Anti-static cleanroom runners provide essential ESD protection by combining conductive and dissipative materials to prevent static discharge in sensitive environments. You'll need to select runners that meet ANSI/ESD S20.20 standards, with resistance levels between 50,000 ohms and 1.0 x 10^9 ohms. Proper installation requires careful grounding techniques, using copper straps every 1000 square feet, and regular maintenance to preserve effectiveness. When choosing between conductive (<1 million ohms) and dissipative (1 million – 1 billion ohms) materials, consider your application's sensitivity and footwear compatibility. Master these fundamentals, and you'll discover a complete system for protecting your cleanroom environment.
Understanding ESD Protection Materials
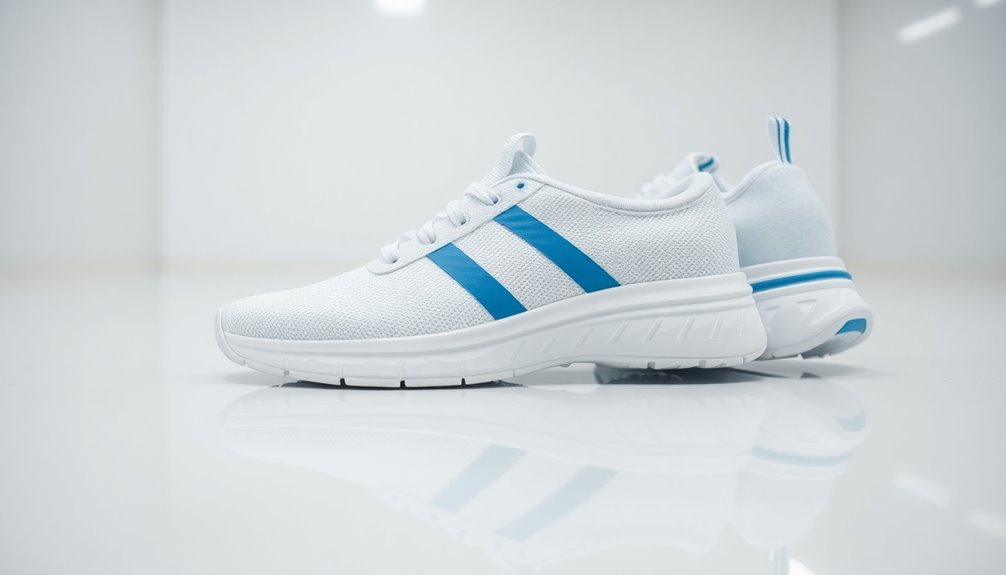
Various ESD protection materials play an essential role in maintaining cleanroom integrity and protecting sensitive equipment from static discharge. When you're selecting materials for your cleanroom, you'll need to focus on both flooring and specialty items that effectively manage static electricity. Small electronic components are especially vulnerable to damage from minimal voltage levels.
ESD flooring systems combine conductive and dissipative materials to reduce charge buildup, while ESD floor sealers enhance their performance and make maintenance easier. Simply walking across standard carpet can generate up to 35,000 volts of static electricity, making proper flooring crucial.
You'll find that static-dissipative plastics are vital components in cleanroom environments, as they provide better protection than standard plastics. These materials work alongside other ESD control measures, including humidity control systems and ionization equipment that neutralize static charges in the air.
To maintain effectiveness, you'll need to implement regular cleaning protocols and maintenance schedules for all ESD protection materials.
Your cleanroom must comply with specific standards like ANSI/ESD S20.20 and IEC 61340, which govern ESD control measures. You'll need to conduct regular audits to confirm your materials meet these requirements.
Remember that different industries may require varying levels of ESD protection, so you should select materials that align with your specific cleanroom classification under ISO 14644 standards.
