To guarantee your product's ESD safety, you'll need to implement seven essential testing methods. Start with contact discharge testing using direct electrode contact and move to air discharge testing that simulates real-world scenarios. Add walking body voltage assessments to evaluate human-generated static. Include surface resistivity measurements using probe methods and conduct material qualification tests to verify compliance. Don't forget indirect discharge testing with coupling planes and environmental control testing under standardized conditions. These proven methods work together to create a thorough ESD protection strategy, and there's much more to explore about each technique's specific protocols and requirements.
Contact Discharge Testing Protocol
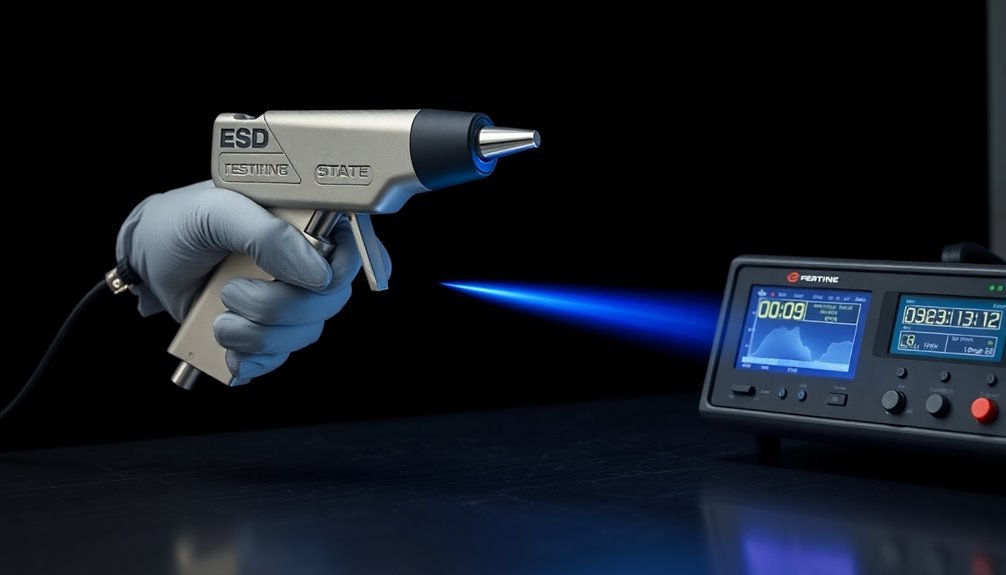
In today's electronic product development, contact discharge testing serves as a critical protocol for evaluating ESD protection. You'll find it's the preferred method under IEC 61000-4-2 standards due to its superior repeatability and reliability compared to air discharge testing.
When you're conducting contact discharge tests, you'll need to follow a specific procedure. Start by placing the ESD test gun's electrode in direct contact with your device under test. The use of shielded cables is essential to minimize interference during testing. You'll then initiate the discharge through the generator's switch, gradually increasing the test voltage to your specified level.
For commercial applications, you'll typically test up to Level 4, which requires an 8 kV discharge. You must focus on testing points that operators would typically touch during normal equipment use. Your test generator needs proper calibration, and you'll want to use pointed contact tips for direct application.
While you're performing the tests, keep in mind that contact discharge offers more consistent results than air discharge, though it doesn't perfectly simulate real-world ESD events. The current waveform must meet specific requirements, including a 0.8 ns rise time and defined current measurements at both 30 ns and 60 ns points.
Air Discharge Method Implementation
While contact discharge testing provides consistent results, air discharge testing better replicates real-world ESD scenarios. To implement this method, you'll need to use an ESD simulator with a rounded tip designed according to IEC 61000-4-2 standards, typically testing at voltages up to 16 kV for commercial applications.
When performing air discharge tests, you'll need to hold the ESD gun perpendicular to your equipment under test (EUT). Close the trigger, then approach the EUT as quickly as possible without causing mechanical damage. Both positive and negative pulses must be tested to ensure comprehensive immunity verification. You might hear a crackling noise at higher voltages, indicating multiple successive discharges.
Remember to remove the ESD gun and retrigger it after each discharge, allowing the EUT to discharge completely between tests.
Environmental factors will greatly impact your test results. You'll notice more frequent ESD events in low humidity and temperature conditions. The speed at which you approach the EUT with the simulator will affect discharge current and rise time.
