To protect your sensitive components in cleanroom environments, you'll need these essential ESD packaging products: static shield barrier bags with Faraday cage protection, LDPE cleanroom poly bags, ESD-safe storage containers, anti-static moisture barrier films, and cleanroom grounding equipment. Don't forget static dissipative packaging materials, high-density polyethylene vacuum bags, ESD-safe sealing solutions, conductive storage totes, and cleanroom static control tools. Each product serves a specific purpose in maintaining contamination-free conditions while preventing electrostatic discharge damage. Understanding how these solutions work together creates the foundation for ideal cleanroom safety.
Static Shield Barrier Bags
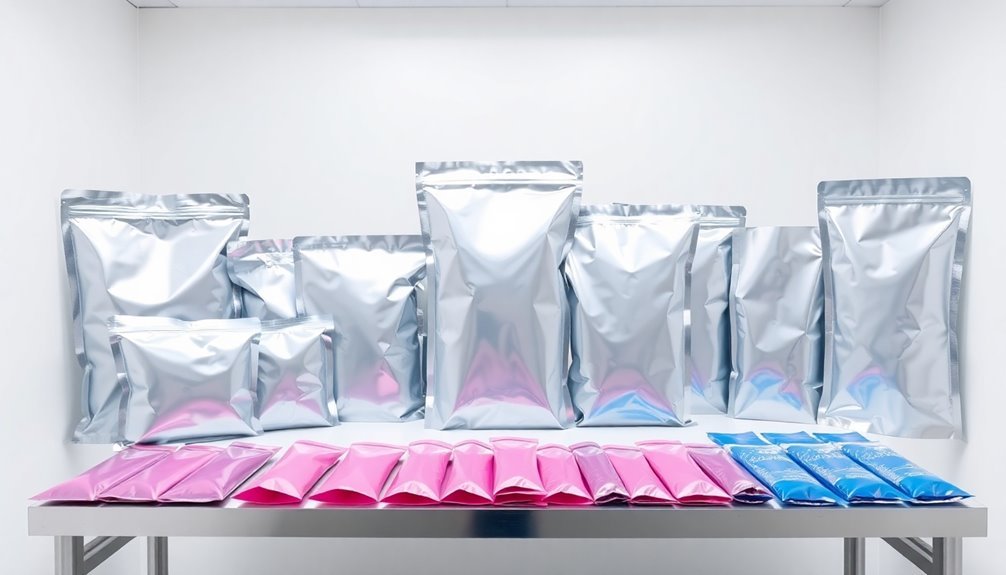
Static shield barrier bags stand at the forefront of ESD protection technology, utilizing a multi-layered construction with metallized shielding to create a Faraday cage effect.
You'll find these bags provide essential protection for your sensitive electronic components, offering less than 15nJ static shielding performance and maintaining a standard thickness of 3.0 mil ±10%.
The advanced four-layer construction includes bottom static dissipative coating, polyethylene, vacuum-metalized polyester, and top static dissipative coating.
When you're handling ICs, PCBs, or other ESD-sensitive devices, these bags deliver impressive mechanical properties. Pack sizes typically come in quantities of 100 units for efficient bulk ordering.
You can rely on their tensile strength of over 5000 PSI (MD) and 5500 PSI (TD), along with puncture resistance of ≥ 12 lbs and heat seal strength of 10 lbs/in.
The bags' light transmission rate of 40% ±5% allows for easy content verification.
You'll find these bags comply with vital standards including ANSI/ESD S541, EIA 625, and ANSI/ESD S20.20.
They're available in both metal-in and metal-out configurations, such as the 3M SCC1000 and SCC1500 series.
For moisture-sensitive components, you can opt for specialized ESD moisture barrier bags that meet IPC/JEDEC J-STD-033 requirements.
The bags' versatility extends to custom sizing options, ensuring you'll get the exact protection your specific application needs.
LDPE Clean Room Poly Bags
Every LDPE clean room poly bag offers exceptional cleanliness and protection, manufactured from virgin low-density polyethylene in controlled environments.
