Different grades of conductive foam protection help you match specific needs for your electronic components. You'll find varying density levels that impact shock absorption and durability – high-density foams offer rigid protection for delicate pins, while low-density options provide flexible cushioning for circuit boards. The foam's electrical properties also differ, with surface resistivity ranging from 10^3 to 10^4 ohms/sq, allowing you to select the right static dissipation level. Your choice affects everything from handling efficiency to long-term component safety. Understanding these distinctions can dramatically improve your ESD protection strategy.
Understanding Conductive Foam Basics
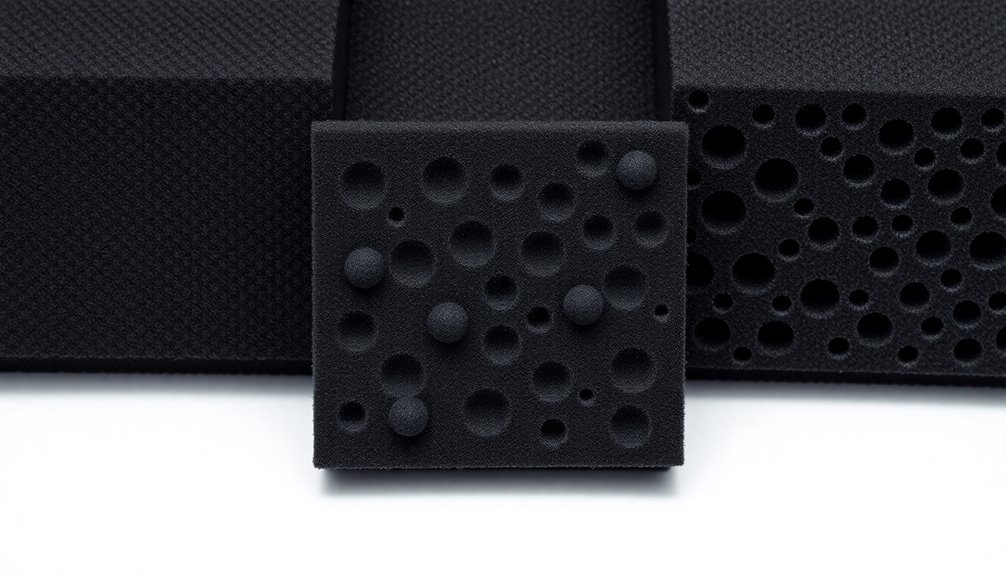
Over the years, conductive foam has become an essential material in electronics protection. You'll find that this specialized foam contains conductive materials like carbon, which gives it unique electrical properties that make it ideal for protecting sensitive electronic components. This protection helps companies achieve reduced product returns while maintaining quality standards.
When you're working with conductive foam, you'll notice it has impressive static dissipation capabilities, with surface and volume resistivity of less than 10^4 ohms. This means it can quickly transfer any static charge to a grounding source, protecting your valuable electronics.
You'll find two main types available: low-density and high-density, each serving different purposes in various applications.
What makes conductive foam particularly valuable is its permanent conductive performance, which isn't affected by humidity changes. When you fully enclose an item within it, it acts like a Faraday cage, providing thorough protection.
The foam's structure, typically made from polyethylene or polyurethane with conductive additives, offers both electrical conductivity and physical protection. You can use it for multiple trips and in-plant handling, and it's customizable to fit your specific size requirements, making it a versatile solution for electronics protection.
Polyethylene Versus Polyurethane Properties
When selecting conductive foam for electronics protection, you'll need to understand the distinct properties of polyethylene and polyurethane materials. Polyethylene foam features a denser, closed-cell structure that's naturally resistant to water and moisture, while polyurethane has a less dense, open-cell composition that excels in shock absorption.
You'll find that polyethylene is the superior choice for ESD protection. When manufacturers add carbon to polyethylene, it achieves a surface resistivity of less than 10^6 ohms, making it ideal for protecting static-sensitive electronic components. The material performs reliably in temperatures from -30 to 80°C, ensuring consistent protection across various environments.
It's also durable and resistant to chemicals, moisture, and mold, which means you can use it repeatedly for storage and transportation.
