The most effective real-time monitoring solutions for your production line combine automated sensor systems, IoT integration, and intelligent analytics dashboards. You'll want to implement environmental sensors for temperature and humidity, machine performance tracking tools, and static detection systems with automated alerts. Consider solutions that offer data visualization, quality control monitoring, and predictive maintenance capabilities. Don't forget safety protocols and emergency response features when selecting your system. Look for platforms that integrate with your existing ERP software and provide mobile accessibility. The right combination of these monitoring tools can transform your production efficiency and bottom line.
Environmental Monitoring Basics
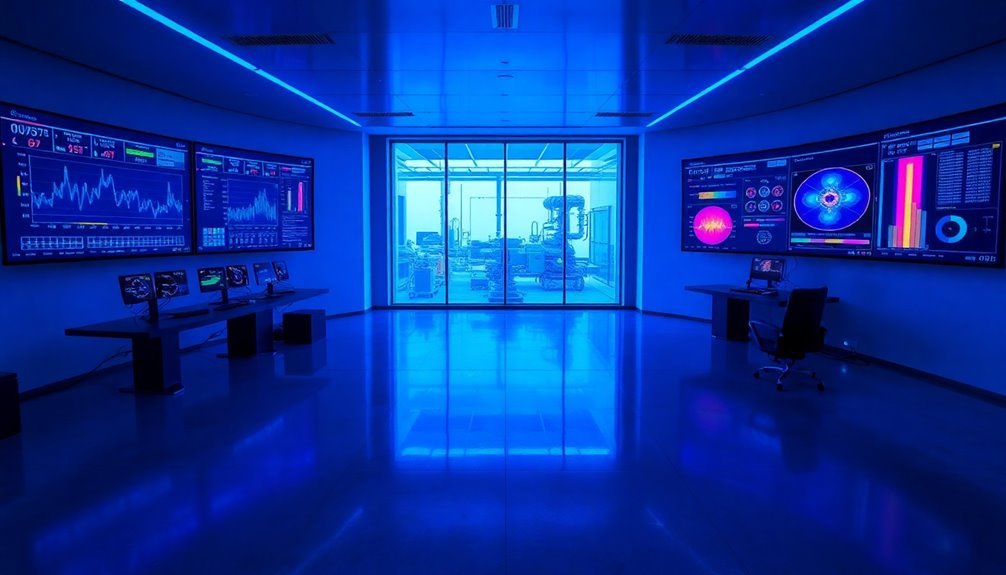
Production efficiency hinges on robust environmental monitoring systems. You'll need to understand that environmental monitoring in production lines involves tracking and controlling factors that can impact your product quality. It's vital for detecting contamination sources early, validating your sanitation processes, and guaranteeing you meet regulatory requirements.
Your environmental monitoring plan must consider process design, product flow, and personnel movement. You'll want to focus on strategic sampling locations, particularly in high-traffic areas and funnel points. Settle plate monitoring should be conducted during each fill operation. By implementing continuous monitoring and real-time data collection, you're able to make prompt decisions based on accurate information.
You must pay special attention to significant control points, including temperature, humidity, and air quality. You'll need to verify your sanitization practices and monitor personnel hygiene consistently. Don't overlook equipment maintenance, as it's essential for preventing contamination.
To implement effectively, you'll want to assemble a diverse team from quality, facilities, production, and microbiology departments. Take a risk-based approach when selecting sampling locations, and guarantee you're complying with FDA regulations and industry guidelines.
Your success depends on continuous monitoring and proper data analysis to identify trends before they become issues.
Real-Time Static Detection Systems
You'll maximize your real-time static detection system's effectiveness by setting precise alert thresholds that match your production line's specific requirements and tolerances.
Through performance data visualization, you can quickly spot trends, anomalies, and potential issues before they escalate into major problems.
Your system's dashboard should display key metrics like equipment status, production rates, and quality indicators in an easily digestible format that enables rapid decision-making. Implementing a comprehensive RTLS infrastructure allows for continuous monitoring of assets and automated tracking of production processes.
Alert Thresholds Integration
Through the implementation of alert thresholds integration, real-time static detection systems provide critical monitoring and protection against electrostatic discharge (ESD) risks on production lines.
