You'll need to maintain specific vacuum pressure ranges between 1-10 torr and flow rates of 20-50 SCFM for effective static control in electronics manufacturing. Your system should include ESD-safe workstations with grounded surfaces, conductive materials, and proper personnel protection. Implement real-time monitoring systems to verify consistent operation, and keep vacuum chambers within medium ranges of 15" to 26" of mercury using dry rotary vane pumps. Regular maintenance and testing of your static control measures will guarantee peak performance. The deeper you explore these specifications, the better equipped you'll be to protect sensitive electronic components.
Understanding Static Control Requirements
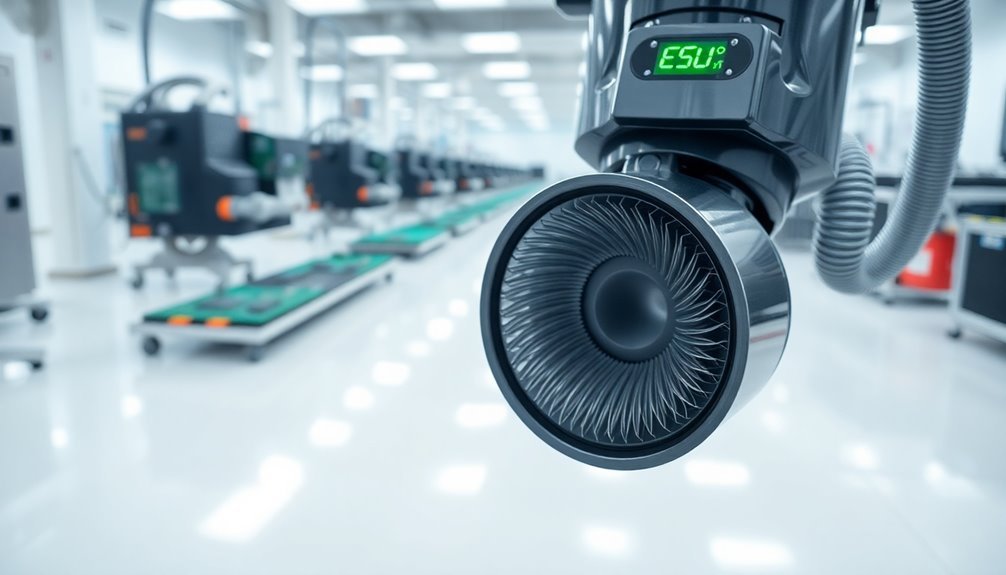
To maintain compliance, you'll need to follow international standards and obtain proper certifications.
As electronic components become more miniaturized, implementing application-specific controls becomes critical for protecting sensitive devices.
Remember that technological advances are making ESD protection in product design less effective, so you must regularly update your control measures and maintain strict adherence to established protocols through consistent training and documentation.
Vacuum System Performance Standards
Your vacuum system's performance standards must meet specific pressure ranges between 1-10 torr for effective static control while maintaining consistent flow rates of 20-50 SCFM.
Modern variable-speed pump systems enable precise vacuum flow adjustment while optimizing energy consumption during operation.
You'll need to implement precise control mechanisms to regulate both the vacuum pressure and flow rates within these parameters to prevent static discharge incidents.
System reliability benchmarks require 99.9% uptime, with redundant systems and real-time monitoring to guarantee continuous operation during critical manufacturing processes.
Optimal Pressure Range Metrics
The backbone of effective vacuum system performance lies in understanding and maintaining ideal pressure range metrics. You'll need to carefully consider the specific vacuum classifications, from low vacuum (1000-1 mbar) to ultra-high vacuum (10^-7 – 10^-14 mbar), to guarantee your system operates within the best parameters for static control applications.
Selecting the right pressure range impacts both system efficiency and control precision. You'll find that different vacuum levels require specific gauge technologies, and you must match these to your process requirements. Piezo gauges provide reliable measurements for pressures down to approximately 1 mbar with excellent stability.
When implementing pressure control systems, consider these critical metrics:
- Differential pressure tolerance: You'll need to maintain consistent pressure differentials across your system, accounting for barometric fluctuations that can affect performance.
- Working vacuum thresholds: Your system should operate within specified working vacuum ranges rather than pushing limits unnecessarily.
