Maintain your cleanroom's humidity levels between 30-40% RH for ideal performance and contamination control. You'll need proper dehumidification equipment, whether it's desiccant or refrigeration systems, matched to your specific requirements. Install continuous monitoring systems with automated alerts, and guarantee regular calibration of sensors. Control airflow at entry points, implement seasonal management strategies, and maximize energy usage through integrated HVAC systems. Don't forget staff training and thorough documentation of all procedures. Regular maintenance, including monthly inspections and quarterly cleaning, is essential for system efficiency. These fundamentals will set you up for deeper insights into cleanroom humidity management.
Understand Your Cleanroom's Humidity Requirements
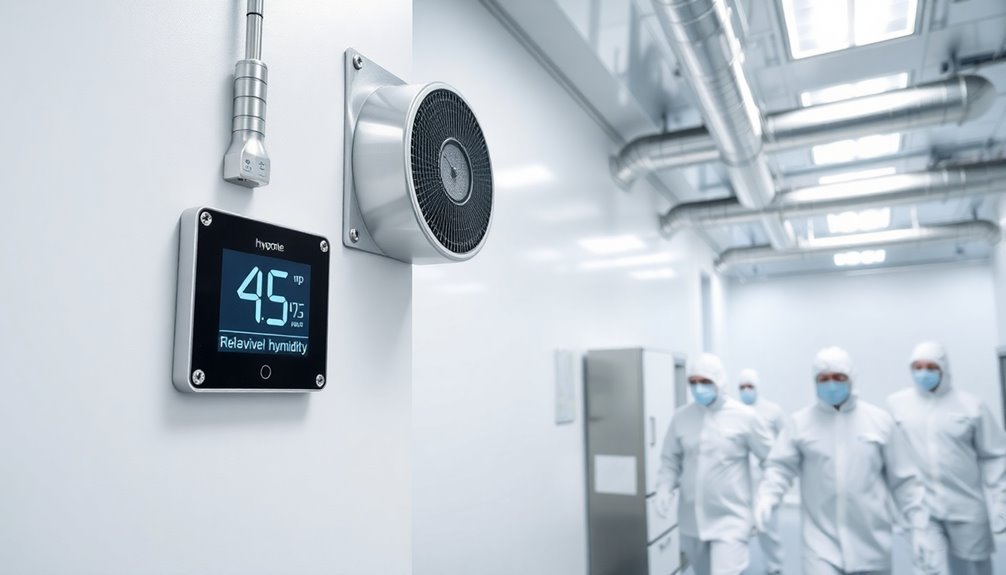
A cleanroom's delicate balance hinges on proper humidity control. You'll need to maintain relative humidity (RH) levels between 30% and 40% for ideal performance, though your specific requirements may vary depending on your industry and processes.
You're dealing with a critical balance: too much humidity promotes bacterial growth and contamination, while too little can cause static electricity problems. For static control, you'll want to aim for 35-40% RH, which provides an effective compromise. Double airlocks may be necessary when there are frequent entries and exits to help maintain proper humidity levels.
If you're in pharmaceuticals, semiconductors, or biotechnology, you'll need even tighter control of these parameters to guarantee product integrity.
Keep in mind that humidity affects multiple aspects of your cleanroom operation. When RH exceeds 60%, you're risking biological contamination.
You'll also need to take into account your employees' comfort, which typically requires 40-60% RH. Your electrical equipment performs better with slightly elevated humidity, but pharmaceutical products often need lower levels for stability.
To stay on top of these requirements, you'll need continuous monitoring using hygrometers. Remember that fluctuating humidity can lead to process control issues, including solvent evaporation and condensation problems that could compromise your product quality.
Select Proper Dehumidification Equipment
When choosing dehumidification equipment for your cleanroom, you'll need to weigh the benefits of desiccant systems against refrigeration-based solutions to determine which best suits your specific humidity control needs.