While polyurethane foam isn't typically conductive, it offers different advantages. You can choose between ester-based polyurethane with smaller cells for rigidity or ether-based with larger cells for softness.
Though it can be treated for conductivity, it's not as effective for ESD protection as polyethylene. However, you can combine both materials in layered applications, leveraging polyurethane's excellent shock absorption with polyethylene's static protection properties.
Density Impact on Protection
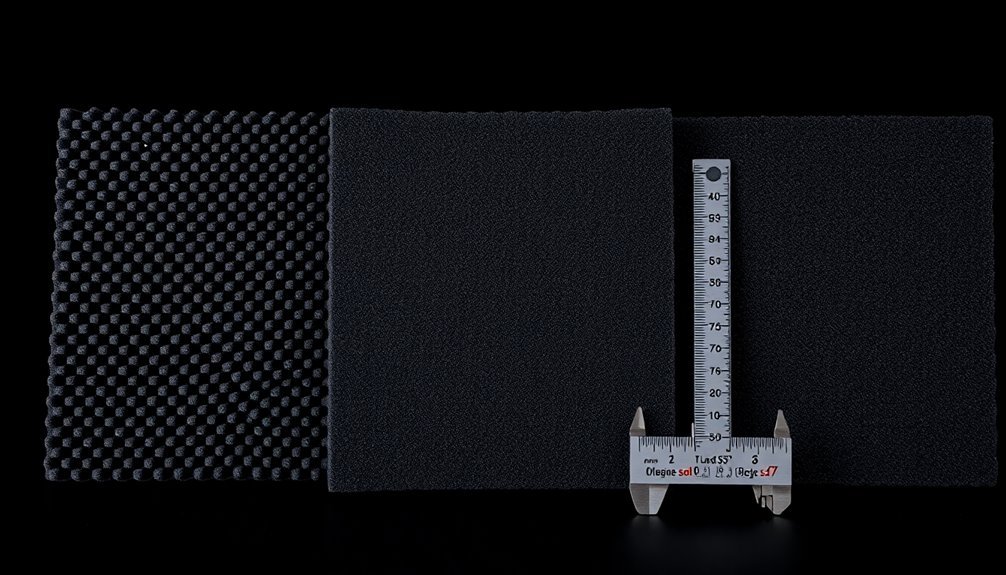
When you're selecting conductive foam for ESD protection, you'll find that density directly influences shock absorption capabilities, with high-density foam offering superior protection against crushing and impact damage.
With a crosslink polyurethane structure, the foam provides consistent protection while maintaining its shape and protective properties over time.
You can rely on high-density foam's rigid structure for repeat handling in manufacturing environments, while low-density options provide adequate cushioning for single-use packaging scenarios.
Your choice between density grades should match your specific handling requirements, as high-density foam maintains its protective properties through multiple uses, while low-density foam may compress more permanently under repeated stress.
Shock Absorption Properties
Throughout the field of protective packaging, foam density plays a critical role in determining shock absorption effectiveness. You'll find that compression deflection and compression set are essential factors when selecting the right foam grade for your needs. Closed-cell beads from the pre-expansion process create the optimal density required for maximum protection.
These properties determine how well the foam can absorb impact and return to its original shape after compression.
When you're evaluating foam protection grades, you'll need to think about the cellular structure's ability to absorb and dissipate kinetic energy. The foam's resilience and energy absorption capabilities directly affect its protective performance.
If you're handling delicate components, you'll want to opt for low-density foams that offer softer, more flexible protection. For applications involving heavy components, you'll find high-density, semi-rigid foams more suitable.
The uniformity of the foam is essential for consistent protection across its surface. You'll notice that different materials offer varying shock absorption properties, and some include fiberglass reinforcement for enhanced flexural strength.
When you're dealing with static-sensitive components, you'll need to think about conductive or anti-static foams that combine shock absorption with ESD protection capabilities.
