To apply anti-static spray safely and effectively, first put on protective gear like gloves and goggles, and guarantee proper ventilation. Clean your target surface thoroughly with detergent and water, removing all dirt and contaminants. Hold the spray can 6-8 inches from the surface and apply using steady, sweeping motions with slight overlap for even coverage. Don't oversaturate the area, and allow proper drying time in a controlled environment. Reapply every 3-6 months for general surfaces, or more frequently for high-traffic areas. For the most reliable protection against static buildup, there's more you'll want to know about proper application techniques and maintenance.
Safety Equipment and Workspace Setup
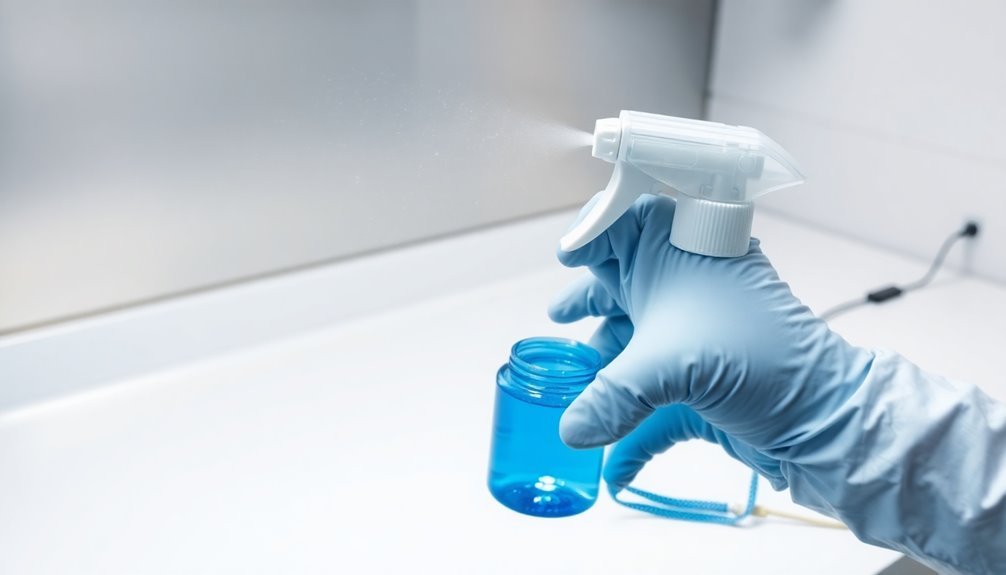
For your work surfaces, spray anti-static solution on non-porous areas and wipe them clean with a dry cloth.
You should always spot test first on delicate materials before full application.
Remember to maintain humidity-independent static control and verify that your surface resistivity meets the required standards of 10^9 to 10^10 ohms per square.
Selecting the Right Antistatic Product
When choosing an anti-static spray, you'll need to focus on key features like volume resistivity levels and longevity of protection to guarantee top performance.
You should check the product's compatibility with your specific surfaces, whether they're fabrics, electronics, or industrial materials, to prevent damage or ineffective application. The most effective solutions can reduce static problems 92% when properly matched to the surface type.
Look for eco-friendly and non-toxic formulations that meet industry standards while minimizing environmental impact, especially if you're using the spray in enclosed spaces.
Key Product Features Required
Selecting an effective anti-static spray requires attention to several critical features. You'll want to guarantee your chosen product contains the essential components: a reliable solvent, surfactant, active compounds, and propellant gas. The spray should come in an aluminum aerosol can for optimal dispensing and protection of the contents.
Look for non-toxic and non-flammable formulations that won't leave stains or harmful residue on your surfaces.
For ideal results, choose a spray that's suitable for your specific application. If you're working with fabrics or electronics, verify that the product is explicitly designed for these materials.
You'll also want to evaluate the spray's durability – some formulations can provide protection for weeks or even months. Check that your selected product meets relevant certifications, especially if you're using it in an ESD-controlled environment.
Environmental factors should influence your choice too. If you're environmentally conscious, opt for biodegradable formulations. The spray should perform well in low humidity conditions and resist moisture.
