ESD monitoring protects your manufacturing profits in five critical ways. You'll catch static buildup issues instantly with real-time detection systems, prevent costly production line failures through strategic monitoring, and achieve up to 95:1 return on investment through data-driven improvements. Your equipment will last longer with continuous protection against damaging electrostatic discharge, while quality assurance tracking guarantees regulatory compliance and minimizes expensive recalls. With potential revenue losses of 6.5% from ESD-related issues, implementing these monitoring strategies can transform your manufacturing operation's bottom line. Let's explore how each approach maximizes your profitability.
Real-Time ESD Risk Detection
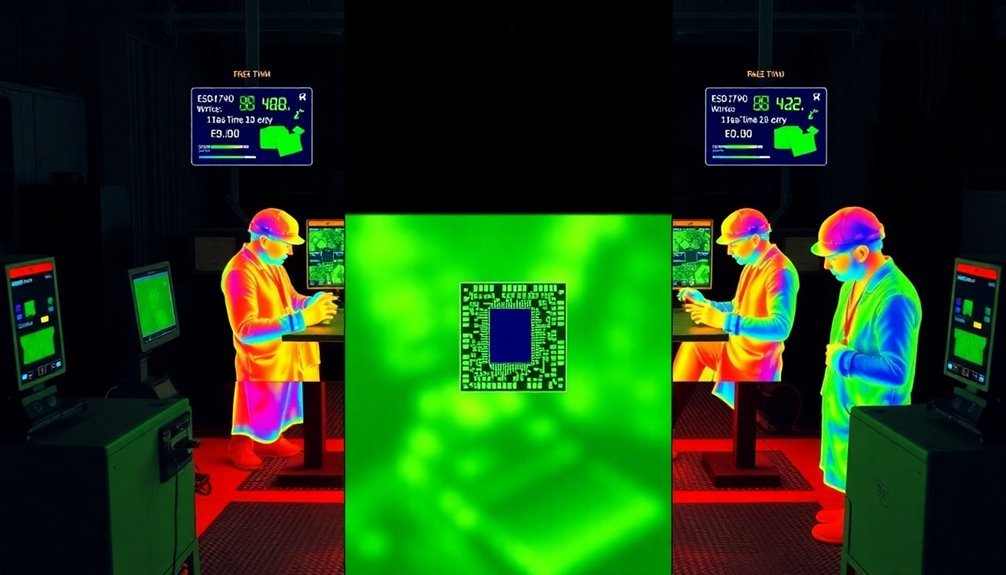
Monitoring electrostatic discharge (ESD) in real time has transformed manufacturing quality control. You'll gain immediate insights into static charge buildup through continuous monitoring systems that track ESD-sensitive components throughout your production line.
These systems don't just detect problems – they create detailed heat maps showing exactly where charges are accumulating, making it easier to identify and address risk areas. The inclusion of dual wire monitors provides an additional layer of reliability by maintaining a secure ground path even if one conductor fails.
With non-contact fieldmeters strategically placed along your manufacturing line, you're able to collect thorough data that's instantly uploaded to a local server. You'll receive immediate alerts when charge levels exceed safe thresholds, allowing your team to take swift corrective action.
The system integrates seamlessly with your existing line management software, providing a complete picture of your ESD protection effectiveness.
You can use this real-time data to make informed decisions about ionizer placement and optimize your ESD protection strategy. The continuous monitoring goes well beyond traditional ESD audits, giving you a robust framework for managing static risks.
Preventing Production Line Failures
Your production line's success hinges on a robust ESD prevention strategy that combines strategic monitoring placement with detailed control measures.
By installing ESD fieldmeters at key locations and integrating continuous monitoring systems into IC handlers, you'll catch potential static discharge events before they cause damage.
To prevent costly production failures, you'll need to implement extensive grounding programs and maintain clean, ESD-safe workstations. Regular training sessions help ensure all employees understand and follow proper ESD safety protocols.
Regular audits of your ESD safety measures guarantee continuous compliance, while proper placement of ionizers in critical areas helps neutralize static charges that could harm sensitive components.
Don't overlook the importance of preventing latent damage – those hidden ESD impacts that mightn't show up until your products are in customers' hands.
You can automatically identify and isolate affected ICs through continuous monitoring systems, saving you from costly returns and reputation damage.
Make certain you're equipping your team with proper tools like grounded wrist straps and ESD-safe materials.
Update your ESD control plan regularly to match advancing technology and increasingly sensitive components.
