To test static-protective packaging materials effectively, you'll need to employ five key methods. Start with surface resistance testing to measure both top-to-top resistance and resistance-to-ground points. Next, conduct static shielding performance tests using dual antennas to evaluate field strength protection. Then perform volume resistance measurements to assess conductivity through the material's thickness. You'll also want to analyze electrostatic decay rates from ±5kV to zero volts. Finally, assess triboelectric charging using Faraday cups or electrostatic field meters. Understanding these testing approaches will reveal deeper insights into your packaging material's protective capabilities.
Surface Resistance Testing Methods
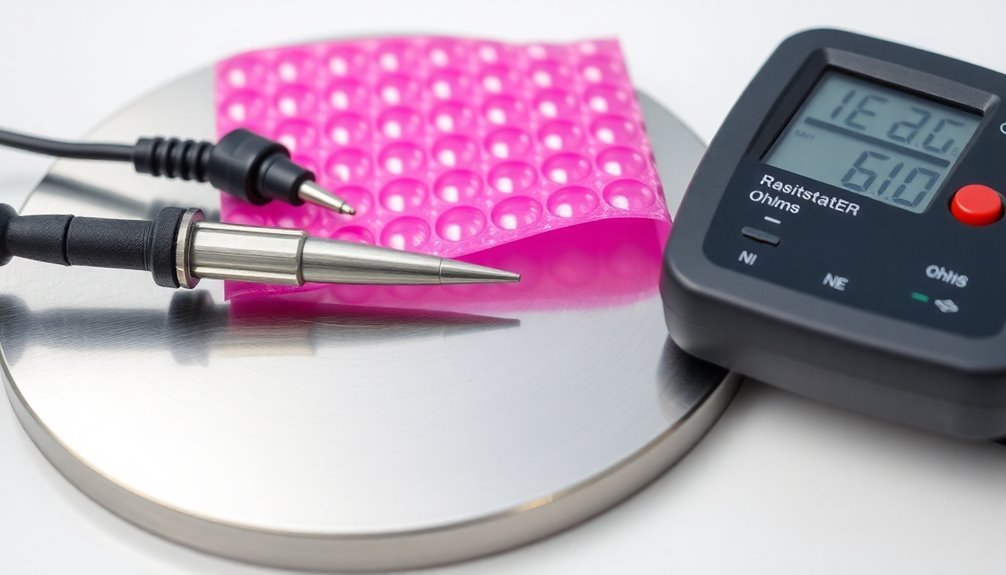
Two primary methods form the foundation of surface resistance testing: Resistance Top-to-Top (RTT) and Resistance-to-Groundable Point (RTG).
When you're conducting RTT testing, you'll measure resistance between two points on the material's top surface, while RTG testing measures resistance from a point on the material to a designated ground point.
You'll need to use metal electrodes to perform these tests effectively, and you can enhance contact quality by adding conductive rubber boots to your electrodes.
It's vital that you conduct your testing under controlled environmental conditions – specifically at 72°F ±5°F and a relative humidity of either 12% or 50%. You'll find that these conditions noticeably impact your measurements' accuracy and repeatability. Testing should adhere to commercial and military standards for consistent results.
For your testing equipment, you can choose between handheld resistance meters or complete resistivity meter kits. The handheld meters work well for testing small areas and irregular shapes, while the thorough kits offer more versatility with various electrodes and accessories.
Don't forget to use spring-loaded pogo pins for ideal surface contact, and make sure your equipment's properly calibrated to manufacturer specifications and industry standards.
Static Shielding Performance
Static shielding performance testing requires a sophisticated dual-antenna configuration, where one antenna transmits signals across various frequencies while another measures the received field strength.
You'll need to calculate the dynamic range by comparing signal strength with and without a barrier to guarantee reliable test results. The difference between maximum and minimum measurable signals must be at least 6 dB above potential shielding. Using standardized frames, you can mount your samples consistently for accurate measurements.
When testing static-protective packaging, you'll want to follow established standards like ASTM D4935-18 for planar materials or ESD STM11.31 for static shielding bags. The latter measures energy penetration using a 1kV Human Body Model discharge.
Your materials might include conductive layers, metalized polyester, or multi-layered structures that create Faraday cage effects.
You must conduct tests under controlled temperature and humidity conditions to maintain accuracy. For a thorough evaluation, you'll need to assess both near-field and far-field performance of your materials.
