You'll need six vital tools to effectively monitor and control static charges in your cleanroom environment. Start with field meters and voltmeters for basic charge measurement, then add surface resistivity testers to evaluate materials and surfaces. Charge decay analyzers help you assess how quickly materials dissipate static, while environmental monitoring systems track important parameters like humidity and temperature. Don't forget ionization balance devices to monitor ion concentrations and personal grounding testers to verify staff safety equipment. Understanding these tools' specific functions and applications will guarantee your cleanroom maintains ideal static control standards.
Field Meters and Voltmeters
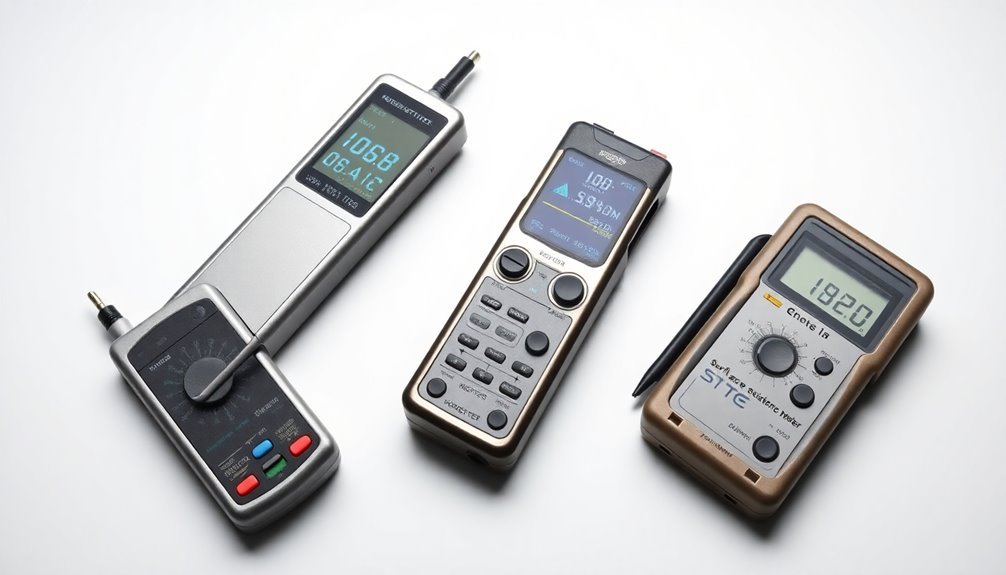
Two essential measuring tools for cleanroom charge control are field meters and voltmeters. These devices help you monitor and manage static charges in critical environments, ensuring the safety of electronic components and manufacturing processes.
Field meters feature non-contacting, chopper-stabilized sensors that provide accurate measurements up to 20 kV. The devices use battery operation with AAA cells. You'll find them equipped with LED guides, four-button controls, and pulsing-beam rangefinders for precise distance measurements.
They're designed for comfort with ergonomic handling and large LCD displays that make readings clear and accessible.
Voltmeters complement field meters by measuring surface voltage and static charge with ±2% accuracy. They'll help you evaluate ionizer effectiveness and calculate conductivity of surfaces.
You can use them to measure voltage differential through insulating materials and determine attractive or repulsive forces between charged surfaces.
Both tools conform to ESD safety standards and come with NIST traceable calibration.
You'll find them invaluable in electronics manufacturing, cleanrooms, laboratories, and industrial operations.
Whether you're testing packaging materials, monitoring equipment, or evaluating antistatic processes, these instruments provide the reliable measurements you need for effective static control.
Surface Resistivity Testing Equipment
Surface resistivity testing equipment stands out among the most important tools for maintaining ESD control in cleanroom environments. You'll find these devices indispensable for measuring the electrical resistivity of various surfaces according to established EOS/ESD, CECC, ANSI, and ASTM test procedures.
When you're evaluating materials, you'll use surface resistivity meters to classify them as conductive, dissipative, or insulative. The typical test kit includes a digital meter with parallel probes and two 5-pound disc probes for precise measurements. The meter's parallel probe design on the back enables quick and efficient surface testing. You'll appreciate features like temperature and humidity displays, which help guarantee accurate readings during your testing procedures.
You can choose from hand-held units for quick quality control checks or complete meter kits for thorough audits. Many models offer multiple test voltage selections and convenient features like automatic zeroing and power shut-off.
