your team to identify potential improvements and analyze your existing inventory for packaging similarities. Down gauging materials can lead to substantial savings on packaging materials while maintaining product protection.
During your audit, look closely at how your staff uses filler materials. Are they following recommended practices with paper, bubble packs, and peanuts? Check if you're using excessive materials or if certain products could manage with lighter packaging.
Don't forget to examine your warehouse layout to guarantee optimal storage of packing supplies and maximum efficiency.
Consider standardizing your packaging wherever possible. You can streamline operations by implementing uniform box sizes for similar products and consolidating packaging materials to reduce variety.
When auditing, verify your shipping classifications to avoid overpayment, and group rarely used packing supplies to minimize waste.
If you're shipping durable goods, explore reusable packaging options or consider partnering with companies that can repurpose your excess packaging materials, reducing both costs and environmental impact.
Choose Sustainable Material Options
Building on your audit findings, sustainable packaging materials offer both environmental benefits and potential cost savings. You'll find that biodegradable options like cellulose, cornstarch, and mushroom mycelium packaging can replace expensive synthetic materials while meeting your protection needs. Corrugated boxes can be recycled up to 10 times to create new packaging materials.
These alternatives often cost less in bulk and can help you avoid environmental penalties or fees.
Consider implementing recyclable materials like glassine packaging or PLA materials, which don't just reduce your environmental impact but can also lower your disposal costs.
Smart packaging designs using cardboard and recycled materials can substantially cut your expenses while maintaining product safety. You'll also benefit from optimized packaging designs that eliminate waste and unnecessary materials.
For specialized products, look into innovative solutions like pressed hay for fragile items or bamboo combined with banana leaves for local shipping. These natural alternatives often cost less than traditional materials and can enhance your brand's eco-friendly image.
If you're handling large volumes, invest in robotics and smart packaging technology to reduce labor costs and improve efficiency. Remember to factor in variable packaging costs based on your products' durability to maximize savings while maintaining protection standards.
Optimize Package Dimensions
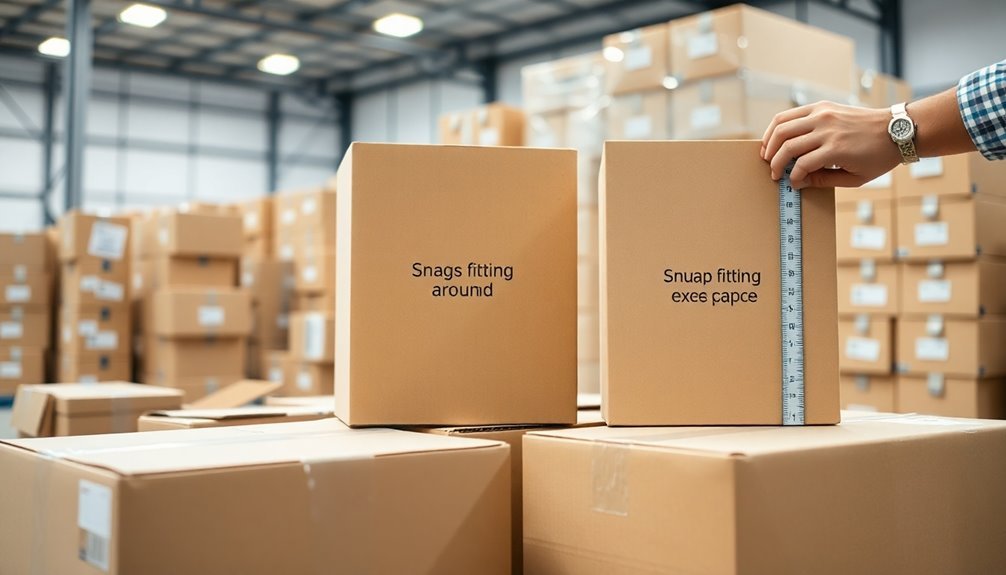
Three key factors drive your shipping costs: weight, volume, and dimensional pricing. By optimizing your package dimensions, you'll reduce material costs and minimize shipping expenses. You'll want to measure your products carefully and select boxes that provide just enough space for adequate protection without excess room.
Consider these proven dimension optimization strategies for your packaging needs:
Product Type | Box Strategy | Cost Impact |
---|---|---|
Small Items | Use padded envelopes | Save 30-50% on materials |
Multiple Products | Consolidate into one box | Reduce per-unit shipping |
Fragile Items | Custom-fit packaging | Minimize damage claims |
Durable Goods | Simple, compact designs | Lower material costs |
Mixed Shipments | Automated size selection | Optimize space usage |
You'll find that implementing automated packaging solutions helps select the perfect box size every time. When you're shipping multiple products, maximize container space by consolidating orders where possible. If you're dealing with small items, switch to padded envelopes instead of boxes. For custom solutions, take precise measurements of your products and design packaging that eliminates unnecessary void space, reducing the need for additional fill materials. Using corrugated cardboard boxes with customized shapes and sizes ensures optimal product protection while maintaining efficient dimensions.
Streamline Handling Processes
Streamlining your handling processes delivers significant cost savings through four critical operational areas: warehouse layout, inventory control, packing procedures, and quality management.
Enhancing Warehouse Layout
Start by enhancing your warehouse layout. Place frequently used materials near packing stations and position high-demand products closer to work areas. You'll want to utilize vertical space with efficient shelving systems while ensuring proper lighting for safety and accuracy. Consider implementing U-shaped configurations to minimize travel distances between workstations.
