To protect your sensitive electronics from static damage, you'll need five essential defense systems: a thorough ESD control program with dedicated coordinators, a robust ground protection system using copper or steel rods, thorough personnel training aligned with ANSI/ESD S20.20 standards, properly designed static-safe workstations with dissipative surfaces, and regular monitoring procedures following IEC standards. Each system works together to create a complete static defense shield, ensuring your electronics manufacturing meets industry requirements while maintaining production efficiency. Discover how these interconnected systems can transform your facility's ESD protection strategy.
ESD Control Program Fundamentals
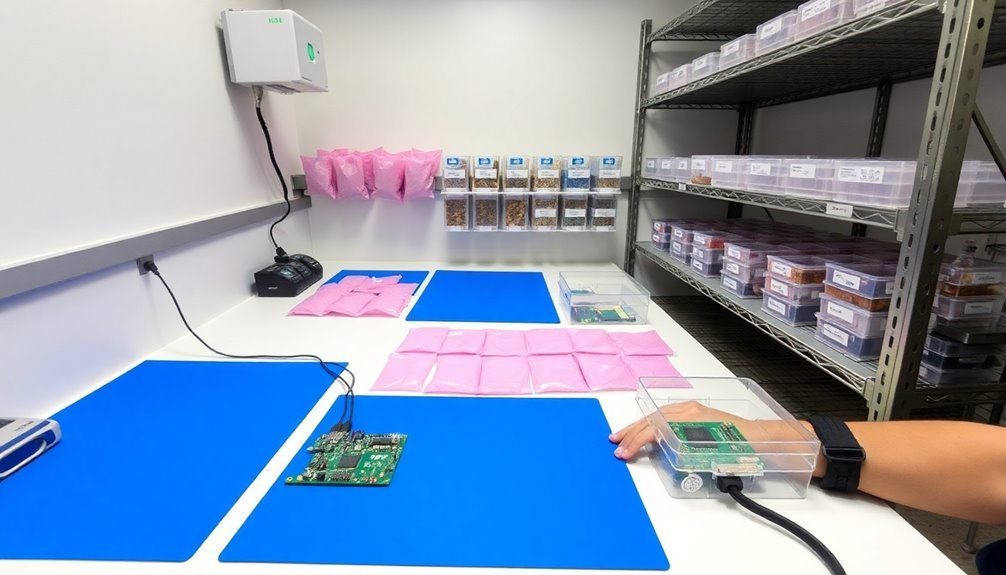
While protecting electronic components from electrostatic discharge (ESD) is crucial, you'll need a well-structured control program to effectively safeguard your manufacturing process.
Start by establishing a documented plan that outlines your program's scope, including specific tasks and procedures needed to protect ESD-sensitive items.
You'll want to appoint an ESD Coordinator and form dedicated teams to oversee implementation.
To guarantee your program meets industry standards, align it with ANSI/ESD S20.20 or IEC 61340-5-1 requirements, which will also support your ISO 9000 certification efforts.
Include detailed training protocols and compliance verification plans with clear, written procedures.
Don't forget to tailor your program to your organization's unique needs and facility layout. Conducting a thorough facility audit helps identify potential ESD problem areas and risks.
You'll need to address every aspect of ESD protection thoroughly, from establishing proper grounding systems to implementing charge generation controls.
Make sure you're maintaining updated documentation of all procedures and regularly reviewing your program's effectiveness.
Remember to create a qualified products list for approved ESD control items and keep your test equipment properly calibrated according to manufacturer specifications.
Ground Protection System Requirements
A proper ESD control program relies heavily on effective grounding systems to maintain static-safe environments. You'll need to install ground rods that meet specific requirements: copper, copper-clad steel, galvanized steel, or stainless steel alloy construction, with a minimum 5/8-inch diameter and 10-foot length. Your ground rods must achieve a maximum resistance of 10 ohms, though some applications require 5 ohms or less. When installing ground leads, use exothermically welded connections for optimal low inductance performance and corrosion prevention.
Component | Requirement |
---|---|
Ground Rod Material | Copper, copper-clad steel, galvanized steel, or stainless steel |
Minimum Diameter | 5/8 inches |
Minimum Length | 10 feet |
Maximum Resistance | 10 ohms (5 ohms for specific applications) |
Connection Method | Exothermic welds |
Within your ESD protected area, you'll need to connect all conductive surfaces to a common ground. Your ESD protective worksurfaces should maintain a resistance between 1.0 x 10^6 and 1.0 x 10^9 ohms. Don't forget to integrate lightning protection that meets NFPA 780 standards and install SPDs rated for at least 50 kA per phase. You'll also need to implement regular testing of all grounding accessories, including wrist straps and footwear, to guarantee continuous protection of your sensitive electronics.