Choosing Between Conductive and Dissipative
After understanding ESD protection materials broadly, you'll need to make a key decision between conductive and dissipative materials for your cleanroom runners. Both options effectively protect against static electricity, but they work differently. Conductive materials, with resistance below 1 million ohms, offer the fastest charge dissipation, while dissipative materials provide controlled discharge with resistance between 1 million and 1 billion ohms. Regular movement and contact on these surfaces necessitates choosing materials with optimal static control properties.
The SRM200 Surface Resistance Meter helps verify material properties before installation. To make the right choice, consider these important factors:
- Application Sensitivity: Choose conductive materials for highly sensitive electronic equipment areas where immediate charge dissipation is essential, or opt for dissipative materials in general electronics manufacturing environments.
- Footwear Integration: If you're using static-protective footwear, dissipative materials often provide better compatibility and enhanced overall performance.
- Environmental Conditions: Consider how temperature and humidity fluctuations might affect your chosen material's performance in your specific facility.
Both materials meet ANSI/ESD S20.20 standards, requiring measurements ≤1.0 x 10^9 Ω. Your final decision should align with your industry requirements, specific application needs, and existing static control measures.
Remember to verify certification compliance with ESD Standard Test Method 7.1 before making your purchase.
Key Installation Requirements
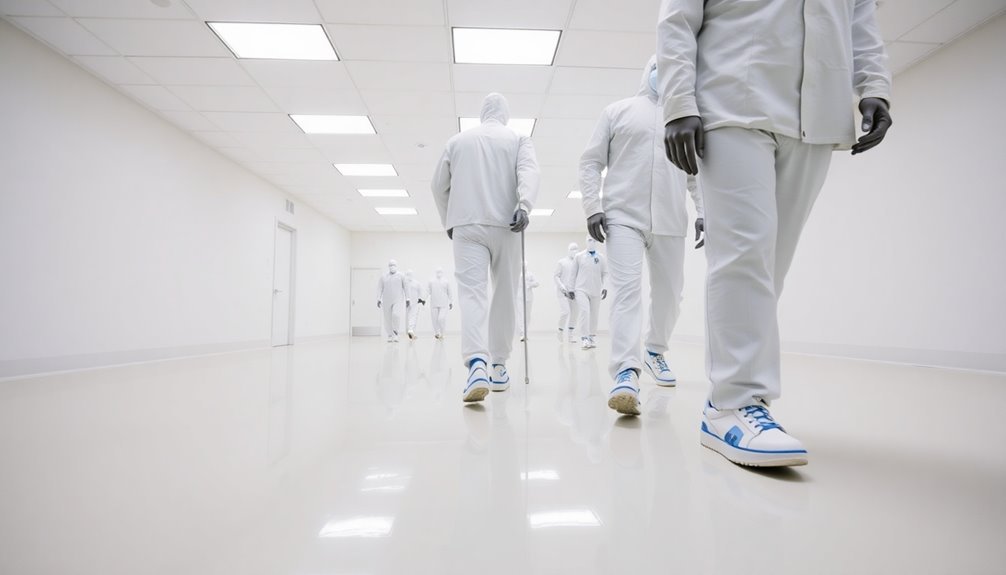
Installing anti-static cleanroom runners requires careful planning and adherence to specific requirements to guarantee peak performance. Before you begin installation, you'll need to assess your existing floor's condition and test for vapor emissions. Make sure you've selected cleanroom-compatible materials that meet ANSI/ESD S20.20 and ANSI/ESD STM97.2 standards. Professional assistance is available through the StaticWorx support line for material selection guidance.
You'll have several installation methods at your disposal. If you're working with existing VCT tile, you can opt for direct installation using fast-drying conductive adhesives, self-adhering ESD sheet flooring, or interlocking systems like GroundLock Extreme. The runners should connect seamlessly with conductive seams to maintain electrical continuity throughout the system. To minimize operational disruption, consider implementing a phased installation approach, working in segments rather than shutting down the entire facility.
During installation, you must verify continuous electrical grounding without isolated conductors. Pay special attention to proper adhesive application and connection points. You'll need to confirm that the runners provide consistent static control through either grounding or dissipation.
