The best anti-static packaging solutions depend on your specific needs, but static shielding bags offer superior protection through multi-layer construction and Faraday Cage effects. You'll find these bags in various thicknesses (2-8 mil) with aluminum and polyester layers that shield sensitive electronics. Anti-static polyethylene bags and moisture barrier materials work well for less sensitive items, while conductive materials provide robust protection for critical components. You can also opt for anti-static bubble wrap or customizable foam solutions to meet unique requirements. Understanding the full range of options will help you make the most cost-effective choice for your static-sensitive shipments.
Understanding Anti-Static Packaging Materials
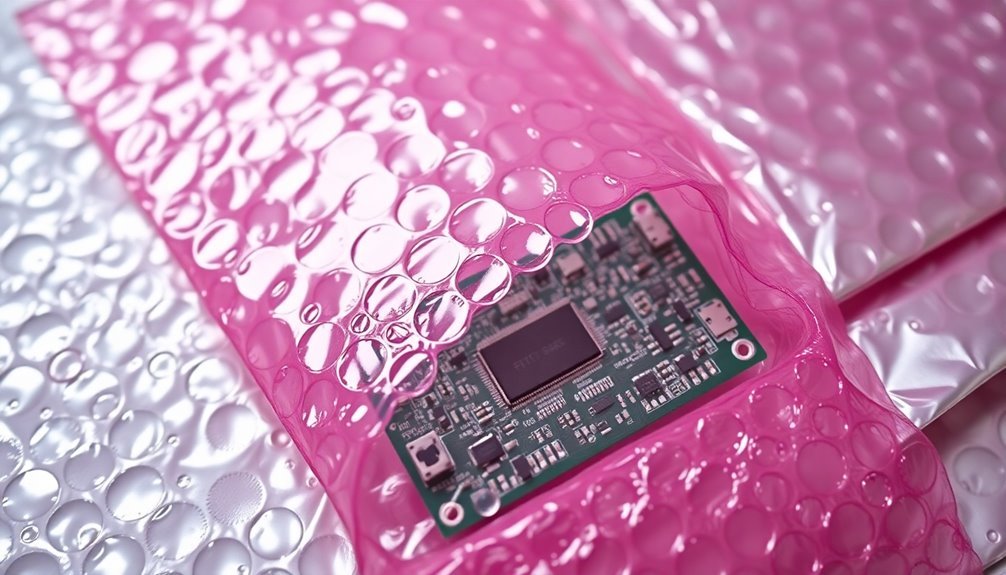
According to industry standards, anti-static packaging materials fall into several distinct categories, each designed to protect sensitive electronics from electrostatic discharge (ESD).
You'll find that static shielding bags offer the highest level of protection through their multi-layer construction, featuring aluminum, static dissipative, and polyester layers. These bags provide Faraday Cage protection in both metal-in and metal-out configurations. The metal-in variety remains the most cost-effective and commonly used option. With 40% transparency, these bags allow for easy visual inspection of components without opening the packaging.
For less critical applications, you can use anti-static polyethylene bags, which come in pink or black varieties. While they don't provide Faraday Cage protection, they're humidity-independent and prevent static buildup effectively.
When you need moisture protection alongside ESD safety, moisture barrier materials combine metalized polyester layers to guard against multiple threats, including corrosion and physical damage.
Specialized anti-static materials offer specific solutions for unique requirements. You'll find conductive materials that provide Faraday Cage protection, and black conductive tubing made from carbon-loaded polyethylene.
These options are often amine-free and N-octanoic acid free, making them ideal for applications where contamination and outgassing concerns exist. The materials range in thickness from 2-8 mil, giving you flexibility in choosing the right protection level.
Types of Anti-Static Protection
These extensive anti-static protection options give you multiple ways to safeguard your sensitive electronic components.
When choosing your packaging solution, you'll find anti-static bags are a versatile option, featuring multiple protective layers and both static-dissipative and static-shielding varieties to match your specific needs.