You'll find that these systems utilize advanced sensor technology and anti-static hardware to continuously monitor static levels. When predefined thresholds are exceeded, you'll receive immediate notifications through multiple channels, including sound alarms, light signals, and mobile app alerts. Operating in non-condensing conditions, these systems maintain reliable performance across humidity levels from 10% to 90%.
The system's industrial gateways transmit data to central monitoring stations, where real-time analysis helps you identify potential risks before they cause damage.
You can configure your alert mechanisms to match your specific production needs. The system's cloud-based monitoring allows you to access data remotely, while dashboard visualizations help you quickly spot trends and anomalies.
You'll benefit from the integration with incident management and ticketing systems, which streamline your response to static-related issues.
The software integration combines data from various sources, giving you an extensive view of static conditions. You can make data-driven decisions to adjust production parameters, ultimately improving product quality and reducing yield losses due to ESD incidents.
Performance Data Visualization
With advanced visualization tools, real-time static detection systems transform complex ESD monitoring data into actionable insights through intuitive dashboards.
You'll find these systems deliver data visualization across multiple devices, from large production floor screens to mobile phones, guaranteeing you're always connected to critical performance metrics. Static control solutions help prevent costly yield losses in semiconductor manufacturing.
The dashboards you'll work with offer low-latency updates and real-time data representation, helping you spot potential issues before they impact production.
You can customize alert thresholds and visualizations to match your specific monitoring needs, while automated analysis tools continuously scan for anomalies in your static detection data.
When you integrate RTLS capabilities, you'll gain additional visibility into asset positioning and status tracking throughout your production environment.
The scalable nature of these visualization systems means you won't need to worry about outgrowing your monitoring solution as your production expands.
You can access your data through both cloud and client-end platforms, giving you flexibility in how you monitor your production line's performance.
The centralized monitoring hub guarantees all your anti-static devices and sensors contribute to a thorough view of your facility's static control effectiveness.
Data Collection and Analysis
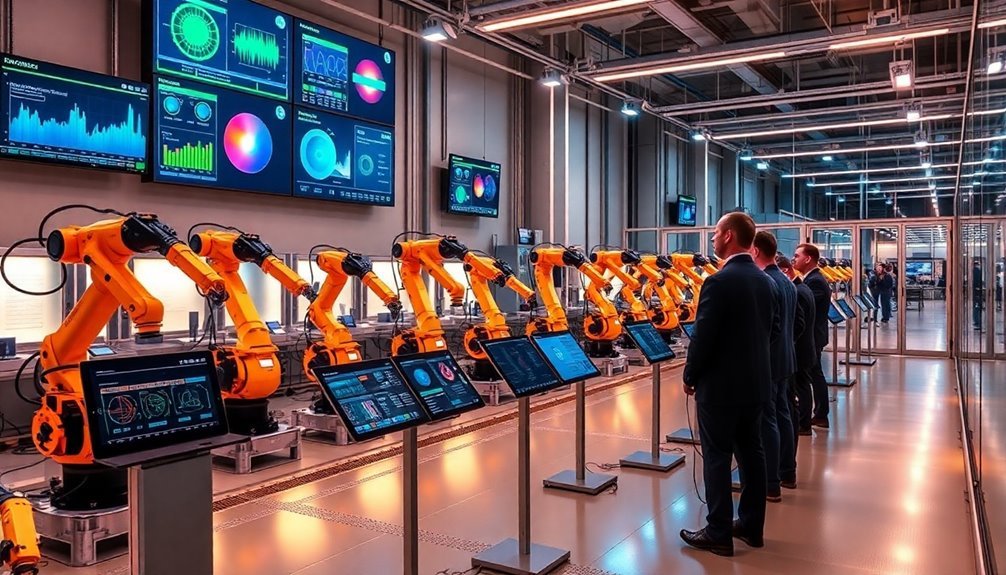
You'll find that automated sensor integration connects directly with your production line through IoT devices and RFID systems, enabling seamless data capture at every critical point.
Your real-time analytics dashboard should display key performance indicators, machine status, and production metrics in an easily digestible format that supports quick decision-making.
The combination of sensor data and visual analytics lets you spot trends, identify bottlenecks, and respond to issues before they impact production quality or efficiency. Edge computing solutions process the collected data locally to minimize latency and ensure instant analysis of production conditions.
