Anti-static foam mats require five essential specifications for ideal performance. You'll need proper surface resistivity (between 10^5 to 10^11 Ω/sq for dissipative materials), suitable material composition (typically carbon-containing conductive foam or chemically enhanced polyurethane), appropriate thickness (commonly 2-3 mil), compatible grounding systems that meet ANSI ESD-S20.20 standards, and verified environmental performance metrics including flammability and slip resistance certifications. Don't forget to take into account the mat's layering options, as single, dual, or triple-layer configurations can greatly impact its effectiveness in your specific workspace. These key elements are just the beginning of understanding anti-static protection.
Surface Resistivity Requirements
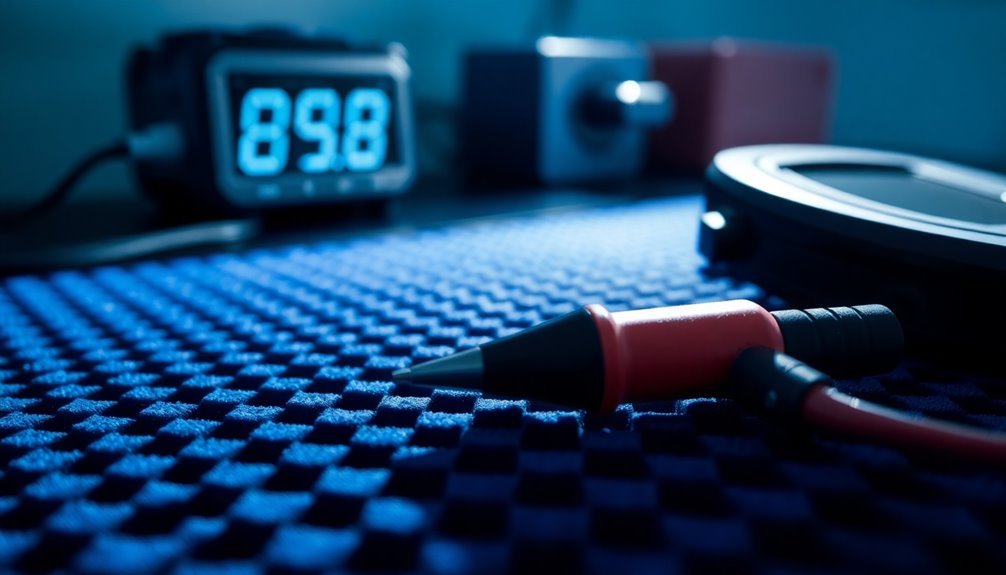
Surface resistivity specifications determine how effectively anti-static foam mats handle electrostatic discharge. You'll need to understand three main material categories when selecting the right mat.
Conductive materials have a surface resistivity below 1 x 10^5 Ω/sq and provide rapid, uncontrolled discharge to ground. While they're antistatic, their fast electron flow isn't always ideal for sensitive components. Regular testing using surface resistance meters ensures consistent performance.
Dissipative materials, with surface resistivity between 1 x 10^5 Ω/sq and 1 x 10^11 Ω/sq, offer the best protection for ESD applications. You'll get controlled electron flow and reliable static discharge, making them perfect for most workplace settings. For optimal performance, consider mats with multiple ESD layers that combine conductive and dissipative properties. Their typical surface resistance ranges from 10^6 to 10^10 ohms/square.
For peak ESD protection, you'll want to avoid insulative materials, which have surface resistivity of 1 x 10^12 Ω/sq or higher. These materials retain static charges and don't provide effective grounding.
When installing your anti-static mat, verify it's connected to a common ground point. The resistance from this point to the AC ground shouldn't exceed 1.0 ohm, and the impedance to the neutral bond should stay under 2.0 ohms.
Material Composition and Layering
Understanding the material composition of anti-static foam mats builds on their resistivity requirements.
You'll find two primary types of foam materials: conductive foam and anti-static foam. Conductive foam contains carbon particles, appears black, and offers surface resistivity below 10^4 ohms/sq, while anti-static foam uses chemically enhanced polyurethane with GMS surfactants and typically comes in pink. The pink anti-static foam allows for slow charge dissipation during use and transport. These mats are commonly used with light colored surfaces to enhance visibility of small parts.
When it comes to layering, you've got several options to take into account. Single-layer homogeneous mats provide basic protection, while three-layer mats incorporate a conductive middle layer for enhanced performance.
Two-layer configurations combine either foam with dissipative vinyl or feature dual rubber layers offering both static dissipative and conductive properties.