Post-installation, establish a regular maintenance schedule and implement clear usage guidelines for personnel. Don't forget to set up routine inspection protocols to verify that your anti-static runners maintain their effectiveness over time.
Proper Grounding Techniques
Proper grounding serves as the foundation for effective anti-static cleanroom runner performance. You'll need to connect your runners to an established grounding point using either copper straps or approved conductive materials. Installing push and clinch snaps at strategic points helps secure grounding connections for optimal performance.
When installing anti-static runners, you can choose from several proven grounding methods, including common point ground connections to the equipment grounding conductor or natural earth ground using copper rods. Installing at least one strap per 1000 square feet of runner material ensures optimal static dissipation coverage.
To guarantee peak performance of your cleanroom runners, implement these essential grounding techniques:
- Install a 24-inch copper grounding strap from the runner to the nearest AC electrical outlet, maintaining continuous contact with the floor material.
- Connect the runners directly to exposed steel support columns using appropriate conductive straps when building structure allows.
- Combine your grounded runners with ESD-compliant footwear to create a complete static control system that meets ANSI/ESD standards.
Your grounding system must maintain resistance levels below 1.0 x 10^9 ohms and keep body voltage accumulation under 100 volts during standard walking tests.
Don't forget to regularly test all grounding connections to verify they're functioning correctly and maintaining proper conductivity throughout your cleanroom environment.
Maintenance and Cleaning Protocols
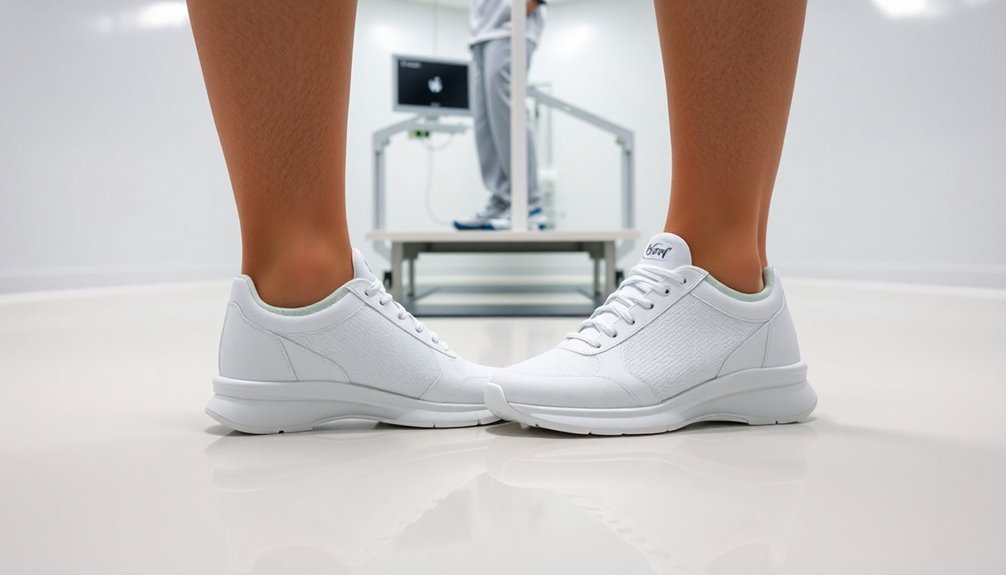
The maintenance and cleaning of anti-static cleanroom runners requires a systematic approach to preserve their ESD-protective qualities.
You'll need to follow specific cleaning methods, starting with dry cleaning to remove loose particles using a cleaning brush or broom. For wet cleaning, you should only use clean water or specialized ESD cleaning solutions, avoiding household cleaners and alcohol-based products.
When cleaning your runners, you'll want to apply the cleaning solution across the entire surface using a lint-free cloth or paper towel. For larger floor mats, use a damp cotton mop, making sure to squeeze out excess solution before application.