Evaluate whether you need a general-purpose or specialized compound, and check if it can be used at full strength or diluted. Finally, guarantee the product offers both immediate static control and long-lasting protection for your specific needs.
Surface Compatibility Analysis
Before diving into specific products, a thorough analysis of surface compatibility stands at the core of effective antistatic spray selection. You'll need to carefully match the antistatic spray's composition with your target surface to guarantee optimal performance and prevent potential damage.
For electronic surfaces, you'll want to choose silicone-based formulas specifically designed for sensitive components. Industry leaders like ACL Staticide and 3M provide reliable solutions for electronics applications. The surface finish of your material matters considerably – smooth surfaces typically increase resistivity, so you might need specialized coatings for these applications.
Consider the chemical makeup of both your surface and the antistatic agents to avoid adverse reactions.
Before making your final selection, you should test the spray on a small, hidden area of your surface. This step helps verify both compatibility and effectiveness.
If you're working with non-conductive laminate surfaces, you'll need to lightly sand them with 180-grit or finer sandpaper to remove glossy finishes that could interfere with the coating's performance.
Remember that different materials require different types of antistatic protection. Don't assume one product will work universally across all your surfaces – what works for plastic mightn't be suitable for glass or metal components.
Environmental Impact Considerations
Now that you've identified compatible surfaces, your antistatic product choice should reflect today's growing environmental concerns.
When selecting an antistatic spray, look for biodegradable options or those made with natural ingredients, as they'll have less environmental impact than traditional chemical-based products. Modern companies are increasingly adopting sustainable ESD solutions to meet global environmental goals.
Consider products packaged in recyclable materials, particularly those made from rPET (recycled water bottles). You'll want to evaluate the product's total lifecycle impact, including its carbon footprint and waste management implications. Many eco-friendly options actually offer lower total ownership costs due to their recyclability and reduced environmental impact.
Be aware that many antistatic sprays contain components toxic to aquatic life. You'll need to prevent spills from entering waterways and guarantee proper disposal methods. When using the spray, always work in well-ventilated areas and keep the product away from water sources.
Check if your chosen product complies with current environmental regulations and industry standards. The electronics industry is shifting toward sustainable practices, so you'll find an increasing number of green alternatives. Look for products that align with both OSHA requirements and environmental responsibility guidelines to guarantee safe, sustainable use.
Surface Preparation Requirements
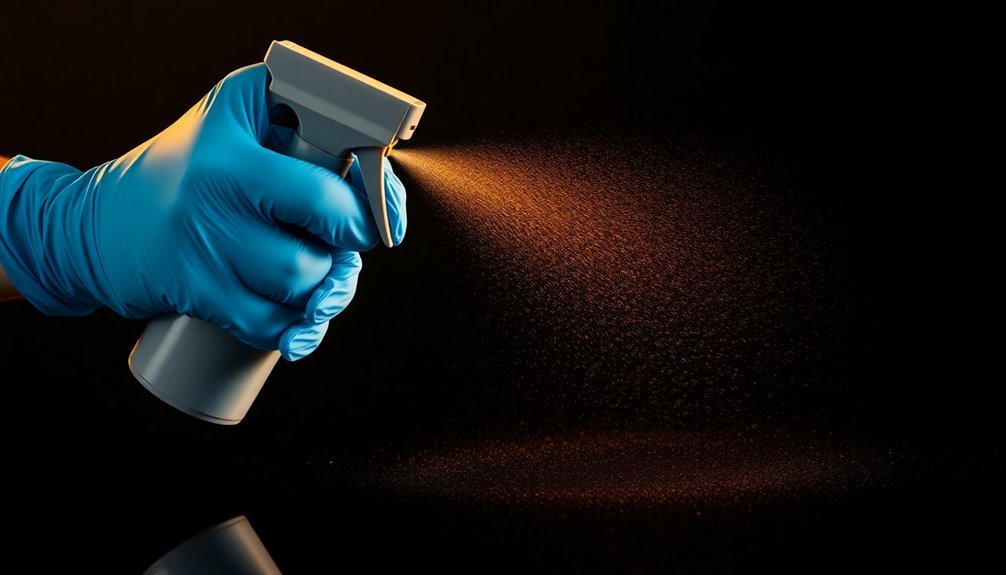
Proper surface preparation remains critical for achieving ideal anti-static spray performance. You'll need to clean, dry, and prepare your surface meticulously before applying any anti-static coating. Start by verifying the surface temperature falls between 55°F to 95°F and condition your paint components for 24 hours at this range.