Automated Sensor Integration Methods
Modern production lines depend heavily on automated sensor networks that seamlessly collect and analyze real-time data. You'll find several integration methods that can optimize your production line's efficiency and reduce downtime. IoT sensors and SCADA systems form the backbone of thorough data management, while RFID technology enables precise inventory tracking throughout your facility.
To maximize the benefits of sensor integration, you'll need to implement machine-level connections through Ethernet networks, allowing direct data collection from your production equipment. This setup enables real-time monitoring of critical metrics like machine utilization, cycle times, and tool life. Digital transformation has revolutionized manufacturing by enhancing both quality and productivity metrics. You can track alarm statuses and analyze maintenance needs before issues become critical.
These integrated systems support your decision-making process through real-time analytics, helping you identify workflow inefficiencies and production waste. You'll be able to calculate inventory turnover rates and monitor working capital requirements more accurately.
The network also provides valuable insights into production costs and unit expenses, while enabling remote viewing capabilities for quick problem resolution. By implementing these sensor integration methods, you're establishing a foundation for predictive maintenance and continuous quality improvement.
Real-Time Analytics Dashboard Design
Building on your sensor integration framework, real-time analytics dashboards serve as the command center for your production line monitoring.
You'll need to design displays that transform complex data streams into clear, actionable insights while guaranteeing seamless integration with your existing systems. Focus on creating customizable interfaces that provide a holistic view of operations to reduce cognitive load on operators. Operational cost metrics can be directly linked to production activities through financial dashboard integration.
To maximize the effectiveness of your real-time analytics dashboard:
- Position always-up displays showing critical metrics across multiple process areas, including machine efficiency, cycle times, and quality control statistics.
- Implement immediate alerts and detailed KPIs that track machine status, production rates, and utility consumption to quickly identify and resolve issues.
- Design visualization components that clearly display shift production numbers, OEE, and bottleneck identification data for quick decision-making.
- Ascertain your dashboard can scale with increasing data volumes while maintaining robust security protocols.
You'll want to prioritize data-driven decision making by incorporating both real-time metrics and trend analysis.
Your dashboard should enable continuous improvement by transforming raw data into actionable insights that drive operational efficiency and reduce downtime across your production line.
Machine Performance Tracking Solutions
Machine performance tracking solutions stand out as critical tools for staying on top of production efficiency.
You'll gain detailed insights into your operations through real-time OEE monitoring, machine utilization tracking, and automated data collection that eliminates manual entry errors. MachineMetrics delivers these insights within minutes of deployment, enabling immediate value from your manufacturing data.
With color-coded visual dashboards, you can instantly spot production issues and address them before they escalate into costly downtime.
These solutions integrate seamlessly with your existing ERP and CMMS systems, providing a complete view of your production landscape.
You'll be able to implement condition-based maintenance programs and optimize capacity using standardized data analysis.
The incorporation of AI and machine learning capabilities lets you analyze vast amounts of production data to identify patterns and anomalies quickly.
IoT integration enables real-time data collection from both modern and legacy equipment, making it easier to scale across your entire operation.
You'll achieve significant ROI through improved efficiency, reduced waste, and enhanced quality control.
Automated Alert Management Tools
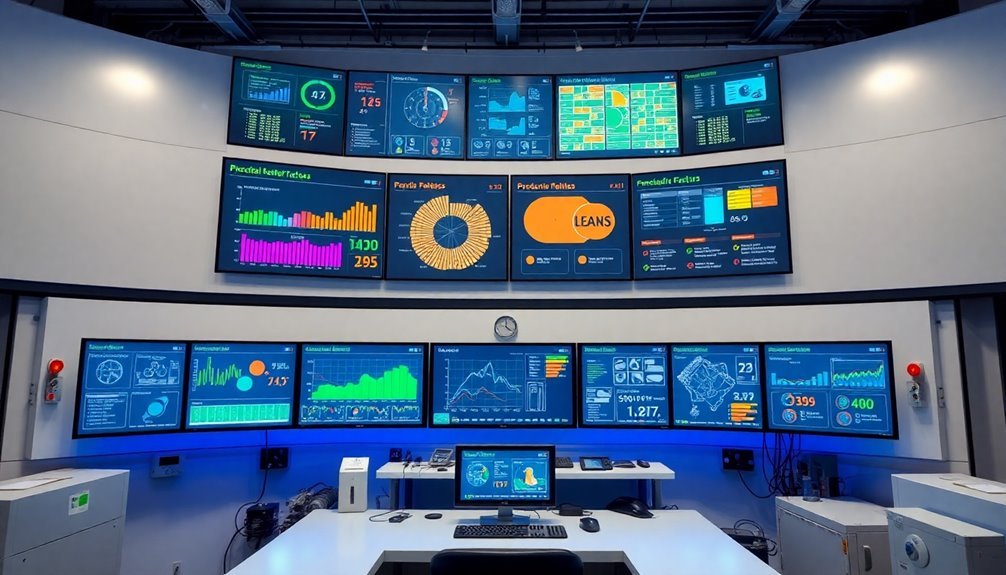
Your automated alert management system needs robust instant response protocols to handle production line issues efficiently.