You'll find these bags produced in certified cleanrooms using pure, nitrogen-purged air and 100% virgin barefoot resin, ensuring they're free from additives and contaminants. These bags feature a 4 mil thickness for optimal durability and protection. Prices for these bags range from $0.05 to $1.42 depending on size and quantity ordered.
You can choose from various thicknesses, including 2 mil, 4 mil, and 6 mil options, to match your specific requirements.
These bags meet ISO 14644-1 Class 5 and IEST-STD 1246D standards, making them ideal for medical, biotechnology, electronics, and aerospace applications.
They're often double-bagged to minimize contamination risks during use.
When you're looking for reliable contamination prevention, you'll appreciate that these bags don't promote outgassing or corrosion.
They provide excellent puncture resistance for heavy items while maintaining FDA and EU compliance.
For environmentally conscious operations, you'll find biodegradable and recyclable options available from suppliers committed to sustainable practices.
You can also customize these bags with features like press-to-close zippers and resealable tapes to suit your specific needs in clean room environments.
ESD-Safe Storage Containers
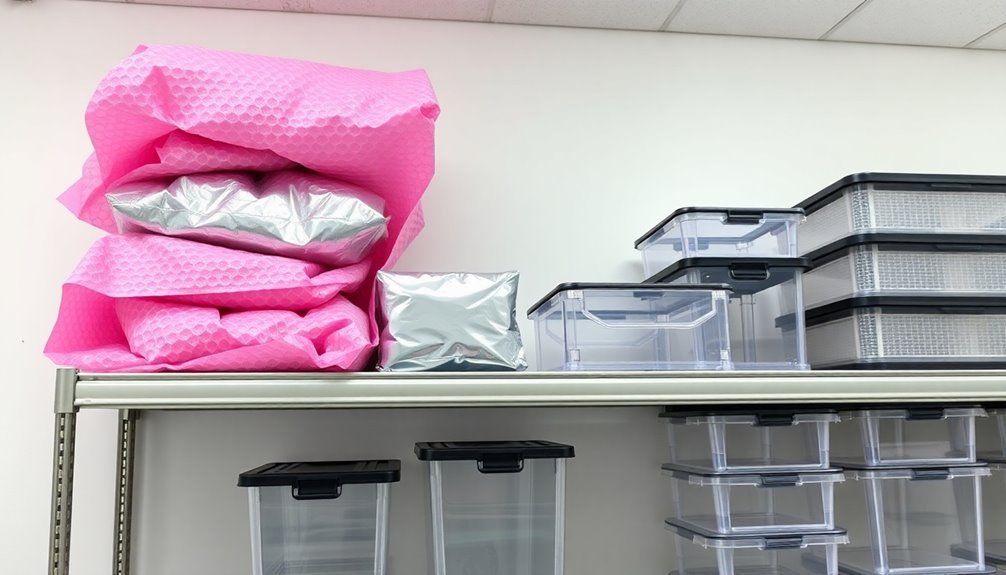
ESD-safe storage containers' robust design combines static dissipative properties with cleanroom-compatible materials, giving you reliable protection for sensitive electronic components.
You'll find various options including round storage bottles, PP trays, divider box totes, conductive corrugated totes, and ESD storage boxes, each engineered with surface resistance ranging from 10^4 to 10^11 Ohm. The translucent design of these containers allows for easy content visibility.
These containers feature essential elements like conductive inserts, foam dividers, and stackable designs that maximize your storage efficiency. The containers are constructed using polypropylene with conductive toner for effective charge dissipation.
You'll appreciate their chemical-resistant construction, protecting against acids, alkalis, and oils while maintaining cleanroom compatibility.
The containers' smooth surfaces make cleaning and maintenance straightforward, ensuring continued compliance with standards like MIL-B-81705 and ANSI/ESD S20.20.
Whether you're working in electronics manufacturing, cleanrooms, or automotive industries, you can choose from multiple sizes to meet your specific needs.
The containers' durability comes from high-quality materials like MDPE and polypropylene, which provide long-lasting performance.
When you're handling sensitive components in your facility, these containers offer the static protection you need while maintaining the cleanliness standards your operations require.
Anti-Static Moisture Barrier Films
Multi-layer anti-static moisture barrier films elevate your cleanroom packaging capabilities beyond basic storage containers.