Manufacturing facilities making lithium batteries and semiconductors require specialized dehumidification equipment to maintain extremely low humidity levels. You must carefully calculate your airflow load requirements, factoring in variables like the number of personnel, entry/exit frequency, and external environmental conditions that could affect moisture levels.
Based on these calculations, you can then select appropriately sized systems, potentially including integrated solutions that combine both desiccant and refrigeration technologies for ideal humidity management.
Evaluate Desiccant Vs Refrigeration
Selecting the right dehumidification system for your cleanroom requires careful evaluation of both desiccant and refrigeration technologies. When you're managing a cleanroom environment, understanding these key differences will help you make an informed decision.
Feature | Desiccant Systems | Refrigeration Systems |
---|---|---|
Humidity Control | ±2% RH accuracy, reaches -18°C dew point | Less precise, limited to 4°C dew point |
Application | Industrial and critical cleanrooms | Residential and light commercial |
Performance | Superior at low temperatures, highly stable | Requires reheating, less effective at low temps |
You'll find desiccant systems excel in demanding environments where precision is essential. They're particularly effective when you need to maintain extremely low humidity levels or operate in cold conditions. While they're typically more expensive initially, they offer superior stability and control. Clean room specifications must be strictly maintained to ensure compliance with regulatory standards.
Refrigeration systems can be suitable if your cleanroom doesn't require extremely low dew points or precise humidity control. They're often more economical for basic applications but may struggle in industrial settings. For best results, you might consider combining both systems – using refrigeration for primary dehumidification and desiccant technology for fine-tuning your humidity levels.
Consider Airflow Load Requirements
Properly sizing dehumidification equipment starts with a thorough analysis of your cleanroom's airflow load requirements. You'll need to calculate the cubic footage of your space and take into account air change rates to determine the appropriate dehumidifier capacity.
Remember that dynamic operational variables can make precise control challenging, so it's crucial to factor in flexibility when selecting your system. High airflow rates typically require up to 5,000 CFM for maintaining ISO-rated conditions.
To optimize airflow patterns and prevent dead zones, you'll want to implement a cascading design that maintains clean air separation. Position your supply and exhaust points strategically, bearing in mind equipment layouts and personnel movement patterns.
Use computational fluid dynamics simulations to validate your design choices.
Here are key operational factors you can't afford to overlook:
- External environmental fluctuations that can impact room integrity
- Pressure differentials between adjacent spaces
- Production-related temperature and humidity variations
- Impact of personnel and material transfer activities
- Requirements for specialized areas needing separate air handling
Don't forget to take into account maintenance and efficiency aspects when making your final selection.
Choose modular designs that offer easy access for repairs and opt for energy-efficient models to reduce operating costs. Your system should maintain continuous operation while meeting specific industry requirements, such as ESD prevention or high-efficiency filtration.
Match System Size Needs
Matching your cleanroom's dehumidification system to its precise size requirements demands careful evaluation of available equipment options.
You'll need to take into account various models ranging from the compact DA 300N for smaller operations to the robust DA 2400N for large-scale industrial applications.
Select your system based on specific CFM ranges, which typically fall between 501-3,000 CFM, depending on your facility's needs.
When sizing your system, focus on the drying capacity requirements of your space.
Different models offer capacities from 7.3 lbs/hr for modest needs up to 31-44 lbs/hr for intensive applications.
The double-wall housing construction provides enhanced durability and thermal performance for long-term operation.
You'll want to choose a desiccant dehumidifier that maintains humidity control within +/-2% RH for ideal cleanroom performance.
If you're managing a smaller cleanroom, the DA 300N might be sufficient, while larger facilities may require the DA 2000N or DA 2400N models.
Take into account power requirements as well – 480V systems are available for high-demand situations.
Don't forget to factor in integration with your existing HVAC system, as your dehumidifier must work seamlessly with other components like reheat systems and cooling coils to maintain precise environmental conditions.