- Gauge accuracy requirements: Direct measurement devices offer better accuracy but remember they're limited to specific pressure ranges.
- Pump capacity metrics: You must match pump performance curves to your required pressure ranges, guaranteeing adequate system redundancy.
Always verify that your chosen pressure ranges align with both your process requirements and equipment capabilities to maintain best static control.
Flow Rate Control Standards
Managing vacuum system flow rates calls for strict adherence to industry-standard control mechanisms and performance metrics. You'll need to implement proper valve selection and control algorithms to maintain stable differential pressure levels critical for your electronics manufacturing processes.
Control Element | Primary Function | Key Consideration |
---|---|---|
Vacuum Valves | Flow regulation | Port geometry for maximum conductance |
PID Controls | Precise pressure management | Algorithm tuning for dead band elimination |
Pump Performance | Capacity maintenance | Atmospheric pressure impact |
Flow Monitoring | Process stability | Differential pressure tracking |
To achieve ideal flow control, you'll want to select vacuum control valves with appropriate port geometries and placement. Don't install control valves between your pump and vacuum volume, as this reduces conductance. You can use PID control algorithms for precise vacuum management, though P-only control might suffice for less demanding applications. A simple structure design helps ensure reliable operation while minimizing maintenance requirements.
Remember that your pump's performance will vary with atmospheric pressure changes – up to 20% in either direction. You'll need to account for these variations when designing your control system. For electronics applications, focus on maintaining stable differential pressure from atmospheric conditions, and consider using oil-free designs to prevent contamination.
System Reliability Parameters
Maintaining reliable vacuum system performance requires careful attention to several critical parameters that directly impact your manufacturing processes. You'll need to monitor both MTBF and MTTR metrics to assess your system's overall reliability and make necessary adjustments. These measurements help you calculate system availability and predict potential failures before they affect production.
Your vacuum system's reliability depends heavily on component selection, environmental conditions, and regular maintenance protocols. You should implement automated control systems to maintain precise pressure levels while minimizing human error. Integrating safety instrumented systems helps prevent accidents and equipment damage while ensuring operational safety.
Temperature stability and humidity management are equally vital, as they directly affect pump performance and system longevity.
To guarantee maximum system reliability, focus on these key parameters:
- Monitor differential pressure readings constantly to maintain proper vacuum tooling operation
- Track humidity levels to prevent pump damage and system failures
- Implement regular calibration schedules using NIST-traceable standards
- Maintain proper water quality for water-sealed vacuum pumps
Consider installing redundant components in critical areas to reduce the risk of total system failure. You'll also want to establish a thorough leak detection program to identify and address potential contamination sources before they compromise your manufacturing process.
Anti-Static Material Selection
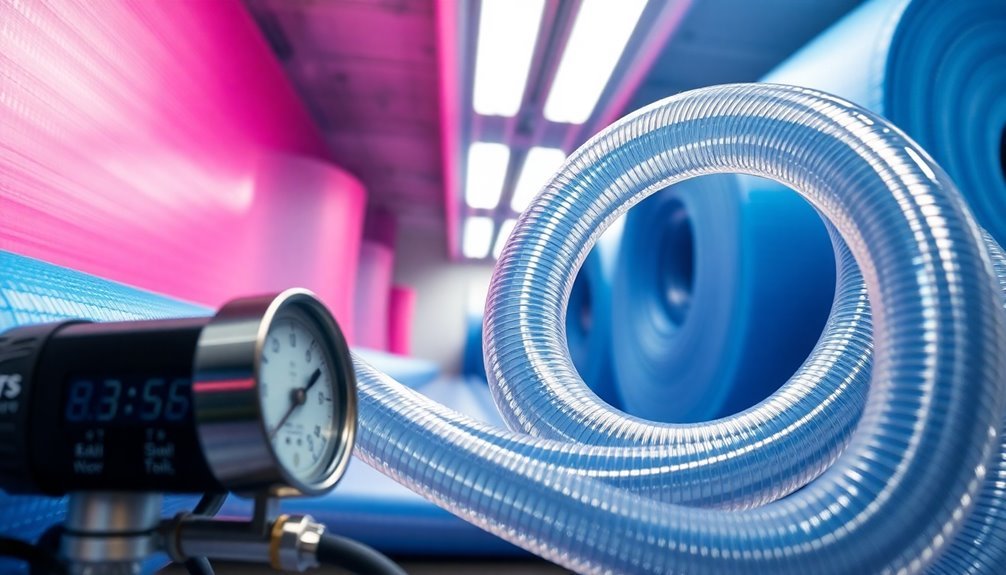
When you're selecting anti-static materials for vacuum applications, conductive rubber offers unique properties that combine flexibility with reliable static dissipation.