These specialized films combine nylon or polyester bases with foil and polyethylene layers to deliver superior protection against moisture, oxygen, and static discharge. They are manufactured in ISO-certified cleanrooms to ensure the highest level of contamination control. The films feature a triple barrier layer that maximizes protective properties.
You'll find these films available in thicknesses ranging from 3.6mil to 6.0mil, offering impressive moisture vapor transmission rates below 0.0006 grams per 100in² per 24 hours at 100°F.
Their oxygen transmission rate of 0.003 grams per 100in² per day guarantees your sensitive components remain protected from oxidation.
The films' robust construction provides excellent durability with MD yield strength at 4000 psi and TD yield at 4300 psi.
You can rely on their puncture resistance exceeding 19lbs and heat seal strength greater than 16lbs/inch for secure packaging.
They're particularly suited for electronic components requiring ESD, EMI, and RFI protection.
You'll appreciate their compatibility with flexographic printing and their compliance with key standards, including ISO certification, IEST-STD 1246D, RoHS, EU No 10/2011, and California Proposition 65.
Whether you need standard or custom specifications, these films deliver extensive protection for your cleanroom packaging needs.
Cleanroom Grounding Equipment
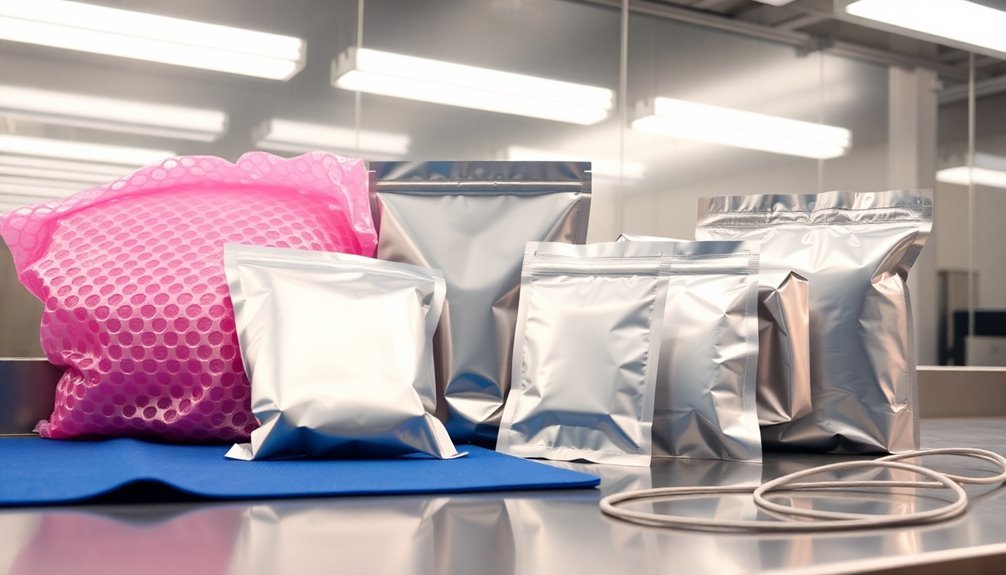
Proper grounding equipment forms the backbone of effective static control in cleanroom environments.
Manufacturing facilities must carefully control ESD as even minor voltage discharges can destroy sensitive components. You'll need various grounding components to maintain an ESD-safe workspace, including ESD wrist straps that connect personnel to unpainted surfaces or grounded workstations. Static dissipative mats provide essential grounding by electrically bonding objects and people, while heel straps, toe straps, and boot straps help ground workers at standing workstations. Fan filter units with HEPA filters require special attention to prevent static buildup from high-velocity air movement.
Your flooring solutions play a vital role in static control. You can choose from static dissipative heat-welded vinyl, vinyl tiles, or epoxy coatings.
Installing copper conducting strips beneath vinyl flooring enhances static dissipation when connected to the cleanroom ground. For peak protection, you'll want to combine these elements with proper ionization systems, such as free-standing or ceiling-mounted de-ionizers.
Don't overlook the importance of furniture grounding. You'll need to equip cleanroom furniture with grounding tabs or drag chains, especially when placed on static dissipative flooring.