Monitor Humidity Levels Continuously
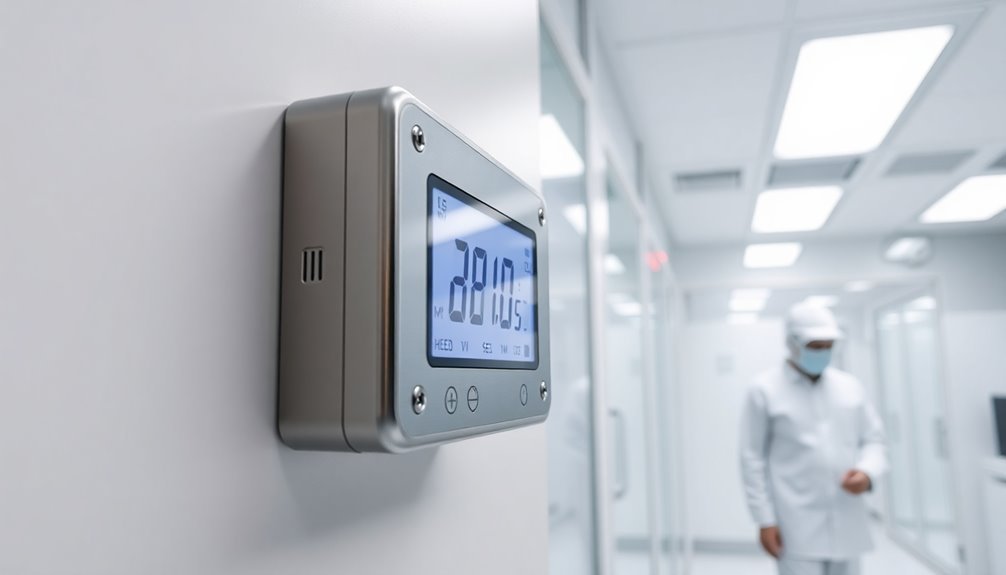
You'll need to set up reliable real-time data collection methods using calibrated sensors to constantly track humidity fluctuations in your cleanroom environment.
Since facility staff training plays a vital role in maintaining cleanroom standards, ensure monitoring personnel are properly educated on system operations.
Integrate your monitoring system with automated alarms that instantly alert you when humidity levels drift outside acceptable parameters.
Maintain strict equipment calibration schedules, typically quarterly or bi-annually depending on your industry requirements, to guarantee your humidity sensors remain accurate and compliant with cleanroom standards.
Real-Time Data Collection Methods
Real-time data collection kicks off with a robust network of high-precision sensors strategically placed throughout the cleanroom environment.
You'll need to integrate these sensors with advanced monitoring devices that continuously track temperature and humidity fluctuations. Modern systems combine wireless transmission capabilities with extensive data logging features, enabling you to make immediate adjustments when conditions drift from ideal ranges.
To effectively implement real-time data collection, you'll want to focus on these key components:
- High-precision sensors working in tandem with data loggers to track minute changes
- Wireless transmission systems that relay information to centralized monitoring stations
- Automated alert mechanisms that notify you of any deviations from set parameters
- Integration with HVAC systems for automatic environmental adjustments
- Extensive data storage for regulatory compliance and trend analysis
You'll find that psychrometers, mechanical hygrometers, and capacitance-type sensors each serve specific monitoring purposes.
By implementing mirror dewpoint indicators and lithium chloride sensors, you're ensuring precise measurements across different environmental conditions. Intelligent control algorithms enable systems to operate efficiently while maintaining optimal conditions.
Remember to maintain regular calibration schedules and train your staff thoroughly on these monitoring systems to maximize their effectiveness.
Alarm System Integration
Building upon your monitoring infrastructure, an integrated alarm system serves as your cleanroom's vigilant guardian.
You'll need to incorporate programmable alarms with customizable thresholds that trigger instant notifications when humidity levels deviate from acceptable ranges. These systems can alert you through email, SMS, or mobile apps, guaranteeing you're always informed of critical changes. The RS 485 Modbus Communication allows for seamless data exchange and system integration across your facility.