Durability During Handling
The density of conductive foam directly impacts its durability during handling operations. High-density foams, at around 1.99 lbs/ft3, offer superior rigidity and stability, making them ideal for applications where components have leaded insertions or require firm support. You'll find these grades excel in static-sensitive environments that demand consistent performance over time. The microcellular structure helps prevent dust and other contaminants from compromising sensitive components during handling.
Lower density options provide different handling advantages, particularly in transit packaging. They're more flexible and softer, allowing for better cushioning against impacts. When you're selecting foam grades, consider that products like Condux Plus can compress over 50% while maintaining their ability to rebound to original dimensions – a key feature for repeated handling.
You'll want to factor in environmental conditions, as these materials maintain their protective properties across a wide temperature range (-95°F to +150°F). The foam's resistance to deformation isn't affected by humidity, ensuring reliable performance in various atmospheres.
For long-term storage applications, high-density varieties offer enhanced chemical and physical stability. Whether you're handling components frequently or storing them long-term, the foam's durability characteristics remain consistent, providing continuous protection against static discharge and physical damage.
Resistance Levels and Applications
You'll find a wide range of resistance levels across protective foam materials, from highly conductive options at <10^4 ohms/cm to anti-static varieties reaching 10^10 ohms.
The Conductive crosslink polyethylene RTT with 10^3 – 10^4 ohms resistance provides an ideal middle-ground option. Each resistance level serves specific ESD protection needs, with lead-insertion grade offering the highest conductivity for direct component mounting, while component grade and static dissipative foams provide intermediate protection levels.
The choice between these materials depends on your specific application, with lead-insertion and component grades requiring no additional Faraday cage, while static dissipative and anti-static foams need external shielding for complete ESD protection.
Resistance Ranges By Material
Different protective foams offer distinct resistance ranges tailored to specific electronics protection needs. You'll find that conductive foam provides the lowest resistance range at 10^3-10^5 ohms, making it ideal for highly sensitive electronic components and EMI shielding applications.
Anti-static foam, with its resistance range of 10^6-10^9 ohms, delivers moderate static control that's perfect for general electronic component protection. Pink EPE foam is commonly used in this resistance category due to its non-cross-linked structure. Static dissipative foam falls between these two ranges, offering a balanced approach for components that don't require extreme protection.
When selecting the right foam grade for your application, consider these critical resistance-based factors:
- High sensitivity components require conductive foam's low resistance (10^3-10^5 ohms) to guarantee immediate static discharge and thorough EMI shielding.
- Moderate protection needs are best served by anti-static foam's higher resistance (10^6-10^9 ohms), which prevents static buildup while maintaining safe discharge rates.
- Components requiring balanced protection benefit from static dissipative foam's intermediate resistance range, offering controlled discharge without the extremes of either conductive or anti-static materials.
The resistance ranges remain stable across environmental conditions, guaranteeing consistent protection regardless of humidity levels.
ESD Protection For Components
Protecting sensitive electronic components from ESD requires carefully matched resistance levels for optimum safeguarding. You'll need to select conductive foam with surface resistivity under 10^(4) ohms/sq and volume resistivity under 10^(4) ohms/cms to guarantee proper protection. Modern electronic devices operating at supply voltages of 1V or lower are particularly vulnerable to ESD damage.
For highly sensitive components, you'll want to use high-density conductive foam that provides maximum contact and shielding.
When you're choosing protection grades, you must consider your components' ESD sensitivity levels. TVS diodes and varistors in your components already provide some internal protection, but they need additional safeguarding during transport and handling. You can match your foam's protection level to your application – use static-dissipative foam for moderately sensitive parts and conductive foam for highly sensitive components.
Your foam selection should align with your overall ESD control strategy. If you're handling components in an electrostatic protected area, you'll want foam that complements your existing protection measures like grounding systems and static control packaging.
Remember that your foam acts as a Faraday cage, so you won't need additional static shielding bags when using appropriate conductive foam grades.