You'll need to guarantee your chosen materials meet standard resistance requirements, typically falling between 10^6 and 10^12 ohms per square for effective static control. Static dissipative materials provide controlled flow of static charges while maintaining higher resistance than fully conductive materials.
Your material selection should prioritize conductive rubber compounds that maintain consistent electrical properties under vacuum conditions while providing the necessary sealing characteristics.
Conductive Rubber Properties
The versatility of conductive rubber makes it an essential material for static control in vacuum systems. When you're selecting conductive rubber for vacuum applications, you'll need to understand how it achieves its conductivity through the incorporation of materials like carbon black or metal particles into the rubber matrix. These fillers create networks that allow electrical current to flow while maintaining the rubber's flexibility and sealing properties. Vulcanization agents improve the rubber's stability and mechanical performance under vacuum conditions.
For vacuum system applications, you'll want to evaluate conductive rubber based on these critical factors:
- Surface resistance values – guarantee they meet your specific static dissipation requirements for vacuum environments
- Environmental stability – confirm the material can maintain its conductive properties under varying humidity and pressure conditions
- Mechanical properties – verify the rubber's ability to maintain seals and flexibility while under vacuum stress
- Compatibility – check that the material works with your existing vacuum system components
You'll find conductive rubber particularly effective for EMI/RFI shielding in vacuum chambers, static dissipation in sensitive electronic manufacturing processes, and creating reliable electrical connections in vacuum environments.
The material's unique combination of conductivity and sealing properties makes it ideal for maintaining both vacuum integrity and static control.
Material Resistance Standards
While conductive rubber serves specific vacuum applications, proper material resistance standards form the backbone of thorough static control programs. When selecting materials for your static control program, you'll need to focus on specific resistivity ranges that guarantee effective static dissipation without compromising your product's integrity.
You must verify that your materials meet RoHS compliance standards, particularly avoiding hazardous substances like lead, mercury, and cadmium. Your materials should demonstrate consistent conductivity properties, allowing static charges to dissipate at a controlled rate.
They'll need to maintain their antistatic performance under your facility's specific humidity conditions and withstand high temperatures during lead-free soldering processes.
When implementing material resistance standards, you'll want to guarantee your selections provide reliable grounding paths and meet ESD control requirements for electrostatic protected areas. Test your materials' performance under controlled conditions to confirm they meet industry-specific regulations.
Remember that your materials' resistance properties shouldn't degrade with repeated handling or processing. For effective static control in vacuum applications, your materials must consistently perform within specified resistance ranges while maintaining compliance with all relevant industry standards.
ESD Safety Measures
Through proper implementation of ESD safety measures, you'll protect sensitive electronic components from potentially devastating static discharge damage. Establishing an electrostatic protected area (EPA) requires thorough grounding systems, controlled environments, proper employee equipment, and robust component protection protocols.
Your facility's grounding system must connect all workstations, tools, and personnel to guarantee static dissipation. You'll need conductive or dissipative materials throughout your EPA to neutralize charges and prevent static buildup.
When handling electronic components, you must use ESD-safe workstations equipped with grounded surfaces, protective mats, and appropriate packaging materials.
For effective ESD control, you'll need to implement these critical measures:
- Train all personnel on proper ESD handling techniques and require them to wear ESD-safe clothing, including smocks and footwear.
- Install and maintain grounded workstations with ESD-safe tools and materials.
- Use protection elements like TVS diodes, suppressors, and varistors at potential contact points.
- Conduct regular audits to verify your ESD control program's effectiveness.
Remember to minimize physical contact between dissimilar materials and guarantee all workers use proper grounding equipment, including wrist straps and cords.