To maximize effectiveness, you'll want to integrate your alarm system with existing HVAC infrastructure. This integration enables automatic adjustments to maintain ideal conditions while providing centralized monitoring capabilities.
Place your sensors strategically throughout the cleanroom, and maintain regular calibration schedules to guarantee accuracy.
Don't forget to customize your alarm settings based on your specific cleanroom requirements. You'll need different thresholds for various processes, and your system should accommodate these variations.
Train your staff thoroughly on system operation and response procedures – they should know exactly what to do when an alarm triggers.
Equipment Calibration Schedules
Throughout your cleanroom's operational lifecycle, maintaining precise calibration schedules for humidity monitoring equipment is crucial for reliable performance.
You'll need to calibrate your equipment at least every six months, though high-sensitivity environments may require more frequent adjustments. Make certain you're following manufacturer recommendations and documenting all calibration activities for regulatory compliance.
To guarantee accurate humidity measurements and ideal cleanroom conditions, implement these critical calibration practices:
- Use high-precision calibration instruments and compare sensor readings against known standards
- Schedule calibrations immediately after any major equipment modifications or adjustments
- Maintain detailed calibration records that include dates, results, and technician information
- Employ trained personnel to perform calibrations using proper methods and tools
- Integrate automated calibration tools when possible to streamline the process
Don't underestimate the importance of continuous monitoring alongside your calibration schedule.
You'll want to keep track of real-time data to identify potential equipment malfunctions early and make necessary adjustments promptly. This approach helps you maintain consistent control over your cleanroom environment while extending equipment life and guaranteeing product quality standards are met consistently.
Control Airflow and Entry Points
Effective airflow control and entry point management serve as the foundation for maintaining stable humidity levels in cleanroom environments.
You'll need to guarantee uniform air distribution throughout your cleanroom using static HEPA filtration modules in recirculating systems. Managing air change rates is essential to offset heat loads from equipment, lighting, and personnel while maintaining environmental tolerances.
To control entry points effectively, you'll want to implement double airlocks to minimize humidity fluctuations from frequent entries and exits.
Consider installing a dedicated AC/heater unit to precondition outside air before it enters your cleanroom. You should also monitor external environmental conditions, as they directly impact your internal humidity control strategies.
Your HVAC system must integrate seamlessly with desiccant systems to regulate both temperature and moisture levels.
Remember that temperature control notably affects relative humidity – lower temperatures reduce humidity, while higher temperatures increase it.
By implementing unidirectional airflow in high-demand areas and maintaining proper filtration, you'll reduce maintenance requirements and optimize your HVAC system's performance.
Keep your sensors calibrated for continuous monitoring and real-time adjustments to maintain precise humidity control.
Implement Desiccant Dehumidification Systems
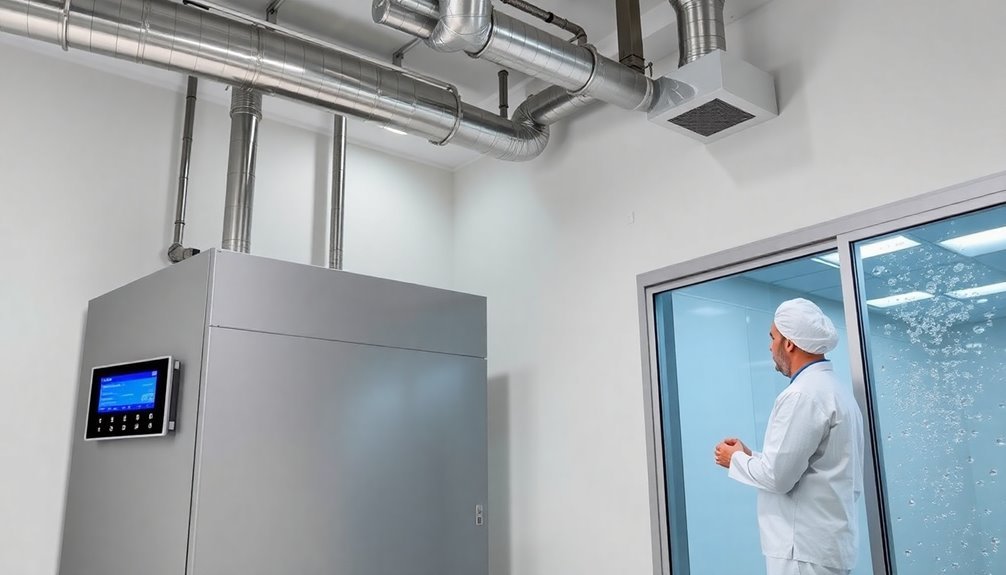
Desiccant dehumidification systems offer significant advantages over traditional HVAC units by maintaining precise humidity control within +/-2% RH and operating efficiently at low temperatures.