Group similar packaging materials together to reduce search time.
Implementing Smart Inventory Management
Implement smart inventory management by adopting Just-In-Time strategies and regularly reviewing stock levels. You'll reduce waste by purchasing smaller quantities and using standardized packaging materials.
Track usage patterns to maintain ideal inventory levels without overstocking.
Simplifying Packing Procedures
Simplify your packing procedures by eliminating unnecessary steps and establishing standardized methods. You'll save time by using pre-formed packaging and minimizing line changes.
Train your staff thoroughly on efficient packing techniques to maintain consistency and speed.
Ensuring Quality Control
Don't overlook quality control measures. Use checklists during packing and conduct regular quality checks to prevent errors.
Monitor return rates to identify packaging issues early, and inspect materials before use. These quality measures will reduce costly mistakes and returns while maintaining customer satisfaction.
Automate Packaging Operations
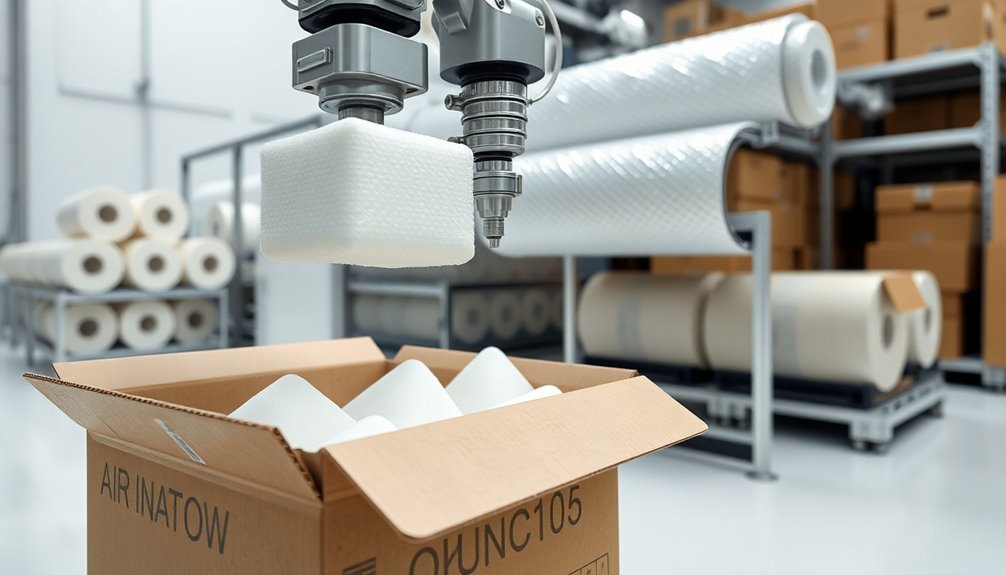
Through strategic automation of packaging operations, you'll maximize efficiency while reducing labor costs and material waste. By implementing robotic arms and conveyor systems, you can substantially increase packaging speed and precision while minimizing workplace injuries.
Automated systems also guarantee consistent quality control through integrated sensors and software that monitor every step of the process. Real-time analytics enable better operational decision-making and troubleshooting.
Consider installing box-making machines that create right-sized packaging on demand. This technology reduces material waste and shipping costs by eliminating the need for oversized boxes and excess void fill. You'll also benefit from dimensional pricing optimization, as automated systems can calculate and create the most cost-effective packaging solutions for each product.
To maximize your automation investment, focus on integrating these systems with your existing production line. Modern packaging automation is highly flexible and can handle various product sizes and shapes while maintaining scalable performance.
You'll see immediate improvements in supply chain efficiency as automated systems reduce errors and inconsistencies. Plus, warehouse optimization through automated packaging processes will boost your overall productivity and help you quickly adapt to changing demand levels.
Frequently Asked Questions
How Long Does It Take to See Cost Savings After Implementing New Packaging?
You'll notice immediate savings in material costs, while larger savings emerge over 3-6 months as you optimize processes. Long-term benefits from sustainable packaging and automation typically show within 12-18 months of implementation.
What Are the Upfront Costs of Switching to Automated Packaging Systems?
You'll need to invest $50,000 to six figures upfront for automated packaging systems. You'll also face costs for maintenance, service, warehouse modifications, and operational expenses. Don't forget to think about financing options.
Can Protective Packaging Solutions Be Tested Before Full-Scale Implementation?
Yes, you can test protective packaging through various methods like visual inspection, vacuum decay tests, seal peel tests, burst tests, and bubble emission tests before committing to full implementation to validate effectiveness and reliability.
How Often Should Packaging Materials and Suppliers Be Evaluated for Cost Efficiency?
You should evaluate your packaging materials and suppliers every 3-6 months. Don't forget to conduct regular audits, track market trends, and compare supplier offers to guarantee you're getting the best value.
What Insurance Considerations Should Be Made When Changing Protective Packaging Methods?
You'll need to review your coverage limits, assess new risks, document all packaging changes, and inform your insurer. Don't forget to validate packaging methods and maintain compliance with industry regulations.
In Summary
You'll find significant savings by implementing these five cost-cutting strategies for protective packaging. Start with a thorough packaging audit, switch to sustainable materials, fine-tune your package dimensions, improve handling efficiency, and automate where possible. When you're ready to reduce waste and boost your bottom line, these practical steps will help you create a more cost-effective packaging operation that protects both products and profits.
Leave a Reply