Vacuum Chamber Design Specifications
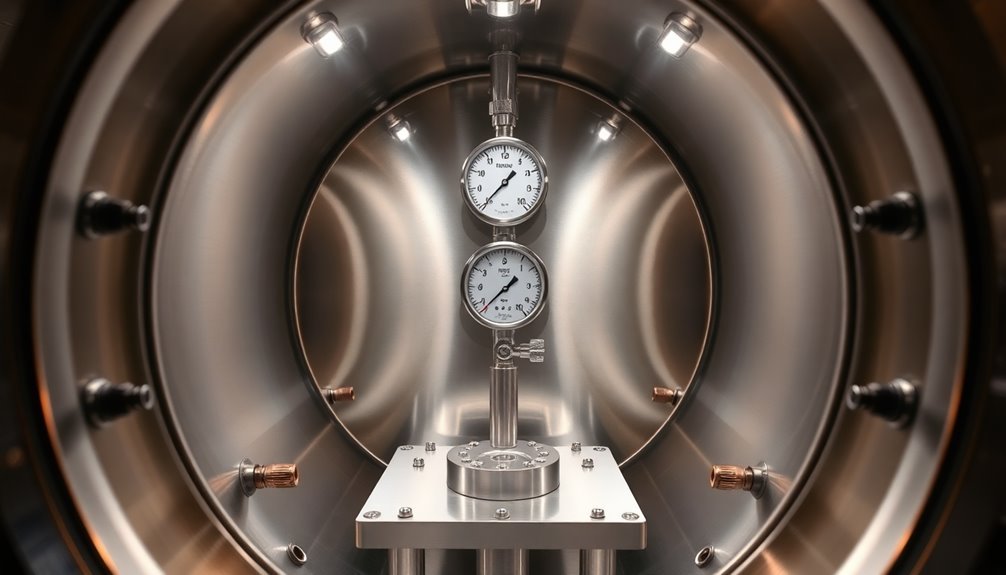
For ideal static control in electronics manufacturing, vacuum chamber design specifications must meet rigorous standards to maintain controlled environments and prevent ESD damage. You'll need to select materials that offer top performance characteristics – stainless steel and titanium are prime choices for high-vacuum applications due to their superior strength and low outgassing properties.
When designing your vacuum chamber, you'll want to focus on critical parameters including boundary conditions, vacuum integrity, and sealing mechanisms. It's crucial that you maintain precise machining tolerances for flanges and sealing surfaces to prevent vacuum leaks.
You'll also need to implement reliable pressure monitoring systems and thermal control measures to guarantee consistent processing conditions.
Your chamber design must incorporate contamination control features to protect sensitive electronic components. This includes selecting materials with minimal gas permeability and installing appropriate vacuum pumps for achieving and maintaining the required pressure levels.
Don't forget to take into account operational requirements like seal integrity maintenance and regular inspection protocols. For semiconductor production and vacuum coating applications, you'll need to guarantee your chamber design supports ultra-clean environments with proper material preparation and handling capabilities.
Equipment Selection Guidelines
Selecting the right vacuum equipment for static control requires careful evaluation of three vital factors: vacuum levels, material compatibility, and safety compliance. You'll need to focus on medium vacuum ranges between 15" to 26" of mercury, which typically calls for dry rotary vane pumps to achieve ideal performance in electronics manufacturing.
When choosing your equipment, consider these essential guidelines:
- Verify that your vacuum pump's flow rates match your specific process requirements – inadequate flow can lead to incomplete static control and potential damage to sensitive components.
- Install anti-static suction cups and conductive materials to prevent static discharge, which is essential for protecting electronic components during handling.
- Monitor your environmental conditions, including temperature, moisture, and particulates, as these factors directly impact vacuum performance and equipment longevity.
- Implement regular maintenance schedules based on your chosen pump type to maintain consistent performance and compliance with safety standards.
Remember that equipment selection isn't just about initial costs – you'll need to factor in energy efficiency, maintenance requirements, and total ownership costs.
For fine or ultra-vacuum applications, consider screw pumps, which offer superior performance for specialized electronic manufacturing needs.