Whether you're testing ESD table mats, flooring, or packaging materials, you'll find these tools essential for compliance verification. You'll need this equipment to maintain cleanroom integrity, prevent static damage, and guarantee compliance with standards like ANSI ESD-S20.20.
It's particularly important if you're working in electronics manufacturing, medical device production, or other static-sensitive environments.
Charge Decay Time Analyzers
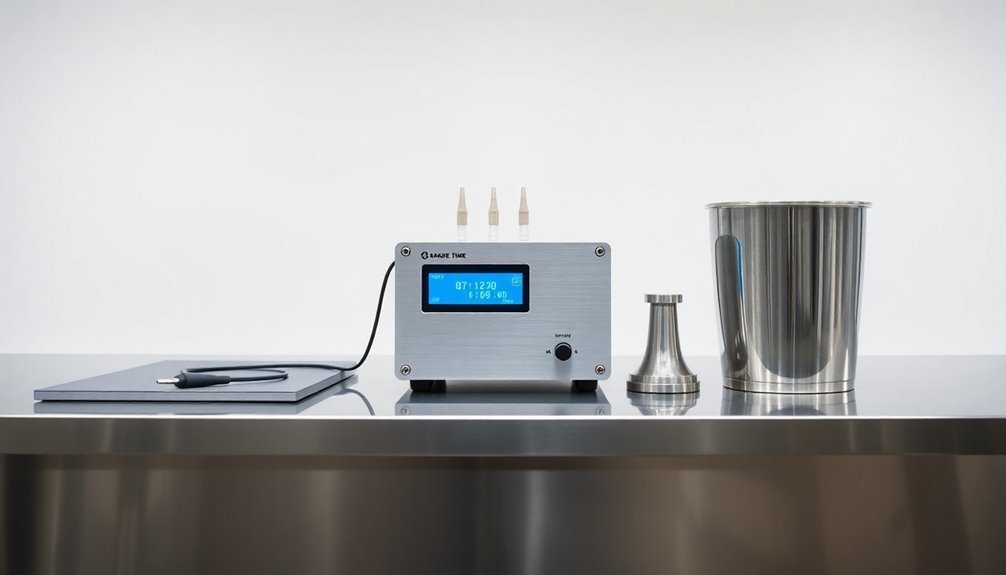
Beyond surface resistivity testing, charge decay time analyzers offer another essential dimension of ESD measurement in cleanroom environments.
You'll find several reliable models available, including the ID917, ID946, and JCI 155v6, each designed to assess how quickly materials dissipate static charges.
These analyzers work by charging your test materials to approximately 5000V using either corona discharge or triboelectrification methods. You can then measure how quickly the charge dissipates to specific threshold points (50%, 10%, and 1% of initial charge). The decay curves are displayed in real-time through sophisticated graphical interfaces.
You'll get real-time data through TFT displays and can store results on your connected PC for detailed analysis.
When you're testing materials, you'll need to follow specific standards like BS EN1149-3:2004 or IEC-61340-4-4.
The analyzers let you select different test voltages and polarities, typically 1kV or 5kV, while offering sampling intervals from 10ms to 10s.
For consistent results, you'll use clamping rings to secure your samples, and some models like the ID-923 can operate within controlled temperature and humidity chambers.
This makes them particularly effective for testing protective clothing, films, and plastics in cleanroom applications.
Environmental Monitoring Systems
A thorough environmental monitoring system serves as your cleanroom's watchdog, continuously tracking multiple critical parameters that affect charge control.
You'll benefit from extensive monitoring of temperature, humidity, pressure differential, and particle counts – all factors that can influence electrostatic behavior in your cleanroom. Cloud or on-premises systems give you flexible installation choices.
The system's real-time data capabilities mean you're instantly alerted when any parameter falls outside acceptable limits. You can monitor everything from a single point to thousands of locations, and the system integrates seamlessly with various sensors through BACnet, MODBUS, and analog inputs.
Your data stays secure through encrypted communications and storage.
You'll find these systems particularly valuable for regulatory compliance, as they meet FDA 21 CFR part 11, GMP, and other critical standards.
The customizable dashboards let you create site-specific floor plans and personalized views of your monitoring data. When issues arise, you're backed by 24/7 support and ongoing training resources.
The investment pays off through improved response times, enhanced data reliability, and reduced contamination risks.