Surface Type | Preparation Method | Special Requirements |
---|---|---|
Composite | Sand with 340-400 grit | Remove all dust |
Metal/Aluminum | Remove oils/contaminants | Use specified primers |
Concrete | Roughen surface | pH must be below 10.0 |
Wood | Sand smooth | Remove sanding dust |
For all surfaces, you'll need to remove any glossy finish using 180-grit or finer sandpaper. After sanding, wipe the surface with Desoclean® 110 cleaner or another suitable solvent. Don't forget to ground all equipment before application to prevent static buildup.
If you're working with previously painted surfaces, wash thoroughly to remove contaminants and rinse with water. For concrete surfaces, verify they've cured for at least 30 days and don't have any form release agents or curing compounds. Avoid applying the coating under high humidity conditions or on surfaces subject to hydrostatic pressure.
Application Methods and Techniques
When applying anti-static spray, you'll need to maintain a consistent distance of 6-8 inches from the surface for ideal coverage.
Start with a clean surface and use even, sweeping motions to guarantee you're distributing the spray uniformly across the target area.
You can achieve the best coverage pattern by slightly overlapping each stroke while moving at a steady pace, preventing oversaturation of any single spot. For best results, apply the spray to a microfiber towel first before wiping down the robot's surfaces.
Proper Spray Distance Control
Setting up the right spray distance stands out as one of the most critical factors when applying anti-static spray. You'll need to maintain a minimum distance of 6-8 inches from the surface to achieve even coverage while preventing oversaturation. This consistent distance helps you avoid creating slipping hazards and guarantees uniform protection across the treated area.
When you're working with electronic components, you'll need to adjust your approach. Instead of spraying directly onto sensitive electronics, use a microfiber towel for safer distribution. If you're handling electronic boards, don't forget to wear an ESD wrist strap to prevent potentially damaging static discharges.
You can choose from several application methods depending on your surface type. For fabrics and general surfaces, direct spraying works well. However, when dealing with electronic components, opt for a lint-free cloth or the dipping method for more precise control.
For larger surfaces requiring uniform coverage, you might want to think about using a transfer roller coating technique. Remember to check the surface's condition before applying the spray and guarantee proper ventilation during application to protect yourself from fumes.
Best Coverage Patterns
A successful anti-static spray application relies heavily on mastering the right coverage patterns. To achieve the best results, you'll need to use steady, sweeping motions while maintaining a consistent distance from the surface.
For most applications, you can either spray directly onto the surface or apply the product using a microfiber or lint-free cloth for better control.
When working with electronics and circuit boards, pay special attention to static-prone areas near chips and connectors. You'll want to clean these surfaces thoroughly before application. For larger surfaces, consider using a transfer roller coating method, while the dipping method works better for smaller components.
Remember to avoid oversaturating surfaces, as this can create slipping hazards.
For specialty applications like robotics or ESD-sensitive equipment, focus on plastic areas where static typically builds up. When treating floors and furniture, apply the spray in smooth, even strokes.
You'll need to reapply every 3-6 months or when static charge becomes noticeable. Always guarantee proper ventilation during application and choose products with appropriate volume resistivity levels (10^10 to 10^12 ohms/cm) for maximum protection.
Surface Preparation Steps
Proper preparation of the surface stands up against the most common anti-static spray failures. You'll need to start by thoroughly cleaning all surfaces with a detergent solution, followed by a complete rinse with clean water to remove dirt, grease, and contaminants.
For specific surfaces, you'll need to follow additional steps. If you're working with new concrete, make certain it's cured for at least 30 days, and roughen any slick areas.
When preparing wood surfaces, sand them until smooth and remove all sanding dust.
Steel surfaces require thorough cleaning and may need a metal primer coat. For galvanized metal and aluminum, you must clean off any oils and apply a suitable primer.