Since air discharge testing isn't as reproducible as contact discharge, you'll need to carefully control these variables and document testing conditions to guarantee reliable results that comply with IEC 61000-4-2 standards.
Walking Body Voltage Assessment
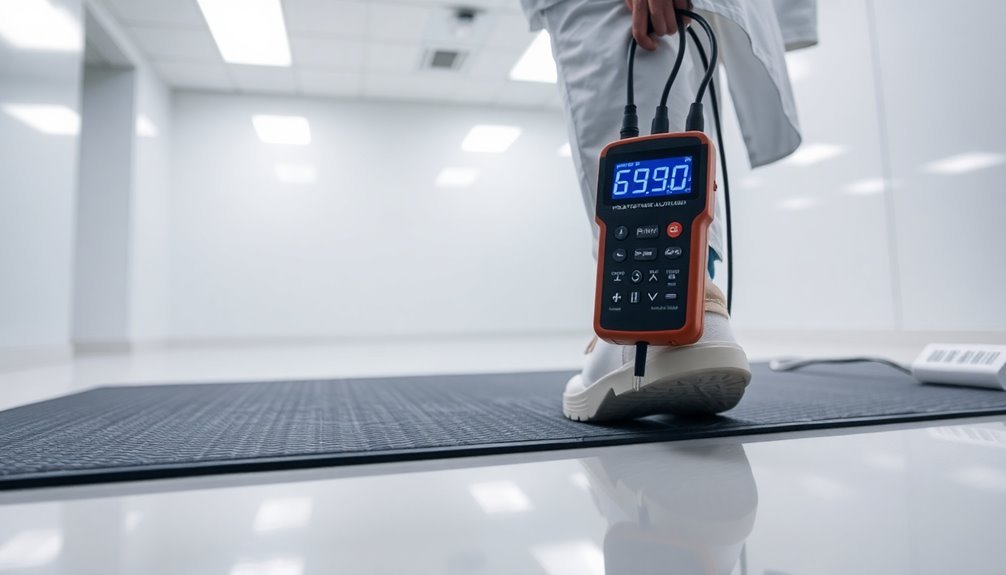
A reliable walking body voltage assessment helps determine if your ESD flooring and footwear systems effectively dissipate static charges. When you perform this test following ANSI/ESD STM 97.2 and IEC 61340-4-5 standards, you'll measure body voltage generated during a six-step walking pattern. Your goal is to guarantee voltage generation doesn't exceed 100 volts, which indicates proper grounding effectiveness.
You'll need specialized equipment to conduct accurate assessments. Modern testing kits like the WT5000 or EFM51.WT provide real-time voltage measurements and data logging capabilities. The 7100.EFM51.CPS.SET field meter delivers essential measurement tools for comprehensive testing. These tools help you verify compliance and maintain detailed records of your ESD control program.
- Simulate real-world conditions by performing the walking test in your actual work environment.
- Monitor voltage levels through specialized meters that display immediate results.
- Document peak voltages and maintain compliance records for quality assurance.
- Clean and maintain your ESD floors and footwear regularly to guarantee consistent test results.
Surface Resistivity Measurement Techniques
Beyond walking body voltage tests, surface resistivity measurements serve as another essential component of thorough ESD testing. You'll find several proven methods to measure surface resistivity, each offering unique advantages for different testing scenarios.
When you're conducting these tests, you'll need to choose between the two-point probe method, which is simpler but less precise, and the four-point probe method, which offers superior accuracy by minimizing contact resistance. If you're testing semiconductor materials, you'll want to use the Van der Pauw method, while the ring tester method works best for evaluating area-to-area resistivity.
The increasing complexity of modern electronics and higher device density makes accurate resistivity testing more critical than ever before. You'll need specific equipment to get accurate results, including a surface resistance test kit, proper electrodes, and a consistent 100-volt power source. Remember to maintain clean test surfaces and account for environmental factors like temperature and humidity, as these can considerably impact your measurements.
To confirm compliance with industry standards, you must follow ANSI/ESD S4.1 for worksurfaces and ANSI/ESD S11.11 for static dissipative materials. Your measurements, expressed in ohms per square, will help classify materials as insulative, dissipative, or conductive, confirming proper ESD protection for your products.
