You'll need a thorough monitoring system that integrates ESD prevention with environmental controls to maintain cleanroom standards. Start with proper grounding equipment, including wrist straps and conductive flooring, while implementing real-time sensors for temperature, humidity, and particle counts. Position your sensors strategically within 200 feet of monitoring stations and guarantee continuous data logging every few minutes. Don't forget to maintain humidity levels between 30-40% and temperature at 21°C (±2°C). Install automated alert systems for immediate notification of any deviations. The following strategies will help you maximize your cleanroom's protection against static charge buildup.
Understanding Static Charge Prevention
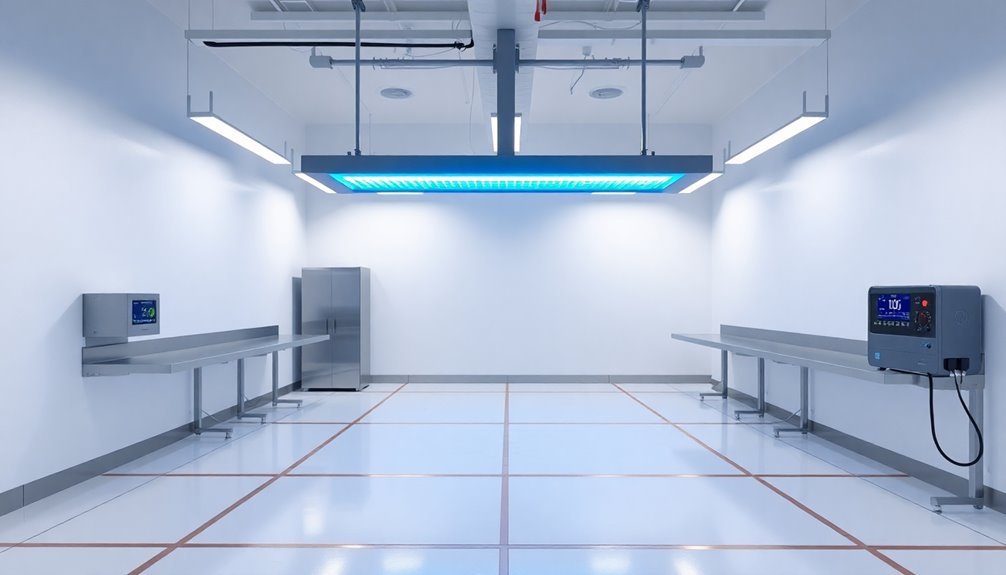
In accordance with cleanroom standards, controlling static charge presents a critical challenge for maintaining product quality and equipment safety. You'll find that electrostatic discharge (ESD) not only causes physical damage to electronic devices but also generates high-frequency electrical pulses that can mimic software bugs and corrupt microprocessor-controlled applications.
Your cleanroom environment naturally generates static through its HEPA filters and low humidity conditions. Without proper dissipation methods, you're facing potential contamination issues as static charges attract or repel particles based on their polarity. To combat this, you'll need to implement thorough grounding techniques for all personnel, equipment, and workstations. The human body can store charges up to 25,000 volts, making proper grounding essential.
You should prioritize using conductive and dissipative materials while minimizing insulators like Teflon that aggressively hold static charges. It's crucial to incorporate ESD flooring systems with compatible footwear to create safe ground paths.
When humidity control isn't practical, you'll want to take into account ionization technology for areas particularly susceptible to static buildup. Remember to conduct regular static audits to identify potential problem areas and verify the effectiveness of your prevention measures.
Your success depends on combining proper grounding, material selection, and ionization strategies.
Essential Monitoring Equipment Requirements
Your cleanroom monitoring setup requires strategic sensor placement at critical control points, including particle counters near work areas and differential pressure sensors at entry points.
Regular calibration and maintenance ensures your monitoring systems consistently deliver accurate measurements over time.
You'll need a reliable real-time alert system that instantly notifies personnel when parameters exceed predetermined thresholds.
Your data logging hardware must meet regulatory requirements with redundant storage capabilities and automated backup systems to guarantee continuous data integrity.
Critical Sensor Placement Strategies
A cleanroom's effectiveness depends heavily on strategic sensor placement and vital monitoring equipment. You'll need to position your sensors up to 200 feet away from the monitoring system while guaranteeing they provide instantaneous readings rather than simple alarm statuses.
To maintain ideal monitoring, you'll want to implement differential pressure sensors between cleanrooms and adjacent areas, temperature sensors for product integrity, and humidity sensors for environmental control. The QuickCheck display system provides immediate visual status updates through color-coded indicators.