You'll want to select a desiccant wheel with a large diameter to guarantee low pressure drop and maximize moisture absorption capacity for your cleanroom's specific requirements.
Your system's regeneration process uses hot air to remove collected moisture from the desiccant material, creating a continuous and energy-efficient cycle that reduces the overall load on your HVAC system.
Advantages Over Traditional HVAC
While traditional HVAC systems have served cleanrooms for decades, modern desiccant dehumidification systems offer distinct advantages that make them increasingly attractive for humidity management.
You'll find these systems deliver superior performance in cold environments where conventional refrigerant-based units struggle. They're also more energy-efficient, helping you cut operational costs while maintaining precise humidity control.
The advantages of desiccant systems extend beyond basic performance metrics. You'll benefit from their compact design and flexible installation options, making them ideal for cleanrooms where space is at a premium.
Their minimal maintenance requirements and fewer moving parts translate to improved reliability and reduced downtime.
Key benefits you'll experience include:
- Reduced energy consumption with potential savings of up to 50% on gas boiler costs
- Consistent performance across varying temperatures, especially in cold conditions
- Enhanced moisture removal capabilities during high humidity situations
- Lower maintenance requirements and longer operational lifespan
- Better air quality control with improved mold and bacterial prevention
These systems integrate seamlessly with existing ventilation setups, offering you a scalable solution that can adapt to your cleanroom's changing needs while maintaining strict environmental standards.
Optimal Desiccant Wheel Selection
Selecting an ideal desiccant wheel requires careful consideration of multiple key factors that directly impact your cleanroom's performance.
You'll need to focus on high-quality desiccant materials like zeolites, silica gel, or activated alumina that won't change phase during moisture collection. These materials should demonstrate strong resistance to degradation and contamination while providing maximum surface area for moisture absorption.
When evaluating wheel construction, verify the desiccant material is thoroughly fused into the surface and evenly distributed.
You'll want a design that minimizes air leakage and maintains consistent air distribution across the wheel. Look for features like intelligent regeneration systems that enhance operational efficiency and reduce energy consumption.
For your cleanroom application, consider the specific performance requirements, including intake temperature, relative humidity targets, and required airflow rates.
You'll need a system that can maintain desired humidity levels consistently while offering continuous operation.
Don't overlook maintenance aspects – choose a wheel that's easy to clean and service. Quality desiccant wheels can last up to 15 years with proper maintenance, so invest in systems that include regular filter replacement capabilities and contamination prevention features.
Regeneration Process And Efficiency
Maximizing the regeneration process stands at the heart of efficient desiccant dehumidification systems. Your system's regeneration cycle relies on a corrugated desiccant wheel that continuously rotates through two distinct airstreams.
As the wheel turns, a smaller exhaust airstream effectively dries off the moisture-laden desiccant material, preparing it for the next absorption cycle.
You'll achieve peak efficiency by utilizing exhaust heat for regeneration, which greatly reduces energy consumption. The process works through a straightforward yet effective mechanism where hot air pulls moisture from the desiccant material, allowing the newly dried sections to rotate back for continued moisture collection.