Plus, energy-efficient designs help keep your operational costs in check while maintaining strict environmental control.
Ionization Balance Measurement Devices
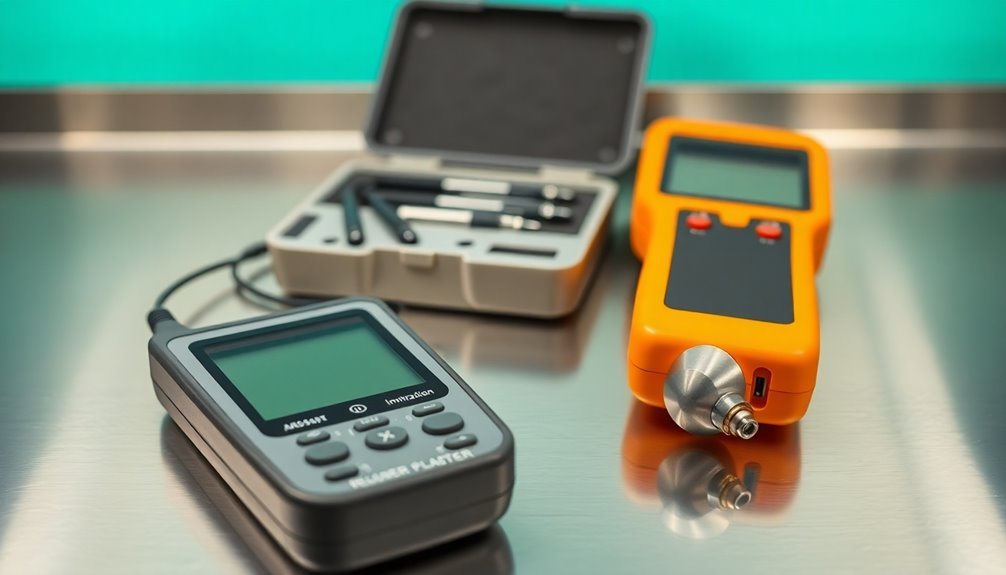
When you're measuring ionization balance in cleanrooms, you'll need specialized detection tools that can accurately monitor both positive and negative ion concentrations.
You'll find that proper calibration of these devices involves regular testing against certified standards, ensuring readings stay within the critical ±5V range for cleanroom applications. Both alpha and corona ionisation methods require precise measurement tools to verify their effectiveness.
To maintain ideal charge control, you should implement continuous balance monitoring using external sensors that can detect environmental fluctuations and trigger automatic adjustments in real-time.
Ion Detector Technologies
Modern cleanroom environments rely heavily on ion detector technologies to maintain precise static charge control. The Charge Plate Monitor (CPM) serves as your primary tool, using a 20 picoFarad capacitance plate to measure electrical charges and evaluate ion balance through voltage readings.
You'll find several types of ion detectors available for your cleanroom needs. Benchtop ionizers work well for specific areas, while overhead units provide broader coverage. Advanced systems can support up to 80 connected emitters through a single controller. If you need targeted control, handheld ionizers offer quick response times. For uniform coverage, you can't go wrong with pulsed DC ion emission bars, and room ionization systems give you superior digital control flexibility.
When selecting ion detection equipment, you'll want to take into account key performance features. Look for balance stability enhanced by ion shields, voltage feedback monitoring for consistent operation, and auto-cleaning capabilities to reduce maintenance time.
For sensitive device manufacturing, make sure you're using Class 0 certified equipment. You'll need to monitor critical metrics like discharge times, offset voltages, and ion density to guarantee peak performance.
Remember to verify that your chosen equipment meets ISO Class 4 standards for cleanroom applications.
Calibration and Testing Methods
Reliable calibration and testing methods guarantee your ionizer performance meets cleanroom standards.
You'll want to focus on two essential measurements: balance (offset) and voltage, both obtained through Charge Plate Monitors (CPMs), which have become the industry's de-facto standard for evaluating ionizer effectiveness.
When you're testing ionizers, your CPM's 20 picoFarad capacitance plate measures how well the device delivers balanced negative and positive ions.
You'll want to check if your ionizer maintains the ideal balance of 0 ±5V, which modern units like the Guardian CR2000 are designed to achieve.
During testing, external sensors help your ionizer adjust its output based on environmental conditions.