Your airflow velocity sensors should be positioned to detect stagnant air pockets and guarantee proper circulation throughout the space.
You must make certain your sensors provide continuous data logging every few minutes and integrate seamlessly with your monitoring systems. It's essential to select sensors that offer digital signal transmission for accurate data collection and maintain high accuracy through regular calibration.
You'll benefit from cloud-based solutions that enable remote access and thorough data management.
For regulatory compliance, your sensor placement strategy should align with ISO 14644 standards. Implement automated alerts through email, text, or external alarms to respond quickly to any deviations from acceptable parameters.
This thorough approach guarantees your cleanroom maintains its required specifications consistently.
Real-Time Alert Systems
Real-time alert systems serve as your cleanroom's vigilant guardian, combining particle counters, sensors, and monitoring software to deliver instant notifications when parameters drift outside acceptable ranges.
You'll need to implement a network of strategically placed sensors that monitor critical parameters including particle counts, temperature, humidity, and differential pressure. Real-time data streams ensure continuous monitoring of all cleanroom conditions.
Your alert system should feature customizable triggers that notify personnel through multiple devices when deviations occur.
You'll want to guarantee your setup includes automated documentation capabilities for maintaining detailed audit trails and regulatory compliance.
The system's data analysis algorithms will help you identify patterns and potential issues before they become critical problems.
To maximize effectiveness, you'll need to select monitoring equipment with proven accuracy and establish regular calibration schedules.
Your system should integrate seamlessly with existing cleanroom infrastructure while providing robust data storage and retrieval capabilities.
Focus on implementing GAMP V model principles during system setup to guarantee reliability and compliance with industry standards.
Data Logging Hardware Requirements
Selecting appropriate data logging hardware stands as the foundation of effective cleanroom monitoring. You'll need equipment that meets precision accuracy standards while guaranteeing robust data storage capabilities for thorough record-keeping. Your hardware must maintain calibration compliance to deliver reliable measurements consistently, enabling efficient data retrieval for quick analysis and reporting.
When implementing your monitoring system, make certain your data logging hardware includes temperature and humidity sensors, particle counters, and differential pressure monitors. Similar to the central monitor unit functionality in healthcare settings, you'll want to integrate these components with advanced data handling capabilities that support real-time analysis and automated logging to eliminate manual processes.
- Choose hardware with precision accuracy ratings of at least ±0.5% for critical parameters
- Install systems with redundant storage capabilities to prevent data loss
- Select equipment that offers automated calibration checks and compliance tracking
- Implement hardware that supports multiple communication protocols for seamless integration
- Verify your system includes built-in alert mechanisms for parameter deviations
Your hardware should support thorough monitoring of air cleanliness, environmental conditions, and pressure differentials while maintaining regulatory compliance.
Don't forget to reflect on scalability features that'll allow your system to grow with your facility's needs.
Humidity Control Systems
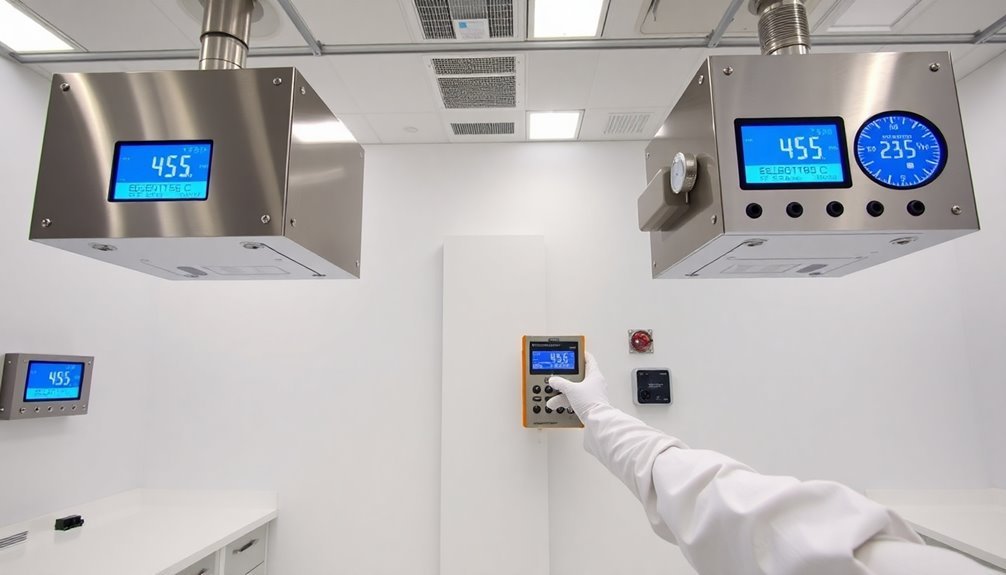
Modern humidity control systems serve as the backbone of cleanroom environmental management, operating within strict parameters to maintain ideal relative humidity levels between 30-40%.