Key aspects you should monitor in your regeneration process include:
- Proper wheel rotation speed to guarantee adequate moisture absorption and regeneration time
- Exhaust airstream temperature for peak moisture removal from the desiccant
- Consistent airflow patterns through both process and regeneration sections
- Regular inspection of the desiccant wheel for any material degradation
- Maintenance of peak temperature ranges between 32 to 86ºF for maximum efficiency
This regeneration cycle's continuous nature guarantees your cleanroom maintains precise humidity levels while minimizing energy costs.
Maintain Steam Humidification Systems
Steam humidification systems' effective operation depends on rigorous maintenance practices to guarantee consistent humidity control in cleanroom environments. To maintain peak performance, you'll need to focus on preventing mineral scale buildup by using distilled or filtered water in your system. Regular inspections and cleaning of heating elements assure consistent steam output and system efficiency.
Maintenance Task | Frequency |
---|---|
Inspect heating elements | Monthly |
Clean mineral deposits | Quarterly |
Check steam distribution | Weekly |
Test water quality | Bi-weekly |
Verify humidity sensors | Monthly |
You'll want to integrate your steam humidification system with your reheat and AC systems for precise humidity control. When you're operating sensitive cleanroom equipment, it's vital to maintain consistent relative humidity levels. Consider implementing micro-climates for areas requiring specific humidity ranges, and don't forget to monitor system efficiency regularly.
If you're using a high-performance system like the Nortec RS Series, you'll still need to follow manufacturer maintenance guidelines. Remember to design your maintenance schedule around your cleanroom's specific needs, considering factors like room size, worker occupancy, and industry requirements. You can improve system longevity by documenting performance metrics and adjusting maintenance frequencies accordingly.
Address Seasonal Humidity Challenges
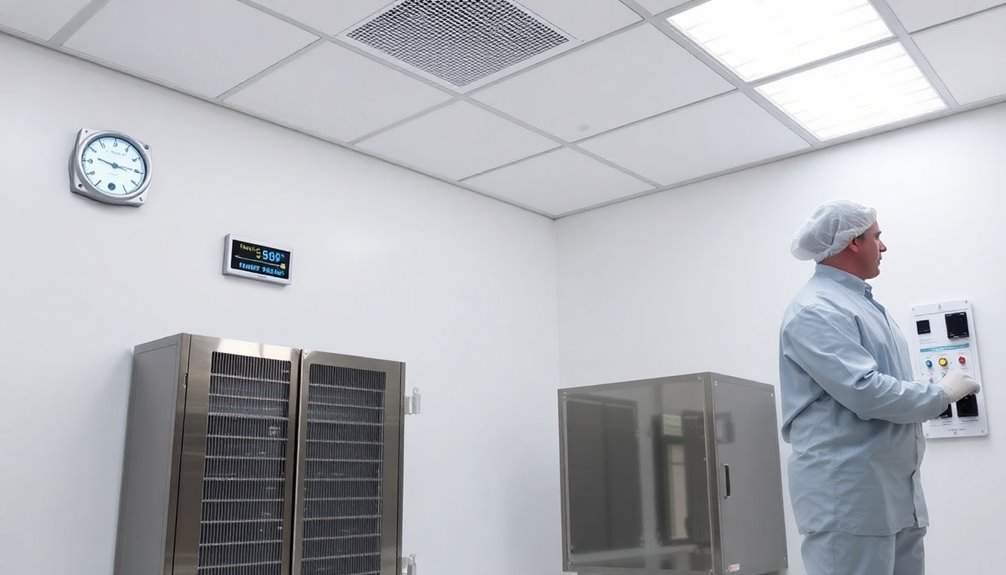
Beyond maintaining your steam humidification systems, you'll need to tackle the distinct challenges each season brings to your cleanroom's humidity control.
Temperature fluctuations and external weather conditions greatly impact your facility's humidity levels, requiring adaptive control strategies throughout the year.