You'll need to establish a regular cleaning schedule based on usage and contamination levels, which can range from daily to monthly maintenance.
Different ESD flooring materials require specific care – vinyl needs periodic buffing or waxing, while carpet and rubber require simpler maintenance like vacuuming or wet mopping.
You should also implement a monitoring program to track temperature, humidity, and airflow conditions.
Don't forget to maintain detailed cleaning records and conduct regular audits to verify your maintenance protocols remain effective and compliant with cleanroom standards.
Testing and Performance Standards
You'll need to regularly test your anti-static cleanroom runners using ANSI/ESD STM97.1 for system resistance and ANSI/ESD STM97.2 for peak voltage measurements.
Your static charge dissipation tests must confirm that the flooring system maintains resistance between 50,000 ohms and 1.0 x 10^9 ohms, while keeping peak voltage below 100 volts.
To maintain compliance with ANSI/ESD S20.20 and IEC 61340-5-1 standards, you must document all test results and perform ongoing verification checks with static-control footwear.
Measuring Static Charge Dissipation
Measuring static charge dissipation in cleanroom environments requires adherence to strict international standards and testing protocols. Standards like ANSI/ESD S20.20:2014 and IEC 61340-5-1:2016 provide extensive guidelines for evaluating anti-static materials and establishing effective control programs.
You'll need to conduct several specific tests to verify your cleanroom runners meet the required standards:
- Surface resistivity testing to measure the material's ability to dissipate static electricity.
- Decay time testing to determine how quickly static charges neutralize.
- Triboelectric charging tests to assess static generation from friction.
When measuring static charge dissipation, you must maintain controlled environmental conditions, particularly humidity levels, as they greatly impact test results.
If you're testing in a cleanroom with HEPA filters, be aware that these filters remove ions from the air, which can affect your measurements. You'll want to use capacitive probe tests for non-contact measurements and verify all testing equipment is properly grounded.
Remember that different materials dissipate charges at varying rates – conductors will show faster dissipation than insulators like Teflon.
Document all test results and maintain consistent testing procedures to guarantee reliable, reproducible measurements.
Essential Compliance Tests
Before installing anti-static cleanroom runners, compliance testing must adhere to strict industry standards like ANSI/ESD S20.20 and ESDA Standard 1.1-2006.
You'll need to conduct several critical tests using approved equipment like the SRM500K Digital Surface Resistance Test Kit to verify proper static control performance.
Start with the electrical resistance test, ensuring your runners measure between 50,000 ohms and 10 million ohms for ideal static dissipation.
You'll then need to perform the body voltage test, which shouldn't exceed 100 volts when using approved ESD footwear. This test simulates real-world conditions and helps verify system compatibility.
Don't forget to monitor environmental factors during testing, as humidity and temperature can greatly impact your results. You'll want to maintain consistent conditions throughout the testing process.
Make sure you're documenting all test results as part of your static control audit, including resistance-to-ground and point-to-point measurements.
Remember to test for out-gassing properties, particularly if you're installing runners in cleanroom environments where airborne molecular contamination must be minimized.
All testing procedures should comply with ASTM guidelines and EOS/ESD standards for thorough verification of your anti-static runners' performance.
