Anti-static foam protection offers customizable solutions through various cutting techniques like die cutting, waterjet, and laser cutting to achieve perfect fits for your sensitive equipment. You'll find multiple foam types available – PE, EVA, EPE, and PU – each with specific properties for different protection needs. Your choice should account for product weight, fragility, and environmental factors to guarantee maximum protection. Custom fabrication services can create precise dimensions and shapes while maintaining the foam's essential static-dissipative properties. Whether you need simple foam sheets or complex 3D-molded inserts, today's manufacturing capabilities can match your exact specifications. The journey to finding your perfect protective solution is just beginning.
Understanding Anti-Static Foam Properties
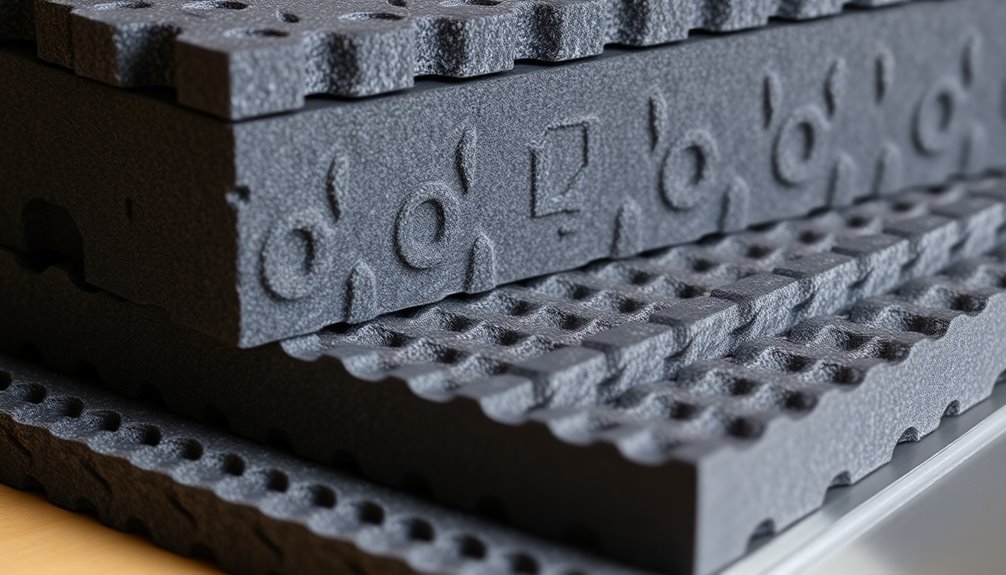
Anti-static foam comes in several vital varieties, each engineered with specific properties to protect sensitive electronic components from static discharge. You'll find PE foam for general-purpose applications, EVA foam with controlled dispersion properties, and EPE foam for high-quality protection. PU foam and crosslink varieties like LD30 and LD32 round out your options for both dissipative and conductive needs.
When you're working with anti-static foam, you'll need to think about its key properties. The material dissipates electrostatic charges while providing essential mechanical protection against shock and impact. Chemically enhanced agents help prevent static charge generation during rubbing contact.
Pink anti-static foam, which you'll commonly encounter, performs best in humid conditions with a volume resistivity of 10^(10) to 10^(12) ohms/cms. However, you should note its limitations – it's designed for single-trip shipping and loses its protective properties over time, especially in low-humidity environments.
For long-term protection, you'll want to think about permanent ESD foams instead of temporary solutions. The foam's surface resistivity typically exceeds its volume resistivity, and you'll need to match these specifications to your specific application requirements to guarantee adequate protection for your electronic components.
Custom Cutting Techniques
Choosing the right cutting technique for your foam applications can dramatically impact your project's success. Each method offers distinct advantages depending on your specific requirements and production volume.
Die cutting is your best choice for high-volume production where you'll need consistent, precise shapes repeatedly. You'll get excellent uniformity, though you're somewhat limited in design complexity. The customized cutting die allows for rapid production of identical foam parts in large quantities.
For intricate designs and complex geometries, waterjet cutting delivers exceptional precision without applying heat to the material. It's particularly effective when you need smooth edges and detailed patterns.