Preventative maintenance programs help avoid costly repairs and equipment downtime in the long run.
You should calibrate your equipment at least annually, but you'll need to increase frequency based on usage patterns.
Don't wait for scheduled maintenance if you notice unusual sounds or irregular measurements – these signs warrant immediate calibration.
For best results, you'll want to use professional calibration services that comply with USP Chapter 41 guidelines.
Some newer models, like CoreStat Ion Blowers, require less frequent maintenance while still providing reliable performance.
Balance Monitoring Best Practices
Today's cleanroom balance monitoring relies heavily on Charge Plate Monitors (CPMs) and specialized ionization measurement devices. You'll find CPMs serve as the industry standard for measuring ionizer performance, providing vital data about balance and offset measurements. These tools help you maintain the ideal ion balance of 0 ±5V, guaranteeing optimal static electricity control.
When you're monitoring cleanroom conditions, you'll need to track several key parameters. Air ionizers with built-in sensors can automatically adjust ion output, while ion emission bars deliver uniform coverage across your workspace. Automated systems provide continuous real-time monitoring of environmental conditions. For thorough monitoring, you'll want to incorporate benchtop and overhead ionizers specifically designed for cleanroom environments.
You can enhance your monitoring effectiveness by implementing external sensors to track environmental changes and adjust ion output accordingly. Don't forget to use ion shields at fan outputs – they'll reduce parasitic ion loss and improve balance stability.
For peak performance, you should maintain your equipment regularly and consider using automatic emitter-point cleaners. When selecting your monitoring tools, verify they meet ISO Class 4 certification standards to guarantee high-quality performance in your cleanroom environment.
Personal Grounding Testers
Safety in cleanroom environments hinges on proper personal grounding testing. You'll need reliable personal grounding testers to verify that your personnel's wrist straps, ground cords, and footwear are functioning correctly to prevent electrostatic discharge (ESD) damage to sensitive electronics.
Modern personal grounding testers like the PGT®120 offer simultaneous testing of wrist straps and both shoes, making your testing process more efficient. You'll find both audible and visual indicators that clearly signal whether someone passes or fails the grounding requirements.
The hands-free mode lets your staff test their footwear without manual intervention, streamlining the entry process to your cleanroom. You can adjust testing limits using dip switches to match your facility's specific ESD standards.
Whether you choose battery power or an external power supply, you'll maintain consistent testing capabilities. When installing these testers, you can mount them on walls or use them as benchtop units.
They work in conjunction with your cleanroom's other ESD control measures, including static dissipative flooring and deionizing systems, to create an all-encompassing charge control strategy that protects your sensitive equipment and products.
Frequently Asked Questions
How Often Should Cleanroom Charge Control Measuring Tools Be Calibrated?
You should calibrate your charge control tools every 6-12 months, depending on usage and risk level. If you're in pharmaceutical settings, calibrate every 6 months; for general manufacturing, annual calibration is typically sufficient.
What Level of Training Is Required to Operate Charge Control Meters?
You'll need intermediate to higher vocational education with specific training in IEC 62052-31 standards. You must complete hands-on training, understand electrical safety, and obtain relevant certifications like Snap-on Multimeter Certification.
Can Multiple Charge Control Measurement Devices Be Used Simultaneously?
Yes, you can use multiple charge control devices simultaneously if they're compatible and properly configured. Just verify they're connected in parallel, use matching charging profiles, and have consistent DIP switch settings for synchronized operation.
What Backup Procedures Exist When Charge Control Measuring Equipment Malfunctions?
When your charge control measuring equipment malfunctions, you'll need to isolate the device, activate backup systems, follow emergency protocols, and conduct diagnostics while maintaining continuous operation through redundant measurement tools.
Do Wireless Charge Control Monitoring Systems Affect Sensitive Cleanroom Equipment?
Yes, your wireless charge control systems can affect sensitive equipment through EMI and RFI interference. You'll need proper shielding, frequency management, and strategic placement to minimize these impacts on your cleanroom instruments.
In Summary
You'll need reliable measurement tools to maintain effective cleanroom charge control. Whether you're using field meters to detect static fields, testing surface resistivity, measuring charge decay times, monitoring environmental conditions, checking ionizer balance, or verifying personal grounding – these instruments are essential for your ESD control program. Choose high-quality tools and calibrate them regularly to guarantee your cleanroom stays within specification.
Leave a Reply