Manufacturing Process and Standards
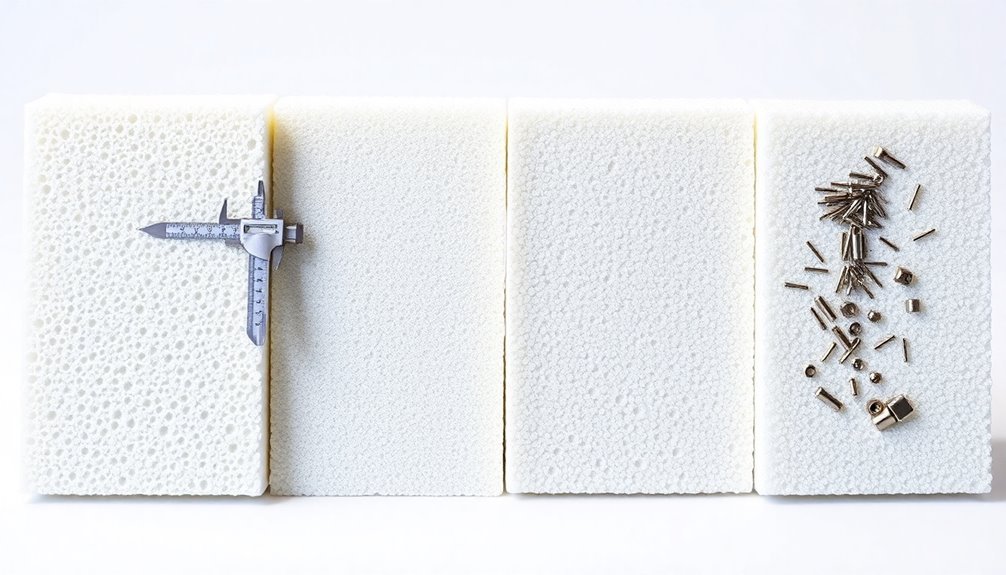
Through carefully controlled chemical processes, conductive foam manufacturing combines specific ratios of polyisocyanates, polyols, and water with conductive components like metal salts or organic compounds.
You'll find that manufacturers use either a single-step method, where they add conductive materials directly to the foam mixture, or a post-treatment approach involving solvent-based application of conductive chemicals.
To meet industry standards, these foams must achieve specific electrical properties, with surface and volume resistivity values below 10^4 ohms for effective ESD protection.
The manufacturing process often takes place in pressurized, closed molds to guarantee uniform cell structure and maximum conductivity throughout the material.
- Quality Control: You'll need to verify that your foam meets the required resistivity specifications, which vary based on your specific application requirements.
- Process Selection: Choose between single-step or post-treatment methods depending on your desired conductivity levels and production scale.
- Material Grade: Consider different foam variants (PU, PE, or PVC) based on your specific needs for EMI shielding, grounding, or general ESD protection.
Storage and Handling Requirements
Proper storage and handling of conductive foam directly impacts its long-term efficacy in protecting sensitive electronic components.
While you'll find that conductive foam is highly resilient across temperatures ranging from +150°F to -95°F, you should still maintain consistent storage conditions to preserve its protective qualities.
You don't need to worry about humidity affecting the foam's performance, as it maintains permanent ESD properties regardless of atmospheric conditions. When you're storing components, you can rely on the foam's consistent resistivity range of 10^3 – 10^4 ohms/sq, which creates a reliable Faraday cage effect when items are fully enclosed. This eliminates your need for additional static shielding bags.
For ideal handling, you'll want to take into account the foam's density based on your specific use case. Choose low-density options for transit packaging where flexibility is key, or select high-density variants for applications requiring frequent handling.
The foam's compression set of 9.8 psi and tear strength of 17 lbf/in guarantee it'll maintain its protective properties during regular use. Remember, the non-contaminating and non-sloughing properties make it safe for critical environments where particulation control is essential.