For items requiring cushioning, you can use anti-static bubble wrap or bubble bags, which offer protection without generating harmful static electricity. A charge of just 30 volts can damage electronic components. The commonly used pink coloring makes these materials easily identifiable in packaging environments.
Unlike standard bubble wrap, these modified versions won't damage your electronics, and they'll help reduce shipping costs due to their lightweight nature.
If you're looking for customizable protection, anti-static foam and void fill packaging provide excellent options.
You can cut foam sheets to size for precise fits, while anti-static void fill works similarly to traditional packing peanuts but without static risks.
For maximum protection, you'll want to take into account static shielding materials.
These specialized solutions create a Faraday cage effect through metalized polyester construction, offering superior protection for highly sensitive electronics.
The translucent nature of many static shielding materials allows you to inspect packaged items without compromising their protection.
Selecting the Right Packaging Solution

To select effective anti-static packaging, you'll need to carefully assess your shipping requirements, including the sensitivity of your electronic components and the environmental conditions they'll face during transit.
You should pair your products with appropriate protective materials, considering factors like static dissipation levels, durability requirements, and whether you need reusable or single-use solutions. Working with a supplier that offers custom sizing options can ensure optimal protection for your specific products. Using thermoformed plastic trays provides a durable and cost-effective solution for secure transport.
When matching materials to products, you'll want to guarantee compliance with industry standards while balancing cost-effectiveness and the specific protection needs of your electronic items.
Evaluate Your Shipping Needs
Before selecting anti-static packaging, you'll need to carefully assess your specific shipping requirements based on several key factors.
Start by evaluating the environmental conditions your products will face during transit, including temperature fluctuations and humidity levels that can affect the performance of anti-static materials.
Consider your product's sensitivity to electrostatic discharge. If you're shipping highly sensitive electronic components, you'll need advanced static shielding solutions, while less critical items might only require static-dissipative packaging.
Your shipping method also plays an essential role – air freight typically demands more robust protection due to increased static generation risks compared to ground transportation.
Don't forget to verify regulatory compliance requirements for your industry and product type. You'll need packaging that meets recognized standards for electrostatic protection to guarantee both legal compliance and customer satisfaction. Partnering with suppliers who follow IEC 61340-1-5 standards ensures your packaging meets international quality benchmarks.
If you're planning frequent shipments, consider investing in reusable packaging solutions to reduce long-term costs.
Remember that your packaging must maintain its protective properties throughout the entire shipping journey while withstanding handling and potential impacts, so choose materials that remain effective under varying conditions.
Match Materials To Products
Selecting appropriate anti-static packaging materials depends directly on your product's sensitivity level and handling requirements.
For standard electronic components, static-dissipative bags or anti-static void fill packaging will provide adequate protection. These options are cost-effective and suitable for non-critical applications.
If you're shipping highly sensitive components, you'll need more robust protection. Metal-in or metal-out static shielding bags offer superior ESD protection, with metal-out bags providing faster static dissipation.
For delicate circuit boards or microprocessors, combine anti-static bubble wrap with static shielding film for thorough protection against both physical and electrical damage.
For uniform-sized items, consider anti-static bubble bags with self-sealing features.
If you're handling larger electronic components, conductive bins or thermoformed plastic trays made from PETG or HDPE provide excellent protection and reusability.
When dealing with irregularly shaped items, anti-static polyethylene foam can be customized to create precise fits.
For industry-specific needs, specialized solutions like ESD polycarbonate trays offer high rigidity, while conductive ABS trays provide a balance of conductivity and durability.
Match your packaging choice to both your product's sensitivity and your operational requirements.
Environmental Impact of Static Protection
The environmental impact of anti-static packaging presents both challenges and opportunities for sustainability in the electronics industry. While these materials help prevent damage to electronic components and reduce waste from damaged products, their production and disposal require careful evaluation of environmental trade-offs.
You'll find that modern anti-static packaging solutions offer several eco-friendly benefits. Materials like Evolon feature compact fiber structures that use fewer resources while maintaining protective qualities. Companies like ITB Packaging have developed innovative designs that use 30% less material than traditional dividers, and you can opt for reusable solutions to further reduce your environmental footprint. These solutions help reduce the $5 billion annual cost associated with ESD damage in the electronics industry. The threadless production process eliminates potentially harmful thread beading interactions with sensitive electronics.