ESD Material Qualification Tests
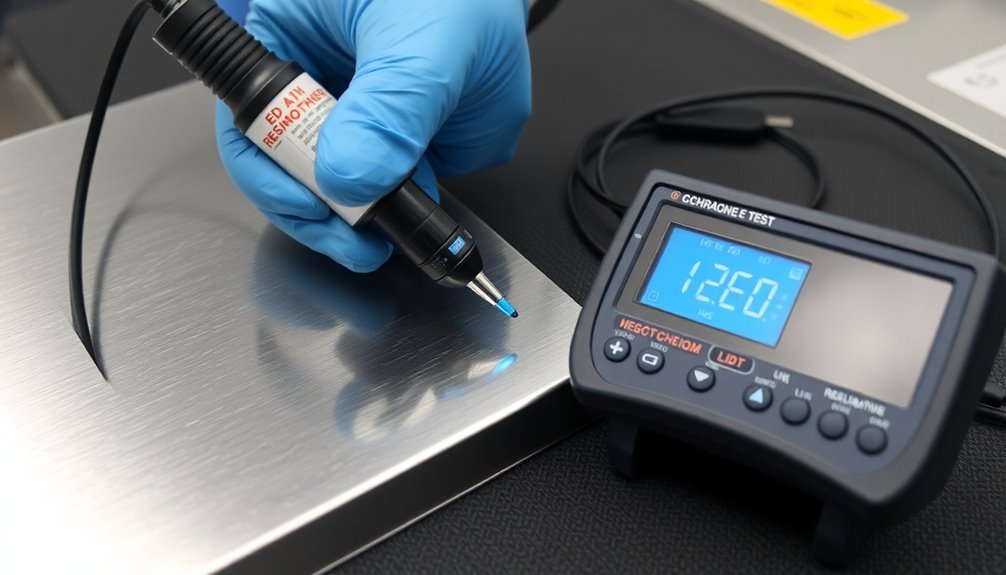
Testing ESD materials requires rigorous qualification procedures to verify they meet industry standards and provide reliable protection.
You'll need to follow specific standards like ANSI/ESD S20.20 and ANSI/ESD S541 for packaging materials to guarantee your ESD control items meet the necessary requirements. Product qualification must be completed before initial use of any ESD control item.
You can qualify materials through several methods, including product specification reviews, independent laboratory evaluations, or internal testing.
The key is maintaining proper documentation and conducting tests under controlled environmental conditions, particularly at specified humidity levels and temperatures.
Essential test procedures to perform:
- Surface Resistance Testing – Conduct at 12% RH and 73°F ±5°F for 48 hours using ANSI/ESD STM11.11-2015
- Volume Resistance Testing – Follow ANSI/ESD STM11.12-2015 guidelines under the same conditions
- Electrostatic Decay Testing – Measure using Mil-STD-3010C with a 2.0-second limit from 5kV to 0 volts
- Static Shielding Testing – Perform according to ANSI/ESD STM11.31-2012 at both 12% and 50% RH
Remember to document any exceptions with technical justification and maintain compliance verification records covering at least one year of testing data.
Indirect Discharge Testing Methods
Your HCP setup requires careful placement beneath the Equipment Under Test (EUT), while ensuring proper insulation from the ground reference plane.
For VCP testing, you'll position the vertical plane at a specified distance from the EUT and apply discharges to simulate real-world scenarios where static electricity affects nearby objects. System-level ESD testing helps evaluate how the entire system responds to these indirect discharge events.
You'll need both a Horizontal Coupling Plane (HCP) and a Vertical Coupling Plane (VCP) properly positioned to conduct effective indirect discharge testing.
Horizontal Coupling Plane Setup
While direct ESD testing evaluates product resilience to immediate discharges, the Horizontal Coupling Plane (HCP) setup simulates indirect electrostatic effects by replicating discharges to nearby objects. The setup ensures proper EMC compliance across various environmental conditions.
You'll need to connect each end of the HCP to the Ground Reference Plane (GRP) using 470kΩ carbon composition resistors, which effectively bleed off any residual charge within microseconds.
To perform HCP testing, you'll position the coupling plane adjacent to your Equipment Under Test (EUT) on an insulating surface.
You'll then charge the capacitor to your desired test voltage (typically up to ±4kV) and discharge it through an ESD gun at selected points on the HCP.