If you're working on small-scale projects that demand high precision, laser cutting provides clean edges and minimal waste. While it's more expensive than other methods, you'll achieve superior accuracy for detailed work in electronics and luxury packaging.
When you need three-dimensional foam shapes, thermoforming is your go-to solution. It's ideal for creating complex 3D parts with smooth finishes, though it may not be cost-effective for large production runs.
Consider your project's volume, complexity, and budget when selecting a cutting method. The right technique will guarantee your anti-foam protection meets exact specifications while maintaining quality standards.
Foam Selection Guide
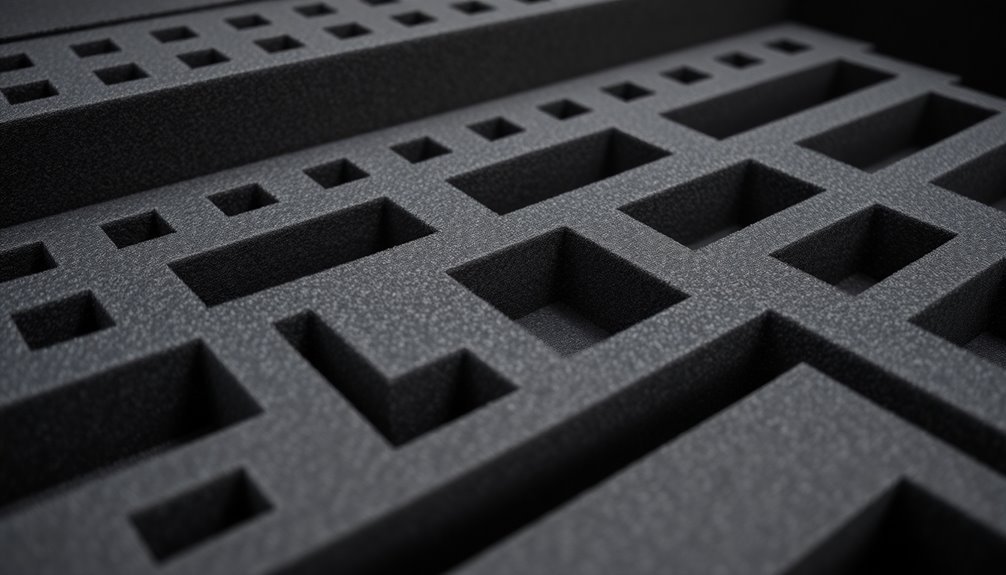
You'll need to carefully match your foam material to your specific protection requirements by considering factors like product weight, fragility level, and cushioning needs.
For ideal protection, you should measure your product's static loading (weight divided by surface area) and determine its G-value rating to select the appropriate foam density. Using drop test data is essential for defining optimal fragility levels.
Your selection process must also account for practical considerations like drop height requirements and budget constraints, which will help narrow down your options between polyethylene, polystyrene, polyurethane, or specialty foams.
Matching Materials to Needs
A successful foam protection strategy begins with selecting the right material for your specific needs. When you're choosing between open-cell and closed-cell foams, evaluate your product's requirements for shock absorption, moisture resistance, and durability. Surface tension reduction is crucial when incorporating foam control agents into your protection system.
You'll want to select open-cell foam when your priority is shock absorption, flame resistance, or airflow. It's particularly useful when you need flexibility and customization options. The larger cell structure makes it ideal for applications where moisture needs to escape, and you can choose between expanded or ether-based polyurethane variants.
For applications requiring insulation and chemical resistance, closed-cell foam is your best choice. You'll find it excels in protecting medical products and sensitive equipment, offering superior resistance to mold and bacteria.
Evaluate expanded polystyrene, polyethylene, or cross-linked polyethylene options based on your specific needs.
Don't forget to factor in the foam's PPI (Pores Per Inch) and thickness – these characteristics directly impact performance. If you're handling electronic components, look for anti-static formulations.
For high-value or fragile items, you might want to evaluate foam-in-place systems that provide customized protection.
Measuring for Optimal Protection
Proper measurements form the foundation of effective foam protection. You'll need to carefully evaluate both the physical dimensions and process conditions to guarantee the best anti-foam performance.