You'll want to configure priority levels that automatically escalate critical alerts to senior staff while routing routine notifications through standard channels.
Instant Response Protocols
Production floor emergencies demand lightning-fast responses, and automated alert management tools provide the backbone for instant reaction protocols. When issues arise, you'll need a system that instantly triggers notifications and coordinates responses across your entire manufacturing operation.
Your instant response protocols should incorporate these critical elements:
- Real-time alert routing that automatically notifies available responders, escalating issues up the chain of command when necessary and ensuring seamless handoffs during shift changes.
- Customizable notification parameters that let you define specific triggers, conditions, and recipients, while integrating with multiple data sources and communication platforms to reach the right people through their preferred channels.
- Embedded standard operating procedures within alerts that guarantee consistent action plans and proper resolution tracking, enabling you to monitor time-to-resolution metrics and response effectiveness.
- 24/7 visibility across your production lines that helps you maintain proper material levels, control inventory movements, and contain defects before they cascade into larger issues.
Alert Prioritization Systems
Every manufacturing floor needs a robust alert prioritization system to prevent alert fatigue and guarantee critical issues receive immediate attention.
You'll want to implement intelligent filtering mechanisms that categorize alerts based on urgency and impact, making sure your team isn't overwhelmed by non-critical notifications.
Set up threshold-based prioritization to automatically determine alert severity levels. You can leverage AI and machine learning capabilities to enhance your alert system's intelligence, greatly reducing irrelevant notifications while spotting genuine concerns.
Your system should detect anomalies by identifying unusual patterns and correlating related alerts, making it easier to address root causes quickly.
You'll benefit from automated response workflows that trigger immediate actions for critical alerts, minimizing human error and response time.
Configure your system to establish different thresholds for various production scenarios, and verify it integrates seamlessly with your existing IT infrastructure.
When you combine these features with thorough analytics, you'll create a prioritization system that not only filters alerts effectively but also provides valuable insights into recurring issues and system performance patterns.
Quality Control Integration
Modern quality control integration represents a critical cornerstone of successful real-time monitoring systems. When you're implementing quality control into your production line, you'll need to focus on seamless data consolidation and automated measurement devices that can deliver instant feedback.
Tools like Line QC and U-WAVE-R work alongside MTConnect protocols to guarantee your systems maintain consistent quality standards while adapting to changing production needs.
To maximize your quality control integration efforts, follow these essential steps:
- Deploy configurable standards that can flex with your diverse product lines while maintaining strict quality parameters.
- Integrate automated measurement devices directly into your production workflow using Sylcom software or similar solutions.
- Establish a centralized data management system that can handle real-time feedback and analysis.
- Implement proper staff training programs to guarantee smooth adoption of new quality control technologies.
Remember that successful integration often faces challenges like system compatibility and data management.
You'll need to address these proactively by choosing scalable solutions that can grow with your production needs. Focus on solutions that offer real-time monitoring capabilities while maintaining compatibility with your existing machinery and workflows.
