When managing antistatic packaging, you'll need to follow seven key standards to maintain effectiveness. Keep your storage environment at 68°F (20°C), implement proper moisture control, and protect materials from UV exposure. You must conduct regular surface resistance testing according to ANSI/ESD guidelines and maintain detailed documentation. Store ESD bags using FIFO inventory methods, perform quarterly inspections, and guarantee proper sealing techniques without staples. For pink antistatic foam, you'll need extra attention to testing schedules. Understanding these standards is just the beginning of mastering ESD protection for your sensitive components.
Understanding Shelf Life Basics
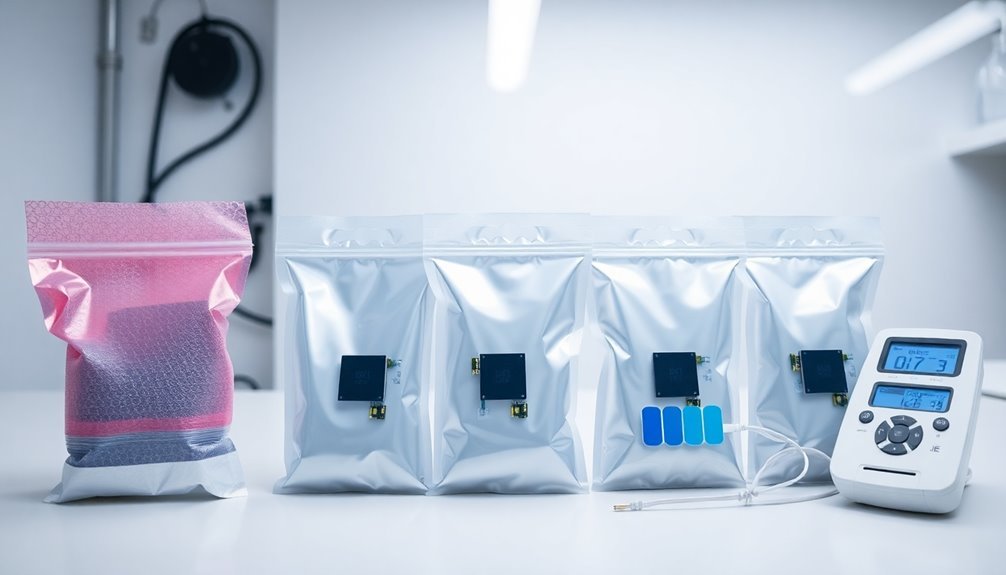
A package's shelf life stands as a significant measure of its usability over time.
Modern canning technology emerged over 200 years ago and revolutionized food preservation capabilities.
You'll find two primary types of shelf life measurements: "best if used by" periods, which focus on maintaining ideal taste and nutritional value, and "life sustaining" periods, which determine how long items remain safely consumable.
You need to understand that shelf life depends heavily on food constituents. While minerals and carbohydrates remain relatively stable, fats can become rancid, proteins can deteriorate, and vitamins often break down due to heat, light, and oxidation exposure. Excess moisture in storage can lead to rapid food spoilage and encourage microbial growth.
Even as these components change, caloric content typically stays constant.
You'll encounter different storage categories that affect shelf life management. Shelf-stable foods can safely remain at room temperature, while refrigerated and frozen items require specific temperature controls.
Dehydrated foods offer impressive longevity, with fruits and vegetables lasting up to 25 years and grains extending to 30 years when properly stored.
To track shelf life effectively, you'll rely on specific codes (SLCs) that identify storage periods in months.
The 85% rule guarantees products display both expiration dates and essential manufacturing information for proper monitoring and rotation.
Storage Environment Requirements
Proper storage goes hand-in-hand with shelf life management when it comes to antistatic packaging. You'll want to maintain a consistent temperature of around 68°F (20°C) and guarantee your storage area stays dry and well-ventilated. Annual compliance audits should be conducted to verify storage conditions meet ESD standards. Following MIL-PRF-81705 standards, all barrier materials must include clear markings indicating their specification compliance and protective qualities.
Moisture and extreme temperatures can cause the aluminum shielding layer to oxidize, compromising the bag's protective properties.
Light exposure is another critical factor you'll need to manage. Keep your ESD bags away from direct sunlight and UV light, as these can greatly degrade the materials and reduce their effectiveness.
Store them in a dark or UV-protected environment whenever possible.