Before applying the anti-static spray, check that the surface temperature is above 50°F (10°C). You'll want to maintain proper ventilation throughout the preparation process and wear protective gear like gloves and goggles.
Don't skip any preparation steps, as they're vital for proper adhesion and performance of the anti-static coating. Remove any loose materials or debris from the surface just before application to guarantee the best possible results.
Coverage Guidelines for Different Materials
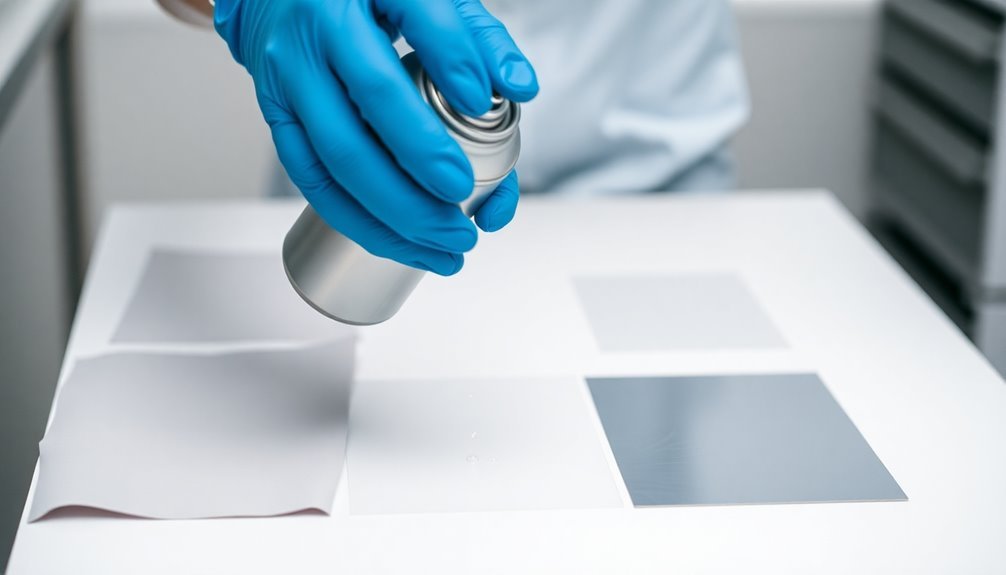
Different materials require specific coverage approaches when applying anti-static spray to guarantee maximum protection and performance.
When treating electronics and sensitive equipment, you'll need to apply a fine mist evenly across surfaces, ensuring proper ventilation during application. The coverage should be light but thorough to protect circuit boards and microprocessors effectively. Using logical reasoning, carefully evaluate surface conditions before applying to ensure optimal results.
For fabrics and upholstery, you can spray directly onto the surface, but always test on a hidden area first to prevent any potential discoloration. You'll find that the spray covers large areas efficiently, especially on porous materials, while reducing static cling and dust buildup.
When working with plastics and polycarbonate materials, you've got multiple application options including spray, flow coat, or dipping. For flow coat applications, you'll achieve approximately 600 square feet of coverage per gallon at 1.5 mil dry thickness. Special formulations are available for complex plastics requiring lower resistance.
For general surfaces like laminate flooring and work areas, you can spray from various angles for complete coverage. The spray works instantly regardless of humidity levels, and you don't need to worry about ozone depletion as it's environmentally compliant with REACH and RoHS standards.
Drying and Curing Times
During the drying and curing process, several key factors influence how quickly your anti-static spray will set. Air movement, relative humidity, and your choice of solvent play vital roles in determining the drying time.
You'll get faster results by using a fan to circulate air around the treated surface, but avoid using heat as it can damage the anti-static coating.
For ideal drying times, consider these essential factors:
- Use a fan on low setting to improve air circulation without disturbing the coating
- Dilute Heavy Duty Staticide with isopropyl alcohol for faster drying on non-porous surfaces
- Apply in a controlled environment with moderate humidity levels
- Choose spray application over wipe-on methods for quicker drying
- Maintain air temperature between 50-60°C for specialized anti-static inks
You'll find that most general-purpose anti-static sprays dry similarly to water, while fast-drying variants can set within seconds. If you're working with Heavy Duty Staticide, you can speed up the process by creating a proper dilution with isopropyl alcohol. For optimal results, use distilled or deionized water when diluting to minimize contaminants that could affect performance.