Cost Savings Through Data Analysis
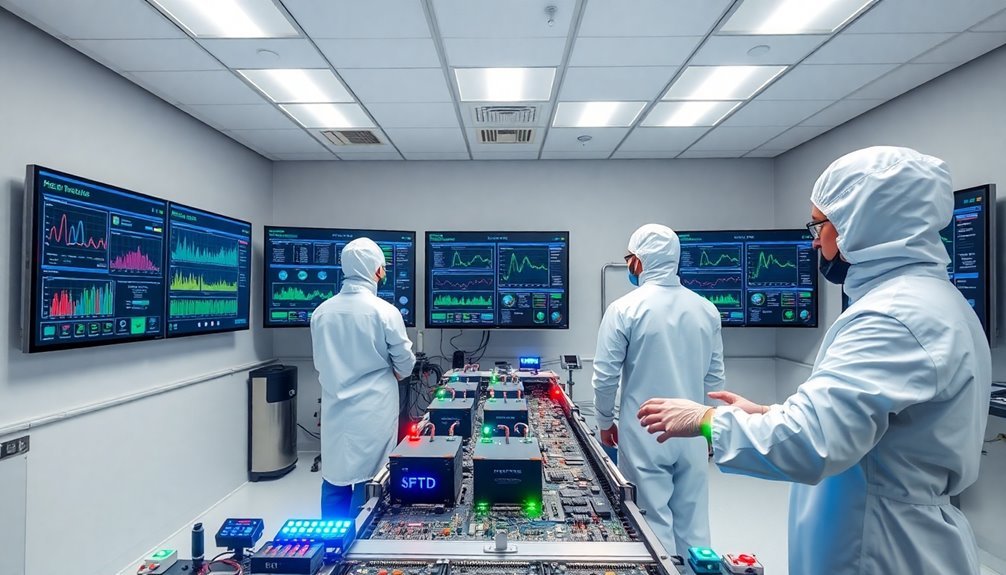
Three key metrics reveal the remarkable financial impact of ESD monitoring: a potential 1,000% yearly ROI, a 95:1 payback ratio, and up to 80% reduction in losses.
You'll find that for every dollar you invest in ESD control, you can save ninety-five dollars while adding roughly 5% to your bottom line without increasing sales.
Hidden costs often lurk in your operational budgets, where ESD-related losses can slash revenues by 6.5% or more. A thorough needs assessment approach helps prevent costly mistakes in implementing ESD solutions.
Some companies discover these losses exceed 10% of their annual revenues when they conduct internal studies.
You'll want to pay attention to latent degradation, which requires costly inspection and rework procedures.
Your data-driven approach should include continuous monitoring of static fields on each PCBA.
You can create heat maps to pinpoint charge buildup locations and make informed decisions about ionizer placement.
Don't forget to maintain regular audits to validate your program's success and justify the savings you've achieved.
As technology evolves, you'll need to adjust your ESD control measures accordingly, keeping your team and management informed of improvements and ROI through consistent feedback and assessment.
Equipment Longevity and Protection
Proper ESD protection delivers a powerful one-two punch: it prevents catastrophic failures while extending your equipment's lifespan. When you implement continuous ESD monitoring, you'll detect potential issues before they cause irreversible damage to your sensitive components, saving you from costly replacements and production delays.
By maintaining an ESD-controlled environment, you're not just protecting individual components – you're safeguarding your entire manufacturing process. Your equipment will operate reliably for longer periods, reducing the frequency of repairs and replacements. Proper ESD controls help prevent latent defects that could lead to premature product failures.
This enhanced longevity translates directly into lower maintenance costs and improved operational efficiency. You'll also contribute to sustainable manufacturing practices by reducing electronic waste and conserving resources.
When your equipment lasts longer, you'll minimize your environmental footprint while maximizing your return on investment. Continuous monitoring guarantees you're maintaining ideal ESD protection levels, preventing both immediate failures and latent defects that could compromise product quality.
The data from your ESD monitoring system will help you identify potential weak points in your protection measures, allowing you to take preventive action before equipment failure occurs.
This proactive approach keeps your production line running smoothly and protects your bottom line.