You'll need a combination of dehumidification modules, industrial humidifiers, and reheat systems to achieve precise control over your cleanroom's moisture content.
To effectively manage humidity, you'll want to implement integrated monitoring solutions that use advanced sensors and hygrometers. Double airlocks at entry points significantly reduce humidity fluctuations from worker traffic.
These tools will help you detect fluctuations before they cause static electricity issues or compromise product quality.
Your system should include thermo-electric dehumidifiers for moisture removal without external water requirements, while steam-based industrial humidifiers can add moisture when needed.
You can prevent equipment failures and product degradation by installing customizable solutions that match your industry's specific requirements.
If you're in pharmaceuticals, you'll need different humidity parameters than electronics manufacturing.
Regular testing and maintenance of your humidity control equipment isn't optional – it's essential for consistent performance.
Make sure you're using a combination of control methods, as relying on a single system often won't provide the precise management you need for ideal cleanroom operations.
Remote Monitoring Technologies
Today's cleanroom monitoring landscape relies heavily on remote technologies that transform how you'll track and manage critical environmental parameters.
With automated data collection systems powered by IoT sensors, you're able to eliminate manual logging while maintaining continuous, accurate monitoring of your cleanroom environment. You'll get real-time alerts and can access your facility's data from anywhere, at any time, through cloud-based platforms. The SMART Alert system provides instant notifications via phone, text, or email for any critical events.
These remote monitoring solutions offer powerful data analytics and visualization tools that help you make informed decisions quickly. You'll benefit from detailed reports, graphs, and seamless integration with your existing building management systems. The platforms guarantee top-tier security while providing regular software updates to keep your monitoring system current and reliable.
- Deploy IoT sensors to capture real-time data across multiple parameters simultaneously
- Access your cleanroom data remotely through any device, guaranteeing 24/7 monitoring capability
- Leverage automated alerts to respond quickly to any environmental changes or deviations
- Generate thorough reports for compliance documentation and trend analysis
- Integrate monitoring data with existing BMS/BAS systems for enhanced operational efficiency
Effective ESD Safety Protocols
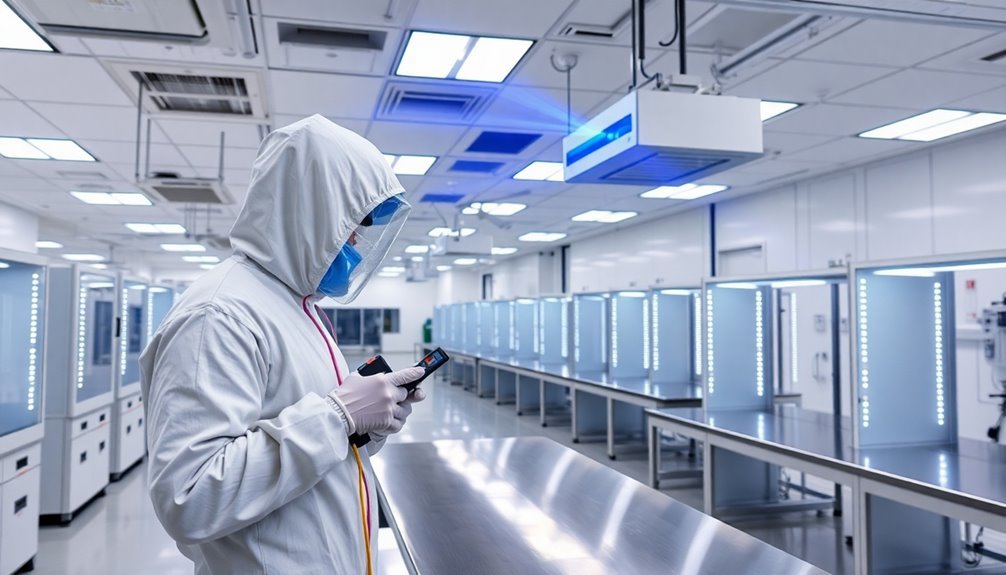
While remote monitoring safeguards your cleanroom's environmental parameters, effective electrostatic discharge (ESD) safety protocols protect your sensitive components and processes.
You'll need to implement thorough grounding systems, including wrist straps and conductive footwear, to prevent static charge buildup that can damage components with voltages as low as 30V.
Start by equipping your cleanroom with antistatic materials for flooring, equipment, and furnishings.