When handling ESD bags, you'll need to:
- Implement a FIFO (First-In-First-Out) system to prevent older inventory from deteriorating in storage
- Never use staples to seal the bags – this damages their protective barrier and renders them ineffective
- Use only approved methods like heat sealing or ESD tape for proper closure
Testing and Verification Methods
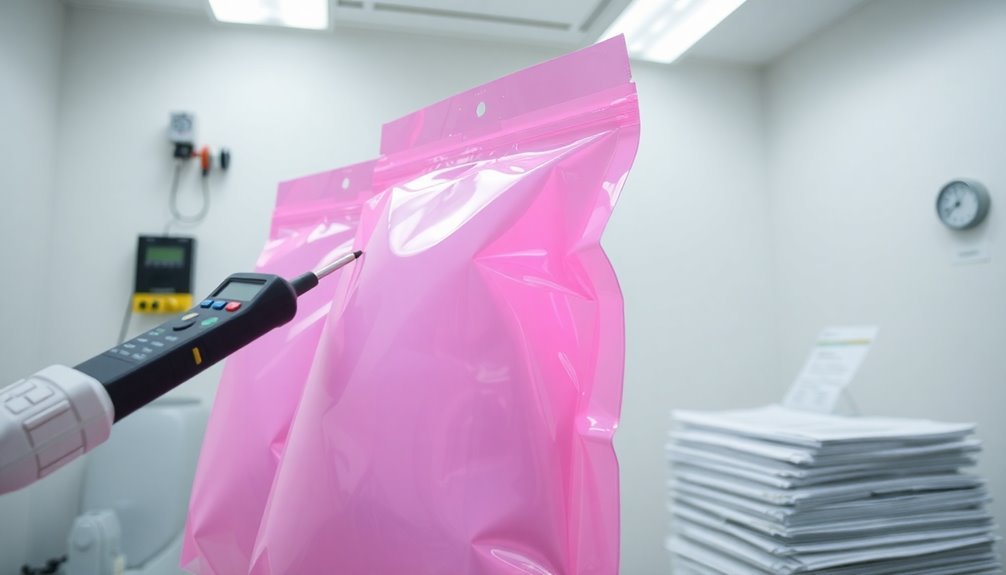
Testing antistatic packaging's effectiveness requires adherence to strict industry standards and methods.
You'll need to follow key testing protocols, including ANSI/ESD S11.4 for qualification requirements and ANSI/ESD STM11.31 for static shielding effectiveness, which must show shielded energy levels below 20 nJ. Counterfeit ESD materials have become a significant concern, making verified lab testing crucial.
Before conducting any tests, you must precondition your samples in an electrostatic test chamber at 12%±3% relative humidity and 73±5°F for at least 24 hours.
Don't test under ambient conditions, as this can compromise your results. Visual inspection alone cannot guarantee compliance as physical measurements are required. You'll need properly calibrated equipment, including electrometers and concentric ring fixtures.
You'll conduct several specific tests: surface resistance (per ANSI/ESD STM11.11), volume resistance (per ANSI/ESD STM11.12), and electrostatic decay (per Mil-STD-3010C, Method 4046).
The decay test must show a reduction from 5kV to 0 volts in under 2.0 seconds. Additionally, you'll need to verify charge retention using the Faraday Cup method and assess static shielding capabilities.
Remember to maintain proper documentation of all test results, including manufacturer traceability and lot code information.
Material Types and Longevity
Static-sensitive electronics demand specific packaging materials, each engineered for different levels of protection.
You'll find conductive packaging, made with carbon-loaded plastics, provides a direct path to ground for static charges, making it ideal for highly sensitive components.
Static dissipative materials, like amine-free polyethylene bags, work by slowing down charge flow, offering adequate protection for less critical items like cables. ESD damage accounts for approximately 25% of all electronics failures.
For maximum protection, you'll want to evaluate shielding packaging that creates a Faraday Cage effect.
These metallized polyester materials are particularly effective for printed circuit boards and other vulnerable electronics. The buried metal construction enhances the protective shielding capabilities.
When moisture poses an additional threat, multi-layered moisture barrier packaging offers thorough protection against both static and corrosion.
- Don't risk thousands in damaged components by using the wrong packaging – conductive materials offer immediate charge dissipation for your most sensitive parts.
- Save money on non-critical items by matching the protection level to your needs – static dissipative materials work perfectly for basic components.
- Protect your investment in harsh environments by choosing moisture barrier packaging that guards against multiple threats simultaneously.
Choose your packaging based on component sensitivity, environmental conditions, and required longevity of protection.