Energy Efficiency Parameters
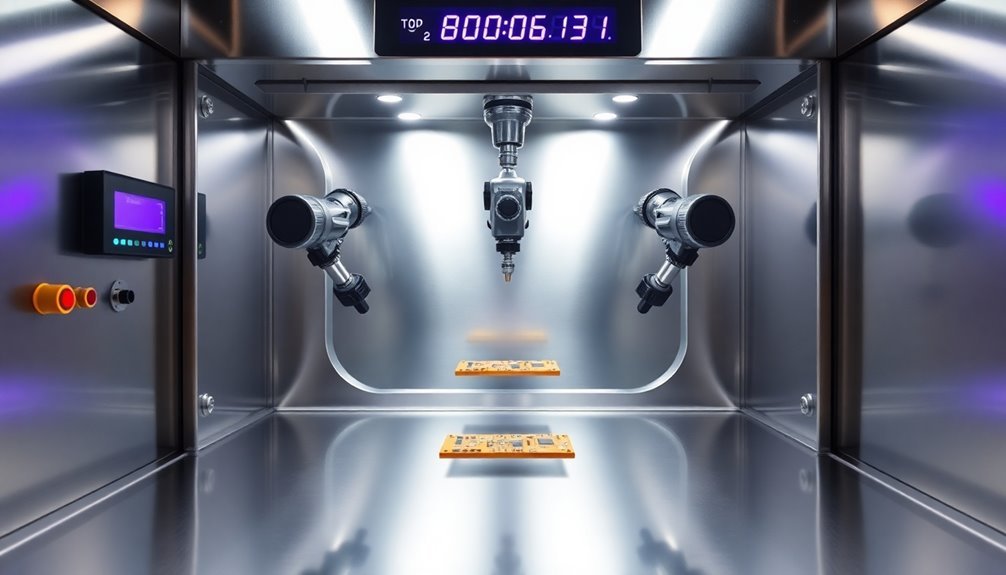
Once you've selected your vacuum equipment, optimizing energy efficiency parameters becomes the next key focus for maintaining cost-effective static control operations.
You'll find significant energy savings by implementing variable speed drives that match motor output to actual demand and utilizing multistage ejectors instead of single-stage designs.
You can achieve a 90-99% reduction in energy consumption by using ejector pumps for intermittent applications. To maximize efficiency, maintain vacuum pressure at ideal levels, such as 5.88 kPa, and implement heat recovery systems to capture and reuse waste energy.
It's essential to prevent air leakage, which can substantially impact your system's performance and energy consumption.
Consider using simulation software like FES to accurately assess your energy consumption patterns and identify optimization opportunities. You'll want to focus on system architecture design that minimizes energy waste while maintaining effective static control.
System Maintenance Protocols
In accordance with industry standards, proper system maintenance protocols form the foundation of reliable vacuum-based static control operations. You'll need to implement daily visual inspections, monitor operating temperatures, and check for unusual noises that might indicate system issues.
Regular maintenance tasks should include filter replacements, performance verification, and thorough cleaning of the surrounding environment.
To maintain effective static control, you must focus on these critical areas:
- Filter Management – Replace filters according to manufacturer guidelines, document all replacements, and guarantee proper installation to prevent contamination.
- Grounding System Integrity – Test connections regularly, replace worn components, and maintain solid grounding points to prevent static buildup.
- Component Inspection – Check all accessible bolts, connections, and parts for wear, replacing them with manufacturer-approved components when necessary.
- Documentation Control – Keep detailed maintenance records, update procedure manuals, and maintain thorough training materials for staff.
Your maintenance schedule should include biannual deep cleaning, annual oil changes, and regular system upgrades when needed. Don't forget to train your personnel on proper maintenance procedures and emergency protocols to guarantee consistent system performance and longevity.