However, you'll need to assess certain environmental challenges. The production of anti-static materials involves energy consumption and resource depletion, while additives and coatings can complicate recycling efforts.
To minimize these impacts, you can choose collapsible designs that reduce storage space and shipping emissions, or explore custom solutions that optimize material usage. Many manufacturers are now developing eco-friendly alternatives and sustainable production processes, making it easier for you to balance protective requirements with environmental responsibility.
Industry Standards and Compliance
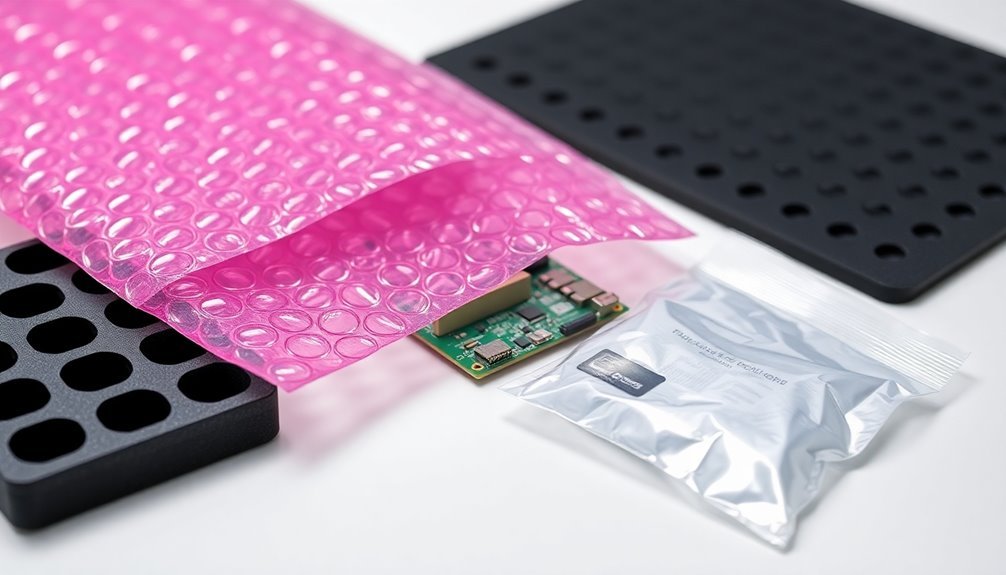
While environmental considerations shape packaging choices, understanding industry standards guarantees your anti-static solutions meet regulatory requirements.
You'll need to verify your packaging materials comply with key standards like ANSI/ESD STM11.11, which requires surface resistance between 106 and 109 ohms, and ASTM D257 for testing DC resistance.
Your anti-static packaging must maintain its protective characteristics throughout the supply chain. Quality testing should be conducted under natural light conditions for accurate inspection results.
For proper compliance, you'll want surface resistivity between 105 and 1012 ohms per square for antistatic materials, while electrostatic shielding materials should measure less than 1 x 104 ohms per square. Conductive materials need to stay below 1 x 105 ohms per square.
Don't forget proper identification – you must mark packages as "ESD shielding," "Conductive," or "Antistatic."
Your materials can't outgas or contain substances that might damage packaged products.
When selecting packaging, you'll need to meet MIL-STD 3010 for package durability and MIL-PRF-81705 for barrier materials.
Remember that static decay time should be .50 seconds or less at 50% relative humidity, as specified by NFPA-99.
Cost Benefits of Static Control
Investing in anti-static packaging pays off substantially, with the electronics industry facing up to $5 billion in annual losses from ESD damage. You'll find that proper anti-static solutions can reduce static-related failures by 25%, leading to significant cost savings across your operations.