Common Installation Mistakes
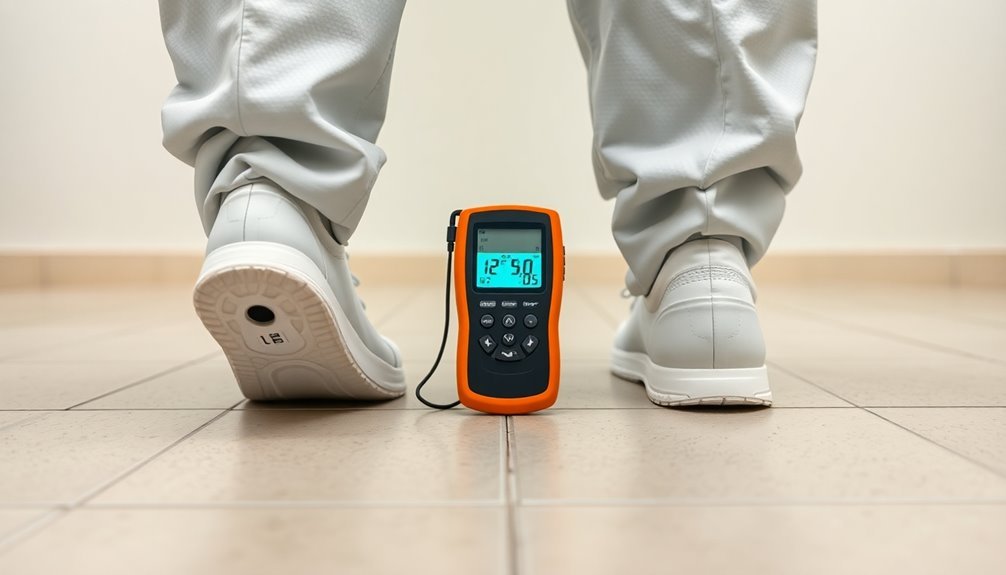
When you're installing anti-static cleanroom runners, improper grounding methods can render your ESD protection ineffective and potentially damage sensitive equipment.
You'll need to guarantee proper connection to designated ground points and verify conductivity through regular testing.
Another critical error to watch for is leaving gaps between runner sections, which can create tripping hazards and compromise the continuous path needed for static dissipation.
Improper Grounding Methods
The cleanroom's most vital grounding failures stem from fundamental installation mistakes that compromise ESD protection. When you're installing anti-static runners, improper grounding methods can render your entire ESD protection system ineffective.
You'll need to pay close attention to both flooring materials and environmental conditions to guarantee proper grounding.
Your grounding system's effectiveness depends heavily on the correct implementation of these vital components:
- Floor material selection – Don't use materials with resistance exceeding 1.0 x 10^9 ohms, and avoid relying solely on antistatic materials that lack proper conductive properties.
- Subfloor preparation – You must test and evaluate subfloor conditions, address moisture vapor issues, and properly treat contaminated concrete before installation.
- ESD footwear integration – Always use appropriate ESD footwear on both feet, regularly inspect heel grounders, and guarantee proper fit for consistent grounding.
Remember to conduct regular testing according to ANSI/ESD standards and maintain detailed compliance documentation.
Don't overlook the importance of testing your flooring as a complete system with specific footwear, as this integration is vital for maintaining effective static control in your cleanroom environment.
Gaps Between Runner Sections
Gaps between cleanroom runner sections create one of the most frequent and problematic installation mistakes you'll encounter. These gaps can severely disrupt the continuous grounding necessary for effective static control, leading to potential equipment damage and contamination risks in your cleanroom environment.
You'll need to pay special attention to the seams between runner sections, as they're particularly vulnerable to grounding disruption. If you're using inadequate adhesives or incorrect connectors, you'll likely experience gaps that compromise your static control system.
Over time, regular foot traffic and wear can worsen these gaps, creating increasingly serious grounding issues.
To prevent these problems, you'll want to implement specific installation strategies. Use conductive adhesives and proper connectors to maintain continuous grounding, and consider overlapping runner sections where possible.
Don't forget to perform regular inspections to identify any developing gaps before they become serious issues.
Remember that proper material selection is essential – you'll want to choose runners that are both durable and easy to install. Train your installation team thoroughly, and implement quality control checks during the installation process to catch and correct any grounding issues immediately.
Complementary ESD Control Products
Within extensive cleanroom environments, complementary ESD control products work alongside anti-static runners to create a complete static protection system.
You'll find that these products integrate seamlessly with your existing setup, enhancing overall protection against static electricity while maintaining cleanroom compliance standards.