- Connect the HCP to GRP using high pulse-rated resistors at both ends
- Position your EUT next to the HCP on the test table
- Apply controlled discharges to multiple points on the HCP
- Monitor your product's response to the coupled electromagnetic interference
The setup allows you to assess how your product handles near-field radiated stress from nearby ESD events, helping you validate its immunity to real-world electromagnetic disturbances.
Your product's performance during these tests determines its classification under standardized criteria.
Vertical Coupling Plane Testing
Standing vertically at a precise 10cm distance from your Equipment Under Test (EUT), the Vertical Coupling Plane (VCP) serves as a critical component for indirect discharge testing. This metal sheet, mounted on a wood stand, simulates real-world ESD events where discharges occur on nearby conductive objects rather than directly on your product. Technical support resources are readily available to guide you through proper setup procedures.
When you're testing products that'll be used in metal cabinets or near industrial machinery, you'll need to ascertain compliance with IEC 61000-4-2 standards using the VCP. You'll connect a bleed-off cable with resistors to safely dissipate charges and secure everything with a tightening clamp.
The VCP's setup allows you to apply stress to your EUT indirectly, which is essential for products that may experience near-field radiated stress in their operating environment.
You'll find the VCP's versatility particularly useful as it's compatible with various ESD generators and can be easily set up on lab benches. During testing, you'll perform both direct and indirect discharges to evaluate your product's immunity to ESD events.
Remember to maintain proper safety protocols by using the provided insulation and bleed resistors to prevent unwanted shocks during testing.
Environmental Control Testing Standards
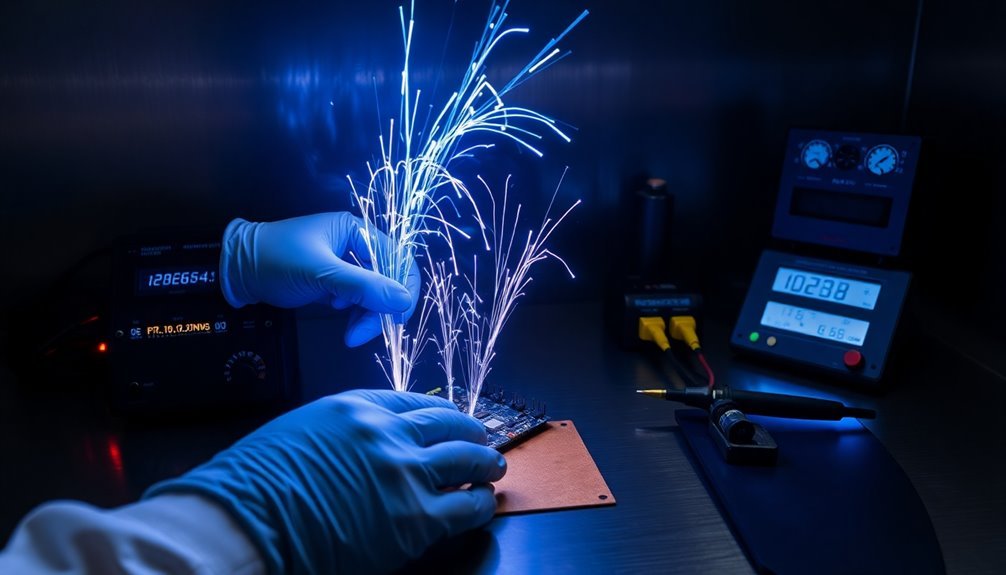
You'll need to maintain strict environmental controls during ESD testing, with temperature typically held between 15-35°C and relative humidity between 30-60% as specified in IEC 61000-4-2.
Your testing room must follow standard setup requirements, including properly grounded surfaces, ESD-safe materials, and adequate spacing between test equipment and walls.
Regular calibration of your ESD testing equipment is essential, with verification checks performed before each test session and thorough calibration conducted annually according to manufacturer specifications and industry standards.
Temperature and Humidity Requirements
In modern ESD testing, precise environmental control plays a critical role in guaranteeing accurate results. You'll need to maintain specific temperature and humidity conditions during testing to comply with established standards. The standard test conditions require 23°C ± 3°C and 12% ± 3% relative humidity, though you can qualify ESD control items at your facility's lowest annual humidity level if it's higher.
When you're conducting ESD testing, pay attention to these critical requirements:
- Test your ESD control items at a minimum of 9% to 15% relative humidity to guarantee they'll function in worst-case scenarios.