Remember to maintain humidity levels between 40-60% to enhance static dissipation, and confirm all your grounding equipment meets ANSI/ESD S20.20 and IEC 61340 standards for thorough ESD protection.
ESD Conductive Storage Totes
Storage totes designed for ESD protection come in multiple styles to safeguard your sensitive electronic components. You'll find conductive and dissipative divider tote boxes, nesting totes, stackable totes, and in-plant handlers, all manufactured from durable materials like Corstat and Durastat for efficient handling systems.
These totes feature carbon-filled copolymer polypropylene materials that meet military specification Mil-B-81075B, ensuring an electrostatic decay rate of less than 0.1 seconds. You'll notice they're always black due to their carbon content, which provides essential conductivity and grounding properties.
The surface resistivity must be 10^5 ohms per square inch or less to maintain proper ESD protection.
You can customize your ESD storage totes with various partition configurations, handles, and ESD foam inserts to fit your specific needs. When you're working with sensitive electronics, you'll appreciate that these totes can be fitted with CFP or Corstat partitions to precisely accommodate boards and assemblies.
For clean room applications, you'll need to take into account that carbon-filled materials may slough particles, so you might need to select alternative materials based on your specific requirements.
Static Dissipative Packaging Materials
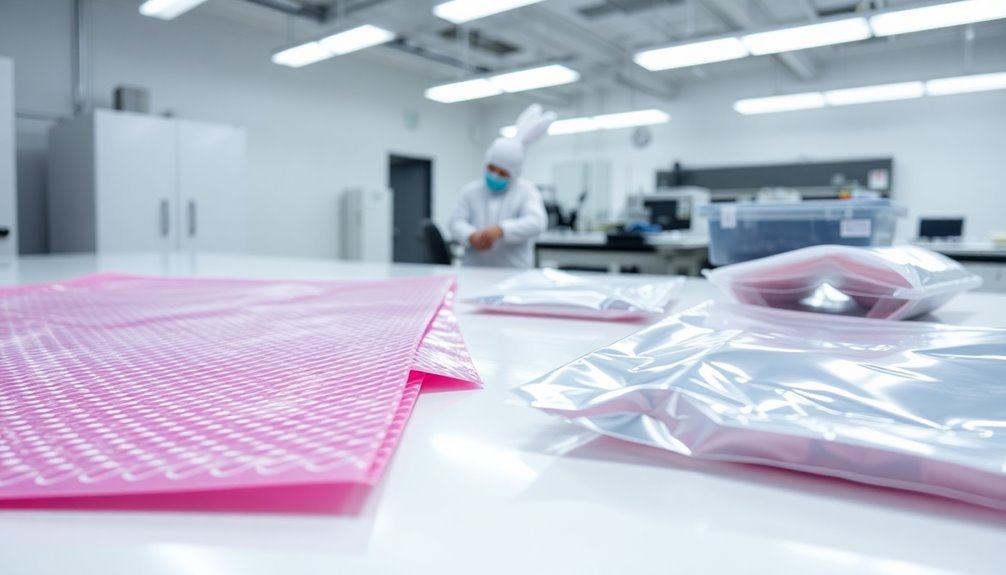
When selecting packaging for sensitive electronic components, you'll need static dissipative materials that offer controlled discharge protection. These materials feature surface resistance between 1 x 10^5 and 1 x 10^12 ohms/square, allowing charges to dissipate within milliseconds through a controlled path to ground.
You'll find these materials are modified with chemical additives, carbon fibers, or sooty particles to achieve their dissipative properties. They're marked with ESD protection symbols and undergo rigorous testing through ring electrode tests and surface measuring devices to ascertain reliability.
You can use static dissipative packaging across various applications. In electronics protection, they'll prevent ESD damage to sensitive components. They're essential in environments with flammable substances, where they prevent sparks and potential explosions.
You'll also find them in medical device packaging and industrial settings where static discharge poses risks.
The benefits you'll gain include preventing damage to electronic components, enhancing safety in hazardous environments, and guaranteeing compliance with ATEX directives. These materials help you reduce equipment downtime and costly repairs while offering custom thermoformed solutions for your specific packaging needs.