When selecting complementary products, you'll want to focus on items that directly support your anti-static runners. These products often include ESD-safe footwear, wrist straps, and specialized work surfaces that meet ANSI/ESD S20.20 standards.
Here are three essential complementary products you should consider:
- ESD floor mats with pre-applied adhesive backing – they provide additional protection in high-traffic areas and changeover zones
- Anti-static clothing and footwear – they guarantee personnel don't introduce static charges while walking on runners
- Grounding points and connection systems – they create a thorough static dissipation network throughout your facility
You'll need to maintain these complementary products alongside your runners, but they're designed for easy cleaning and long-term durability.
Most feature low-maintenance materials that won't compromise your cleanroom's integrity while providing consistent static protection throughout their lifecycle.
Material Selection Criteria
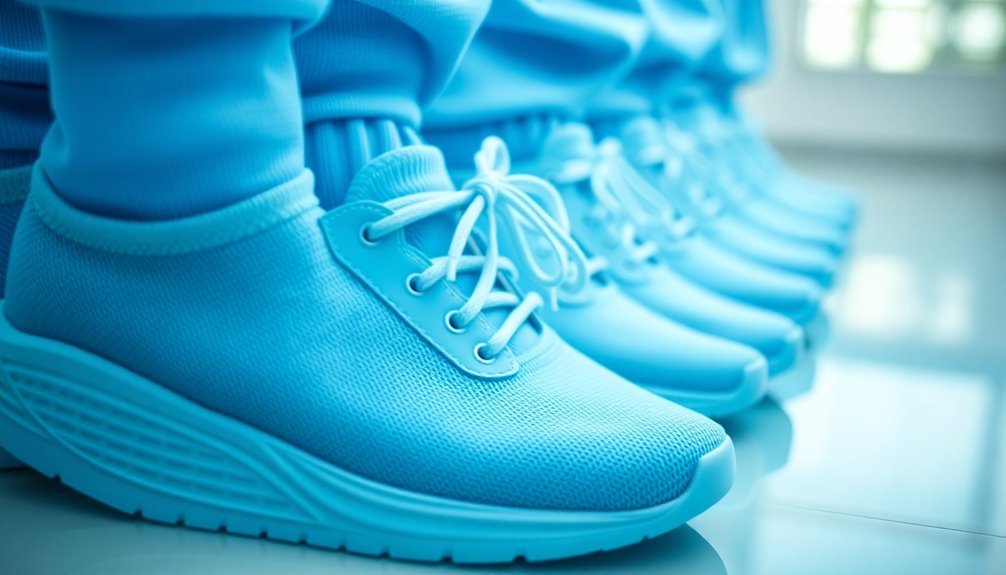
Carefully selecting materials for cleanroom runners requires balancing multiple critical factors, including static dissipation capabilities, durability, and particle resistance.
You'll need to verify your chosen materials can effectively dissipate static electricity while maintaining their properties over time, regardless of environmental conditions.
When evaluating materials, look for those that don't rely on humidity for their static dissipative properties. Your runners' materials should exhibit strong conductivity for proper grounding and incorporate antistatic properties to prevent charge generation from the start.
You'll want to avoid materials that can shed particles or degrade quickly, as these will compromise your cleanroom's integrity.
Consider materials that meet ISO 14644 and CSM standards while offering minimal cleaning requirements.
You'll find that conductive rubber compounds often provide the best balance of properties, combining effective static dissipation with strong particle resistance.
Don't overlook the importance of breathability and comfort, as these factors directly impact compliance with cleanroom protocols.
Remember that your chosen materials must work in conjunction with complementary ESD control measures like air ionization systems and conductive footwear to create a thorough static control solution.
Safety and Compliance Measures
You'll need to verify your cleanroom runners meet the ANSI/ESD STM7.1 standards for static control flooring systems, which require regular compliance testing and documentation.
Your testing protocols should include surface resistance measurements to maintain values below 1.0 x 10^9 ohms, along with routine inspections for physical damage or wear.