Personnel Training and Certification
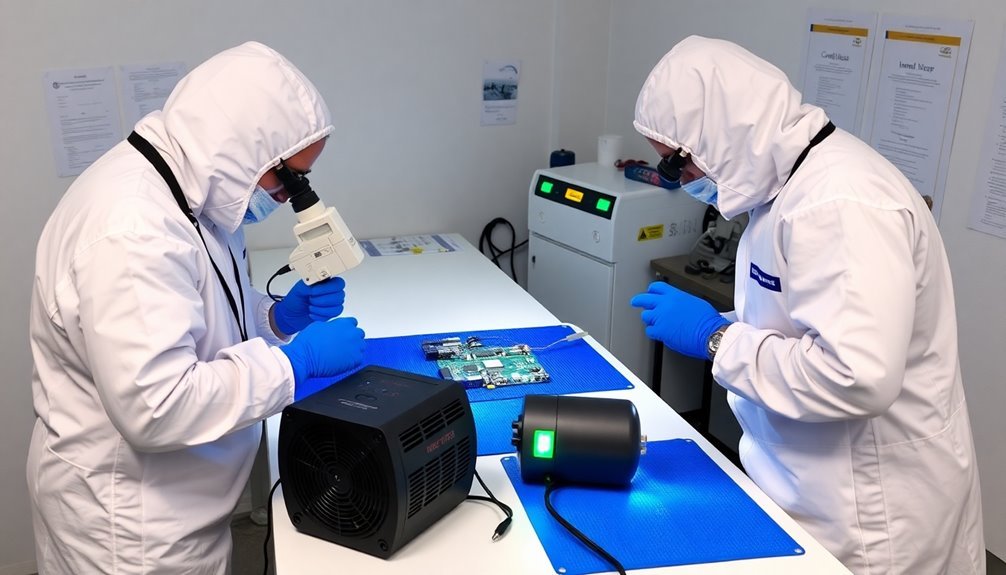
Effective personnel training sits at the heart of any successful ESD control program. You'll need thorough instruction covering static electricity basics, charge formation, and proper handling techniques to protect sensitive electronic components. Industry standards like ANSI/ESD S20.20 and IEC 61340-5-1 form the foundation of these training requirements. A stable humidity level control helps minimize static buildup during component handling.
Your training program should include both theoretical knowledge and hands-on practice with ESD control measures. You'll work with experienced trainers who understand real-world challenges in managing static discharge risks. They'll teach you preventive measures, proper tool usage, and material handling techniques specific to your workplace environment.
Once you've completed the training, you'll receive certification that validates your ESD control knowledge. This certification isn't just a piece of paper – it demonstrates your commitment to quality and safety while helping your company maintain compliance.
You'll need to stay current through continuing education, as standards and best practices evolve. The investment in training pays off through reduced equipment failures, improved productivity, and significant cost savings from preventing ESD-related damage.
Static-Safe Workstation Design Elements
Static-safe workstation fundamentals form the cornerstone of electronics manufacturing and repair environments. To create an effective static defense system, you'll need to incorporate several critical design elements that work together to minimize electrostatic discharge risks.
Your workstation's foundation starts with a properly grounded work surface made of static-dissipative materials like rubber, vinyl, or laminate. You'll need to connect this surface to a common-point grounding system, which serves as the central hub for all your ESD protection equipment. The surface resistance should measure between 1 megohm and 1 gigohm for optimal protection.
Make sure you're using wrist straps and foot grounders to maintain consistent grounding while you work.
Don't overlook the importance of proper shielding materials. You'll want to store and transport sensitive components in conductive bags or tote boxes.
For areas where you're handling insulators like circuit boards or synthetic materials, you should install ionizers to neutralize static charges.
Your workstation must comply with industry standards like ANSI/ESD S20.20 and IEC 61350-5-1. Regular testing of all ESD equipment is essential – use ESD testers to verify the functionality of wrist straps, heel grounders, and other protective gear.
Remember to document all testing and maintenance procedures to maintain compliance.