Remember that very dry conditions (below 15% humidity) won't negatively impact the drying process or the spray's effectiveness.
Maintenance and Reapplication Schedule
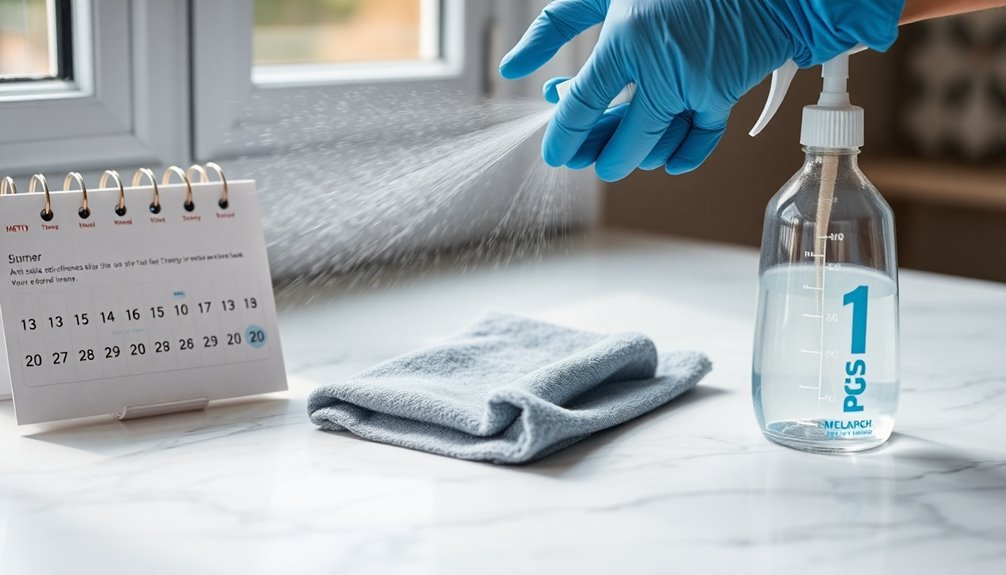
Once your anti-static spray has dried, maintaining its effectiveness requires a consistent reapplication schedule. Different surfaces require varying frequencies of treatment to maintain maximum protection against static electricity.
For high-traffic work surfaces, you'll need to reapply the spray every 2-3 days, while electronics require weekly or bi-weekly treatments.
Your carpets need treatment every 1-2 months in heavy-use areas and every 2-4 months in medium-use spaces. Don't forget to treat fabric and plastic chairs monthly with anti-static spray or wipes.
Equipment cases and work surfaces typically need reapplication every 2-3 months, but you might need to treat them more often based on usage. For your carts and wheel casters, plan on quarterly applications.
Media storage units should receive treatment monthly or bi-monthly.
Remember to adjust your reapplication schedule based on environmental conditions and usage intensity. You'll want to monitor humidity levels and surface wear to determine if you need more frequent applications.
Always clean surfaces thoroughly before reapplying the spray, and maintain proper ventilation during application to guarantee the best results.
Troubleshooting Common Problems
While anti-static sprays are generally effective, you may encounter several common issues during application and use. If you notice static electricity persisting, first check that you're wearing natural fiber clothing like cotton instead of synthetic materials that can generate more static.
You'll also want to maintain proper humidity levels in your space, as dry air considerably increases static buildup.
When troubleshooting static problems, watch for these key indicators:
- Crackling or popping sounds around your treated surfaces
- Unexpected shocks or sparks when touching items
- Static cling that returns quickly after treatment
- Visible residue or spotting on treated surfaces
- Equipment malfunctions following application
If you're experiencing persistent issues, verify you've selected a non-flammable anti-static spray that's appropriate for your specific materials. Don't forget to check that your spray hasn't expired, as this can reduce its effectiveness.