Start by measuring the foam height and formation rate under your specific operating conditions, using specialized foam height sensors or stability analyzers for accurate results.
You'll want to conduct bench testing to determine the most effective defoamer concentration. Begin with small dosages and gradually increase them while monitoring the results. Use precise metering equipment, such as peristaltic pumps, to maintain accurate dosing levels. Following manufacturer dosage guidelines is crucial for optimal performance.
Don't forget to take into account temperature, pH, and shear conditions that might affect the defoamer's performance.
To maintain the best protection, you'll need continuous monitoring and adjustment. Keep track of foam breakthrough points and visual indicators of excessive foaming. Test different application points to find where the defoamer works most effectively in your system.
Document your findings and maintain detailed records of dosage requirements and performance metrics. Remember to verify that your measurements align with safety regulations and environmental standards while verifying that the defoamer remains compatible with your process conditions.
Design Specifications For Packaging
Creating effective design specifications for packaging requires careful consideration of both technical and consumer-focused elements. You'll need to start by developing clear goals that align with your target audience's preferences while guaranteeing the packaging meets essential protective requirements.
When designing anti-foam protection packaging, you'll want to focus on dynamic cushioning calculations to determine the ideal thickness needed for each face of the product. You must select materials that can withstand various environmental challenges, including temperature shifts, electrostatic charges, and impact forces. The primary packaging layer must make direct contact with the product to provide immediate protection.
Your specifications should detail how the packaging will seal out dust, moisture, and other contaminants.
The structural design must account for practical considerations like manufacturability, cost efficiency, and storage space requirements. You'll need to integrate these technical aspects with consumer-centric features that make the packaging easy to handle and use.
Don't forget to specify how your design will maintain brand consistency through appropriate color schemes, typography, and visual elements.
Your final specifications should include detailed measurements, material requirements, and production guidelines that guarantee both protection and user experience goals are met while staying within budget constraints.
Material Handling Best Practices
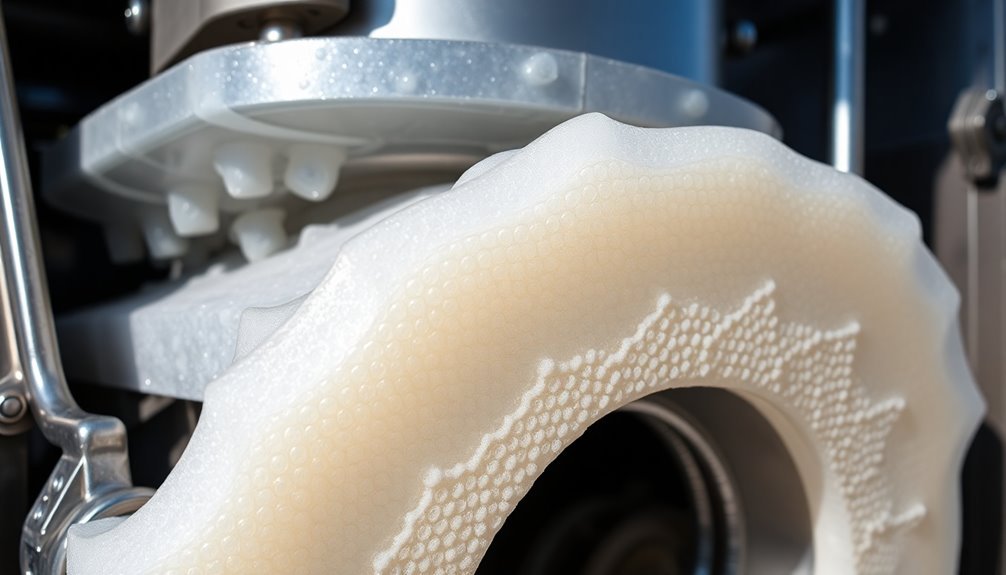
When handling anti-foam materials, you'll need to follow proper loading procedures by lifting containers close to your body and using mechanical aids whenever possible.
Training employees on ergonomic principles helps prevent workplace injuries and strains during material handling tasks.
