Setting up an anti-static workstation requires seven key standards for maximum protection. You'll need dual-layer rubber mats with proper resistivity ratings, paired with secure grounding cables connected to your facility's equipment ground. Install a common point grounding system that links all components, including wrist straps and heel grounders. Your workspace should feature conductive flooring and regular testing procedures using an SRT meter kit. Position all equipment close to the main ground connection, and maintain clean, well-documented maintenance records. Understanding these standards marks your first step toward complete ESD protection mastery.
Essential Surface Materials and Grounding

Setting up an effective anti-static workstation starts with choosing the right surface materials and implementing proper grounding methods. You'll need to focus on dual-layer rubber mats that combine a conductive bottom layer with a static dissipative top layer. The mats provide chemical and heat resistance for long-term durability in industrial environments. These mats should have a low resistivity of 10^4 – 10^5 MΩ to guarantee consistent grounding.
When grounding your workstation, you'll want to connect your anti-static mats to electrical outlets through grounding cables. It's crucial to follow a two-step grounding process: first, ground all components to the same electrical ground point, then connect them to the equipment grounding conductor.
You can also incorporate conductive or dissipative flooring systems paired with ESD control footwear for additional protection.
For maximum safety, you'll need to mount earth bonding points using stainless steel studs with screw ring terminals. These connections provide secure attachment points for your wrist straps and grounding cords.
Remember to place your workstation within an electrostatic protected area (EPA) and use multi-layered bench matting to protect sensitive devices.
Regular evaluations of your ESD control measures will guarantee continued effectiveness and safety.
Personnel Protection Equipment Requirements
When you're working with static-sensitive components, you'll need to wear a properly tested wrist strap connected to a common point ground through a coil cord set.
Your wrist strap must make direct contact with your skin and be tested daily to guarantee it maintains the correct resistance range for static dissipation.
If you're moving around the workspace, you'll need to switch to ESD footwear like heel grounders combined with ESD floor mats to maintain continuous grounding protection. These workstations should include earth bonding points with stainless steel studs for secure grounding connections.
Essential Wrist Strap Guidelines
Anyone working with electronic components must use proper wrist straps as essential personnel protection equipment. When setting up your workstation, make certain your wrist strap connects properly to a grounding source and fits snugly against your skin. Bright colored straps are commonly used to enhance visibility and safety awareness in the workplace.
The strap's conductive fibers, typically made of silver-woven materials, create a safe path for static discharge while preventing skin irritation.
To maintain your wrist strap's effectiveness, you'll need to perform regular inspections and cleaning. Don't wait until damage occurs – replace your wrist strap according to your company's guidelines, whether quarterly, semi-annually, or annually. Your total system resistance shouldn't exceed 35 megohms as per ANSI/ESD S20.20 standards.
- Test your wrist strap daily using continuous monitoring systems for instant feedback on functionality
- Keep the conductive surface clean and free from debris to maintain consistent grounding
- Check for wear and tear on both the band and grounding cord, replacing damaged components immediately
For maximum protection, you'll want to connect your wrist strap to approved grounding points like bonding plugs or ESD mats. Remember that touching non-grounded surfaces can compromise your static protection, so maintain awareness of your movements while working.
Footwear Grounding Best Practices
Along with proper wrist straps, effective footwear grounding forms a complete ESD protection system for electronics handling. You'll need to select footwear with conductive elements like copper rivets, carbon insoles, or silver stitching to maintain consistent grounding. Leather soles provide superior conductivity, especially when combined with natural perspiration.
When setting up your workstation, make certain you're using ESD-compliant footwear in conjunction with proper flooring materials. Indigenous cultures recognized that naturally tanned leather provided optimal grounding properties for footwear. You'll achieve the best results on conductive surfaces or ESD flooring mats.
Don't rely on standard shoes when working on non-conductive surfaces like asphalt, as they'll compromise your grounding effectiveness.
Your grounding footwear should fit comfortably without restricting movement, and you'll want to wear natural fiber socks to enhance conductivity.
Test your footwear regularly using an ESD tester to verify compliance with IEC-61340-5-1 standards. You must wear grounding shoes on both feet to maintain proper body-to-ground connection.
Remember to avoid using grounding footwear during lightning storms, and if you have electronic medical implants, consult your doctor before implementing any grounding solutions at your workstation.