Cost Benefits and Value Analysis
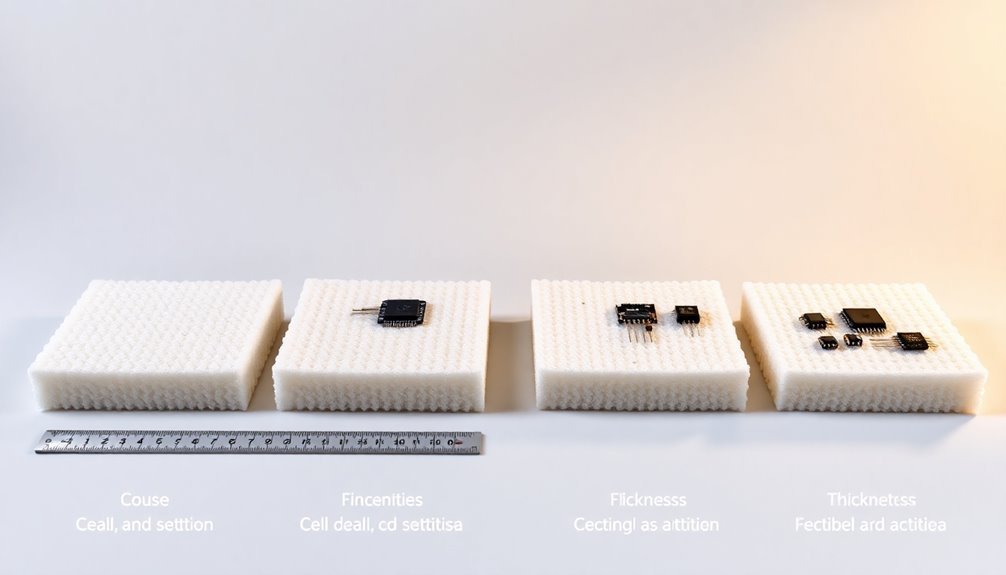
Investment in conductive foam protection represents substantial cost advantages despite its higher initial price point. While you'll pay more upfront compared to standard anti-static or static dissipative foams, the long-term savings and protection value make it a smart economic choice.
You're getting permanent ESD protection, superior cushioning, and moisture resistance that translates into reduced damage costs and fewer component replacements.
The foam's durability and reusability create an impressive return on investment through:
- Reduced maintenance costs – you won't need to replace the foam frequently, and it eliminates the need for additional static shielding materials.
- Protection of valuable components – by preventing ESD damage, you'll save on expensive replacement parts and minimize production downtime.
- Enhanced efficiency – the foam's customization options and reliable performance lead to streamlined handling processes and fewer quality control issues.
When you factor in the foam's resistance to tears, chemicals, and repeated use, you'll find that the cost per use decreases markedly over time. The quality preservation of your sensitive electronic components further justifies the initial investment, making conductive foam protection a cost-effective solution for long-term applications.
Frequently Asked Questions
Can Conductive Foam Be Recycled or Disposed of Safely?
You can recycle conductive foam through sulfonation, mechanical processing, or chemical degradation methods. You'll find it's safer to recycle than dispose of, as it helps reduce landfill waste and environmental impact.
How Often Should Conductive Foam Packaging Be Replaced in Regular Use?
You should inspect your conductive foam regularly, but replacement isn't time-based. As long as it passes quality checks and shows no physical damage or degradation, you can continue using it for multiple trips.
Does Extreme Humidity Affect the Conductivity of Foam Materials?
Yes, you'll find that extreme humidity substantially affects foam conductivity. Your foam material's conductivity increases when exposed to high moisture levels, as water's high thermal conductivity influences the foam's overall performance.
Can Conductive Foam Be Custom-Colored Without Affecting Its Protective Properties?
You can custom-color conductive foam without compromising its protective properties if the dyeing process doesn't disrupt carbon particle distribution. Just guarantee the coloring method won't interfere with the foam's conductivity and ESD protection.
Are There Special Cleaning Methods for Maintaining Conductive Foam's Effectiveness?
You'll need to clean conductive foam using gentle foam swabs and IPA solution. Don't scrub harshly, as it can damage the foam's protective properties. Always use non-corrosive cleaners and avoid excess moisture.
In Summary
You'll need to carefully match your conductive foam grade to your specific ESD protection requirements. Consider your product's sensitivity, handling frequency, and storage conditions when selecting between polyethylene and polyurethane options. By choosing the right density and resistance levels, you're not only protecting your components but also optimizing your cost efficiency. Don't overlook proper storage and handling to maintain the foam's protective properties.
Leave a Reply