You'll need to choose between vinyl and rubber materials based on your specific needs. Vinyl mats are cost-effective and easy to modify, making them popular for tabletop applications.
If you're working in environments with high heat or chemical exposure, rubber mats offer superior durability despite their higher cost.
Remember that proper grounding is essential regardless of the material composition you select, as it guarantees effective static charge dissipation.
Thickness and Size Options
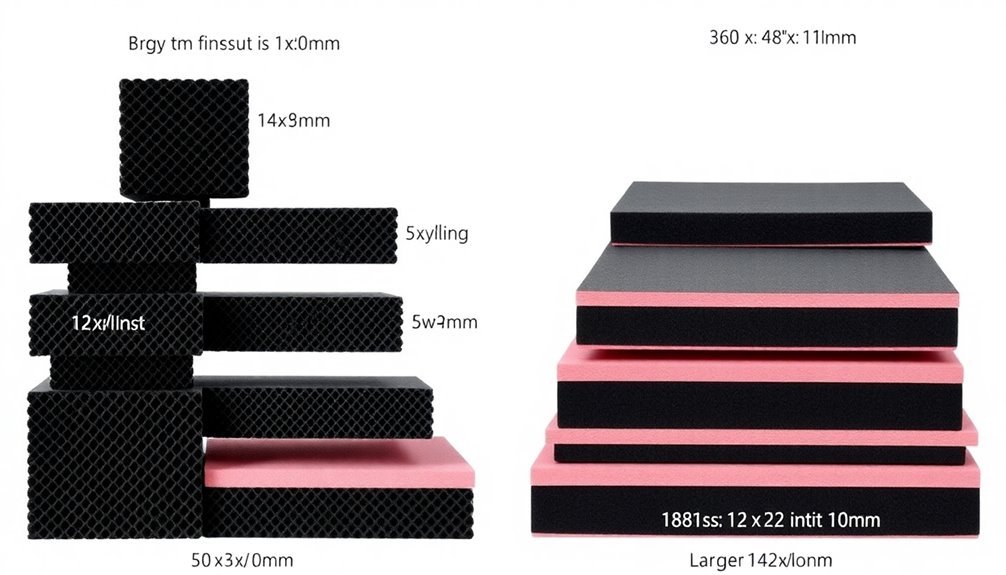
When selecting anti-static foam mats, you'll encounter a range of thickness and size options to match your specific requirements. For standard thickness, you'll typically find 2 mil and 3 mil options available for anti-static floor mats, though specific requirements may call for different thicknesses achieved through material layering. The industrial-grade rubber construction ensures optimal static dissipation while maintaining durability.
You can purchase ESD mats in standard roll sizes of 50' or 60' lengths, with four common width options: 24", 30", 36", and 48". If you're looking for ready-to-use solutions, pre-cut mats come equipped with grounding hardware for immediate installation. Many products offer lifetime warranty on conductivity performance.
You'll also find that most suppliers offer custom cutting services to fit your workspace dimensions precisely. Your application's specific needs will determine the ideal thickness and size for your anti-static foam mat.
For industrial settings, you'll want to assess more durable, thicker options, while mission-critical or military applications may require precise specifications that meet stringent standards.
Remember that both thickness and size directly impact your mat's performance and effectiveness, so you'll need to carefully evaluate your workspace requirements before making a selection.
Grounding System Compatibility
Beyond selecting the right dimensions, proper grounding system compatibility guarantees your anti-static foam mat functions effectively.
You'll need to understand whether your workspace requires an ESD mat with direct grounding or an anti-static mat that can dissipate charges gradually. ESD mats must connect to a ground cord through the center screw of an outlet, while anti-static mats can work effectively without direct grounding when placed on conductive surfaces. Anti-static mats provide moderate electrical resistance for safer charge dissipation. Manufacturers recommend using heel grounders with floor mats for complete static protection.
- ESD mats require proper grounding cables and must comply with ANSI ESD-S20.20 standards for peak protection
- You can integrate anti-static mats with other ESD protection equipment like wrist straps and ionizers
- Ground cords for ESD mats include built-in resistors to guarantee controlled discharge rates
- Your choice between ESD and anti-static mats should match your specific environmental risks and requirements
When handling sensitive electronic components, you'll want to opt for ESD mats due to their low resistance and superior grounding capabilities.
These mats excel in high-risk environments and can be seamlessly integrated with your existing safety equipment.
Remember that proper installation and grounding are essential for preventing potential shock hazards and guaranteeing consistent static discharge control.