Quality Assurance Compliance Tracking
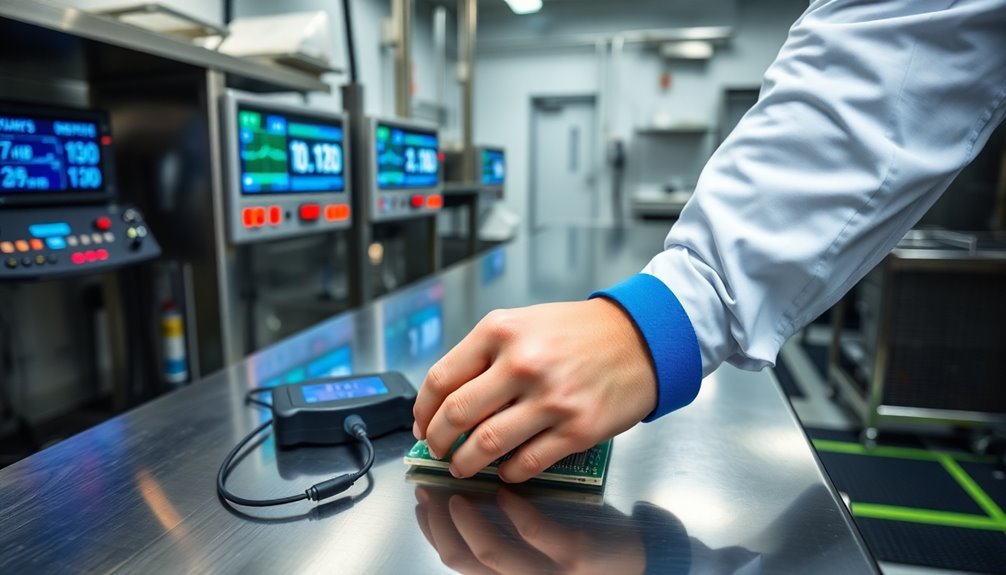
While protecting equipment is essential, maintaining robust quality assurance standards requires thorough compliance tracking. Your ESD monitoring system can serve as a powerful tool for ensuring consistent quality and regulatory adherence through real-time data collection and analysis.
You'll find that implementing an extensive ESD control program helps you identify sensitive items and establish clear procedures for protection. By monitoring ESD events in real-time, you can quickly spot deviations from quality benchmarks and take immediate corrective actions, minimizing costly production delays and potential product defects. Root cause analysis helps pinpoint exact deviation points, enabling targeted solutions and process improvements.
Modern quality tracking software enhances your compliance efforts by integrating with existing systems and providing advanced analytics. You'll benefit from automated features that streamline quality assurance processes, including digital storage of product information and automated work instruction distribution.
These tools help you maintain detailed documentation of your quality control measures and support your regulatory compliance requirements.
Through continuous monitoring and automated reporting, you can track each product component from start to finish, ensuring complete traceability. This systematic approach not only helps you maintain high quality standards but also facilitates efficient product recalls if needed, protecting your bottom line and reputation.
Frequently Asked Questions
How Often Should ESD Monitoring Equipment Be Calibrated and Certified?
You'll need to calibrate your ESD monitoring equipment quarterly for basic checks, while performing thorough annual certifications. Don't forget weekly workstation inspections and monthly static surveys to maintain ideal protection.
Can Wireless ESD Monitoring Systems Integrate With Existing Manufacturing Software Platforms?
Yes, you can integrate wireless ESD monitoring systems with your existing software platforms through protocols like Modbus RTU, enabling real-time data exchange and seamless connectivity with your manufacturing systems and cloud services.
What Backup Systems Are Recommended if Primary ESD Monitoring Fails?
You'll want redundant monitoring systems, cloud-based backups, and portable ESD detectors ready. Don't forget to implement automated data logging and maintain multiple sensor types for thorough coverage during primary system failures.
How Do Temperature and Humidity Affect ESD Monitoring Accuracy?
Both temperature and humidity can affect your ESD monitoring accuracy. You'll find high temperatures can cause device drift, while low humidity increases static buildup. Keep your environment stable for reliable readings.
Which International Standards Govern the Certification of ESD Monitoring Equipment?
You'll need to follow both ANSI/ESD S20.20 and IEC 61340-5-1 standards for ESD monitoring equipment certification. These standards require regular calibration and verification of your monitoring devices' accuracy and performance.
In Summary
By implementing these five ESD monitoring strategies, you'll safeguard your manufacturing profits through early risk detection, reduced downtime, and data-driven decisions. You can extend equipment life, maintain quality standards, and prevent costly product failures. When you're tracking ESD compliance systematically, you're protecting both your bottom line and your reputation in the industry.
Leave a Reply