Production Line Safety Protocols
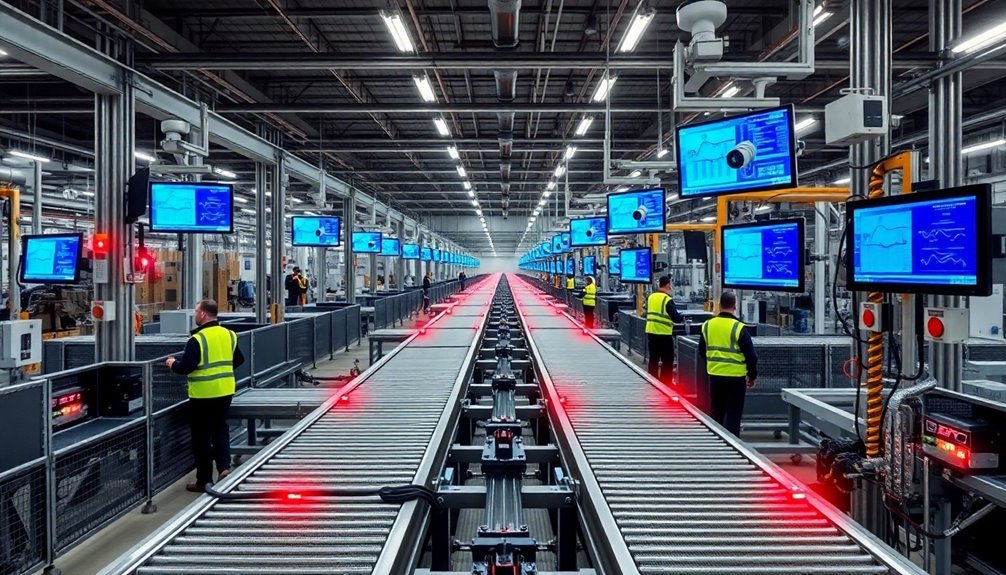
Implementing robust safety protocols on your production line isn't just about compliance – it's essential for protecting workers and maintaining operational efficiency.
You'll need to establish a thorough system that combines real-time monitoring with preventive measures. Start by installing safety sensors and machine guards on your equipment to prevent accidents and automatically shut down machinery when unsafe conditions are detected.
Implement strict lockout/tagout procedures for maintenance work, and make sure your predictive maintenance system tracks equipment performance to prevent failures before they occur.
You should conduct regular risk assessments and update them whenever you modify your production processes. Train your employees thoroughly on safety procedures and provide frequent refresher courses to keep safety awareness high.
Don't forget to enforce PPE requirements and maintain clear emergency exits throughout your facility. Set up strategically placed first aid stations and make sure your emergency response plans are well-practiced.
Install proper ventilation systems to maintain air quality, and keep fire suppression equipment readily accessible. Create a feedback system where workers can report potential hazards, and consider implementing a peer reward program to encourage safe practices.
Static Prevention Technologies
On production lines, effective static prevention technologies are essential for maintaining product quality and worker safety.
You'll find that implementing a thorough static control system requires both active and passive solutions, including grounding, bonding, and ionization systems. By utilizing real-time monitoring with static meters and sensors, you can quickly identify and address potential static buildup issues before they impact your operations.
To effectively manage static in your production environment, follow these key steps:
- Install AC ionizers at critical points along your production line, as they naturally produce opposite polarity for more efficient static neutralization.
- Implement regular monitoring protocols using static meters to measure effectiveness and identify problem areas.
- Train your staff on proper use of anti-static PPE and grounding techniques.
- Select industry-specific solutions and suppliers that match your unique production requirements.
You'll need to take into account your specific industry applications when choosing static prevention technologies.
For instance, if you're in plastics manufacturing, you'll want to focus on resolving process control issues, while cleanroom environments require specialized certified ionization equipment to maintain strict contamination standards.
Continuous Monitoring Best Practices
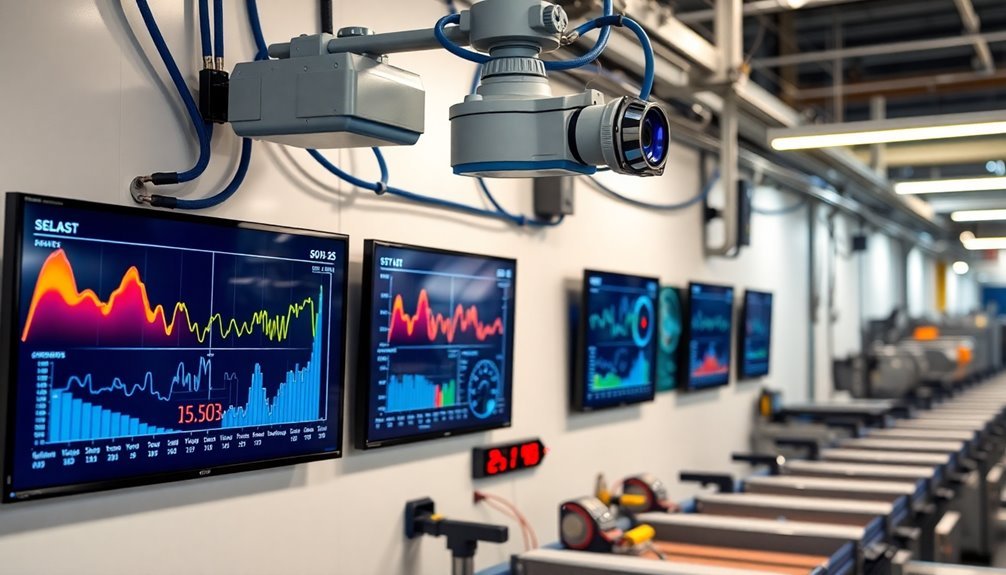
In accordance with industry standards, continuous monitoring best practices revolve around defining clear KPIs and establishing systematic data collection protocols.