You can expect both immediate and long-term financial benefits when implementing anti-static packaging solutions. Here's how the savings break down:
Cost Area | Impact of Anti-Static Packaging |
---|---|
Product Damage | Reduces losses by up to 33% |
Returns | Fewer product returns and replacements |
Operations | Improved efficiency in handling and processing |
Logistics | Reduced reverse logistics costs |
Long-term | Sustained protection and customer satisfaction |
Customization Options and Applications

Designed to meet diverse industry needs, anti-static packaging solutions offer extensive customization options across materials, sizes, and specifications.
You'll find tailored solutions ranging from custom-sized containers to specialized materials like PETG Anti-Static and Conductive Styrene, all adaptable to your specific requirements.
When you're protecting sensitive electronic components, you can choose from various applications. For shipping motherboards, GPUs, and integrated circuits, you'll need static shielding bags that create a Faraday Cage effect.
If you're storing SMD components, anti-static foam inserts and thermoformed plastic trays provide both protection and organization.
The material selection process lets you match your protection level to your needs. You can opt for static dissipative materials in non-critical applications or upgrade to full static shielding materials for highly sensitive components.
For additional customization, you'll find options in material thickness, density, and specialized features like humectant additives in LDPE.
You can further enhance your packaging with custom printing for branding and labeling, while specialized void fill materials guarantee protection against physical impacts during transit.
Metal-in and metal-out bags offer varying levels of static shielding based on your requirements.
Future of Anti-Static Packaging
Innovation drives the future of anti-static packaging toward smarter, more sustainable solutions.
You'll see a significant shift toward biodegradable and recyclable materials, with manufacturers focusing on natural polymers that offer inherent static-dissipative properties. This eco-friendly approach will help you reduce waste while maintaining effective protection for your sensitive electronic components.
Material technology advancements will provide you with enhanced conductivity and improved static-dissipative properties.
You'll benefit from new nanoparticle innovations that offer superior anti-static performance and better moisture barriers, guaranteeing your products stay protected even in challenging environments.
Smart packaging integration will revolutionize how you monitor and protect your items.
You'll be able to track package conditions in real-time through embedded sensors and RFID tags, while intelligent materials automatically adjust to environmental changes to maintain ideal protection levels.
These innovations will operate within a framework of stricter regulatory compliance and standardization.
You'll need to verify your packaging meets international standards like ANSI/ESD S20.20, as global harmonization efforts continue to evolve. Regular audits and certifications will become increasingly important to maintain quality and compliance in your anti-static packaging solutions.
Frequently Asked Questions
How Long Does Anti-Static Protection Last After the Package Is Opened?
Once you've opened your anti-static package, protection diminishes immediately. You'll need to handle components quickly, as the protective properties won't last. For ongoing protection, you'll want to reseal or transfer items promptly.
Can Anti-Static Packaging Be Damaged by Extreme Temperatures During Shipping?
Yes, your anti-static packaging can be damaged by extreme temperatures. High heat can degrade the material's ESD protection properties, while severe temperature changes might make some materials brittle and less effective at protecting components.
Are There Special Storage Requirements for Unused Anti-Static Packaging Materials?
You'll need to store unused anti-static packaging in a humidity-controlled, clean environment away from sunlight and moisture. Don't fold materials, and follow manufacturer's guidelines for temperature ranges and expiration dates.
What Cleaning Methods Are Safe to Use on Anti-Static Packaging?
You can safely clean anti-static packaging by using a dry, lint-free cloth for dust removal. For tougher spots, use a slightly damp cloth or specialized anti-static cleaners, but avoid abrasive materials.
Can Anti-Static Packaging Interfere With Barcode Scanning or RFID Tracking?
While most anti-static materials won't affect your barcode scanning, metalized static shielding bags can interfere with RFID tracking. You'll find regular anti-static bags and plastic trays work fine with both scanning methods.
In Summary
You've explored the world of anti-static packaging and now understand the importance of protecting sensitive electronics from static discharge. Whether you're choosing pink poly bags, metallic films, or conductive foams, selecting the right solution depends on your specific needs and budget. Remember to take into account environmental impact and industry standards when making your choice, and stay informed about emerging technologies in static protection.
Leave a Reply