If you're testing complete systems, consider using MIL-STD-1377 for weapon enclosures and cables. Remember to verify your testing setup's dynamic range before measuring each sample to guarantee precise results, and test multiple samples to confirm consistency in shielding effectiveness.
Volume Resistance Measurement
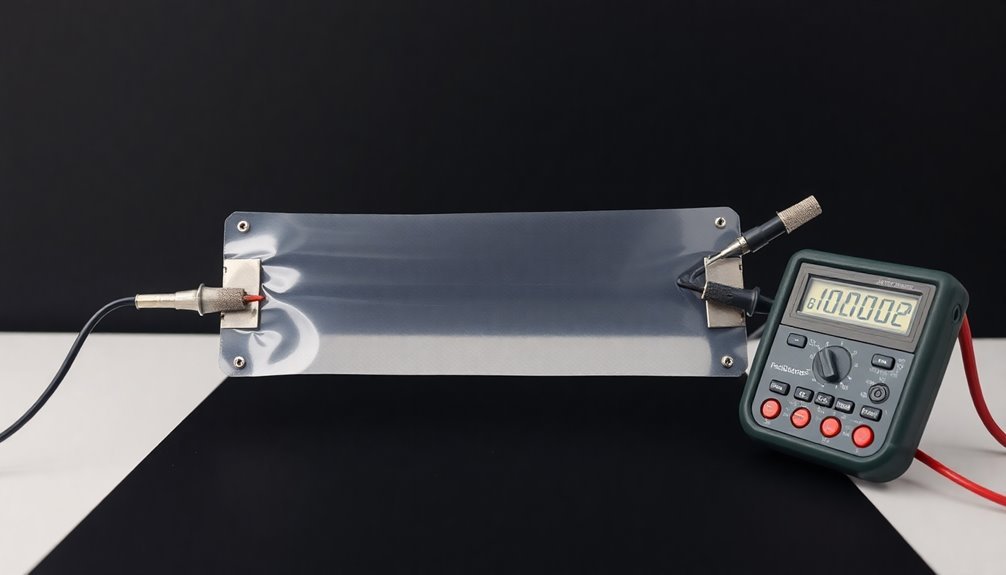
When measuring volume resistance in static-protective materials, you'll need to evaluate how well electricity conducts through the material's thickness using standardized methods like ASTM D257 or ANSI/ESD STM11.12.
You'll calculate volume resistivity by multiplying the resistance by the electrode surface area divided by the sample thickness, expressing results in ohm-cm.
To perform accurate measurements, you'll place electrodes on opposite faces of your test sample. Make sure you've properly conditioned your samples in a controlled environment at 12% ± 3% RH and 73°F ± 5°F. Testing is critical since materials can generate voltages up to 40,000 volts under certain conditions.
You'll need specialized equipment like ohmmeters and test fixtures to get reliable readings.
Your measurements should align with industry standards. For conductive materials, you'll want to see values less than 1.0 x 10^3 ohms, while insulative materials should measure greater than or equal to 1.0 x 10^11 ohms. Static dissipative materials will fall between these ranges.
Watch out for common challenges that can affect your results. You'll need to maintain good electrode contact, verify proper sample conditioning, and regularly calibrate your equipment.
Remember that material heterogeneity and environmental factors can influence your measurements, so control these variables carefully.
Electrostatic Decay Analysis
Beyond measuring volume resistance, you'll need to understand how quickly materials can dissipate static charges through electrostatic decay analysis. This vital test measures the time it takes for a material to bleed off accumulated static charge, with acceptable decay times being less than 2.0 seconds according to industry standards.
Low humidity environments can significantly affect testing outcomes since surface resistance increases when relative humidity drops. You'll conduct the testing using Method 4046 from MIL-STD-3010C, which evaluates decay from ±5kV to ±0 volts. Before testing, you must precondition your samples at 12%±3% relative humidity and 73±3°F for at least 48 hours.
Cut your samples to 3" x 5" dimensions after completing other electrical tests.
To perform the analysis, you'll use calibrated test fixtures to charge your samples to a specific voltage, then measure how quickly they dissipate the charge. For more stringent testing, you can modify the procedure to measure decay from ±5kV to ±500 volts.
This analysis is essential for protecting ESD-sensitive devices and designing effective packaging systems. You'll need to verify your materials comply with key standards like ANSI/ESD STM11.12 and ESD S541, which classify packaging materials based on their static protective characteristics.