Environmental Performance Standards
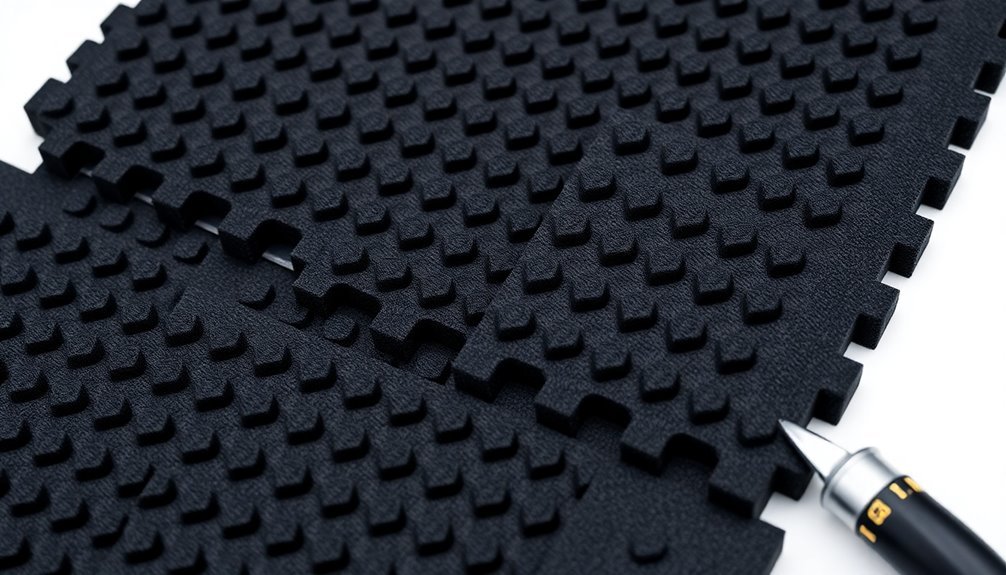
The environmental performance standards for anti-static foam mats encompass four critical testing categories: surface flammability, slip resistance, comfort compression, and ESD performance.
For flammability testing, you'll need to ascertain your mats meet DOC FF1-70 standards, where specimens must pass the pill test with char areas staying within specified limits. You can also verify compliance through alternative methods like BS 4790 or ISO standards 11925-2 and 9239-1.
When it comes to slip resistance, your mats must achieve a static coefficient of friction of 0.60 or higher under ASTM C1028 testing. You can verify this using methods like the British Pendulum Test (ASTM E303) or NFSI 101-C protocols.
Your mat's compression characteristics should fall between 20% and 60% deflection under standard testing conditions. You'll want to avoid mats that compress less than 20% (too hard) or more than 60% (too soft).
For ESD performance, you'll need to verify resistance levels using ANSI/ESD S7.1 standards. Your anti-static mats should measure between 10^10 to 10^12 ohms, while static dissipative mats should range from 10^6 to 10^9 ohms.
Frequently Asked Questions
How Long Does an Anti-Static Foam Mat Typically Last Before Needing Replacement?
You'll need to replace your anti-static foam mat within a year, but you should test it earlier. Regular usage, humidity, and handling can reduce its lifespan, so check ESD properties frequently.
Can Anti-Static Foam Mats Be Stacked on Top of Each Other?
You shouldn't stack anti-static foam mats, as it can compromise their electrical conductivity and grounding effectiveness. If you must store them, lay them flat or roll them individually to maintain functionality.
Are Anti-Static Foam Mats Safe to Use Around Food Preparation Areas?
You shouldn't use anti-static foam mats around food preparation areas. They're designed for electronics, not food safety, and could potentially leach chemicals. Instead, use mats specifically approved for food service environments.
Do Anti-Static Properties Remain Effective When the Mat Gets Wet?
No, you shouldn't rely on wet anti-static mats. Moisture typically compromises their effectiveness unless they're specifically designed for wet conditions. Your standard foam anti-static mats work best in dry environments only.
Can Anti-Static Foam Mats Be Used Outdoors or in Extreme Temperatures?
You shouldn't use anti-static foam mats outdoors or in extreme temperatures. They aren't designed for these conditions, as UV light, moisture, and temperature extremes can degrade the material and compromise their anti-static properties.
In Summary
You've now got the essential specs needed to select the right anti-static foam mat for your workspace. Consider your specific resistivity needs, choose appropriate materials and thickness, verify grounding compatibility, and guarantee it meets environmental standards. Don't forget to check the mat's size options for your workspace requirements. When you follow these guidelines, you'll protect your sensitive electronics effectively.
Leave a Reply