High-Density Polyethylene Vacuum Bags
Beyond static dissipative materials, High-Density Polyethylene (HDPE) vacuum bags offer superior protection in cleanroom environments. These specialized bags, manufactured from pure HDPE, provide exceptional strength and puncture resistance while maintaining ultra-low outgassing properties.
You'll find them particularly valuable in semiconductor, pharmaceutical, and medical device applications where cleanliness is paramount.
When you're working in ISO-certified cleanroom environments, these bags deliver:
- Superior gas barrier protection and excellent handling characteristics, ensuring your components remain contamination-free
- High purity construction without slip agents or anti-block additives, meeting IEST-CC-STD 1246D level 100 cleanliness standards
- Custom sizing and thickness options, produced in ISO class 5, 6, and 7 environments with third-party certification
You'll notice their cloudy appearance and easy-opening design, making them practical for daily use while maintaining stringent cleanliness requirements.
They're specifically engineered for vacuum packaging applications where intimate contact with sensitive components is necessary.
With their production in controlled cleanroom environments and rigorous in-house lab testing, you can trust HDPE vacuum bags to protect your most critical products from contamination.
ESD-Safe Sealing Solutions
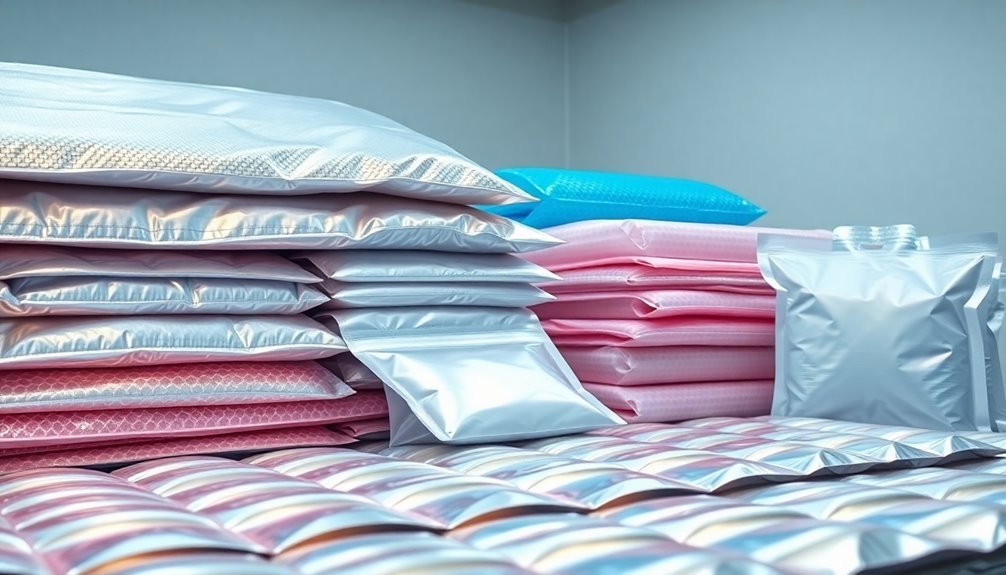
Three critical components make up effective ESD-safe sealing solutions in cleanroom environments: conductive tapes, static dissipative materials, and specialized sealing systems. You'll find products like NovaStat tape designed specifically for ESD-sensitive applications, guaranteeing your electronic components remain protected from static damage during handling and storage.
ESD Solution | Primary Function | Key Benefit |
---|---|---|
Conductive Tapes | Static Control | Prevents sudden discharges |
Dissipative Materials | Charge Drainage | Reduces ESD risk gradually |
Sealing Systems | Package Protection | Maintains content integrity |
When you're working with sensitive electronics, you'll need to confirm your sealing solutions comply with ANSI/ESD S20.20 and IEC 61340 standards. These regulations govern everything from material selection to grounding requirements. Your sealing materials must effectively handle static-prone substances like polyethylene and nylon while preventing harmful charge buildup. By implementing proper ESD-safe sealing solutions, you'll greatly reduce the risk of component damage and maintain your cleanroom's integrity. Remember that effective sealing isn't just about containing products – it's about protecting your valuable electronic components from invisible yet potentially devastating static charges.