You'll want to clean all surfaces thoroughly before application and make sure you're using proper grounding techniques when working with electronic equipment. If problems continue despite these measures, you may need to consult a professional or consider additional solutions like anti-static mats.
Storage and Handling Best Practices
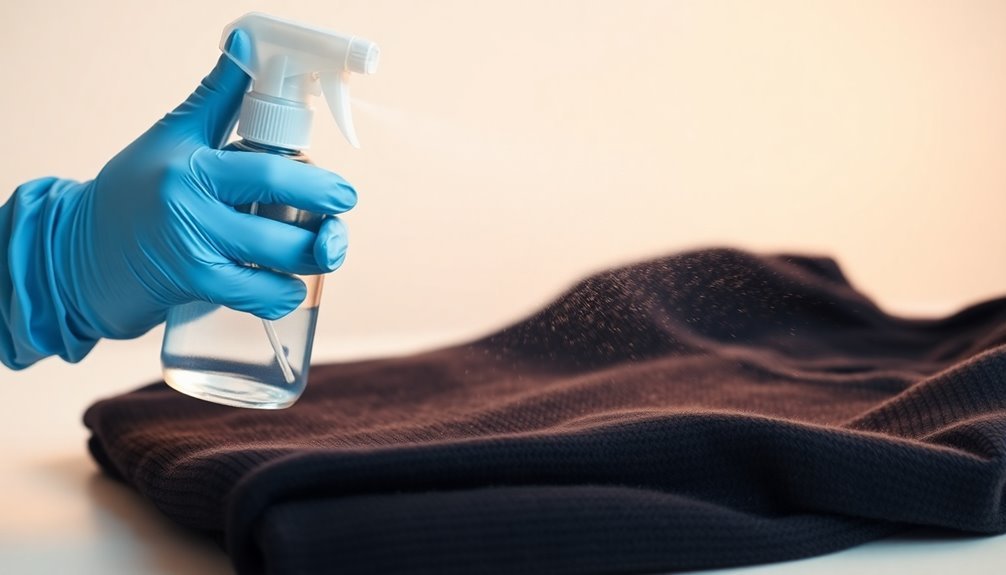
For the safe and effective use of anti-static sprays, proper storage and handling practices are essential. Always store your anti-static spray in its original container with the lid tightly sealed, and keep it in a cool, dry place away from direct sunlight.
The storage area should be well-ventilated and maintained at temperatures below 50°C/122°F.
You'll need to protect your anti-static spray from potential hazards. Store containers upright in designated areas equipped with sprinklers and appropriate fire extinguishers. Don't place them near heat sources, open flames, or incompatible materials. Make sure you're following Level 2 Aerosol storage requirements if your local regulations specify them.
If you experience a spill, don't flush it with water. Instead, contain it using vermiculite, dry sand, or approved absorbent materials.
When handling containers, wear protective gear to prevent skin contact or splashing. Keep your storage area secure and inaccessible to children and unauthorized personnel.
When it's time for disposal, don't puncture or crush the containers. Place them in sealed containers and follow your local hazardous materials disposal regulations.
Environmental Impact and Disposal
When you're done with your anti-static spray, you'll need to properly dispose of the aerosol can by using an approved puncturing system and recycling the empty container as scrap metal.
You can minimize environmental impact by choosing eco-friendly anti-static products that have lower aquatic toxicity and following strict spill prevention protocols that keep the product from entering drains or waterways.
If a spill occurs, immediately contain it using inert materials like sand or earth, and dispose of the contaminated absorbent material according to local regulations.
Safe Disposal Methods
Proper disposal of anti-static spray requires careful attention to environmental safety and regulatory compliance. When you're ready to dispose of your anti-static spray can, you'll need to follow specific procedures to protect both yourself and the environment.
To safely dispose of anti-static spray containers, use an approved aerosol can puncturing system like Aerosolv. These systems help you drain the contents safely while preventing accidental fires or chemical releases.
Make sure you're working in a well-ventilated area and following the manufacturer's instructions carefully.
