You'll save time and guarantee accuracy during static control audits with these three calibration tips. First, verify your measurement tools against reference instruments before starting, confirming they're within acceptable tolerances. Second, maintain clean, properly labeled equipment with clear documentation of power requirements, configurations, and maintenance schedules. Third, use high-quality, laminated calibration labels that include dates, ID numbers, and integrated barcodes for efficient tracking. Following these essential steps will strengthen your audit process, and there's much more to explore about optimizing your static control procedures.
Calibration Label Management Systems
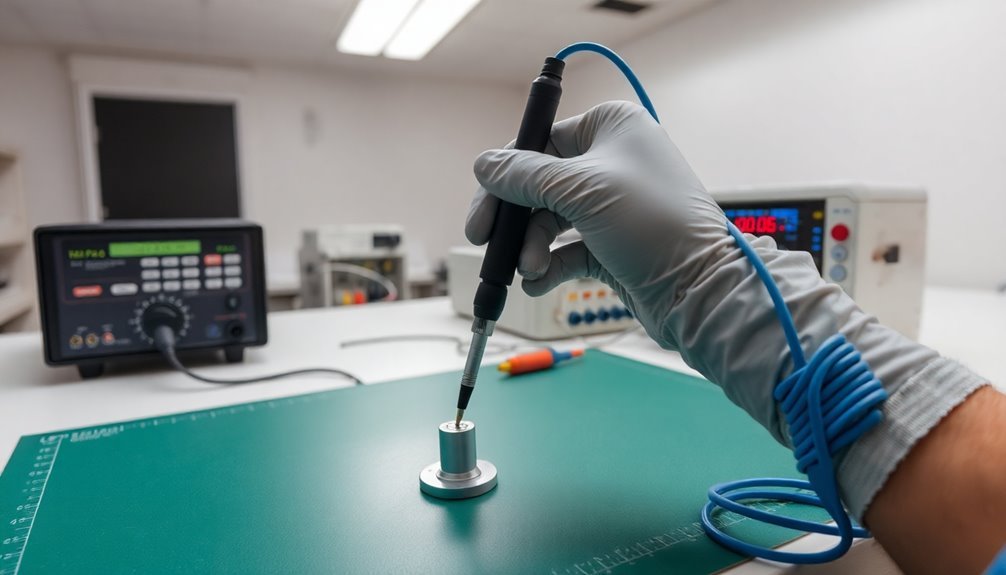
When you're managing calibration labels, you'll need a robust system that guarantees accurate tracking and compliance. Your labels must include essential information like calibration dates, due dates, ID numbers, and the responsible organization's details. Clean and dry surfaces are crucial for proper label adhesion.
To streamline this process, integrate your label production with calibration software that can automatically generate accurate, standardized labels.
You'll find that barcode integration is particularly valuable, as it allows you to scan and populate gage information instantly, reducing manual entry errors. Choose high-resolution, laminated labels for durability, and make certain they meet all relevant ISO, GMP, and industry standards.
If you're conducting field calibrations, consider using portable label printers to maintain consistency across all locations.
For maximum label management, you'll want to establish clear protocols for both permanent and removable labels. Clean and prepare surfaces properly before applying labels, and implement a tracking system for gage loans and returns.
Your system should generate detailed reports on gage usage patterns and maintain thorough records for audit purposes. Remember that your label management system isn't just about organization – it's vital for maintaining compliance with quality certification standards and regulatory requirements.
Equipment Documentation Access Points
Building on proper label management, equipment documentation for access points requires careful attention to both physical and digital organization.
You'll need to maintain detailed records of your access points' power requirements, ensuring they're connected to proper 802.3af or 802.3at PoE switches or compatible power injectors.
When documenting your installation points, you should record specific mounting configurations and any additional hardware used. The dual-band capabilities enhance wireless connectivity across both 2.4 GHz and 5 GHz frequencies.
Make sure you've noted the DHCP settings and CAPWAP UDP port configurations, as these are essential for troubleshooting. You'll want to keep records of your site survey results and document the precise locations where each access point is installed.
Keep track of your controller configurations, including time settings and firmware versions.
Document your DHCP Option 43 settings and maintain a list of controller IP addresses assigned to each access point.
You should also create a troubleshooting guide that includes LED status indicators and their meanings, power specifications, and network configuration details.
Store records of each access point's registration status and include maintenance schedules.
Remember to update your documentation whenever you make changes to the system's configuration or perform firmware updates.