Pink Foam Special Considerations
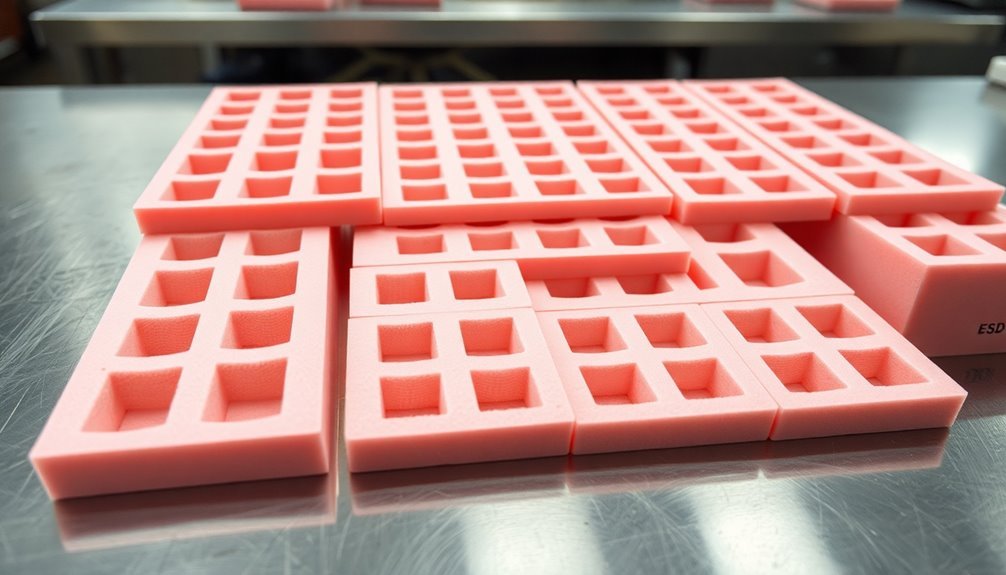
You'll need to regularly test your pink ESD foam to guarantee it maintains its antistatic properties, as these materials naturally degrade over time through exposure to environmental factors like humidity, temperature, and handling. The material's closed-cell structure provides excellent resilience during its effective lifespan. Foreign object debris can be a significant concern when using foam materials in sensitive electronics environments.
When planning your storage solutions, consider that pink foam's uncertain shelf life and deterioration patterns make it a risky choice for long-term ESD protection of sensitive components.
To mitigate these risks, you should explore permanent alternatives such as carbon-loaded plastics or metallized bags that offer more stable and predictable ESD protection characteristics.
Testing Requirements Over Time
Within the domain of antistatic packaging, maintaining consistent ESD protection requires rigorous testing protocols and special attention to material degradation.
You'll need to follow ANSI/ESD S541 guidelines while implementing a thorough compliance verification plan that includes surface resistance and shielding effectiveness tests.
To guarantee your ESD packaging remains effective, you must:
- Conduct annual audits to verify that all materials meet regulatory standards and haven't deteriorated beyond acceptable limits.
- Test packaging materials regularly, especially if they've been exposed to environmental stressors like heat, moisture, or UV light.
- Document and track all testing results to identify trends and potential issues before they compromise your sensitive components.
You shouldn't store ESD packaging materials in environments with extreme temperatures or humidity levels.
Keep them in their original packaging and implement a FIFO (First-In-First-Out) inventory system to prevent using outdated materials.
When you notice any signs of damage, such as tears, rips, or scratches, dispose of the affected items immediately.
Remember that certain materials, like pink foam, have limited shelf lives and require more frequent testing to maintain their protective properties.
Material Degradation Risk Factors
Through extensive industry testing, pink foam has emerged as one of the most vulnerable materials to degradation in antistatic packaging applications. You'll find that pink foam's unpredictable degradation patterns and short shelf life make it particularly challenging for long-term ESD protection strategies.
Risk Factor | Impact | Required Action |
---|---|---|
Short Lifespan | Rapid loss of ESD protection | Regular testing and replacement |
Surface Contact | Component damage potential | Minimize direct contact |
Environmental Exposure | Accelerated deterioration | Control storage conditions |
When you're working with pink foam, you'll need to monitor several critical factors. The material's tendency to break down can create foreign object debris (FOD), which poses additional risks to sensitive components. You'll notice that regular compliance verification becomes essential, as the foam's antistatic properties can degrade without visible signs. Don't rely on visual inspection alone – implement a strict testing schedule to guarantee continued effectiveness.
Remember that pink foam's intimate contact with sensitive components increases the risk of damage if degradation occurs. You'll need to establish clear replacement protocols and maintain detailed documentation of material age and testing results to prevent ESD-related failures.
Alternative Storage Solutions
Given pink foam's inherent limitations, exploring alternative storage solutions can greatly improve your ESD protection strategy. High-density cross-linked polyethylene foam offers you a more permanent solution, while conductive foam provides superior static discharge protection.