Here are the essential steps for proper disposal:
- Ground the puncturing unit using anti-static wires to prevent static electricity buildup
- Puncture and drain the can's contents into EPA-compliant containers
- Segregate the drained chemicals based on compatibility
- Recycle the empty metal containers separately
- Clean up any spills immediately using appropriate spill kits
Remember to wear proper protective equipment throughout the disposal process.
If you're unsure about disposal requirements in your area, contact your local waste management authority for guidance.
Never dispose of aerosol cans in regular trash, as they can pose serious environmental and safety risks.
Eco-Friendly Product Selection
Selecting eco-friendly anti-static sprays plays a crucial role in reducing your environmental footprint. When choosing a product, look for options containing natural components like plant extracts and essential oils instead of harsh chemicals.
Check for biodegradable certifications from organizations like BPI, and verify that the product features non-toxic formulations safe for both you and the environment.
Pay attention to eco-friendly labeling and third-party certifications. Products with ISO 14001 certification guarantee environmentally responsible manufacturing practices. You'll want to choose brands that prioritize sustainable production methods, including water conservation and zero-waste manufacturing processes.
Consider the product's overall environmental impact by checking if it's manufactured locally to reduce transportation emissions. Look for companies that use renewable energy sources in their production and implement sustainable materials sourcing.
The best eco-friendly anti-static sprays will have minimal packaging waste and clear disposal instructions.
You can identify genuine eco-friendly products by their mild, pleasant odors and biodegradable ingredients. Remember that authentic sustainable products will back their environmental claims with proper certifications and independent audits, helping you make an informed choice that aligns with your environmental values.
Spill Management Protocol
Effective spill control measures are essential when working with anti-static sprays to protect both you and the environment. Keep a spill kit nearby that includes absorbent materials, protective gloves, and appropriate cleanup supplies.
If a spill occurs, act quickly to contain it and prevent it from reaching drains or soil.
For safe and responsible spill management, follow these key protocols:
- Immediately contain the spill using absorbent materials from your spill kit
- Wear protective equipment before handling any chemical spills
- Clean the affected area thoroughly using appropriate cleaning methods
- Document the incident, including the amount spilled and cleanup steps taken
- Dispose of cleanup materials in sealed, labeled containers according to local regulations
Never wash anti-static spray spills down drains or allow them to contaminate stormwater systems. If you're dealing with a large spill that you can't manage safely, contact your local hazardous waste authorities immediately.
To prevent future incidents, store your anti-static spray in a secure location with proper containment measures, and regularly inspect containers for damage or leaks. Remember to minimize product usage and consider eco-friendly alternatives whenever possible.
Frequently Asked Questions
Can Antistatic Spray Be Used on Electronics While They're Running?
You shouldn't apply antistatic spray while electronics are running. Always power off your devices first to prevent potential electrical damage. It's safer and more effective to spray when the equipment is completely off.
Will Antistatic Spray Affect Touchscreen Sensitivity on Mobile Devices?
If you use antistatic spray correctly, it won't affect your touchscreen's sensitivity. Make sure you're using a compatible spray and letting it dry completely before using your device to avoid any issues.
Can I Mix Different Brands of Antistatic Sprays Together?
No, you shouldn't mix different brands of antistatic sprays. It's unsafe and can create hazardous reactions, reduce effectiveness, void product warranties, and produce toxic fumes. Always use one brand as directed by the manufacturer.
Does Humidity Level Affect How Long Antistatic Spray Remains Effective?
Yes, humidity levels directly impact your antistatic spray's longevity. You'll need more frequent reapplication in high-humidity environments, while low-humidity conditions may extend effectiveness but require careful monitoring to maintain static protection.
Can Antistatic Spray Remove Existing Static Damage From Electronic Components?
No, you can't use anti-static spray to repair existing static damage in electronic components. Once static discharge has damaged internal circuits or components, they're permanently affected. The spray only prevents future static buildup.
In Summary
Proper application of anti-static spray isn't complicated once you've mastered the basics. Remember to wear your safety gear, prepare surfaces thoroughly, and maintain consistent coverage. You'll need to reapply based on your material type and environmental conditions. Store your anti-static spray properly and dispose of containers responsibly. When you follow these guidelines, you'll effectively control static electricity in your workspace.
Leave a Reply