You should optimize your storage space by stacking heavier containers at the bottom and maintaining clear pathways between storage areas to prevent accidents.
Make sure you're maximizing vertical space while keeping frequently used anti-foam products easily accessible, and always secure containers to prevent spills or leaks.
Safe Loading Procedures
Through careful implementation of safe loading procedures, workers can substantially reduce workplace accidents and injuries during material handling operations. You'll need to guarantee proper dock safety by marking edges clearly and installing barriers with warning signs. It's vital to use dock boards or plates to bridge gaps between docks and trailers, and always secure truck wheels with chock blocks.
When loading or unloading materials, you shouldn't operate powered equipment without proper training and authorization. Modern facilities are increasingly implementing smart wearable devices to monitor worker fatigue and environmental risks during loading operations. Use mechanical aids like forklifts, hand trucks, and dollies whenever possible, and make sure there's adequate lighting in truck trailers. Keep drivers in designated waiting areas during operations.
Safety Element | Required Action | Key Equipment |
---|---|---|
Dock Edge | Mark clearly | Warning signs |
Gap Protection | Bridge spaces | Dock boards |
Vehicle Security | Prevent movement | Chock blocks |
Material Support | Use aids | Forklifts/dollies |
Worker Safety | Wear PPE | Boots/gloves/helmets |
Remember to maintain clear aisles and sufficient clearance for equipment movement. You'll need to use ramps or blocking when working between different levels, and always wear appropriate PPE including steel-toed boots, gloves, and hard hats during handling tasks.
Storage Space Optimization
Effective storage space optimization builds upon safe loading practices to maximize warehouse efficiency and productivity. You'll need to start by evaluating your current layout, measuring total usable space, and identifying areas where you're losing valuable storage capacity through inefficiencies or poor organization.
Maximize your vertical space by implementing tall shelving units and considering mezzanine levels where appropriate. You can double or triple your storage capacity without expanding floor space by using high-reaching pallet racking systems and adjustable shelving that adapts to your changing inventory needs.
Choose the right storage system for your specific requirements. If you're handling large, sturdy products, floor stacking might work best. For fast-moving items, consider pallet-flow racking with FIFO rotation. Push-back racking can help maximize space while minimizing handling time.
Implement the 5-S methodology and lean management principles to maintain organization and reduce waste. Place your highest-selling products in easily accessible locations, and conduct regular reviews to eliminate obsolete inventory.
Remember to schedule quarterly evaluations to gather employee feedback and make necessary adjustments to your layout for continuous improvement.
Protection Standards For Sensitive Equipment
Three core principles govern protection standards for sensitive equipment: safeguard design, performance criteria, and physical protection measures. You'll need to guarantee your machinery complies with EN ISO 12100 and the Machinery Directive while implementing protection against tampering and unauthorized access.
Regular maintenance by qualified personnel isn't just recommended—it's essential for maintaining equipment integrity and operational safety.
To protect your sensitive equipment effectively, you'll want to incorporate various protective devices and safety measures:
- Install electrosensitive protective equipment (ESPE) like light curtains and laser scanners to secure danger zones without physical barriers
- Implement pressure-sensitive mats and edges that can immediately halt dangerous movements
- Use two-hand pushbuttons and enabling devices to keep operators' hands safely positioned
- Follow safety distance requirements specified in EN ISO 13854 and EN ISO 13857
Don't forget about personal protective equipment (PPE) requirements. Your safety measures should include appropriate hand protection, eye protection, and hearing protection based on specific task requirements.
Remember that supporting utilities like power and HVAC systems must also be secured to prevent operational disruptions and maintain equipment integrity.