To effectively manage seasonal humidity variations, implement a thorough monitoring and control system that combines multiple approaches.
You'll need to integrate your air conditioning with desiccant systems while maintaining consistent airflow distribution to prevent moisture buildup.
During winter months, when high air exchange rates affect humidity levels more dramatically, you'll need to make regular system adjustments.
Key strategies for addressing seasonal challenges include:
- Utilizing thermo-electric dehumidifiers for efficient moisture reduction during humid seasons
- Installing multiple sensors throughout your cleanroom to monitor and maintain precise humidity levels
- Implementing sophisticated control systems that automatically adjust to external conditions
- Combining resistive steam and ultrasonic humidifiers for energy-efficient operation
- Maintaining humidity within the 30-40% range while preventing static buildup and condensation
Regular testing and system examination guarantee your cleanroom maintains ideal humidity conditions regardless of seasonal changes.
Optimize Energy Usage
Efficiently managing your cleanroom's humidity requires a strategic balance between performance and energy consumption. You'll need to implement several key measures to enhance your energy usage while maintaining strict humidity control standards.
Start by upgrading your HVAC system with smart fan filter control panels that centralize management of humidity, pressure, and temperature sensors. You can greatly reduce power consumption by maintaining efficient air exchange rates and installing high-performance motors.
Don't overlook the importance of regular maintenance, which extends system lifespan and keeps energy usage in check.
Consider incorporating energy-efficient technologies like ultrasonic humidifiers for cool mist production and desiccant systems for improved dehumidification. You'll find that insulated wall panels help retain conditioned air, while programmable fan speed adjustments enable precise airflow control.
For thorough efficiency, integrate your air conditioning with desiccant systems and implement redundant control mechanisms.
You can further enhance energy usage by installing double airlocks to minimize humidity introduction and using dedicated AC units to precondition outside air.
Monitor external conditions regularly and employ adaptive control systems that automatically adjust to environmental changes, ensuring your cleanroom maintains ideal humidity levels while minimizing energy waste.
Prevent Microbial Growth
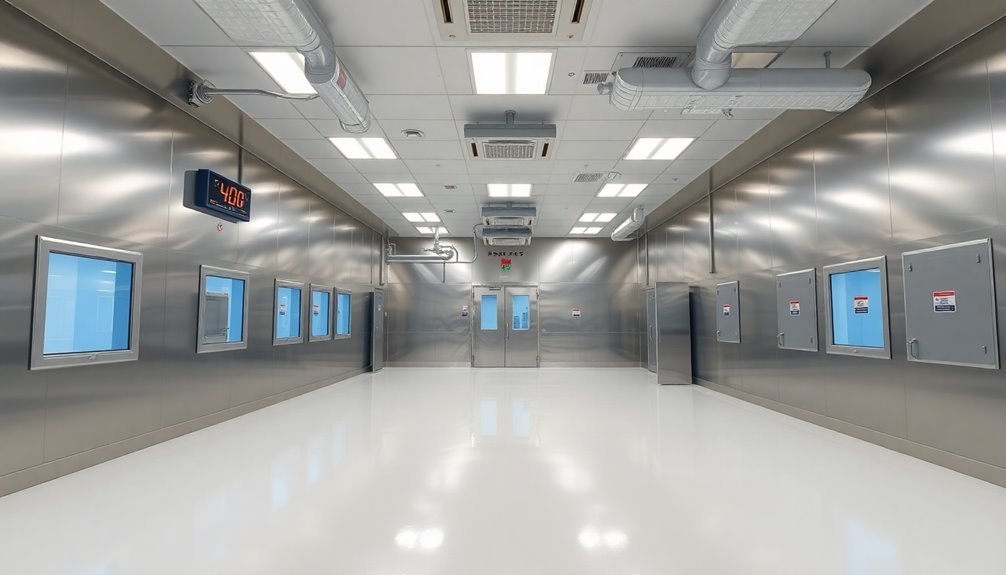
Maintaining proper humidity control is critical for preventing microbial growth in your cleanroom environment. You'll want to keep relative humidity levels between 30% and 40% to create conditions that inhibit bacterial and mold proliferation.