Triboelectric Charge Assessment
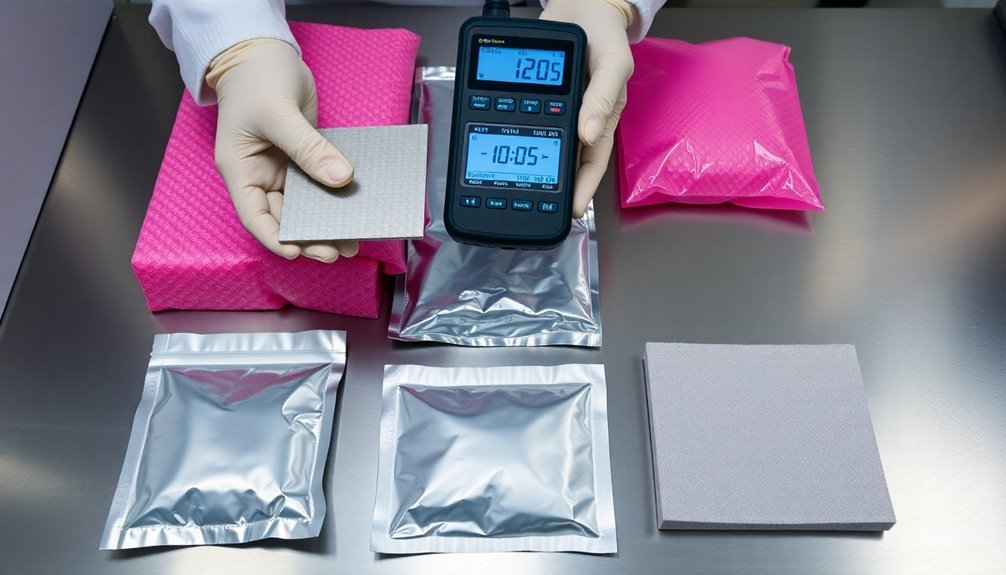
During triboelectric testing, you'll need to evaluate how materials generate static charges through contact and separation. Using a Faraday Cup or electrostatic field meter, you can measure the charge accumulation when materials interact. The process follows ESD ADV 11.2 guidelines and helps determine which materials perform best for static-protective packaging.
To effectively assess triboelectric charging, you'll want to focus on these critical steps:
- Test actual parts with their packaging materials by shaking them in a bag and measuring the charge in a Faraday Cup.
- Calculate material capacitance using the V = Q/C relationship when dropping items with known voltage.
- Evaluate material performance under various environmental conditions to guarantee consistent protection.
- Compare results between different materials to identify those with low charging propensity.
You'll need to remember that even dissipative or conductive materials can generate significant charges, so don't skip testing them. The selection of conductive, dissipative, or anti-static materials is crucial for specific applications. Focus on materials that maintain low charging characteristics while avoiding those that might outgas or damage your products.
Your test results will help you set proper material specifications and distinguish between suitable and unsuitable packaging options.
Frequently Asked Questions
How Often Should Static-Protective Packaging Materials Be Retested for Compliance?
You'll need to determine your own retesting frequency based on your product's value, failure risks, and usage conditions. Document your chosen schedule in your ESD control plan and follow it consistently.
What Environmental Factors Can Affect the Reliability of Static-Protective Packaging Tests?
You'll need to control temperature (73°F ±3°F) and humidity (12% ±3%) during testing. Watch for storage conditions, handling processes, and personnel movement, as these factors can affect your static-protective packaging test results.
Can Static-Protective Packaging Materials Be Reused After Initial Use?
Yes, you can reuse static-protective packaging up to six times if it passes inspection for tears and damage. You'll need to check the bag's quality and test its shielding properties between uses.
What Are the Storage Requirements for Maintaining Effectiveness of Static-Protective Materials?
You'll need to store static-protective materials at 73°F ±3° with 12% ±3% relative humidity. Don't expose them to extreme conditions. Keep packaging intact, without holes or tears, to maintain effectiveness.
How Do Different Handling Procedures Impact the Performance of Static-Protective Packaging?
You'll reduce your packaging's effectiveness if you roughly handle, bend, or fold materials. Excessive rubbing and improper grounding can generate unwanted static charges. Always handle with care and maintain proper ESD procedures.
In Summary
You'll find these five testing methods essential for evaluating static-protective packaging materials in your quality control process. By implementing surface resistance, static shielding, volume resistance, electrostatic decay, and triboelectric charge assessments, you're ensuring your materials meet industry standards. Don't skip any of these critical tests – they work together to verify your packaging's ability to protect sensitive electronic components from damaging static discharge.
Leave a Reply