Monitoring and Testing Procedures
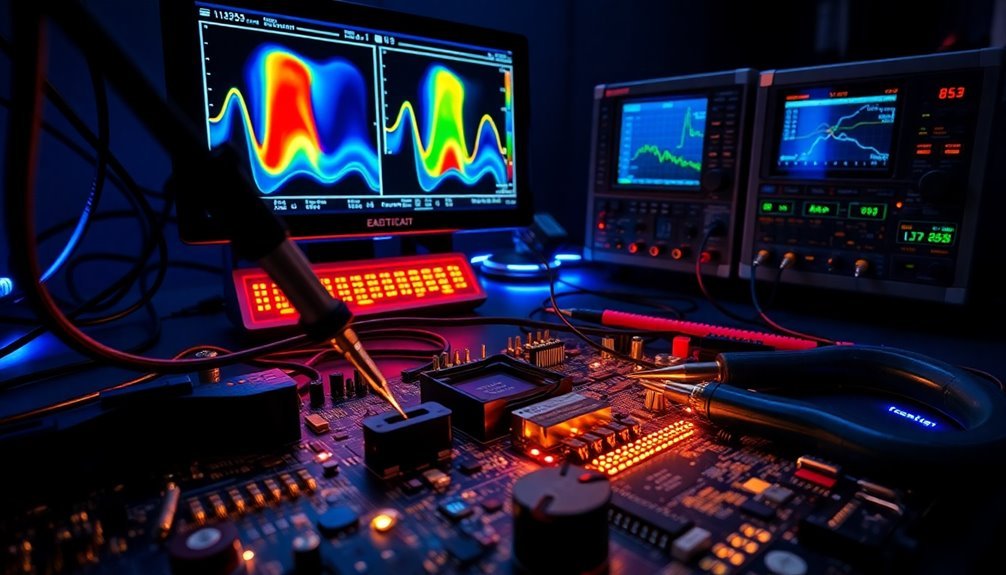
Rigorous monitoring and testing procedures serve as the backbone of any thorough ESD defense system. You'll need to follow industry standards like IEC 61000-4-2, which establishes the essential requirements for ESD testing.
If you're working with specific sectors, you must also comply with standards like EN 60601-1-2 for medical devices or ISO 10605 for automotive products. The thorough assessment helps protect your investment in product development and customer satisfaction.
You'll start your testing with specialized ESD generators and current probes, applying precise ESD pulses at increasing voltages from 2 kV up to 8 kV for contact discharge, and up to 15 kV for air discharge. Make sure you're delivering at least 10 discharges per polarity, with one-second intervals between each pulse.
You must test all four sides of your equipment under test while it's operating normally.
Don't forget to maintain strict temperature and humidity control in your testing environment. You'll need proper safety equipment, including grounding wrist straps, dissipative gloves, and anti-static mats.
Regular workspace testing with ground/polarity testers is essential. By following these procedures, you'll identify potential design flaws and prevent costly product failures before they reach your customers.
Frequently Asked Questions
How Long Does ESD Protective Packaging Maintain Its Effectiveness During Storage?
Your ESD packaging can maintain effectiveness for up to 5 years when you store it properly in controlled conditions. You'll need to monitor temperature, humidity, and regularly test materials to verify continued protection.
Can Esd-Safe Materials Be Recycled Without Compromising Future Protective Properties?
You can recycle some ESD materials like single-polymer pink bags, but their protective properties often degrade during recycling. For best results, you'll need specialized recycling processes that maintain conductive properties.
What Humidity Levels Are Optimal for Minimizing Static Buildup?
You'll want to maintain relative humidity between 40% and 60% to minimize static buildup. If you let levels drop below 30%, you'll face increased ESD risks, while exceeding 60% can cause corrosion.
How Often Should Ionizing Equipment Be Calibrated for Maximum Effectiveness?
You'll need to calibrate your ionizing equipment every six months, per JESDD625-A standards. If you notice frequent adjustments are needed, shorten the calibration interval. Always verify performance with a Charge Plate Monitor.
Are Wireless Devices Allowed in Static-Protected Areas With Proper ESD Controls?
Yes, you can use wireless devices in static-protected areas if you've implemented proper ESD controls. Just make certain you're following grounding protocols, maintaining humidity levels, and using appropriate anti-static materials and protection equipment.
In Summary
You'll need all five of these defense systems working together to create an effective ESD control program. Don't skip any components – proper grounding, trained staff, well-designed workstations, and regular testing are essential for protecting sensitive electronics. Make sure you're following industry standards and keeping detailed records of your monitoring results. When implemented correctly, these systems will substantially reduce ESD-related failures.
Leave a Reply