You'll want to install ionization systems and maintain proper humidity levels to neutralize static charges effectively.
Don't forget to use ESD-safe packaging and storage solutions to protect your sensitive components throughout their handling process.
Your personnel should follow strict gowning protocols and use appropriate cleanroom garments. Always ensure personnel move minimally and carefully to reduce particulate generation.
You'll need to enforce proper grounding procedures through wrist straps or flooring/footwear systems.
Make sure you're controlling indirect contamination sources by prohibiting makeup, food, and unapproved cleaning supplies in your cleanroom.
Train all service personnel to follow the same rigorous protocols as your technicians.
Remember to regularly clean and maintain your cleanroom environment to prevent static charge accumulation and guarantee continuous ESD protection.
Environmental Parameter Tracking Methods
Modern cleanroom monitoring demands you'll integrate wireless sensor networks to track multiple environmental parameters simultaneously across your facility.
Your team can leverage these networks to collect real-time data from strategically placed sensors that measure temperature, humidity, particle counts, and differential pressure.
You'll maximize operational efficiency by implementing visualization dashboards that display this data through intuitive graphs and instant alerts, enabling quick responses to any environmental deviations.
Wireless Sensor Network Integration
Integrating wireless sensor networks into cleanroom environments revolutionizes how facilities track and maintain vital environmental parameters. You'll find that these networks combine distributed nodes with heterogeneous designs to create a thorough monitoring system that's both efficient and scalable.
The wireless communication infrastructure enables real-time data transmission while maintaining flexibility for future expansions.
When you're implementing a wireless sensor network, you'll need to address several key considerations to guarantee peak performance. Energy management becomes essential, as battery-powered sensors require efficient power utilization. You'll also want to focus on network security and proper data management to protect sensitive information and maintain regulatory compliance.
- Deploy different types of nodes strategically to cover all vital monitoring points while maximizing coverage efficiency
- Implement robust security protocols to protect against unauthorized access and data breaches
- Establish regular calibration schedules to maintain sensor accuracy and reliability
- Set up automated alerts for immediate notification of parameter deviations
- Use data analytics tools to identify trends and predict potential issues before they occur
These networks integrate seamlessly with existing building management systems, providing you with a unified platform for monitoring and controlling your cleanroom environment.
Real-Time Data Visualization Methods
Throughout cleanroom operations, effective real-time data visualization methods serve as the cornerstone of environmental parameter tracking. You'll need customizable dashboards that display continuous data flows from your temperature and humidity sensors, allowing you to monitor critical parameters instantly and respond to any deviations.
Your visualization system should integrate with high-precision sensors to provide accurate temperature readings and relative humidity data. Set up automated alerts that notify you immediately when parameters exceed acceptable ranges through your computer, tablet, or smartphone. This guarantees you can take prompt corrective actions to maintain cleanroom integrity.
For compliance purposes, you'll want to implement automated logging features that record all environmental data and parameter excursions. These logs support your ISO 14644-1 requirements and help you meet FDA 21 CFR Part 11 standards.
Use advanced algorithms to analyze historical trends, enabling you to enhance your cleanroom performance over time. Configure your dashboard to display real-time data alongside historical trends, helping you identify patterns and potential issues before they become critical.
This thorough approach guarantees you're maintaining ideal cleanroom conditions while meeting regulatory requirements.
Critical Cleanroom Maintenance Standards
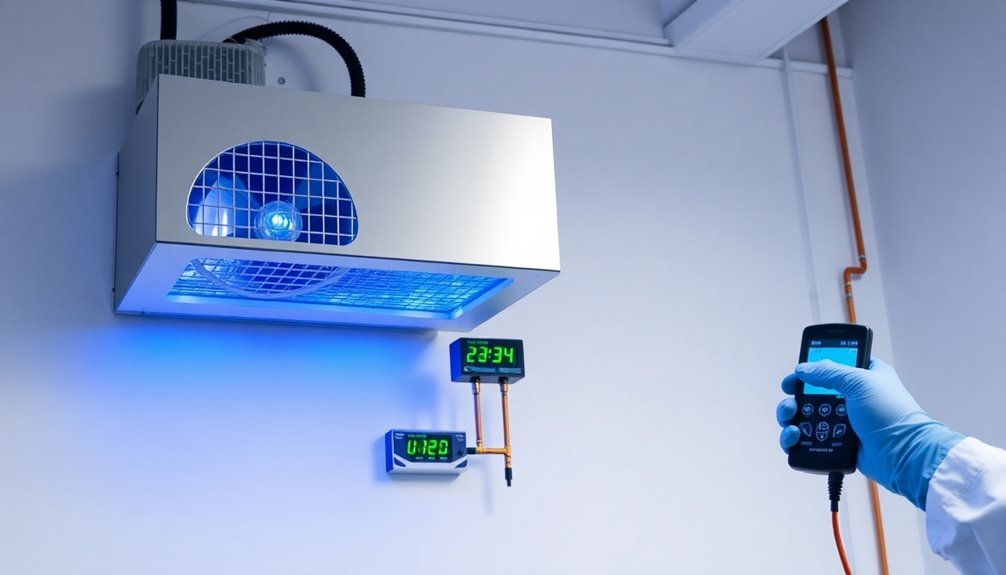
Maintaining vital cleanroom standards requires strict adherence to specific environmental controls and monitoring protocols.