Common Point Ground Installation
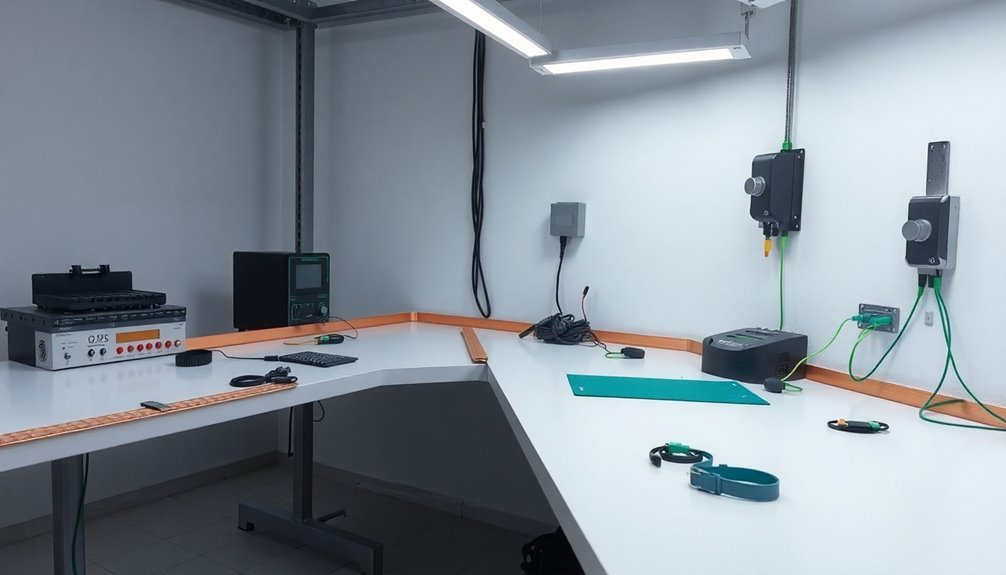
The proper installation of a common point ground forms the backbone of any effective anti-static workstation. You'll need to connect all grounding elements to the same common point, which should link directly to your facility's "green wire" equipment ground. For compliance with ANSI/ESD S6.1 standards, confirm each workstation has its own individual ground connection. Static discharge events can result in billions of dollars in damage annually, making proper grounding essential.
When installing your common point ground, follow these essential steps:
- Mount your grounding hub or block to the workbench using #10 screws, making sure it's easily accessible
- Install conductive snaps on your anti-static mats and connect them to the grounding hub using appropriate cables
- Test all connections with an ohmmeter to verify proper resistance levels to ground
You'll want to use multi-grounding hubs equipped with standard banana jacks and ring terminals for your setup. Connect these using a 10-foot black tinsel wire PVC cord with a #10 ring terminal.
Don't forget to manage your ground wires neatly using wire brackets to prevent tripping hazards. Regular testing of your ground connections is vital – use tools like the Desco 98130 AC Outlet Analyzer to verify proper electrical outlet wiring.
Workspace Layout Best Practices
Properly organizing an anti-static workstation's layout requires careful attention to both ergonomic and ESD safety principles. You'll need to position your equipment directly in front of your workstation while ensuring at least 20 inches of under-desk clearance and a minimum width of 27½ inches for your work surface. Use a surface resistivity meter to verify proper grounding connections across all workstation components.
To maintain proper static control, you'll want to connect all grounding components to the green wire building ground point. Your workspace should include static dissipative materials with resistance between 1 megohm and 1 gigohm, and you'll need to eliminate or cover any insulators like carpets or wood surfaces with grounded materials.
Set up your workstation components systematically: lay the table mat flat with snaps facing you, connect your wrist strap directly to the common point ground, and position your floor mat in front of the workbench. Don't forget to use heel grounders for complete personnel grounding.
In low humidity environments, you'll need additional precautions like ionizers and anti-static floor mats. Keep your cables organized and secured to prevent tripping hazards and static buildup.
Remember to position your equipment to maintain relaxed shoulders and proper wrist angles not exceeding 5 degrees.