When implementing these safety measures, you must integrate proper grounding connections and verify compatibility with your facility's ESD control program, including personnel protective equipment and monitoring systems.
Regulatory Standards Conformity
Through a complex network of standards and regulations, anti-static cleanroom runners must comply with multiple regulatory frameworks to confirm safety and performance.
Your cleanroom footwear needs to meet ISO 14644-1 specifications for particle control while simultaneously adhering to ANSI/ESD S20.20 requirements for static control. USP standards add another layer of complexity, especially if you're working in pharmaceutical environments.
To verify your anti-static runners meet regulatory standards, you'll need to confirm these critical requirements:
- System resistance must remain below 1.0 x 10^9 ohms when tested as part of the complete footwear-flooring system.
- Body voltage generation can't exceed 100 volts when wearing the runners with proper grounding.
- Materials must pass out-gassing tests to prevent contamination within the cleanroom environment.
You'll need to maintain documented records of compliance testing, including periodic verification of both ESD properties and particle generation characteristics.
Your runners should undergo regular testing as part of your facility's compliance program, with particular attention to resistance measurements and charge generation properties.
Remember that continuous monitoring systems can help streamline these verification processes while confirming consistent regulatory conformity.
Testing Protocol Implementation
In line with established safety protocols, implementing a thorough testing program for anti-static cleanroom runners requires systematic attention to multiple parameters.
You'll need to begin by installing 12" x 24" samples of your ESD flooring material on insulative support, making certain to secure them with adhesive as they'd be in actual installation. Don't forget to include a seam to accurately simulate real-world conditions.
For resistance testing, you'll want to conduct both Resistance to Ground (RTG) and Point-to-Point (RTT) measurements. Use a 5 lb electrode connected to your resistance meter, starting at 10 volts and increasing to 100 volts if resistance exceeds 1.0 x 10E6 ohms.
You should test each sample six times from fixed probe locations to guarantee consistency.
During your testing procedures, you'll need to maintain proper environmental conditions. Keep the floor conditioned at 12% ±3% humidity for at least 72 hours before testing.
Always use a grounding plug for AC ground connection and ascertain all your testing equipment is properly calibrated and cleaned before measurements.
Remember to document all results for compliance verification.
Frequently Asked Questions
Can Anti-Static Runners Be Installed Over Existing Carpet or Flooring Materials?
Yes, you can install anti-static runners over your existing floor or carpet. You'll want to make certain the surface is clean, flat, and stable to prevent slipping and maintain proper electrical conductivity.
What Is the Average Lifespan of Anti-Static Cleanroom Runners Under Normal Use?
Under normal use, you'll find your anti-static runners typically last 2 to 5 years. However, if you're using them in heavy soldering environments, they'll only last 3 to 6 months with constant exposure.
Do Temperature and Humidity Changes Affect the Performance of Cleanroom Runners?
Yes, temperature and humidity greatly affect your runners' performance. You'll notice reduced static dissipation in low humidity, while high humidity can degrade materials. Keep your environment at 30-40% RH for ideal performance.
How Quickly Can Static Charges Dissipate Through Properly Installed Runners?
Through properly installed runners, you'll see static charges dissipate within milliseconds to seconds. Your charges will transfer quickly when you're using conductive materials grounded correctly, especially with proper humidity levels maintained.
Are There Specific Shoe Cover Requirements When Walking on Anti-Static Runners?
You'll need ISO-compliant shoe covers with ESD rubber soles and conductive grounding ribbons. Make sure they're rated for your cleanroom class and feature static dissipative fabric with proper elastic fit.
In Summary
You've now got the knowledge to select, install, and maintain anti-static cleanroom runners effectively. Don't underestimate the significance of proper grounding and regular maintenance – they're essential for ESD protection. When you're choosing between conductive and dissipative materials, remember to take into account your specific facility needs. Keep these guidelines handy, follow safety protocols, and you'll maintain ideal ESD protection in your cleanroom environment.
Leave a Reply