Industry Compliance Standards
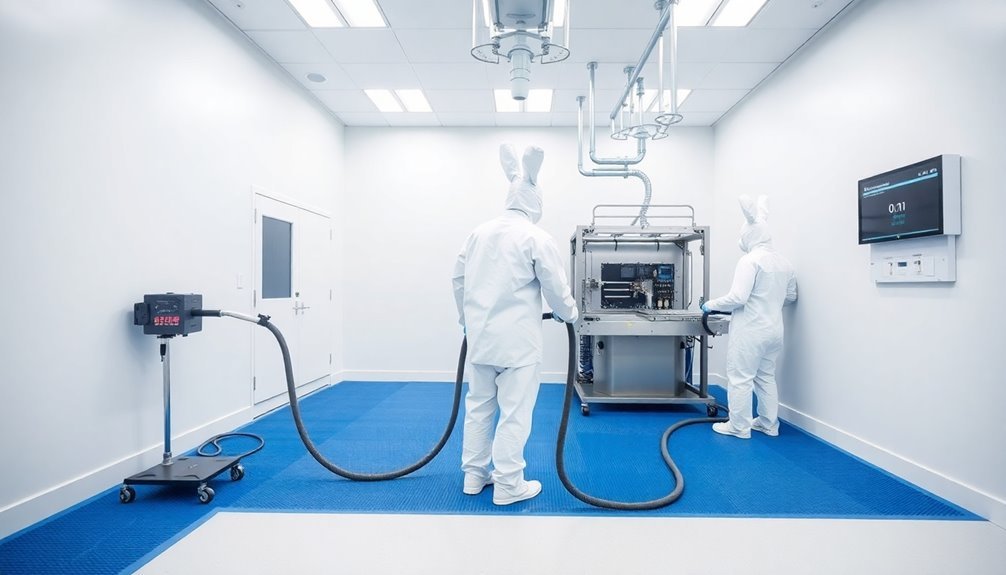
Throughout the static control industry, compliance with established standards forms the cornerstone of safe and effective operations. You'll need to follow several key standards, including NFPA 77 for static electricity control procedures and IEC 60079 for explosive atmosphere protection.
ANSI/ESD S20.20 certification is particularly vital, as it verifies your facility's ESD control program meets recognized benchmarks.
For your vacuum equipment and workspaces, you must guarantee all components meet specific resistance requirements. Your ESD control garments need to maintain a system resistance below 3.5 x 10^7 ohms, while your packaging must comply with ANSI/ESD STM11.11, STM11.12, or STM11.13 standards.
You'll also need to implement proper grounding methods through wrist straps and appropriate footwear.
If you're working in specialized industries, you'll need additional certifications. Military and aerospace projects require MIL-STD-1686 compliance, while semiconductor manufacturing demands IEC 61340-5-1 certification.
Don't forget about environmental regulations – you'll need to guarantee your operations comply with RoHS and REACH directives, especially when working with electrical and electronic equipment in EU markets.
Frequently Asked Questions
How Often Should Anti-Static Suction Cups Be Replaced in High-Volume Production?
You'll need to replace anti-static suction cups every 3-6 months in high-volume production. Monitor wear patterns, material degradation, and static control efficacy regularly. Replace immediately if you notice reduced performance.
Can Multiple Vacuum Systems Be Integrated With Existing Cleanroom Infrastructure?
Yes, you can integrate multiple vacuum systems with your cleanroom infrastructure, but you'll need dedicated lines, HEPA filtration, and proper contamination controls. Always guarantee compliance with cleanroom standards during integration.
What Backup Solutions Are Recommended During Emergency Vacuum System Shutdowns?
You'll need battery backups for electronics, liquid CO2 systems for temperature control, and compressed air backups. It is crucial to implement redundant vacuum units and automated monitoring to prevent complete system failures during emergencies.
How Does Temperature Fluctuation Affect Static Control in Vacuum Systems?
You'll notice temperature changes directly impact static control in vacuum systems by redistributing surface charges. When temps drop, you'll face increased ESD risks due to reduced surface conductivity and compromised humidity-based charge dissipation.
Are There Specific Humidity Requirements for Optimal Vacuum-Based Static Control?
You'll want to maintain 40-60% relative humidity for ideal static control, even in vacuum systems. Though vacuum chambers are sealed, humidity control in surrounding areas helps prevent static buildup during component handling.
In Summary
You'll need to maintain strict adherence to ESD safety protocols while ensuring your vacuum systems meet industry standards. Keep your equipment regularly calibrated, use appropriate anti-static materials, and monitor system performance daily. By following these guidelines and staying compliant with current regulations, you'll protect sensitive electronic components and maintain efficient manufacturing operations. Remember to document all maintenance and testing procedures for quality assurance.
Leave a Reply