Testing and Maintenance Procedures
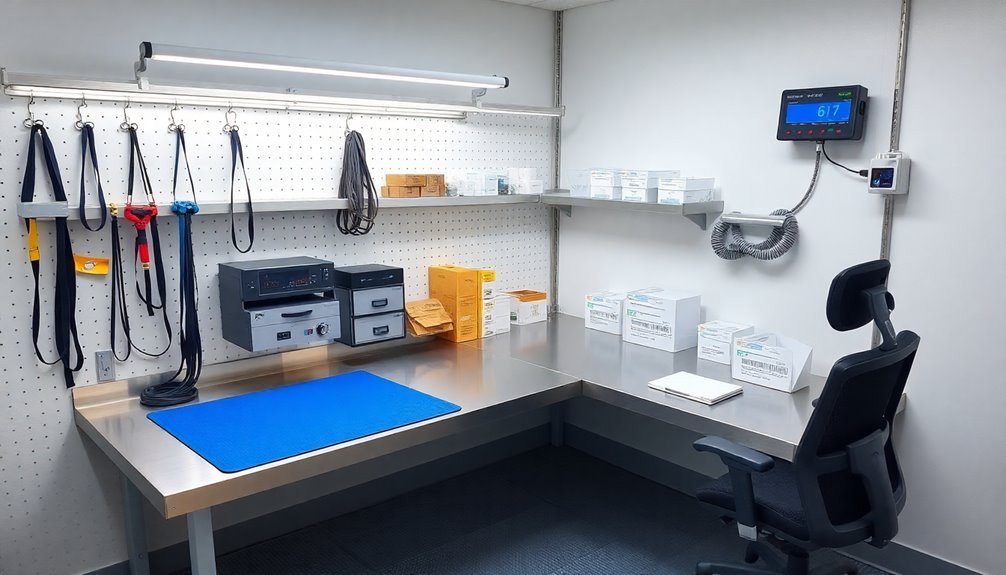
Maintaining a reliable anti-static workstation requires regular testing and thorough maintenance procedures. To guarantee your workspace meets ESD protection standards, you'll need to conduct both surface resistance and surface-to-ground tests using an SRT kit meter with heavy electrodes. Place these electrodes at different locations on your ESD mat and aim for readings between 1 x 10^6 and 1 x 10^10 ohms. Annual certification must be completed and documented for all ESD stations to maintain compliance.
Keep your anti-static workstation in top condition by following these essential maintenance steps:
- Clean your ESD mat regularly using appropriate cleaning products that won't generate static charges
- Inspect all grounding cables, connections, and wrist straps for wear or damage
- Monitor and control humidity levels while maintaining detailed maintenance records
Don't forget to calibrate your testing equipment regularly. Start by checking your SRT kit meter's battery life and replace batteries when needed.
You should also verify that each ESD station remains electrically isolated from ground and includes the correct number of meg-ohm resistors for your mat length.
Remember to document all test results using the ESD Station Certification Record (FRM-1145) for compliance and tracking purposes.
Equipment Positioning and Connections
You'll want to position your ESD mats with the button side facing up on all work surfaces, creating a network of controlled static discharge points throughout your workstation.
Connect each mat's grounding cord to both the button and a common ground point, ensuring all equipment shares the same electrical potential.
Your strategic layout should maintain proper resistance levels between 1.0 x 10^6 and 1.0 x 10^9 ohms, while keeping cables organized and secured to prevent workplace hazards. Regular use of wrist grounding straps helps maintain consistent personal grounding when handling sensitive electronic components.
Strategic Ground Point Layout
The strategic placement of equipment in an anti-static workstation directly impacts its effectiveness in preventing ESD damage. You'll need to position your components to create the shortest possible path to the common ground point, guaranteeing all workstation elements share the same electrical ground connection.
This setup minimizes the risk of static buildup and provides reliable discharge paths for any accumulated charges.
When laying out your ground points, focus on these critical elements:
- Position your workbench components close to the main ground connection, using secure attachments that you'll need to check regularly
- Install grounding snaps at consistent intervals on your anti-static mats, connecting them to the common ground point
- Set up your personnel grounding equipment, like wrist straps and heel grounders, with direct access to the ground plane
You'll want to incorporate a thorough ground plane design that connects all components, including PCBs and connectors. For higher frequency applications, implement a multi-ground strategy while avoiding ground loops.
Remember to verify your grounding system's integrity through regular testing and maintain all connections to guarantee continuous protection against ESD damage.
Mat Placement Best Practices
Proper mat placement serves as the foundation of an effective anti-static workstation. You'll need to position your anti-static mats on conductive work surfaces or connect them directly to electrical outlets using grounding cables.
Make sure your mats cover the entire work area and don't place them on insulating materials like carpets or wooden surfaces, as this will reduce their effectiveness.
You'll want to establish reliable ground connections using appropriate grounding cables and 10mm snaps. Install these snaps at the mat's corner or every 10 feet for longer mats.
It's vital to connect your wrist straps to the same ground point as your ESD mat through a common point ground system.
For complete protection, integrate your mats with other ESD components like wrist straps and heel grounders. If you're working in an area with mobile personnel, you'll need ESD floor mats combined with proper footwear.
Don't forget to install ESD equipment testers to monitor your grounding system's effectiveness. Remember to follow ANSI/ESD S6.1 standards and regularly test your setup to maintain compliance and guarantee optimal static protection.