Storage And Shipping Solutions
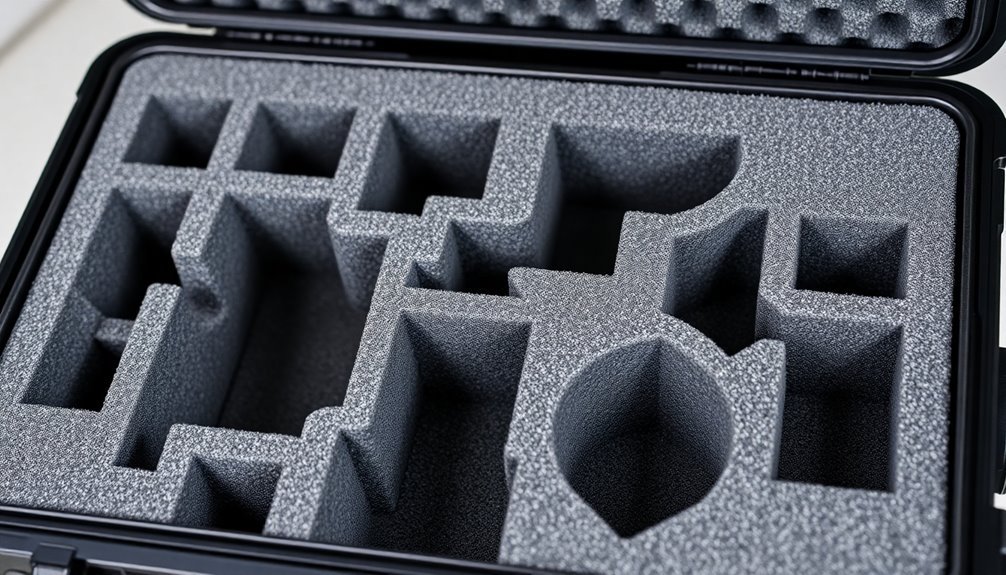
For military and industrial equipment, thorough storage and shipping solutions demand both versatility and precision. You'll find various storage options, from weapon racks to mobile shelving systems, all designed to maximize operational readiness while ensuring your equipment's security and accessibility.
Climate-controlled storage plays a vital role in protecting your sensitive equipment. You'll benefit from advanced humidity control technology that prevents corrosion and reduces maintenance requirements for items like drones, aircraft, and electronic devices.
When you're storing military vehicles or equipment, these controlled environments will substantially extend their operational lifespan.
Your storage needs can be met through customizable solutions, including tactical readiness lockers and high-density mobile systems. You'll appreciate the all-steel construction and advanced security features, while the modular design lets you adapt to changing storage requirements.
For shipping, you've got access to various foam packaging materials, including polyurethane, polyethylene, and pyrosorb foam. These materials will protect your equipment from vibration and impact damage during transport.
You can choose custom foam inserts or pick-and-pluck solutions to create perfect-fit packaging that meets IMDS, REACH, and RoHS regulations.
Frequently Asked Questions
Can Anti-Foam Materials Be Safely Used With Food Processing Equipment?
Yes, you can safely use food-grade anti-foam materials in your food processing equipment. They're regulated, non-toxic, and must comply with specific standards like 21 CFR 173.340 for food safety certifications.
What Is the Average Lifespan of Custom-Cut Foam Inserts?
You'll find custom-cut foam inserts typically last 5-8 years with proper care. However, your usage frequency, stored items' weight, and environmental conditions can shorten or extend this lifespan substantially.
How Do Temperature Extremes Affect Anti-Static Foam Properties?
Your anti-static foam's properties will substantially degrade at high temperatures above 75°C, causing faster decay and reduced ESD protection. You'll notice decreased viscosity and weakened antistatic performance in extreme temperature conditions.
Are There Eco-Friendly Alternatives to Traditional Anti-Foam Materials?
Yes, you'll find numerous eco-friendly anti-foam options made from vegetable oils and natural biopolymers. They're biodegradable, non-toxic, and often perform better than traditional materials while meeting strict ecological and food-safety standards.
Can Custom Foam Inserts Be Modified After Initial Cutting?
Yes, you can modify custom foam inserts after initial cutting by carefully trimming, adding layers, or using adhesives. However, you'll need proper tools and patience, as complex modifications might affect the foam's protective qualities.
In Summary
You'll find that properly implemented anti-foam protection goes beyond just selecting the right material. By understanding sizing requirements, cutting techniques, and protection standards, you're better equipped to safeguard sensitive equipment. Whether you're shipping electronics or storing delicate instruments, custom-fit anti-static foam solutions protect your investments. Remember to follow material handling guidelines and storage protocols for ideal results.
Leave a Reply