Measurement Tool Verification Process
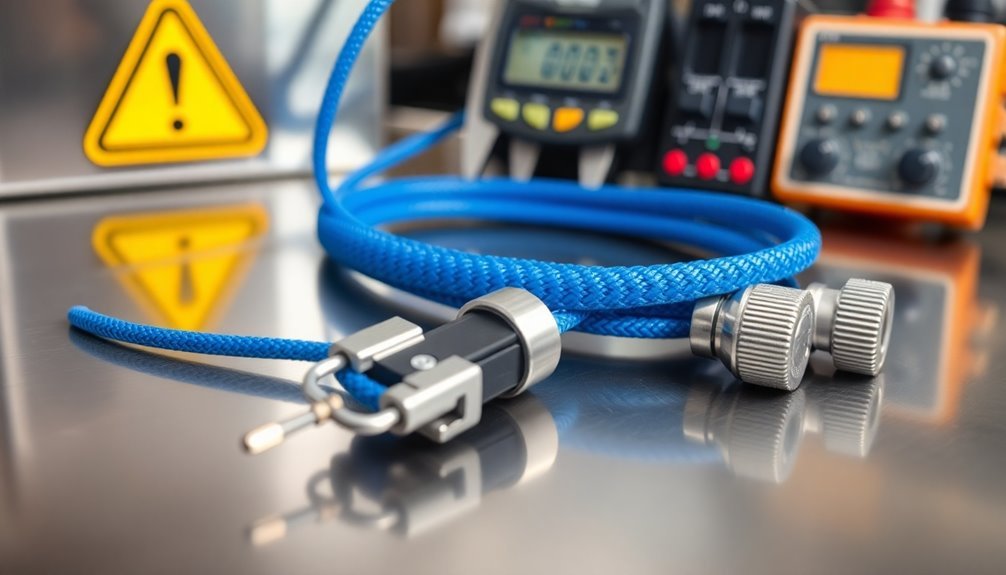
Understanding measurement tool verification helps you maintain accurate static control readings without the complexity of full calibration.
You'll need to regularly check if your measurement tools are performing within their specified limits and operating as intended.
To verify your static control measurement tools, compare their readings against a reference instrument. While this reference doesn't need to be NIST traceable, it should be reliable enough to confirm your equipment's performance.
You're looking to ascertain the tool's measurement error falls within acceptable tolerances for your application.
During verification, don't make any adjustments to the equipment – that's what calibration is for. Instead, focus on checking if the tool meets its specified requirements and performs consistently.
You can do this by testing various components of the measurement signal and documenting the results. State-recognized testing laboratories must conduct verifications for legally regulated measuring instruments.
Remember that verification isn't a replacement for calibration but serves as an intermediate check between calibrations.
It's a straightforward way to confirm your tools remain reliable without the formal process of establishing metrological traceability.
Make verification part of your regular maintenance routine to catch potential issues before they affect your measurements.
Frequently Asked Questions
How Often Should Static Dissipative Footwear Be Tested for Electrical Resistance?
You should test your static dissipative footwear daily, especially in high-risk environments. Don't skip testing, as it is crucial to verify the footwear's resistance remains between 0.1 and 100 MΩ for proper protection.
What Humidity Levels Are Optimal for Preventing ESD in Manufacturing Areas?
You'll want to maintain humidity between 30-70% RH in your manufacturing areas, with 40-60% being ideal. For best ESD prevention, aim for levels above 50% RH to minimize static electricity buildup.
Can Esd-Safe Packaging Be Reused After Initial Product Shipment?
You can reuse ESD-safe packaging if it's undamaged and properly inspected. But you'll need to check for tears, wrinkles, or compromised conduction paths before reusing, as these issues can reduce the packaging's protective properties.
When Should Ionizers Be Replaced Versus Serviced for Optimal Performance?
You should replace your ionizer when it shows persistent balance issues, failed compliance tests, or irreparable emitter damage. Otherwise, regular service and cleaning can maintain ideal performance through routine maintenance and calibration.
How Do Temperature Fluctuations Affect ESD Control Equipment Calibration Accuracy?
Temperature fluctuations can greatly impact your ESD equipment's calibration accuracy. You'll notice reduced precision and reliability when temperatures vary outside specified ranges. It's essential you maintain stable environmental conditions during calibration procedures.
In Summary
You'll maintain better control over your static auditing by implementing these three key practices. Keep your calibration labels organized and current, verify quick access to equipment documentation at designated points, and regularly confirm your measurement tools. When you're consistent with these fundamentals, you'll reduce errors, save time, and assure more reliable static control audit results across your facility.
Leave a Reply