You'll find that combining different materials can create a thorough protection system tailored to your specific needs.
For maximum protection of your sensitive electronic components, consider these proven alternatives:
- Custom die-cut inserts and trays that perfectly cradle your components, eliminating movement and providing consistent static protection throughout the storage period.
- Conductive foam solutions that offer reliable, long-term static dissipation without the shelf-life concerns associated with pink anti-static foam.
- High-density polyethylene foam with adhesive backing that guarantees secure placement and enhanced protection against physical damage.
You can further strengthen your storage strategy by implementing multiple protection layers.
Consider using ESD-safe bags in conjunction with foam inserts, or combine conductive containers with custom-cut foam padding. These solutions provide more reliable long-term protection than pink foam alone, guaranteeing your sensitive components remain safe throughout their storage lifecycle.
Shielding Bag Shelf Life
You'll maximize your shielding bags' protection period by storing them in controlled environments at 68°F with proper ventilation and minimal exposure to sunlight.
Your bags should undergo regular compliance testing to verify they still meet ANSI/ESD S541-2018 standards, especially as they age.
When properly maintained in ideal conditions, your shielding bags can retain their protective properties for up to 5 years, though it's crucial to implement a FIFO inventory system.
Storage Extends Protection Period
Proper storage conditions can considerably extend the shelf life of your ESD shielding bags, with some materials lasting up to 5 years in controlled environments.
You'll need to maintain a stable temperature of around 68°F (20°C) in a dry, well-ventilated space while keeping the bags in their original packaging.
It's essential to protect your investment by avoiding exposure to UV light, which can oxidize the aluminum shielding layer.
To maximize your ESD bags' longevity and effectiveness, implement these vital practices:
- Store bags away from heat, cold, sunlight, and moisture – these elements can quickly degrade your materials and compromise their protective properties.
- Conduct regular inspections and annual spot checks to verify your bags haven't deteriorated or become damaged.
- Follow a First In First Out (FIFO) inventory system to maintain fresh stock and prevent using outdated materials.
Remember that different materials have varying shelf lives – dissipative materials typically last 12 months, while metallized shielding bags offer extended protection.
You'll want to discard any bags showing signs of damage, such as rips, tears, or scratches.
Don't take chances with questionable bags; recycling them and ordering new ones is more cost-effective than risking damage to sensitive components.
Testing Requirements Over Time
Regular testing of ESD bags assures they maintain their protective qualities throughout their service life. You'll need to follow strict testing protocols and verification procedures to guarantee your bags meet ANSI/ESD S541 standards. Plan periodic surface resistance tests and add them to your compliance verification schedule.
Test Type | Frequency |
---|---|
Surface Resistance | Quarterly |
Visual Inspection | Monthly |
Shielding Effectiveness | Semi-annually |
Environmental Controls | Weekly |
Your storage conditions considerably impact the bags' effectiveness. Keep them in a controlled environment at 68°F (20°C), away from direct sunlight and moisture. You'll maximize shelf life by implementing a FIFO inventory system, ensuring older bags get used first.
Remember to document all testing results and maintain detailed records of your bag inventory. If you find any ripped, torn, or scratched bags during inspection, dispose of them immediately. While manufacturer warranties typically cover one year, you can extend your bags' shelf life up to five years with proper storage and regular testing. Different bag types have varying shelf lives, so you'll need to adjust your testing schedule based on whether you're using dissipative or shielding bags.
Maximum Durability Under Control
While ESD shielding bags can last up to five years in controlled environments, their durability depends heavily on storage conditions and handling practices.
You'll maximize shelf life by storing bags in a dry, well-ventilated room at 68°F (20°C), away from direct sunlight, and in their original packaging. Different types of bags offer varying lifespans – conductive bags can last beyond 5 years, while anti-static bags typically serve best within 2 years.
To maintain ideal protection for your sensitive components, you'll need to watch for environmental factors that can compromise bag integrity.
UV light exposure can degrade dissipative materials, while moisture and temperature extremes can damage metal layers through oxidation.
- Your ESD bags won't protect your valuable components if they've been compromised by poor storage – don't risk thousands in damaged electronics.
- You're putting your entire production line at risk by using degraded bags – implement FIFO processing to maintain fresh inventory.
- Your quality control depends on proper storage – maintain logs, conduct annual audits, and test surface resistance before use.
Remember to follow ANSI/ESD S541-2018 packaging standards and recycle any questionable bags rather than risking component damage.