You'll need to identify specific, actionable metrics that align with your manufacturing environment's unique requirements and challenges.
To implement effective monitoring practices, you should focus on proactive rather than reactive approaches. This means you'll want to set up systems that can detect anomalies and performance degradation before they lead to significant issues.
You can leverage automation tools to enhance your monitoring effectiveness and guarantee consistent data collection across all shifts and equipment.
Your monitoring strategy should emphasize real-time data analysis using advanced technologies like sensors, cameras, and RFID tags.
You'll need to standardize your data collection methods to establish reliable benchmarks across different machines and production lines.
When analyzing data, prioritize actionable insights that can prevent outages and minimize downtime.
Don't forget to integrate your monitoring systems with existing ERP solutions to create a thorough view of your operations.
This integration will help you identify bottlenecks more effectively and optimize your production processes while maintaining superior quality control standards.
Manufacturing Process Optimization
Building on effective monitoring practices, manufacturing process optimization takes your production capabilities to the next level.
By combining real-time data analysis with automated processes, you'll transform your production line into a lean, efficient operation that consistently delivers high-quality products.
To maximize your manufacturing process optimization, focus on these key areas:
- Implement thorough process optimization techniques like Six Sigma and Lean Manufacturing to eliminate waste, reduce variations, and streamline your operations through data-driven decision making.
- Leverage real-time analytics to track inventory levels, monitor demand fluctuations, and identify potential disruptions before they impact your production schedule.
- Deploy automated and augmented processes using IIoT devices to monitor facility data, enhance safety, and create thorough transparency across your production line.
- Establish standardized data collection and best practices by comparing performance across different machines and shifts, helping you set realistic benchmarks and identify areas for improvement.
Frequently Asked Questions
How Long Does Staff Typically Need for Training on Real-Time Monitoring Systems?
You'll need several weeks to months for extensive training, depending on your role's complexity. You can expect hands-on sessions, theoretical learning, and ongoing workshops to maintain your proficiency with monitoring systems.
What Is the Average Return on Investment Timeframe for Implementation?
You'll typically see ROI within 8-9 weeks of implementation, with systems often achieving a 6X return. Downtime reduction alone can deliver 116-290% ROI, while quality improvements and efficiency gains accelerate your payback period.
Can Multiple Production Facilities Be Monitored From a Single Control Center?
Yes, you can efficiently monitor multiple production facilities from one control center. You'll have real-time data collection, integrated insights, and centralized control across all locations through cloud-based monitoring systems and IoT devices.
How Frequently Should System Calibration and Software Updates Be Performed?
You'll need to calibrate your systems annually at minimum, but critical equipment may require monthly checks. Schedule software updates quarterly, unless security patches demand immediate attention based on manufacturer recommendations.
What Backup Systems Are Recommended During Network Outages or System Failures?
You'll need UPS systems, diesel generators with ATS, redundant data storage, and cloud-based backups. Don't forget to implement local mirror servers and emergency communication protocols for immediate failover capability.
In Summary
You'll find real-time monitoring solutions essential for maintaining efficient production lines. By implementing these tools and best practices, you're better equipped to prevent downtime, optimize performance, and guarantee worker safety. Start with basic environmental monitoring and gradually integrate more sophisticated systems. Don't forget to regularly review and update your monitoring protocols to stay ahead of potential issues and maximize manufacturing efficiency.
Leave a Reply