ESD Protection Performance Standards
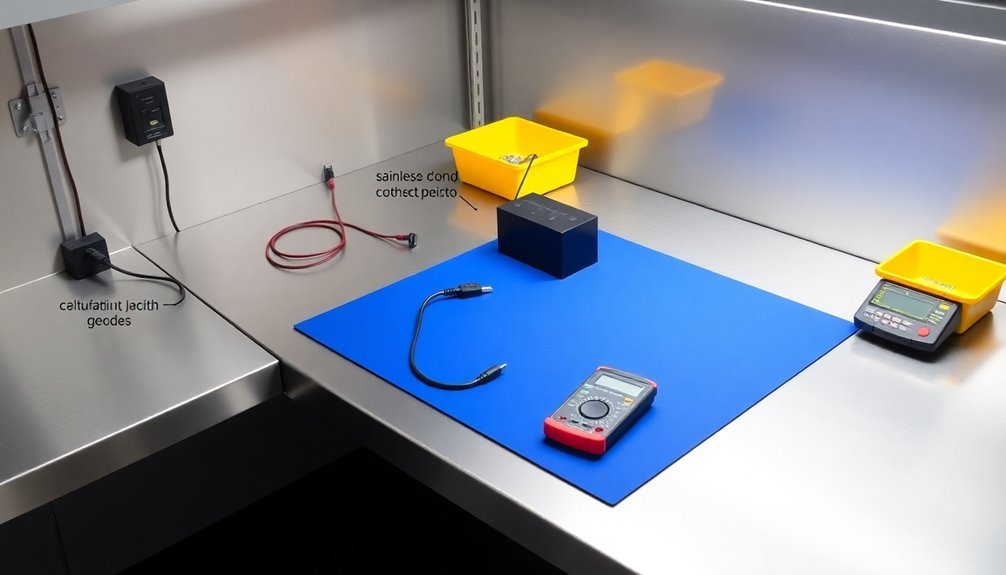
Successful ESD protection depends heavily on adhering to established industry standards and performance requirements. You'll need to follow key standards like ANSI/ESD S20.20 and IEC 61340-5-1, which provide exhaustive guidelines for creating and maintaining effective electrostatic protective areas (EPAs). These standards define specific limits for ESD control items and measures, ensuring your workstation meets industry requirements.
When setting up your anti-static workstation, you'll need to comply with these essential performance standards:
- ESDA framework requirements for developing and implementing your ESD control program
- JEDEC JESD625B specifications for proper grounding techniques and ESD-safe material selection
- IEC 61340-5-1 guidelines for creating a complete EPA that shields components from damage
Your workstation's performance must be evaluated under specific environmental conditions, particularly regarding humidity levels.
You'll need to implement continuous monitoring devices to verify all grounded components maintain their path to ground.
Remember that different industries may require additional specific standards – for instance, if you're working with the Department of Defense, you'll need to comply with MIL-STD-1686 requirements on top of general ESD protection standards.
Frequently Asked Questions
Can Wireless Devices Be Safely Used at an Esd-Protected Workstation?
Yes, you can safely use wireless devices at ESD workstations if you've implemented proper grounding measures, use ESD-safe equipment, and guarantee the device is protected. Always follow strict ESD protocols while handling them.
How Does Humidity Affect ESD Protection Effectiveness?
You'll find that higher humidity substantially improves your ESD protection by increasing surface conductivity. When you maintain levels above 40%, you'll reduce static build-up and minimize the risk of damaging electronic components.
Are ESD Protection Measures Necessary When Working With Low-Voltage Electronics?
Yes, you'll absolutely need ESD protection for low-voltage electronics. They're actually more susceptible to damage than higher-voltage components, as CMOS devices can be destroyed by static charges you can't even feel.
What Emergency Procedures Should Be Followed During an ESD Control Failure?
You'll need to immediately isolate the affected area, shut down equipment if necessary, assess damage, document the incident, and contain affected components. Don't forget to use ESD-safe materials during your emergency response.
How Often Should Ionizer Performance Be Verified in Cleanroom Environments?
You should verify your cleanroom ionizer's performance at least every 6 months. However, if you're working in critical environments, you'll need more frequent testing – typically monthly or quarterly for peak performance.
In Summary
You'll minimize ESD risks by following these seven standards for your anti-static workstation. Remember to regularly test your grounding systems, maintain proper surface materials, and guarantee all personnel consistently use required protective equipment. Don't overlook the importance of correct equipment positioning and workspace layout. By implementing these practices, you're safeguarding sensitive components and maintaining a reliable ESD-protected environment.
Leave a Reply