FIFO Inventory Control
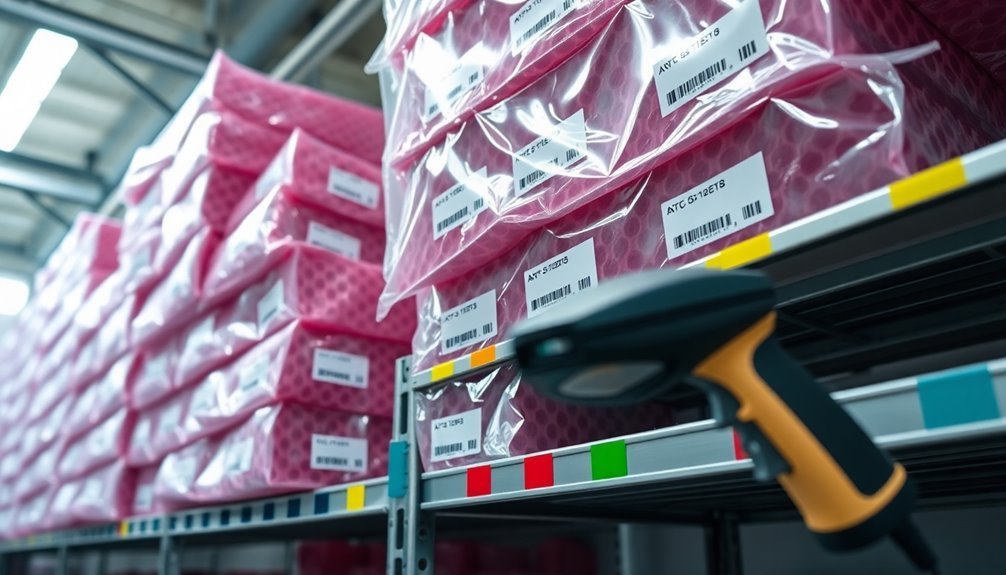
Today's fast-paced manufacturing environments demand efficient inventory management, and FIFO (First In, First Out) stands as a cornerstone method for controlling stock flow. When you implement FIFO, you'll guarantee that your oldest inventory items are sold or used first, preventing product obsolescence and maximizing your stock turnover.
To successfully execute FIFO, you'll need specialized storage systems with separate loading and unloading aisles. Live Pallet Racking, Drive Through, and AR Shuttle systems can help you maintain proper product rotation.
You'll also want to integrate a warehouse management system (WMS) to track your inventory in real-time and record entry and exit dates accurately.
FIFO's benefits extend beyond basic inventory control. You'll reduce the risk of product expiration, minimize waste, and lower storage costs. It's particularly essential when you're handling perishable items, pharmaceuticals, or technology products.
Unlike LIFO (Last In, First Out), FIFO complies with international financial reporting standards and typically results in higher net income during inflationary periods.
For ideal results, you can combine FIFO with other inventory management models while maintaining strict quality control measures.
Frequently Asked Questions
Can ESD Packaging Be Reused After Exposure to High Humidity?
You shouldn't reuse ESD packaging after high humidity exposure, as it can degrade the material's protective properties. It's best to discard the affected packaging and use fresh materials to guarantee proper ESD protection.
What Happens When Antistatic Packaging Materials Are Exposed to Extreme Cold?
When you expose antistatic packaging to extreme cold, you'll notice it becomes brittle, loses flexibility, and might crack. The material's static-dissipative properties can diminish, while cold, dry conditions increase static buildup risks.
How Do Different Cleaning Solutions Affect Antistatic Packaging Properties?
You'll damage antistatic properties if you use harsh cleaners like Dettol or IPA wipes. Instead, use mild, neutral ESD-specific cleaning solutions that won't leave residues or compromise your packaging's static-protective features.
Are There Specific Disposal Requirements for Expired ESD Packaging Materials?
You'll need to dispose of expired ESD packaging through approved hazardous waste facilities. Always check local regulations, use proper containers, and maintain disposal records. Follow manufacturer's guidelines for specific material requirements.
Can Antistatic Properties Transfer Between Materials When Stored Together Long-Term?
No, you won't see antistatic properties transfer between materials during long-term storage. Each material maintains its own inherent properties, so there's no risk of cross-contamination when you store different items together.
In Summary
You'll maximize your antistatic packaging's effectiveness by following these seven standards and implementing proper FIFO inventory control. Remember to regularly test your materials, monitor storage conditions, and pay special attention to pink foam's unique requirements. Don't forget that shielding bags have specific shelf life limitations. When you're consistent with these practices, you'll maintain peak ESD protection and avoid costly component damage.
Leave a Reply