You'll need to guarantee your cleanroom maintains a consistent temperature of 21°C (±2°C) and relative humidity between 30-40% to prevent bacterial growth and static buildup. Your air filtration system must incorporate HEPA or ULPA filters with proper maintenance schedules, while maintaining airflow velocities between 0.305 to 0.508 meters/second for ISO Class 1 environments.
Regular cleaning using specialized non-residue cleaners and non-shedding equipment is essential for maintaining your cleanroom's integrity.
You should implement continuous monitoring systems to track particle counts, microbial contamination, and filtration efficiency, enabling quick responses to any deviations from acceptable parameters.
- Monitor temperature and humidity fluctuations hourly to prevent costly production errors
- Replace HEPA/ULPA filters according to manufacturer specifications to maintain peak filtration
- Use only cleanroom-certified cleaning equipment and agents to prevent contamination
- Maintain detailed logs of all environmental parameters for trend analysis
- Calibrate monitoring equipment regularly to guarantee accurate measurements
Your commitment to these maintenance standards will help safeguard your cleanroom's operational efficiency and prevent contamination-related issues.
Personnel Training and Compliance
Beyond rigorous environmental controls, effective cleanroom operations depend heavily on well-trained personnel who understand and follow strict protocols.
You'll need to implement extensive training programs that emphasize both theoretical knowledge and practical applications through interactive, real-world examples rather than relying solely on traditional teaching methods.
Your training program must cover cleanroom classification awareness, including 'as built', 'at rest', and 'operational' categories.
You should guarantee staff understand the engineering aspects, risk assessment protocols, and contamination prevention measures. Regular testing using contact plates and finger dabs will confirm their adherence to protocols.
To maintain compliance, you'll need to establish clear documentation of all training activities and regularly assess staff competency.
Implement automated monitoring systems that track environmental conditions and provide real-time alerts for any deviations.
Make sure your staff handbook includes detailed personal hygiene expectations, and display these requirements prominently in poster form.
Follow EU GMP Annex 1 guidelines for qualification, content, methods, and evaluation.
You'll need to demonstrate that your personnel training assessment and qualification processes are thorough and ongoing to meet regulatory requirements.
Frequently Asked Questions
How Often Should Cleanroom Monitoring Equipment Be Recalibrated?
You'll need to recalibrate your cleanroom monitoring equipment every 6-12 months, depending on your industry requirements, usage patterns, and manufacturer recommendations. High-risk environments may require more frequent calibration to maintain accuracy.
What Backup Systems Are Recommended During Power Outages?
You'll need UPS systems for critical equipment and backup generators for air handlers. Make certain you've integrated both systems for seamless power shift, and don't forget to test your generators monthly for reliability.
Can Mobile Phones Be Safely Used Inside Cleanrooms?
No, you shouldn't use mobile phones inside cleanrooms. They're significant contamination risks and violate standard protocols. You must use designated communication areas outside the cleanroom and follow proper decontamination procedures when re-entering.
How Do Seasonal Changes Affect Cleanroom Static Control Measures?
You'll need to adjust your humidity control systems seasonally, especially in winter when dry air increases static risks. Maintain 50% RH year-round and modify your ionization and grounding measures accordingly.
What Are the Cost-Effective Alternatives to Permanent Ionization Systems?
You can use portable ionizers, benchtop units, and localized workstation systems as cost-effective alternatives. They're flexible, easy to maintain, and provide targeted protection while offering significant savings compared to permanent installations.
In Summary
You'll find that implementing extensive cleanroom monitoring solutions for static charge prevention requires a multi-faceted approach. Combine real-time environmental tracking systems, proper humidity controls, and ESD safety protocols while ensuring your staff maintains strict compliance standards. By integrating remote monitoring technologies with thorough personnel training, you're better equipped to protect sensitive materials and maintain peak cleanroom conditions.
Leave a Reply