- Monitor both temperature and humidity variations throughout the testing period, as significant changes can affect your results.
- Condition your test environment to match your facility's actual conditions, especially when they differ from standard parameters.
- Document seasonal variations in your testing plan to capture data at the lowest annual humidity levels.
You'll need to verify that your ESD control items meet ANSI/ESD S20.20 or IEC 61340-5-1 standards regardless of environmental conditions.
Remember that while humidity controls aren't mandatory, your ESD control items must perform effectively at your facility's lowest humidity levels.
Testing Room Setup Standards
Through careful adherence to IEC 61000-4-2 standards, proper testing room setup forms the foundation of reliable ESD testing results.
You'll need to include essential components like ground reference planes, horizontal coupling planes, and vertical coupling planes to guarantee consistent and repeatable tests. Your setup must maintain precise dimensions and measurements as specified in the standard.
When setting up your testing environment, you'll want to place your equipment under test (EUT) on appropriate insulating material.
Don't forget to incorporate bleed-off cabling and resistors into your setup – they're essential for accurate results. Your testing room should minimize external influences that could compromise test integrity.
You'll need to arrange your ESD simulator (or gun) and discharge networks according to the standard's specifications.
If you're conducting air discharge tests, you'll typically use larger test levels up to 16 kV for commercial applications.
Make sure you've properly positioned your test tables and floor-standing setups to accommodate various EUT sizes.
Remember to maintain proper spacing between your ground reference planes and coupling planes, as these components are critical for creating a controlled test environment that meets IEC standards.
Equipment Calibration Guidelines
Proper equipment calibration serves as the cornerstone of reliable ESD testing results. You'll need to follow strict guidelines that align with standards like IEC 61000-4-2 and ANSI/ESD S20.20 to maintain accuracy in your testing procedures.
Regular calibration guarantees your measurements remain traceable to national and international benchmarks, while proper documentation helps track adjustments and maintain quality assurance.
To establish an effective calibration routine, consider your testing frequency, sample volume, and specific application requirements. You'll want to follow manufacturer guidelines for calibration intervals while accounting for environmental factors like humidity and ionization that can affect your results.
- Document all calibration outcomes and adjustments in a detailed log
- Use only approved calibration services with qualified personnel
- Maintain continuous monitoring systems for ESD integrity
- Keep your grounding systems properly installed and regularly checked
Remember to regularly review and update your calibration procedures as technology and industry standards evolve.
If you're conducting frequent tests, consider developing in-house calibration capabilities to streamline your process. Always guarantee your calibration equipment receives proper maintenance and updates to maintain testing accuracy and reliability.
Frequently Asked Questions
How Long Should Electronic Products Rest Between Consecutive ESD Test Discharges?
You should allow your electronic products to rest for 1 second between consecutive ESD test discharges, ensuring proper device recovery and compliance with IEC 61000-4-2 standards. Adjust timing based on device sensitivity.
Can ESD Testing Equipment Calibration Affect Product Classification and Immunity Levels?
Yes, your ESD testing equipment's calibration directly impacts product classification and immunity levels. You'll get inaccurate results with poorly calibrated equipment, which can lead to incorrect sensitivity ratings and unreliable protection assessments.
What Safety Precautions Should Operators Take When Performing High-Voltage ESD Tests?
You'll need to wear proper insulation, maintain a safe distance, use interlocked fixtures, avoid touching connections during tests, and follow discharge procedures. Don't forget to activate warning lights and keep unauthorized personnel away.
Do Wireless Devices Require Different ESD Testing Protocols Than Wired Electronics?
Yes, you'll need to test wireless devices differently. While they follow similar IEC standards, you must conduct additional RF sensitivity tests, antenna-specific ESD testing, and evaluate EMI/RFI interference during wireless transmission.
How Does Product Packaging Influence the Selection of ESD Testing Methods?
Your product's packaging type directly affects which ESD tests you'll need, as you must consider barrier materials, static dissipative properties, and environmental factors to guarantee complete protection during storage and shipping.
In Summary
You've now learned the seven essential ESD testing methods to protect your products. Whether you're conducting contact discharge tests or evaluating environmental controls, these protocols will help safeguard your electronics from static damage. Don't skip any of these vital steps – they're your defense against costly failures. Implement these methods consistently, and you'll maintain the highest standards of ESD protection for your products.
Leave a Reply