When humidity rises above these levels, you'll face increased risks of condensation and material degradation that can compromise your cleanroom's integrity.
To effectively manage humidity and prevent microbial growth, implement these essential strategies:
- Install an integrated system combining air conditioning with desiccant technology for thorough humidity control
- Monitor humidity levels continuously using hygrometers to detect fluctuations quickly
- Maintain proper airflow distribution to prevent moisture buildup in any area of your cleanroom
- Schedule regular maintenance of your humidity control equipment to guarantee consistent performance
- Conduct frequent testing to verify that humidity levels meet your specific requirements
Remember that temperature directly affects relative humidity, so you'll need to monitor both factors closely.
Different materials and processes in your cleanroom may require specific humidity levels, so adjust your control systems accordingly.
Don't overlook the impact of external conditions – weather changes and nearby moisture sources can substantially influence your cleanroom's humidity levels.
Document Humidity Control Procedures
Proper documentation of humidity control procedures builds upon your microbial prevention efforts and serves as the foundation for consistent cleanroom operations. You'll need to establish clear standards, maintain detailed records, and guarantee your team understands their responsibilities in maintaining ideal humidity levels between 30-40% RH.
Control Aspect | Required Documentation | Action Frequency |
---|---|---|
Monitoring Systems | Calibration records, sensor data logs | Daily checks, quarterly calibration |
Staff Training | Training completion records, competency assessments | Annual training, monthly reviews |
Maintenance | Service records, repair logs, inspection reports | Monthly maintenance, annual overhaul |
Compliance | Regulatory audits, deviation reports, corrective actions | Quarterly audits, immediate reporting |
Your documentation should include precise procedures for using monitoring equipment, responding to deviations, and maintaining control systems. Make certain you're keeping detailed records of temperature influences, especially when operating below 21°C, as this affects your humidity readings by ±2% RH. Integrate your documentation into your facility's quality management system, making it easily accessible to staff and auditors. Don't forget to regularly update your procedures to reflect changes in industry standards and regulatory requirements, maintaining a living document that evolves with your cleanroom operations.
Frequently Asked Questions
How Often Should Cleanroom Humidity Sensors Be Calibrated?
You'll need to calibrate your humidity sensors at least annually, but if you're operating in harsh conditions or high humidity environments, you should increase the frequency to every 3-6 months for ideal accuracy.
What Emergency Procedures Should Be in Place for Humidity Control System Failures?
You'll need backup power systems, emergency shutdown protocols, isolation procedures, and contingency plans ready. Make sure your staff's trained and can quickly implement temporary humidity controls during system failures.
Can Portable Dehumidifiers Be Used as Backup Systems in Cleanrooms?
You shouldn't rely on portable dehumidifiers as cleanroom backups due to their limited capacity, lack of HEPA filtration, and contamination risks. Instead, consider industrial-grade dehumidification systems designed specifically for cleanroom environments.
How Do Cleanroom Gowning Materials Affect Humidity Control Performance?
Your choice of gowning materials directly impacts humidity control. Non-woven fabrics and film laminates can trap moisture, while breathable materials allow better moisture exchange. Consider fabric permeability when selecting cleanroom garments.
What Humidity Indicators Should Be Visible to Cleanroom Personnel During Operations?
You'll need to monitor real-time humidity percentage and temperature readings on large LED displays. Look for blinking alerts or alarm indicators that show when levels are out of specification during your cleanroom operations.
In Summary
Managing your cleanroom's humidity isn't just about hitting target numbers – it's about maintaining product quality and regulatory compliance. You'll need to implement these strategies consistently while monitoring their effectiveness. Don't forget to regularly review and update your humidity control procedures as seasons and requirements change. When you've mastered these humidity management tips, you'll create a more reliable and efficient cleanroom environment.
Leave a Reply