Cleanroom Static Control Tools
You'll find static neutralizing equipment essential for maintaining ideal ESD control in your cleanroom environment, as these tools effectively eliminate harmful static charges that could damage sensitive components.
Your personnel need proper grounding tools, including wrist straps and heel grounders, to safely discharge any built-up static electricity while working with sensitive materials.
These control tools, when combined with proper training and monitoring systems, help you meet stringent cleanroom requirements while protecting your valuable products from ESD damage.
Static Neutralizing Equipment Benefits
Static neutralizing equipment serves as a critical defense against electrical charges that can damage sensitive materials and compromise cleanroom operations. Through advanced ionization systems, you'll find thorough protection against static-related issues while maintaining cleanroom integrity.
You can maximize your cleanroom's effectiveness by deploying air ionization technology that actively neutralizes static electricity and facilitates particle removal. These systems work continuously in critical areas like desiccators and workstations, ensuring consistent protection for your sensitive materials.
Here's how static elimination tools enhance your cleanroom operations:
- High-performance ionizers can neutralize static charges in as little as 0.5 seconds, providing rapid protection for sensitive components.
- Wide-area elimination systems reach up to 3 meters, offering extensive coverage for larger workspaces.
- Compact fan static eliminators provide visual confirmation of successful static removal, ensuring reliable performance.
For specific applications, you'll find specialized solutions like ionizing equipment for air showers, desiccators, and nonconductive materials.
Grounding Tools For Personnel
While ionization systems actively neutralize static charges in the air, proper personnel grounding forms the foundation of cleanroom ESD protection. You'll need to implement multiple grounding solutions to effectively protect your sensitive components and maintain cleanroom integrity. Start with ESD flooring combined with conductive footwear, including heel grounders or ESD shoes, to create a reliable path to ground.
Your personnel should wear ESD-safe clothing, such as full-length "bunny suits" or lab coats made with static-dissipative materials. These garments, woven with conductive threads, work in conjunction with other grounding tools to prevent charge accumulation.
Tool Type | Primary Function | Key Benefit |
---|---|---|
Wrist Straps | Direct grounding | Immediate charge dissipation |
ESD Footwear | Floor connection | Continuous mobility protection |
Dissipative Mats | Workstation safety | Local charge control |
ESD Chairs | Seated protection | Movement freedom |
Full Body Suits | Complete coverage | Total personnel protection |
Remember that cleanroom environments present unique challenges due to low humidity and HEPA filtration. You'll need to maintain strict protocols regarding permitted clothing materials, as items like fleece can generate significant static charges that attract contaminating particles.
Frequently Asked Questions
How Often Should ESD Packaging Materials Be Tested for Conductivity Performance?
You should test ESD packaging materials semi-annually for conductivity performance, though testing frequency can vary based on your product's sensitivity and failure risks. Always test after maintenance or when materials show wear.
Can Different Types of ESD Packaging Materials Be Safely Used Together?
Yes, you can safely combine different ESD packaging materials. You'll get better protection when you pair conductive materials with dissipative ones, or use shielding bags with anti-static bubble wrap and ESD-safe foam.
What Temperature Ranges Affect the Anti-Static Properties of Cleanroom Packaging?
You'll find most anti-static properties work best between 20-26°C. Temperatures outside this range can reduce effectiveness, while extreme fluctuations beyond 21°C ± 2°C may compromise your packaging's static-control capabilities.
How Long Do Permanent Anti-Static Treatments Typically Last in Storage Conditions?
Under proper storage conditions, you'll find permanent anti-static treatments typically last 12 months for standard materials, while extended-life materials can maintain their properties for up to 3 years when stored away from UV light.
Are Recycled ESD Packaging Materials as Effective as New Ones?
Yes, you'll find recycled ESD packaging materials are just as effective as new ones. They retain their electrostatic discharge protection properties through the recycling process, and they'll still meet industry standards for protecting your electronics.
In Summary
You'll find these 10 essential clean room ESD packaging products are crucial for protecting sensitive electronic components and maintaining contamination control. When you're implementing these solutions in your facility, don't forget to regularly inspect and maintain each item. By combining proper ESD packaging with consistent handling protocols, you're ensuring both product safety and clean room integrity.
Leave a Reply